Injection molding is a versatile process that allows for the mass production of intricate polymer objects, transforming raw plastic granules into finished products in just a few steps.
Injection molding is a fascinating process used in the manufacturing of plastic parts, from small components to large panels. It involves melting plastic pellets, injecting the molten plastic into a mold, cooling it to solidify into the desired shape, and finally ejecting the finished part.
This process is favored for its precision, efficiency, and versatility in creating complex geometries and large volumes of parts.
In this article, we’ll delve into the intricacies of how injection molding works, its key components, the types of polymers used, and its applications in the construction industry.
So, whether you’re a curious learner or a professional seeking a refresher, this comprehensive guide has got you covered.
Key takeaways:
- Injection molding allows for the mass production of complex shapes.
- It is versatile, capable of producing large volumes of items.
- Precision is achievable, thanks to high-tech molding machines.
- Different types of polymers can be used in the process.
- Injection molding is cost-effective for large-scale production.
Definition of Injection Molding

Injection molding is a manufacturing process commonly used in the construction industry. It involves heating a material, which is then forced into a mold. The material takes the shape of the mold, hardens, and then is removed. The process is widely used for several reasons:
- Versatility: It’s capable of creating a vast array of complex shapes and sizes.
- High Volume Production: Offers the ability to produce items in large quantities, making it an excellent solution for mass production.
- Precision: Craft intricate and detailed components with a high degree of accuracy.
- Material Variety: Works with a broad spectrum of materials, not limited to just plastics but extends to metals and ceramics.
Injection molding opens up numerous possibilities in construction, from producing small fasteners for structures to developing large moldings for architectural applications. It provides ample leeway for creativity without compromising on the strength and durability of the final product.
Process of Injection Molding
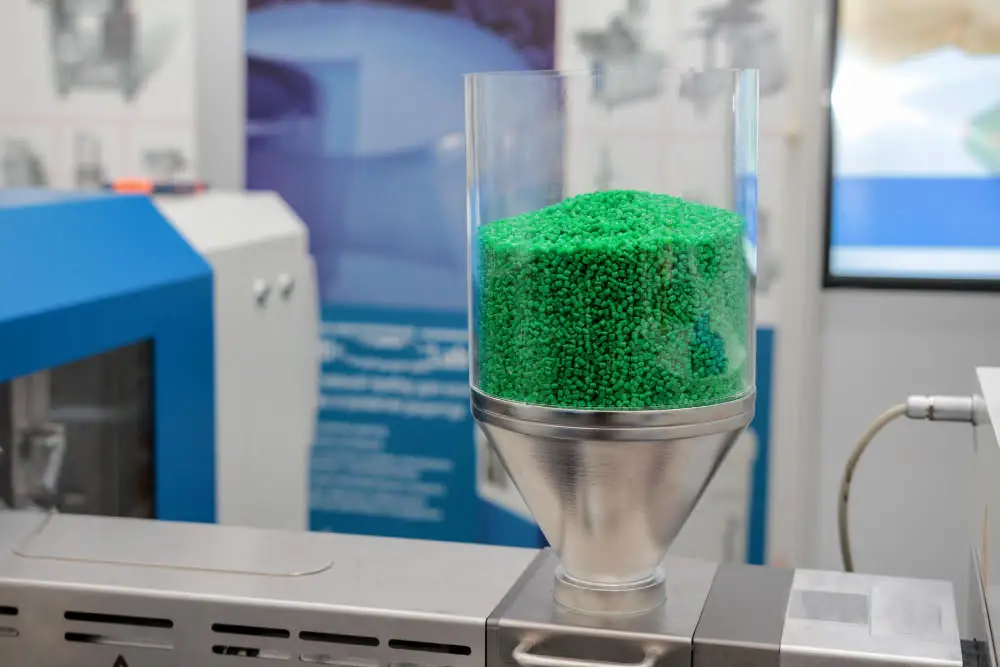
The process typically begins with the melting of the polymer material, which is fed into the injection molding machine. Once the material reaches a liquid state, it is pushed into a mold cavity shaped exactly like the desired end product.
