Choosing the right injection molding machine requires careful consideration of factors such as materials, size, energy efficiency and safety features.
Selecting the right injection molding machine is crucial for any construction project involving polymers. It’s not just about the size or the price; factors such as the type of polymer, the product’s design, and production volume also play significant roles.
This article will guide you through each step of the selection process, ensuring that you choose the most suitable machine for your specific needs. From understanding the basics of injection molding machines to comparing different models based on their features, you’ll find all the necessary details here.
So, whether you’re a beginner or an experienced professional, this comprehensive guide will help you make an informed decision.
Key takeaways:
- Understand the plastic parts you intend to mold
- Choose the correct machine type for injection molding
- Calculate clamp tonnage requirements accurately
- Determine the injection unit size based on shot weight, mold thickness, injection pressure, and plasticizing rate
- Avoid common machine selection mistakes and their consequences
Knowing the Plastic Parts You Intend to Mold
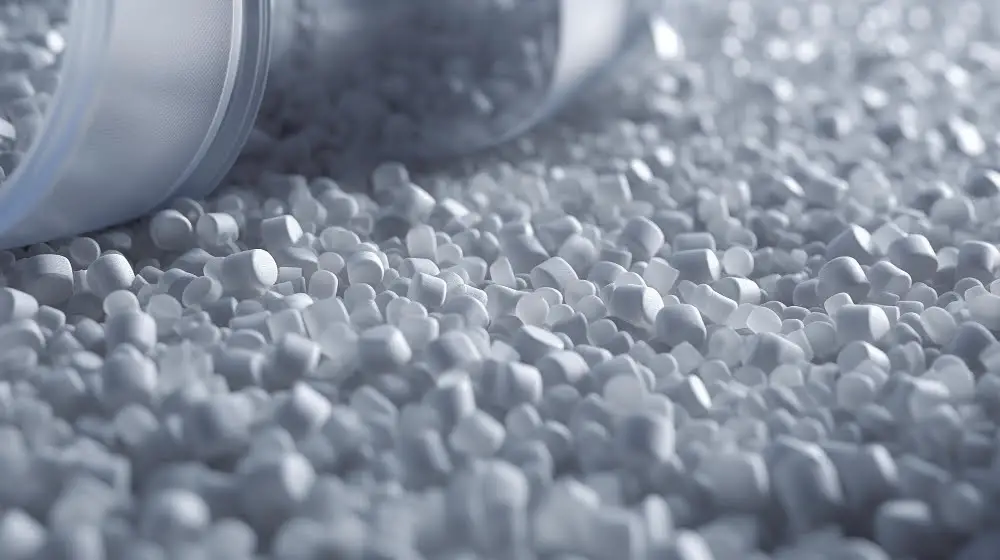
To start with, a deep understanding of the properties of the plastic materials you plan to mold significantly informs your machine selection. Here, the major considerations are the type and grade of plastic, size, weight, and geometry of the part.
The type and grade of plastic plays a significant role not only in determining the physical properties of the final product but also in indicating the processing conditions for the plastic, such as temperature and pressure requirements. Certain materials might require specific types of machines, while others can be processed by a range of machines.
Size and weight of the part significantly influence the size of the machine that you will need. For instance, if the part is large and heavy, a machine with a larger clamping force and a larger mold space is needed.
Geometry of the part is also paramount; complex shapes might require specialized machines with sophisticated control systems.
Recognizing these specifics is vital in identifying suitable machine models for the job at hand, guiding your further selection process towards the most efficient and economic choices.
