Discover the remarkable world of creep-resistant plastics and their essential role in enhancing durability, safety, and longevity across various industries.
Have you ever noticed how some plastic materials tend to deform over time, especially when subjected to constant stress or load? This phenomenon is known as “creep” and can be a real headache for engineers and designers who rely on plastics in their constructions. But fear not, because there are creep-resistant plastics that can withstand even the most demanding applications.
In this article, we’ll explore what creep is, why it happens, and how these special polymers work to combat it. So buckle up and let’s dive into the world of creep-resistant plastics!
Definition of Creep Resistance
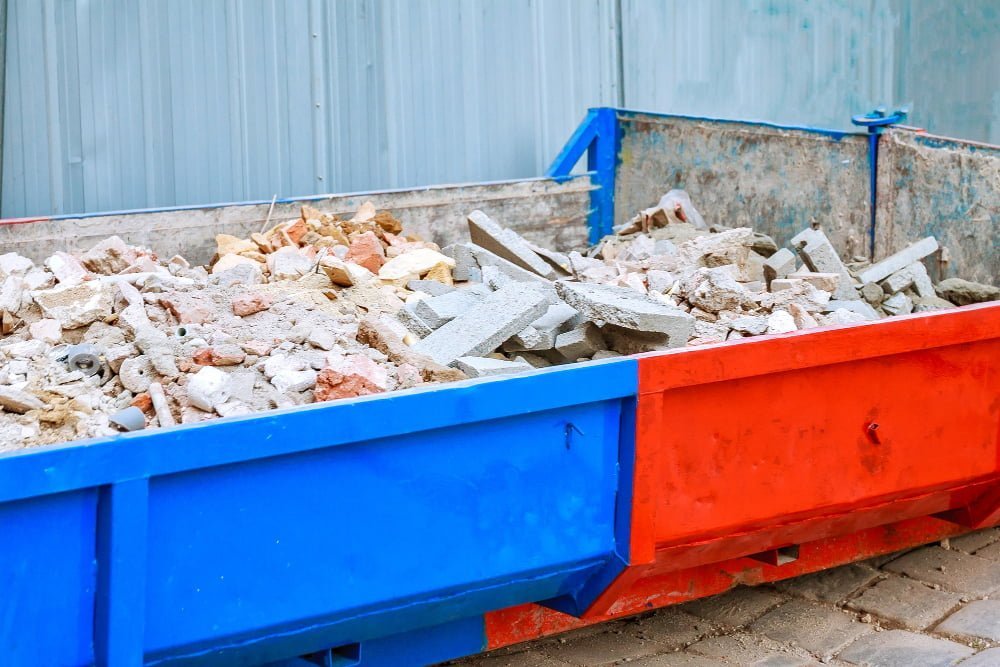
It’s a critical property for materials used in construction, manufacturing, and engineering applications where long-term durability and stability are essential. Creep can cause permanent damage to structures or components that experience prolonged exposure to high loads or temperatures.
Therefore, creep-resistant plastics play an important role in ensuring safety and reliability across various industries such as aerospace, automotive, medical devices production among others.
The creep behavior of polymers depends on several factors such as temperature, humidity level (in some cases), applied load/stress magnitude & directionality (tensile/compressive/shear). The rate at which the deformation occurs also varies depending on these factors; it may be slow initially but accelerate with time until failure occurs if not addressed properly.
Creep resistance is crucial for materials used in applications where they will be subjected to constant stress/load over extended periods.
Importance of Creep Resistance
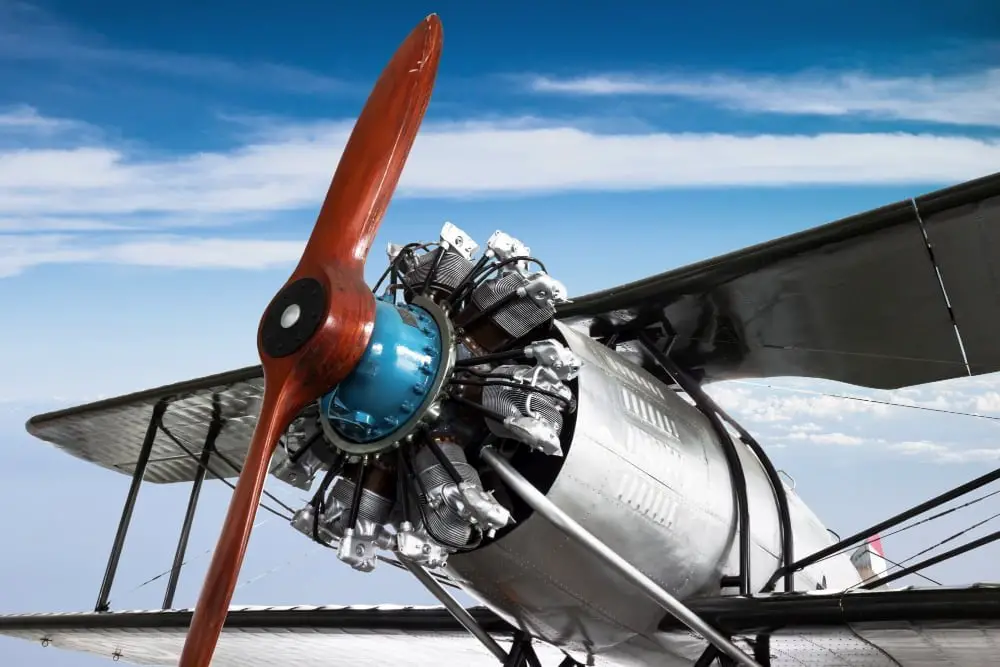
It refers to the ability of a material to resist deformation under constant load or stress over time. In construction, creep-resistant plastics are essential because they provide long-term stability and durability, even when subjected to high loads or extreme temperatures.
For example, imagine you’re designing an aircraft component that needs to withstand high pressure and temperature changes during flight. If you choose a plastic material with poor creep resistance, it could deform over time due to the constant stress placed on it by these conditions.
This could lead not only to structural failure but also potential safety hazards for passengers and crew.
Similarly, in automotive manufacturing where parts need longevity despite exposure from harsh environmental factors such as heat generated by engines or UV radiation from sunlight; choosing materials with good creep-resistance can ensure that components remain functional throughout their lifespan without requiring frequent replacements.
Understanding Creep in Plastics
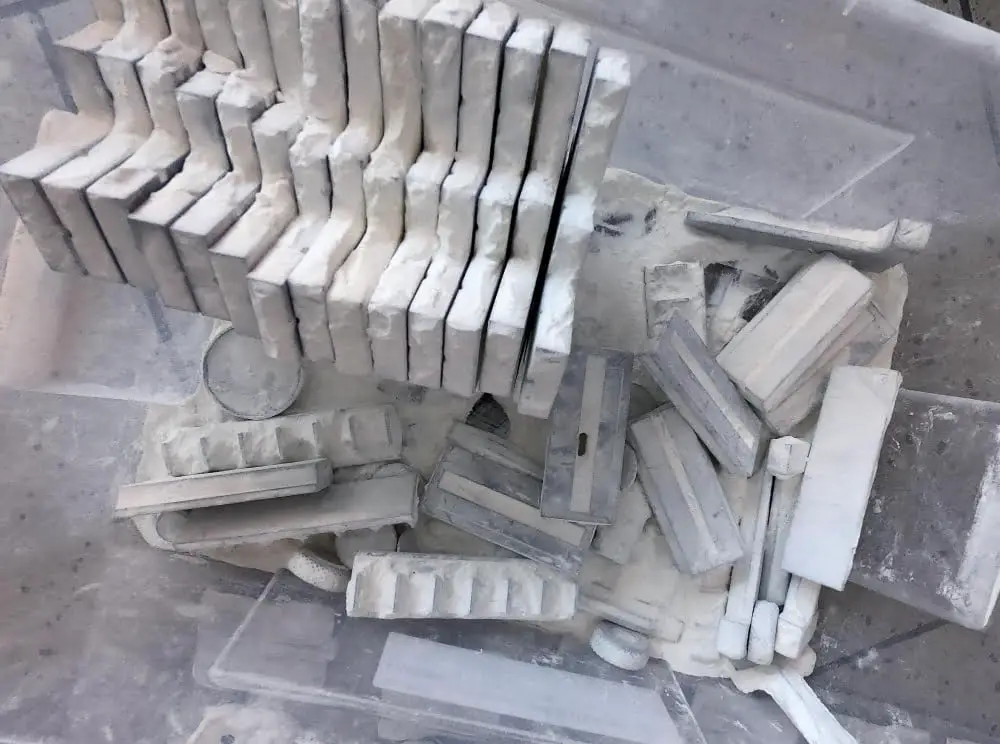
It occurs when a material is subjected to constant stress or load, causing it to slowly deform under the pressure. This can be particularly problematic in construction applications where long-term durability and stability are essential.
Understanding creep requires an understanding of the molecular structure of polymers. Polymers consist of long chains of repeating units called monomers, which are held together by chemical bonds.
When stress is applied, these chains begin to slide past each other, leading to deformation.
The rate at which creep occurs depends on several factors such as temperature, humidity levels and exposure time among others; therefore engineers must take into account all these variables when designing structures made from plastic materials.
Characteristics of Creep-Resistant Materials

These materials have unique characteristics that make them ideal for use in various applications where creep resistance is critical. One of the most important features of creep-resistant plastics is their ability to withstand high temperatures without deforming or breaking down, making them suitable for use in harsh environments such as aerospace, automotive, and industrial settings.
Another characteristic of these materials is their excellent dimensional stability over time. Unlike traditional plastics that tend to shrink or expand under different conditions, creep-resistant polymers remain stable and retain their original dimensions even after prolonged exposure to heat or pressure.
Moreover, these special polymers exhibit exceptional mechanical properties such as high tensile strength and toughness while maintaining flexibility at low temperatures. This makes them ideal for use in applications where durability and impact resistance are essential.
In addition to being highly resistant against deformation due to constant loading over time (creep), they also possess other desirable properties like chemical inertness which makes them resistant against corrosion from chemicals; UV-resistance which prevents degradation from sunlight exposure; flame retardancy which reduces the risk of fire hazards among others.
Types of Creep-Resistant Plastics
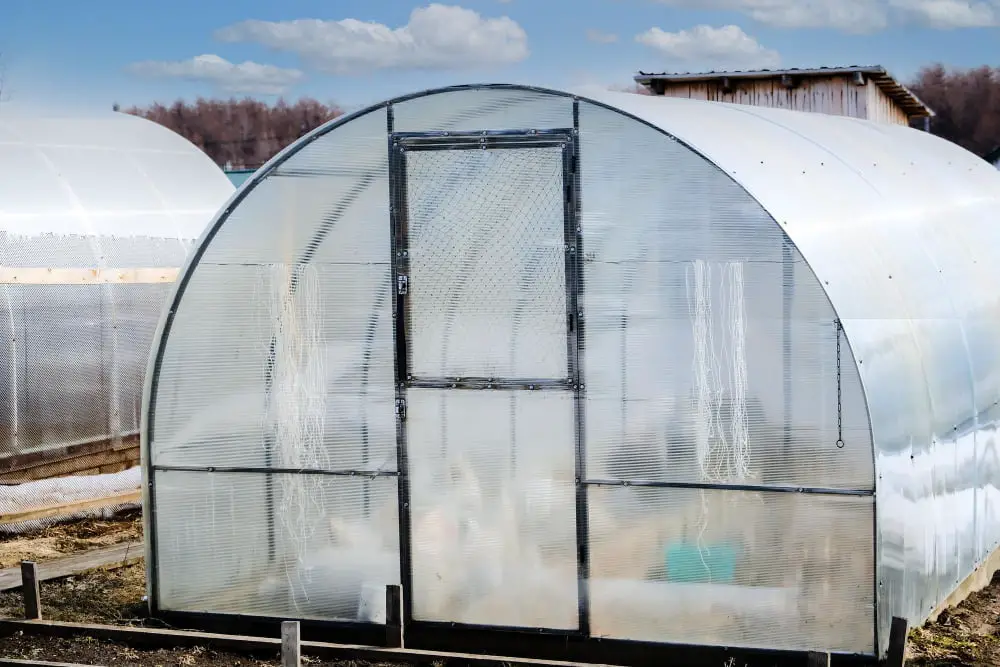
Some of the most common creep-resistant polymers include polycarbonate (PC), polyetherimide (Ultem® PEI), polyphenylene sulfide (PPS), and polyvinyl chloride (PVC). These materials are known for their excellent resistance to deformation under load, high-temperature stability, chemical resistance, and mechanical strength.
Polycarbonate is a popular choice for applications that require transparency or impact resistance. It has good creep performance at elevated temperatures up to 140°C.
Polyetherimide is another high-performance polymer that offers exceptional dimensional stability even at extreme temperatures ranging from -40°C to 170°C.
Polyphenylene sulfide is a thermoplastic material with excellent chemical resistance and thermal stability up to 260 °C. PVC has good electrical insulation properties as well as being resistant against chemicals such as acids or bases.
Other types of creep-resistant plastics include PEEK(polyether ether ketone) which can withstand continuous use in environments where temperature exceeds 250 °C; PAI(polyamide-imides) which have superior wear-resistance; PSU(polysulfones) which offer great hydrolysis-resistance; PETG(PET copolyester glycol-modified); PPSU(polyphenylsulfone); PVDF(Polyvinylidene fluoride).
Polycarbonate (PC) Properties and Creep Resistance

It is widely used in various industries, including automotive, construction, and electronics. PC has high impact strength and can withstand extreme temperatures without losing its mechanical properties.
This makes it an ideal material for applications that require durability and reliability over time.
One of the key factors contributing to PC’s creep resistance is its amorphous structure. Unlike crystalline polymers that have ordered molecular arrangements, amorphous polymers lack long-range order in their molecular chains.
As a result, they are less prone to deformation under stress or load.
Another factor affecting the creep performance of PC is its glass transition temperature (Tg). Tg refers to the temperature at which an amorphous polymer transitions from a hard glassy state to a soft rubbery state upon heating or cooling.
The higher the Tg value of a material, the more resistant it will be against deformation at elevated temperatures.
In addition to these inherent properties of polycarbonate itself as well as other materials like Ultem® PEI mentioned earlier on this list also improve polycarbonate’s overall performance when blended with them.
