Understanding how to calculate yield loss in the plastic extrusion process is key for optimizing productivity and minimizing waste in polymer-based construction projects.
Calculating yield loss in the plastic extrusion process involves a careful analysis of the weight of the raw materials used and the final output.
Yield loss occurs when the weight of the finished product is less than the weight of the raw materials used.
To calculate this, subtract the weight of the finished product from the weight of the raw materials, then divide the result by the weight of the raw materials and multiply by 100 to get a percentage.
This article will delve into the details of each step, including how to accurately measure weights, potential causes of yield loss, and strategies to minimize it in your plastic extrusion process.
Key takeaways:
- Yield loss is the difference between the weight of raw materials and the weight of the finished product.
- Factors affecting yield loss include material quality, operation conditions, equipment maintenance, and operator skill.
- To calculate yield loss, subtract the weight of the finished product from the weight of the raw materials and divide by the weight of the raw materials.
- Regular monitoring of yield loss helps identify issues and optimize the extrusion process.
- Strategies to reduce yield loss include equipment maintenance, accurate process control, material planning, operator training, recycling defective products, and implementing quality control measures.
Understanding the Plastic Extrusion Process
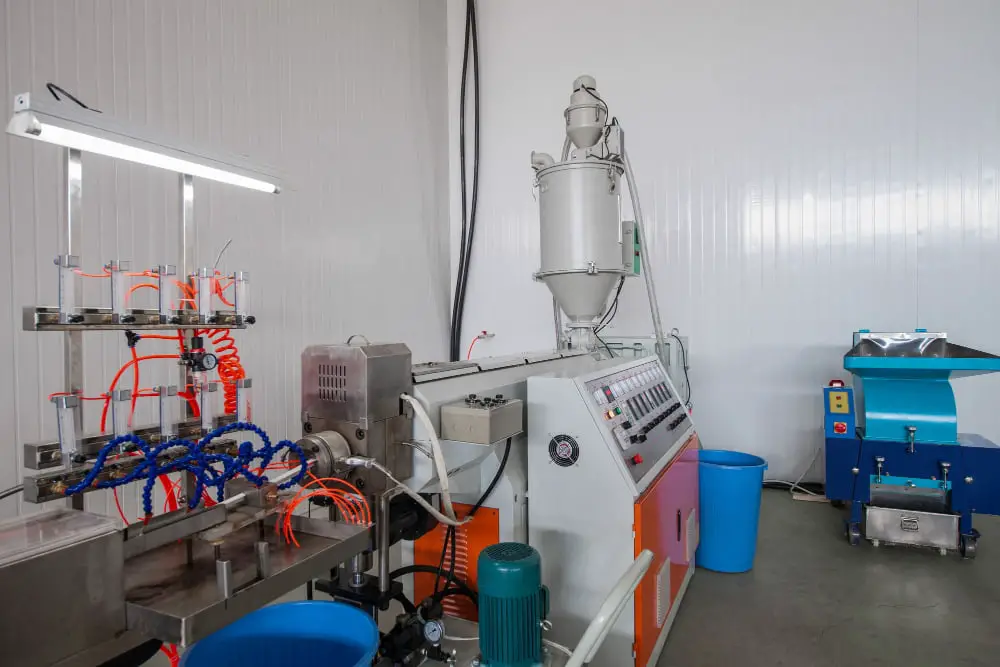
Plastic extrusion is a high-volume manufacturing process, during which raw plastic is melted and formed into a continuous profile. This technique finds frequent use in the production of items such as piping, wire insulation, and plastic sheeting.
In this sequence, the raw plastic material (usually in the form of granules) is first loaded into a hopper. It’s then directed into a heated barrel through a rotating screw mechanism. The heat and pressure inside the barrel melt the plastic, turning it into a viscous liquid.
The molten plastic is pushed through a die, which gives the plastic its final shape as it cools and hardens. After this step, the newly formed plastic is cut into desired lengths or rolled for later use.
The process can be adjusted according to the type of plastic being used and the product specifications. Variations in factors like temperature, pressure, and screw speed will significantly affect the result. Monitoring and modifying these parameters as needed are crucial for achieving optimal production efficiency.
There are two main types of plastic extrusion: single screw (most commonly used due to its simplicity and cost-effectiveness) and twin screw (used for more complex, higher performance applications).
