Discover effective strategies to minimize shrinkage in injection molding, thereby enhancing the quality and durability of your polymer products.
Shrinkage in injection molding is a common challenge that many face, but there are effective ways to manage it. By optimizing the processing parameters such as holding pressure, holding time, and cooling time, you can significantly reduce shrinkage.
Material selection also plays a crucial role, as different polymers have varying shrink rates. Furthermore, the design of the mold itself, including wall thickness and gate location, can influence the shrinkage.
In this article, we will delve into each of these factors in detail, providing you with a comprehensive guide on how to reduce shrinkage in injection molding.
Key takeaways:
- Optimize processing parameters to reduce shrinkage.
- Proper material selection is critical in managing shrinkage.
- Mold design and wall thickness affect shrinkage.
- Understanding the dynamics of shrinkage helps with control.
- Consider client requirements and product use to minimize shrinkage.
Understanding the Causes of Shrinkage in Injection Molding
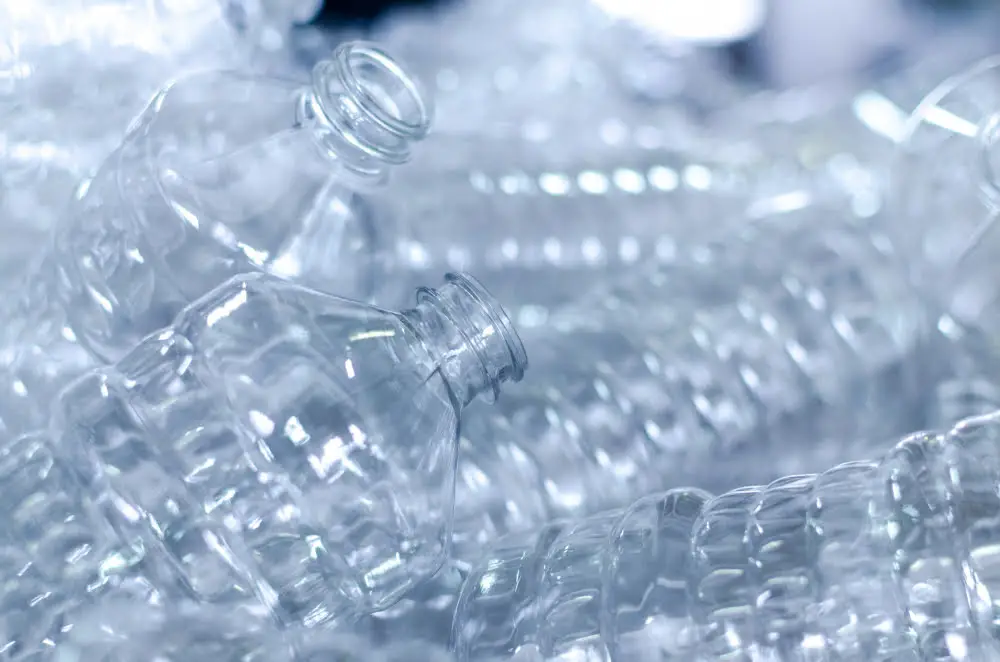
Shrinkage in injection molding typically occurs due to three core factors: the cooling process, pressure variances, and material choice.
The cooling process is the first instance where shrinkage can occur. As the molten plastic cools in the mold, it contracts, causing the material to potentially pull away from the sides of the mold and reduce the final part size. Controlling cooling rates and ensuring even cooling can manage this factor.
Pressure variances within the mold also contribute to shrinkage. Higher packing pressures can decrease part shrinkage by ensuring the mold is optimally filled. However, maintaining a balance is crucial because excessive packing pressure might lead to overpacking and cause stress, which could result in additional shrinkage problems.
Material choice plays a significant role in determining the amount of shrinkage that can occur. Different materials have different levels of shrinkage – some materials like nylon, experience higher shrinkage rates, whereas others, like certain types of polyethylene, have relatively low shrinkage rates. Proper material selection can lessen the likelihood of shrinkage.
In our next section, we will delve into the dynamics of shrinkage in the injection molding process, equipping you with comprehensive insight into this often challenging factor.