Choosing the Correct Machine Type for Injection Molding
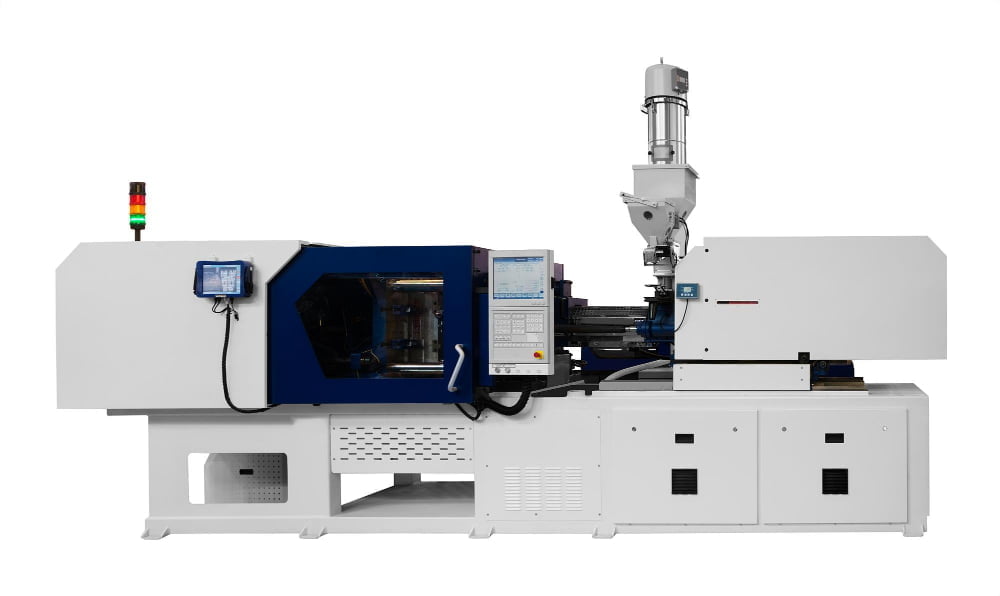
When it comes to injection molding machines, two key types dominate the industry: hydraulic and electric.
Hydraulic machines, being the traditional type, are known for their high clamping force – making them suitable for producing larger components. Powered by hydraulic pumps, they often require more maintenance and can be a bit noisy during operation. However, they offer excellent resistance to wear and tear, and their versatility is a big draw for many manufacturers.
On the other hand, electric machines are becoming increasingly popular due to their energy efficiency and precision molding capabilities. They consume less electricity, operate quietly, and are easier to maintain with fewer moving parts. Electric machines provide accurate, repeatable movements which leads to high-quality plastic parts. The downside is that they can be costly and may not provide the required force for larger plastic parts.
For niche applications, hybrid machines, which combine hydraulic power and electric precision, is a compelling choice. It offers the benefits of both types, such as high clamping force and precision molding.
Specific requirements such as the size and intricacy of the plastic parts, production volume, and budget dictate which type of machine is suitable. Always work with a reputable manufacturer or distributor to avoid pitfalls and ensure optimal performance and longevity of the machine.
Calculating Clamp Tonnage Requirements
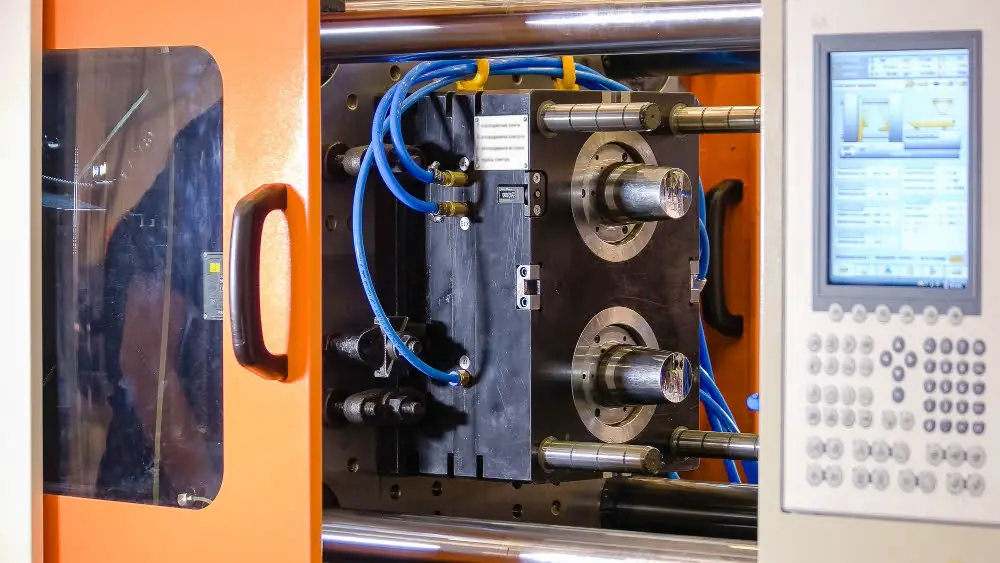
In terms of clamp tonnage, make an accurate estimate about the amount of pressure required. The concept is relatively simple: Clamp tonnage ensures that the mold stays closed during the plastic’s injection process.
