Discover the effective ways to enhance cushion injection molding in polymers for boosted structural integrity and performance.
To increase cushion in injection molding, it’s crucial to understand that the cushion is a small amount of plastic material that’s left in the injection barrel at the end of each molding cycle. This ensures that there’s always enough material to completely fill the mold cavity.
To increase the cushion, you can adjust the shot size on the injection molding machine. This involves increasing the amount of material in the barrel before the injection process begins. However, it’s important to note that while increasing the cushion can improve the quality of the finished product, it can also lead to overpacking and related issues if not monitored carefully.
In the following sections, we will delve deeper into the process, discussing the importance of cushion in injection molding, how to accurately measure it, and the potential problems that can arise from improper cushion management.
Key takeaways:
- Importance of Cushion: Ensures accurate and complete filling of plastic parts.
- Optimal Cushion Size: Finding the right cushion size is crucial for each plastic part.
- Recognizing Inconsistent Cushion: Common cause of defects, monitor for variations.
- Control Measures: Adjust machine parameters, material selection, and pre-treatment.
- Use of Technology: Advanced machines with cushion monitoring technology.
Understanding the Basics of Cushion Injection Molding
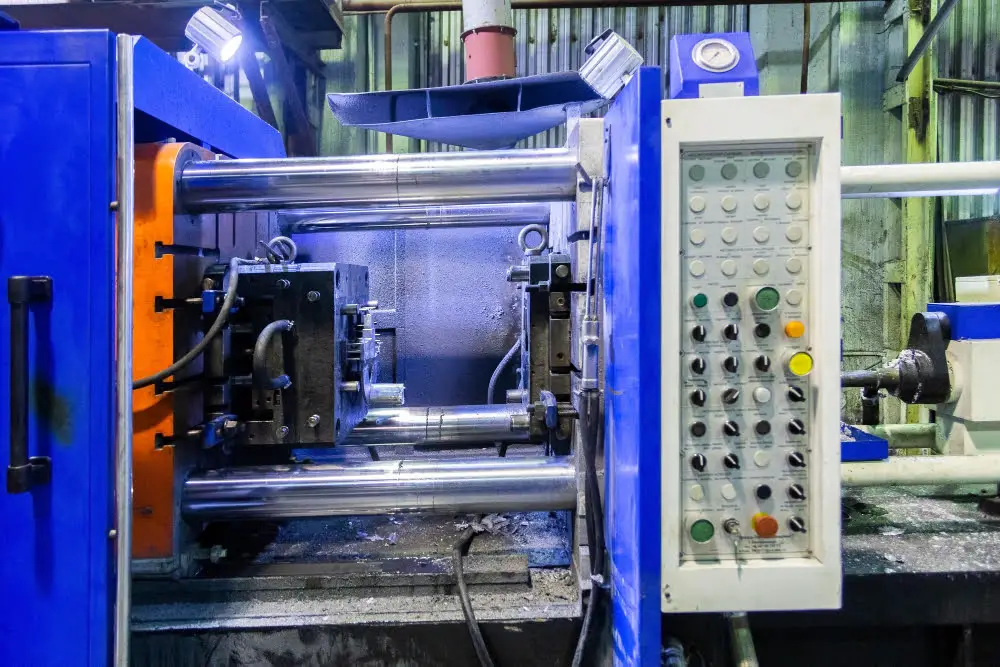
Cushion injection molding, known in the industry as the machine’s “shot volume control”, is an essential concept for achieving product consistency and reducing defects in injection-molded plastic parts. The cushion is a reserved volume of molten plastic inside the barrel of an injection molding machine.
At the heart of the process is the creation of a molten plastic reservoir that ensures consistent pressure and volume when the machine injects the plastic into the mold. It plays an instrumental role in maintaining accurate and consistent part dimensions.
Here are key aspects of cushion injection molding:
- Importance of Cushion: It provides a buffer during the final stages of injection, ensuring that each part is accurately and completely filled with plastic. It also accommodates the natural shrinkage of cooling plastic, helping to prevent voids and sink marks.
- Optimal Cushion Size: For each plastic part, there’s a correct cushion size. An oversize cushion results in wasted material while an undersized one can cause incomplete parts. Process optimization involves finding and maintaining this ideal cushion size.
