Delving into the world of construction polymers, this article unravels the cost factors that influence the average price of a plastic extrusion line.
The cost of an average plastic extrusion line is influenced by several factors, including the type of polymer used, the complexity of the extrusion process, and the size of the production line.
Generally, a standard plastic extrusion line costs between $30,000 to $200,000.
However, for custom-made, larger or more complex lines, the cost can exceed this range.
This article will delve deeper into the factors influencing the cost, different types of plastic extrusion lines, and tips to optimize your investment.
Stay tuned to understand the detailed breakdown of these costs and how to make the best decision for your construction project.
Key takeaways:
- Plastic extrusion lines typically cost between ,000 to 0,000.
- Custom-made or more complex lines can exceed this range.
- Payment options include outright purchase, equipment loans, leasing, and renting.
- Operating expenses include initial setup costs, utility expenses, labor costs, maintenance costs, and waste management costs.
- Raw material costs, including fluctuations in prices and the type of plastic used, also impact the overall cost.
Average Plastic Extruder Machine Price
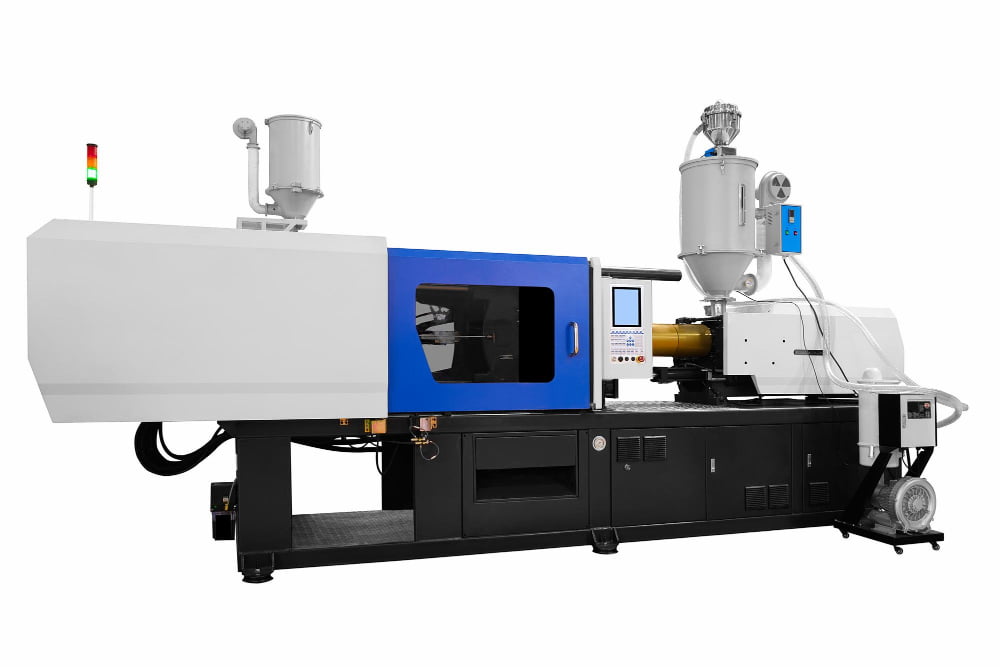
A variety of factors influence the overall cost of a plastic extruder machine. To begin with, the machine’s model and specifications play a significant part; highly advanced models with superior output capacity tend to have a higher price tag. For example, a basic single screw extruder can range from $10,000 to $50,000, whereas twin screw extruders can cost up to $400,000.
Aside from the machine’s specifications, the brand also affects the cost. Established brands known for their quality and service might offer their machines at a premium.
Lastly, customization features such as output capacity and size, type of materials to be processed, and additional add-ons like dryers or mixers can substantially affect the final cost of the extrusion line.
Remember, a comprehensive evaluation of your manufacturing needs, budget, and long-term goals is crucial before investing in an extruder machine. From there, you can undertake research and consultations to make an informed purchase.
Payment Options for Purchasing Plastic Extrusion Equipment
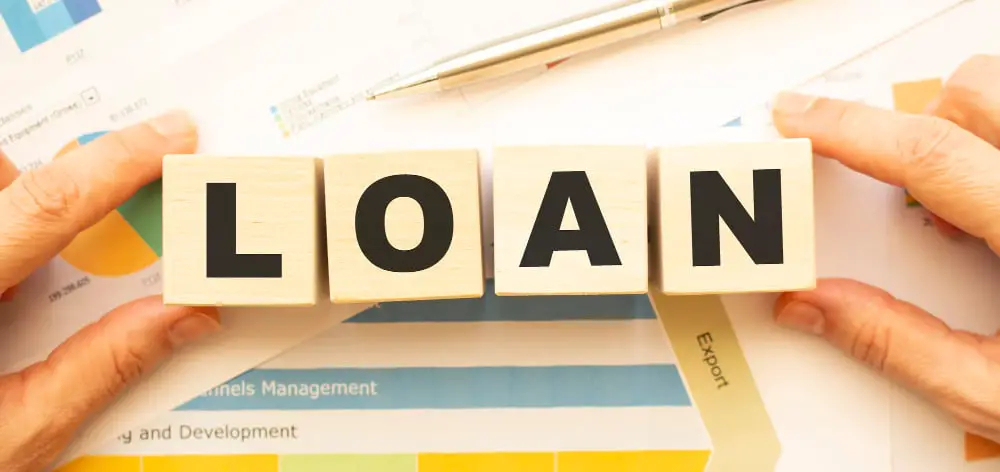
Many businesses offer a variety of flexible options to make the purchase of plastic extrusion equipment more accessible and manageable.