A low tonnage may cause the mold to open slightly, leading to errors like flash, where excess material seeps out of the part’s edges. Equally, too much tonnage may cause unnecessary wear and tear on the machinery and the molds themselves, leading to unwarranted repair costs.
To calculate the clamp tonnage, consider these key factors:
- The projected area of the part being molded. In simple terms, take the longest dimension of the part, multiply it by the widest dimension. This gives the total square area of the part.
- The number of cavities in the mold. More cavities require more pressure.
- The type of plastic material used. Every plastic material has a different injection pressure. Check the molding pressure of the plastic material you’re using.
- Factor in the safety factors. A safety factor between 1.5 to 2 is often used to ensure adequate pressure and account for any potential variables during the molding process.
Once these factors are determined, use the formula: Clamp tonnage = Projected Area X Number of Cavities X Injection Pressure X Safety Factor.
This straightforward calculation will guide you toward the right clamp strength for your specific molding task.
Determining the Injection Unit Size
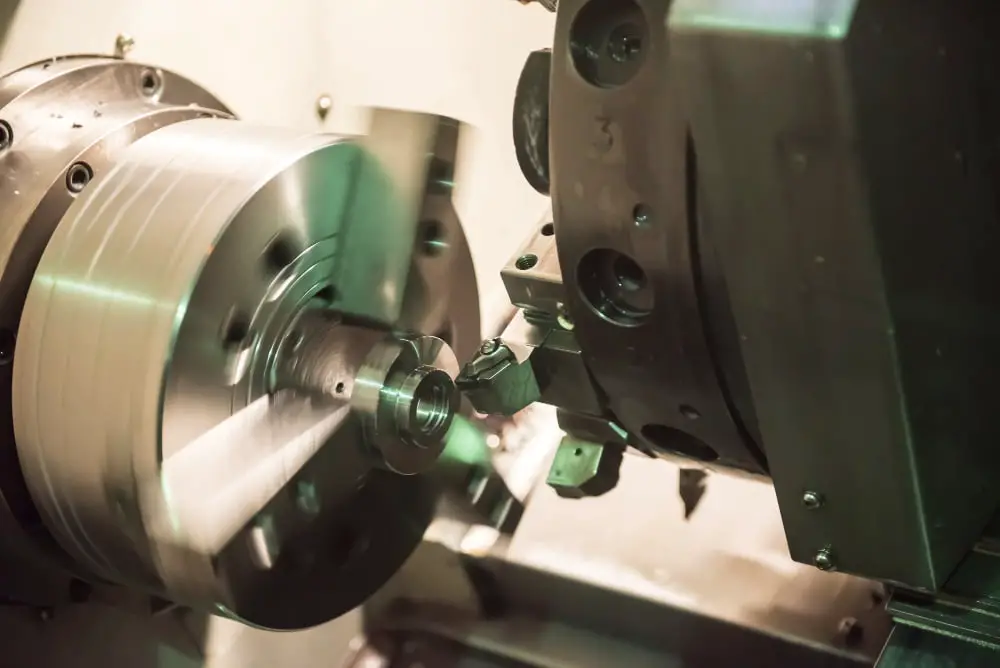
When selecting the appropriate injection unit size, several important factors should be evaluated.