- Recognizing Inconsistent Cushion: It’s a common cause of defects in injection-molded parts. Any changes in material viscosity, temperature, machine performance, or mold condition can influence cushion consistency. Regular machine and process monitoring is crucial to detect and respond to variations.
- Control Measures: To achieve an optimal cushion, tweaking machine parameters such as back pressure, injection speed, and barrel temperatures may be necessary. Proper material selection and pre-treatment can also play a significant role in enhancing process stability.
- Use of Technology: Advanced injection molding machines now come equipped with cushion monitoring technology that provides real-time feedback, allowing for immediate adjustment and enhancing precision, yield, and product consistency.
It’s clear that cushion optimization is a vital part of attaining high-quality outputs in injection molding. Harness its advantages by acquiring a detailed understanding of its role, and learn how to effectively manage it in every round of molding. By doing so, the end product will reflect your keenness for quality, precision, and efficiency.
Selecting the Right Polymer Material for Cushion Injection Molding
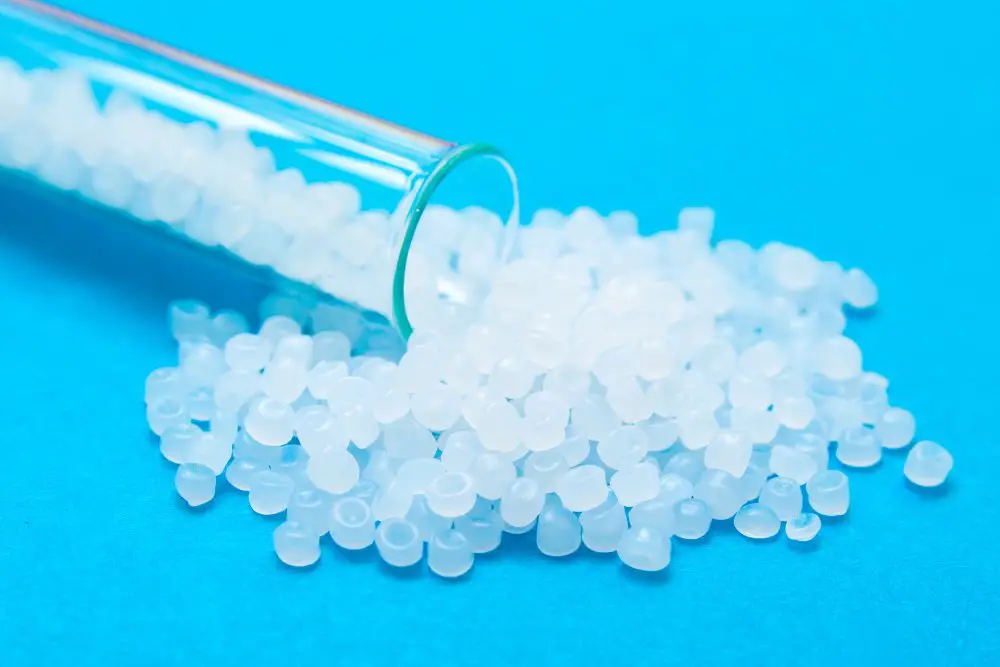
Certain polymers offer unique qualities, making them ideal for different cushioning properties. For durable, flexible, and waterproof cushioning, silicone-based polymers can be considered. For high-resilience cushioning, polyurethane (PU) based polymers are highly recommended. Additionally, thermoplastic rubber exhibits qualities like high elasticity and weather resistance, suitable for outdoor applications.
Choosing the right material involves considering:
- The end-use of the cushion.
- Specific properties required, such as elasticity, hardness, resilience or weather resistance.
- Government and industry regulations for safety and environmental impact.
- The production cost. Economical polymers can reduce manufacturing costs while premium polymers may offer superior properties.
Finally, always ensure optimum polymer quality. This impacts not only the cushioning properties but also the efficiency and success of the injection molding process. To verify quality, one can use a number of tests such as tensile testing or differential scanning calorimetry.
Implementing material selection strategies and constant testing promotes a highly efficient and cost-effective cushion injection molding process. Always remember, it’s not just about selecting the ‘best’ polymer, but the ‘right’ polymer for the specific demand of the application.
