Discover the latest advancements and challenges in polymer insulation manufacturing for the building industry with our expert insights.
Polymer insulation is becoming increasingly popular in the building industry. This type of insulation is made from synthetic materials that are lightweight, durable, and easy to install. But with any new technology comes challenges.
We’ll explore the advancements and challenges of polymer insulation manufacturing in the building industry. From its benefits to its limitations, we’ll cover everything you need to know about this innovative product.
Key takeaways:
- Polymer insulation is a lightweight, durable, and easy-to-install option for the building industry.
- Advancements in manufacturing techniques allow for precise control and consistent-quality products.
- Advancements in materials include closed-cell foam technology and environmentally-friendly blowing agents.
- Polymer insulation offers energy efficiency benefits, reducing reliance on heating and cooling systems.
- Fire safety concerns have been addressed with additives and improved manufacturing practices.
Polymer Insulation Types
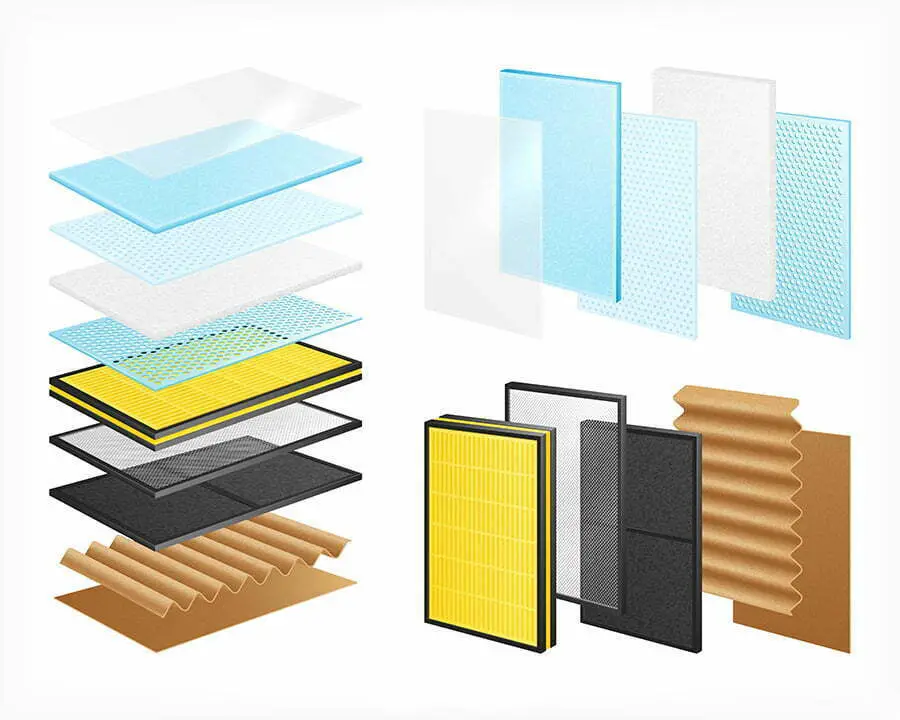
Polymer insulation is a type of insulation that is made from synthetic materials such as polyurethane, polystyrene, and polyisocyanurate. These materials are lightweight and easy to install, making them an attractive option for builders looking to save time and money.
There are several types of polymer insulation available in the market today. One popular type is spray foam insulation which can be applied directly onto walls or ceilings using specialized equipment.
Another common type is rigid board insulation which comes in large sheets that can be cut to fit any space.
Next, we will explore some benefits as well as limitations associated with polymer insulation manufacturing in detail so you have a better understanding on how it works!