Detailing the Factors Affecting Yield Loss in Plastic Extrusion
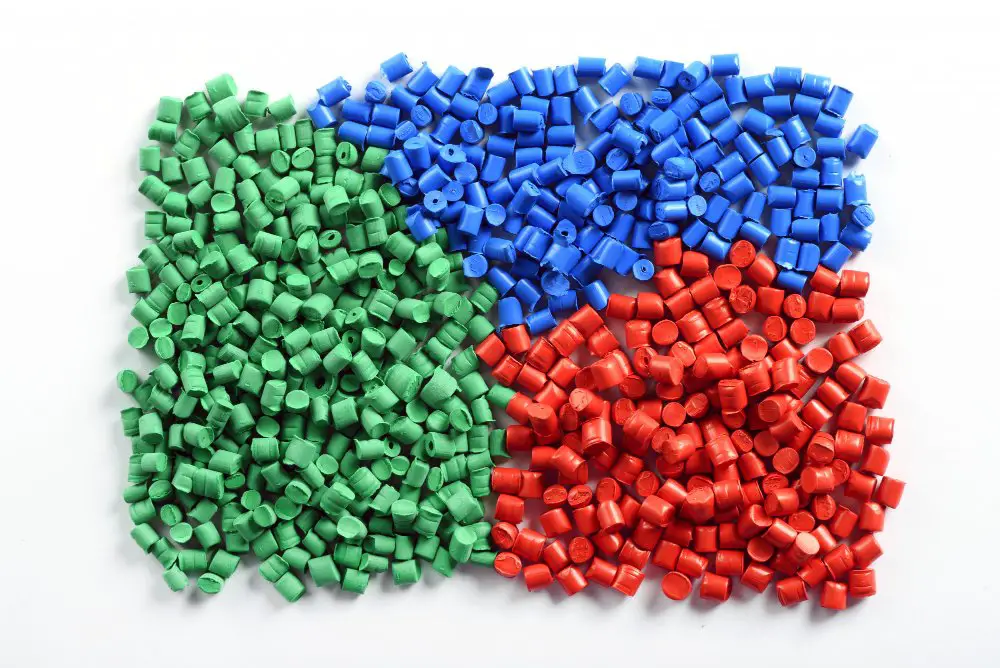
A multitude of factors come into play in the event of yield loss during the plastic extrusion process. These factors are often interconnected, and a slight change in one could noticeably affect production quality or quantity.
Material quality becomes a significant factor here. The quality of polymers used in the extrusion process can greatly affect the subsequent yield. Inferior raw materials could lead to an unreliable and inconsistent output.
The precision in control of operation conditions also contributes. In precise extrusion temperature, conveyor speed, and cooling rates could lead to deformations, shrinkage, or wasted plastic. Besides, unoptimized parameters of the extruder, such as screw design or barrel temperatures, might also lead to yield loss.
Equipment maintenance is another critical aspect. Regular cleaning and maintenance of the equipment reduces the cases of technical disruptions that could result in yield loss.
Lastly, operator skill and training. Adequately trained operators can identify potential issues early and adjust the process accordingly to decrease yield loss. They can also maintain operational efficiency and consistency, significantly minimizing the risk of errors or mishandling.
Now that these contributing factors have been identified, the subsequent sections will provide a guide on how to calculate and reduce this yield loss.