Here are the key points of the process:
- Melting: The polymer is initially in granular form, put into a hopper. The hopper drops the polymer into a heated barrel where it is melted.
- Injection: The liquid material is subjected to high pressure and speed, pushing it into the mold cavity.
- Cooling: Once inside the mold, the material starts to cool and solidify, taking the precise shape of the mold. Cooling is a critical part of the process, as it directly affects the structure and quality of the final product.
- Ejection: After the polymer is cooled, the mold opens and the finished product is ejected. The mold is then ready for the next cycle.
It’s crucial to monitor the temperature, pressure, and cooling rate throughout the process as these factors significantly influence the characteristics of the final product.
Materials Used in Injection Molding
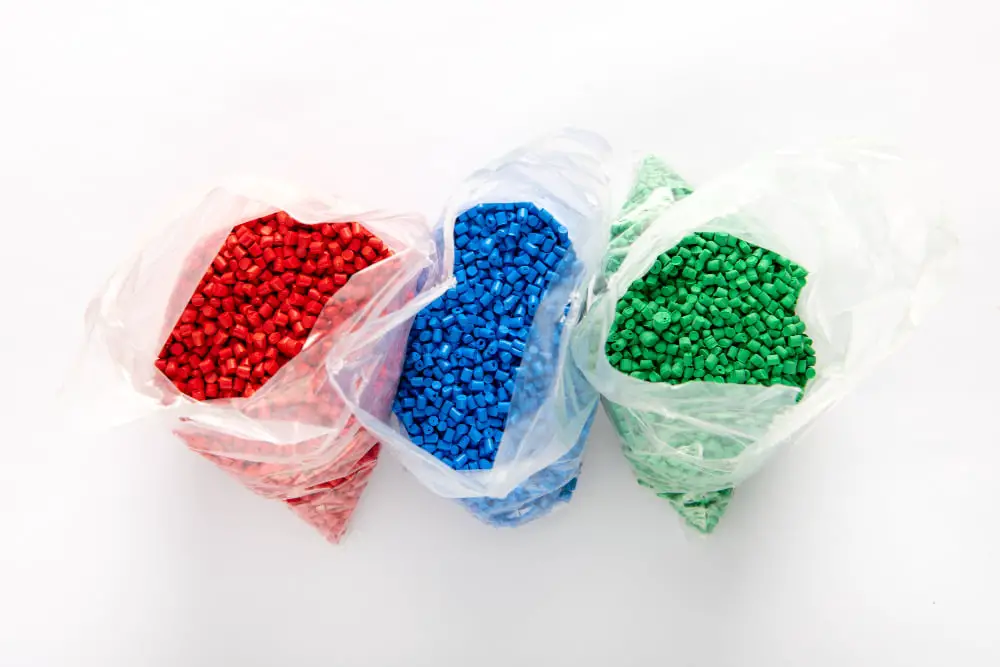
A variety of materials can be used for injection molding, depending on the desired final product’s characteristics. Thermoplastics, a type of polymer that becomes pliable when heated and solid when cooled, are the most commonly used. Examples of thermoplastics include Polyethylene, PVC, Polystyrene, Polypropylene, and ABS.
Thermosets, another type of polymer, also form a vital part of injection molding. Unlike Thermoplastics, Thermosets irreversibly cure, meaning they won’t melt or change shape after being molded. Think of materials like Epoxy and Phenolic Resin.
Elastomers, combining properties of both plastics and rubber, can also be subjected to this process. Their elasticity makes them perfect for products that need to return to their original shape after being distorted.
Choosing the right polymer depends on several factors, including temperature resistance, strength requirements, cost, and durability. For instance, Polyethylene, being durable and lightweight, is frequently used in creating bottles or other packaging materials. ABS, known for its high impact resistance and toughness, is often used in making power tool housing.
