Discover the game-changing benefits of extruded polymer insulation, a revolutionary method for enhancing heat retention in buildings, explained in simple terms by our construction industry expert.
This cutting-edge approach to heat retention in buildings is changing the game when it comes to energy efficiency and comfort.
In this article, we’ll explore extruded polymer insulation, how it works, and why it’s quickly becoming a popular choice for builders and homeowners alike.
So please grab a cup of hot cocoa (or your beverage of choice), get cozy, and let’s dive into this exciting topic!
Key takeaways:
- Extruded polymer insulation provides superior heat retention in buildings.
- It is made through a process of melting thermoplastic material and forcing it through a die to create rigid foam boards.
- Compared to traditional insulation materials, extruded polymer insulation offers better thermal performance, moisture resistance, and durability.
- It improves energy efficiency and reduces heating and cooling costs.
- Installation methods include rigid panels and spray foam applications.
Polymer Extrusion Process
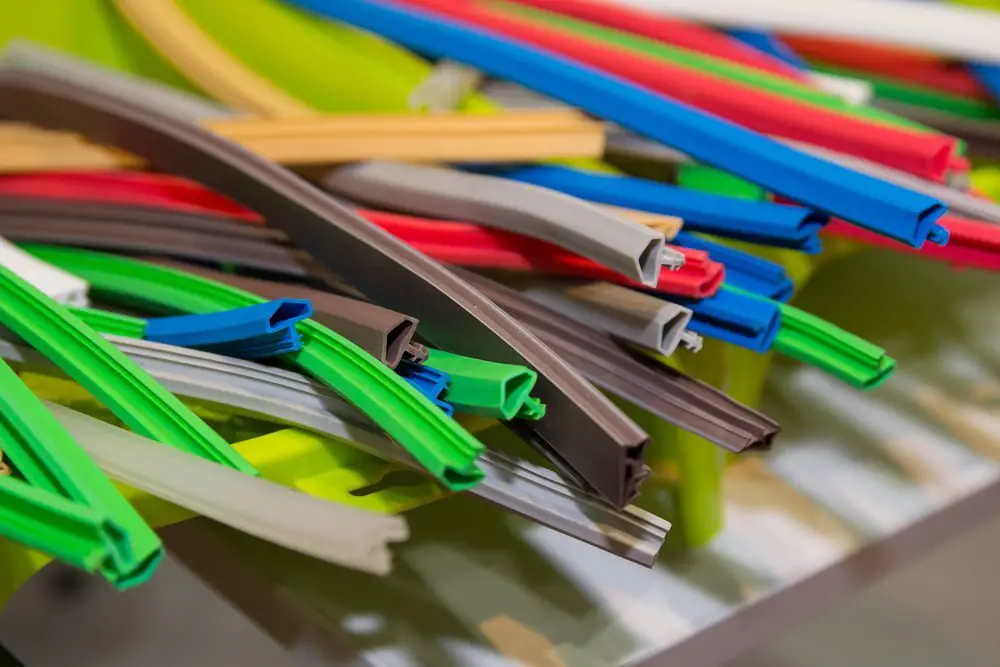
To understand how extruded polymer insulation works, it’s important to first understand the polymer extrusion process. This manufacturing technique involves melting a thermoplastic material and then forcing it through a die to create a specific shape or form.
In the case of extruded polymer insulation, this process is used to create rigid foam boards that are designed for use in walls, roofs, and floors. The foam boards comprise tiny closed cells that trap air inside them – an excellent insulator against heat transfer.
Another popular use of extrusion is to create profiled rubber strips for weatherstripping.
Not only does it provide superior thermal performance compared with traditional materials like fiberglass or cellulose; but also offers other advantages such as moisture resistance and durability over time.
It’s no wonder why builders and homeowners alike are turning towards using extruded polymer insulation when constructing new buildings or renovating existing ones!