Traditional outright purchases involves paying for the machine upfront, this might be the most cost-effective in the long run as no interest is added. However, it also means a large initial capital outlay.
Equipment loans could be considered as an alternative. Financial institutions or manufacturers may offer these. Payment is spread over an agreed period, lessening the immediate financial burden. It should be noted, the final cost will be higher due to the interest.
Leasing is another available option. Similar to renting, a monthly fee is charged for a predetermined period. It involves less upfront capital and may include maintenance. It, however, does not lead to ownership.
Finally, there’s renting. This is typically used for short-term needs – perhaps for a specific project or to meet increased demand. This option has the advantage of no commitment to the specific machine and provides the opportunity to try before you buy.
Negotiation can be conducted regardless of the chosen payment option. It’s recommended to discuss with suppliers or leasing companies to find the best possible terms. Businesses may also look into different financing opportunities or programs to help offset the cost.
Remember to consider potential tax benefits when determining the best payment option. Consulting with tax professionals to explore depreciation benefits and tax deductions is advisable.
To protect the investment, insurance is crucial. Various policies are available, from equipment insurance, liability insurance, to business interruption insurance.
Lastly, make sure to get a warranty. This can save substantial future expenses in case of malfunctions, damages or breakdowns. Manufacturers or suppliers often provide warranty information, so be sure to review the details.
Operating Expenses in Plastic Extrusion Line Cost
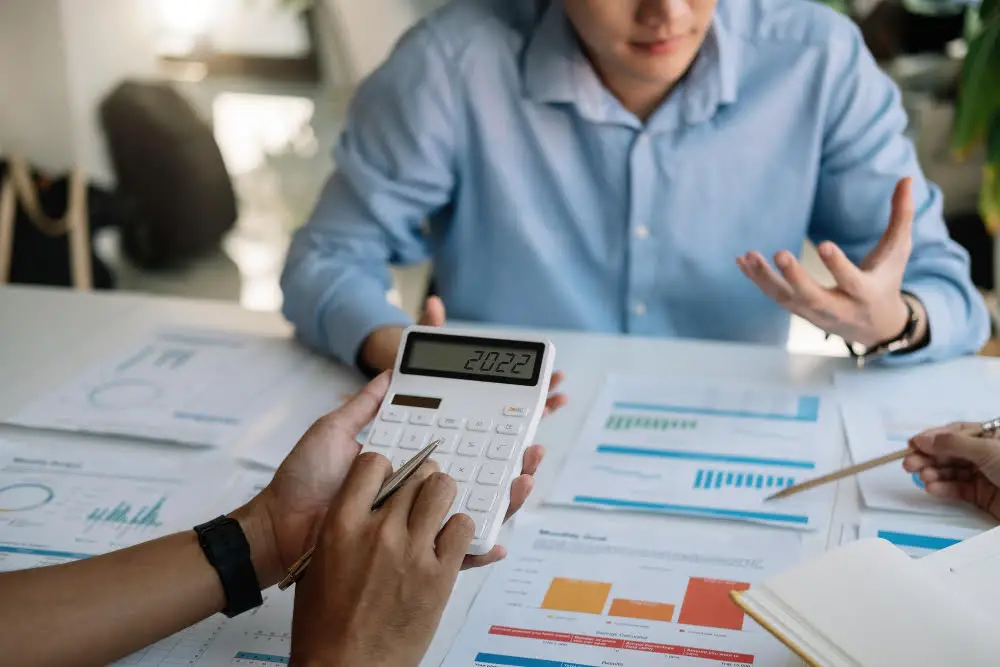
Fundamentally, the cost of operating a plastic extrusion line is covered by various specific expenses. These include the initial investment required for setting up the line which often includes purchasing the extruder machine, extrusion tools and calibration equipment.
Other critical components include the costs related to utilities such as electricity and gas. Plastic extrusion is often a power-intensive process, and the expense of such utilities can significantly impact operation costs.
Labor is another integral part of operating expenses. The amount of labor required and associated costs depends on several factors including the size of the extrusion line, the complexity of the operations, and the localized cost of labor.
Maintenance of the equipment falls into this category as well. Regular inspection and servicing of machinery along with any unexpected repairs can also add up quickly.
Finally, waste management costs should be planned for. This includes material wastage that occurs during the manufacturing process, as well as the cost of disposing of waste in a manner that’s compliant with environmental regulations.
These are the primary components of operating expenses in a plastic extrusion line. While each expense can be managed and optimized to a certain extent, it’s critical to understand each one to effectively control overall operational costs.
