Discover the fascinating world of plastics as we delve into various types and their versatile uses, transforming industries and our daily lives.
Plastics have become an essential part of our daily lives, and it’s hard to imagine a world without them. They are used in everything from packaging materials to construction products.
However, not all plastics are created equal. There are different types of plastics with varying properties that make them suitable for specific applications.
In this blog post, we will explore the different types of plastics and their uses in various industries. So whether you’re curious about the plastic products you use every day or want to learn more about the versatility of these materials, keep reading!
Basic Categories of Plastic
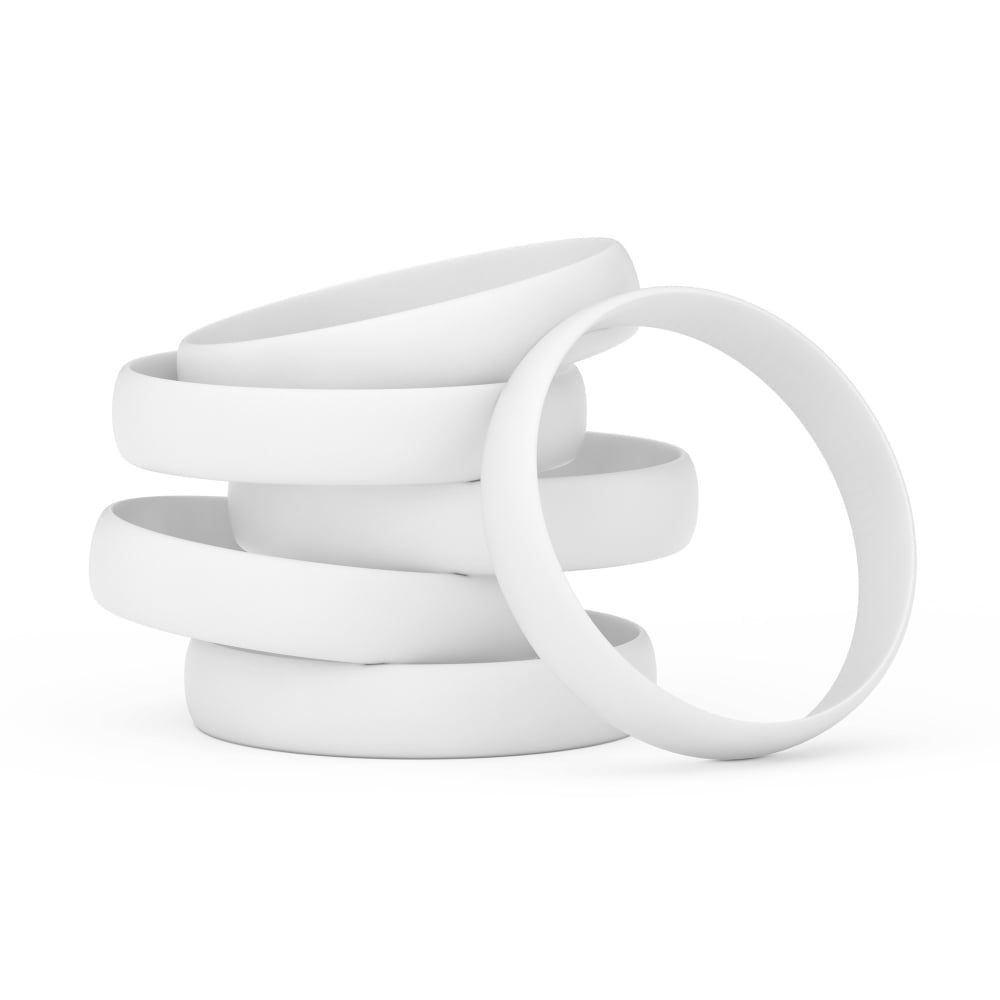
They have become an essential part of our daily lives, but not all plastics are the same. There are two basic categories of plastic: thermoplastics and thermosetting plastics.
Thermoplastics soften when heated and harden when cooled repeatedly without undergoing any chemical change in their composition. This property makes them ideal for recycling as they can be melted down multiple times to create new products.
Examples include polyethylene terephthalate (PET), high-density polyethylene (HDPE), low-density polyethylene (LDPE), polyvinyl chloride (PVC), polystyrene (PS) among others.
On the other hand, thermosetting plastics undergo a chemical reaction during processing that causes them to set permanently once they cool down after being heated once or twice; this means they cannot be re-melted or recycled easily like their counterparts above. Examples include epoxy resins, silicone rubber, acrylics/polymethyl methacrylate(PMMA) among others.
Thermoforming Plastics
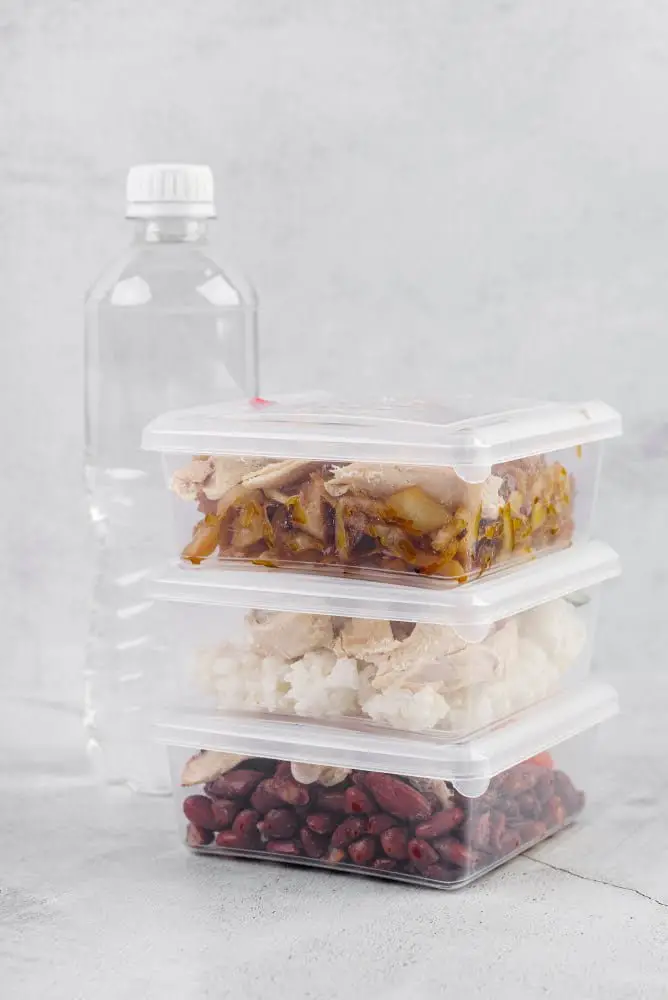
This process is commonly used in the production of packaging materials, such as trays, containers, and blister packs.
The thermoforming plastics used for this process are typically thermoplastics that can be heated and cooled multiple times without losing their properties. Some common types of thermoforming plastics include polystyrene (PS), polyvinyl chloride (PVC), polyethylene terephthalate (PET), and high-impact polystyrene (HIPS).
One advantage of using thermoformed plastics is their ability to create complex shapes with precise details at relatively low costs compared to other manufacturing processes like injection molding or blow molding.
Thermosetting Plastics
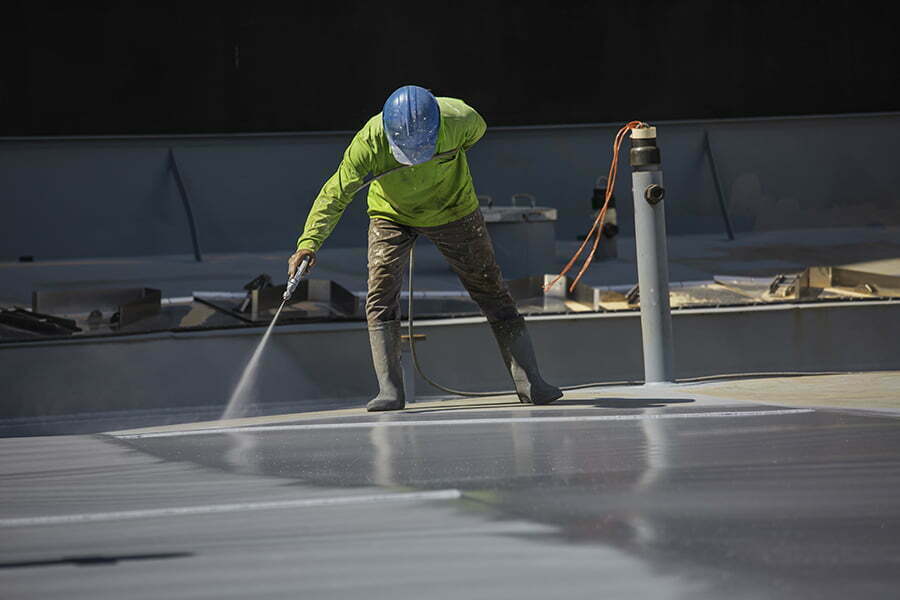
This process, known as curing, results in the formation of a rigid and durable material that cannot be melted or reshaped once it has been formed. Thermosetting plastics have excellent mechanical properties such as high strength and stiffness, making them ideal for use in applications where durability is essential.
One common example of thermosetting plastic is epoxy resin. Epoxy resins are widely used in construction materials such as adhesives, coatings, and composites due to their exceptional bonding strength and resistance to heat and chemicals.
Another example is phenolic resin which finds its application mainly in electrical components like circuit boards because it can withstand high temperatures without melting or degrading.
Thermoset plastics also offer superior dimensional stability compared to other types of polymers since they do not shrink during the curing process. This property makes them suitable for manufacturing precision parts with tight tolerances required by industries like aerospace engineering.
Polyethylene Terephthalate (PET)
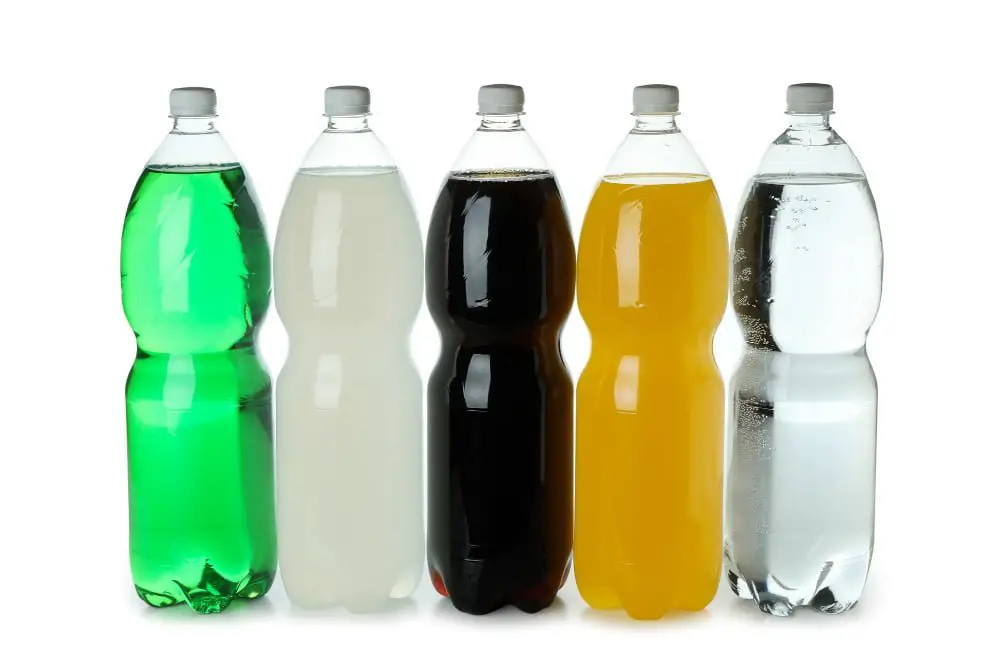
It’s lightweight, durable, and has excellent clarity, making it an ideal material for water bottles and food containers. PET can also be recycled multiple times without losing its quality or strength.