Polycarbonate Film Properties
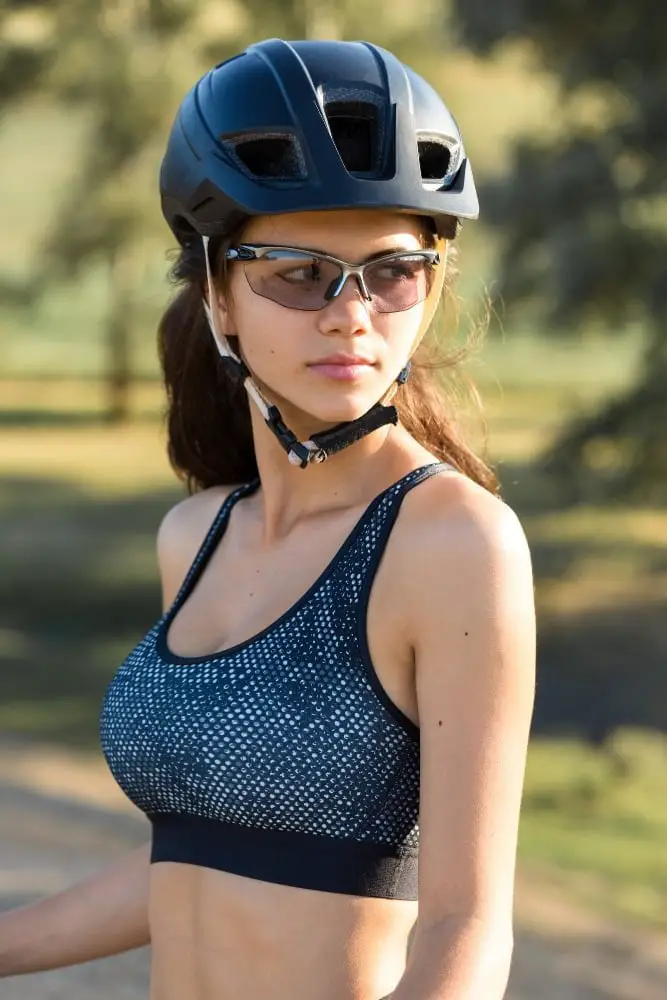
Polycarbonate film is a thin, flexible sheet made from this material and has several unique properties that make it an attractive choice for various industries.
One of the most notable features of polycarbonate film is its high impact strength. It can withstand significant force without cracking or breaking, making it suitable for use in safety equipment such as face shields and protective eyewear.
Polycarbonate film offers exceptional optical clarity with low distortion levels compared to other plastics.
Another advantage of using polycarbonate films over traditional glass materials is their lightweight nature while still maintaining high strength properties. This makes them perfect for applications where weight reduction plays a crucial role in performance optimization.
Moreover, PC films have excellent heat resistance capabilities which allow them to maintain their physical integrity even at elevated temperatures up to 135°C (275°F). They also exhibit good electrical insulation properties which make them useful as dielectric layers between conductive components or substrates.
Polyetherimide (Ultem® PEI) Applications and Characteristics
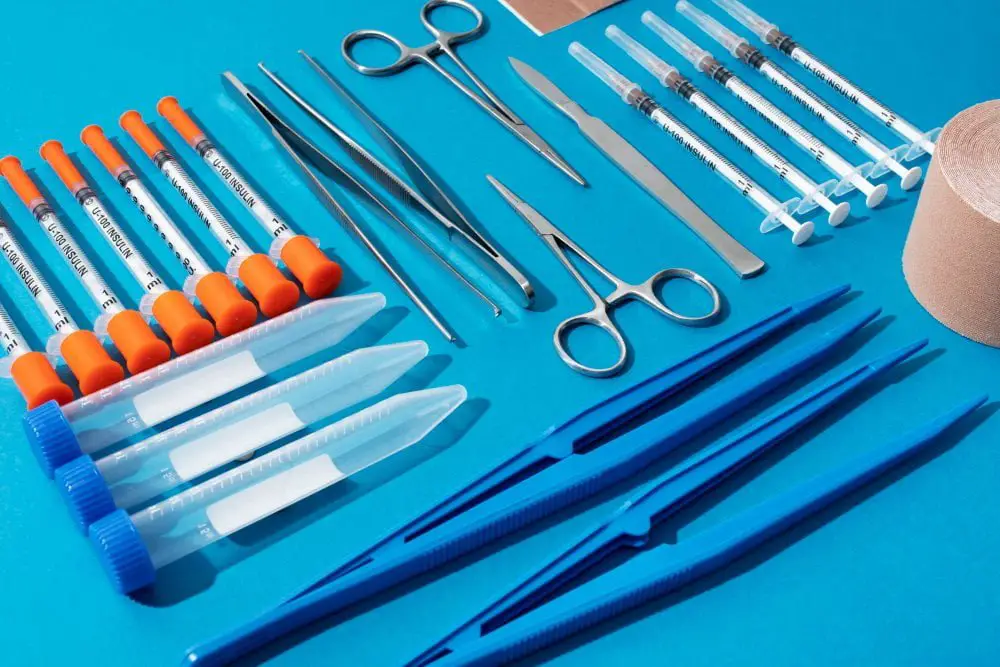
It has become increasingly popular in various industries due to its unique combination of properties. PEI is commonly known by the brand name Ultem® and can be found in applications ranging from aerospace to medical devices.
One of the most significant advantages of PEI is its ability to withstand high temperatures without losing mechanical properties or deforming under load. This makes it an ideal material for use in hot environments such as automotive engine components or aircraft interiors.
PEI also exhibits exceptional electrical insulation properties, making it suitable for electronic components like connectors and switches. Its inherent flame retardancy further enhances its safety profile when used in these applications.
Another notable characteristic of PEI is its biocompatibility, which makes it suitable for use in medical devices such as surgical instruments or implants where contact with bodily fluids occurs.
Polyetheretherketone (PEEK) Resistance
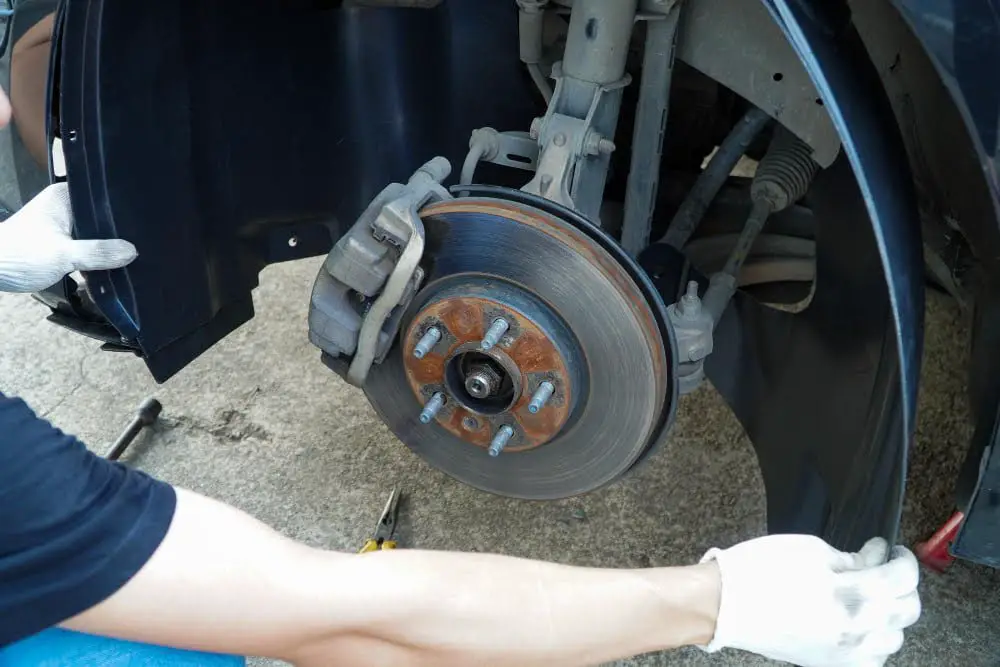
PEEK has become increasingly popular in various industries due to its exceptional creep resistance and ability to withstand extreme temperatures. This material can maintain its strength even when exposed to continuous loads or elevated temperatures for extended periods of time.
PEEK’s unique molecular structure provides it with superior creep resistance compared to other plastics such as nylon or acetal. It also has excellent dimensional stability, making it ideal for applications where tight tolerances are required.
In addition to its impressive mechanical properties, PEEK is highly resistant to chemicals such as acids and bases. It also maintains good electrical insulation properties over a wide range of frequencies and temperatures.
Due to these characteristics, PEEK finds use in many demanding applications across different industries including aerospace engineering, automotive manufacturing medical devices production among others.
Polyphenylene Sulfide (PPS) Benefits
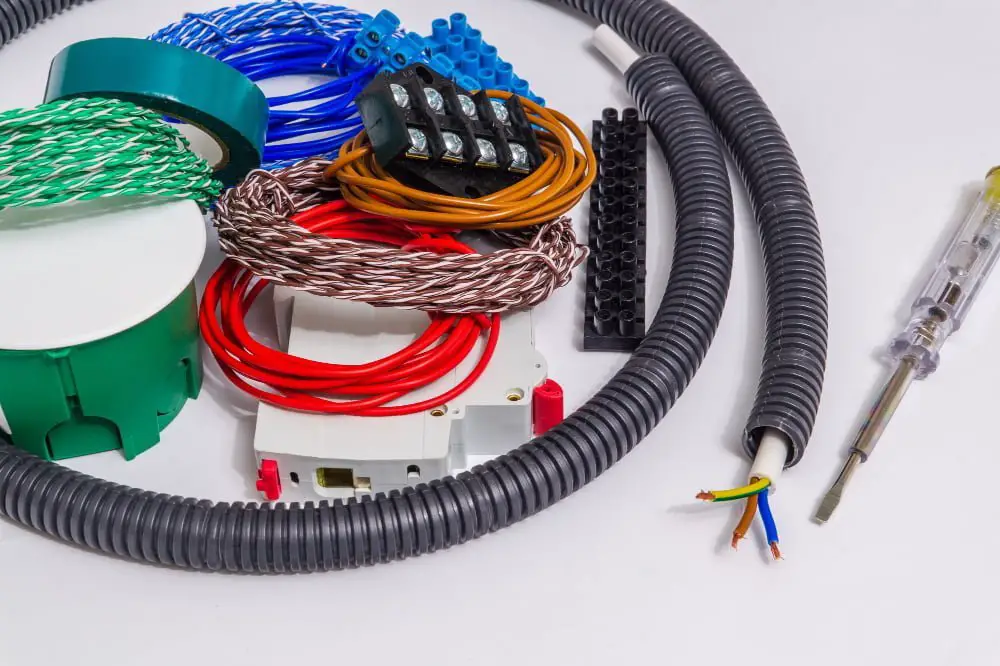
This material has gained popularity in various industries due to its unique combination of properties, including chemical resistance, dimensional stability, and flame retardancy. PPS can withstand continuous use at temperatures up to 240°C without significant deformation or degradation.
One of the main benefits of PPS is its exceptional strength and stiffness. It has a high modulus of elasticity that makes it ideal for applications where rigidity and durability are critical factors.
PPS offers excellent electrical insulation properties which make it suitable for electronic components such as connectors and switches.
Another advantage of using PPS is its outstanding chemical resistance against acids, bases, solvents as well as hydrocarbons like gasoline or diesel fuel making it an ideal choice for automotive parts exposed to harsh environments.
Polyimide (PI) Characteristics and DuPont™ Vespel®
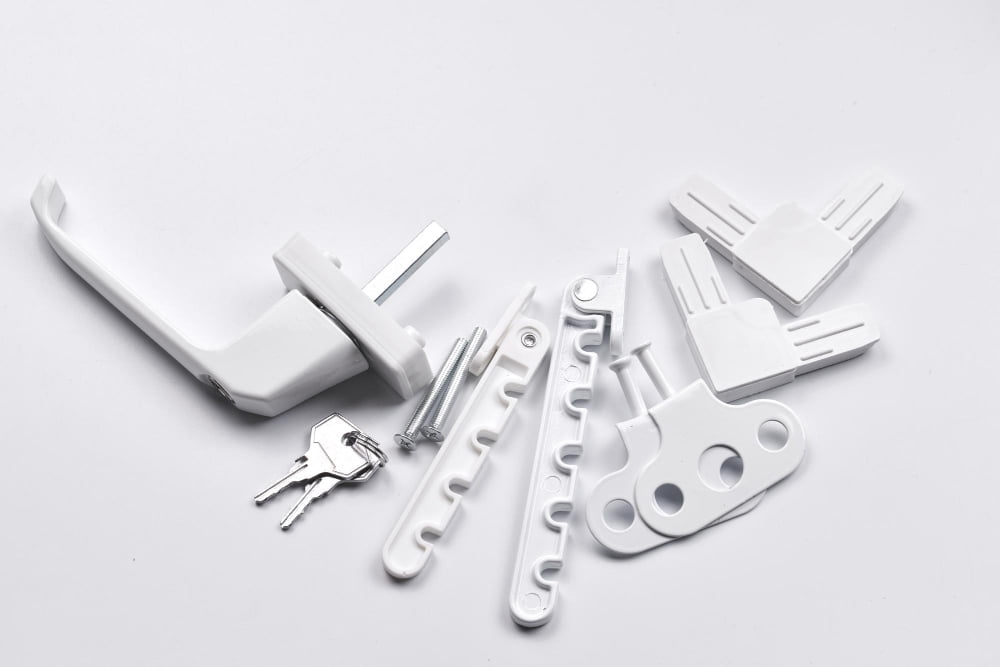
It is widely used in the aerospace industry for its ability to withstand extreme temperatures and harsh environments. One of the most popular brands of PI is DuPont™ Vespel®, which has been trusted by engineers for over 50 years.
DuPont™ Vespel® offers exceptional mechanical properties at elevated temperatures, making it ideal for use in applications such as bearings, seals, bushings, and other critical components where reliability is paramount. Its unique combination of strength and toughness allows it to maintain dimensional stability even under heavy loads or prolonged exposure to heat.
In addition to its superior performance characteristics, DuPont™ Vespel® also boasts excellent wear resistance properties that make it an attractive choice for demanding industrial applications. Its low coefficient of friction ensures smooth operation while reducing energy consumption.