Efficiency Boosting Techniques in Cushion Injection Molding
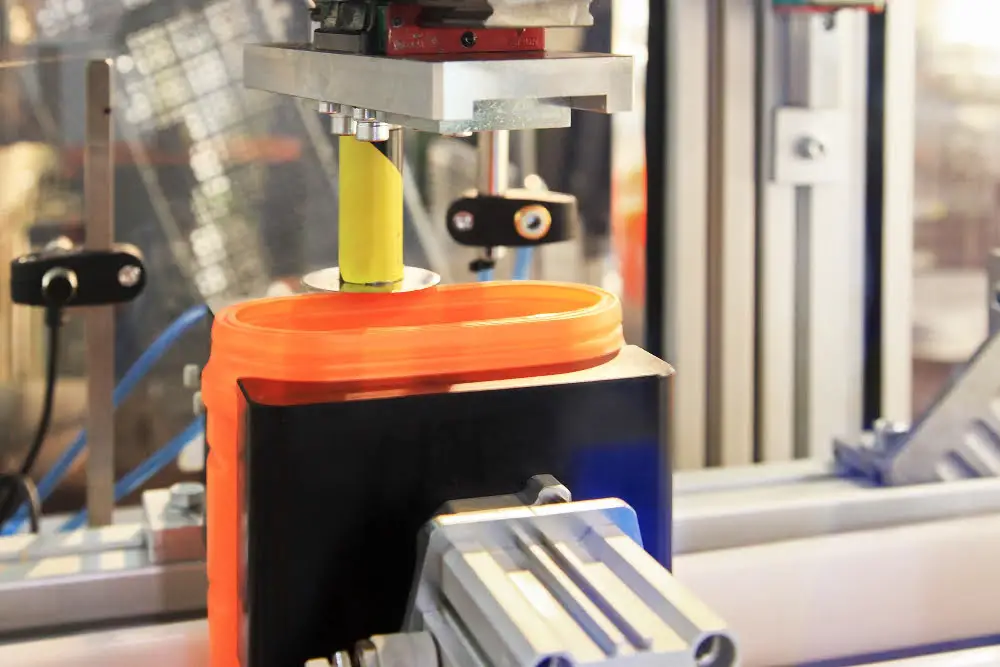
Maintaining uniform wall thickness during the injection process can enhance energy efficiency significantly. This eliminates the need for extended cooling times, thus saving energy and increasing productivity.
Material temperature is another critical factor. Ensure the polymer is at the optimal temperature before injection. This state improves the flow and reduces the risk of defects or stress points forming in the finished product.
Employing a slow-fast-slow plunger speed method can greatly improve the efficiency and consistency of the finished product. Starting and ending with a slow pace while speeding up in the middle phase helps ensure a balanced and complete fill of the mould.
Use advanced control systems with real-time monitoring capabilities. These systems can provide immediate feedback, allowing you to adjust the process parameters swiftly for superior part quality and enhanced efficiency.
Mitigating machine wear is essential. Consider investing in high-quality components and regularly schedule maintenance. This approach reduces downtime and increases the operational lifespan of the molding machine.
Finally, keep in mind the organization and cleanliness of the injection molding area. A well-kept workspace can improve workflow, productivity, and the safety of the operation overall.