Insulation Materials: Types and Properties
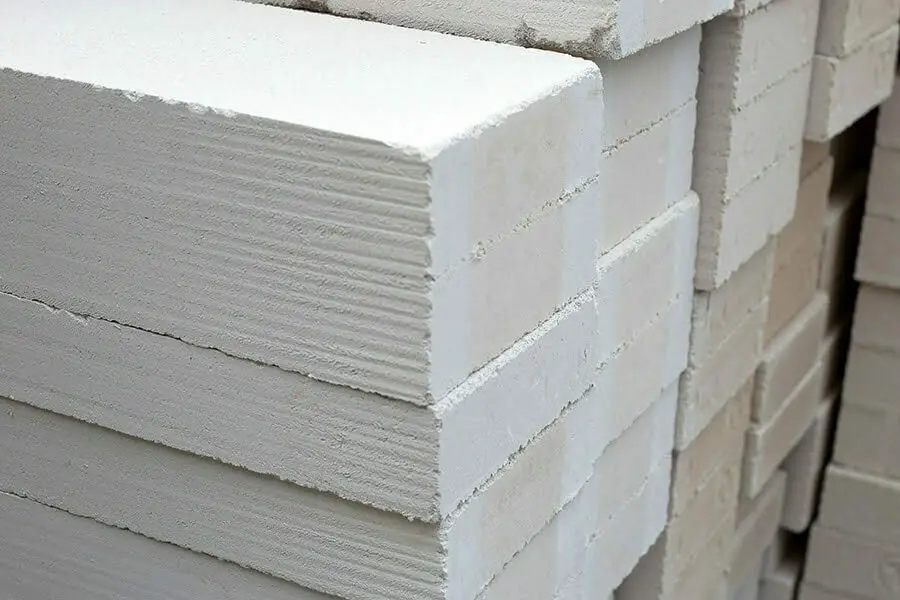
When it comes to insulation materials, there are a variety of options available on the market. Some common types include fiberglass batts, cellulose, and spray foam.
Each material has its own unique properties that make it suitable for different applications.
For example, fiberglass batts are made from tiny glass fibers and come in pre-cut panels or rolls. They’re easy to install and relatively inexpensive but may not be as effective at preventing air leaks as other materials.
Cellulose insulation is made from recycled paper products treated with fire retardants. It’s eco-friendly and can be blown into hard-to-reach areas for maximum coverage but may settle over time if not installed properly.
Spray foam insulation is a popular choice for new construction projects because it expands to fill gaps completely, creating an airtight seal that prevents heat loss or gain effectively.
Despite the various benefits of these traditional insulation materials mentioned above; they have their limitations when compared with extruded polymer insulations which we will discuss further in this article.
Heat Retention in Buildings
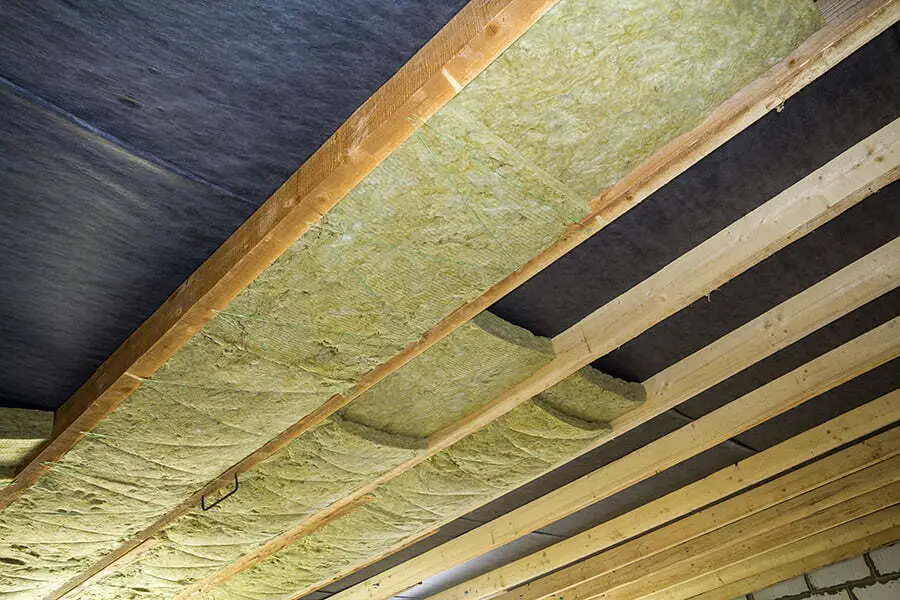
When it comes to keeping our homes warm and cozy, insulation is key. Without proper insulation, heat can easily escape through walls, floors, and ceilings – leaving us shivering in the cold.