Apart from being used in the packaging industry, PET has other applications such as textiles manufacturing where it’s spun into fibers to make fabrics like polyester. The medical field also uses PET to create equipment like MRI scanners due to its non-reactive nature.
However, despite its recyclability properties which have made it popular among environmentalists worldwide; there are concerns about the safety of using this plastic for food storage purposes since some studies suggest that chemicals from plastics may leach into foods when heated or exposed to acidic substances over time.
High-Density Polyethylene (HDPE)
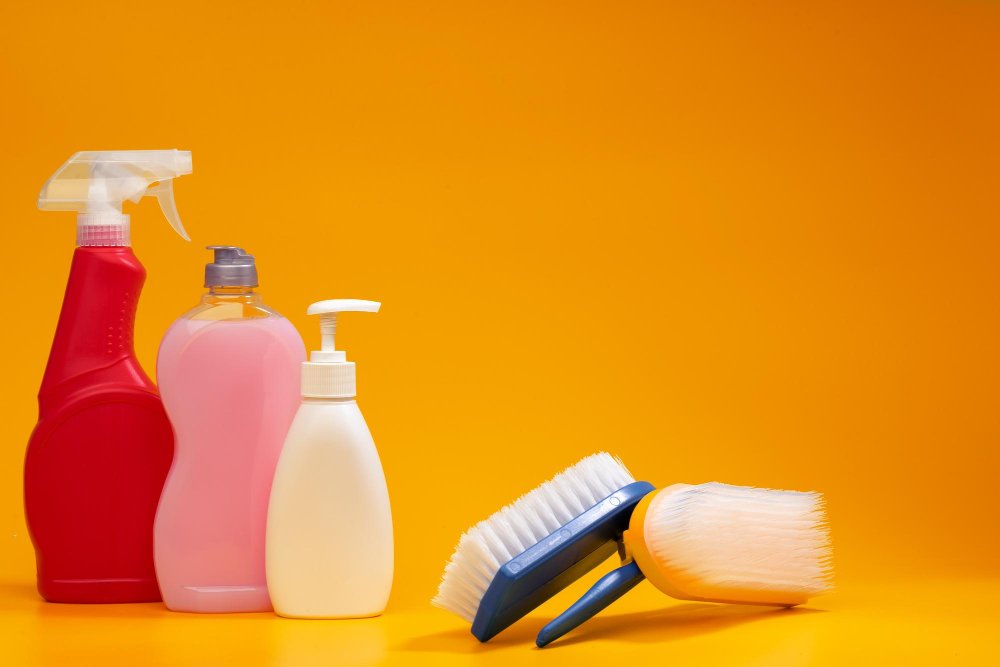
It is made from petroleum, which makes it resistant to moisture and chemicals, making it ideal for use in packaging materials such as milk jugs, detergent bottles, and food containers.
HDPE’s high strength-to-density ratio also makes it an excellent material for pipes used in water distribution systems. Its resistance to corrosion means that HDPE pipes can last up to 100 years without needing replacement.
In addition to its practical applications, HDPE is also environmentally friendly. It can be recycled into new products or repurposed into non-plastic items like lumber or park benches.
Low-Density Polyethylene (LDPE)
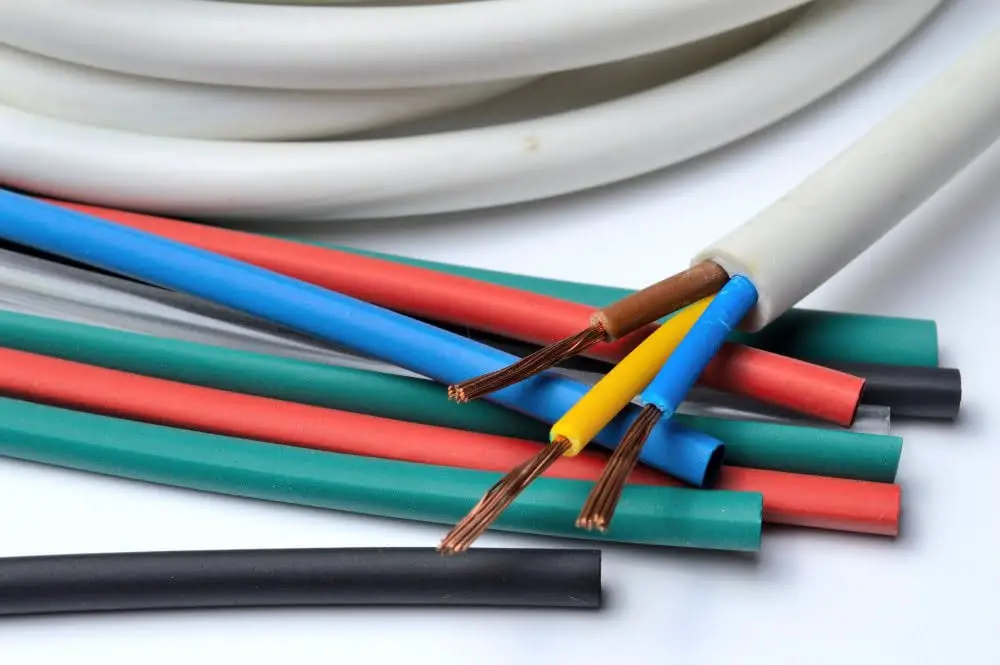
It is commonly used in packaging materials, such as plastic bags and films, due to its flexibility and transparency. LDPE can also be found in various household items like squeeze bottles, toys, and wire insulation.
One significant advantage of LDPE is its resistance to moisture. This property makes it an ideal material for products that need protection from water or humidity.
It has excellent chemical resistance properties which make it suitable for use in the food industry.
However, one downside to using LDPE is its low melting point compared to other plastics; this means that products made with this material may not withstand high temperatures without deforming or melting.
Polyvinyl Chloride (PVC)
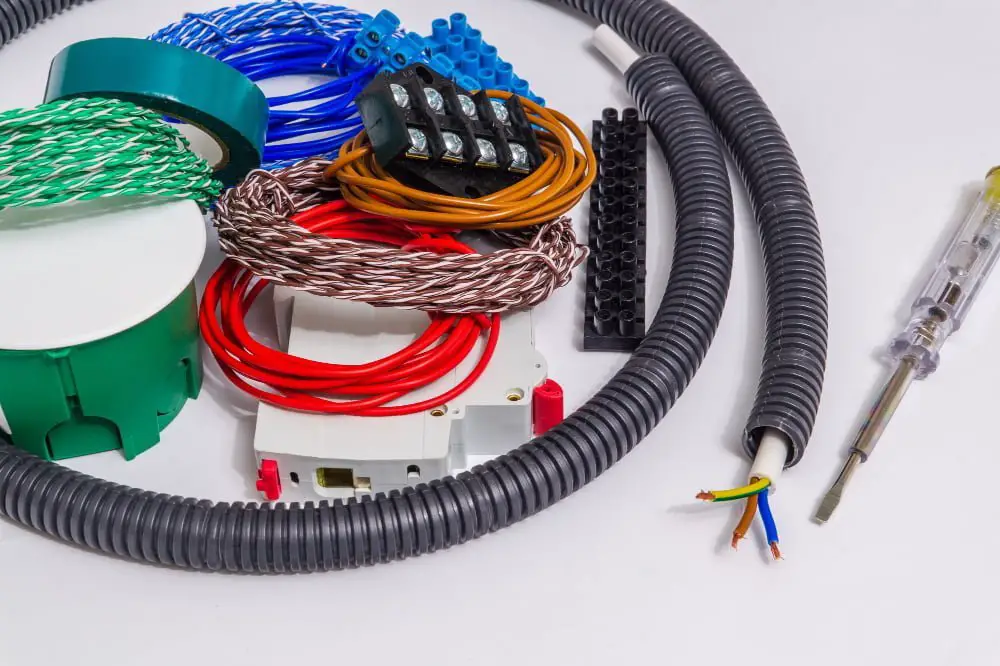
It is a thermoplastic polymer that can be easily molded and shaped, making it ideal for manufacturing pipes, electrical cables, flooring materials, and even clothing. PVC is known for its durability and resistance to chemicals and weathering.
One of the most significant advantages of PVC over other plastics is its low cost. This makes it an attractive option for manufacturers looking to produce products at scale without breaking the bank.
PVC’s versatility means that it can be formulated with different additives to enhance specific properties such as flexibility or flame retardancy.
However, despite being widely used in many applications due to its affordability and versatility; there are concerns about the environmental impact of PVC production as well as disposal after use since they do not degrade quickly like some other plastics.
Polypropylene (PP)
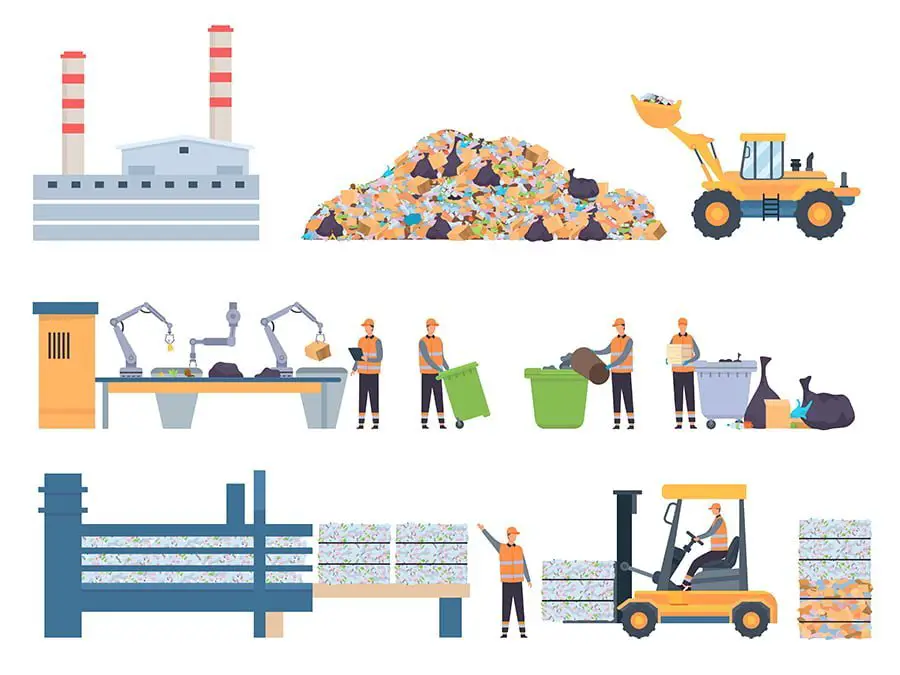
It is used in various applications, including packaging materials, automotive parts, toys, and medical devices. PP has excellent resistance to fatigue and impact as well as high melting point which makes it ideal for use in products that require durability.
One of the most significant advantages of PP is its recyclability. It can be recycled multiple times without losing its properties or quality.
This makes it an eco-friendly option compared to other plastics that are not easily recyclable.
Another advantage of polypropylene is its ability to withstand high temperatures without deforming or melting; this property makes it suitable for use in microwave-safe containers and dishwasher-safe products.