Raw Materials Cost in Plastic Extrusion Process
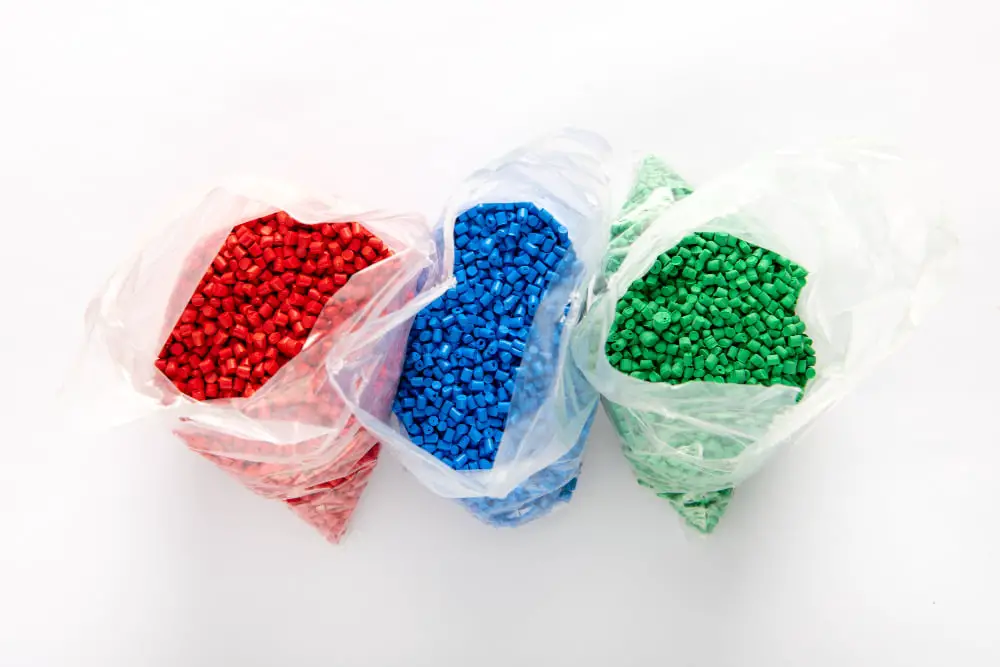
A key factor affecting the plastic extrusion process is the cost of the raw materials. Two major variables in this context are the price variations in manufacturing materials and the type of plastic used.
Regular fluctuations in polymer prices mean that material costs can differ significantly. Buyers are advised to keep a close eye on these changes and adjust purchasing strategies accordingly.
The type of plastic also has its own impact on the expenses. Lower prices can be anticipated when common polymers like Polyethylene (PE) or Polyvinyl Chloride (PVC) are used. However, if your process requires specialty or high performing resins like Polystyrene (PS) or Acrylonitrile Butadiene Styrene (ABS), you should expect considerably higher costs.
Ordering in bulk can generally lower the unit price of raw materials. It would be wise to negotiate quantity discounts if large volumes are being purchased regularly.
Another factor to consider is waste reduction. By improving efficiency in the production process through better design and attention to detail, you can save money on unnecessary material usage.
One should always quality check material deliveries. This will ensure that you’re actually receiving what was ordered and that it meets necessary quality standards. Bad quality or wrong type of plastic can inflict unnecessary additional costs.
Also, consider the delivery reliability of your supplier. Disruptions in supply can lead to costly production downtimes.
Take into account the packaging of the material. Loose pellet packaging can have an impact on handling and potential spillage waste, while containers may tick up your cost but cut waste and spillage.
Lastly, investing in quality raw materials can significantly influence the lifespan of your machinery, potentially reducing long-term maintenance and equipment replacement costs.
Labor Costs in Plastic Extrusion Line
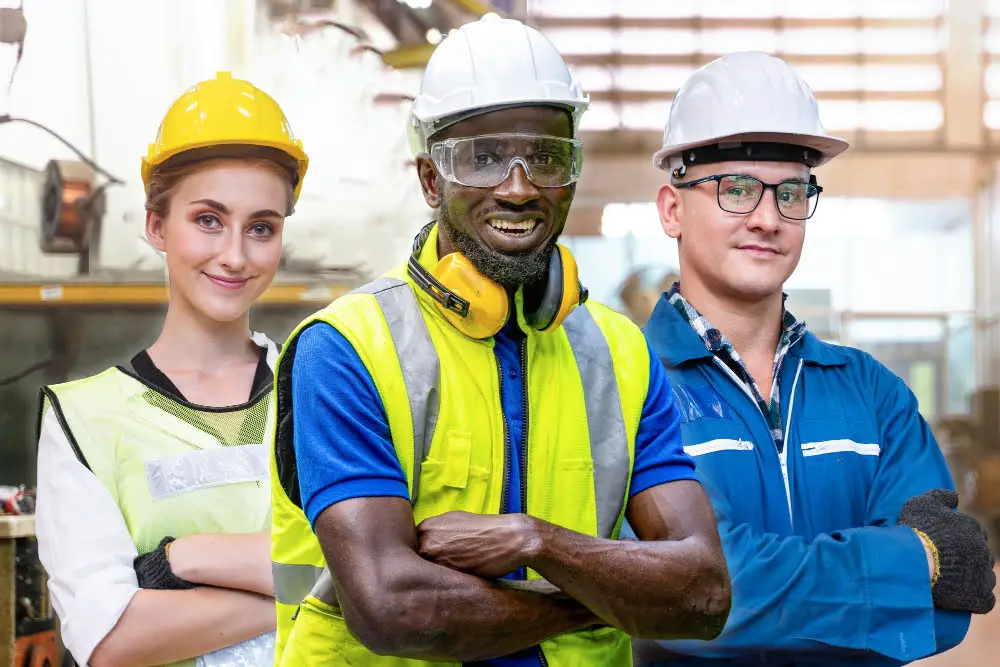
The workforce powering a plastic extrusion line is a significant factor in its cost calculation. But why does this matter?