Shot weight is a key consideration. It refers to the volume of plastic material the machine can inject in one cycle. It’s important to match shot weight with the expected weight of the molten plastic that will form your final part. In addition, it’s advised to select a machine that can handle slightly more material than you think you’ll need to cover any unexpected requirement changes.
The second factor is mold thickness. Consider the intended thickness of your molded parts. The machine you choose should have an injection unit that’s capable of properly filling and packing the mold.
Next, it’s essential to look at injection pressure. Each material has a different viscosity, thus needing a different force to push the plastic into the mold. Well-chosen injection pressure ensures efficient filling and optimum product quality.
Finally, consider the plasticizing rate, which relates to how fast the machine can heat and mix the plastic before it’s injected. This feature is important if speed and cycle times are critical for your operation.
Keep these factors in mind to ensure appropriate injection unit sizing for your specific project. Remember, this significant choice directly impacts the quality and production efficiency of your injection molded parts.
Avoiding Common Machine Selection Mistakes and Their Consequences
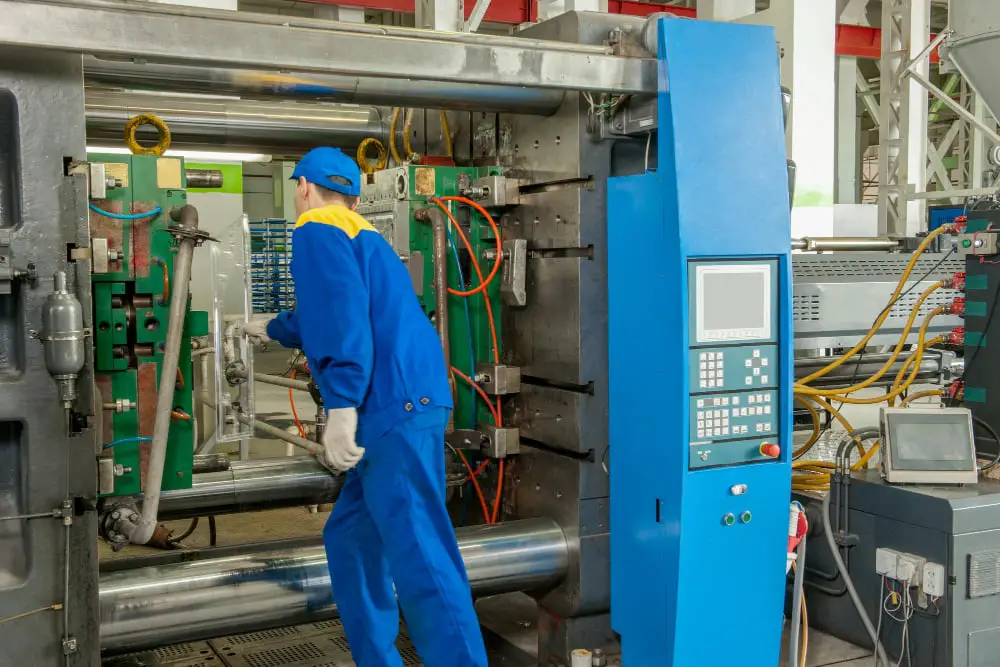
To ensure the success of your injection molding project, keep the following pitfalls and their subsequent impacts in mind:
One common mistake lies in oversizing the machine. It leads to substantial operational expenditure; without added benefits, you are paying for superfluous energy and space. Instead, the machine should be of optimal size for minimal wastage and maximal efficiency.
Another error is overlooking the machine’s part and shot size capabilities. If the machine doesn’t align with your project’s requirements, it can result in poor quality products or even damage to the machine. The clamp tonnage and the shot size should correspond directly to the intended plastic part’s size and weight.
Neglecting aftersales services and support can also be detrimental. Unresolved machine issues can halt your operations and result in lost revenue. Choose a supplier who offers reliable aftersales service.
Finally, remember that underestimating the necessity of a machine with advanced controls can limit the precision and repeatability of your molding process, affecting the final product’s quality.