Polystyrene (PS)
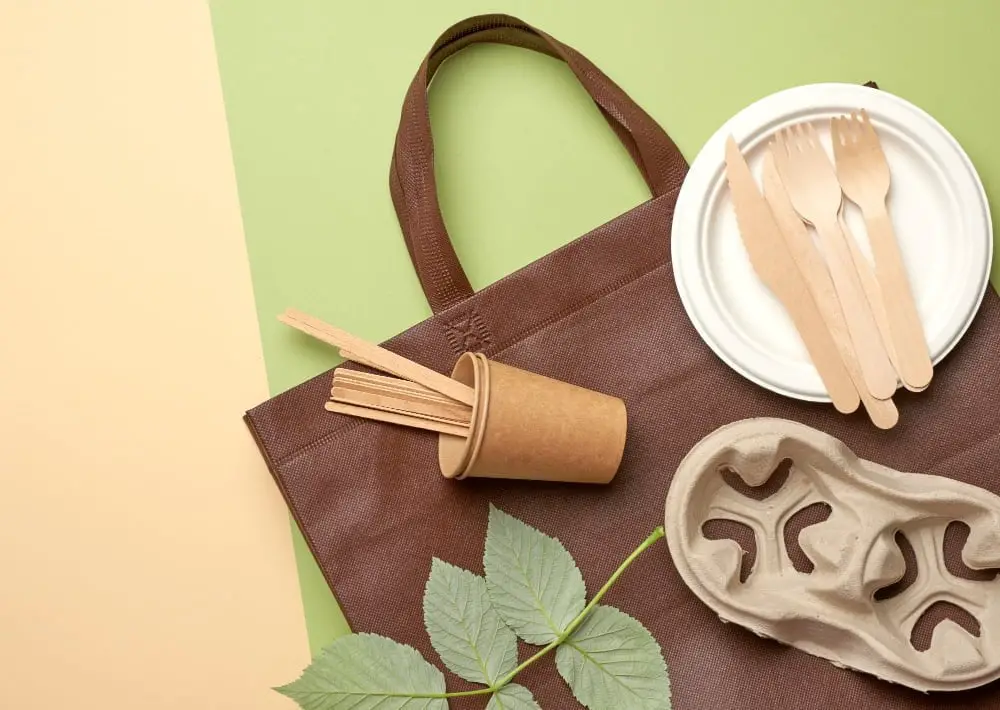
It is a lightweight, rigid, and transparent plastic that has excellent insulation properties. Polystyrene can be easily molded into different shapes and sizes, making it ideal for use in various applications.
One of the most common uses of polystyrene is in packaging materials such as foam cups, food containers, and packing peanuts. Its insulating properties make it an excellent choice for keeping food hot or cold during transportation.
Polystyrene also finds its application in the construction industry as insulation material due to its thermal resistance property. It’s used to insulate walls and roofs of buildings to reduce heat loss during winter months while keeping them cool during summer months.
Polycarbonate (PC)
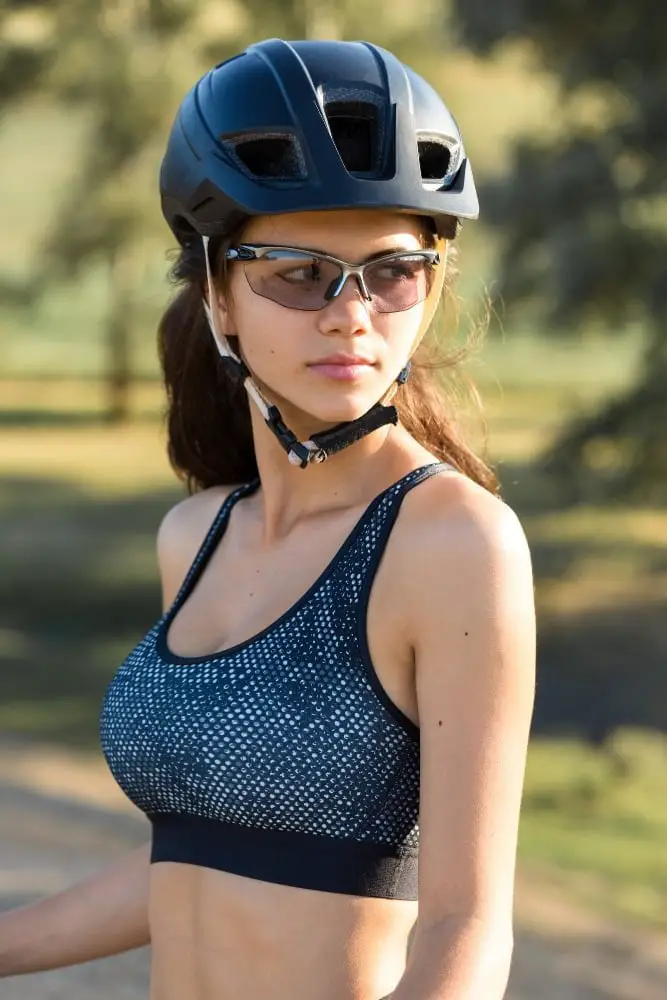
It is commonly used in applications where safety and durability are essential, such as bulletproof windows, eyewear lenses, electronic components, medical devices, and automotive parts.
One of the unique properties of polycarbonate is its ability to withstand extreme temperatures without breaking or deforming. This makes it an ideal material for use in harsh environments where other plastics would fail.
Another advantage of polycarbonate over other plastics is its optical clarity. It allows up to 90% light transmission while maintaining superior strength compared to glass or acrylic materials.
In addition to being strong and transparent, polycarbonate also offers good electrical insulation properties making it suitable for use in electrical equipment like switches or connectors.
Despite all these advantages offered by Polycarbonates there are some concerns about their environmental impact due to the presence of Bisphenol A (BPA), which can leach out from PC products into food items causing health issues if ingested regularly over time. However new BPA-free versions have been developed recently which address this issue effectively.
Acrylonitrile Butadiene Styrene (ABS)
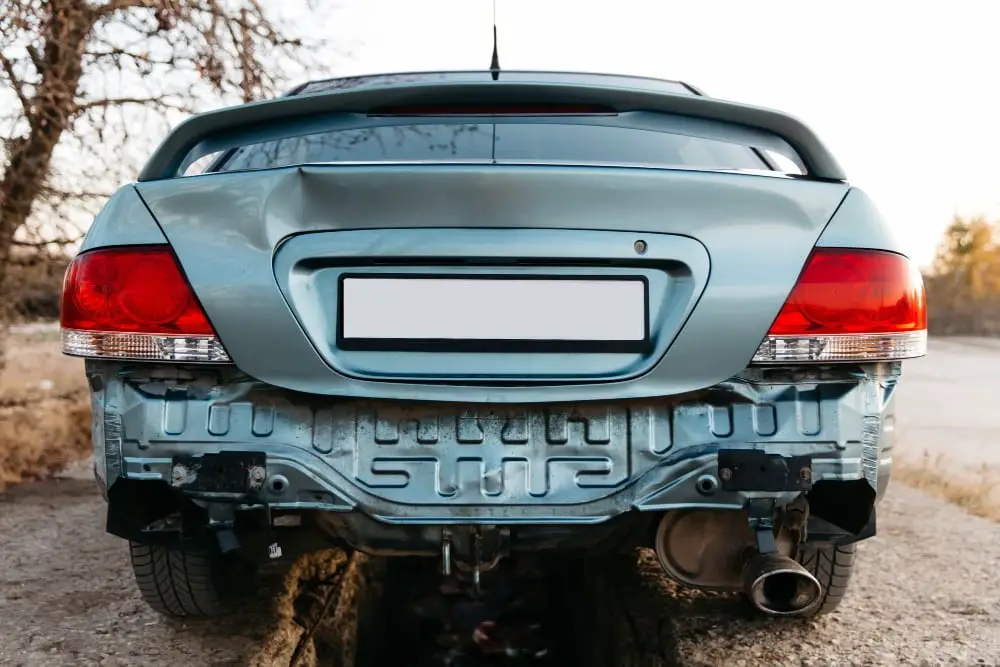
It’s a combination of three monomers, acrylonitrile, butadiene, and styrene. ABS has excellent impact resistance and toughness even at low temperatures making it ideal for applications where durability is essential.
ABS plastic can be easily molded into different shapes using injection molding or extrusion techniques. Its versatility makes it suitable for use in the automotive industry to manufacture car bumpers, dashboard trims as well as interior parts such as door panels.
In addition to its use in the automotive industry, ABS plastic also finds application in consumer electronics such as computer keyboards and housings for printers due to its high strength-to-weight ratio.
One of the significant advantages of ABS over other plastics like polycarbonate (PC) or polyvinyl chloride (PVC) is that it can be easily modified by adding fillers or additives without affecting its properties significantly. This property makes ABS an attractive option when manufacturers need specific characteristics from their products while maintaining affordability.
Polyamide (PA)
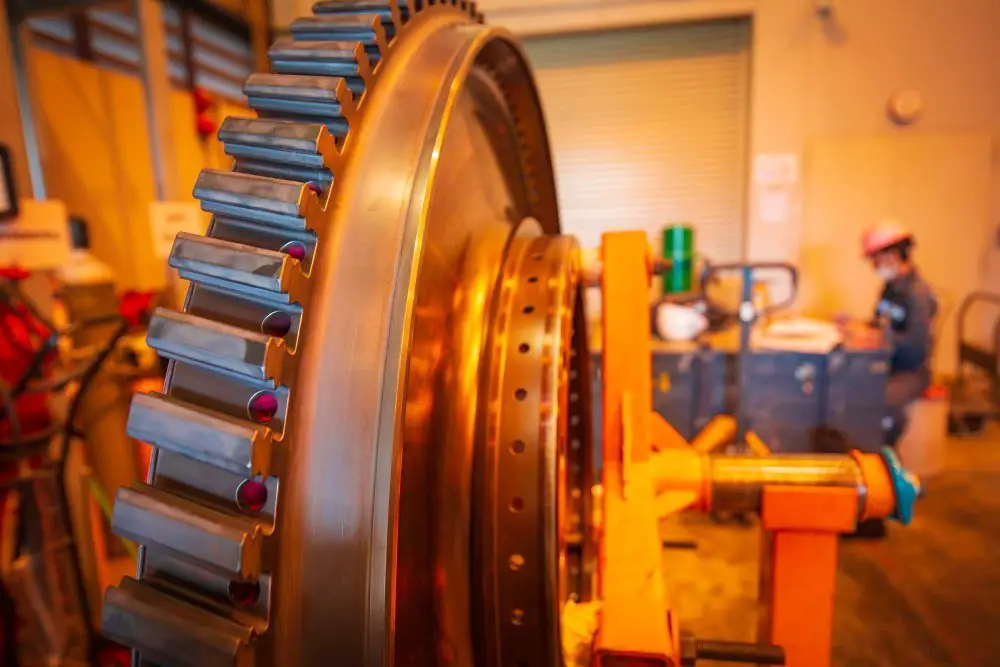
It’s commonly used in the production of textiles, automotive parts, electrical components, and industrial machinery. Polyamides are also known as nylon due to their use in the production of synthetic fibers.
One significant advantage of polyamide plastics is their ability to withstand high temperatures without losing their mechanical properties. This makes them ideal for use in applications where heat resistance is essential.
Another benefit of polyamides is that they have excellent chemical resistance against oils and solvents. They are also resistant to abrasion which makes them suitable for manufacturing gears or bearings.
In addition to these benefits mentioned above PA has some disadvantages too such as it absorbs moisture easily which can lead it towards swelling or warping if not handled properly during processing.