Manufacturing Techniques
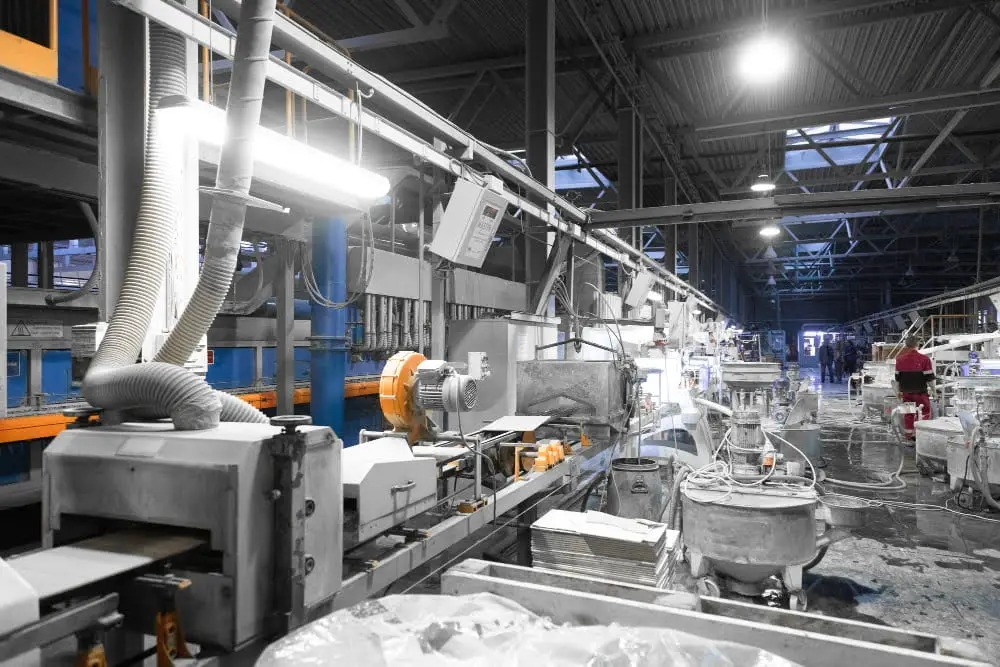
Manufacturing techniques have come a long way since the days of my father’s fiberglass insulation installation. Polymer insulation, for example, is manufactured using advanced techniques that allow for precise control over its properties and performance.
One such technique is extrusion, which involves melting polymer pellets and forcing them through a die to create a continuous shape. This process allows manufacturers to produce consistent-quality polymer insulation in various shapes and sizes.
Another manufacturing technique used in polymer insulation production is injection molding. In this process, molten plastic material is injected into a mold cavity under high pressure where it cools down and solidifies into the desired shape.
These manufacturing techniques make the production of polymer insulation more efficient and ensure that each product meets strict quality standards.
As technology continues to advance, we can expect even more innovative manufacturing methods that will further improve the performance of building materials like polymer insulation.
Advancements in Materials
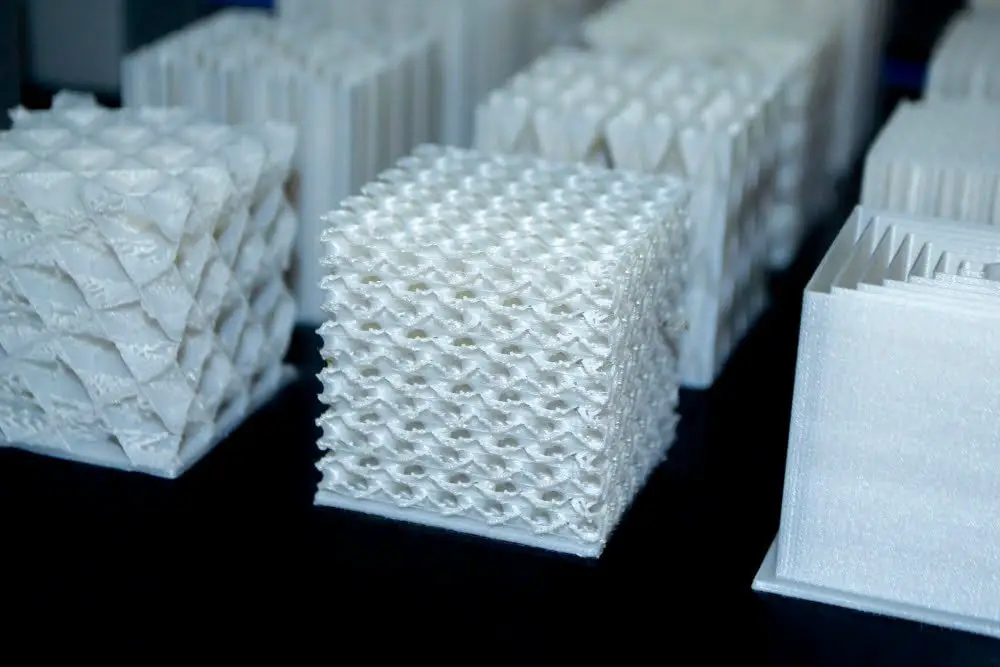
Polymer insulation is a type of insulation that is made from synthetic materials such as polyurethane, polystyrene, and polyisocyanurate. These materials are lightweight and have excellent insulating properties.