Acrylic: Pros and Cons
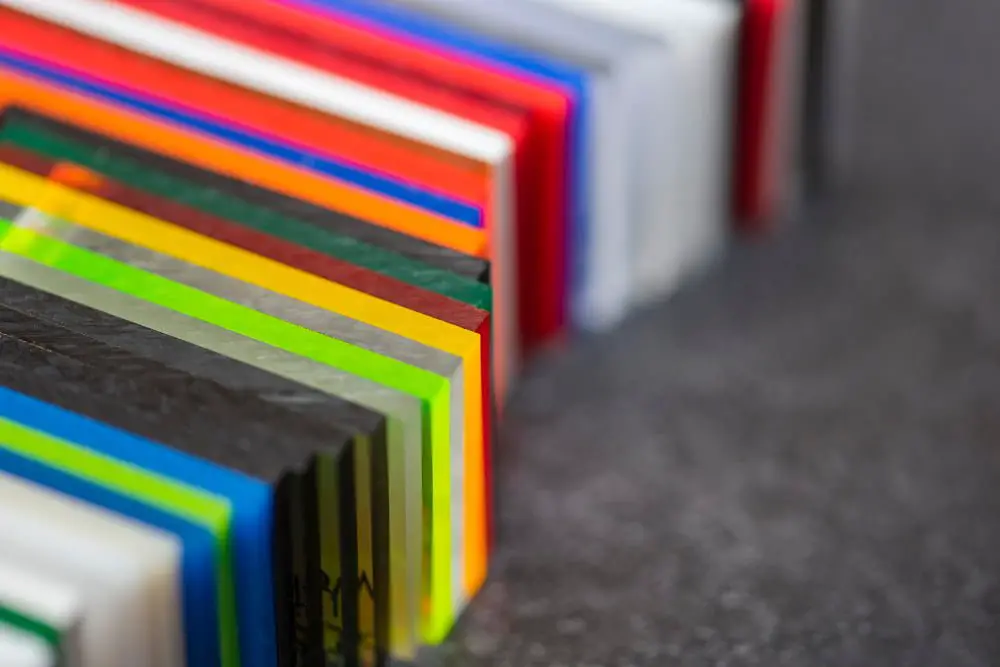
It is widely recognized for its excellent optical clarity, high impact resistance, and weatherability. However, like any other material, acrylic has its pros and cons.
Pros:
- Optical Clarity: Acrylic offers exceptional transparency with a light transmission of up to 92%, making it an ideal choice for applications where visual aesthetics are crucial.
- Impact Resistance: Acrylic is highly resistant to impact compared to glass or other plastics of similar thicknesses.
- Weatherability: This plastic can withstand exposure to UV radiation without yellowing or becoming brittle over time.
- Machinability: Acrylic can be easily machined using standard tools such as saws and drills.
Cons:
- Scratch Sensitivity: Although acrylic resists shattering upon impact better than glass does when scratched repeatedly with abrasive materials; it may develop scratches that could affect the appearance of the product over time if not handled carefully.
- Thermal Expansion Coefficient – The thermal expansion coefficient of PMMA varies depending on temperature changes which may cause dimensional instability in some cases
- Chemical Resistance – PMMA exhibits poor chemical resistance against solvents such as acetone
Despite these limitations mentioned above; acrylic remains one of the most versatile materials available today due to its unique combination of properties.
Polyvinyl Chloride (PVC): Advantages and Disadvantages

It is known for its versatility, durability, and cost-effectiveness. PVC can be found in various applications such as pipes, flooring materials, electrical cables insulation and more.
Advantages: One of the main advantages of PVC is its low cost compared to other polymers like polycarbonate or polyetherimide. It’s easy to process and can be molded into different shapes without losing its properties.
Another advantage of PVC is that it’s resistant to chemicals like acids or bases which makes it suitable for use in chemical processing plants. Moreover,PVC has good weatherability characteristics making it ideal for outdoor applications where exposure to sunlight may cause degradation over time.
Disadvantages: Despite all these benefits there are some disadvantages associated with using PVC as well. One major concern about this material relates to environmental issues because during production dioxins are released which have been linked with cancer development.
Furthermore,PVC products tend not last long when exposed directly under UV light due their poor resistance against ultraviolet radiation leading them becoming brittle over time.
Polydicyclopentadiene (pDCPD): Benefits and Drawbacks
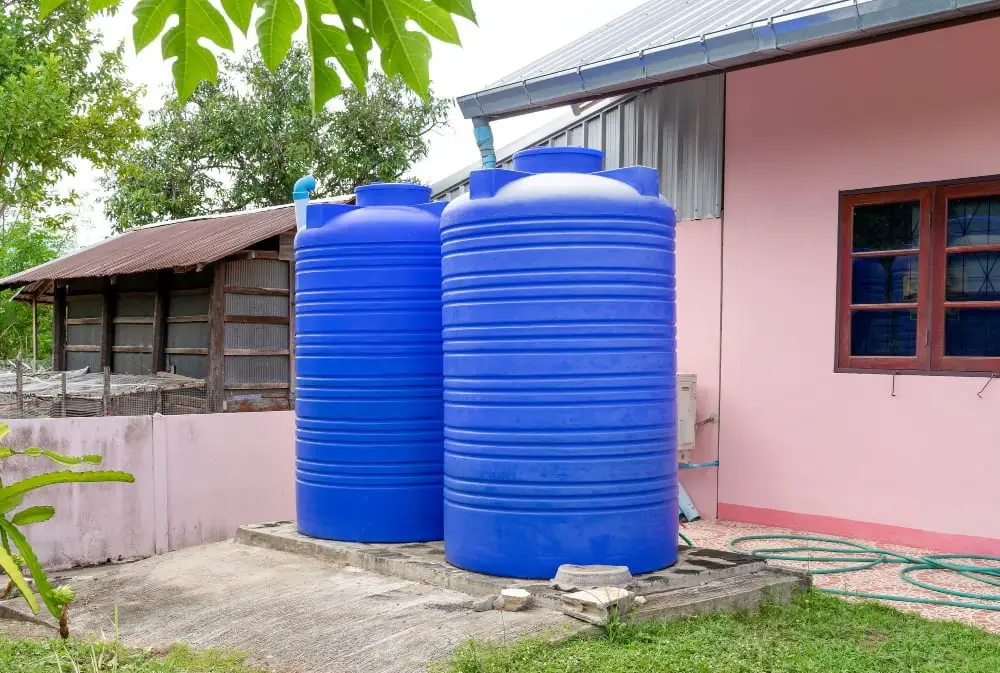
It is commonly used in the automotive, construction, and marine industries for applications such as bumpers, fenders, grilles, manhole covers and water tanks.
One of the main benefits of pDCPD is its ability to withstand high temperatures without deforming or breaking down. This makes it an ideal material for use in harsh environments where other plastics would fail.
PDCPD has excellent chemical resistance properties which make it resistant to corrosion from acids and other chemicals.
However, there are also some drawbacks associated with using pDCPD. One major drawback is that it can be difficult to process due to its high viscosity when heated which can lead to longer cycle times during production.
Another issue with this material is that it cannot be recycled like many other plastics because once cured; they become a solid mass making them impossible or very difficult to melt down again.
Aluminum Composite Material (ACM)
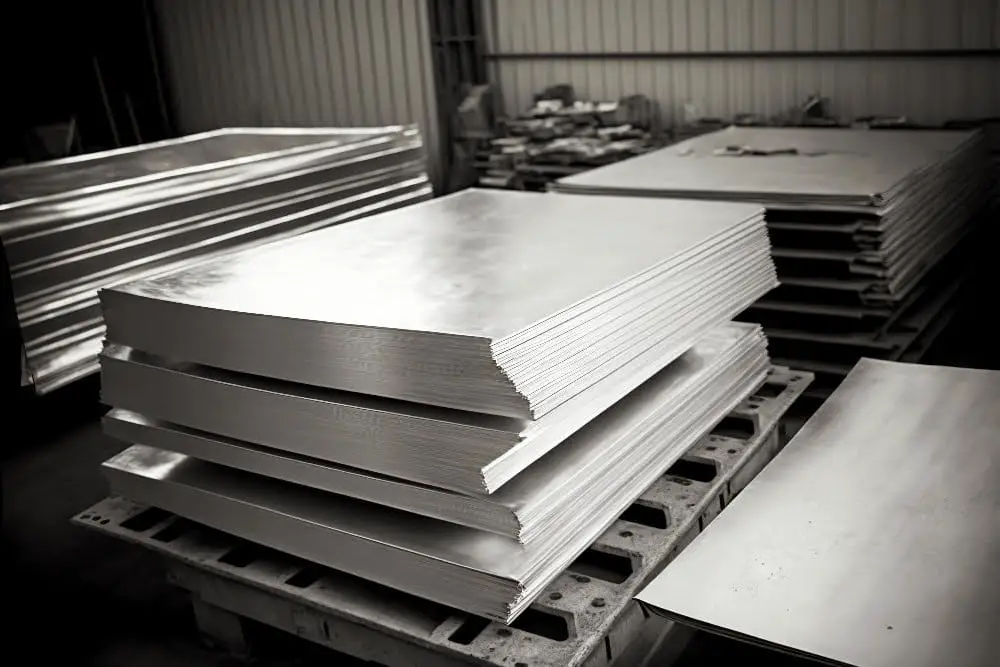
ACM consists of two thin aluminum sheets bonded to a non-aluminum core, typically made of polyethylene or fire-resistant mineral-filled material. This sandwich-like structure provides excellent rigidity, impact resistance, and weatherability while maintaining its flatness over time.
One significant advantage of ACM is its versatility in terms of color options and finishes. The surface can be coated with various paints or metallic finishes to achieve the desired aesthetic effect without compromising performance.
It can be easily fabricated into different shapes using standard woodworking tools such as saws or routers.
ACM’s creep resistance properties make it an ideal choice for applications where long-term stability is critical, such as building facades or signage systems exposed to harsh environmental conditions like wind loads or temperature fluctuations.
CE Canvas Phenolic
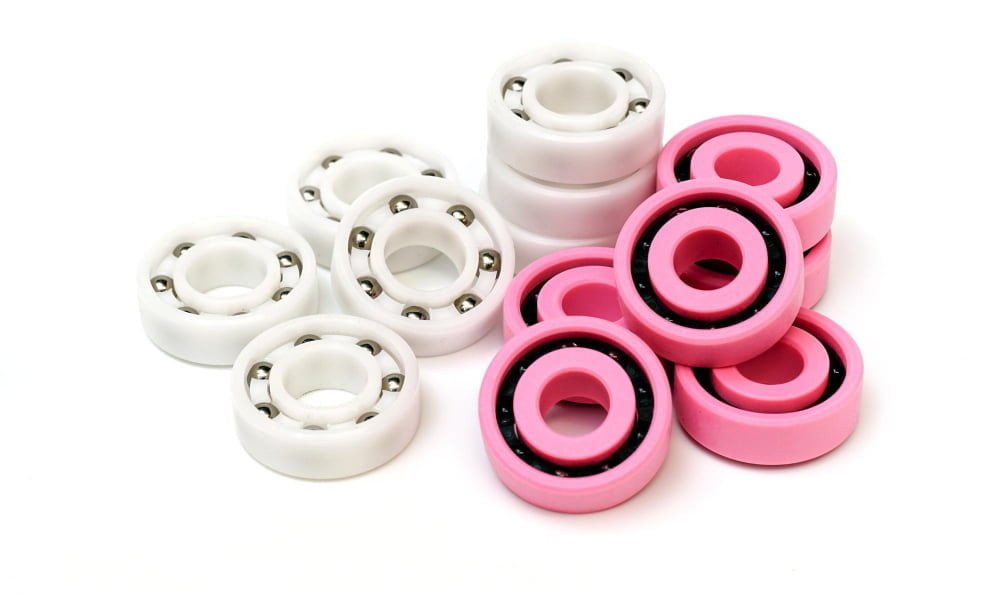
It is made by impregnating layers of canvas cloth with phenolic resin and then compressing them under high pressure and temperature. The result is a strong, durable material that can withstand heavy loads without deforming over time.
CE Canvas Phenolic finds its use in various applications such as gears, bearings, electrical insulators, bushings and other mechanical parts where high strength and dimensional stability are required. Its ability to resist deformation even under extreme conditions makes it an ideal choice for demanding industrial environments.
One notable feature of CE Canvas Phenolic is its low coefficient of thermal expansion which means it does not expand or contract much when exposed to changes in temperature. This property makes it suitable for use in precision instruments where dimensional accuracy must be maintained over a wide range of temperatures.
ECTFE Ethylene Chlorotrifluoroethylene
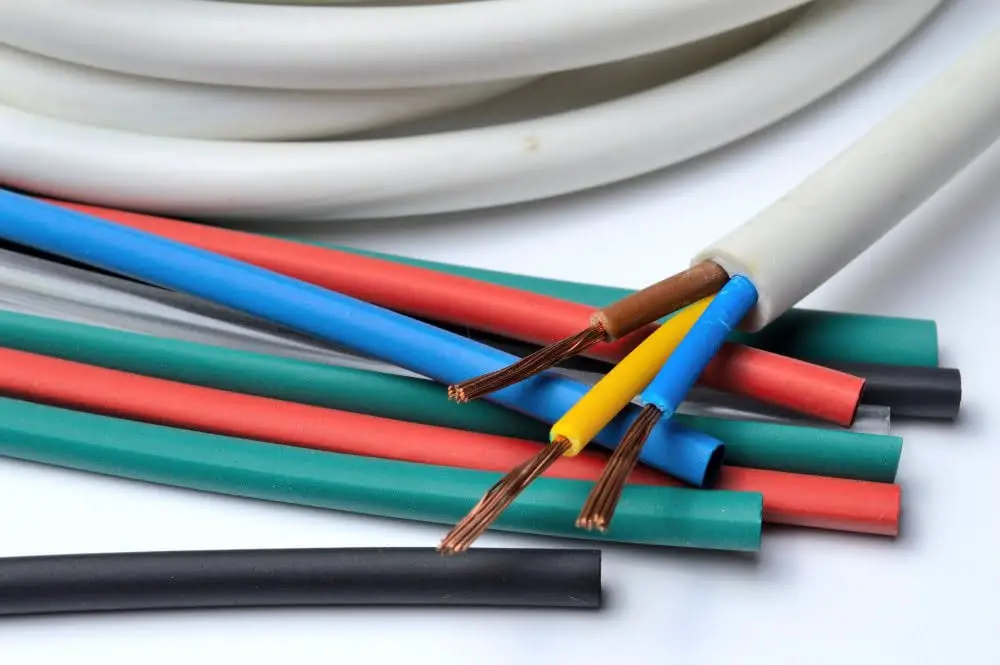
This polymer has exceptional chemical and thermal resistance, which makes it suitable for use in harsh environments where other materials may fail. ECTFE is commonly used in the construction of chemical processing equipment, as well as electrical components such as wire insulation and cable jackets.
