Discover how to accurately calculate the tonnage for an injection molding machine, a crucial step in optimizing your polymer construction projects.
Calculating the tonnage for an injection molding machine is a crucial step in the construction process, ensuring that the machine can handle the pressure required to create the desired polymer components.
The formula to calculate this is simple: clamp tonnage equals projected area of the part, multiplied by the number of cavities, multiplied by the injection pressure.
The projected area is measured in square inches, while the injection pressure is typically 2-5 tons per square inch for most materials.
This article will guide you through the details of each variable, ensuring that you can accurately calculate the tonnage for your specific injection molding machine and polymer material.
Key takeaways:
- Correlation with Clamp Force
- Tonnage and Mold Size
- Factor in Material Selection
- Engineering Design Consideration
- Machine Specification Attribute
Understanding the Concept of Tonnage in Injection Molding
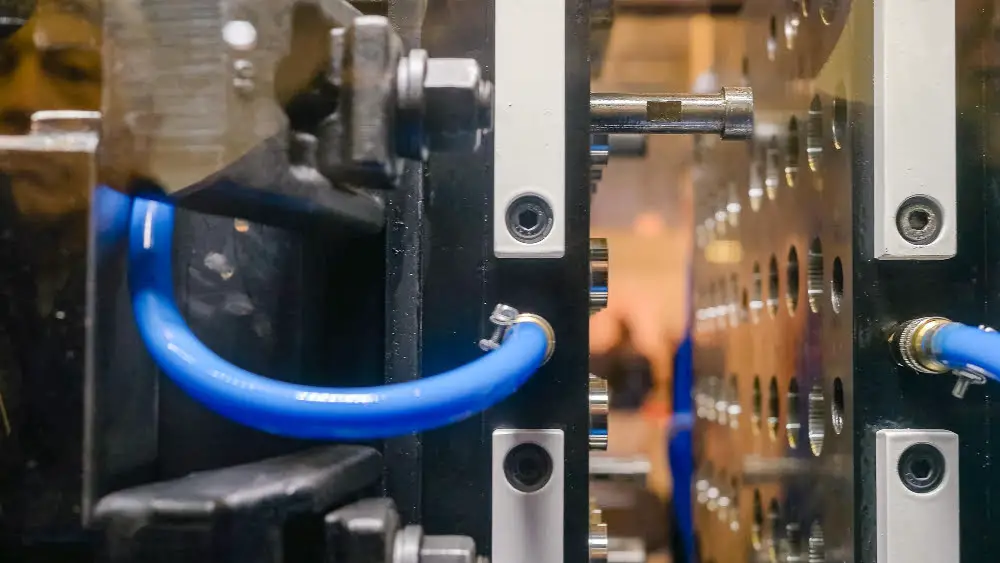
Tonnage in injection molding refers to the force applied by the machine to keep the mold closed during the injection process. This resistance against the pressure of the injected plastic is crucial to prevent the mold from opening, which could result in defects within the final product.
1. Correlation with Clamp Force: A common misconception is that ‘tonnage’ implies the volume or weight of the final product. Instead, it represents the clamp force required to counteract pressure from the injected plastic.
2. Tonnage and Mold Size: The tonnage relates directly to the size of the mold being used. Larger molds require higher tonnage to maintain tight closure during injection.
3. Factor in Material Selection: Different plastics have varying viscosities which can alter the pressure required to fill the mold. As such, your tonnage will differ based on material choice.
4. Engineering Design Consideration: Tonnage calculation is integral to the engineering and design process of molds. It allows for the accurate design of both molding equipment and the molds themselves for efficient, high-quality output.
5. Machine Specification Attribute: The ‘tonnage’ of an injection molding machine is often a key specification, representing its capacity to withstand the pressure of the plastic being injected. This is instrumental in machine selection for specific molding projects.