In addition, many molding processes involve the use of additives to enhance the properties of these base materials. Additives can improve factors like color, flame resistance, and improved strength. Choosing the right combination of materials and additives can ensure a final product with optimal characteristics for its intended use.
Precision Achievable With Injection Molding
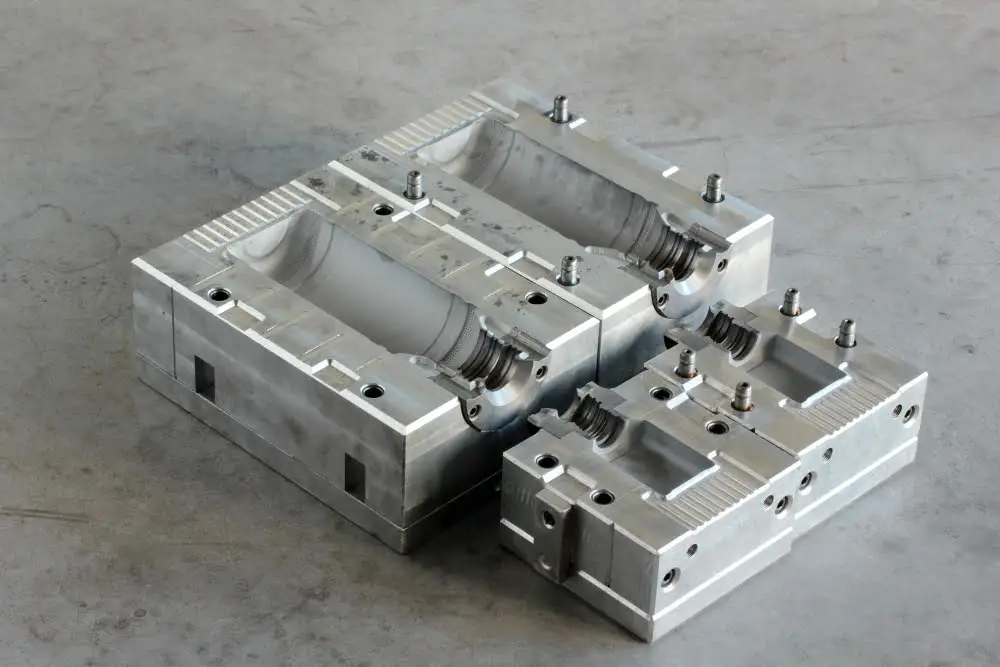
With advancements in technology, injection molding has remarkably improved its precision capabilities, allowing manufacturers to create parts with intricate details and geometric complexity.
Firstly, designers must establish clear specifications. Then, these precise guidelines communication to the molding machine, which creates a part to match the exact dimensions set out in the digital design.
High-precision injection molds are made from hardened steel or aluminum. The hardened steel molds last longer, whereas aluminum molds offer cost advantages but are less durable. The decision between steel and aluminum depends on the volume of the production run.
Virtually any thermosetting plastic or thermoplastic can be used in an injection molding machine. The choice of plastic material impacts the final part’s quality and durability. Manufacturers often opt for materials like polypropylene, ABS, and nylon for their favorable properties.
Surface finishes play a vital role in the precision of the final product. These finishes range from high gloss to textured surfaces and directly impact the product’s appearance, function, and durability.
Lastly, attention to cooling periods is crucial for ensuring dimensional stability of the molded parts. Too rapid cooling can lead to shrinkage and warping, while slow cooling may induce stress crystallization.
Realizing the maximum precision achievable with injection molding requires careful consideration of these factors – mold material, plastic type, surface finish, and cooling procedure – with an understanding that each element contributes to the final product’s overall quality and functionality.
