Exploring the capabilities of injection molding, we delve into understanding just how thin plastic can be molded using this versatile technique.
In the world of injection molding, the thickness of the plastic part plays a crucial role. While it is technically possible to injection mold plastic as thin as 0.025 mm, it’s generally more practical and cost-effective to stay within the range of 1.5 mm to 3 mm.
This is due to several factors, including the type of plastic used, the complexity of the part’s design, and the capabilities of the injection molding machine.
Delving deeper into the topic, we’ll explore factors like cooling times, warping, and the role of material selection, which all contribute to determining the optimal thickness for your injection molded plastic parts.
Key takeaways:
- Wall thickness of injection molded plastic parts usually ranges from 1.5mm to 3mm.
- Thinner walls can lead to incomplete or weak parts, while thicker walls take longer to cool and can cause deformities or sinking.
- Material selection, mold design, injection pressure, cooling time, and machine capability all impact wall thickness.
- Thermoplastics allow for thinner walls compared to thermoset plastics.
- Design elements, mold shape, dimensional stability, cooling lines, and gate location affect wall thickness.
Understanding Injection Molding Wall Thickness
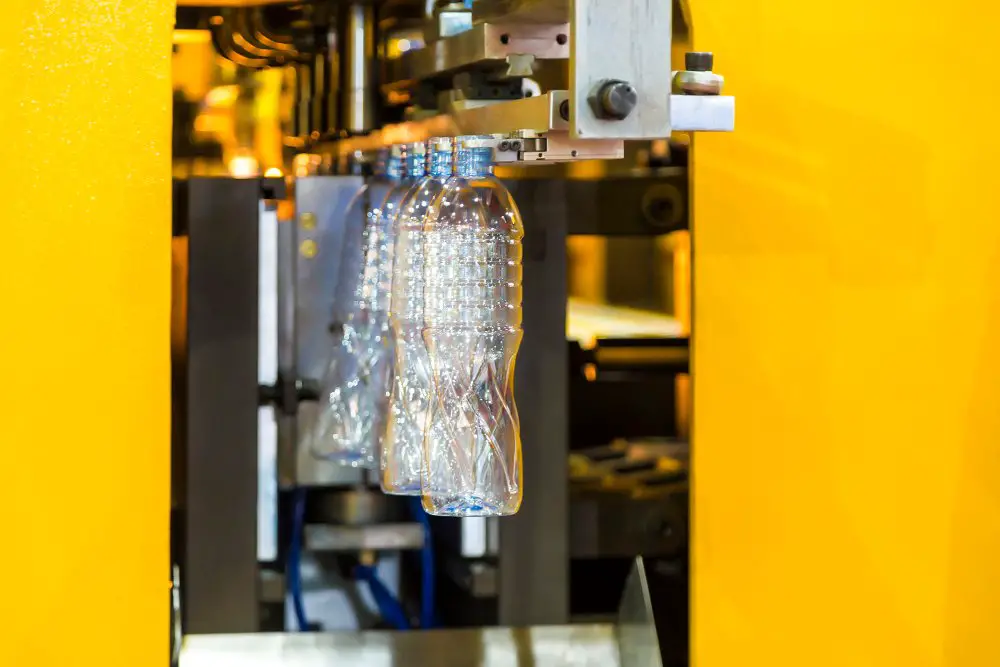
Injection molding, a common method of manufacturing plastic parts, requires careful consideration of wall thickness. In this process, molten plastic is forced into a mold under high pressure. The consistency of the wall thickness of the molded part plays a major role in the part’s durability, functionality, and overall quality.
- Wall thickness refers to the distance between one surface of the part to its opposite. It determines how much material is needed, affects cooling time, and influences the strength and weight of the finished product.
- Consistent wall thickness is crucial to prevent defects. If the walls are too thin, the plastic may not fill in the mold correctly, leading to incomplete or weak parts. If they are too thick, they take longer to cool, which can cause deformities or sinking.
- Ideally, the wall thickness should be uniform. However, it is sometimes necessary to vary it due to design requirements. In such cases, gradual transitions should be incorporated to avoid abrupt changes that can create stress points.
- Wall thickness impacts the cost of injection molding. More material and longer cooling times both lead to higher manufacturing costs.