Exploring the Dynamics of Shrinkage in the Injection Molding Process
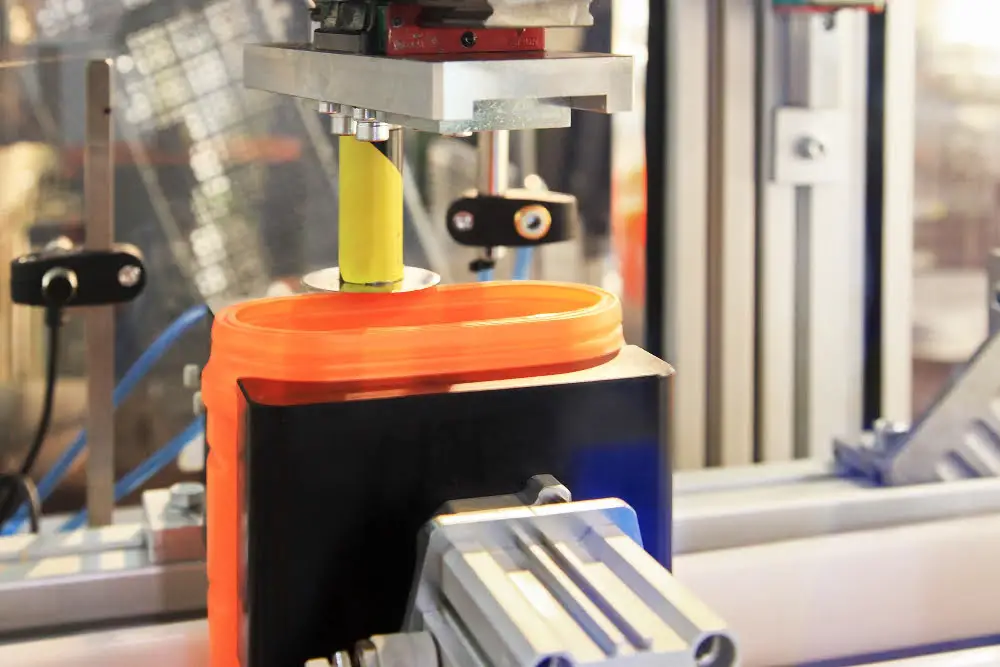
The process of injection molding is quite dynamic, and shrinkage is an intrinsic part of it.
The plastic material is first heated until it reaches a molten state. It is during this phase that the polymer chains become highly mobile, causing the material’s volume to increase.
The molten plastic is then injected into the mold, which is cooler than the plastic. Once inside the mold, the plastic begins to cool and solidify or ‘set’, gradually adopting the shape of the mold.
The cooling process is when the shrinkage primarily occurs. As the plastic solidifies, its volume begins to decrease – this reduction in volume is what we refer to as ‘shrinkage’.
Shrinkage continues, albeit at a slower rate, even after the molded plastic is ejected from the mold. This is due to the residual heat in the plastic causing further cooling and solidification, and thus further shrinkage.
Factors such as the type of plastic being used, the design of the mold, and the conditions under which the molding process is carried out, all contribute to the amount of shrinkage that can occur. Understanding these mechanics allows for the effective control and reduction of shrinkage, improving the dimensional accuracy of the final product.