Complex Details Achievable With Injection Molding
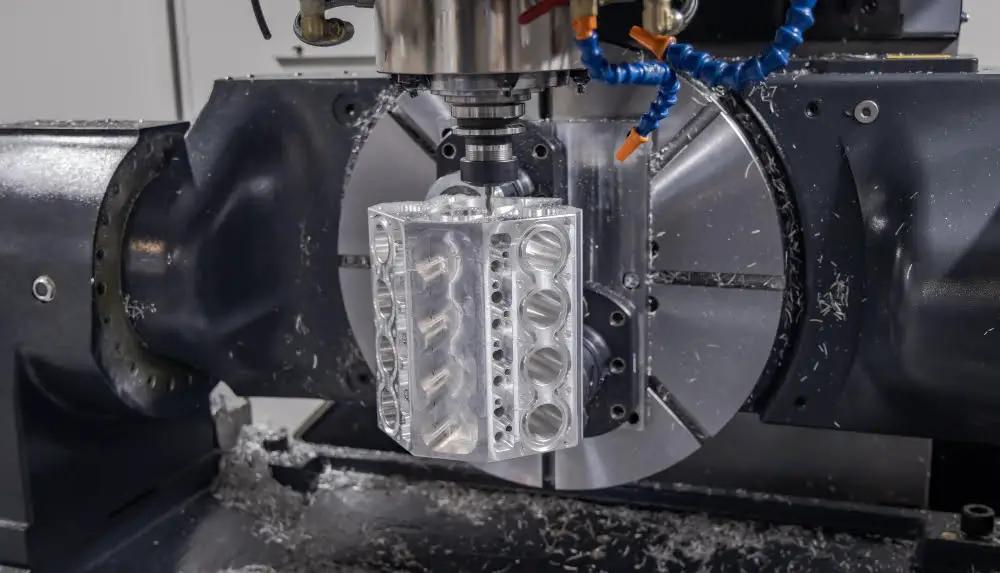
With injection molding, minute details are not lost but instead, firmly maintained in the final product. This advanced technology allows for the reproduction of intricate designs and patterns, which may be impossible to achieve by hand.
Multiple features can be incorporated into one part. This results in less manual assembly and fewer parts to maintain or replace, enhancing the operational efficiency of the construction process.
Another advantage is the creation of thin-walled sections. Often found in various construction materials, thin walls can be efficiently designed and produced at a fraction of the cost of other production methods.
Unmatched surface finish quality is also a critical aspect. With the right selection of materials and additives, an array of surface finishes and textures can be achieved, thus further expanding the stylistic and functional possibilities for construction.
Last but not least, undercuts – the features that cannot be de-molded in a straight pull mold due to their interlocking nature – can also be included in the designs. With specialized tools, these undercuts are handled in the process, making complex geometries feasible with injection molding.
Indeed, the application of injection molding brings endless possibilities in capturing complex details needed in construction.
Cost Efficiency of Injection Molding
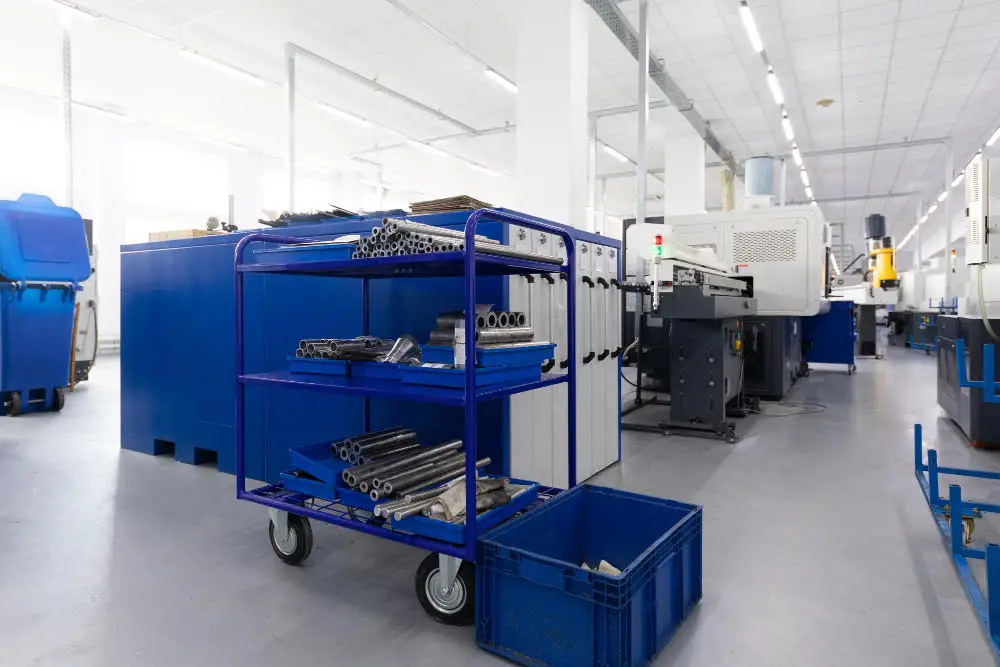
While injection molding may present a heftier initial investment due to the cost of molding tools, it becomes more economical in high-volume production runs.