That’s why builders and homeowners alike are always on the lookout for new ways to improve heat retention in buildings.
As I continued my research into extruded polymer insulation (XPI), I was impressed by its ability to provide superior thermal performance compared to traditional materials like fiberglass or cellulose. XPI is made from a closed-cell foam that has been extruded under high pressure – resulting in a material with excellent insulating properties.
But what really sets XPI apart is its durability over time. Unlike other types of insulation that can settle or degrade over time (resulting in decreased effectiveness), XPI maintains its shape and insulating properties for years to come.
In addition to providing better energy efficiency for your home (which translates into lower heating bills!), improved heat retention also means greater comfort during those chilly winter months. No more huddling under blankets or cranking up the thermostat just trying stay warm!
So if you’re looking for an innovative approach to improving your home’s energy efficiency while also increasing comfort levels year-round, consider giving extruded polymer insulation a try!
Energy Efficiency and Cost Savings
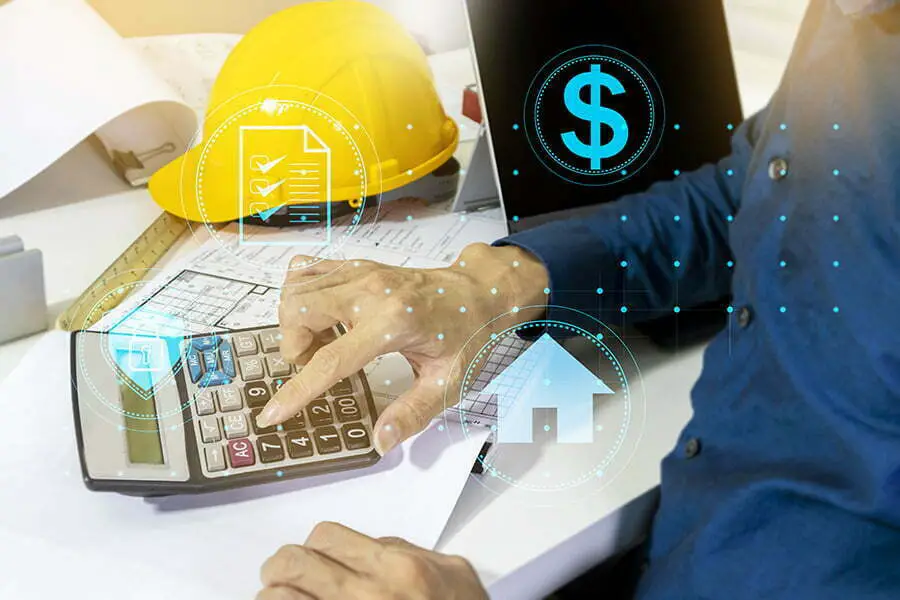
When it comes to keeping our homes warm in the winter and cool in the summer, energy efficiency is key. Not only does it help us stay comfortable, but it also saves money on utility bills and reduces our carbon footprint.
Compared to traditional insulation materials like fiberglass or cellulose, extruded polymer insulation offers superior thermal performance with a lower environmental impact. Its closed-cell structure creates an effective barrier against heat transfer, meaning less energy is needed to maintain a consistent indoor temperature.