Significance of Precise Tonnage Calculation in Injection Molding
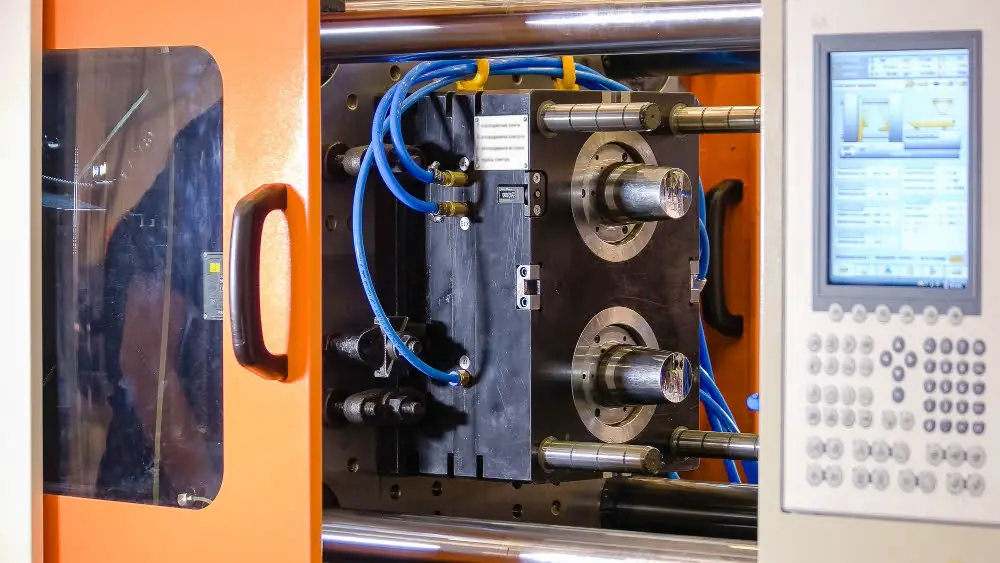
A well-calibrated tonnage in injection molding is instrumental for a variety of reasons:
- It ensures the optimal use of resources, minimizing both waste and energy consumption. Overestimation or underestimation of tonnage can lead to inefficient machine operation.
- Appropriate tonnage safeguards the lifespan of the mold. Insufficient pressure can result in incomplete filling, leading to poor-quality output. Excessive force, on the other hand, can cause mold wear and possible damage.
- Maintaining the right tonnage helps achieve consistent output. This is important in production environments where uniformity of products is crucial. Deviations caused by inaccurate tonnage could lead to compromised product integrity.
- Correct tonnage calculation impacts the safety of operations. Excess tonnage can put undue stress on the machine, increasing the potential for hazardous malfunctions.
- Efficient tonnage calculation assists in deciding the right machine for a specific project. Knowing the required force ensures that neither a too large nor a too small injection molding machine is chosen, optimizing investment and production capabilities.
How to precisely calculate tonnage:
- Measure the projected area of the mold. This includes the cavity and the runner system.
- Identify the material’s melt factor. Different polymers will require different melt factors, which influence the amount of force necessary to inject the molten polymer into the mold.
- Calculate the tonnage by multiplying the projected area by the melt factor. This will give you the required force in tons.
It’s important to note that these are general steps and actual calculations may vary based on specific project requirements. Always consult with a professional when unsure.