The significant advantage of injection molding is its ability to scale. Once the initial costs are covered, the price per unit during injection molded manufacturing is extremely low.
The price also tends to drop drastically as more parts are produced. Such a scale of economy cannot be matched by other manufacturing processes, making injection molding cost-effective for large-scale production.
The injection molding process is generally faster than other molding processes, which further increases its efficiency and cost-effectiveness. The speed of the process is contingent on the complexity of the mold, but generally, a time frame from 15 to 120 seconds can capture most injection molding cycle operations.
With injection molding, there’s significantly less waste as any leftover or scrap material can be recycled and re-used in the process. This capability decreases costs and promotes a more sustainable practice.
The accuracy achieved with injection molding also contributes to cost efficiency. The high level of precision reduces the need for finishing techniques or further processing, translating to saved time and resources.
By choosing injection molding, companies can not only save money through production scaling but also benefit from the speed and sustainability of the process. The end result is a more cost-effective solution for high-volume production needs.
Challenges in Injection Molding: High Initial Cost and Size Limitations
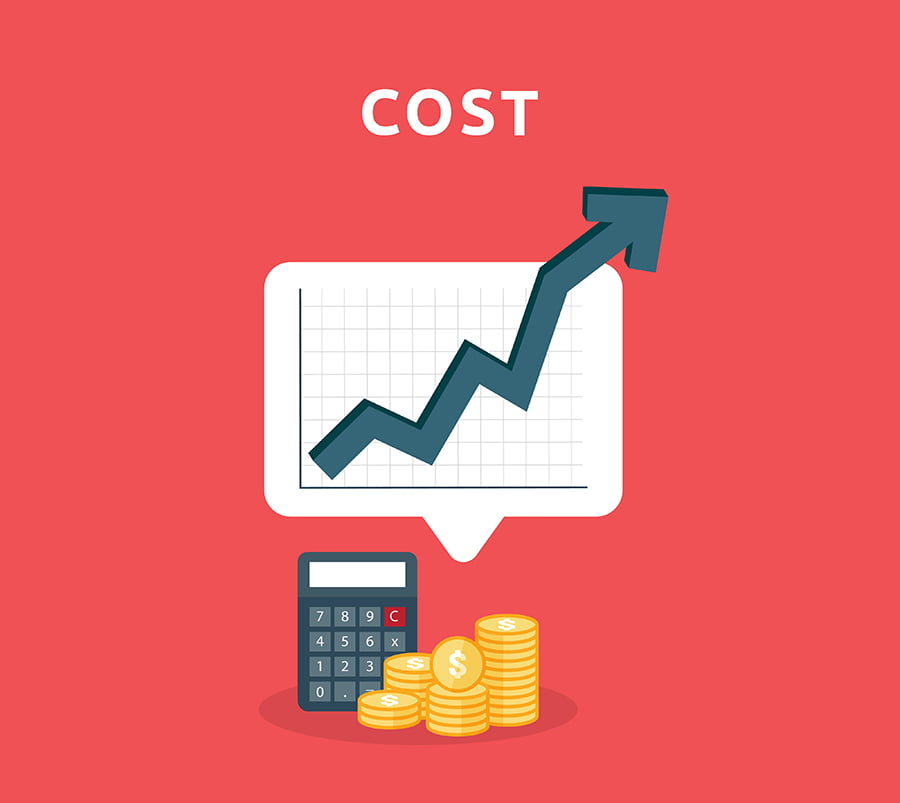
Despite the numerous advantages, there are significant limitations with injection molding to be considered.