Understanding these concepts allows effective planning and execution of injection molding projects. Decision-making concerning wall thickness thus becomes an essential aspect of the manufacturing process.
Determining the Minimum and Maximum Wall Thickness
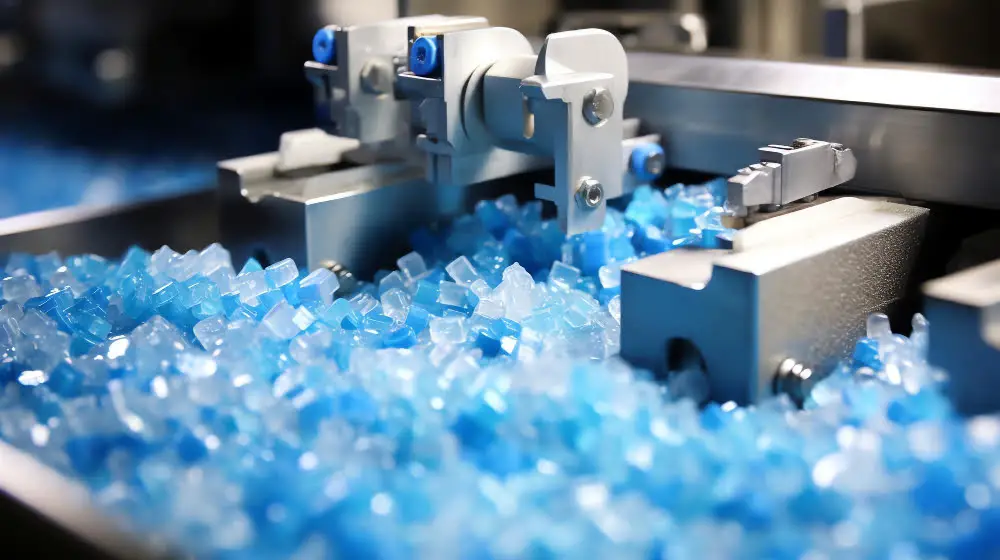
To determine the minimum and maximum wall thickness, one must take into account several key ideas:
The average wall thickness for most materials ranges between 0.03 to 0.04 inches. Thinner walls can be achieved with specific materials and specialized techniques while maintaining integrity and functionality.
To establish maximum thickness, the cooling process is considered. Thicker walls require prolonged cooling times, making the production process inefficient. To avoid this, a nominal wall thickness of 0.150 inches is generally recommended.
The process includes carefully selecting a design that caters to the required minimum and maximum thickness. This involves evaluating the part’s function, the processing conditions, and the particular necessities of the project.
Material selection also plays an integral role. Certain materials accommodate more variance, making it possible to create thicker or thinner walls as required. Polystyrene, for instance, can be molded into thinner sections compared to more rigid polymers.
Mold design, anticipated shrinkage, and flow length of the plastic material through the mold channels are other considerations that directly affect the feasibility of achieving the desired wall thickness.
Finally, ensuring uniform wall thickness is crucial. Inconsistent thickness can cause deformities due to uneven cooling rates, leading to defects such as warping or stress marks. It’s advisable to avoid abrupt transitions from thin to thick sections in the design.