Effective Ways to Manage and Prevent Shrinkage in Injection Molding
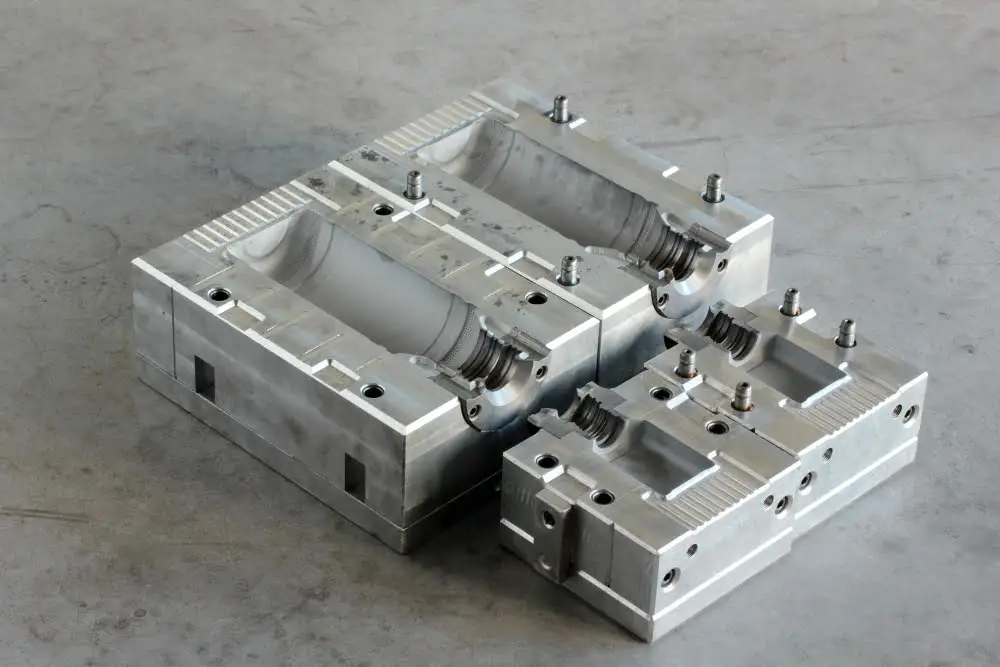
Managing shrinkage in injection molding involves a combination of optimising the molding process, using the right materials, and understanding client specifications. Here are notable strategies:
Proper Mold Design: Molds need a uniform wall thickness for even cooling, and hence, less shrinkage. Designing the molds with rounded corners can also reduce the effect of shrinkage.
Choice of Material: Material choice highly influences shrinkage. Thermoplastics, for example, have different shrink rates. Understanding these rates helps in the selection of appropriate materials for molding.
Control of Molding Conditions: Conditions such as temperature, pressure, and cooling time can be manipulated to manage shrinkage. It is vital to maintain optimal conditions throughout the process.
Use of Filling Simulation software: Software tools allow prediction and control of shrinkage by simulating material flow and cooling behaviors.
Mold Temperature Control Systems: Using such systems can maintain the mold temperature within a specified range, ensuring even shrinkage.
Post-Molding Annealing: This process involves heating the part above its glass transition temperature and then slowly cooling it to relieve internal stresses and thus reduce shrinkage.
Adherence to these mechanisms reduces the likelihood of shrinkage, thereby boosting the quality of the products. By embracing a troubleshooting attitude, manufacturers can identify and tackle the root cause of shrinkage in the injection molding process.
Understanding Client Specific Requirements to Reduce Shrinkage
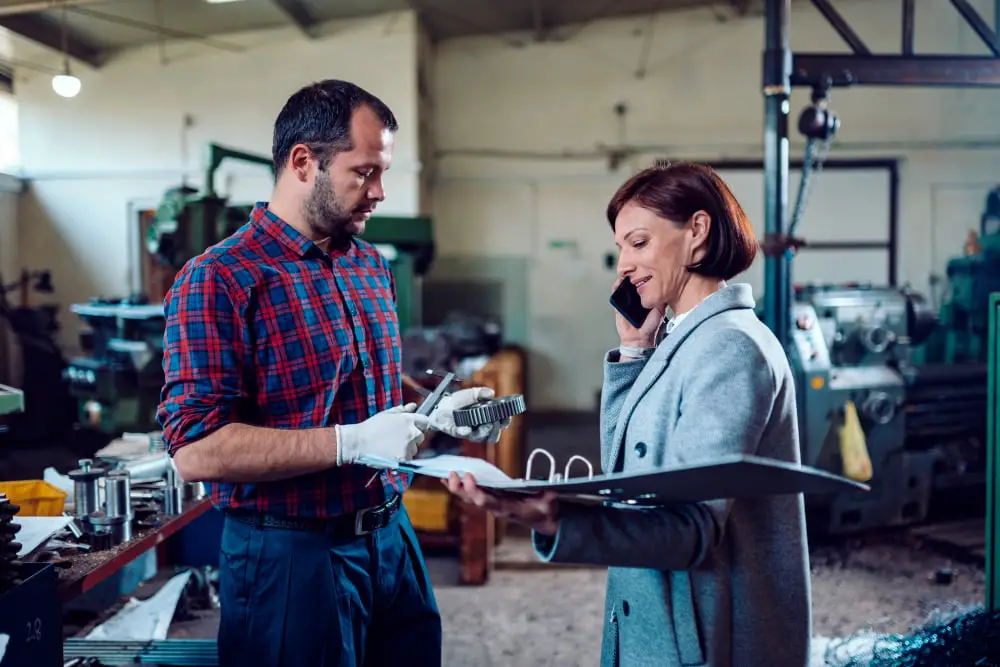
Gaining an in-depth understanding of the client’s expectations and product use can offer invaluable insight in curbing shrinkage. Essential information includes the part’s function, the environment in which the part will be used, amount of load the part will bear, and the longevity of the element. All this information shapes the selection and treatment of the polymer during injection molding.