First, the initial investment can be a major setback. Setting up the machinery and creating custom molds can be quite expensive. This makes it a less viable option for smaller companies or for producing items in limited quantities. Economies of scale play a key role, since the more units produced, the lower the cost per unit – thus, injection molding is primarily advantageous for mass production.
Secondly, there are constraints on the size of the items that can be produced using this technique. Large items require larger and more expensive machines and molds, which may not be feasible for some manufacturers. The process is suited better to relatively small, consistent, and policy-sized objects, and scaling up may come with complexities that need specific methods to overcome.
These challenges should be factored into the decision when manufacturers are considering whether to use injection molding in their production process.
Applications of Injection Molding in Construction Industry
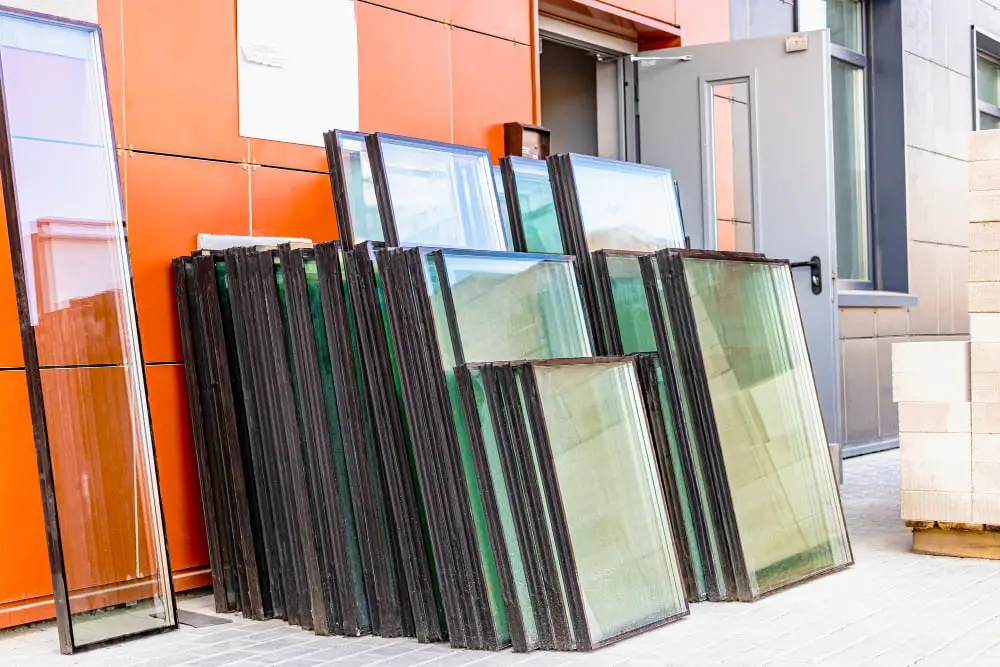
This versatile process finds numerous applications in the construction industry, owing to its capability to create a variety of complex and intricate designs, in both small and large volume productions.
Hermetically sealed windows, one of the core products produced using injection molding, enhance a building’s insulation and energy efficiency.
Molded plastic plumbing components like valves, fittings, and pipes introduce both durability and cost-effectiveness to the construction process.
The production of vinyl siding and gutters, praised for their longevity and maintenance-free properties, relies heavily upon injection molding.
Lighting fixtures, although not strictly structural, contribute to both the functionality and aesthetics of any constructed space, with molded parts providing design flexibility.