Factors Influencing Wall Thickness in Injection Molding
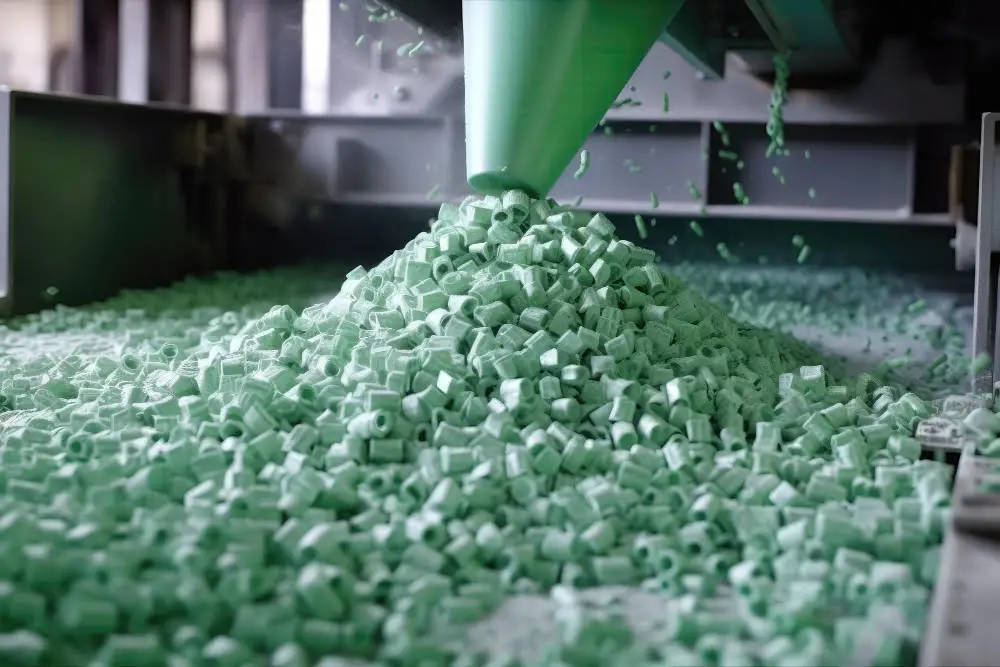
Several elements can impact the wall thickness in injection molding, necessitating careful consideration and monitoring:
1. Material selection: Different plastics have varying flow rates, affecting how thin a wall can be while remaining structurally sound. For example, thermoplastic polymers like polyester and nylon can fill thinner walls better than stiffer polymers such as polyethylene.
2. Mold design: The mold’s layout and gating system can influence the flow of polymer and therefore the obtainable wall thickness. Proper mold design ensures even and efficient material flow.
3. Injection pressure and speed: High injection pressure and speed can facilitate better filling in thin-walled sections. However, these must be appropriately controlled to prevent defects like warping or sink marks.
4. Cooling time: Quick cooling can lead to shrinkage, so balance is necessary to avoid reducing the wall thickness further.
5. Machine capability: Machines with higher clamp forces are better suited for molding thinner walls, as they can tightly hold the mold cavities together, preventing any leakage or flash.
By comprehending the impact of these factors, adjustments can be made to the process or materials to achieve the desired wall thickness in injection molding.
Choosing the Right Material for Desired Wall Thickness
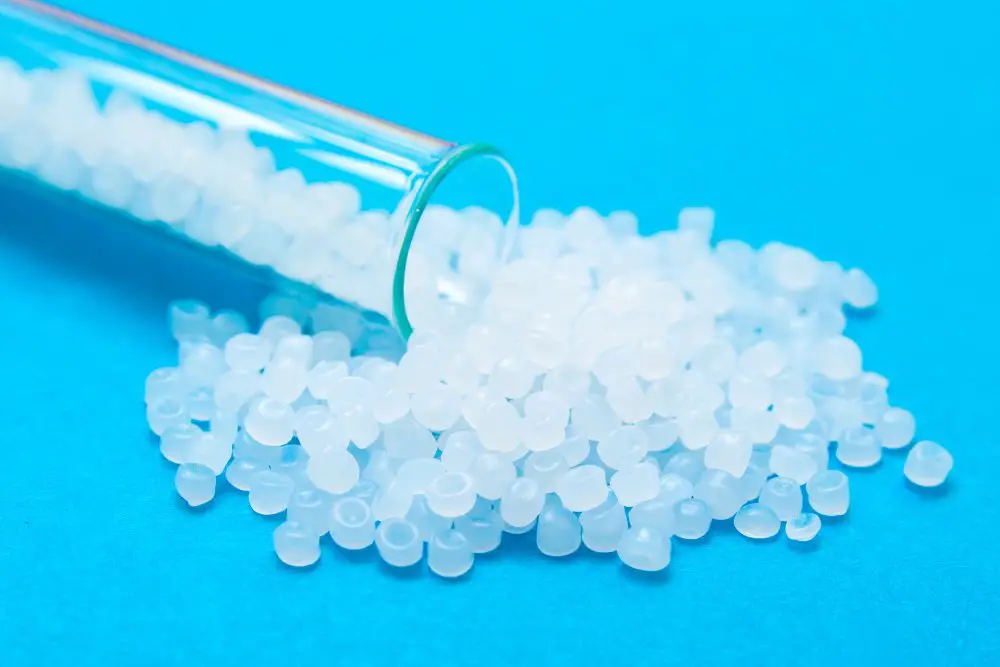
The choice of plastic material greatly influences the possible wall thickness in injection molding. Thermoplastics, for instance, allow for thinner walls compared to thermoset plastics due to their unique physical properties.