Determining Factors Influencing Tonnage Requirements
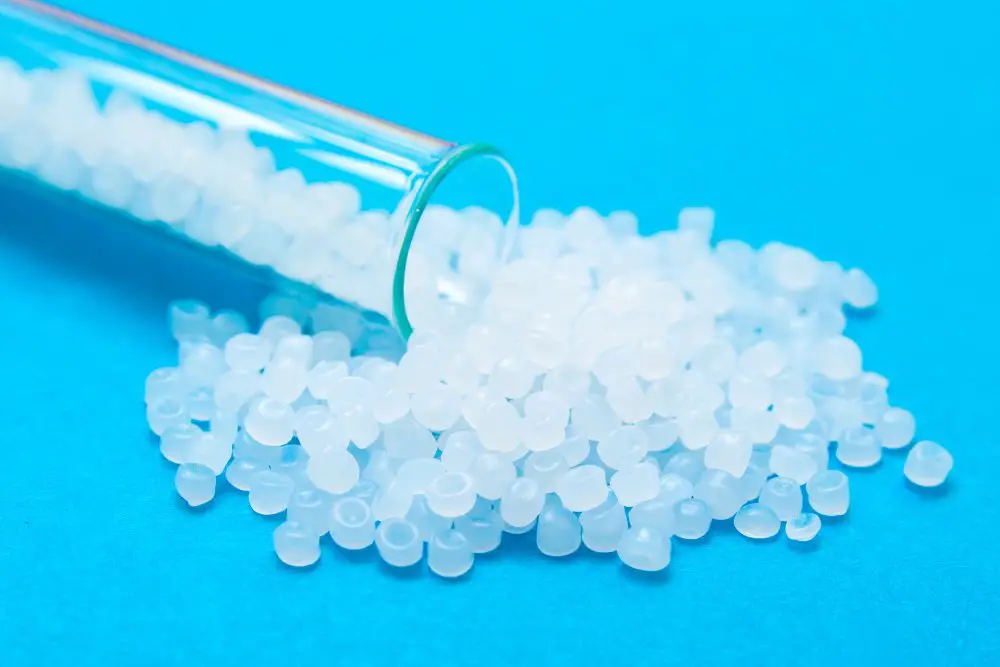
Materials chosen for the molding process significantly influence tonnage requirements. Softer materials, such as polyethylene, require less tonnage compared to harder ones like polystyrene.
The part’s design, including its thickness, is another factor. Thin-walled parts necessitate less force, hence less tonnage, than thick-walled ones.
Projected area, being the total surface area of the part that touches the mold during the process, also matters. A larger projected area demands a higher tonnage.
Runner system, whether it’s a hot or cold type, plays a key role. Hot runner systems generally lower the tonnage requirement by reducing the effective part size.
The gating location is another determinant. Parts with edge gating require less tonnage compared to those with center gating.
Ambient conditions, such as the temperature and moisture in the air, can subtly affect the behavior of materials, thus influencing tonnage.
Lastly, molding processes differ. For instance, foam molding requires less tonnage than standard injection molding as it exerts less back pressure on the clamp due to the gaseous nature of the blow agent.
Procedure in Calculating Injection Molding Machine Tonnage
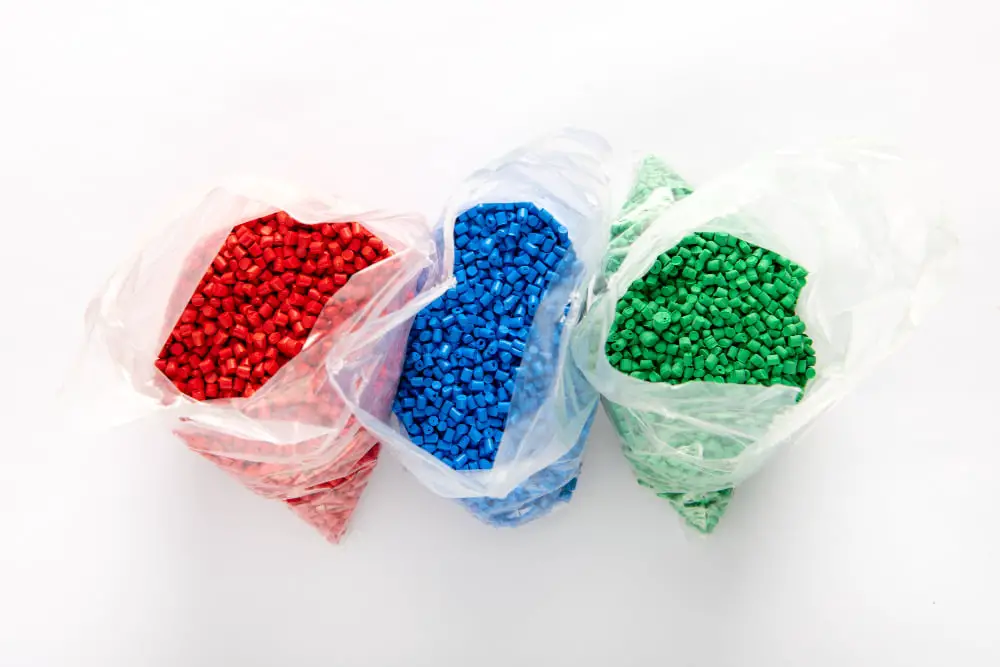
The process begins by determining the projected area of the part being molded. This area is obtained by taking the footprint measurement and multiplying the length times width. For irregularly shaped parts, employ a simplified 2D representation when calculating area.