Components for HVAC systems such as housings, fan blades, and filters also benefit from the precision and mass production capabilities of injection molding.
Injection molding allows for the creation of soundproofing elements and insulation components, ensuring comfort and sustainability in residential and commercial buildings.
Finally, highly aesthetic yet functional elements, like the construction of custom door handles and cabinet hardware, bring an additional touch of customization that injection molding can uniquely provide.
This vast array of applications shows just how integral injection molding is in the world of building and construction.
Comparison: Injection Molding Vs 3D Printing
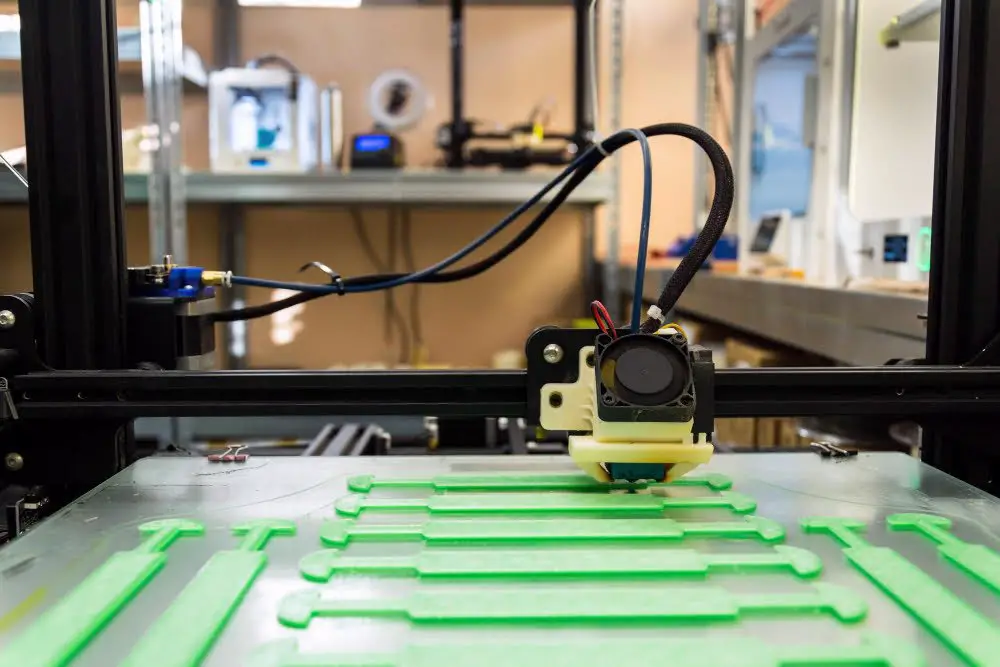
In terms of flexibility and variation, 3D printing appears to stand out. It enables the creation of fully customized parts on a relatively smaller scale. However, for large-scale production, 3D printing can be time-consuming and costly.
On the other hand, injection molding excels in mass production. Once the initial setup costs have been offset, it becomes incredibly time efficient and cost effective. Molded parts require little to no post-production work as they have a finished appearance after being ejected from the mold, saving time and labor expenses.
Different materials can be utilized in both processes. Plastics are common in both, but whereas injection molding is often limited to thermoplastics and elastomers, 3D printing can also work with metals and ceramics.
The choice between injection molding and 3D printing largely depends on the project scale, budget, and desired materials. Generally, injection molding is preferred for making multiple copies of the same item, while 3D printing is beneficial for creating unique, highly customized pieces.