Each of these errors has significant impacts which may include compromised product quality, increased downtime, additional repair or replacement costs, and potential project delays. By being mindful of these pitfalls, you can make an informed machine selection that best suits your needs.
Preparation Before Selecting Suitable Injection Molding Machine Models
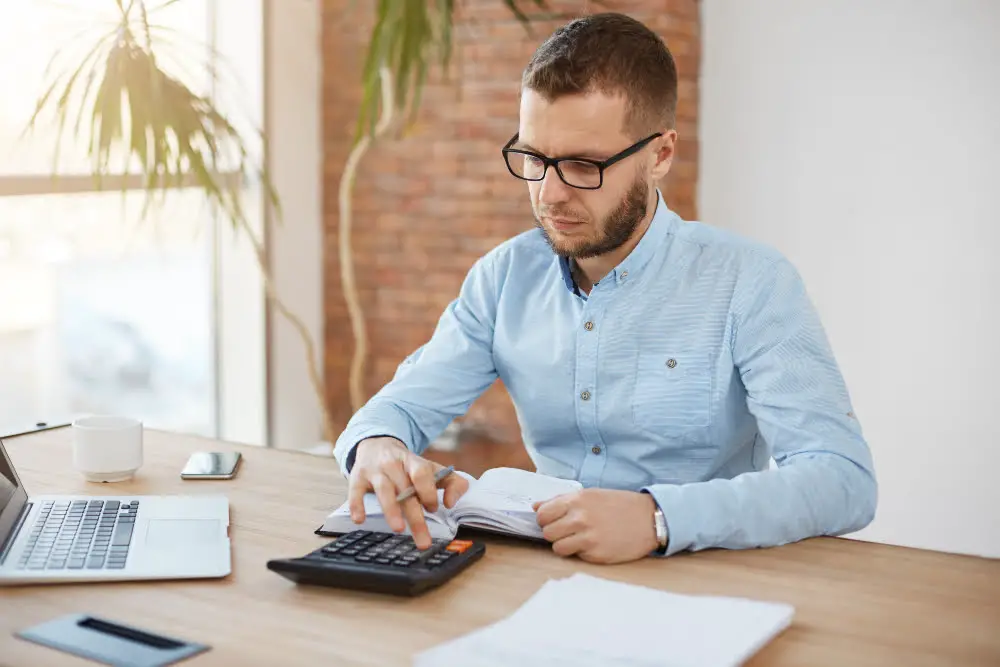
Before embarking on the process of selecting an injection molding machine, adequate preparation is vital. This entails understanding the intended operation and the plastic parts to be molded.
Firstly, identifying the types of plastics for the operation is key. Plastics vary in terms of strength, flexibility, and temperature requirements. Thus, the machine must be compatible.
Secondly, accurately calculate the size of the parts to be molded. This includes their weight and dimensions, which directly impact the machine’s size and capacity requirements.
Thirdly, the target production volume is also a crucial consideration. A high-volume operation might necessitate an assembly line of machines, while smaller volumes may only require a single machine.
Finally, evaluate your budget constraints. The cost of injection molding machines can vary depending on their capabilities and specifications. Understanding your budget can help to narrow down your options and focus on machines that meet both your operational requirements and your financial constraints.
By preparing effectively, selection becomes streamlined, leading to optimal utilization of time and resources. Understanding the requirements in depth allows for a comprehensive and informed decision while minimizing potential errors or oversights.