Firstly, it’s crucial to consider the skill level required for various operations. Highly specialized tasks require trained personnel, whose wages are typically higher than less-skilled workers.
Then, an adequate number of staff members is vital to maintain efficiency. Too few employees could slow down production, while too many could inflate costs unnecessarily.
Employer’s liabilities including health insurances, worker’s compensation, and benefits also add up to the overall expense.
Lastly, don’t forget the overtime charges. Depending on the production schedules and workload, these can also impact the total labor costs.
These points are key not only to understanding the ‘fundamentals’ but also the ‘details’ of labor costs in the context of the plastic extrusion process. Remember, a well-managed labor force can significantly reduce these costs and boost overall profitability.
Energy Bill Expenses in Plastic Extrusion Lines
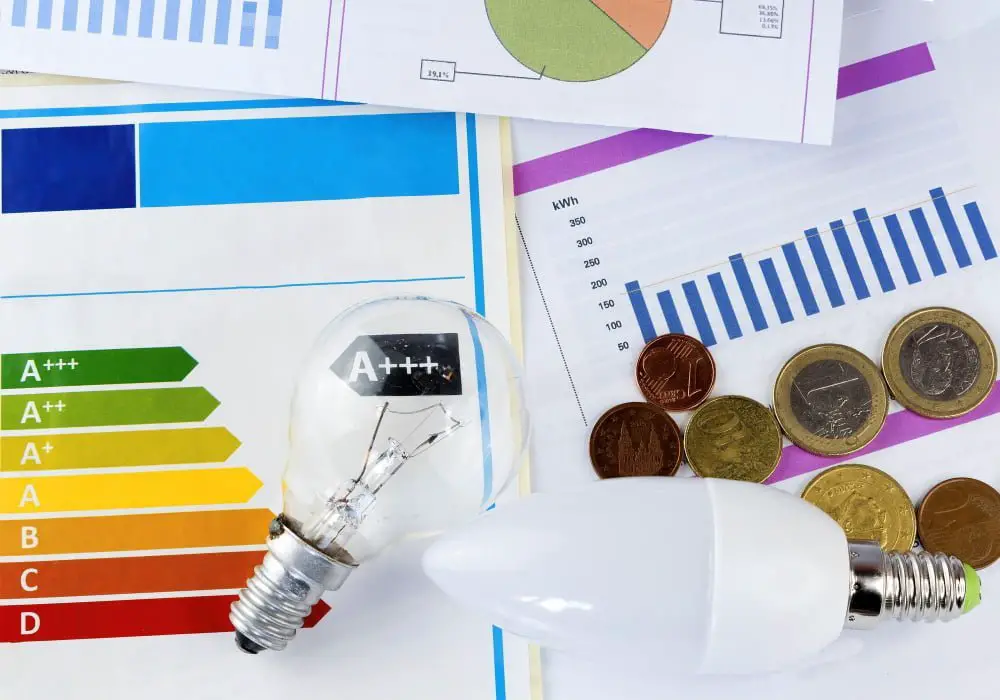
Extruding plastic is an energy-intensive process so a significant portion of manufacturing costs can be attributed to the energy bill. The following factors make energy bills a crucial determinant of overall costs:
- Energy Intensive Nature of Extrusion: Extrusion involves the melting and molding of plastic, both of which require substantial energy input, contributing to elevated electricity bills.
- Type of Extruder: Single screw extruders typically consume less energy than twin-screw extruders, impacting energy costs.
- Machinery Age: Older machinery tends to be less energy-efficient, thus increasing electricity consumption.
- Maintaining Optimal Operating Temperatures: Controlling the temperature within the desired range throughout the extrusion process requires ongoing energy input.
- Lighting and HVAC: Lighting and Heating, Ventilation, and Air Conditioning system costs also contribute to the overall energy bill.
- Standby Energy Consumption: Machines left inactive but still drawing power (‘phantom load’) can also influence energy costs.
Efficiency measures to consider:
- Equipment Upgrades: Investing in energy-efficient equipment can lower the overall energy bill.
- Maintenance: Regular service and maintenance improve machine efficiency and thereby lower energy costs.
- Standby Energy Conservation: Close monitoring of standby power by implementing stricter shutdown procedures can help reduce energy costs.
- Process Optimization: Fine-tuning the manufacturing process can result in energy savings.
- Energy Audit: Regular energy audits can identify areas of energy wastage and provide solutions to enhance energy efficiency.