Step-by-step Guide On How to Calculate Yield Loss in Plastic Extrusion
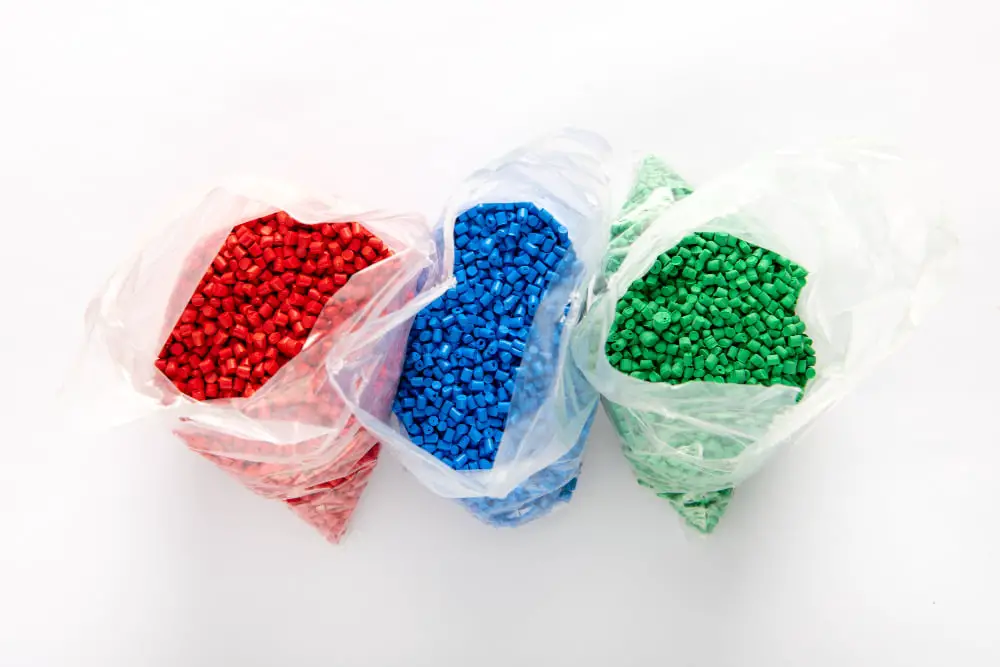
First off, begin with collecting relevant data from the extrusion process. This includes the starting weight of the raw polymer material, the weight of the extruded products, and the weight of any waste or scrap produced.
Next, bring into focus the actual yield from the extrusion process. This is the weight of the acceptable extruded products. Subtract this from the starting weight of the raw materials.
The subsequent step involves calculating the weight of the lost material. This can be done by adding the weight of the waste or scrap to the difference obtained in the previous step.
Then, calculate the yield loss percentage. Divide the weight of the lost material by the starting weight of the raw materials and multiply the result by 100.
Lastly, use this yield loss percentage to monitor and compare performance over time. Significant changes may reveal issues in the production process. Regular monitoring can also help identify trends and analyze the effect of any modifications made to the process.
Remember, yield loss calculations are most effective when performed regularly and consistently, to accurately reflect any changes or trends in production efficiency.
Common Mistakes While Calculating Yield Loss in Plastic Extrusion
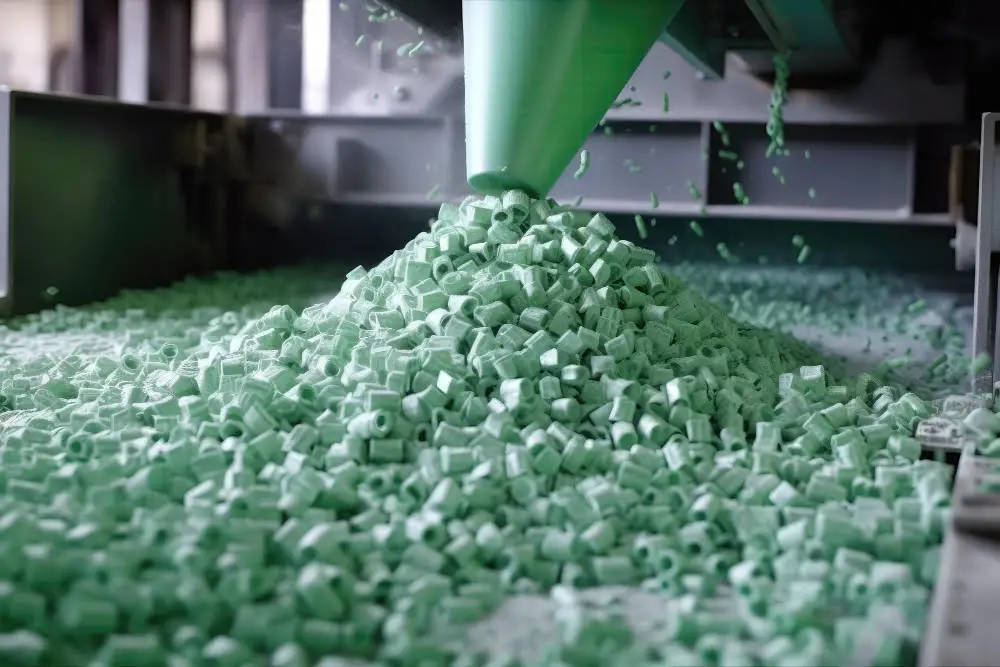
Common errors often arise from misunderstandings of the extrusion process. One such mistake is ignoring the influence of temperature. Temperature plays a key role in the plastic’s viscosity, which impacts the ease of extrusion and overall material loss. Implementing a consistent temperature monitoring system in the extrusion process can aid in achieving more accurate yield loss calculations.