They are also durable and moisture resistant, making them ideal for use in buildings.
One of the major advancements in polymer insulation manufacturing has been the development of closed-cell foam technology. Closed-cell foam has a higher R-value (a measure of thermal resistance) than open-cell foam because it contains more air pockets per cubic inch.
This means that closed-cell foam provides better insulation than open-cell foam.
Another advancement in polymer insulation manufacturing is the use of blowing agents that do not deplete the ozone layer or contribute to global warming. In the past, blowing agents such as chlorofluorocarbons (CFCs) were used to create foams with good insulating properties but had negative environmental impacts.
Today’s manufacturers have developed new blowing agents like hydrofluoroolefins (HFOs), which do not harm our planet’s protective ozone layer or contribute significantly to climate change while still providing high-quality performance levels for their products.
These advancements make polymer-based insulations an attractive option for builders looking for sustainable solutions without sacrificing quality or efficiency when installing them into their projects’ walls and ceilings!
Energy Efficiency Benefits
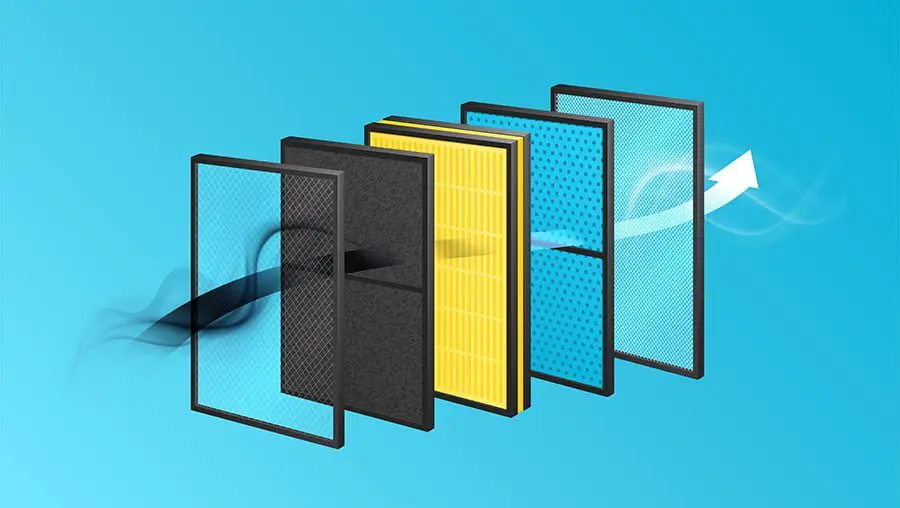
One of the most significant benefits of polymer insulation is its energy efficiency. With advancements in insulation technology, homeowners can now save money on their energy bills while also reducing their carbon footprint.
Polymer insulation has a higher R-value than traditional fiberglass or cellulose insulation, providing better thermal resistance and keeping heat inside during colder months and outside during warmer ones.
This results in less reliance on heating and cooling systems to maintain comfortable temperatures within homes or buildings.
Moreover, polymer insulations are designed to be air-tight which means they prevent drafts from entering your home through gaps around windows or doors that could cause cold spots throughout your house.