Rent or Lease Expenses for Plastic Extrusion Equipment
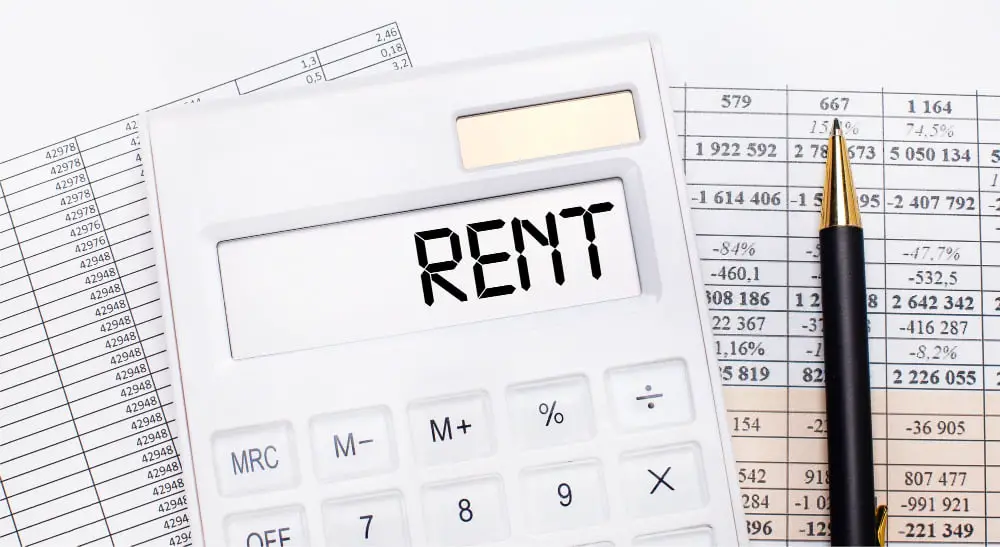
Deciding between renting or leasing plastic extrusion equipment heavily depends on a variety of factors. Here are the key considerations:
- Duration of the project: Short term projects may warrant renting, while long-term commitments could benefit more from a lease agreement.
- Financial capabilities: Lease agreements often require less capital upfront and can be more financially feasible for smaller construction firms.
- Equipment availability: The desired model and specifications may not always be available for rent. Leasing, on the other hand, typically offers a wider selection of equipment.
- Maintenance: In most rental agreements, the responsibility of regular maintenance falls on the renter. In leasing contracts, the lessor usually handles this.
- Update technology: Leasing contracts enable companies to update to newer technology more seamlessly with the end of lease term upgrades, thus keeping up with technology trends and staying competitive.
Remember, making an informed decision between renting or leasing requires comprehensive analysis of these considerations alongside your business’s needs and goals.
Maintenance Expenses for Plastic Extrusion Line
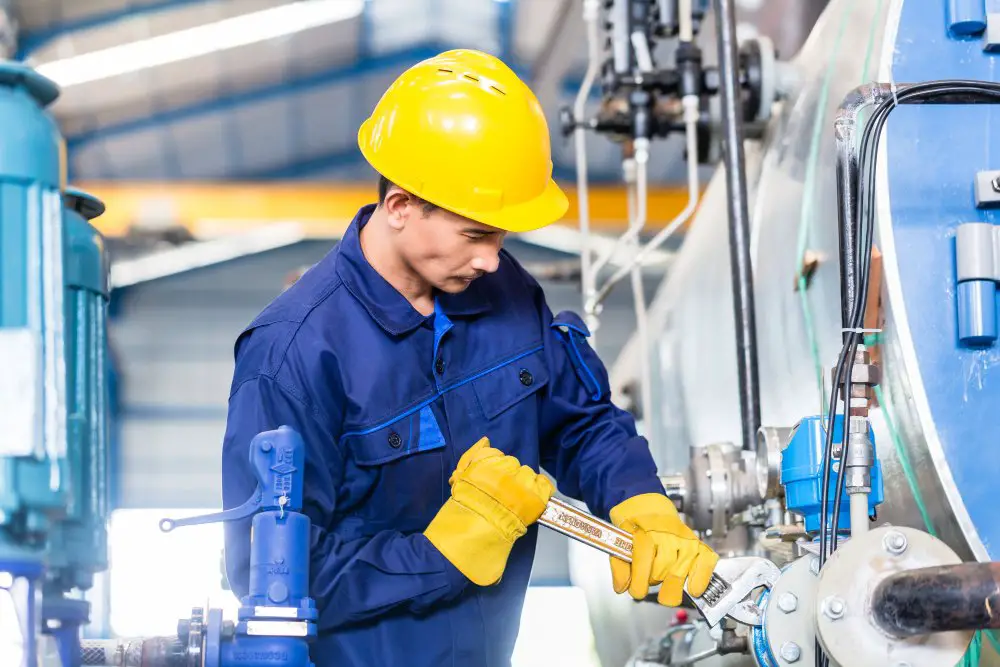
Maintenance primarily covers the upkeep expenses associated with keeping an extrusion line functional and efficient. It’s generally classified into three categories: preventive, corrective, and predictive maintenance.
Preventive maintenance involves regular checks and service to avoid sudden machine failure. This might include cleaning, lubrication, minor adjustments, and parts replacements done at predetermined intervals.
Corrective maintenance, on the other hand, addresses issues that arise unexpectedly during operations. Prompt attention prevents minor problems from escalating into major ones that could disrupt the manufacturing process and lead to cost inflation.