Another common mistake is overlooking the importance of material consistency. Variations in the raw materials can lead to inconsistencies in the finished product, thereby impacting the yield loss calculation. Consistently sourcing high-quality raw materials helps to maintain a reliable yield.
Not periodically recalibrating equipment also leads to inaccuracies. The continual wear and tear of machinery may affect the precision of extrusion, thereby skewing yield loss calculations. Regular maintenance and recalibration ensure the accuracy of the measurements.
Lastly, operators often underestimate the effect of waste or scrap generated during the extrusion process. Every bit of material that doesn’t become part of the finished product – including trimmings, rejects, or any other waste – is part of the yield loss. Being diligent about measuring and tracking these additional losses can significantly improve the accuracy of yield loss calculations.
Importance of Calculating Yield Loss in Plastic Extrusion
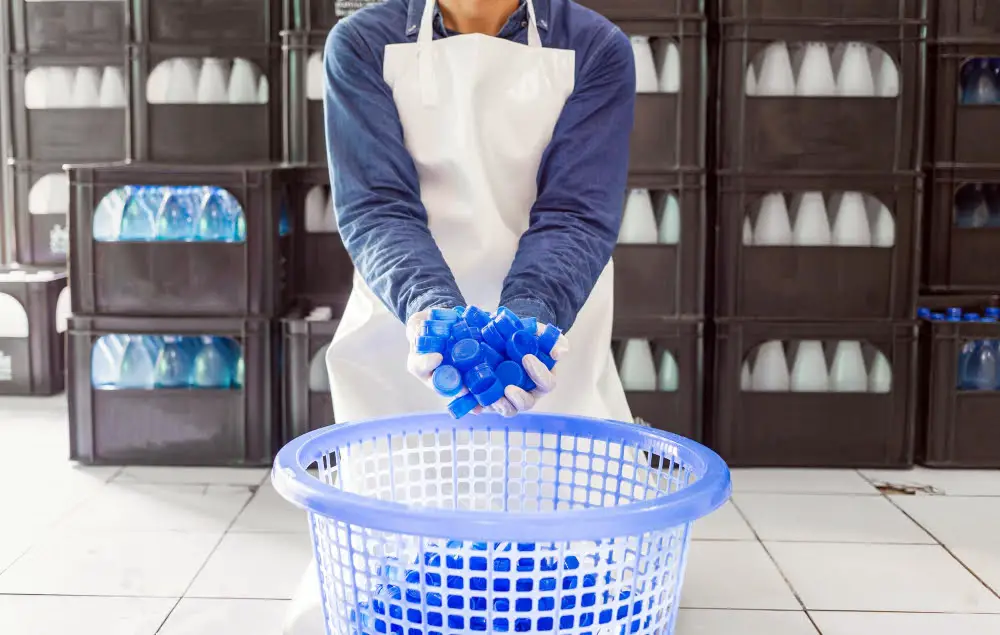
For businesses in the plastic extrusion industry, understanding and calculating yield loss is key.
The main reasons for its importance are:
- Cost Saving: Yield loss has a direct correlation with business expenses. By identifying and quantifying losses, businesses can target specific areas for improving efficiency and lowering production costs which directly results in greater profit margins.
- Process Optimization: Quantifying yield loss aids in systematizing extrusion processes. By identifying the causes of loss, adjustments can be made to control variables such as temperature, feed rate, or screw design to enhance the overall operation.
- Quality Assurance: Accurate calculation of yield loss helps ensure the consistency of the finished product. A high yield loss could indicate an issue with the formulation or the process parameters, compromising the product quality.