Polyurethane (PU)
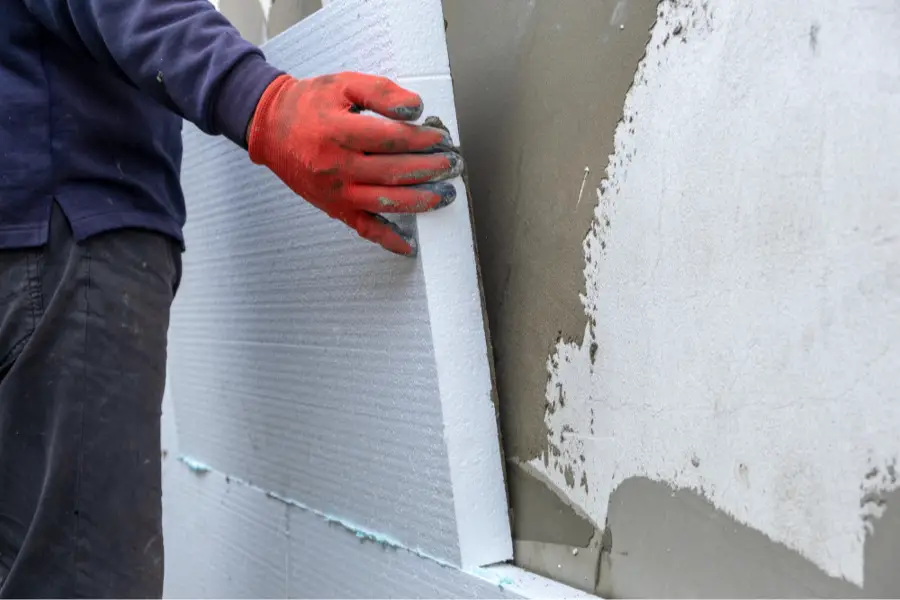
It is made by reacting diisocyanates with polyols, which results in a material that can be rigid or flexible depending on the formulation. PU foam, for example, is used in furniture cushions and insulation materials due to its excellent thermal insulation properties.
In construction applications, PU coatings are used as waterproofing agents for roofs and foundations. They provide an effective barrier against water penetration while also being resistant to UV radiation and weathering.
In the automotive industry, PU foam is commonly used in car seats due to its ability to absorb impact energy during collisions. It can be molded into various shapes making it ideal for use as dashboards or door panels.
One of the most significant advantages of Polyurethane (PU) plastics over other types of plastics lies in their durability and resistance to abrasion making them suitable for industrial applications such as conveyor belts or rollers where wear resistance plays an important role.
Epoxy Resins
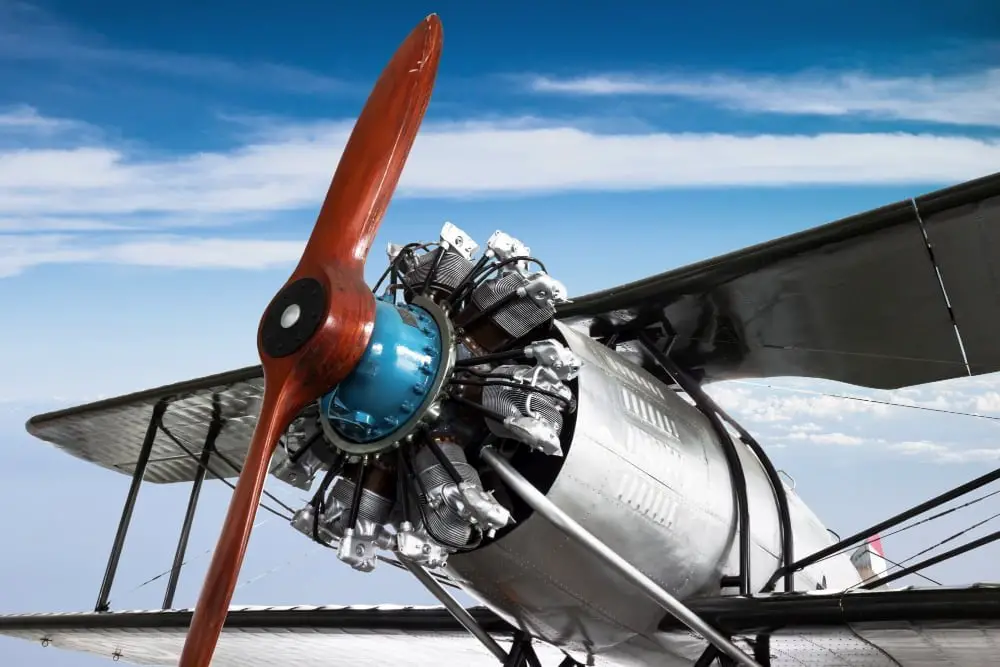
They are known for their excellent adhesive properties and high strength-to-weight ratio. Epoxy resins consist of two components – the resin and the hardener – which must be mixed together before use.
Once mixed, epoxy resin can be applied to various surfaces such as metal, wood or concrete to create a strong bond that is resistant to water and chemicals. It can also be used as a coating material for floors or countertops due to its durability.
One significant advantage of using epoxy resins is their ability to withstand extreme temperatures without losing their structural integrity. This makes them ideal for use in aircraft parts where they need to withstand high altitudes or engine components where they need resistance against heat.
However, it’s essential always follow safety precautions when working with epoxy resin since it contains harmful chemicals that may cause skin irritation if not handled properly. Epoxy Resin has become an indispensable material in many industries due its unique properties such as adhesiveness ,strength-to-weight ratio ,and temperature resistance.
Silicone Rubber
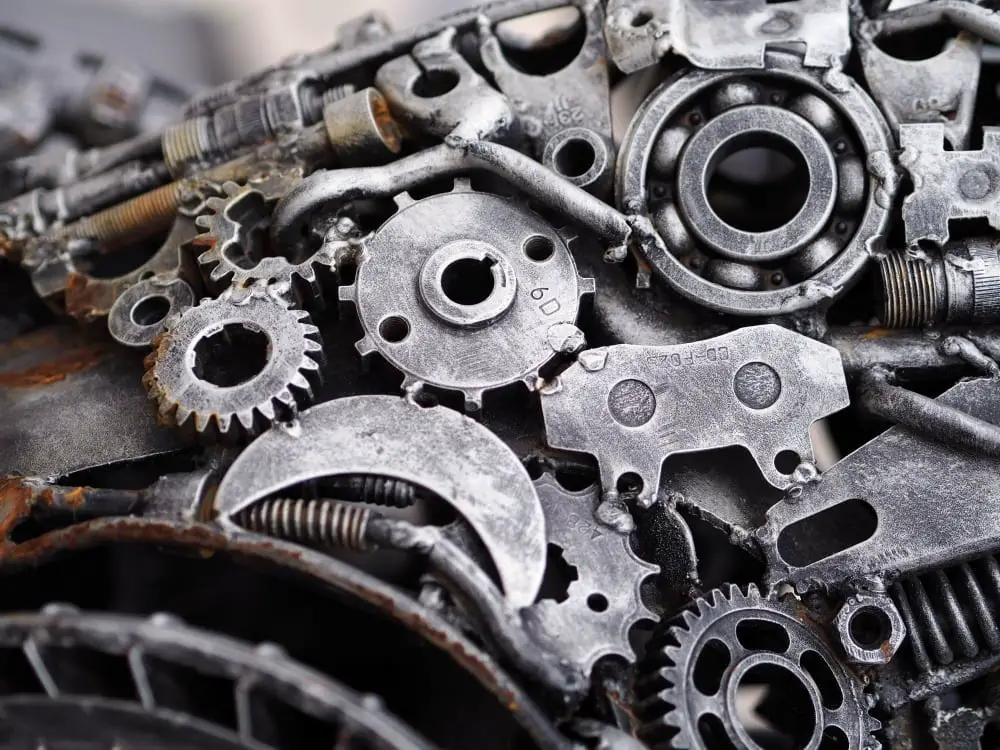
It is used in various applications where flexibility and durability are required. Silicone rubber can withstand extreme temperatures ranging from -55°C to 300°C without losing its properties or breaking down.
One of the most common uses of silicone rubber is in the manufacturing of gaskets and seals for automotive engines. The material’s ability to resist heat makes it ideal for use in engine components such as valve covers, oil pans, water pumps, and thermostats.
In addition to automotive applications, silicone rubber also finds use in medical devices due to its biocompatibility with human tissue. It can be molded into different shapes and sizes while maintaining its strength even after prolonged exposure to body fluids or sterilization processes.
Another application area for silicone rubbers includes electrical insulation materials because they have good dielectric properties over a wide range of frequencies making them suitable for insulating wires & cables as well as electronic components like capacitors & transformers.
Acrylic or Polymethyl Methacrylate (PMMA)
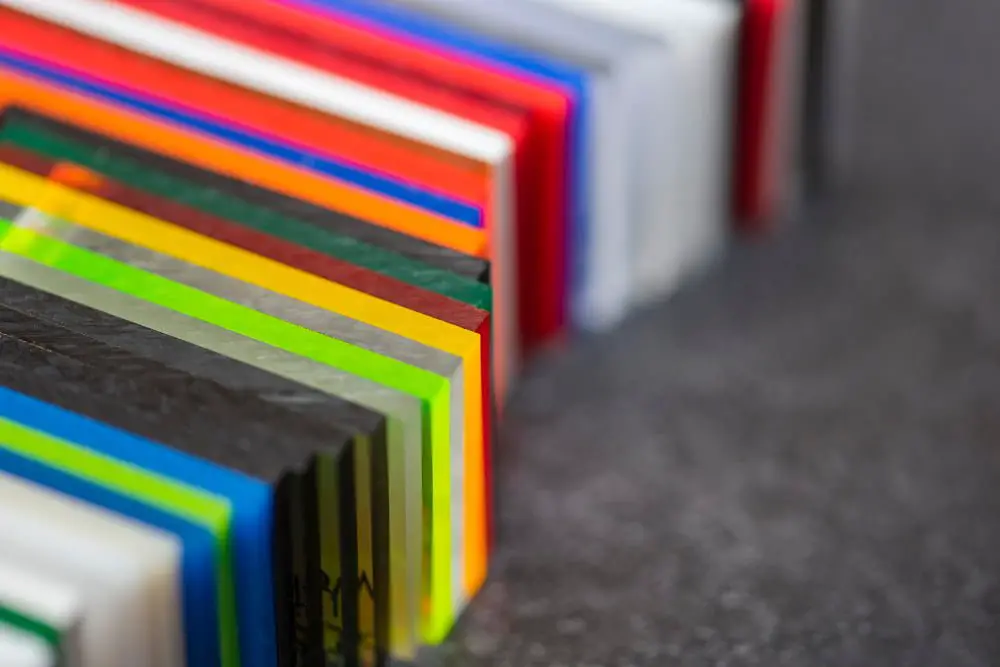
It is commonly used in the production of lenses, signs, displays, and lighting fixtures. PMMA can also be colored to produce vibrant hues for various applications.
One of the most significant advantages of PMMA over glass is its impact resistance. Acrylic sheets are much more durable than glass and less likely to break upon impact.
This makes it an ideal material for use in areas where safety concerns are paramount.
Another advantage of acrylics over other plastics such as polycarbonate (PC) is their UV stability; they do not yellow or become brittle when exposed to sunlight like some other plastics do.
PMMA’s versatility extends beyond traditional uses such as signage and display cases; it can also be found in automotive parts, medical devices, aquariums, furniture pieces like chairs & tables among others due to its durability properties.
Types of Plastic & Their Applications

Each type of plastic has unique properties that make it suitable for specific uses. For example, Polyethylene Terephthalate (PET) is commonly used in the production of water bottles and food containers due to its transparency and resistance to impact.
High-Density Polyethylene (HDPE), on the other hand, is often used for pipes and fittings because it can withstand high temperatures and pressures.
Polyvinyl Chloride (PVC) is another popular plastic with diverse applications such as electrical cable insulation, window frames, flooring tiles among others due to its durability and low cost.