Yet more modern is predictive maintenance, a proactive approach that uses data-driven strategies to anticipate potential failures. Ideally, this approach uses sensors to monitor machine performance and artificial intelligence to analyze the data, thereby identifying abnormalities and predicting when equipment might fail.
Every company needs to adopt a blend of these maintenance strategies to keep their extrusion line performing optimally. Key to this is investing in well-trained personnel, as well as advanced monitoring and diagnostic tools. Regularly budgeting for these expenses can help avoid unexpected costs and downtime, thereby improving the overall efficiency and profitability of the plastic extrusion line.
Transport Fees: Transportation of Plastic Extrusion Equipment
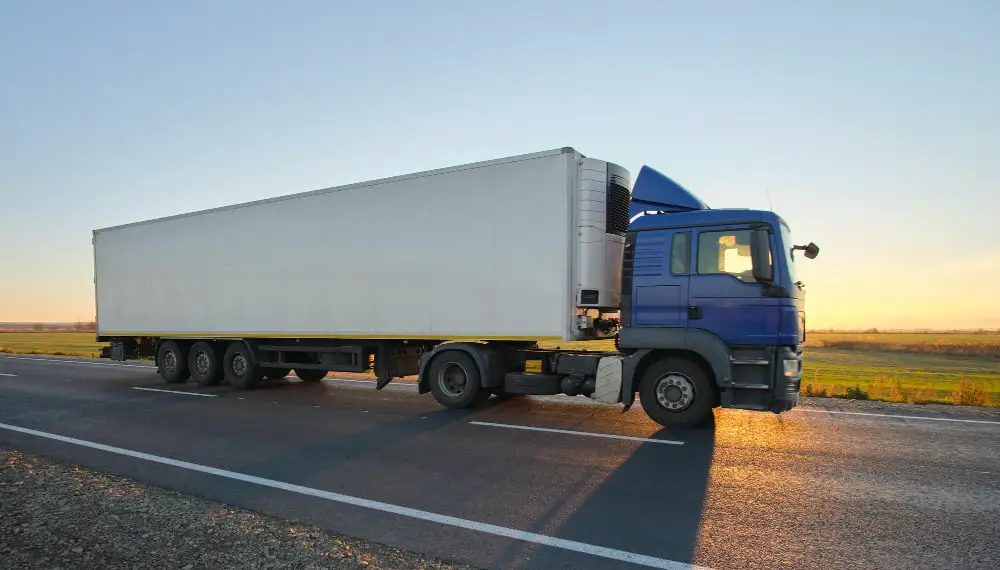
The complexity of the machinery, paired with the distance between the manufacturing site and the location of the construction project, can significantly influence transportation costs.
1. Size and Weight of the Equipment: Extrusion equipment is typically large, heavy-duty machines, which means specialist transport may be needed to ensure safe delivery.
2. Distance and Mode of Transport: The further away the manufacturing site, the higher the transport cost. Also, mode of transportation – air, sea, or road, each with their own rates – determines the cost.
3. Special Handling Requirements: Owing to their delicateness, these machines often need expert handlers during transport. This may increase the costs.
4. Import Charges: If the equipment is being brought from a foreign country, import duties and charges can add considerably to the carriage bill.
To avoid unexpected expenses, secure a quote inclusive of all delivery charges. If importing, consider hiring an experienced importing agent to handle the process and understand all the costs involved.
Insurance Premiums for Plastic Extrusion Machines
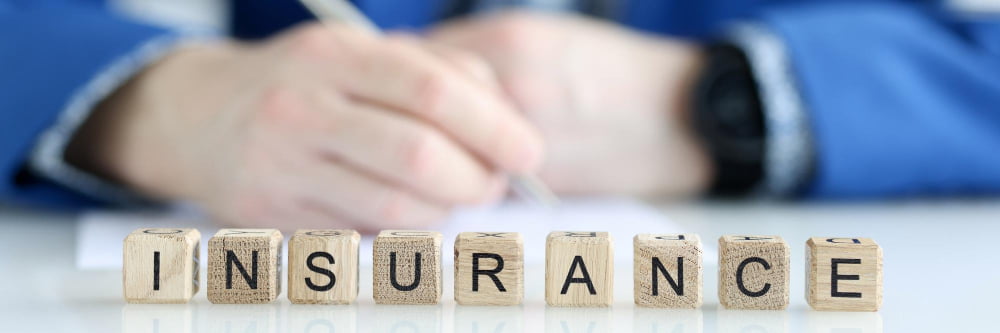
Insurance premiums form part of the overall costs incurred when operating plastic extrusion machines. These premiums cover any undesirable incidents like machine breakdowns, worker accidents, or loss due to unforeseen events.
Firstly, it is crucial to identify a reliable insurance company that provides comprehensive coverage for your equipment. This covers not only the machine but also the operator and the manufacturing facility.
Second, evaluate various insurance policies available for such machinery. Consider factors such as coverage limit, deductible, and premium amounts. You might want to consult with an insurance broker to get the best deal.
Third, understand the policy inclusions and exclusions. This specifically details what circumstances the insurance will compensate for, and what it won’t. This knowledge significantly reduces the risk of unexpected insurance claim rejections.
Lastly, regularly review and update the policy reflecting the machine’s depreciating value. This ensures you are not overpaying on premiums, keeping your operational costs in check.