Identifying and Addressing Common Causes of Inconsistent Cushion
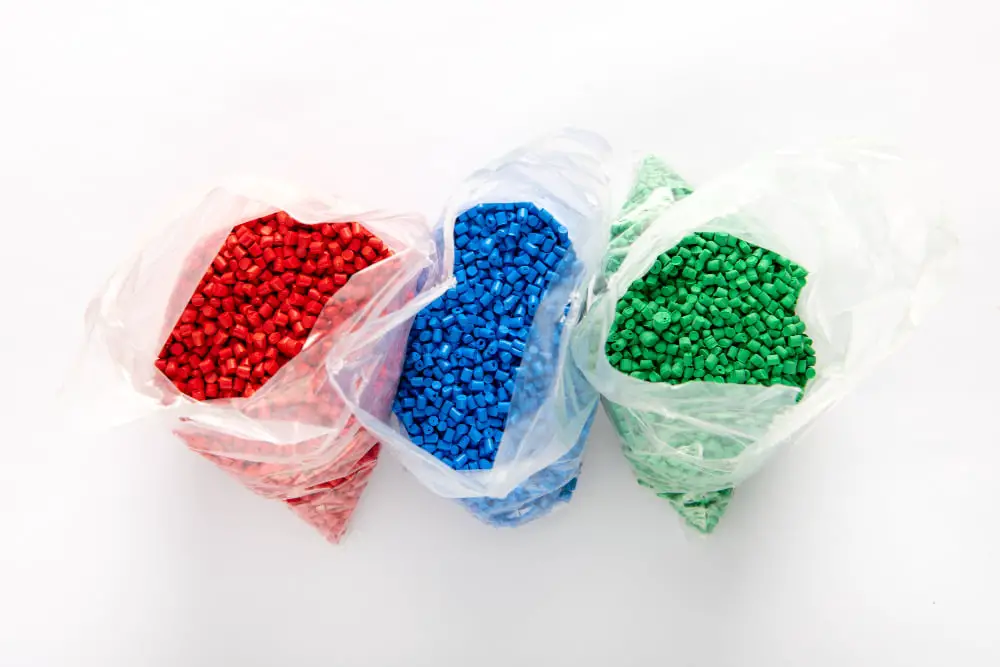
Inconsistent cushion is predominantly caused by three factors in the molding process: fluctuations in material consistency, machine malfunctions, and improper processing parameters.
Material consistency is vital. Ensure the materials are free from moisture, contamination, or other impediments that could lead to inconsistency.
Machine malfunctions are another common cause. Regular equipment maintenance is crucial. Always monitor any signs of wear and tear and replace or repair components promptly.
Processing parameters play a significant role. Accurately calculate and set the right injection speed, back pressure, and screw RPM to ensure a consistently optimal cushion.
Skillful handling of these potential pitfalls helps in delivering reliable and high-quality cushion injection molding production. Utilizing automation technologies in the process can also significantly reduce inconsistencies, further improving the cushion molding process.
Cost-Effective Solutions and Techniques for Cushion Injection Molding
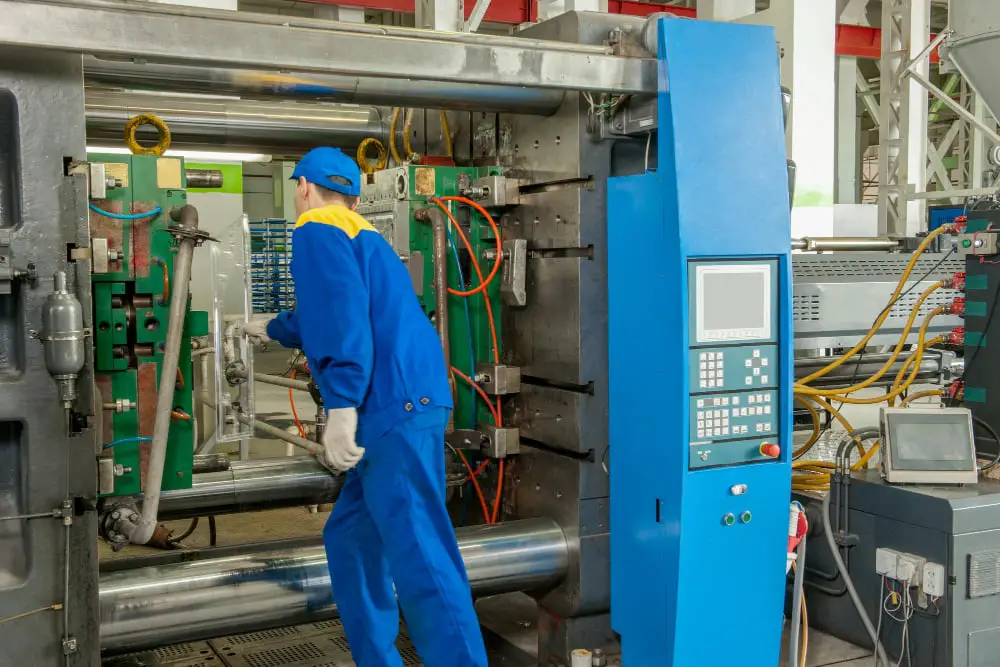
Managing material usage is a vital aspect in reducing costs. High-quality polymers are cost-effective, as they reduce defects and wastage.