- Determine part’s function: Knowing what the product will be used for allows manufacturers to select a polymer compound that can effectively reduce shrinkage while fulfilling its purpose.
- Understand the environment: The conditions in which the product will be used, including temperature and humidity, affects the type of polymer chosen and the injection molding process.
- Assess the load bearing capacity: If the part is expected to bear significant load, more sturdy and less shrinkable materials can be used.
- Consider the product’s lifespan expectations: For a product expected to last for many years, materials with higher resistance to shrinkage over time can be selected.
By applying these considerations in the planning phase, the problem of shrinkage can be addressed efficiently right from the beginning of the manufacturing process.
Solutions for Shrinkage Reduction in Injection Molding
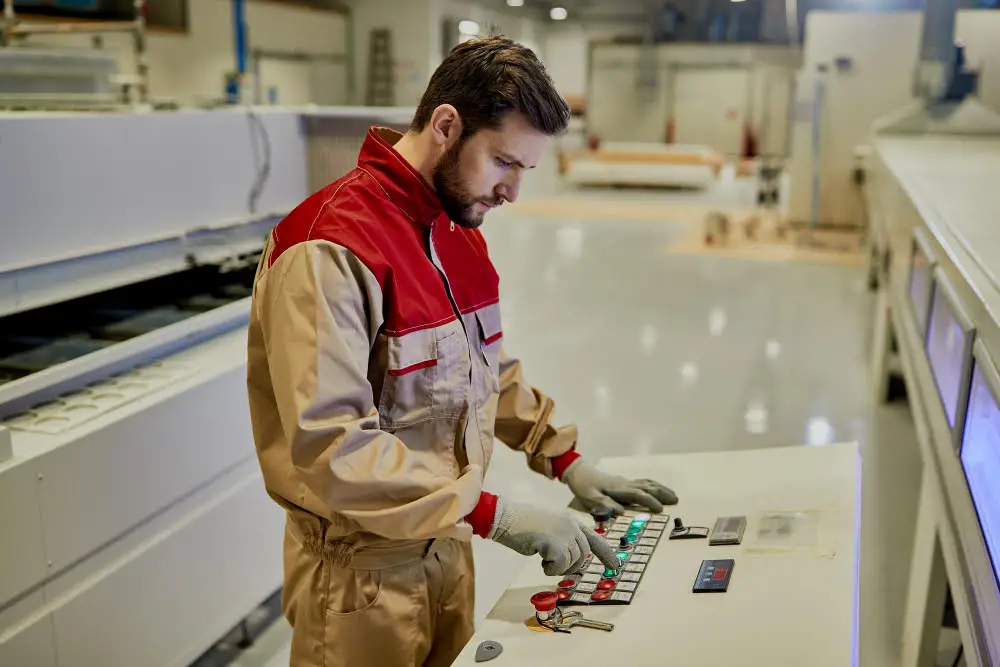
To combat the issue of shrinkage, several solutions can be applied to the injection molding process:
Control material temperature: This is vital in reducing shrinkage. A well-controlled material temperature correlates with how the plastic cools and contracts. Too hot and the polymer chains contract more, causing higher shrinkage.
Adjust injection speed: A slower injection speed tends to cause less shrinkage. However, this should be balanced as very slow speeds may result in premature cooling of the polymer, potentially causing defects.
Modify mold temperature: A lower mold temperature typically causes less shrinkage as the material cools more quickly, reducing the amount of time for the polymer chains to contract.
Optimize packing pressure: Achieving the right packing pressure is crucial for balancing the filling and packing phases and minimizing shrinkage. This typically involves increasing packing pressure to ensure the mold is filled fully, but not to the point of causing material stress which can lead to shrinkage.
Choosing the right polymer: Some polymers have low molecular contraction, reducing shrinkage levels. For example, crystalline polymers typically shrink more than amorphous polymers.