But what about cost? While extruded polymer insulation may have a higher upfront cost than other options, its long-term benefits make it worth considering for any building project. By reducing heating and cooling needs year-round, homeowners can save significantly on their monthly utility bills over time.
Installation Techniques
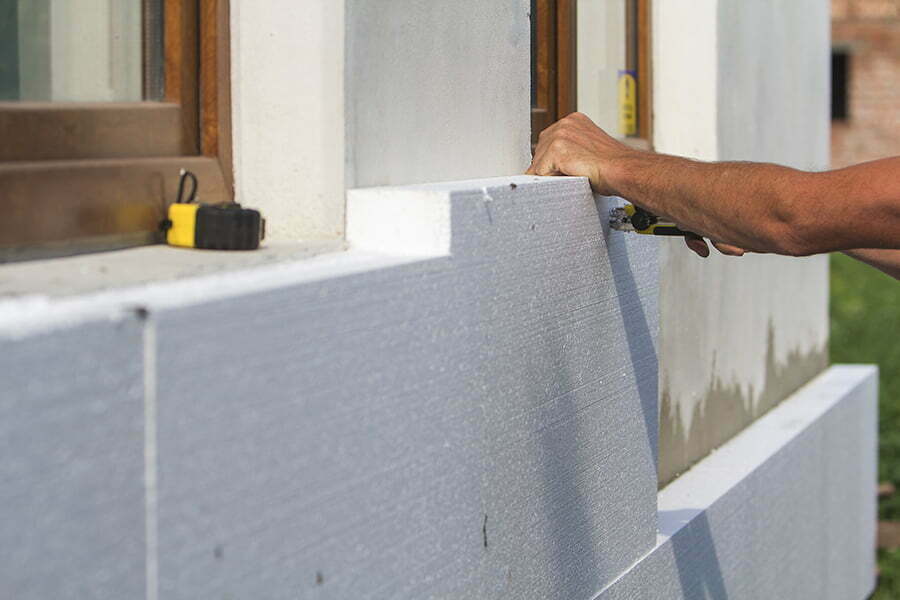
Now that we understand what extruded polymer insulation is and how it works, let’s take a closer look at the installation process. One of the benefits of this type of insulation is its versatility in application.
Extruded polymer can be installed in various ways, including as rigid panels or sprayed onto surfaces.
For new construction projects, rigid panels are often used to insulate walls and roofs. These panels are cut to size on-site and then attached directly to the framing using mechanical fasteners or adhesive.
In retrofit situations where access may be limited, spray foam applications can be used instead. This involves spraying liquid foam onto surfaces which then expands into a solid layer once cured.
Regardless of the installation technique chosen, it’s important that proper safety measures are taken during installation due to potential health hazards associated with some types of insulation materials.
Extruded polymer insulation offers an innovative approach for builders looking for energy-efficient solutions without sacrificing comfort or design aesthetics. With its versatile application methods and superior thermal performance properties compared to traditional options like fiberglass batts or blown-in cellulose fibers – it’s no wonder why more homeowners than ever before are choosing this material for their homes!