Using polymer insulation can lead to significant savings for homeowners over time by reducing their monthly utility costs while also contributing positively towards environmental sustainability efforts.
Fire Safety Concerns
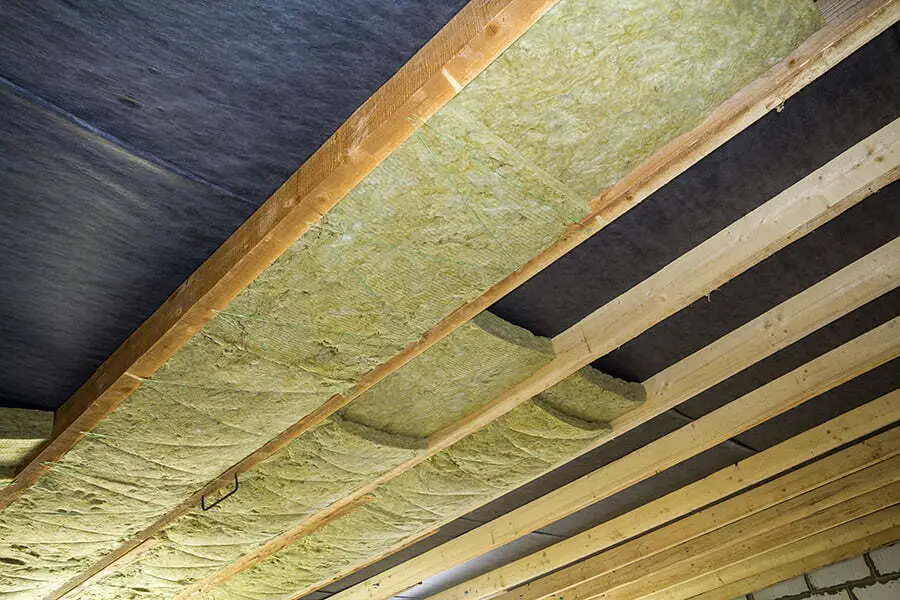
While polymer insulation has many benefits, there are also concerns about its fire safety. That’s why it’s important to understand the potential risks associated with using polymer insulation.
Polymer materials can be highly flammable if they’re not treated properly during manufacturing. This means that if a fire were to occur in a building with improperly treated polymer insulation, it could spread quickly and cause significant damage.
However, advancements have been made in recent years to improve the fire resistance of polymer insulation products. Manufacturers now use additives such as flame retardants and smoke suppressants to make their products safer for use in buildings.
It’s important for builders and contractors to ensure that they’re using high-quality polymer insulation products from reputable manufacturers who prioritize safety standards. By doing so, we can continue reaping the benefits of this innovative technology while minimizing any potential risks associated with its use.
Environmental Impact
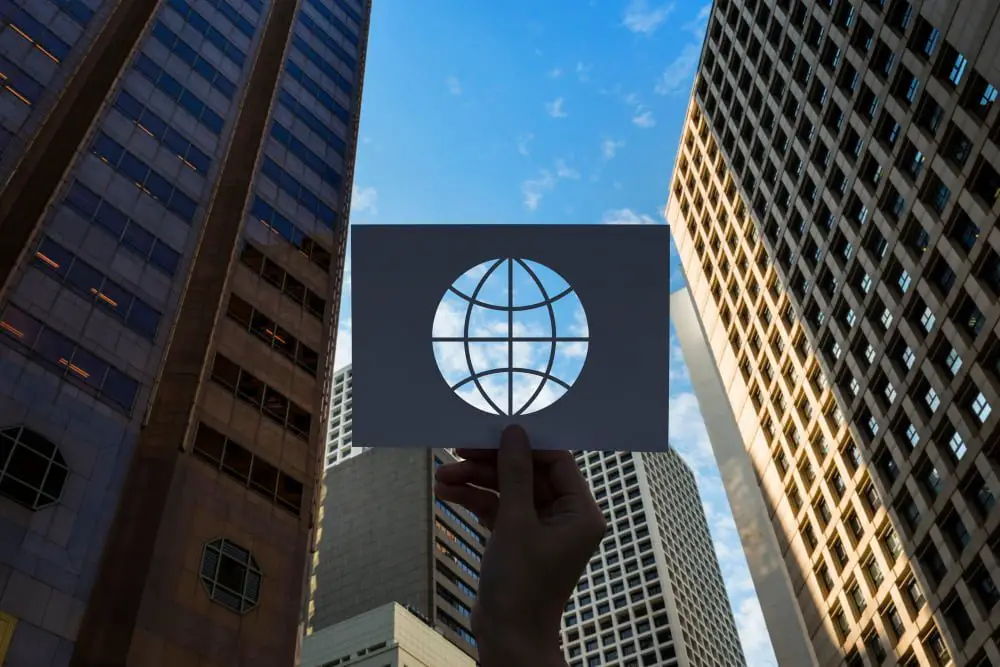
While polymer insulation has many benefits, it’s important to consider its environmental impact. As a synthetic material, polymer insulation is not biodegradable and can take hundreds of years to decompose in landfills.