One of the key benefits of ECTFE is its ability to withstand prolonged exposure to chemicals without degrading or losing its mechanical properties. It can resist a wide range of acids, bases, solvents and oxidizing agents at elevated temperatures up to 150°C (302°F).
This material has low flammability characteristics due to its high limiting oxygen index (LOI), making it suitable for fire-retardant applications.
Another advantage offered by ECTFE over other polymers like PTFE or FEP lies on its superior abrasion resistance which allows longer service life under abrasive conditions.
Expanded PVC Material
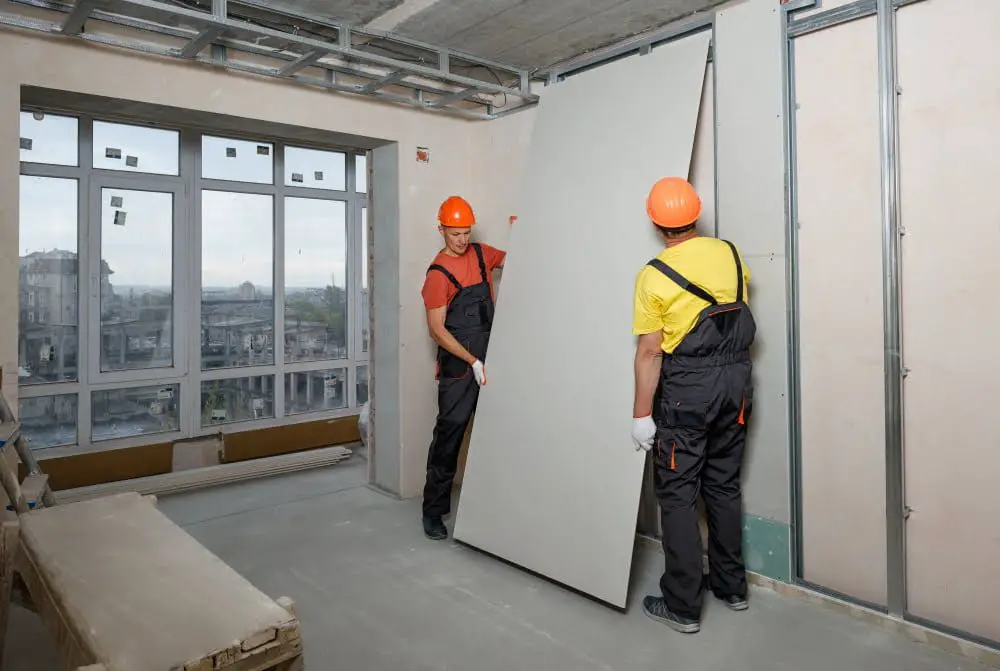
It is made by expanding polyvinyl chloride (PVC) foam sheets, which results in a rigid yet flexible material with low water absorption and good thermal insulation. Expanded PVC can be easily cut, shaped, drilled or printed on making it ideal for various applications such as signage, displays, exhibits and more.
One of the key benefits of expanded PVC is its high strength-to-weight ratio which makes it an attractive alternative to heavier materials like wood or metal. Its closed-cell structure provides superior moisture resistance compared to other foams making it suitable for outdoor use.
G10/FR-4 Glass Epoxy
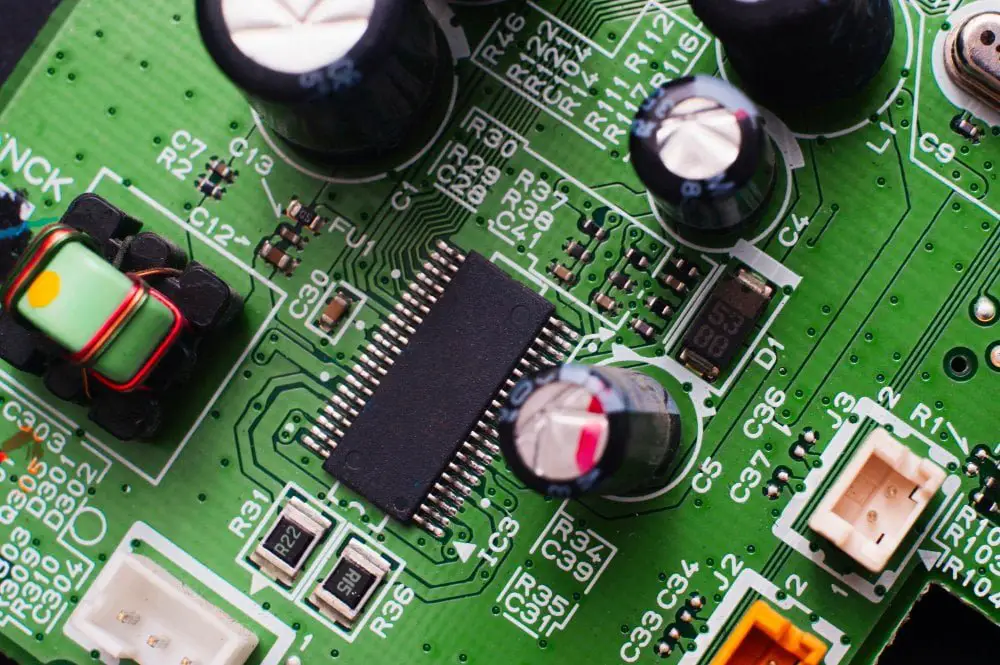
It is known for its excellent electrical insulation properties, high strength, and resistance to moisture, chemicals, and heat. This type of creep-resistant plastic finds extensive use in the aerospace industry for manufacturing structural components such as circuit boards, insulators, gaskets or washers.
The G10/FR-4 Glass Epoxy’s ability to withstand extreme temperatures makes it ideal for applications that require thermal stability. Its low coefficient of thermal expansion ensures dimensional stability even under varying temperature conditions.
Moreover, this material has good machinability which allows it to be easily cut into various shapes without compromising its mechanical properties. The combination of these features makes G10/FR-4 Glass Epoxy a popular choice among engineers who need reliable materials that can perform well under harsh environments.
GPO-3 Thermoset Polyester
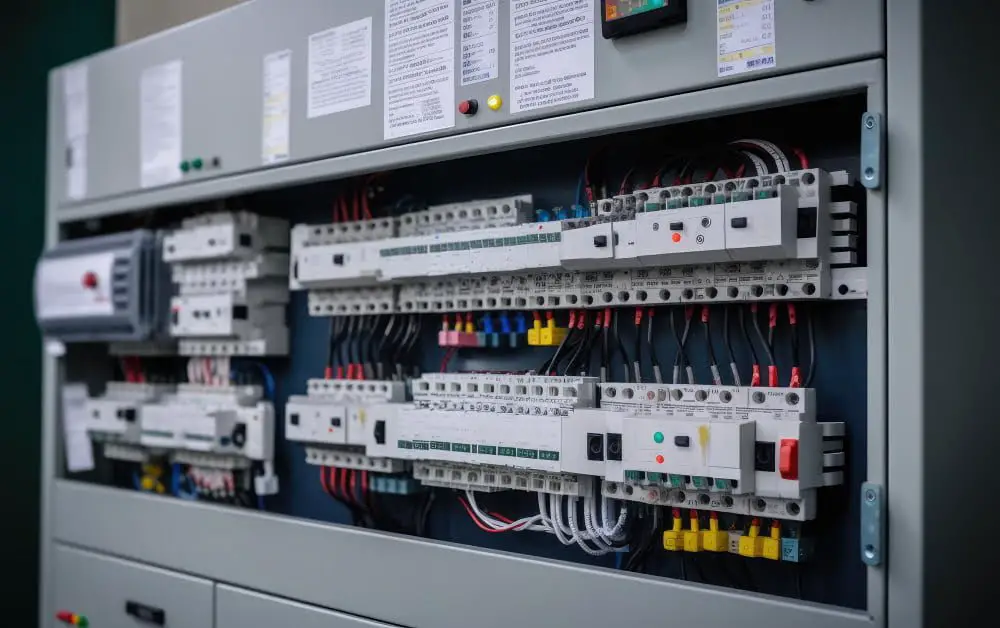
It is commonly used in electrical applications such as switchgear components, bus bar supports, and insulators due to its superior dielectric properties. GPO-3 also has good flame-retardant properties which make it ideal for use in fire-resistant applications.
One of the key advantages of GPO-3 over other thermoset materials is its ability to withstand high temperatures without losing its structural integrity or dimensional stability. This makes it an excellent choice for use in harsh environments where extreme heat or cold may be present.
In addition to being highly resistant to creep deformation under load, GPO-3 also exhibits low water absorption rates which help maintain its physical properties even when exposed to moisture over extended periods of time.
High Impact Polystyrene (HIPS)
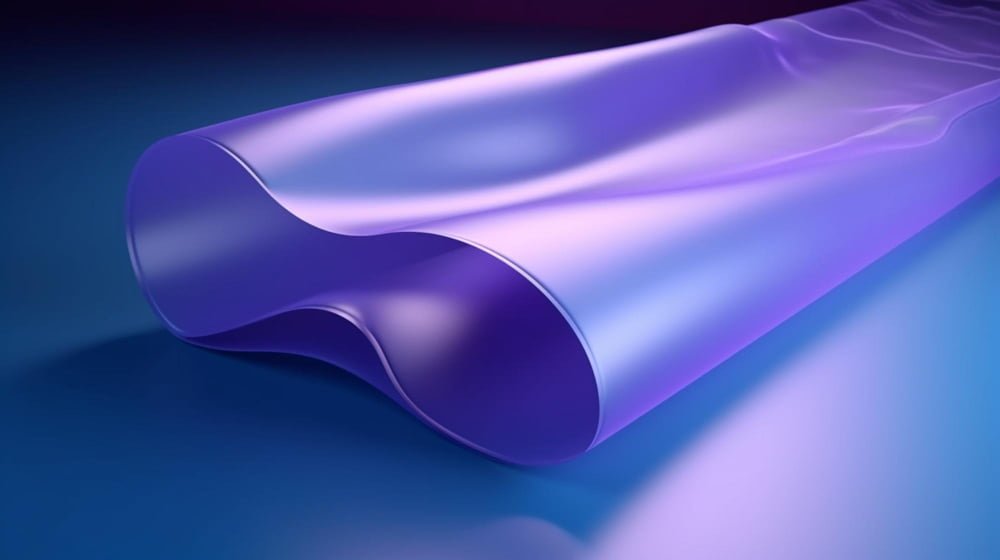
It is widely used in the construction industry for various applications, including packaging, toys, and household appliances. HIPS has high impact strength and good dimensional stability even under constant load or stress conditions.
One of the reasons why HIPS is so effective at resisting creep deformation is its unique molecular structure. The polymer chains are tightly packed together with very little free space between them.
This makes it difficult for the chains to slide past each other when subjected to external forces.
Another advantage of using HIPS in construction projects is its affordability compared to other engineering plastics such as polycarbonate or polyetherimide (Ultem® PEI). Despite being relatively inexpensive, it still offers excellent mechanical properties that make it suitable for many different applications.
In addition to its superior creep resistance and cost-effectiveness, HIPS can also be easily processed through injection molding or extrusion techniques into complex shapes without losing any of its desirable properties.
KYDEX® Thermoplastic Sheet
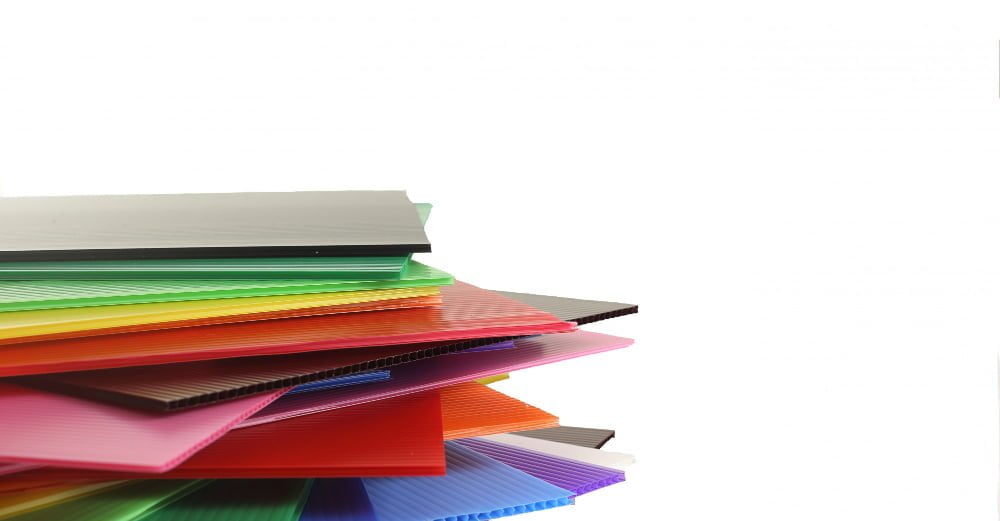
This thermoplastic sheet has excellent impact resistance, chemical resistance, and fire retardancy properties. It also offers superior formability, making it easy to mold into complex shapes without sacrificing its structural integrity.
One of the key advantages of KYDEX® is its ability to resist creep deformation over time. Its low coefficient of linear thermal expansion (CLTE) ensures dimensional stability even under varying temperature conditions.
KYDEX® sheets are available in a wide range of colors and textures that can be customized according to specific design requirements.
KYDEX® thermoplastic sheets have found applications across various industries such as aerospace, transportation equipment manufacturing, medical devices production among others due to their exceptional performance characteristics.