Environmental Impact
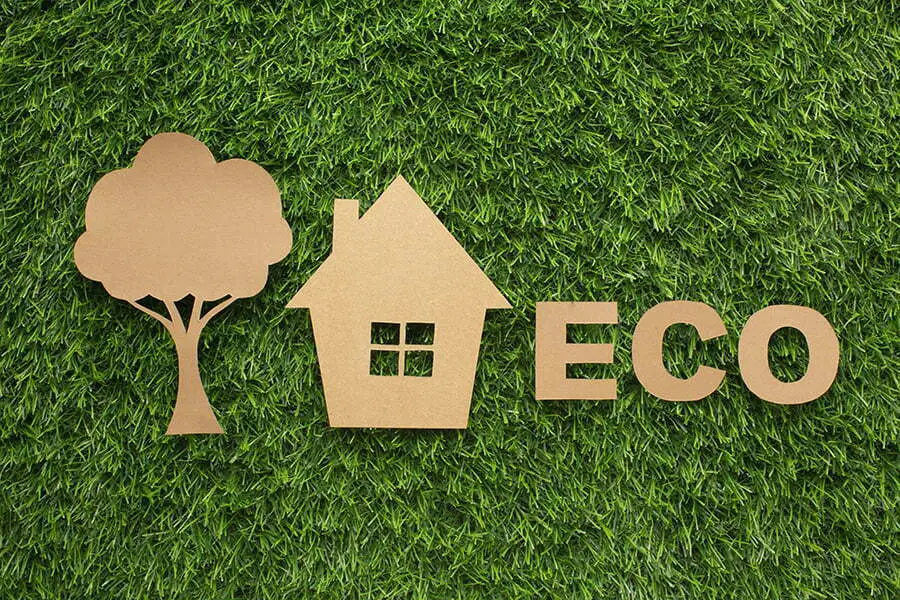
Unlike traditional insulation materials like fiberglass or foam board, which can release harmful chemicals and greenhouse gases during production and installation, extruded polymer insulation is made from non-toxic materials that are safe for both humans and the planet.
In fact, many manufacturers of extruded polymer insulation use recycled content in their products. This means that waste plastic materials are repurposed into high-quality building components instead of ending up in landfills or oceans.
Because this type of insulation creates an air-tight seal around a building’s envelope (the outer layer), it helps prevent drafts and reduces the need for heating or cooling systems to work overtime – ultimately leading to lower carbon emissions.
Choosing extruded polymer insulation over other types can have significant environmental benefits while still providing top-notch thermal performance. It’s exciting to see how innovations like this one are making strides towards more sustainable construction practices!
Durability and Lifespan
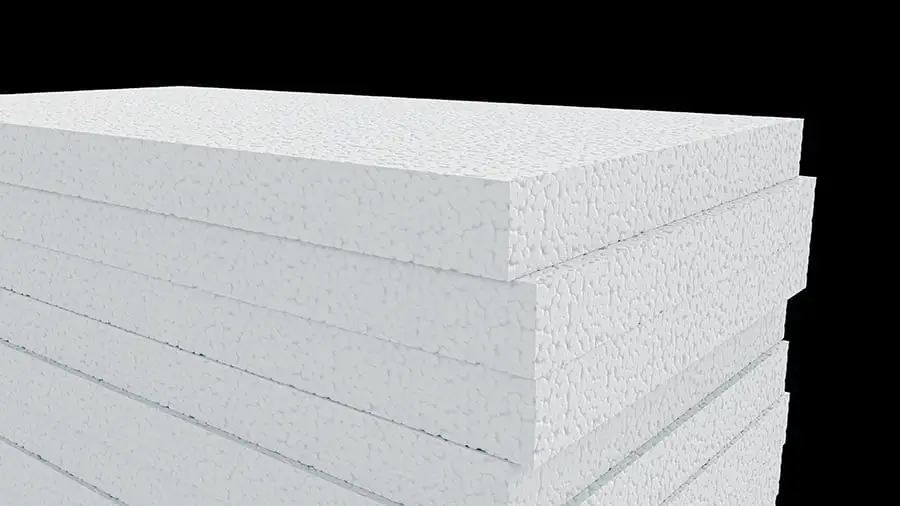
One of the most important factors to consider when choosing insulation for your home or building is durability. After all, you want an investment that will last for years to come and won’t require frequent replacements or repairs.
When it comes to extruded polymer insulation, durability is a major selling point. This type of insulation is made from high-density closed-cell foam that can withstand wear and tear over time.
It’s also resistant to moisture, mold, and pests – common issues that can compromise the effectiveness of other types of insulation.
Unlike some traditional forms of fiberglass or cellulose insulations which may need replacing every 10-15 years due to settling or degradation caused by moisture absorption; Extruded Polymer Insulation has a much longer life span with little-to-no maintenance required once installed properly.