Polyethylene and Polypropylene are solid options for molds requiring thinner walls. They yield consistent results and are easy to work with. Conversely, thermoset materials like epoxy and phenolic compounds, due to their brittleness, typically demand thicker walls.
Polycarbonate and ABS (Acrylonitrile Butadiene Styrene) can also accommodate thin walls but require careful temperature and pressure control during the molding process.
For highly intricate or thin-walled designs, specialized materials like liquid crystal polymers may be used. They offer superior flow characteristics, allowing for high detail in molded parts without requiring excessively thick walls.
Finally, note the importance of material strength. Balancing the need for thinner walls with the demands of the part’s function is crucial. While a thin wall can reduce material costs and boost production speed, it shouldn’t compromise the integrity and functionality of the final part.
The Role of Geometry in Determining Wall Thickness
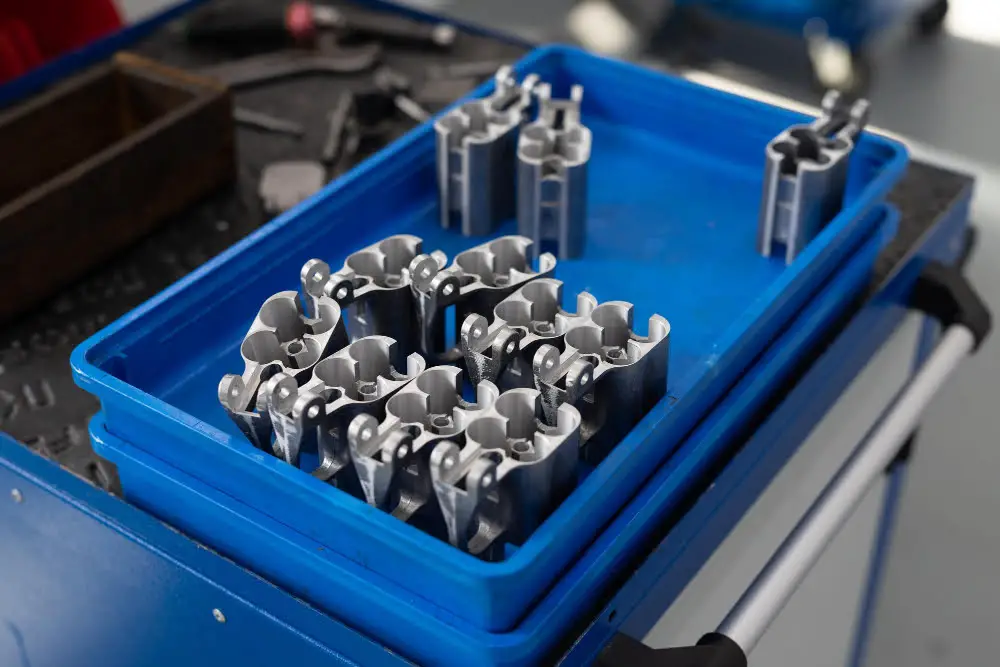
To grasp the influence of geometric factors on injection molded plastic wall thickness, certain key concepts need to be understood:
Design elements with extreme angles or sharp corners may contribute to variations in wall thickness, creating issues like warping or shrinkage.
The shape of the mold plays a significant role. Complex, intricate shapes can lead to inconsistencies in wall thickness due to uneven cooling times.
Dimensional stability is crucial. Adjustments to the mold design can improve consistency in wall thickness by controlling the flow of melted plastic during the injection process.
In-mold cooling is a critical consideration. Where the cooling lines are placed can impact how uniformly the plastic cools and thus affects the wall thickness.
Proper gate location (where the plastic enters the mold) is important. Carefully positioning the gate can ensure even flow of material, thereby maintaining uniform wall thickness across the entire part.