LE Linen Phenolic
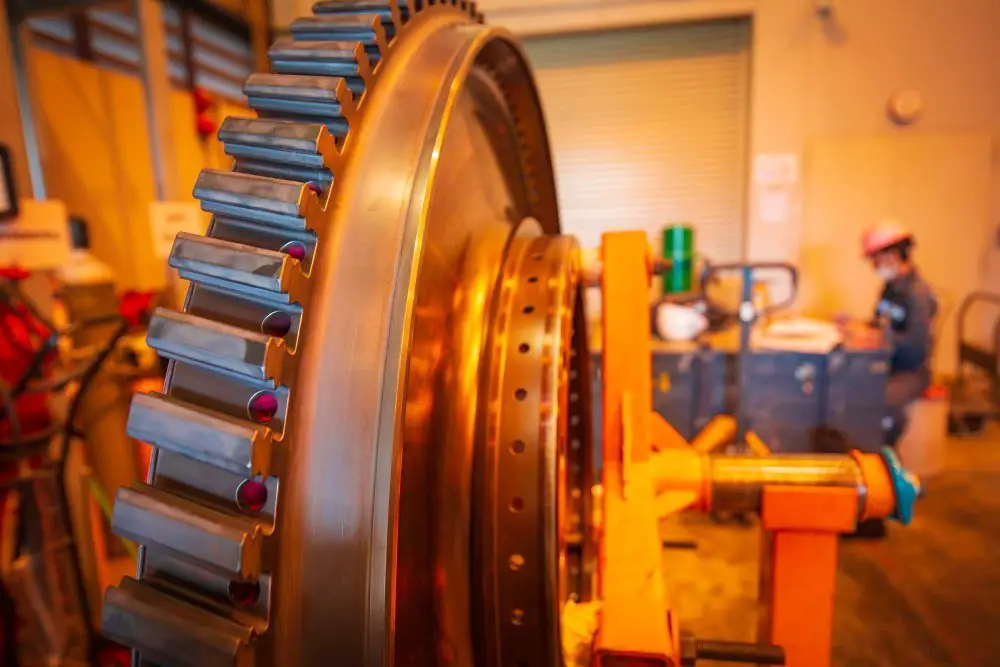
It is made by impregnating layers of linen fabric with phenolic resin, which is then cured under high pressure and temperature to form a hard, durable material. LE Linen Phenolic has been used in various applications such as electrical insulators, gears, bearings, bushings and other mechanical parts where high strength and wear resistance are required.
One of the key advantages of LE Linen Phenolic over other materials like metals or ceramics is its ability to withstand constant stress without deforming or breaking down over time due to creep. This makes it an ideal choice for applications that require long-term durability even under harsh conditions.
In addition to its exceptional creep resistance properties, LE Linen Phenolic also offers good electrical insulation properties making it suitable for use in electrical components such as switchgear panels or transformers.
Noryl® Modified PPO
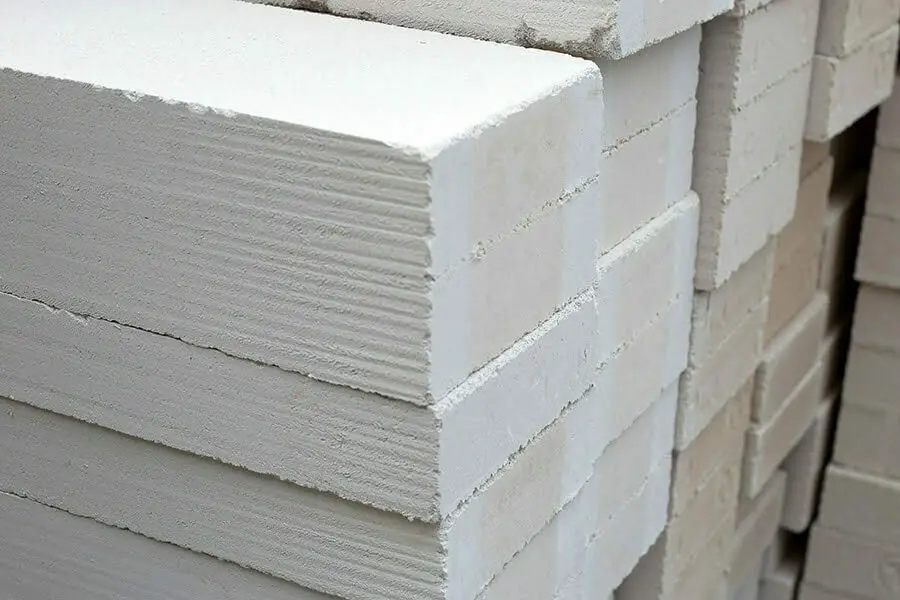
It is a blend of polyphenylene oxide (PPO) and polystyrene (PS), which gives it unique properties that make it ideal for various applications in the automotive, electrical/electronics, and industrial sectors.
One of the key benefits of Noryl® Modified PPO is its exceptional creep performance. This material can withstand prolonged exposure to stress or load without deforming or losing its shape over time.
Its low coefficient of thermal expansion also makes it an excellent choice for parts that require tight tolerances.
In addition to its mechanical properties, Noryl® Modified PPO has good chemical resistance against acids, bases, alcohols as well as hydrocarbons such as oils and fuels. This makes it suitable for use in harsh environments where other materials may fail due to corrosion or degradation.
The automotive industry uses Noryl® Modified PPO extensively in under-the-hood components such as engine covers because they need materials with high heat deflection temperatures while maintaining their structural integrity even at elevated temperatures. Moreover, the electrical/electronics sector utilizes this material mainly because of its superior dielectric strength making them perfect insulators.
Nylon and Its Creep Resistance
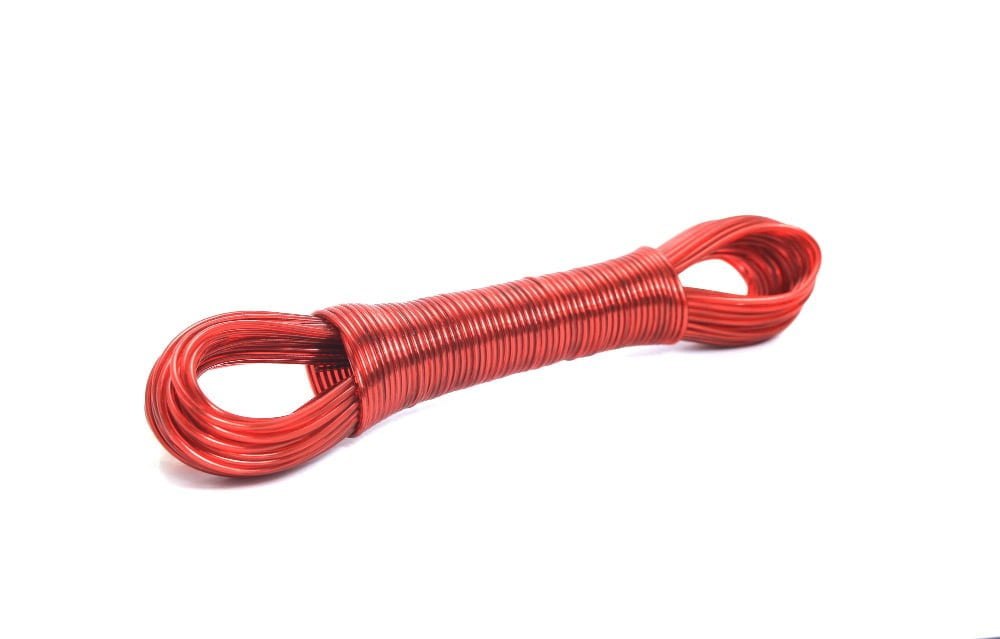
It is widely used in various applications such as automotive parts, electrical components, and consumer goods. One of the key advantages of nylon is its creep resistance.
Creep-resistant nylons are designed to withstand long-term stress or load without deforming or losing their shape over time. This makes them ideal for use in structural components where dimensional stability and reliability are critical factors.
The creep resistance of nylon depends on several factors such as molecular weight, crystallinity level, temperature exposure duration under load conditions among others. Nylon 6/6 (PA66) has been found to have better creep performance than other types like Nylon 6 (PA6).
In addition to its superior mechanical properties and good chemical resistance against oils & greases; it’s also lightweight which makes it an attractive option for many industries looking for durable yet lightweight materials.
PAI Polyamide-imide
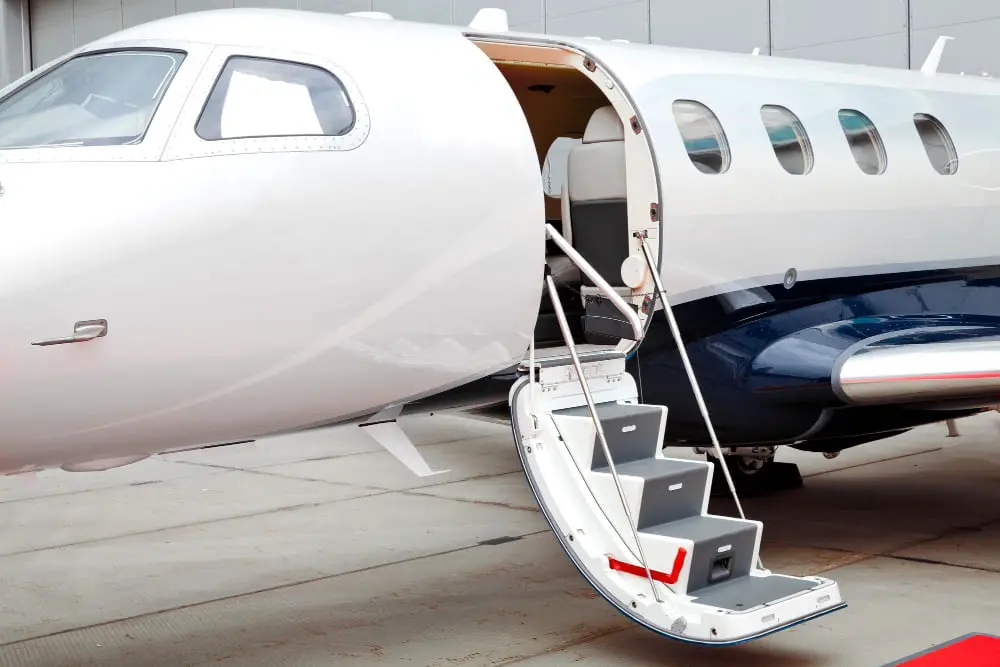
This polymer has exceptional mechanical strength and stiffness, making it ideal for use in demanding applications such as aerospace, automotive, and electronics industries. PAI also offers good chemical resistance to acids and bases.
One of the key advantages of PAI is its ability to maintain dimensional stability over time. It can withstand prolonged exposure to heat without deforming or losing its shape.
This makes it an attractive option for parts that require tight tolerances or need to maintain their shape under load.
Another benefit of PAI is its low coefficient of thermal expansion (CTE). CTE refers to how much a material expands or contracts with changes in temperature.
A low CTE means that the material will experience minimal dimensional changes when exposed to temperature fluctuations.
PAI has excellent wear resistance properties due to its high hardness level and low friction coefficient compared with other polymers like PEEK or PEK.
PBT Polybutylene Terephthalate
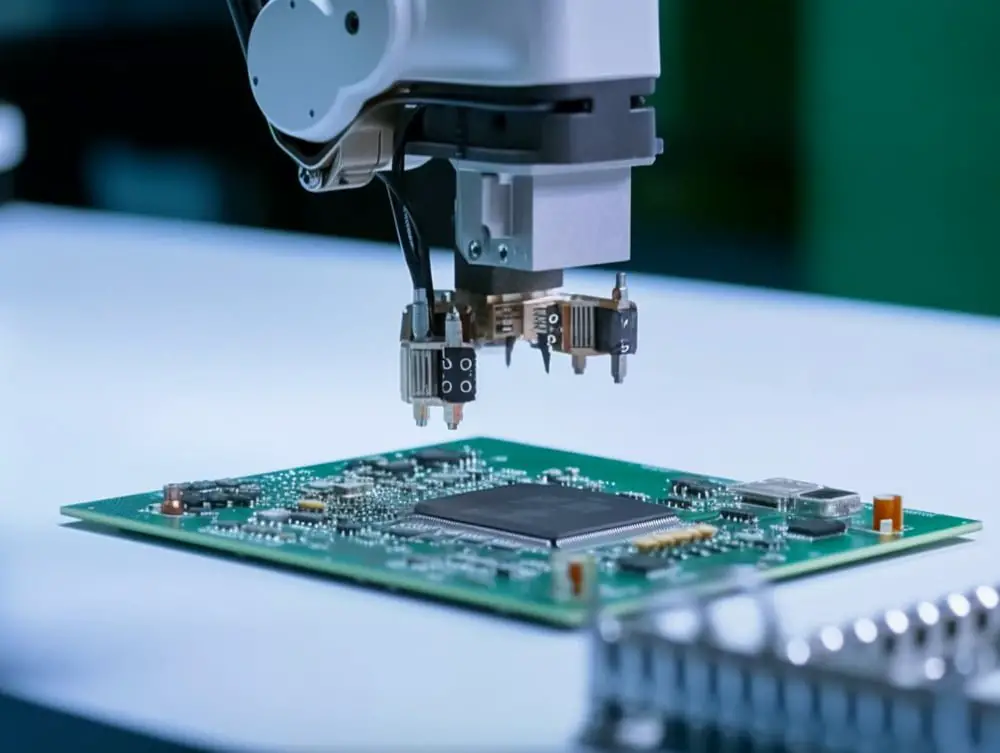
PBT has a unique combination of properties such as good dimensional stability, low moisture absorption, and high strength. It also offers excellent electrical insulation properties and can withstand temperatures up to 150°C.
One of the most significant advantages of PBT is its ability to maintain its shape over time without deforming or breaking down under stress. This makes it an ideal material for use in automotive parts such as gears, bearings, and housings where constant exposure to heat and pressure can cause other materials to fail.
In addition to automotive applications, PBT’s creep-resistant properties make it suitable for use in electronics manufacturing where components are subjected to continuous stress during operation. Its ability to resist deformation ensures that electronic devices remain functional even after prolonged periods of usage.