Remember to consider insurers who provide coverage customized specifically for plastic extrusion machines, as they are familiar with the machine operations and potential risks associated with them.
Depreciation Charges in PVC Extrusion Plant Operating Costs
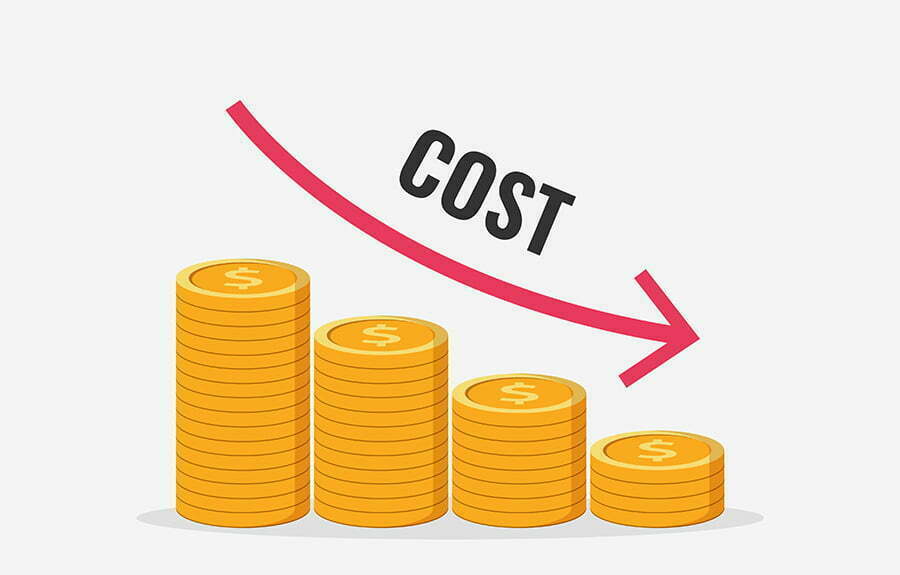
Depreciation stands as a significant portion in the life cycle cost of a PVC extrusion plant.
First, recognize that depreciation refers to the gradual decrease in value of an asset over time or the expense recorded to reduce the value of an asset. In this case, the asset is the extrusion equipment.
The value of an extrusion plant decreases over time due to wear and tear, and obsolescence.
Understanding depreciation methods is essential when calculating these costs. Primarily, there are two methods used: straight-line and declining balance.
Straight-line depreciation involves spreading the cost of your machinery equally over its estimated useful lifespan.
The declining balance method accelerates the amount of depreciation taken in the early years of the asset life.
Choosing the appropriate strategy depends on how frequently or heavily the extrusion machine is used.
Make sure to consider some factors influencing the depreciation costs such as initial purchase price of the equipment, estimated life expectancy of the machine, and the estimated salvage value (the estimated value of the asset at the end of its useful life).
The depreciation cost can either be factored into the cost of production or set aside as a separate expense for bookkeeping and tax purposes. For this, it’s advisable to consult with a tax professional or verified accountant experienced in machinery and equipment dealing.
Remember that calculating depreciation accurately is key to understand the full cost and profitability of your PVC extrusion plant.
Taxes and Duties On Plastic Extrusion Equipment
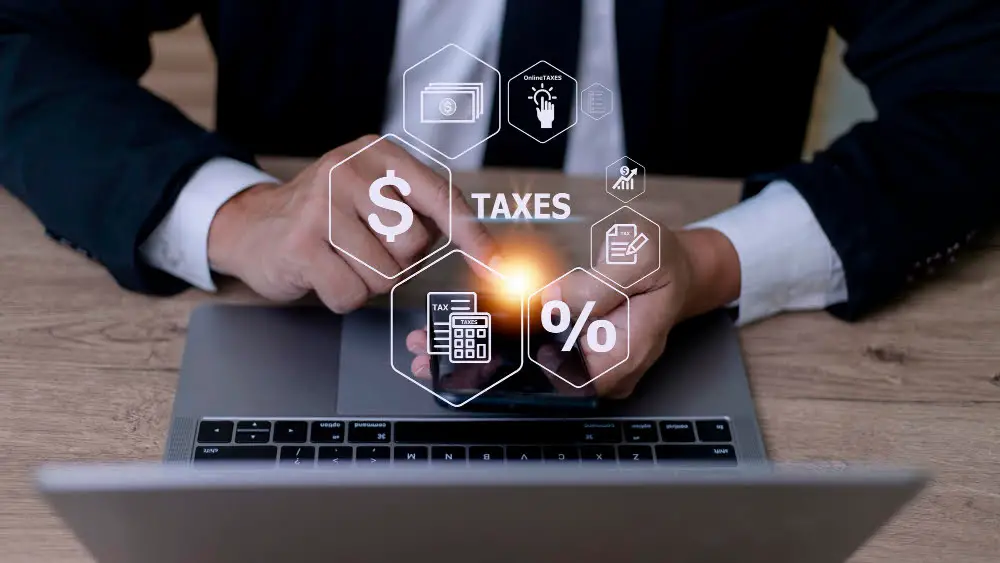
Taxes and duties can notably impact the total cost of plastic extrusion equipment. These governmental charges come typically in two forms: Value Added Tax and customs duties.