- Environmental Responsibility: Evaluating yield loss also contributes to sustainability. Reduced waste in production processes leads to less environmental pollution, affirming the company’s commitment to eco-friendly practices.
In order to reliably calculate yield loss, one must regularly monitor the plastic extrusion process, collect relevant data, and then apply the appropriate mathematical formula or analytical tool.
How to Reduce Yield Loss in the Plastic Extrusion Process
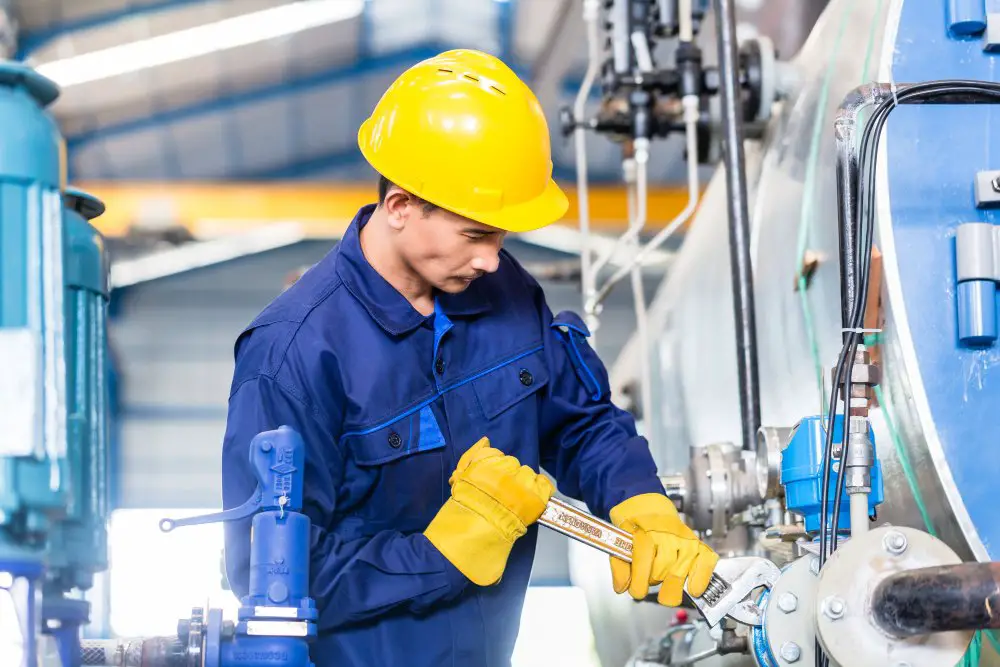
To bring down yield losses in the plastic extrusion process, consider the following actions:
Ensure Proper Maintenance of Equipment: Regular servicing of extrusion machines can forestall failures that cause waste. Keeping the barrel temperatures and pressures within the recommended benchmarks will ensure efficient extrusion and minimize wastage.
Use Accurate Process Control Systems: Automated control systems can offer precision in temperature settings, feeder rates, and other important parameters. This helps to restrict deviations, improving the product quality and yield.
Plan Material Usage: Maintain a meticulous record of material input and output. Understanding the polymer properties can also play a crucial role in reducing poor quality output.
Train Operators: Imparting training to machine operators to handle situations like machine downtime, material spillage or a start-up hiccup can significantly diminish yield loss.
Recycle Defective Products: Instead of discarding them, defects can be recycled, reducing material loss. However, this must be done ensuring it doesn’t hamper final product quality.
Adopt a Lean Manufacturing Approach: Lean manufacturing emphasizes eliminating waste. Extrusion defects, waiting time, and inventory excesses can be effectively minimized, improving overall efficiency and yield.
Implement Quality Control: Regular checks at different stages of the process can detect errors in the early stages. Immediate rectification avoids compounding errors leading to yield loss.