PCTFE Polychlorotrifluoroethylene
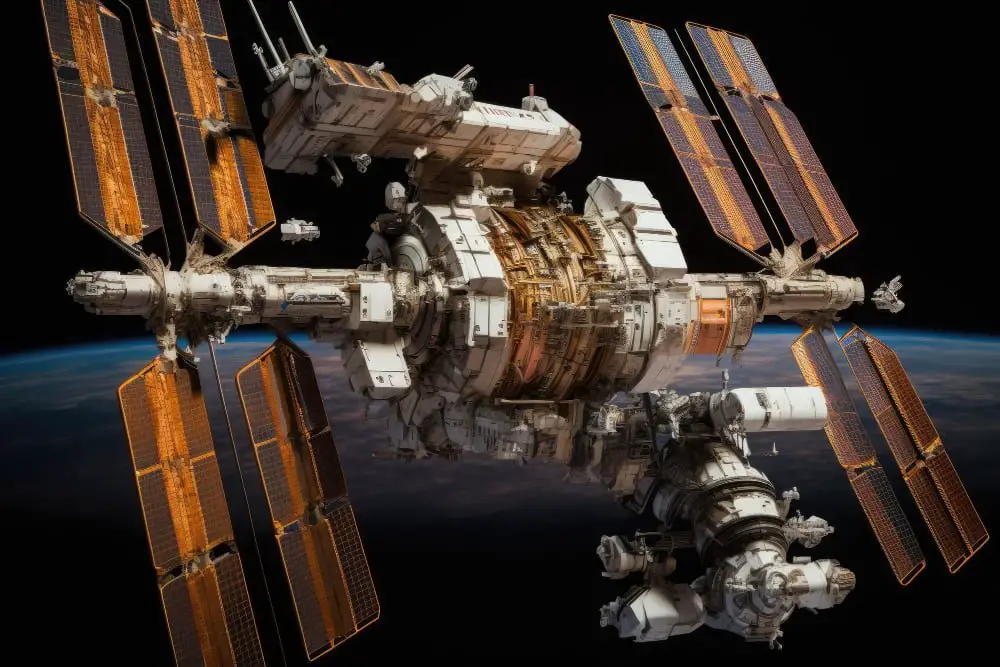
It is a fluoropolymer that has superior chemical and thermal stability compared to other plastics. PCTFE’s unique properties make it an ideal material for use in demanding applications such as aerospace components, electrical insulation parts, and medical devices.
One of the most significant advantages of PCTFE is its low coefficient of friction which makes it suitable for sliding or rotating applications where wear resistance and lubricity are essential. This polymer has exceptional gas barrier properties making it useful in packaging materials used to store sensitive products like pharmaceuticals.
Another benefit of using PCTFE over other polymers like PVC or PETG is its ability to withstand extreme temperatures ranging from -400°F (-240°C) up to 400°F (204°C). This feature makes it an ideal choice for cryogenic storage containers used in laboratories or space exploration missions.
PET: Polyethylene Terephthalate and Creep Performance
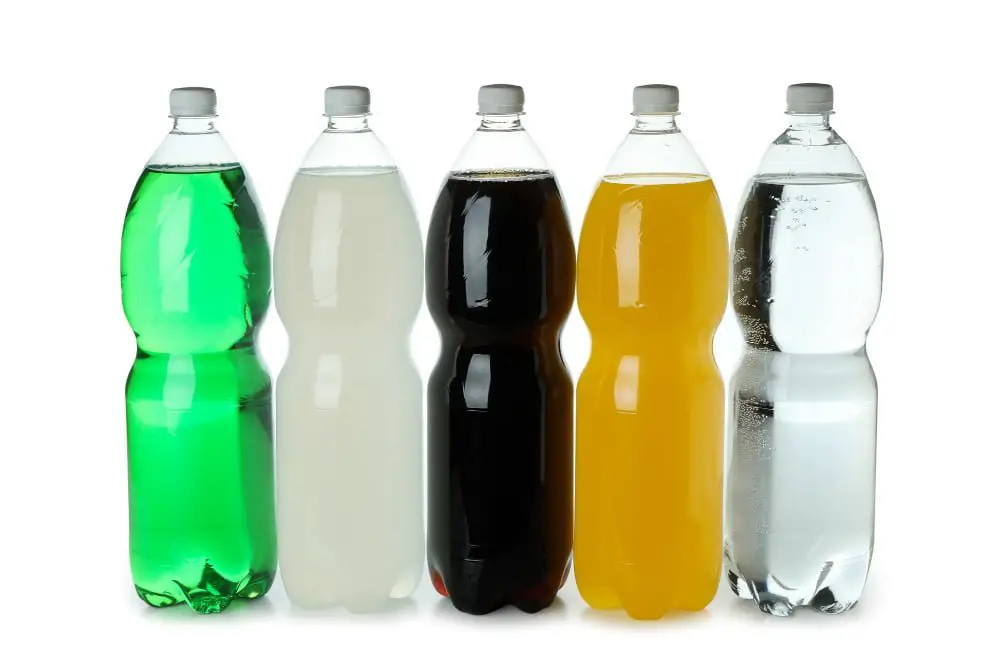
PET is widely used in the production of bottles for carbonated drinks and water due to its high strength-to-weight ratio and durability. It also finds applications in various industries such as textiles, packaging films, automotive parts, and electrical components.
One of the reasons why PET exhibits good creep performance is because it has a highly crystalline structure with strong intermolecular forces between its chains. This makes it resistant to deformation under load over time.
In addition to being creep-resistant, PET also offers other benefits such as chemical resistance against acids and bases; low moisture absorption; good dimensional stability; easy processing through injection molding or extrusion techniques; recyclability (as it can be melted down into new products); and cost-effectiveness compared to other engineering plastics like polycarbonate or PEEK.
PETG: PET Copolyester
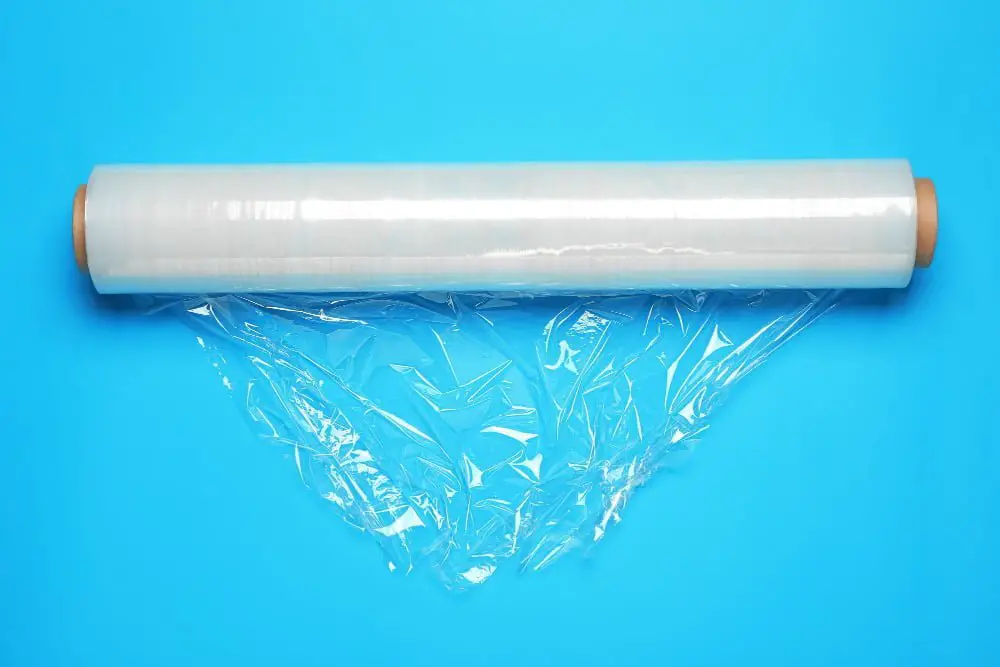
It’s a popular choice for applications where durability and toughness are essential. PETG has high impact strength and can withstand repeated use without cracking or breaking down over time.
One of the unique properties of PETG is its clarity, making it an ideal material for products that require transparency such as packaging materials. It’s easy to process using various manufacturing techniques like injection molding and extrusion.
In construction applications, PETG sheets are used in glazing systems due to their superior impact resistance compared to traditional glass panes. They also offer better insulation properties than glass which makes them suitable for energy-efficient buildings.
Polyester Film and Creep Performance
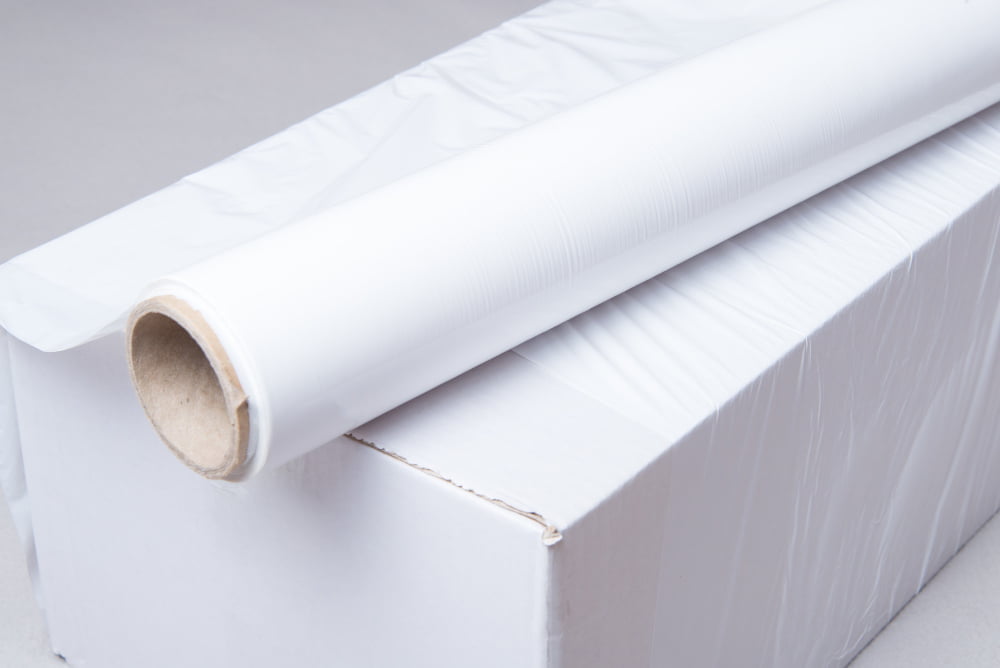
It is known for its excellent mechanical properties such as high tensile strength and dimensional stability. However, like other plastic materials, polyester film can also experience creep under constant stress or load.
The degree of creep in polyester films depends on several factors such as temperature and humidity levels. High temperatures accelerate the rate of deformation while low humidity levels increase the stiffness of the material leading to reduced creep resistance.
To improve its performance against creeping over time when subjected to constant loads or stresses at elevated temperatures (above 50°C), manufacturers have developed specialized grades with enhanced thermal stability that can withstand higher operating conditions without significant deformation.
These advanced grades are designed with additives that help reduce molecular mobility within the polymer matrix hence reducing susceptibility to creeping even under harsh environmental conditions. The result is a more durable product that maintains its shape over extended periods making it ideal for use in demanding applications where dimensional accuracy is critical.
PPSU Polyphenylsulfone
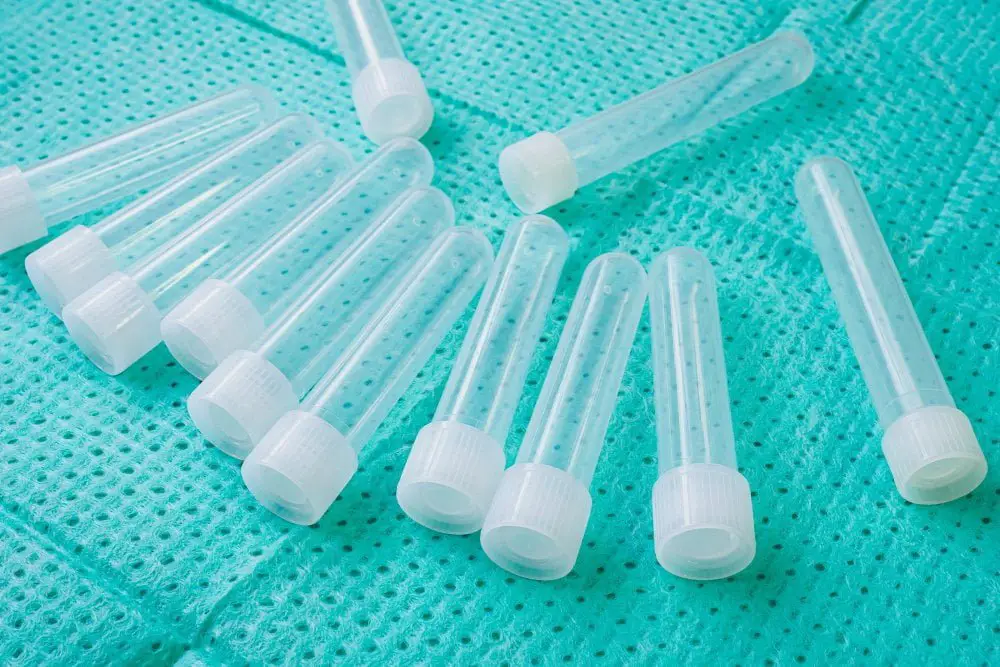
PPSU has superior mechanical properties compared to other amorphous polymers such as polycarbonate and polysulfone. It also offers good chemical resistance, high-temperature stability, and exceptional dimensional stability.
One of the most significant advantages of PPSU is its ability to withstand repeated sterilization cycles without losing its physical or mechanical properties. This makes it an excellent choice for medical devices and equipment that require frequent cleaning or sterilization.
PPSU’s unique combination of strength, toughness, heat resistance, and chemical inertness make it suitable for various industrial applications such as aerospace components like aircraft interiors parts where fire safety standards are critical; automotive parts like fuel system components; electrical insulation materials due to their dielectric strength; plumbing fixtures because they can handle hot water temperatures up to 180°F (82°C); food processing equipment due to their FDA compliance status.
PSU Polysulfone

PSU has a unique combination of properties, including high-temperature resistance, chemical resistance, and dimensional stability. It also offers good electrical insulation properties and can be easily processed using injection molding or extrusion techniques.
One of the most significant advantages of PSU is its ability to maintain its mechanical strength over time under constant load or stress. This makes it an ideal material for components that require long-term durability and reliability such as medical devices, automotive parts, aerospace components among others.
In addition to its exceptional creep performance characteristics at elevated temperatures up to 150°C (302°F), PSU also provides excellent hydrolysis resistance which makes it suitable for use in hot water environments without any degradation in performance.