The manufacturing process for this type of insulation requires energy and resources that contribute to greenhouse gas emissions.
However, advancements in technology have led to the development of more sustainable options for polymer insulation manufacturing. Some companies are using recycled materials or renewable energy sources during production to reduce their carbon footprint.
As builders and consumers become more environmentally conscious, there is a growing demand for eco-friendly building materials like sustainable polymer insulation. By choosing products with lower environmental impacts, we can help create a healthier planet while still enjoying the benefits of modern construction technology.
Recycling and Waste Management
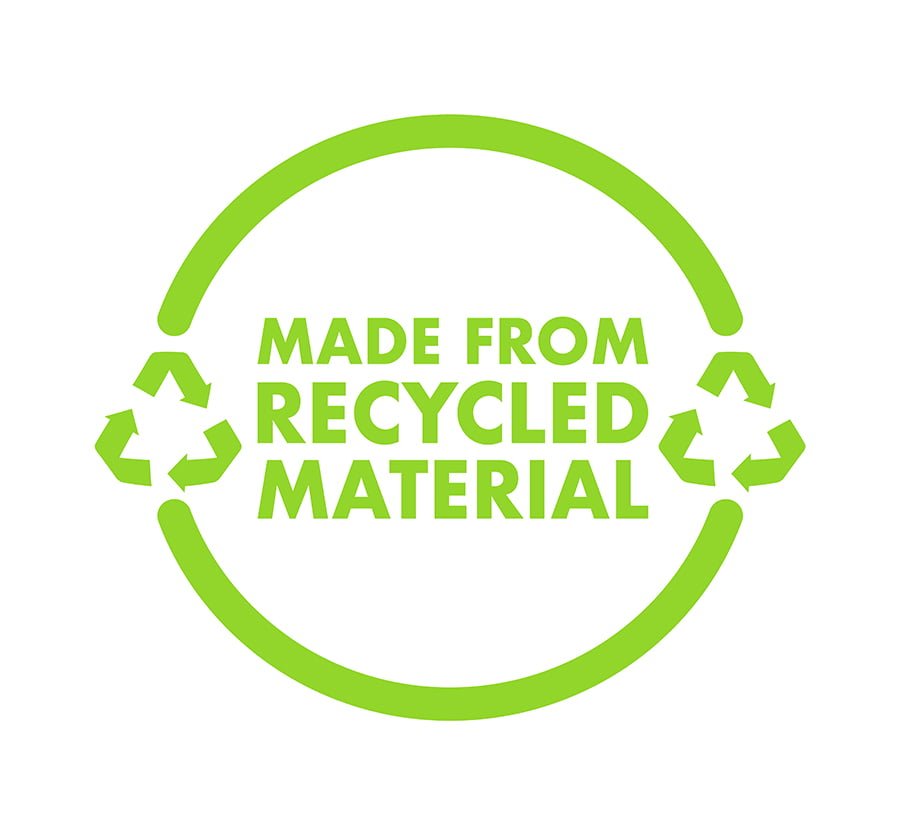
As we discussed earlier, polymer insulation is a great alternative to traditional insulation materials. However, like any product, it has its own set of challenges. One such challenge is recycling and waste management.