Polystyrene(PS), which comes in two forms: expanded polystyrene(EPS) or extruded polystyrene(XPS), finds use as thermal insulation material while Acrylonitrile Butadiene Styrene(ABS) plastics are widely employed in automotive parts manufacturing because they have excellent mechanical strength.
Types of Plastic & Their Recycle Codes
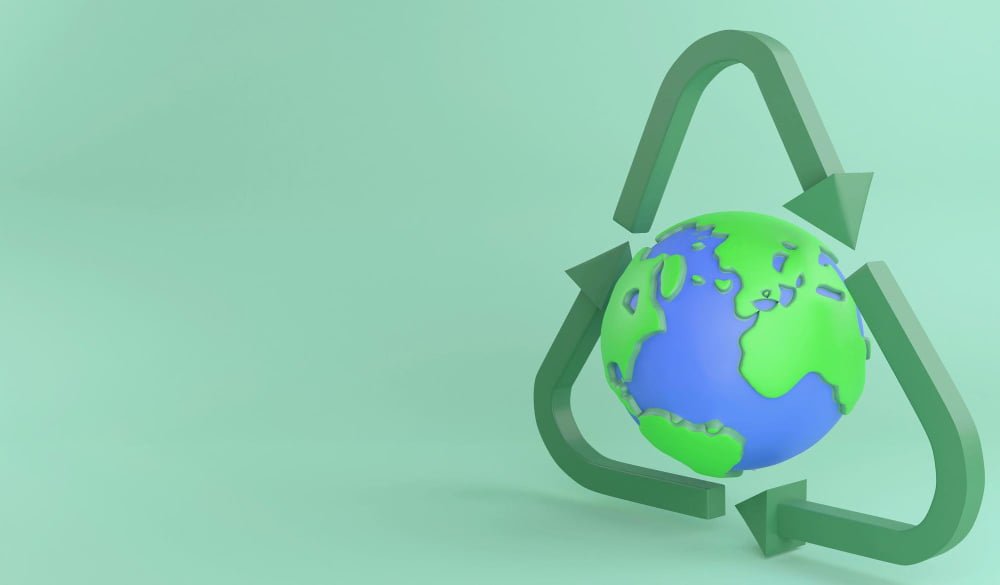
It helps to reduce the amount of plastic waste that ends up in landfills and oceans, conserves natural resources, and reduces greenhouse gas emissions. However, not all plastics are recyclable or recycled equally.
To make recycling easier and more efficient, the Society of Plastics Industry (SPI) developed a coding system for different types of plastics known as recycle codes or resin identification codes (RIC). These codes are usually found on the bottom or side walls of plastic products inside a triangle made up arrows with numbers from 1-7.
Each code represents a specific type or family group based on its chemical composition. For instance:
- Code 1: Polyethylene Terephthalate (PET)
- This type is commonly used for water bottles; it’s lightweight but strong enough to hold liquids without leaking.
- Code 2: High-Density Polyethylene (HDPE)
- It’s used in milk jugs because it can withstand high temperatures without melting.
- Code 3: Polyvinyl Chloride(PVC)
- PVC is often found in pipes due to its durability against chemicals like acids and bases
- The other four most common types include Low-Density Polyethylene(LDPE),Polypropylene(PP), Polystyrene(PS),and Other which includes polycarbonate(PC) among others
Biodegradable Plastics
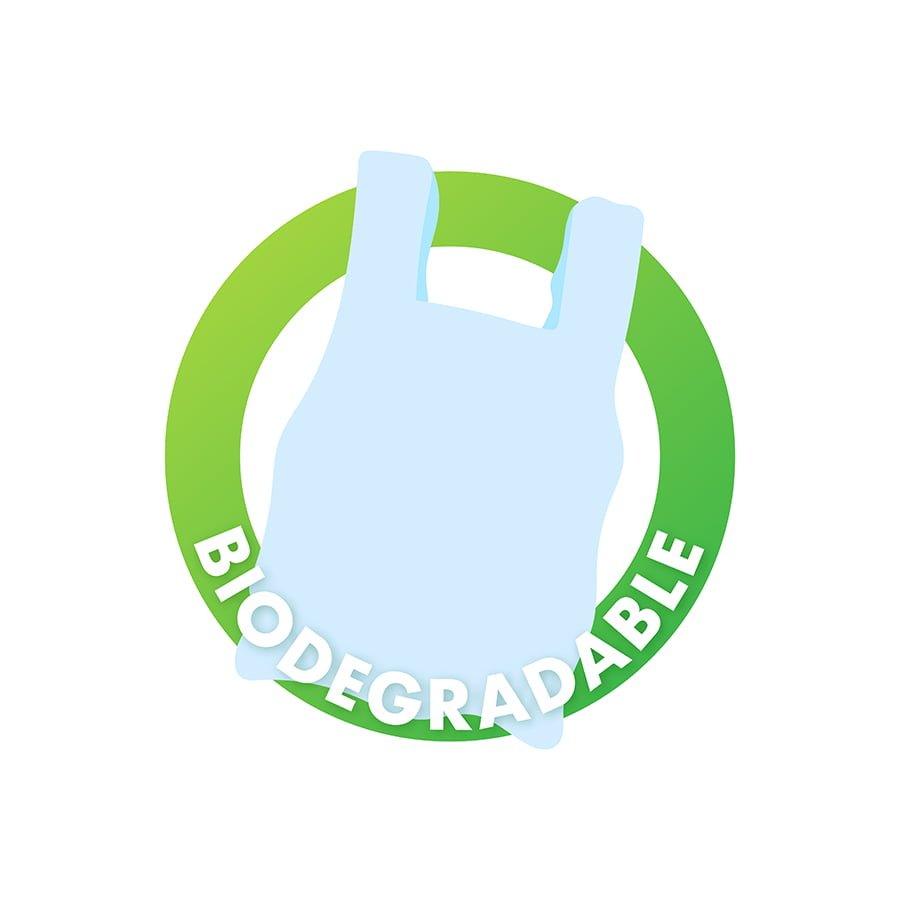
These plastics can be broken down by microorganisms into natural substances such as water, carbon dioxide, and biomass. Biodegradable plastics are made from renewable resources like corn starch or vegetable oil instead of petroleum-based products.
One significant advantage of biodegradable plastics is that they reduce the amount of waste in landfills since they break down faster than traditional plastic materials. They also have lower greenhouse gas emissions during production compared to conventional plastic manufacturing processes.
However, it’s important to note that not all biodegradable plastics are created equal. Some require specific conditions like high temperatures or humidity levels for decomposition while others may only degrade partially and leave behind harmful microplastics.
Despite these limitations, the development and use of biodegradable plastics offer a promising solution towards reducing environmental pollution caused by non-biodegradables such as single-use packaging materials commonly found in our daily lives.
Recycled Plastics
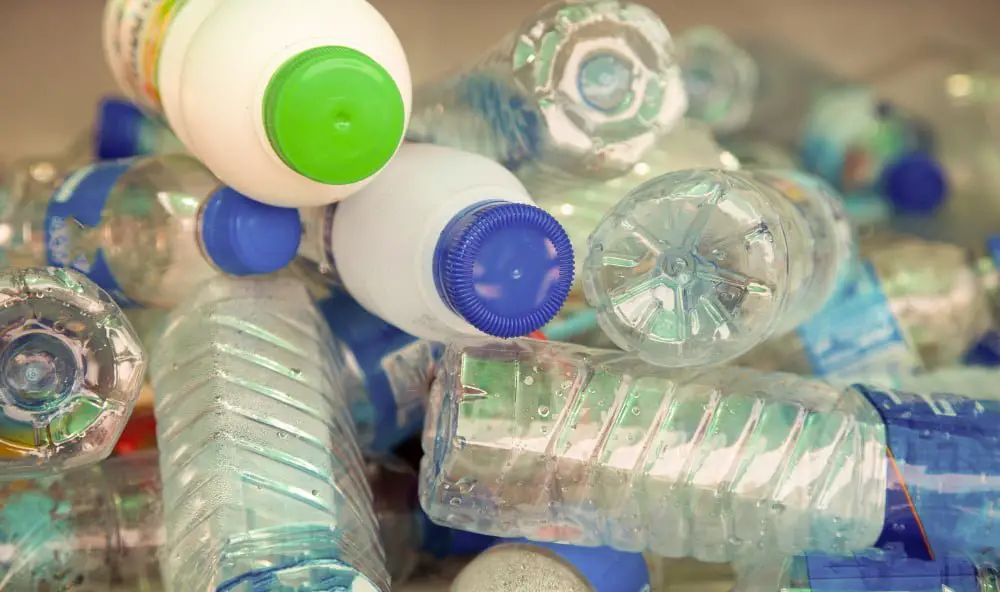
Recycling plastic helps reduce the amount of waste that ends up in landfills or oceans, conserves natural resources, and reduces greenhouse gas emissions. Recycled plastics are used to make a wide range of products such as clothing fibers, carpeting materials, furniture components and packaging materials.
The process for recycling plastic involves collecting discarded items made from specific types of plastic (usually identified by their recycle codes), cleaning them thoroughly before shredding into small pieces called flakes. These flakes are then melted down into pellets which can be used in manufacturing new products.
One significant advantage of using recycled plastics is that they require less energy to produce than virgin plastics since the material has already been processed once before. Recycling helps conserve non-renewable fossil fuels like oil which would otherwise be required for producing new virgin plastic.
However not all types of recycled plastics have equal quality; some may lose their strength or durability during the recycling process making them unsuitable for certain applications such as food packaging where hygiene standards must be met.
Plastic Additives
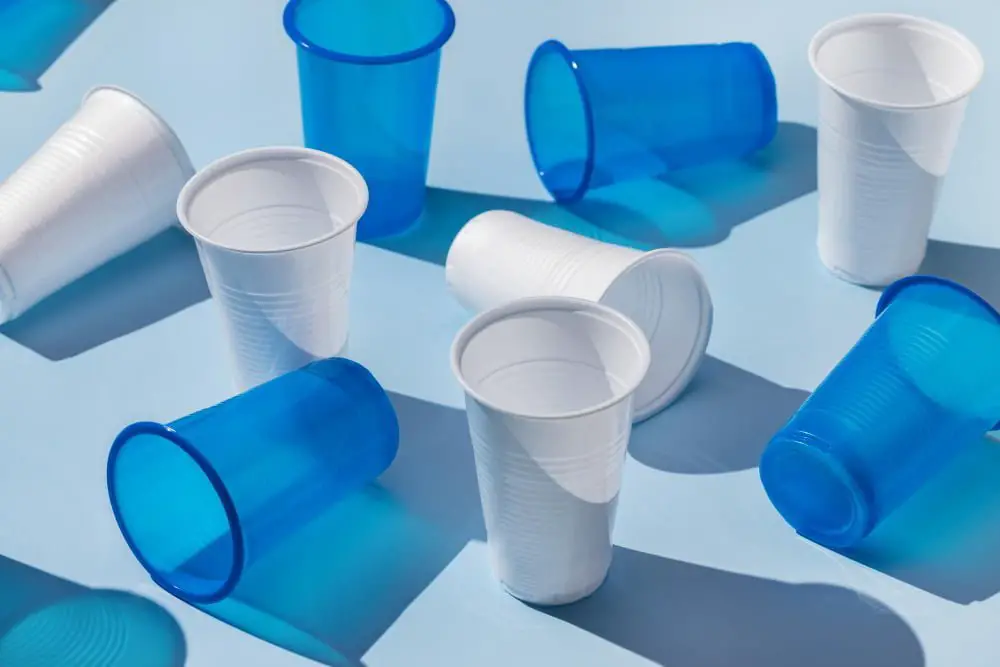
They can enhance the strength, durability, flexibility, and appearance of plastic products. Some common types of additives include stabilizers that protect against degradation from heat and UV light; plasticizers that increase flexibility; flame retardants that reduce flammability; colorants for aesthetic purposes, and antimicrobial agents for hygiene applications.