Reducing residual stress: Shrinkage can also be caused by residual stress in the molded part. This can be reduced by ensuring a smooth flow of the material during the injection process and minimizing warpage after ejection from the mold.
The Role of Materials in Minimizing Shrinkage in Injection Molding
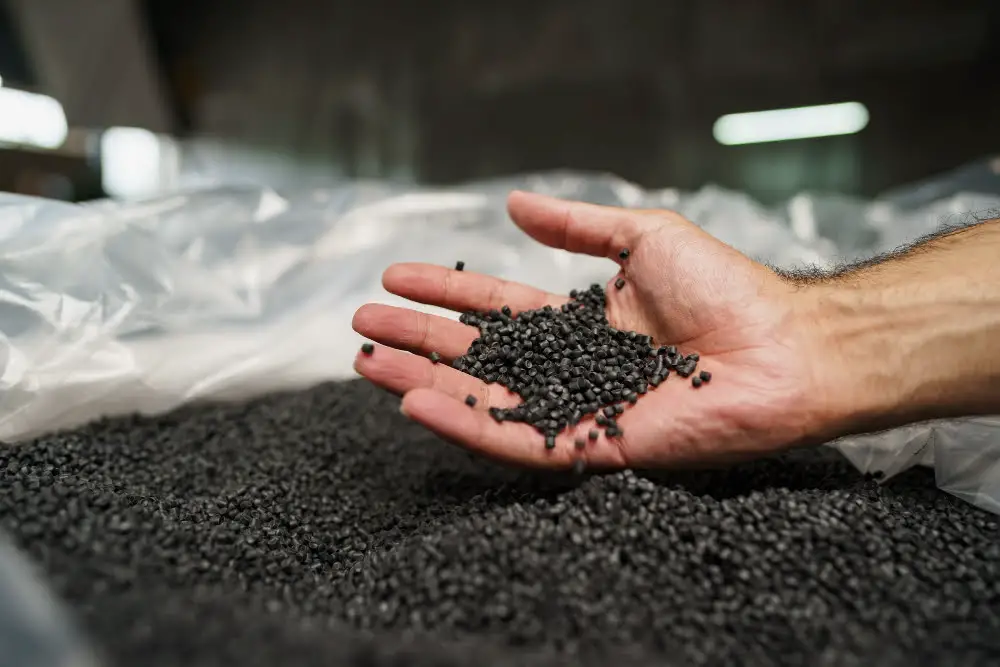
Choosing the appropriate polymer is crucial in reducing shrinkage. Each material behaves differently under varying conditions of temperature and pressure. High-performance thermoplastics, such as Polyetheretherketone (PEEK) and Polyphenylene Sulfide (PPS), are known for their low shrinkage rates.
Material selection should also take into account the end-use of the product. For outdoor applications, Ultraviolet (UV) resistant polymers like Acrylonitrile Butadiene Styrene (ABS) are beneficial. These materials are not just resistant to sunlight but also exhibit minimal shrinkage.
Moisture-resistant polymers can prove instrumental in mitigating shrinkage. Materials like Polyethylene (PE) and Polypropylene (PP) are inherently resistant to moisture, thereby ensuring dimensional stability and mitigating shrinkage in humid conditions.
In some scenarios, material modification through the addition of fillers can be used to minimize shrinkage. Fillers, such as glass fibers, can enhance the dimensional stability of the polymer during and after the molding process.
Finally, the use of flame-retardant materials such as flame-resistant Polyvinyl Chloride (PVC) can be beneficial in applications where exposure to high temperatures is anticipated. These materials not only provide safety against fire hazards but can also help in minimizing the shrinkage associated with thermal expansion and contraction.