Choosing the Right Materials for Injection Molding
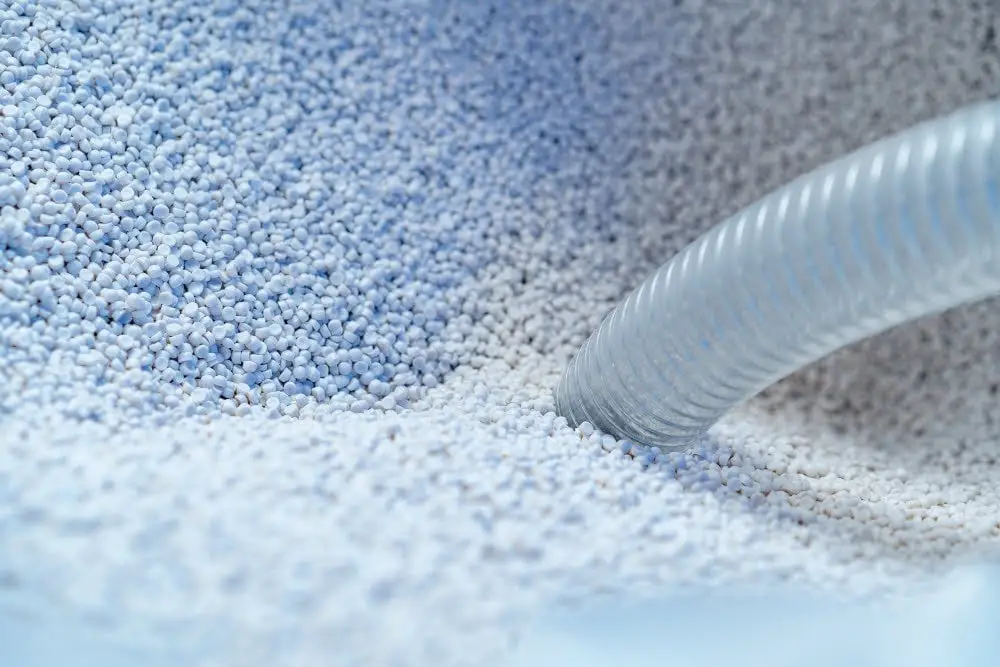
Certainly, understanding the unique properties of the different types of polymers is key when choosing the right ones for injection molding.
Materials like Polystyrene, Polyethylene, and Polypropylene are commonly used because of their excellent flow ability and cost-effectiveness. They’re perfect for everyday household items because they’re durable and resistant to wear and tear.
Next, you have performance polymers like Polybutylene terephthalate (PBT) and Polyethylene terephthalate (PET). These are ideal for more intricate parts because they can withstand high temperatures and have excellent dimensional stability.
Rarer, but equally relevant are specialty plastics. Materials such as Polyether ether ketone (PEEK) or Polysulfone (PSU) are expensive, but come in play when creating parts that need to withstand extremely harsh environments. They have excellent mechanical properties and can resist very high temperatures.
There’s also the option of using filled materials. Here, the polymers are filled with additives like glass or carbon fiber. This significantly improves properties such as toughness, strength and heat resistance of the end product.
The key here is understanding your end product and its application. This would determine properties you’d prioritize, and therefore, the type of polymer to choose for your injection molding process. By carefully assessing these factors, you can ensure the successful execution of your construction project.
FAQ
How does injection moulding work step by step?
Injection moulding follows a process where molten plastic is injected into a mould via a sprue, fills the cavities through runners and gates, cools down, and then the mould is opened and ejector rod of the machine pushes the ejector plate to release the mouldings.
How does plastic molding work?
Plastic molding works by pouring molten plastic into specific molds, allowing it to cool and harden, thus creating customized plastic shapes suitable for various applications.
What is injection moulding work?
Injection moulding is a manufacturing process that involves injecting molten materials into a mould to produce large volumes of identical items.
What materials are commonly used in the injection moulding process?
Common materials used in the injection moulding process include thermoplastic polymers, elastomers, and metals.
How is the quality and durability of an injection moulded product ensured?
The quality and durability of an injection moulded product are ensured through rigorous testing, precise control of the moulding process, and the use of high-quality polymer materials.
What are the main advantages and disadvantages of using injection moulding in construction?
Injection moulding in construction is advantageous due to its cost efficiency, speed of production, and precision in creating complex shapes, but is disadvantaged by its high initial setup costs, limitations with the size of molded objects, and difficulty in changing designs once molds are created.
Recap