However, some additives have raised concerns about their potential health effects on humans and the environment. For example, bisphenol A (BPA), a chemical used in polycarbonate plastics found in food containers and water bottles has been linked to hormonal imbalances.
To address these concerns manufacturers are developing safer alternatives such as BPS (bisphenol S) which is less harmful than BPA but still provides similar benefits.
Plastic additives play an essential role in enhancing the properties of different types of plastics used across various industries.
Plastic Packaging
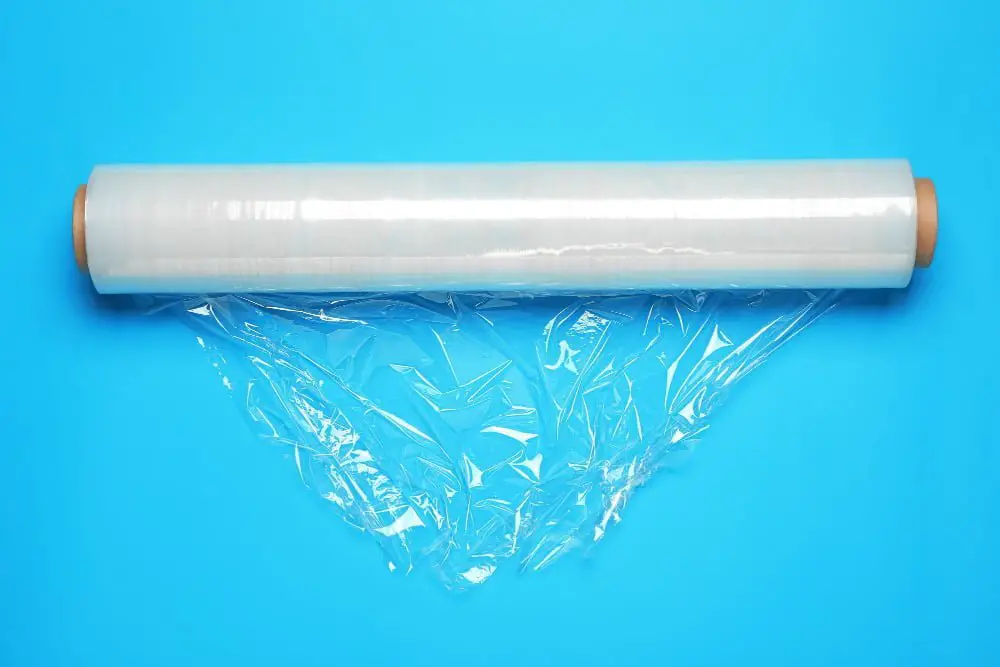
It’s used to package everything from food and beverages to cosmetics and household products. Plastic packaging has many advantages, including its durability, flexibility, and ability to be molded into different shapes.
However, plastic packaging also has its downsides. One major issue is that it contributes significantly to plastic waste pollution in our environment.
Single-use plastics like bags and straws are particularly problematic as they often end up in landfills or oceans where they can take hundreds of years to decompose.
To address this problem, there have been efforts by governments around the world towards reducing single-use plastics through bans or taxes on their use while encouraging more sustainable alternatives such as reusable containers made from glass or metal.
Some companies are exploring innovative ways for creating biodegradable plastic materials that break down naturally without harming the environment while still maintaining their functionality as a reliable form of packaging material.
Medical Plastics
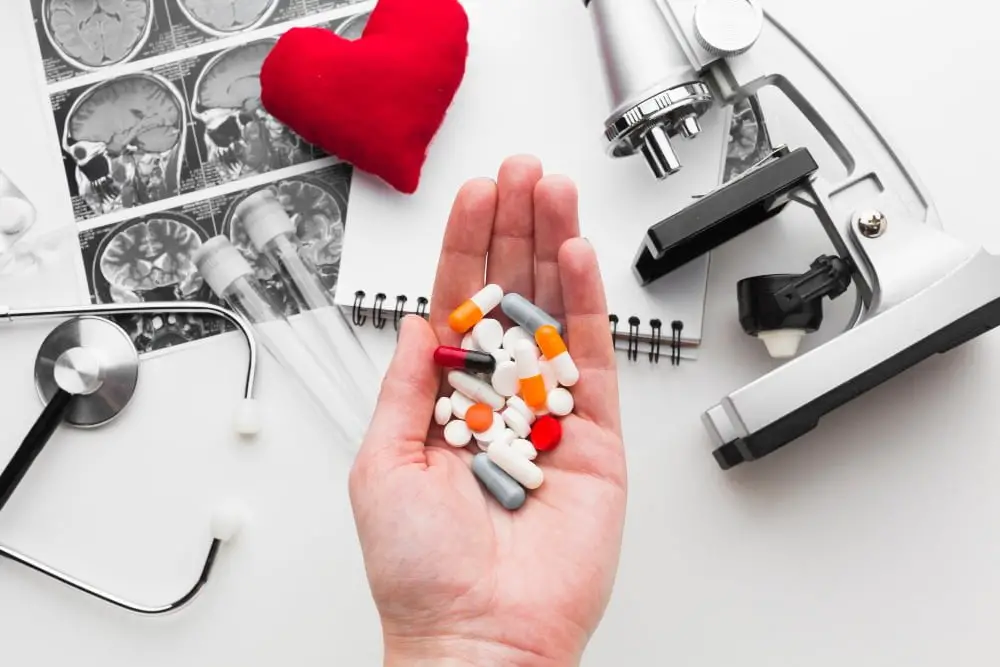
Medical plastics are used in various applications such as surgical instruments, implants, drug delivery systems and diagnostic equipment. They offer advantages over traditional materials like metal or glass due to their lightweight nature and ease of sterilization.
One example is polycarbonate (PC), which is commonly used for medical devices that require transparency like incubators or blood oxygenators. Polyurethane (PU) has excellent biocompatibility properties making it ideal for implantable devices like pacemakers or catheters.
Another plastic material widely used in the healthcare sector is polyvinyl chloride (PVC). It’s flexible yet durable nature makes it suitable for tubing applications such as IV lines while its transparency allows easy monitoring of fluid flow.
The use of plastics in medicine has not only improved patient outcomes but also reduced costs associated with traditional manufacturing methods.
Automotive Plastics
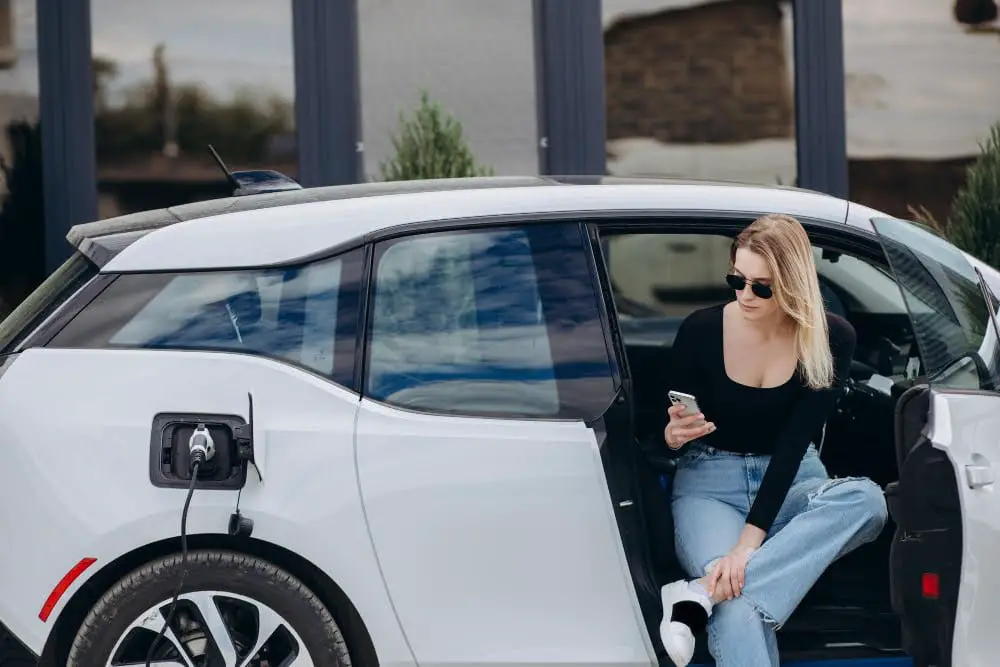
The use of plastics in vehicles has increased significantly over the years as automakers seek to reduce weight and improve performance. Plastic components can be found in almost every part of a car from bumpers to dashboards.
One significant advantage of using plastic parts is that they are much lighter than metal parts, which helps reduce vehicle weight and increase fuel efficiency. For example, replacing a steel bumper with one made from thermoplastic polyolefin (TPO) can save up to 20% on overall vehicle weight.
Another benefit is that plastic components are easier and cheaper to manufacture than their metal counterparts while still maintaining high durability standards required for safety regulations.
Moreover, plastics offer greater design flexibility allowing manufacturers more freedom when designing new models or updating existing ones. They also provide better resistance against corrosion compared with metals used in automobiles.
Construction Plastics
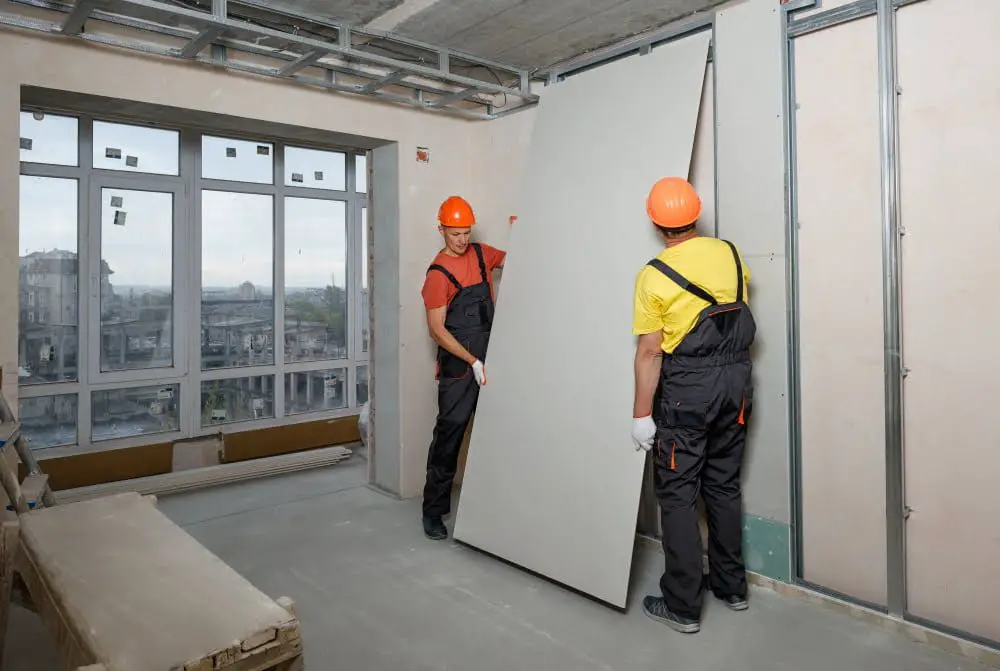
They have replaced traditional materials such as wood, metal, and concrete in many applications. One of the most common uses of plastic in construction is for insulation purposes.
Plastic foam boards made from polystyrene or polyurethane are used to insulate walls, roofs, floors and foundations.
Plastic pipes have also become a popular choice for plumbing systems because they are lightweight yet strong enough to withstand high pressure. PVC pipes are commonly used for water supply lines while ABS pipes work well with drainage systems.