Polymer insulation can be recycled but the process requires specialized equipment and facilities that are not widely available yet. This means that most of the polymer waste ends up in landfills where decomposing takes hundreds of years.
To address this issue, manufacturers are exploring ways to reduce waste during production by optimizing their manufacturing processes and using recycled materials wherever possible. Some companies have also started offering take-back programs for used or leftover material from construction sites.
In addition to reducing waste during production and disposal stages, architects and builders can also design buildings with sustainability in mind by incorporating features such as green roofs or solar panels which help reduce energy consumption overall.
While there’s still work left to do when it comes to recycling polymer insulation effectively on a large scale basis; however these efforts show promise towards creating more sustainable building practices for future generations while keeping our environment clean at the same time!
Cost Analysis of Polymer Insulation
Polymer insulation has gained significant popularity in the building industry due to its excellent thermal performance and energy efficiency. However, one crucial aspect that needs consideration is the cost analysis of polymer insulation.
While it may have a higher upfront cost compared to traditional insulation materials, such as fiberglass or mineral wool, it offers long-term benefits that can outweigh the initial investment.
The manufacturing process of polymer insulation involves advanced technologies and specialized equipment, which can contribute to higher production costs. Factors like raw material prices and market demand also influence the overall cost of polymer insulation products.
However, when evaluating the true value of polymer insulation in terms of energy savings and reduced heating or cooling expenses over time, it becomes evident that these benefits often offset any additional costs incurred during installation. Polymer insulations’ high thermal resistance properties help maintain stable indoor temperatures while minimizing heat transfer through walls or roofs.
Moreover, unlike some conventional insulating materials prone to moisture absorption or degradation over time—leading to decreased effectiveness—polymer-based solutions offer superior durability with minimal maintenance requirements. This longevity translates into long-term savings for homeowners by reducing replacement or repair costs associated with other types of insulations.
It’s important for builders and contractors alike to consider not only immediate expenses but also evaluate lifecycle costs when making decisions about construction materials like polymer insulation.
Regulatory Implications On Polymer Insulation Manufacturing
These regulations aim to ensure the safety, quality, and environmental sustainability of polymer insulation products.
One key aspect that manufacturers need to consider is compliance with fire safety codes. Polymer insulation materials must meet specific fire resistance requirements to minimize the risk of spreading flames in case of a fire.
This involves testing for flame spread, smoke generation, and heat release properties.
There are regulations related to thermal performance standards for polymer insulation products. These standards determine how well an insulating material can resist heat transfer and contribute towards energy efficiency in buildings.
Environmental considerations also play a significant role in regulatory compliance for polymer insulation manufacturing. Many countries have implemented guidelines regarding the use of certain chemicals or substances that may be harmful or have adverse effects on human health or the environment during production or disposal processes.
Manufacturers must adhere to these regulations by using approved raw materials and employing sustainable production practices that minimize waste generation while maximizing resource efficiency.
Role of Polymer Insulation in Sustainable Construction
With the increasing focus on reducing energy consumption and minimizing environmental impact, builders are turning to polymer insulation as an eco-friendly alternative.
One of the key benefits of polymer insulation is its excellent thermal performance, which helps to reduce heat transfer through walls, roofs, and floors. By effectively insulating buildings from external temperature fluctuations, polymer insulation reduces the need for excessive heating or cooling systems.
This not only saves energy but also lowers greenhouse gas emissions associated with traditional HVAC systems.
Furthermore, many types of polymer insulations are made from recycled materials or can be recycled themselves at the end of their lifespan. This significantly reduces waste generation and promotes a circular economy approach in construction.
In addition to its thermal properties and recyclability aspects, polymer insulation also offers other sustainability advantages such as moisture resistance and durability. It helps prevent condensation within building structures by acting as a barrier against moisture infiltration while maintaining structural integrity over time.