Lastly, the application of core-cavity concepts can be an effective way to control wall thickness, especially for hollow parts or components. Applying these factors correctly can help in achieving consistent and desired wall thickness in injection molded plastic.
Achieving Consistent Walls and Features With Material and Geometry Adjustments
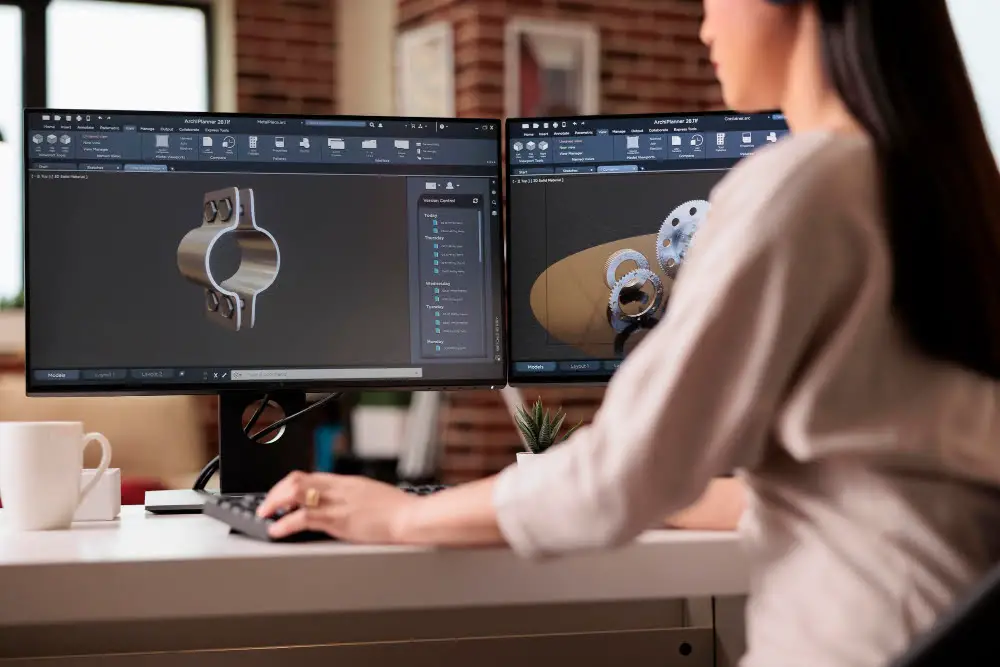
To obtain consistent wall thickness in injection molding, attention should be focused on two crucial aspects – material selection and geometry configuration.
The chosen material plays a definitive role in the evenness of the injection mold’s walls. Polymers exhibit characteristics such as flow rate and shrinkage which can significantly influence the wall thickness. For example, using a polymer with a high flow rate may lead to thinner and more consistent walls, while polymers with high shrinkage tend to form uneven walls post cooling.
Adjusting mold geometry can also assist in attaining consistent walls. Draft angles can be optimized to prevent the plastic material from sticking to the mold. The transition between features should be made as smooth as possible to avoid the formation of uneven sections.
Steps to follow in order to achieve consistent walls and features include:
- Selecting a polymer with characteristics conducive to your intended wall thickness.
- Consulting with a polymer expert or material manufacturer may help in making an informed choice.
- Utilizing software simulation tools to predict possible outcomes of wall consistency based on selected material and mold geometry.
- Incorporating gradual transitions and draft angles into the mold’s geometry design to ensure smooth transitions and easy ejection of the molded part.
- Regularly monitoring and maintaining the molding machine to ensure constant pressure and temperature, crucial factors which can affect the consistency of the wall thickness.