Another application of plastic in construction is roofing materials such as corrugated sheets made from polycarbonate or fiberglass-reinforced polyester (FRP). These materials offer excellent resistance against weathering elements like UV radiation which makes them ideal for outdoor use.
In addition to these applications mentioned above; plastic composites can be found on decks & patios where they provide an attractive finish that requires little maintenance compared with traditional wooden decking options.
Consumer Electronics Plastics
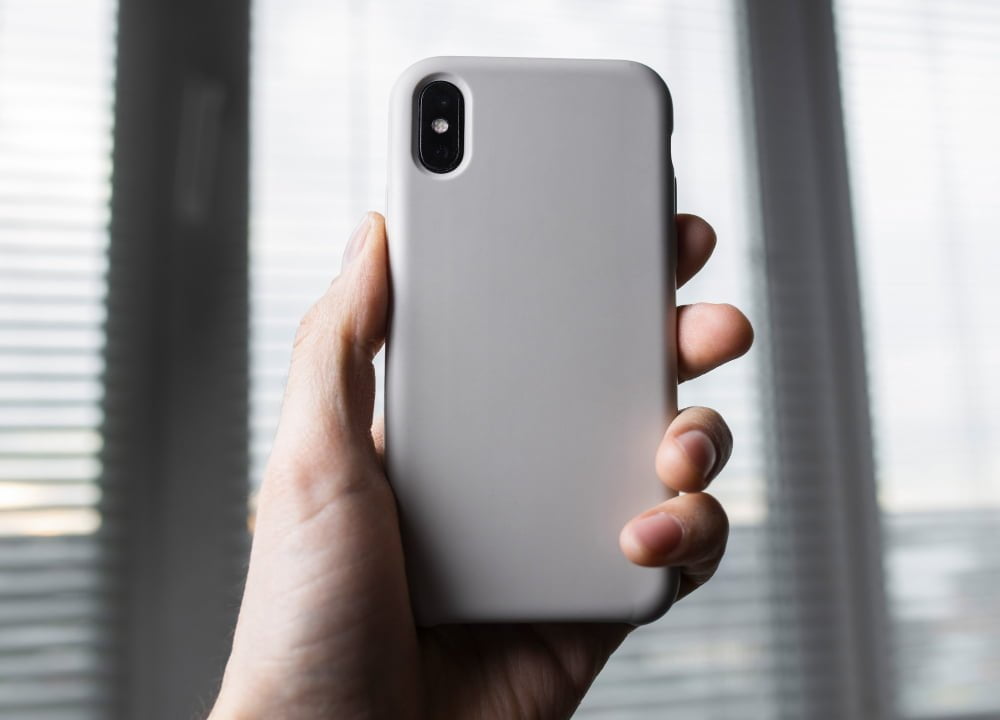
From smartphones to laptops, televisions to gaming consoles, plastic plays a crucial role in their design and functionality. The use of plastics has enabled manufacturers to create sleek and lightweight devices that are easy to handle.
Polycarbonate (PC) is one type of plastic commonly used for electronic device casings due to its high impact resistance and durability. It can withstand accidental drops or impacts without cracking or breaking easily.
Acrylonitrile Butadiene Styrene (ABS) is another popular choice for electronic device housings because it’s strong, durable, heat-resistant, and lightweight. ABS also provides excellent electrical insulation properties making it ideal for electrical components such as switches.
Polypropylene (PP), on the other hand, finds application in battery cases due to its chemical resistance properties which prevent leakage from batteries while ensuring safety during usage.
Consumer electronics have become an integral part of our daily lives; they help us stay connected with loved ones across distances while providing entertainment at our fingertips.
Plastic Toys and Sports Equipment
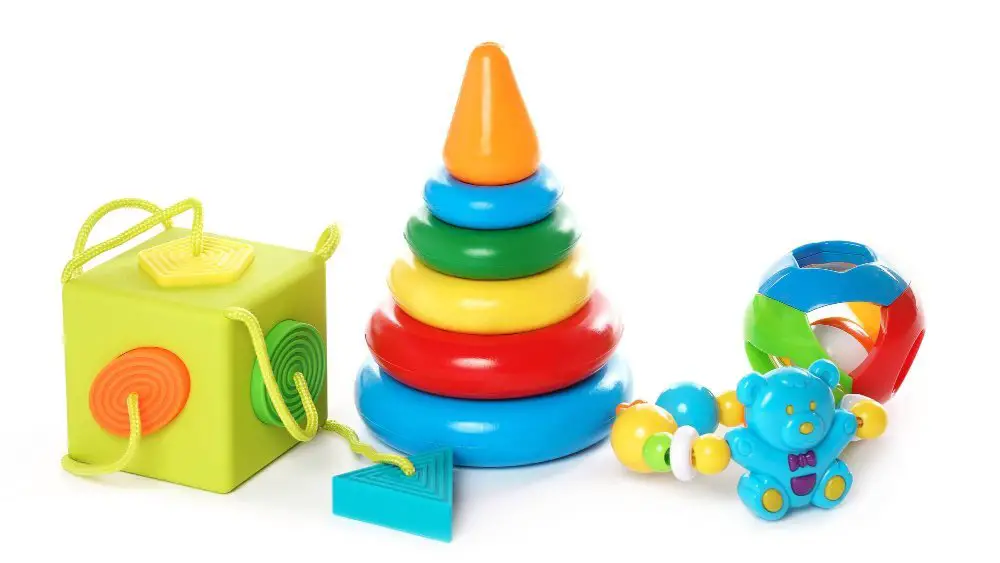
From children’s toys to professional sports gear, plastic has revolutionized the way we play and interact with the world around us.
One of the most significant advantages of plastic in toy manufacturing is its durability. Plastic toys can withstand rough handling, making them ideal for young children who tend to be less gentle with their belongings.
Plastics are lightweight and easy to mold into various shapes, allowing manufacturers to create intricate designs that would be impossible using other materials.
In terms of sports equipment, plastics offer several benefits over traditional materials such as wood or metal. For example, they are lighter in weight than metal but still strong enough to handle heavy loads without breaking or bending out of shape easily.
This makes them perfect for use in items like helmets or protective padding where strength is essential but weight must also be kept low.
Agricultural Plastics
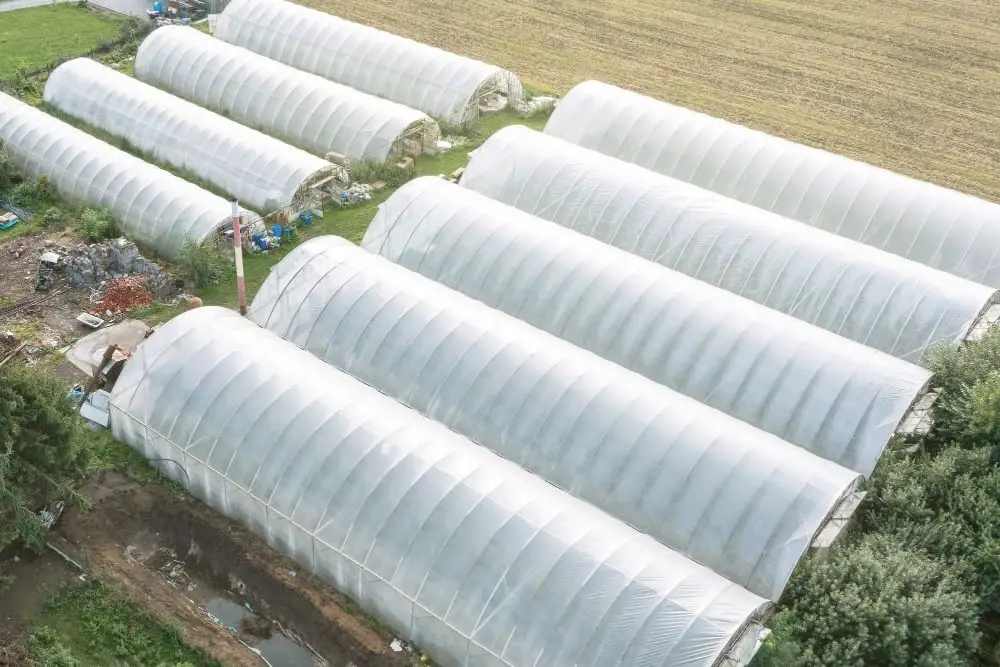
Agricultural plastics are used in different applications, including greenhouse covers, mulch films, irrigation pipes and fittings, silage bags and bale wraps. These plastic products help farmers increase crop yields while reducing water usage and weed growth.
Greenhouse covers made of polyethylene film provide a controlled environment for plants to grow throughout the year. The film is UV stabilized to withstand harsh weather conditions such as extreme heat or cold temperatures.
Mulch films are another type of agricultural plastic that helps control weeds while retaining soil moisture levels. They also regulate soil temperature which can improve plant growth rates.
Irrigation pipes made from PVC (Polyvinyl Chloride) or PE (Polyethylene) materials ensure efficient water distribution across fields with minimal wastage due to leaks or evaporation losses.
Silage bags and bale wraps protect animal feed from spoilage caused by exposure to air during storage periods. These plastics have high oxygen barrier properties that prevent mold formation on stored feeds hence ensuring their quality remains intact until feeding time.
Environmental Impact of Plastics
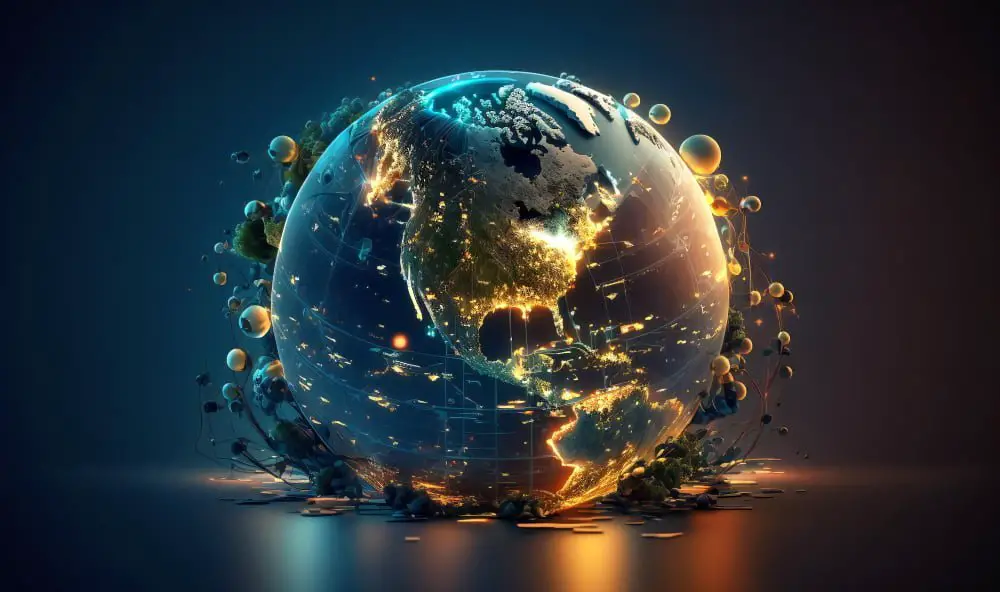
Plastic waste is one of the most pressing environmental issues facing our planet today. The durability and resistance to degradation that make plastic so useful in everyday life also mean that it can persist in the environment for hundreds or even thousands of years.
Plastic pollution has become a global problem, with millions of tons ending up in oceans and waterways each year. Marine animals mistake plastic debris for food, leading to injury or death from ingestion or entanglement.
Furthermore, when plastics break down into smaller particles called microplastics (less than 5mm), they can enter the food chain through marine organisms and eventually end up on our plates.