XX Paper Phenolic Material
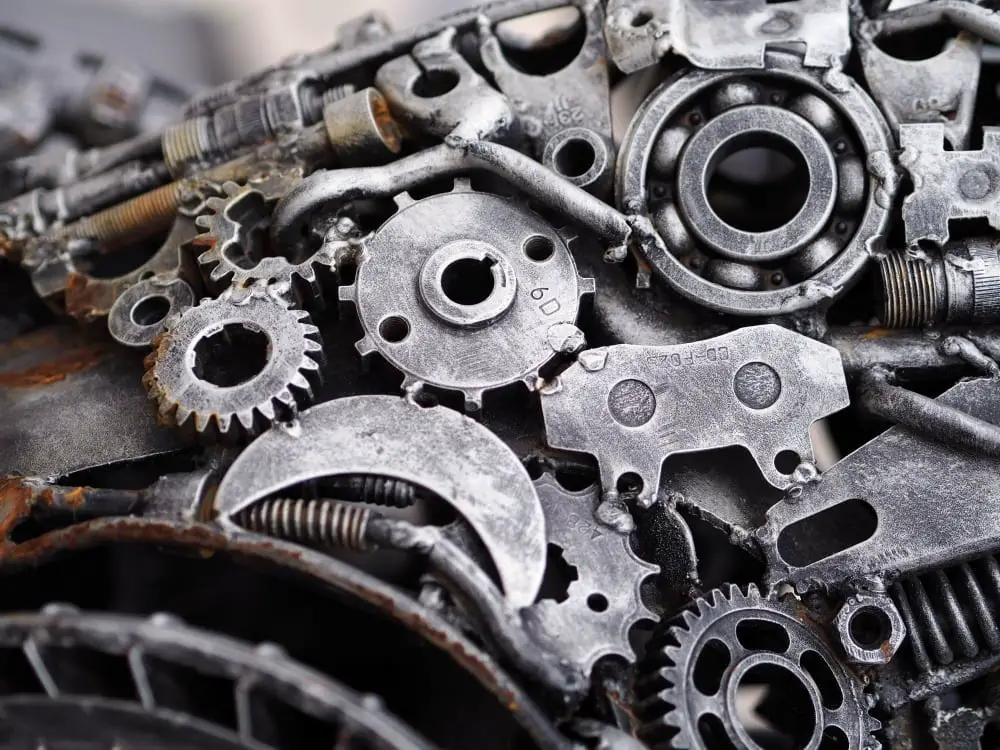
It is made by impregnating layers of paper with phenolic resin, which is then cured under high pressure and temperature to form a hard, dense material. XX Paper Phenolic Material has been used in various applications such as electrical insulators, gears, bearings, bushings and other mechanical parts.
One of the key advantages of XX Paper Phenolic Material over other materials like metals or plastics is its ability to withstand high temperatures without losing its strength or shape. This makes it an ideal choice for applications where heat resistance and dimensional stability are critical factors.
Another advantage of this material lies in its low coefficient of thermal expansion (CTE). CTE refers to how much a material expands when heated up; the lower the CTE value means less expansion occurs during heating up process.
In contrast with metal components that can expand significantly due to changes in temperature causing misalignment issues between mating parts leading into failure on equipment operation; using XX paper phenolics will help reduce these problems since they have very low coefficients compared with metals.
Factors Affecting Creep Resistance
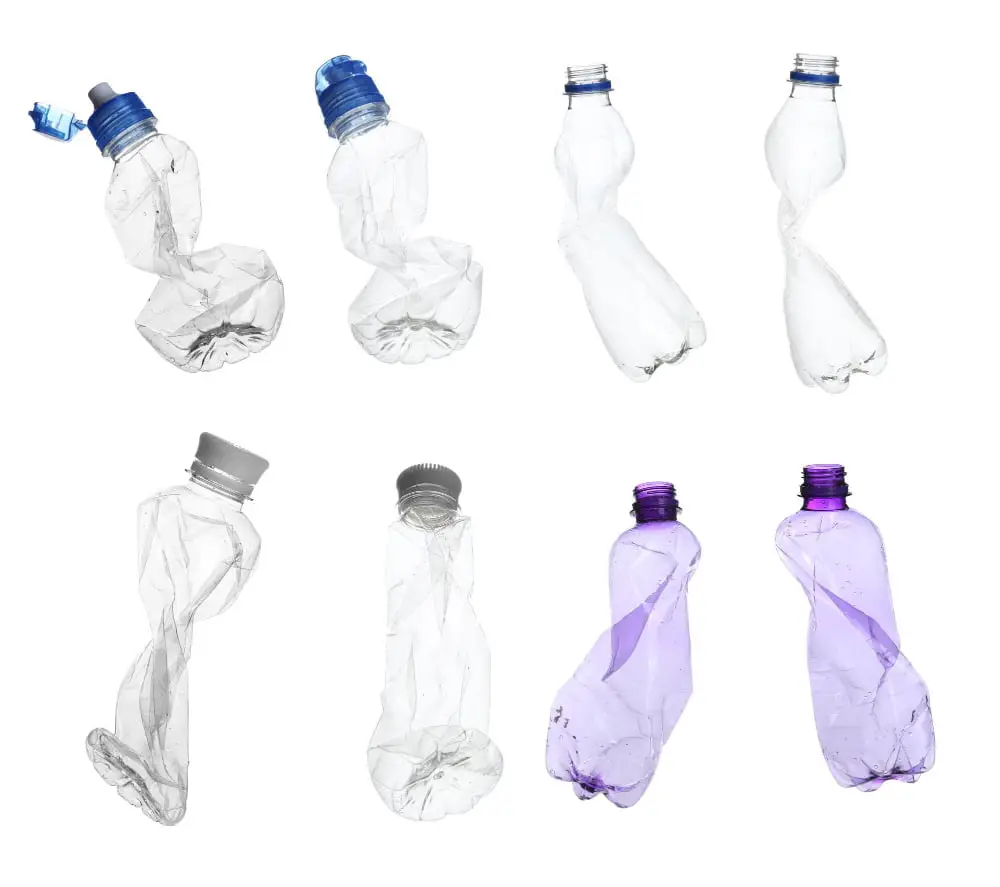
Several factors can affect the creep resistance of polymers, including temperature, humidity, pressure, and chemical exposure. High temperatures tend to accelerate creep by increasing molecular mobility within the material.
Humidity can also weaken plastic structures by promoting hydrolysis or moisture absorption in some cases.
Pressure is another factor that influences creep behavior since it affects how much force a material can bear before deforming permanently over time. Chemical exposure may cause degradation or embrittlement of certain plastics leading to reduced strength and stiffness.
Other factors such as processing conditions during manufacturing (e.g., cooling rate), additives used in formulations (e.g., fillers), and polymer structure (e.g., crystallinity) may also impact the creep performance of plastics.
Understanding these various factors affecting creep resistance is crucial for selecting appropriate materials for specific applications where durability under constant stress or load is required.
Creep Testing Methods
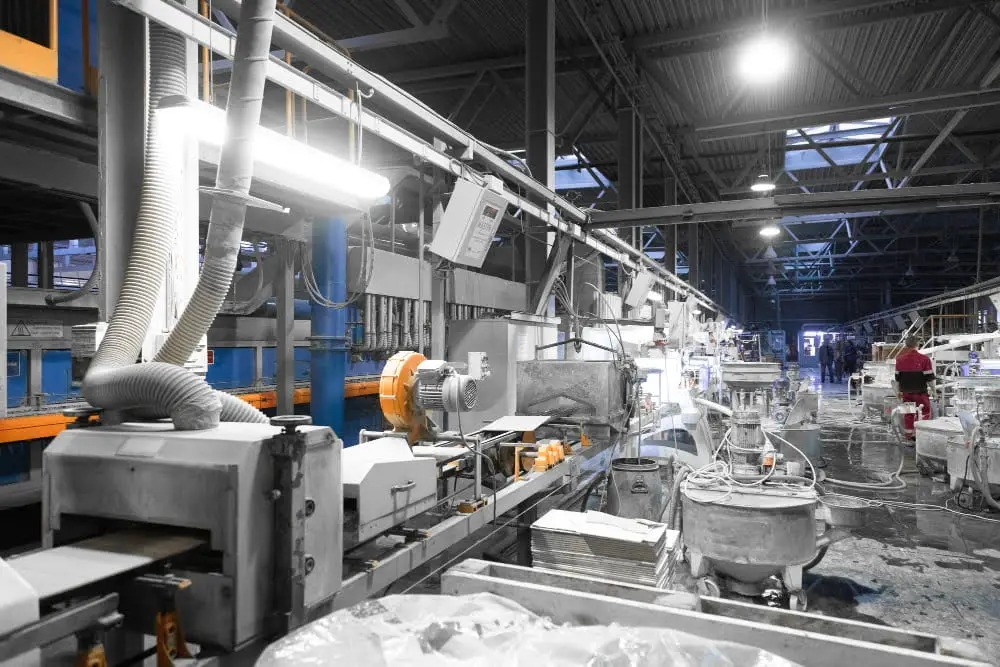
It involves subjecting a material to constant stress or load over an extended period while measuring its deformation. The results obtained from these tests help engineers and designers select the most appropriate materials for their applications.
There are several methods used to test creep resistance, including tensile, compression, flexural, and shear testing. Tensile testing measures how much force is required to stretch a sample until it breaks under constant load conditions.
Compression tests measure how much force is needed to compress a sample until it fails under constant load conditions.
Flexural tests involve bending samples at specific angles while applying loads that cause them to deform over time gradually. Shear tests measure the amount of force required for two parallel surfaces of plastic material subjected perpendicular forces that cause them slide against each other.
The choice of method depends on various factors such as cost-effectiveness, accuracy requirements and availability of equipment among others.
Improving Creep Resistance
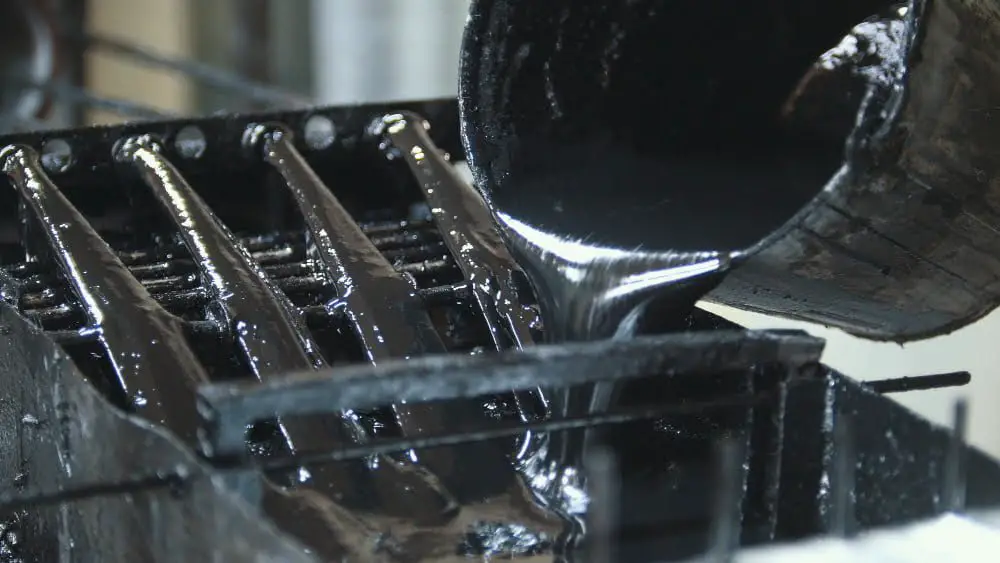
Fortunately, there are ways to improve creep resistance in plastic components. One of the most effective methods is by adding fillers or reinforcements that increase stiffness and reduce deformation under load.
For example, glass fibers or carbon fibers can be added to thermoplastics like polypropylene (PP) or nylon (PA) to enhance their mechanical properties and creep resistance. These reinforced plastics have higher strength-to-weight ratios than traditional materials while maintaining excellent dimensional stability over time.
Another way of improving creep resistance is through cross-linking polymers during manufacturing processes such as radiation curing or chemical crosslinking. This process creates a three-dimensional network structure within the polymer matrix which improves its ability to resist deformation under stress.
Proper design considerations such as reducing sharp corners and edges on parts can also help minimize localized stresses that contribute significantly towards material failure due to creeping effects.
Creep Resistance in 3D Printing
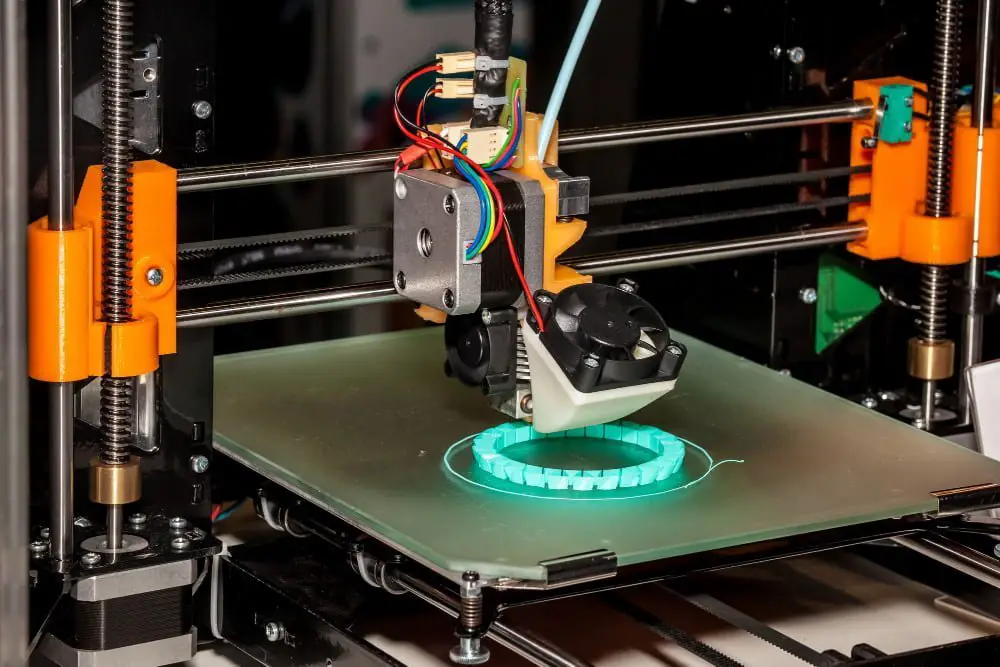
Creep resistance is a crucial factor in 3D printing because printed parts are often subjected to constant stress and load. The use of creep-resistant materials ensures that these parts maintain their shape and structural integrity over time.