Second is considering material selection. Every plastic material comes with its specific maximum allowable clamp force, usually defined in tons per square inch. Polystyrene, for instance, requires 5-6 tons per square inch, while a larger force, say 8-10 tons per square inch, is required for materials like ABS or nylon.
Third, you multiply the projected area of your part by the maximum allowable clamp force of the material. This will give you a tonnage need for the total projected area of the mold.
An essential step is factoring in the number of cavities in the mold. If you plan to mold more than one part at a time, the resultant tonnage estimate should be multiplied by the number of cavities.
The next step is to incorporate safety measures into your computations. It’s crucial to add a 10% safety factor, meaning 10% of the tonnage result is added to the overall figure. This is to cater to any unforeseen pressures during the molding cycle.
Lastly, bear in mind that real-life practice might necessitate adjustments. Adjustments might be warranted due to differing pressures along the mold thickness or unique molding parameters. Real-world practice will help refine the tonnage needed round by round, getting it as accurate as possible.
Using a Clamp Tonnage Calculator Effectively
Clamp tonnage calculators offer an efficient method to estimate the tonnage required for an injection molding process. They incorporate critical information such as material used, surface area of the part, and mold cavity pressure to provide a ballpark figure.
There are several key points to consider when using these calculators:
- Input validation: Ensure all the information provided, such as part size, number of cavities, and material type, is accurate. Incorrect data can lead to flawed results.
- Material selection: Different materials require different pressures. It is essential to choose the specific material from the calculator’s database accurately.
- Importance of part’s surface area: The calculator will require the total surface area of the part being molded. This significantly influences the clamp force requirements.
- Maximum pressure: Most calculators come with a standard maximum pressure setting for plastic injection molding. While this is a general guideline, it’s advisable to check with the supplier for material-specific pressure limits.
- Understand the results: When the calculator provides the estimated tonnage, do not consider this as the exact value. Always adjust based on your machine and material specifications for optimal results.
The aim is straightforward application of these principles, which should proven instrumental in using a clamp tonnage calculator effectively.