Maintenance and Durability Aspects of Polymer Insulation
One key benefit is its resistance to moisture absorption, which helps prevent mold growth and structural damage. Unlike traditional insulation materials like fiberglass or cellulose, polymer insulation does not degrade when exposed to water or high humidity levels.
Polymer insulation has excellent thermal stability and can withstand extreme temperatures without losing its insulating properties. This means that it remains effective in both hot summers and cold winters.
Another advantage of polymer insulation is its resistance to pests such as rodents or insects. Unlike other types of insulations that may provide nesting opportunities for pests, polymers create a barrier that deters them from entering the building envelope.
Furthermore, polymer-based insulations are known for their long lifespan compared to other materials commonly used in construction. They have high mechanical strength and do not easily compress over time under normal conditions.
In terms of maintenance requirements, polymer insulation typically requires minimal upkeep once installed properly by professionals. It does not settle or sag over time like some traditional forms of insulation might do due to gravity’s effects on heavier materials.
Innovations in Polymer Insulation: Case Studies
These advancements have brought about significant improvements in terms of energy efficiency, durability, and ease of installation. Let’s take a look at some case studies that highlight these innovative solutions.
One such case study involves the development of aerogel-based polymer insulation. Aerogels are lightweight materials with exceptional thermal properties due to their high porosity and low density.
By incorporating aerogels into polymer matrices, manufacturers have created insulation materials that offer superior thermal performance compared to traditional options.
Another interesting innovation is the use of phase change materials (PCMs) in polymer insulation systems. PCMs can absorb or release heat during phase transitions, effectively regulating indoor temperatures by storing excess heat during warmer periods and releasing it when temperatures drop.
This technology has proven particularly effective in reducing heating and cooling costs while maintaining comfortable indoor environments.
Furthermore, advancements in nanotechnology have led to the development of nanoporous polymers for insulation purposes. These polymers possess an intricate network structure at a nanoscale level which enhances their insulating capabilities significantly while maintaining flexibility and ease-of-use during installation.
Researchers are exploring bio-based polymers as sustainable alternatives for conventional petroleum-derived plastics used in insulation manufacturing processes today. These bio-based polymers can be derived from renewable sources such as plant oils or agricultural waste products like corn stalks or sugarcane bagasse.
By utilizing these innovative materials instead of fossil fuel-derived counterparts, the environmental impact associated with traditional plastic production can be reduced significantly without compromising on performance characteristics required for efficient building envelope design.
These case studies demonstrate how ongoing research efforts continue to push boundaries within the realm of polymer insulations, resulting in more energy-efficient buildings, reduced carbon footprints, and improved occupant comfort levels. As technology continues to evolve rapidly within this sector, we can expect even more exciting innovations that will revolutionize the way we insulate our buildings in the future.
FAQ
How are polymer insulators made?
Polymer insulators are constructed by covering a fiberglass rod core with weather sheds made from various materials, including silicone rubber, EPM, EPDM, CE, and polytetrafluoroethylene (PTFE or Teflon).
What is the raw material for polymer insulators?
The raw material for polymer insulators is silicon rubber.
What polymer is used for insulation?
The polymer used for insulation is typically ethylene propylene diene monomer (EPDM), ethylene propylene monomer (EPM), silicone rubber, or an EPDM/silicone rubber alloy.
What is the lifespan of polymer insulators?
The expected service lifespan of polymer insulators is over 50 years.
What processes are involved in the manufacturing of polymer insulators?
The manufacturing of polymer insulators involves processes such as mixing of raw materials, molding or extrusion, curing, and finishing.
How does the performance of polymer insulators compare with traditional ceramic ones?
Polymer insulators often outperform traditional ceramic ones due to their enhanced resistance to pollution, lighter weight, superior flexibility and overall lower maintenance requirements.
What factors influence the lifespan of polymer insulators in various environmental conditions?
The lifespan of polymer insulators in various environmental conditions is influenced by factors such as UV radiation, temperature fluctuations, humidity, pollution level, and mechanical stress.
Recap