Advancements in technology have provided data analysis tools, helping to monitor the entire process. These tools provide actionable insights, alerting when there’s irregularity or inefficiency.
Maintaining regular machine servicing is a tried-and-true method of reducing unexpected downtimes and costly repairs.
Exploring automation opportunities can significantly cut labor costs and enhance consistency. Robotics and automated systems can handle repetitive tasks with precision.
Implementing the use of energy-efficient machines and techniques can lower energy consumption drastically.
Lean manufacturing principles can be applied to condense the process, removing unnecessary steps and maximizing productivity.
Adopting a Just-In-Time inventory system can reduce storage costs and enhance material handling efficiency, ensuring materials are only ordered when necessary.
Using computer-aided design (CAD) can pre-empt potential design faults, saving both time and resources in the manufacturing process.
By following these methods, it is possible to increase cushion injection molding performance without drastically increasing costs.
Harnessing Practical Resources for Maximum Efficiency in Cushion Injection Molding
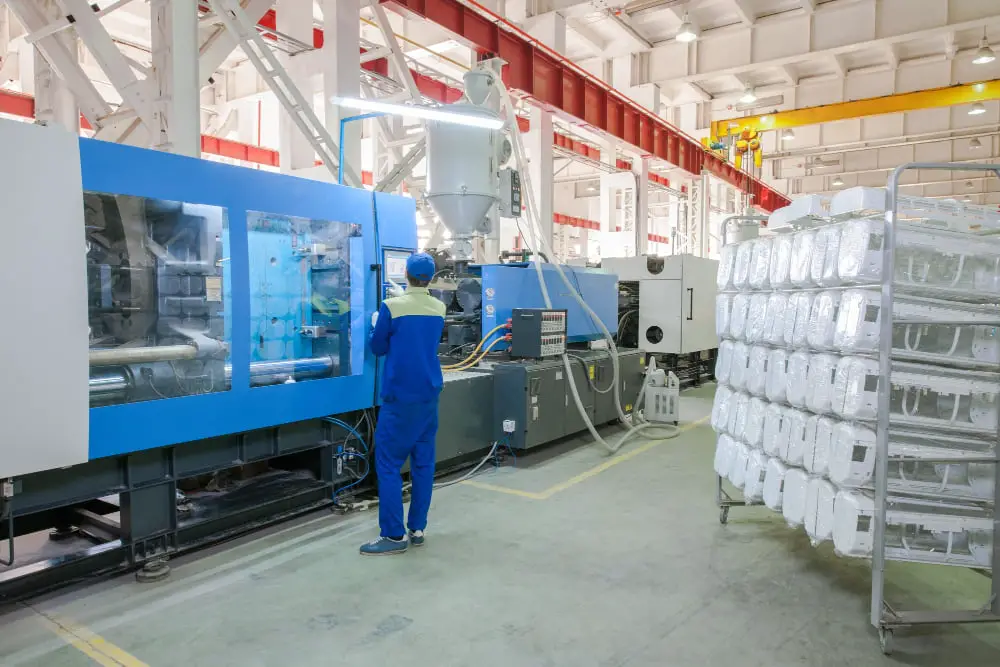
Harnessing practical resources involves the careful selection and utilization of the best tools, methods, and materials to achieve maximum efficiency in cushion injection molding.
First on the list is the use of high-quality injection molding machines equipped with advanced technologies. Modern machines offer better control over speed, pressure, and temperature which are vital for consistent molding processes.
Secondly, training and development of staff is indispensable. Whether it’s the machine operator or the quality control manager, a better understanding of the process significantly improves efficiency and reduces waste.
Thirdly, the use of software tools cannot be overstated. Tools like Computer-Aided Design (CAD) and Computer-Aided Manufacturing (CAM) help in mold design and process optimization respectively. A well-designed mold reduces cycle time and increases productivity.
Lastly, maintaining a robust preventative maintenance schedule ensures machines are always in optimal condition. Regular cleanings, inspections, and lubrication reduce downtime and increase overall machine lifespan.
Enhancing cushion injection molding efficiency is not about grand, complex changes but rather small, strategic decisions and consistent habits that lead to beneficial results.