Considerations for Optimal Wall Thickness in Injection Molding
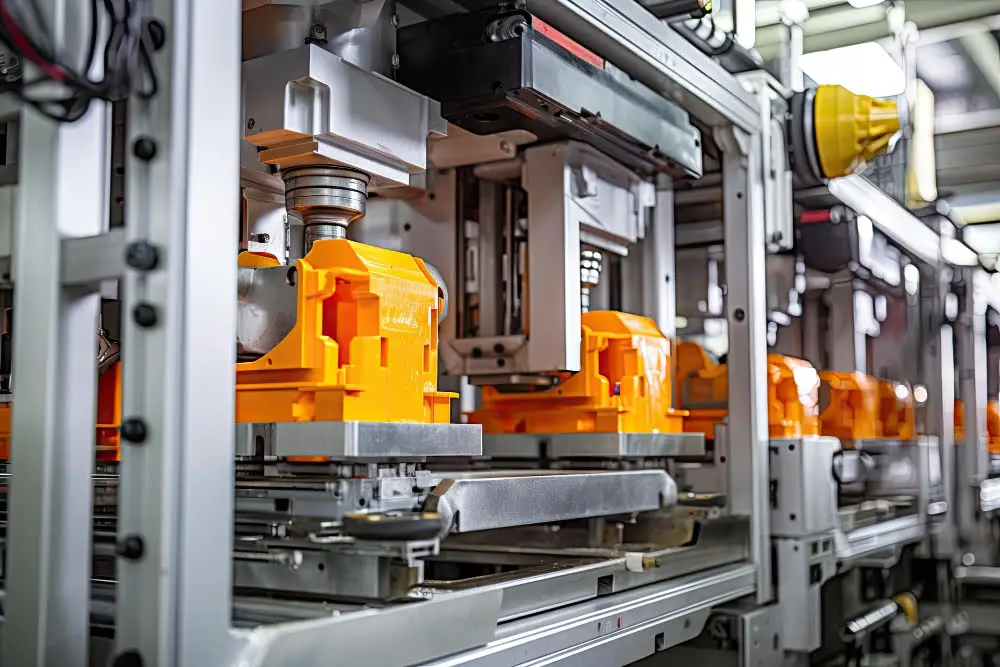
Balancing function with manufacturability is essential in determining an optimal wall thickness. The following key factors should guide this process:
Precision Molding: Make sure the mold design is precise, ensuring minimal shrinkage or warping. This demands steel molds for high volume production or aluminum molds for shorter runs.
Material Properties: Different polymers behave differently. Some, like Nylon, lend themselves to thin walls due to high flow properties. Others, like Polypropylene, may require a thicker wall to prevent brittleness.
Design Complexity: The more intricate the design, the more critical the uniformity of wall thickness. Different thicknesses cool at different rates, potentially leading to warp or sink marks.
Molding Machine Specifications: The capacity of the injection molding machine significantly influences the wall thickness. A machine with higher pressure capacity facilitates the creation of thinner walls.
Guidelines follow industry standards, suggesting a minimum wall thickness of 0.025 inches for ABS and similar materials, or 0.015 inches for flow-friendly materials like Nylon.
To achieve optimal wall thickness, it is critical that design, material, molding process, and machine specifications are harmonized, thereby ensuring high-quality, cost-effective production.
FAQ
What is the minimum thickness of plastic components?
The minimum thickness of plastic components for efficient, high volume production ranges from 0.025 to 0.050 inches (0.635 – 1.27mm) depending on the size of the part.
What is the thickness limit for injection molding?
The thickness limit for injection molding generally ranges between 1 to 5 mm.
What is the minimum precision that can be expected of an injection molded component?
The minimum precision that can be expected of an injection molded component is typically ± 0.500 mm (0.020”), though under certain conditions, tolerances down to ± 0.125 mm (0.005”) may be achievable.
Why is uniform thickness important in injection molding?
Uniform thickness in injection molding is crucial to prevent warping, cracking, twisting, and overall failure during the cooling process, while also minimizing shrinkage and residual stress in the final product.
How does the type of polymer influence the thickness of injection-molded plastic components?
The type of polymer impacts the thickness of injection-molded plastic components as different polymers exhibit varying flow characteristics during molding, with polymers having high melt-flow rates resulting in thinner components, while those with low melt-flow rates produce thicker components.
What techniques can be applied to achieve ultra-precise thickness in plastic molding?
Achieving ultra-precise thickness in plastic molding can be realized through techniques such as injection molding, extrusion processes, and rotational molding, all with careful control of parameters like temperature, pressure, and mold-time.
How does maintaining consistent component thickness improve the performance of injection-molded products?
Maintaining consistent component thickness in injection-molded products improves performance by promoting uniform cooling, reducing warping, and ensuring structural stability.
Recap