Value Added Tax, or VAT as it is commonly known, is applied to the cost of goods and services. As a general rule, VAT applies to all stages of the supply chain, including the sale of machinery used in the plastic extrusion process. The exact rate of VAT varies wildly from country to country, which therefore directly influences the overall price of the equipment.
Customs duties, on the other hand, come into play when plastic extrusion equipment is imported. These duties are a form of tax imposed on importation of goods and vary according to factors such as the country of origin, type of machinery and its intended use. Import tariffs can significantly increase the initial price of the equipment.
Navigating these different taxes and duties may seem daunting. Steps to handle this include:
- Consulting with tax professionals to understand the implications
- Contacting the relevant governmental agencies for accurate information
- Implementing the use of accounting software to keep track of the expenditures
- Building the probable tax and duties into the budget from the outset to avoid surprises
It’s essential to be aware of these potential costs and plan ahead, as they can increase the initial investment in plastic extrusion equipment substantially.
How to Buy Plastic Extrusion Equipment
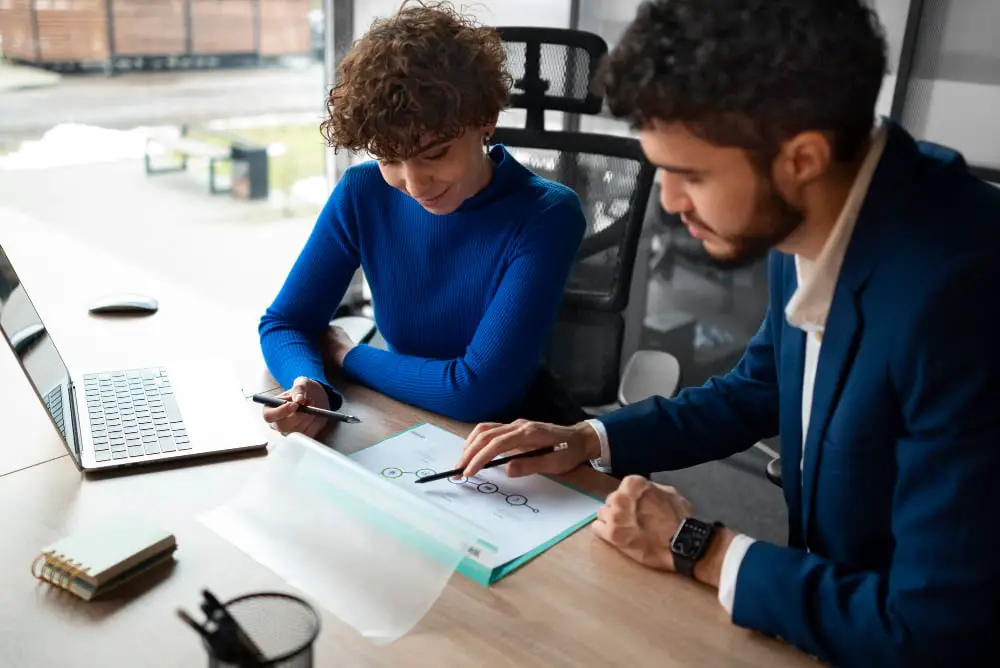
When purchasing plastic extrusion equipment, several elements contribute to making an informed decision.
First, identify your specific requirements. Assess the type, size, and quality of products your production line will be handling. Various machines cater to different needs, from complex items like medical tubes to simpler ones like plastic packaging materials.
Analyzing vendor credibility is a crucial step. Checking their track record, customer reviews, and after-sale services will help confirm their reliability.
Remember to evaluate the machine’s quality. Ensure that the equipment is durable, reliable, and efficient, but also suits your budget constraints.
Consider the machine’s energy efficiency. An energy-efficient model may cost more upfront, but could lead to substantial savings in the long run.
Lastly, take note of the availability of replacement parts. Ease of maintenance and accessible spare parts will prove beneficial in the long run to keep the equipment operational and reduce downtime.
In summary, buying plastic extrusion equipment involves not just inspecting the features of the machine itself, but also assessing vendor credibility, long-term operating costs, and maintenance considerations.
FAQ
How much does plastic extrusion cost?
The cost of plastic extrusion generally depends on the intricate design factors and raw material choice, although it typically falls below $1,000.
Is plastic extrusion expensive?
No, plastic extrusion is not expensive upfront, but can become slightly more costly over time due to medium costs per part.
What is the cost of an extruder?
The cost of an extruder can range from $50,000 for a small single screw lab extruder to well over a million for a large high-speed twin screw extruder, depending on size and capabilities.
What are the key factors influencing the price of a plastic extrusion line?
The key factors influencing the price of a plastic extrusion line include the quality of the components, the complexity of the machine design, the brand reputation, and the after-sales service offered.
What additional costs are associated with operating a plastic extrusion line?
Additional costs associated with operating a plastic extrusion line include expenses related to energy consumption, raw material procurement, maintenance, labor, and compliance with regulatory standards.
Can cost-effectiveness be improved in plastic extrusion technique?
Yes, cost-effectiveness in the plastic extrusion technique can be improved by optimizing the production process, reducing waste, and reusing the left-over materials.
Recap