Implementing Quality Control Measures to Minimize Yield Loss in Plastic Extrusion
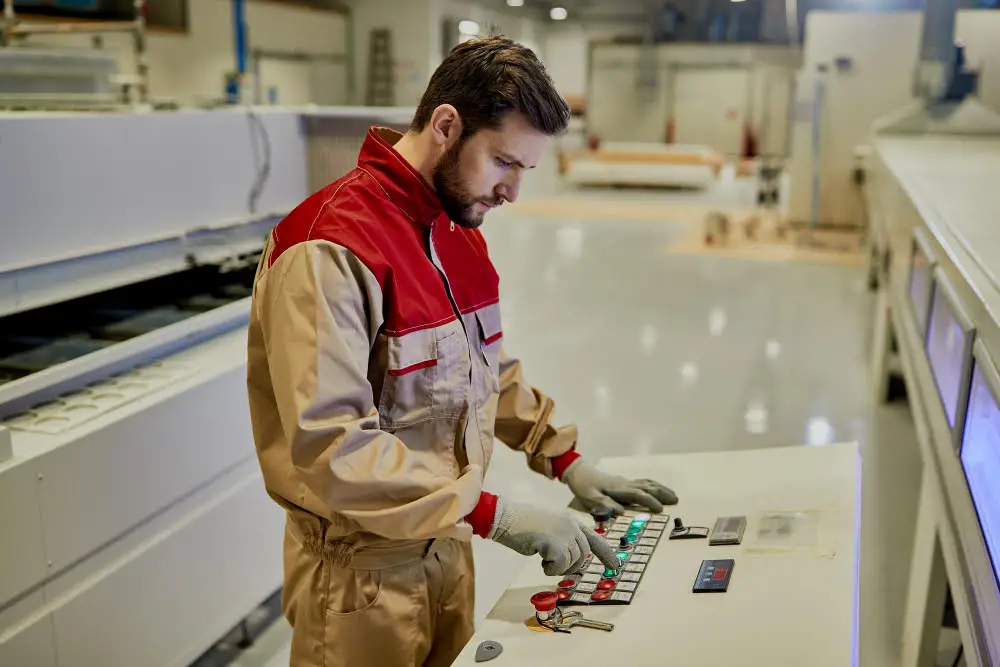
To effectively implement quality control measures, it is pivotal to understand how they can directly impact the reduction of yield loss in the plastic extrusion process.
Start with utilizing advanced temperature control systems. Fine-tuning temperature settings based on material requirements can optimize the overall process, reducing the likelihood of defects and preventing waste from the injection stage itself.
Next, consider in-line monitoring systems. These devices continuously check the quality of extruded plastics, detecting inconsistencies such as variations in thickness or width, ultimately enabling immediate rectification of any process faults.
Incorporating frequent inspections and maintenance of the extrusion machinery is crucial. Regular checks can spot and fix potential issues that could cause a loss in yield, including a misaligned die or excess material buildup.
Lastly, investing in personnel training is key. Certified operators with the correct knowledge about the functioning, ideal settings, and troubleshooting of the extrusion line can effectively mitigate yield loss, enhancing the overall productivity of the process.
By integrating these quality control measures, organizations can more efficiently manage the potential issues that prompt yield loss, thereby enhancing the efficiency of the plastic extrusion process.
FAQ
What is the formula for extrusion output?
The formula for extrusion output can be calculated as 2.64 x D²Nhρ, where D denotes diameter in inches, N represents screw speed in rpm, h marks channel depth in inches, and ρ indicates melt density in gm/cc.
How do you calculate extrusion throughput?
Extrusion throughput is calculated by the formula: System’s Volumetric Drag Flow – System’s Volumetric Pressure Flow.
How do you calculate extrusion?
The extrusion multiplier is calculated by dividing the extrusion width, typically set at 0.45, by the average measured wall thickness.
What determines the extruder output?
The output of the extruder is primarily determined by the difference between the drag flow and pressure flow, with the quality of the product influenced by the laminar shear mixing occurring in the metering zone.
What factors influence the speed of the plastic extrusion process?
The speed of the plastic extrusion process is influenced by factors such as the type of polymer used, the temperature of the extrusion process, the design of the die, and the speed of the cooling phase following extrusion.
How does the choice of polymer material affect the efficacy of extrusion?
The choice of polymer material significantly impacts the efficacy of extrusion as different polymers have varying melting points, compressive strength and viscosity, which influence the ease of extrusion, final shape stability, and overall performance of the extruded product.
How can one measure the efficiency of a plastic extrusion operation?
The efficiency of a plastic extrusion operation can be measured by evaluating factors such as the output rate, quality of the final product, energy consumption, downtime, and the amount of waste produced.
Recap