Influence of Molding Conditions On Shrinkage
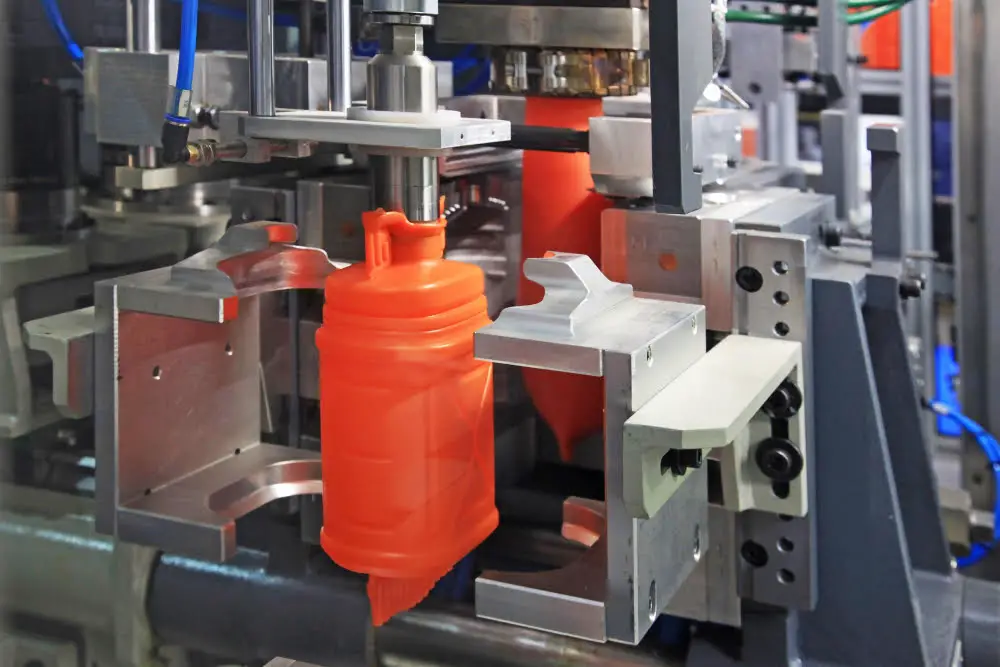
Molding condition plays a pivotal role in managing the level of shrinkage in the injection molding process. These conditions include temperature, pressure, and cooling rate, which can be fine-tuned to control the shrinkage.
Temperature settings in the molding process are crucial. Using too high or too low a temperature can lead to excessive shrinkage. A balanced temperature, within the specific heat range of the polymer, minimizes the risk of shrinkage.
Pressure also impacts the shrinkage rate. Proper pressure is needed to fill the mold completely, avoiding premature cooling and thus reducing shrinkage.
The cooling rate is another key factor. Faster cooling can lead to a significant shrinkage, particularly at the surface, causing warping. Hence, a slower, more controlled cooling rate is preferable.
Apart from these factors, the orientation of the components within the mold and the overall design of the mold itself also matter. A well-designed mold with appropriately oriented components can distribute the pressure more evenly and ensure a complete fill, thus preventing shrinkage.
Furthermore, using consistent processing conditions is essential. Inconsistent conditions could lead to differing levels of shrinkage throughout a production run.
Therefore, monitoring and adjusting these molding conditions can help to significantly reduce shrinkage in injection molding.
FAQ
What causes shrinkage in injection molding?
The shrinkage in injection molding is predominantly caused by high molecular weight resins, which possess a higher viscosity and induce a greater pressure drop, resulting in higher shrink rates in the final molded part.
How can you reduce the shrinkage of polypropylene?
To reduce the shrinkage of polypropylene, it’s necessary to increase injection pressure, decrease injection speed, enhance hold-on pressure, extend cooling time, ensure proper cooling line conditions, and moderate temperatures to below 200°C, preferably around 180-190°C, with a special emphasis on reducing Hot Runner Mould (HRM) temperature if applicable.
What are the factors affecting shrinkage in plastics?
The factors affecting shrinkage in plastics include part thickness, flow length, gate size, melt temperature, mold temperature, fill time, hold time, hold pressure, cooling time, and backpressure.
How does the injection molding process temperature affect polymer shrinkage?
The injection molding process temperature significantly influences polymer shrinkage, as higher temperatures can increase the material’s fluidity, leading to more shrinkage when the polymer cools and solidifies.
How does the choice of polymer type influence shrinkage in injection molding?
The choice of polymer type in injection molding directly influences shrinkage, as different polymers contract at different rates due to their unique thermal properties and crystallinity levels.
How can cooling rates and pressure influence the final shrinkage of the molded polymer?
Cooling rates and pressure directly influence the final shrinkage of the molded polymer, as higher cooling rates and increased pressures usually reduce shrinkage by limiting polymer chain mobility, promoting better molecular packing, and reducing residual stresses.
Recap