Driving Profitability Through Optimized Cushion Injection Molding
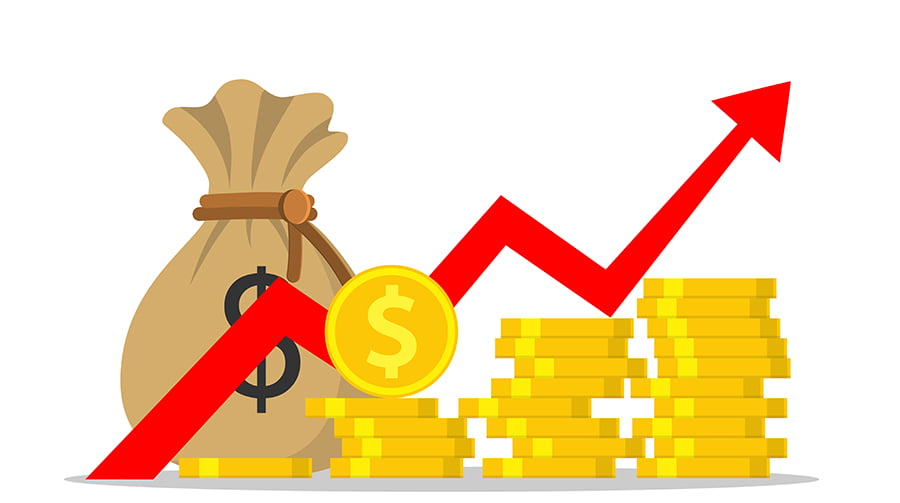
Implementing well-thought-out tactics can transform the process of cushion injection molding, boosting both results and profitability.
Reducing raw material waste is a proving strategy. Utilize monitoring systems that feed real-time data into a central dashboard to optimize material usage. Careful management can result in significant savings.
Adopting an energy-efficient machinery model helps drive down operating costs. Look for options that are touted for their lower energy consumption. With time, they can have a major impact on your bottom line.
Workforce training cannot be overlooked. A team that is adept at handling the machinery, troubleshooting issues, and maintaining quality control ensures that the production line stays efficient.
Investing in advanced automation leads to increase in productivity. Automated systems can handle repetitive tasks, yielding better accuracy and consistency, and allowing the human workforce to focus on more complex aspects of the production process.
It’s key to regularly maintain and service the machinery. The upfront cost of preventive maintenance often outweighs the heavy repair costs resulting from breakdowns or system failures.
Lastly, fostering supplier relationships is vital. It allows you to negotiate contracts that might help reduce input costs and ensure a regular supply to meet the production demands.
Each of these steps is pivotal in driving profitability through optimized cushion injection molding and a thorough understanding of them can be game-changing in the industry.
FAQ
Why is my injection molding machine not holding cushion?
Your injection molding machine may not be holding cushion either due to insufficient back pressure requiring an increase for consistent shot to shot, or because of wear or damage on the screw, barrel and check ring.
What size cushion for injection molding?
For injection molding, cushion values are generally maintained around 0.20 in. or 5 mm for screw diameters of 25 to 60 mm, with larger cushions necessitated for larger screw diameters, in congruence with the viable rule among molders that cushion values should align with a certain percentage of the shot size or the screw diameter.
What is cushion in injection molding?
In injection molding, a cushion refers to the residual material left in the barrel, in front of the screw, after mold filling and pack stages, that prevents the screw from bottoming out against the front of the barrel, thus ensuring control of packing.
What is the reason for cushion variation in injection molding?
The variation in cushion in injection molding is primarily caused by improper packing, insufficient pressure, and inconsistent shot sizes, leading to a higher rate of discarded parts due to unacceptability.
How is the cushion size adjusted in the injection molding process?
The cushion size in the injection molding process is adjusted by modifying the screw’s back pressure and rotation speed.
What are common issues associated with insufficient cushion in injection molding?
Insufficient cushion in injection molding can lead to poor quality molded parts such as shrinkage, warping, short shots, and inconsistent dimensional properties.
What role does cushion play in ensuring the quality of molded parts?
Cushion ensures the quality of molded parts by maintaining consistent pressure during the injection molding process, thereby preventing shrinkage or deformation of the part.
Recap