Understanding the Injection Molding Machine Selection Process
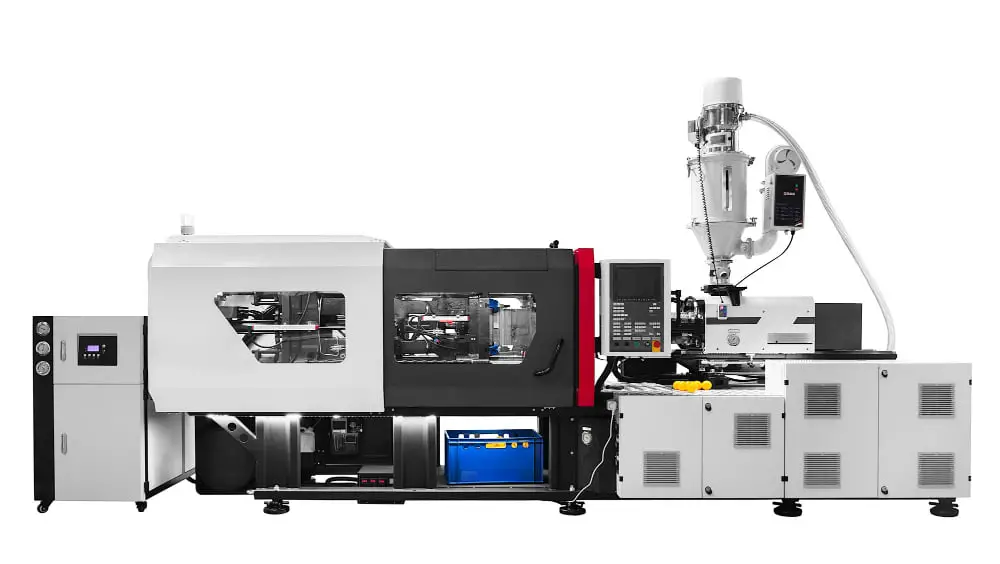
Selecting the right injection molding machine is vital and requires understanding of specific criteria. Start by analyzing the part’s intended usage, including withstanding force, dealing with temperature changes or wear and tear. Other key points to consider will be, application of the part, mold materials, cavity pressure, and plastic types being used.
Further, let’s look into the nitty-gritty of injection molding machine selection. Be cautious of the machine’s injection velocity and pressure as it should be adaptable enough to manage a variety of plastic materials. The machine should also be capable of controlling the speed of the injection process.
The plasticizing capacity is important too; ensure the machine can handle the required shot weight, meeting the plasticizing demands of each individual part. Also, understand the functionality of the mold for adequate clamping force provision. In addition, to achieve efficient molding, the machine should anticipate the stability, precision, and flexibility of the entire molding process.
Lastly, taking into consideration the equipment’s economic efficacy is crucial. The energy consumption, ease of maintenance, and long-term value for the investment significantly affects the operational cost-effectiveness of the injection molding machine. If thought through properly, each of these factors will guide in making an informed decision in selecting an optimal injection molding machine.
FAQ
How to choose plastic injection molding machine?
To choose a plastic injection molding machine, you need to assess the material type, use of fillers in this material, the size of the molded shot, the time needed for a cycle, the residence duration, the required pressure for plastic injection, the time it takes for the screw to recover, and the screw’s physical design.
How do I know what size injection molding machine I need?
To determine the size of an injection molding machine required, calculate 2.5 times the surface square inches of the part, adding an additional 10% as a safety factor; for instance, a part with 120 square inches would necessitate a machine with 300 tons of pressure.
How do you calculate tonnage for injection molding machine?
The tonnage for an injection molding machine can be calculated by multiplying the projected area of the molded part (in square inches) by the clamp factor (tonnage needed per square inch from the material data sheet).
What is the most common injection molding machine?
The most common injection molding machine is the hydraulic type, which is operated by a hydraulic pump and a fixed speed electrical motor.
What are the key factors to consider in injection molding machine maintenance?
Key factors to consider in injection molding machine maintenance include regular check-ups of hydraulic pressure, mould and machine cleanliness, proper lubrication, and examination of wear and tear.
How does the type of polymer influence the choice of an injection molding machine?
The type of polymer influences the choice of an injection molding machine by determining the required temperature, pressure, and dwell time settings for optimal processing of specific materials.
How do environmental factors affect the performance of an injection molding machine?
Environmental factors such as temperature and humidity can significantly influence the performance of an injection molding machine by affecting the properties of the polymer and the efficiency of the molding process.
Recap