If you’re looking for an effective solution for heat retention in buildings with long-lasting results then Extruded Polymer Insulation should definitely be on your list!
Comparative Analysis of Extruded Polymer Insulation With Other Insulation Materials
When it comes to insulation materials for buildings, there are various options available in the market. One such option is extruded polymer insulation, which offers several advantages over other types of insulation materials.
Compared to traditional insulating materials like fiberglass or mineral wool, extruded polymer insulation provides superior thermal performance. Its closed-cell structure helps minimize heat transfer by trapping air within its cells.
This results in better heat retention and energy efficiency for buildings.
Extruded polymer insulation also has a higher R-value compared to many other insulating materials. The R-value measures the material’s resistance to heat flow; a higher value indicates better thermal resistance.
With its high R-value, extruded polymer insulation can effectively reduce heating and cooling costs by minimizing energy loss through walls, roofs, and floors.
Another advantage of using extruded polymer insulation is its moisture resistance properties. Unlike some traditional insulating materials that can absorb water or retain moisture when exposed to damp conditions, this type of insulation remains unaffected by moisture intrusion due to its closed-cell structure.
Furthermore, unlike fiberglass or mineral wool that may release harmful particles into the air if damaged or disturbed during installation or maintenance activities (such as cutting), extruded polymer foam does not pose any health risks associated with airborne fibers.
In terms of durability and longevity, extruded polymer foam stands out as well. It is resistant against rotting and decay caused by pests like termites or rodents since it does not provide them with food sources nor serve as a suitable habitat for their growth.
Extrud ed polymer insulation offers numerous benefits over other types of insulation materials. Its superior thermal performance, higher R: value, moisture resistance properties, and long-lasting durability make it an excellent choice for enhancing energy efficiency while ensuring comfort inside buildings.
Innovations and Future Trends in Extruded Polymer Insulation
Researchers and manufacturers are continuously working to improve the performance, efficiency, and sustainability of these materials.
One notable innovation is the development of high-performance polymer blends that offer enhanced thermal resistance while maintaining structural integrity. These advanced blends can provide superior insulation properties compared to traditional materials like fiberglass or foam board.
Another promising trend is the incorporation of nanotechnology into extruded polymer insulation. By adding nanoparticles to the material matrix, researchers have been able to enhance its thermal conductivity properties significantly.
This allows for better heat retention in buildings while reducing energy consumption.
Furthermore, there has been a growing focus on sustainable solutions within the industry. Manufacturers are exploring ways to incorporate recycled polymers into their products without compromising performance or durability.
This not only reduces waste but also contributes towards a more circular economy.
Advancements in manufacturing processes have led to improved quality control measures for extruded polymer insulation production lines. Automated systems now ensure consistent thicknesses throughout each panel or sheet produced, resulting in higher overall product reliability.
Looking ahead at future trends, research efforts are underway towards developing smart polymers that can adapt their insulating properties based on environmental conditions such as temperature changes or humidity levels within a building’s interior space. The continuous innovations and emerging trends inextrudedpolymerinsulationare revolutionizingthe constructionindustry by providingmore efficientand sustainableheatretention solutionsfor buildings.
Health and Safety Considerations in the Use of Polymer Insulation
Fortunately, extruded polymer insulation is generally considered safe for use in construction projects. However, it is still essential to follow proper handling procedures and take necessary precautions.
One important aspect to consider is the potential release of volatile organic compounds (VOCs) during the manufacturing process or when exposed to high temperatures. VOCs can have adverse effects on indoor air quality and human health if not properly managed.
Therefore, it’s crucial to choose products that meet industry standards for low VOC emissions.
Proper ventilation should be ensured during installation or renovation projects involving polymer insulation materials. Adequate airflow helps dissipate any residual odors or fumes that may be present initially.
Furthermore, personal protective equipment (PPE) should be used by workers who handle extruded polymer insulation materials regularly as a precautionary measure against skin irritation or respiratory issues caused by prolonged exposure.