Understanding Common Errors in Tonnage Calculation
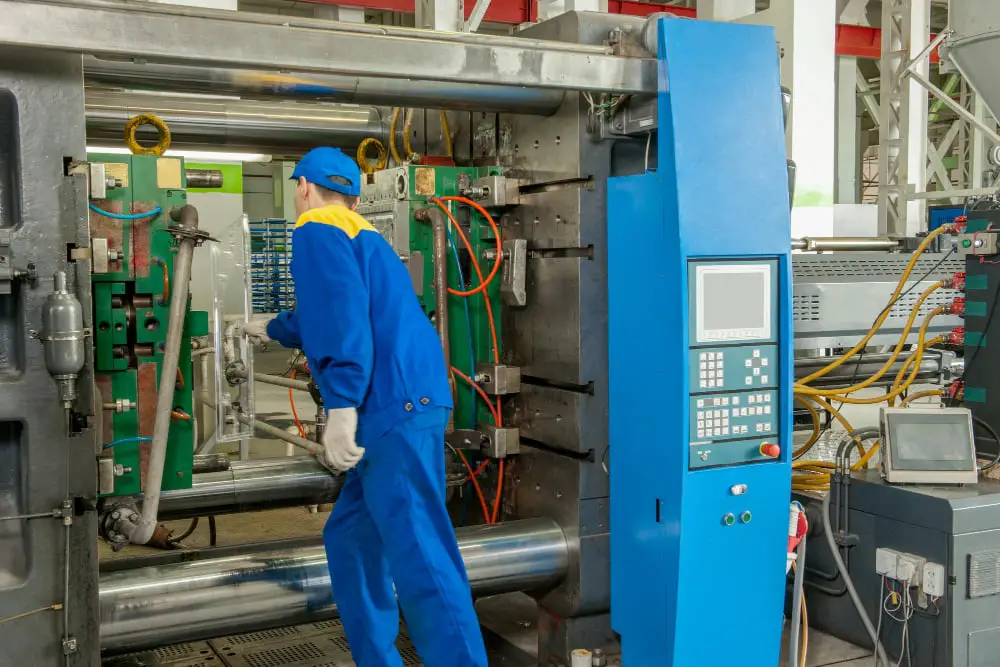
Common errors encountered during tonnage calculation fall mostly into three categories:
Overestimation or underestimation of the molding area can lead to a significant miscalculation of required tonnage. This typically happens when the part’s size and thickness are not accurately factored into the calculation. It’s crucial to precisely measure the projected area, consider wall thickness and incorporated any variations of the mold design into the calculation.
Not considering the type of plastic material used is another frequent mistake. Various materials require different amounts of pressure for successful injection molding. For instance, some plastics are stiffer and necessitate higher pressure, which would increase the tonnage requirement of your injection molding machine. It’s imperative to determine the exact type of plastic material and its specific injection pressure before calculating the tonnage.
Ignoring the effects of mold temperature on the molding process is a third common error. A higher mold temperature would reduce the plastic’s viscosity, lowering tonnage requirements, and vice versa. Regularly monitoring and controlling the mold temperature is equally important to obtaining a precise tonnage calculation.
The key to avoiding these common errors is incorporating all of these factors – your material’s characteristics, mold temperature, and precise projected area, including any variations in the mold design – into your tonnage calculation.
Effects of Incorrect Tonnage Calculation On Mold Longevity and Product Quality
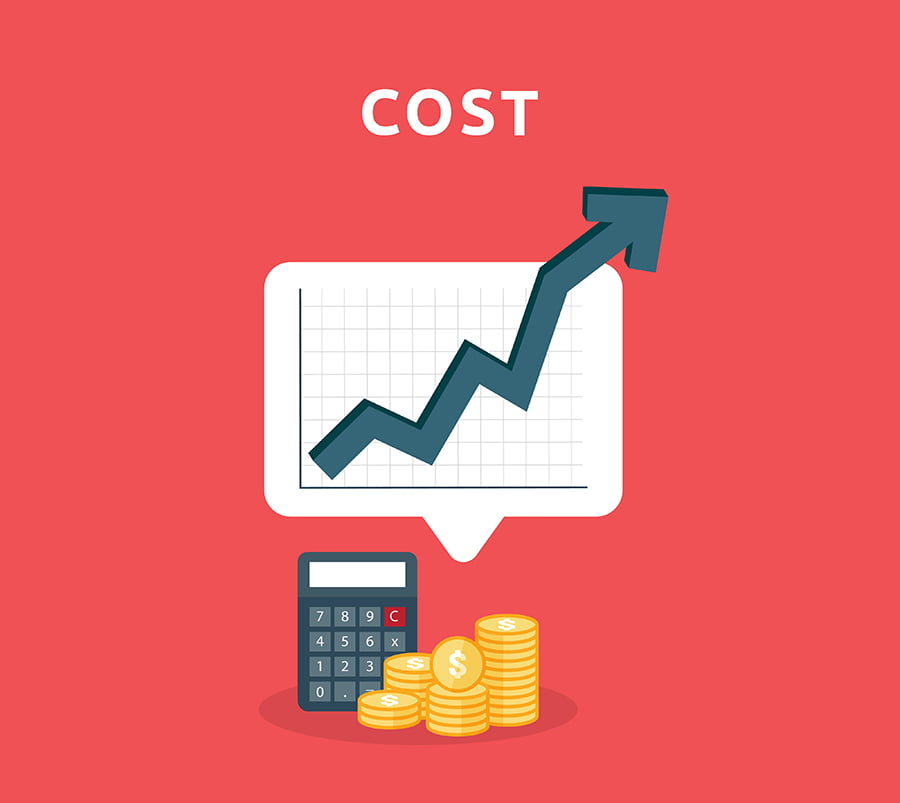
Excessive tonnage application can lead to over-clamping, which inadvertently stresses the mold, causing early wear and tear. Mold life reduces significantly with this unneeded strain. Not only will replacement cost increase, but repeated mold purchasing also leads to additional downtime and productivity loss.
A feebler tonnage application might lead to under-clamping, leading to inadequate mold closure. It causes an undesirable phenomenon called “flashing”. Here, polymer melt squeezes into the mold’s parting line, creating thin, unattractive “flaps” on the final product, damaging the material aesthetically and structurally.
Incorrect tonnage can thus impact the polymer filler dispersion within the product. Underfilling and overfilling both can cause inconsistencies in wall thickness or formation of brown streaks, affecting the final product quality.
The performance of molded parts can be impaired by incorrect tonnage, leading to reduced part strength and stability. It can also affect the part’s resilience, causing early failure in its function.