The production process itself is another source of environmental impact as it requires large amounts of energy and resources such as oil extraction which contributes significantly to greenhouse gas emissions causing climate change.
Plastic Waste Management
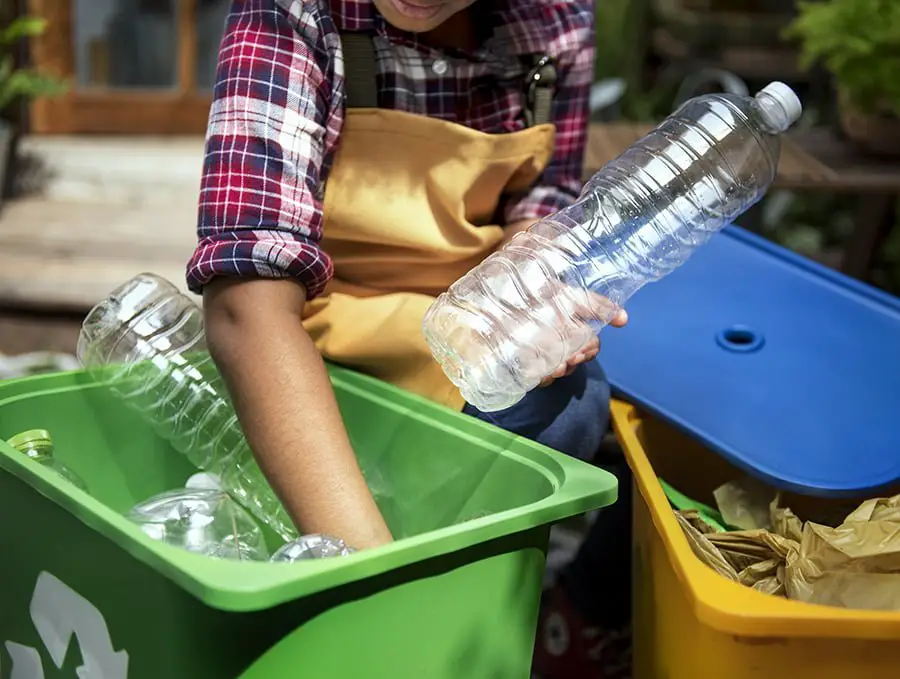
The increasing use of plastics has led to an alarming rise in plastic waste, which poses a significant threat to the environment and human health. Plastic pollution affects marine life, contaminates soil and water bodies, and contributes significantly to greenhouse gas emissions.
To manage plastic waste effectively, it’s essential first to reduce our consumption of single-use plastics such as straws, bags, bottles etc., by opting for reusable alternatives or biodegradable options where possible. Recycling is another crucial aspect of managing plastic waste; however only 9% of all the plastic ever produced has been recycled so far.
In addition to reducing consumption and recycling efforts we need better infrastructure for collection & sorting facilities along with public awareness campaigns on proper disposal methods like segregation at source (home/office) before handing over recyclables/waste materials at designated collection points.
Governments can also play their part by implementing policies that encourage sustainable practices such as extended producer responsibility (EPR), which holds manufacturers accountable for their products’ end-of-life disposal costs.
Plastic Recycling Technologies
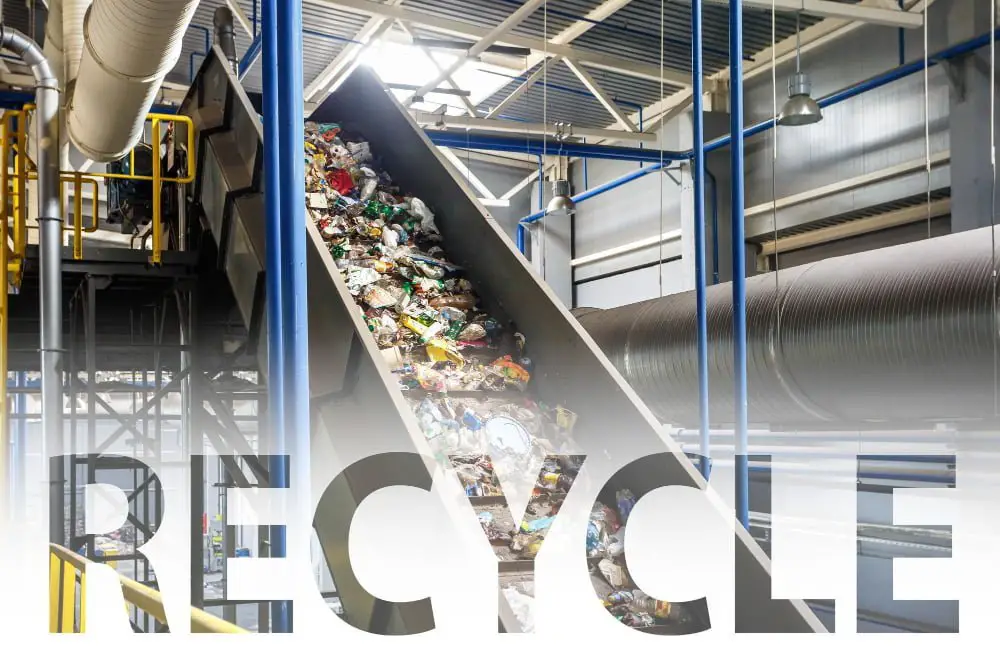
It helps to reduce the amount of plastic waste that ends up in landfills and oceans, thereby reducing environmental pollution. There are different recycling technologies available for plastics, including mechanical recycling, chemical recycling, and feedstock recycling.
Mechanical Recycling: This process involves shredding used plastics into small pieces or pellets that can be melted down and reformed into new products. Mechanical recycling is the most common form of plastic recycling globally.
Chemical Recycling: Chemical processes break down used plastics into their constituent monomers or other chemicals that can be reused as raw materials for new products.
Feedstock Recycling: This process converts used plastics back to their original petrochemical building blocks through a series of chemical reactions. The resulting product can then be refined further to produce virgin-quality polymers suitable for use in various applications.
Reducing Plastic Pollution
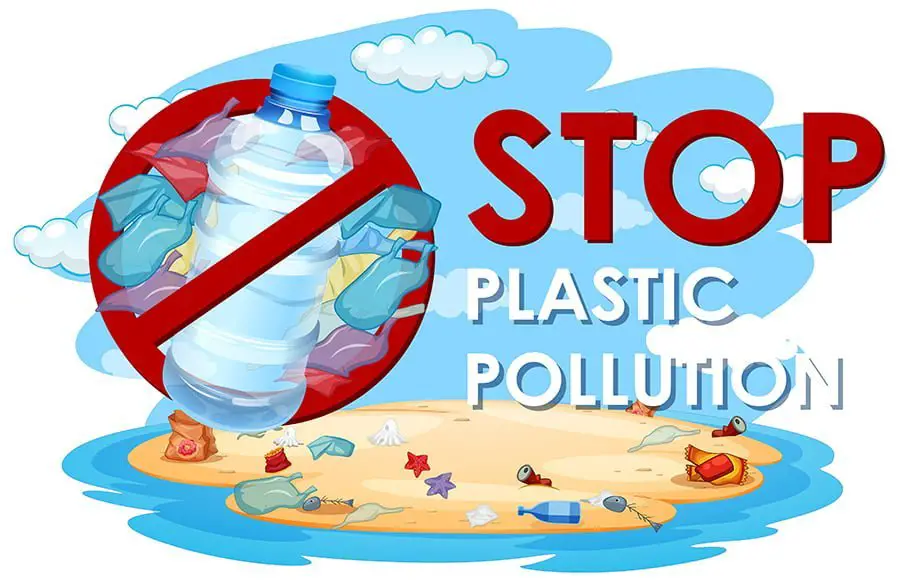
It’s estimated that by 2050, there will be more plastic in the ocean than fish if we don’t take action to reduce plastic waste. Fortunately, there are several ways we can all contribute to reducing plastic pollution.
One way is by reducing our use of single-use plastics such as straws and water bottles. We can opt for reusable alternatives like metal or glass straws and refillable water bottles instead of buying bottled water.
Another way is through proper disposal of plastics. Recycling helps keep plastics out of landfills where they can take hundreds or even thousands of years to decompose fully.
Governments also play an essential role in reducing plastic pollution through policies such as banning single-use plastics or implementing extended producer responsibility programs where manufacturers are responsible for the end-of-life management of their products.
Future of Plastics
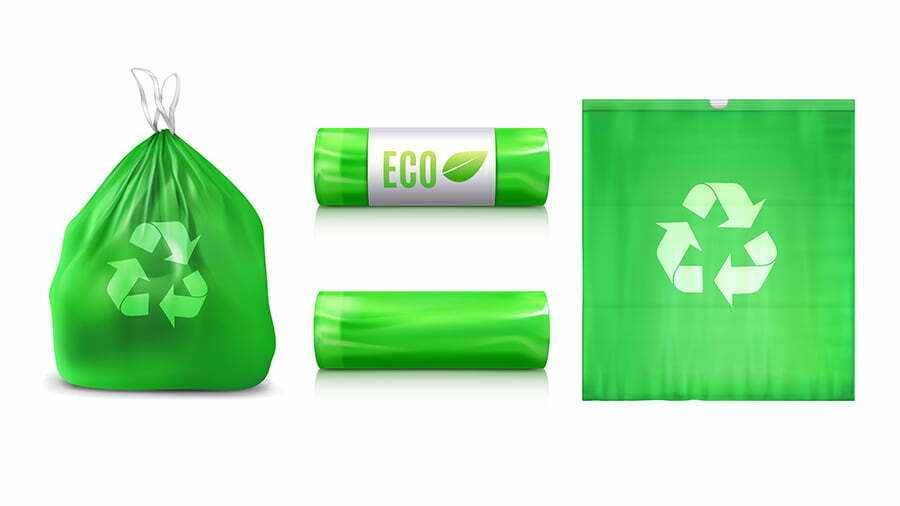
One area of focus is the development of bioplastics, which are made from renewable resources such as corn starch or sugarcane. Bioplastics have the potential to reduce our reliance on fossil fuels and decrease plastic waste in landfills.
Another promising development is the use of recycled plastics in manufacturing processes. By using recycled materials instead of virgin plastic, we can reduce energy consumption and greenhouse gas emissions while also diverting waste from landfills.
In addition to these advancements, researchers are exploring ways to make existing types of plastics more environmentally friendly by improving their biodegradability or developing methods for recycling difficult-to-process materials like mixed-plastic waste.
As consumers become increasingly aware of environmental issues related to plastic use, there has been a growing demand for eco-friendly alternatives. This trend has led companies across industries – from food packaging manufacturers to automotive suppliers -to invest in research into sustainable alternatives that meet consumer needs without compromising performance or affordability.
FAQ
What are 10 uses of plastics?
Plastics have 10 uses such as packaging containers, bottles, drums, trays, boxes, cups, vending packaging, baby products, and protective packaging, leveraging their versatile, hygienic, lightweight, flexible, and highly durable properties.
What are the list of plastic uses?
Plastic uses include packaging, building and construction, textiles, consumer products, transportation, electrical and electronics, and industrial machinery.
What are the environmental impacts of different types of plastics?
Different types of plastics have varying environmental impacts, including greenhouse gas emissions, water pollution, and harm to marine life.
How can various plastics be recycled and repurposed effectively?
Various plastics can be recycled and repurposed effectively by sorting, cleaning, shredding, melting, and reforming them into useful products such as containers, textiles, construction materials, and more.
What are the health and safety concerns associated with the use of different plastics?
Health and safety concerns associated with different plastics include exposure to chemicals, endocrine disruption, environmental pollution, and plastic ingestion by marine life.
Recap