Lastly, regular maintenance and inspection of the installed polymer insulation are recommended over time as wear and tear can occur due to environmental factors such as moisture ingress or physical damage from external sources like pests.
Regulatory Standards and Compliance in Polymer Insulation Industry
These standards ensure that the materials used in construction meet specific requirements for safety, performance, and environmental impact.
In many countries, there are regulatory bodies responsible for setting these standards and monitoring compliance. They establish guidelines regarding factors such as fire resistance, thermal conductivity, moisture absorption rates, and durability of polymer insulation products.
Compliance with these regulations is essential to ensure that buildings are safe for occupants while also minimizing any negative impact on the environment. Manufacturers must adhere to strict testing procedures to demonstrate their product’s compliance with these regulations before they can be sold on the market.
Some regions have specific certifications or labels that indicate a product’s adherence to certain quality or sustainability criteria. For example, LEED (Leadership in Energy and Environmental Design) certification is widely recognized as an indicator of environmentally friendly building practices.
It is important for builders and contractors to stay informed about relevant regulatory requirements when selecting extruded polymer insulation products.
Maintenance and Repair of Extruded Polymer Insulation
Here are some key points to consider:
1. Visual Inspection: Conduct regular visual inspections to identify any signs of damage or deterioration, such as cracks, gaps, or discoloration.
This can help detect potential issues early on.
2. Cleaning: Keep the surface clean by removing dirt, debris, and other contaminants that may accumulate over time.
Use a mild detergent solution and a soft brush or cloth for cleaning purposes.
3. Sealing Gaps: If there are any visible gaps or openings in the insulation material due to wear and tear or improper installation, it is crucial to seal them promptly using appropriate sealants recommended by manufacturers.
4. Moisture Management: Ensure proper moisture management around the insulation system as excessive moisture can degrade its performance over time.
Address any water leaks promptly and maintain adequate ventilation within the building envelope.
5.Repairing Damaged Sections: In case of significant damage like punctures or tears in extruded polymer insulation panels, it’s important not only to repair but also replace those sections if necessary for maintaining consistent thermal efficiency throughout the building envelope.
6. Professional Assistance: For complex repairs beyond your expertise level, seek professional assistance from qualified contractors who specialize in working with extruded polymer insulations. They have experience dealing with specific challenges related to these materials while ensuring compliance with industry standards.
By following these maintenance practices diligently, you can extend the lifespan of your extruded polymer insulation and maximize its energy-saving benefits. Remember that proactive care will save you money on potential costly replacements down-the-line.
FAQ
How does polymer extrusion work?
In polymer extrusion, a polymer material along with selected additives is melted, then continuously shaped and cooled by passing it through a screw and die system.
What is extruded insulation in cables?
Extruded insulation in cables refers to a protective layer created by pulling a wire through a heated polymer resin, which cools and solidifies to provide added protection.
How is extruded polystyrene insulation made?
Extruded polystyrene insulation is produced through an extrusion process where plastic resin and other additives are merged and forced through a die, followed by cooling and expansion into its final form.
Can thermoplastics be extruded?
Yes, thermoplastics can be extruded, enabling the production of hollow tubes, sheets of different thicknesses, unique plastic parts, wire insulation, and packaging films.
What is the process involved in the production of polymer concrete?
The process involved in the production of polymer concrete includes the mixing of a polymeric resin with aggregates, followed by curing to create a hardened composite material.
How does the injection molding process work for thermoplastics?
The injection molding process for thermoplastics involves heating the polymer until it becomes molten, then injecting it under pressure into a mold where it cools and solidifies into the desired shape.
What are the key differences between thermoform plastics and thermoset plastics in construction?
In construction, the key differences between thermoform plastics and thermoset plastics lie in their processing and reusability, where thermoform plastics can be reheated, reshaped multiple times, and recycled, while thermoset plastics, once set, cannot be remelted or reshaped and are therefore less recyclable.
Recap