Next, the process of correction becomes time-consuming and costly. Once an incorrect tonnage problem is detected, molders need several runs and a lot of material wastage to correct the issues – iterations that could have been avoided with precise tonnage from the beginning.
Lastly, incorrect tonnage may cause an increase in the required cooling time, consequently slowing down the production speed and hampering the overall manufacturing efficiency.
In each of these instances, the importance of precision in calculating and applying the correct tonnage in injection molding is acutely felt, underscoring the urgent need for comprehensive understanding and accurate execution of the process.
FAQ
How do you calculate the capacity of an injection Moulding machine?
To calculate the capacity of an injection moulding machine, use the formula mass divided by density, for instance, if the machine screw diameter is 28mm, the material density is 1.52g/cm3 (for PVC material), with a screw weight of 40.6g, the shot size or machine shot capacity would be 43.4mm.
What is the tonnage capacity of injection molding machine?
The tonnage capacity of an injection molding machine is typically 200 tons, factoring in a 10% safety factor to a base capacity of 180 tons.
What is the formula for tonnage calculation?
The formula for tonnage calculation is GT = K1V, where GT represents the gross tonnage, K1 is a constant calculated as K1 = 0.2 + 0.02 log10 V, and V stands for the volume of a ship’s enclosed spaces measured in cubic metres.
How many tons per square inch for injection molding?
The necessary tonnage for injection molding typically ranges from 2 to 4 tons per square inch of projected area.
How does the size of the mold affect the tonnage needed in an injection molding machine?
The size of the mold in an injection molding machine directly influences the required tonnage, with larger molds necessitating higher tonnage to ensure adequate force is applied to keep the mold closed during the injection process.
What factors influence the tonnage calculation for an injection molding machine?
The tonnage calculation for an injection molding machine is influenced by factors such as the projected area of the component, the resin characteristics, the number of molds, and the maximum allowable injection pressure of the machine.
How does material choice impact the required tonnage of an injection molding machine?
The material choice impacts the required tonnage of an injection molding machine as it determines the necessary clamping force, with stiffer materials needing higher tonnage machines due to their higher injection pressure requirements.
Recap