One example of a popular material used for 3D printing is polycarbonate (PC). PC offers excellent mechanical properties, including high strength, toughness, and heat resistance.
It also exhibits good creep resistance compared to other thermoplastics such as ABS or PLA.
Another material gaining popularity in 3D printing applications is polyetherimide (PEI), commonly known by its brand name Ultem® PEI. This polymer boasts exceptional thermal stability up to high temperatures while maintaining excellent dimensional stability under load conditions.
Creep testing methods can be applied during the design phase of a part before it goes into production using additive manufacturing techniques like Fused Deposition Modeling (FDM) or Stereolithography Apparatus(SLA). These tests help determine which materials will perform best under specific loading conditions while ensuring optimal performance throughout the product’s lifespan.
Industry Specific Applications
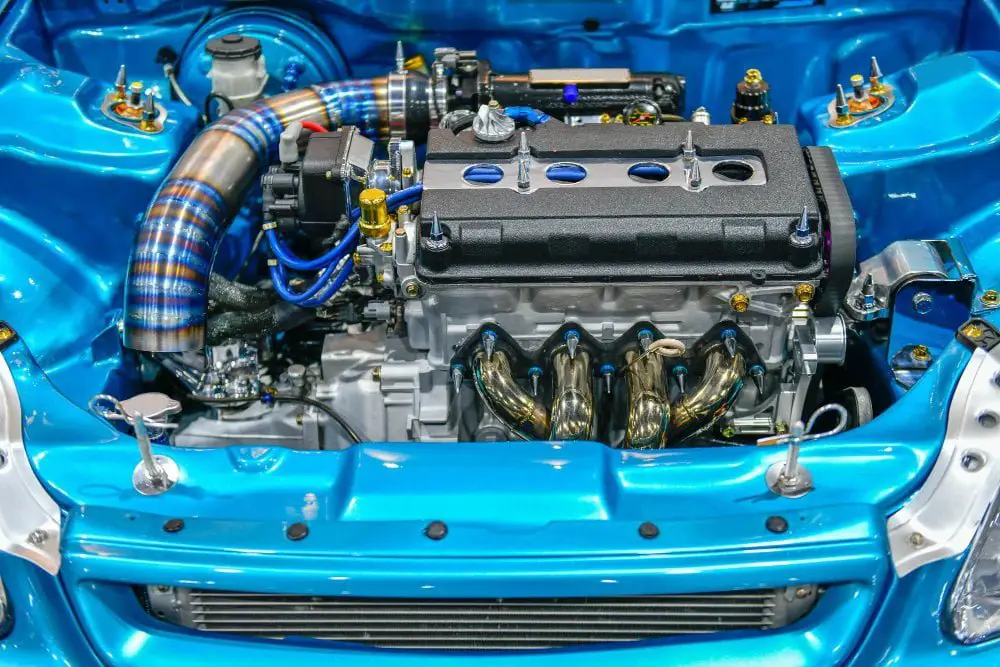
In the automotive industry, these materials are used in engine components such as gears and bearings that require high strength and durability. The aerospace sector also relies on creep-resistant plastics for manufacturing aircraft parts like wing flaps, landing gear doors, and interior cabin panels.
In the construction industry, creep-resistant polymers are used in roofing membranes to provide long-lasting protection against harsh weather conditions. They’re also utilized in window frames due to their excellent thermal insulation properties.
The electronics industry has not been left behind either; manufacturers use these materials for making connectors that can withstand high temperatures without deforming or losing conductivity over time.
Moreover, medical devices such as implants require biocompatible materials with low levels of toxicity and good mechanical performance over extended periods of time – this is where creep-resistant plastics come into play.
Creep-Resistant Plastics and Industrial Applications
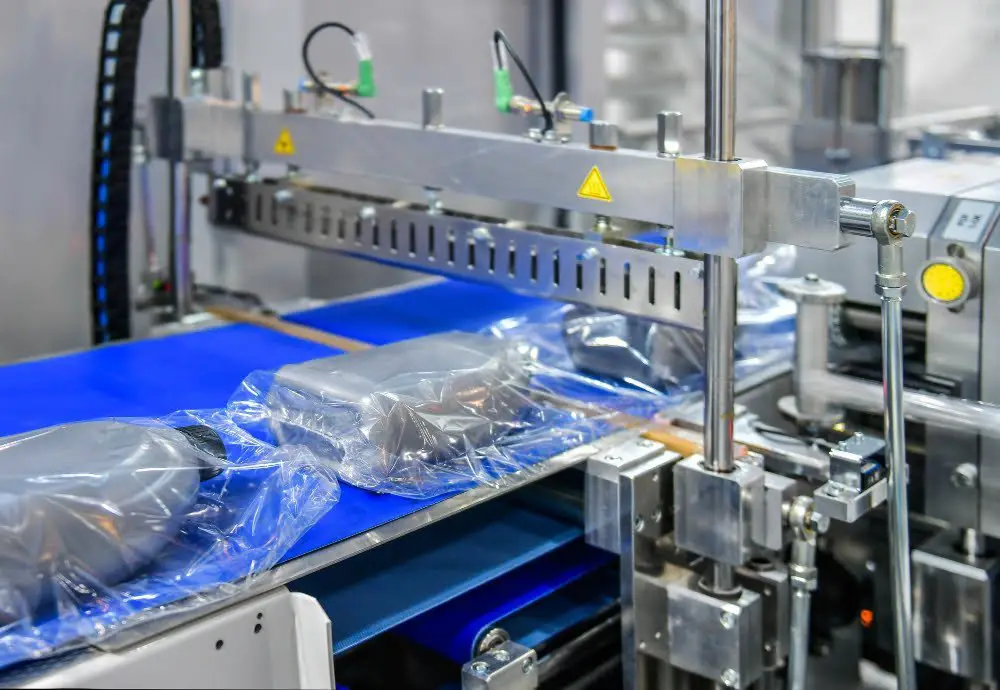
These materials are widely used in the automotive, aerospace, construction, and electronics industries where they play a crucial role in enhancing product performance and safety.
In the automotive industry, creep-resistant plastics are used for manufacturing engine components such as gears, bearings, pumps as well as interior parts like dashboards. The high-temperature resistance of these materials makes them ideal for use under extreme conditions.
Similarly, creep-resistant polymers find extensive application in the aerospace industry where they are utilized to manufacture aircraft components that require high strength-to-weight ratios such as wing structures or landing gear assemblies.
The construction sector also benefits from using creep-resistant plastics since these materials can withstand heavy loads without deforming over time. They can be found in building facades or roofing systems that need to endure harsh weather conditions while maintaining their structural integrity.
Finally yet importantly is the electronics industry which relies on plastic films with excellent dimensional stability even at elevated temperatures.
Environmental Impact
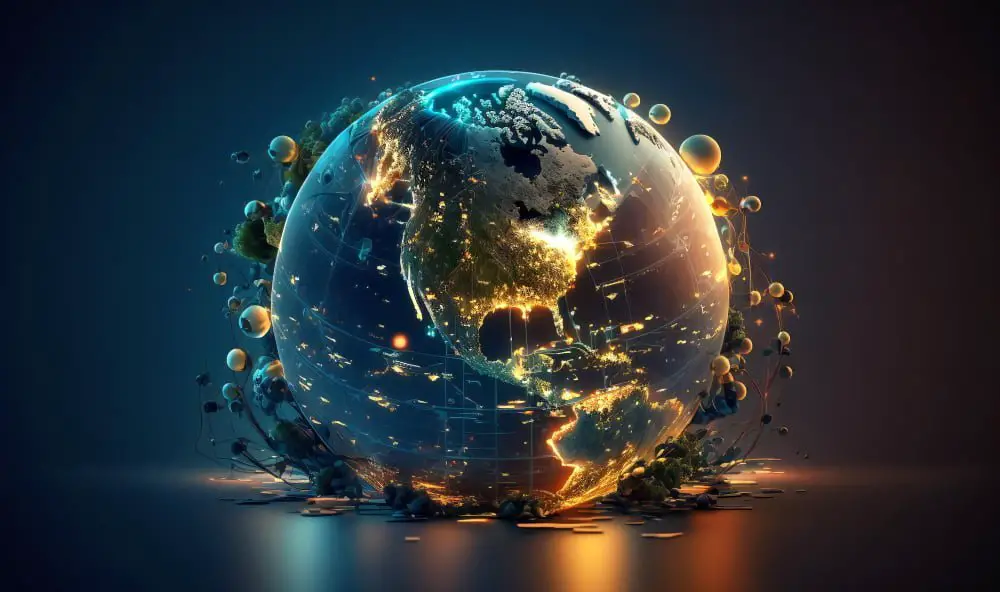
While these materials offer numerous benefits in terms of durability and longevity, they can also have a negative environmental impact if not disposed of properly.
Many types of creep-resistant plastics are recyclable, which is an excellent way to reduce waste and minimize their environmental footprint. However, some polymers may require specialized recycling processes that aren’t widely available or cost-effective.
Some plastic materials used for construction purposes may contain harmful chemicals that can leach into soil or water sources over time. It’s crucial to choose high-quality products from reputable manufacturers who prioritize sustainability and eco-friendliness in their production processes.
Advancements in Creep-Resistant Plastics
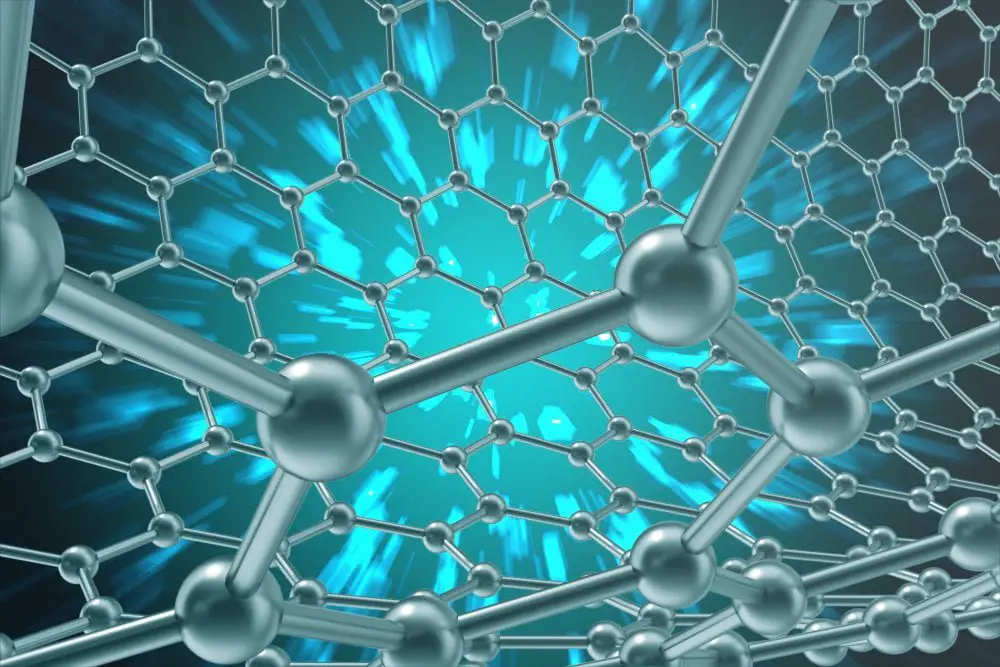
For instance, researchers are exploring the use of nanotechnology to enhance the mechanical properties of polymers, including creep resistance. By incorporating nanoparticles into plastic materials, scientists can create composites with superior strength and durability.
Another area where significant progress has been made is in 3D printing. Creep-resistant plastics are now being used extensively in additive manufacturing applications due to their ability to withstand high temperatures and loads over extended periods without deforming or breaking down.
Moreover, manufacturers are continually improving existing materials by tweaking their chemical composition or processing techniques for optimal performance under specific conditions. This approach has resulted in a wide range of specialized creep-resistant plastics tailored for various industrial applications such as aerospace engineering, automotive manufacturing, medical devices production among others.
In conclusion; advancements continue at an unprecedented pace within this field as more research is conducted on how best we can improve these essential materials’ properties while minimizing environmental impact during production processes.
FAQ
What plastic is best for creep resistance?
The best plastics for creep resistance are acrylic, PVC, and pDCPD, as each has its advantages and disadvantages depending on the intended application.
What is creep resistance plastics?
Creep resistance plastics are materials with a high level of resistance to deformation under prolonged stress, and among them, thermosetting resins generally exhibit better creep resistance than thermoplastic resins.
What is the most creep resistant material?
The most creep resistant material is carbon-fibre and glass-fibre composites, as they exhibit good creep resistance when the fibres carry the applied load.
Is polypropylene creep resistant?
Answer: Polypropylene is not highly creep resistant, as it exhibits a creep deformation of 1.5% at room temperature under a 5 MPa load after one year, compared to polycarbonate’s 0.2% deformation.
How do creep resistant properties vary among different types of plastics?
Creep resistance properties in plastics vary depending on their molecular structure, with some materials exhibiting better long-term resistance to deformation under continuous load than others.
What factors contribute to the development of creep resistance in plastics?
“Incorporating fillers, additives, and blending various polymers are key factors that contribute to the development of creep resistance in plastics.”
How can creep resistance be enhanced in existing plastic materials?
Creep resistance in existing plastic materials can be enhanced by incorporating reinforcements like fibers, fillers, or inorganic nanoparticles.
Role of Temperature in Creep Resistance
The temperature plays a crucial role in the creep resistance of plastics. As the temperature increases, so does the likelihood of creep deformation.
This is because elevated temperatures cause polymer chains to move more freely, leading to increased molecular mobility and easier chain slippage. Consequently, polymers with higher glass transition temperatures (Tg) tend to exhibit better creep resistance at elevated temperatures compared to those with lower Tg values.
At high temperatures, polymers may also experience thermal degradation or chemical reactions that can further compromise their mechanical properties and accelerate creep deformation. Therefore, it is essential for engineers and designers to consider both the operating temperature range and material selection when aiming for optimal long-term performance in applications where creep resistance is critical.
To enhance a plastic’s ability to withstand high-temperature environments without significant creeping over time, various strategies can be employed such as incorporating fillers or reinforcing agents into the polymer matrix or modifying its molecular structure through cross-linking or blending techniques. These approaches help restrict chain movement and improve overall dimensional stability under load at elevated temperatures.
Biodegradable Creep-Resistant Plastics: Future Trends
These innovative materials not only offer environmental benefits but also possess creep resistance properties. Creep-resistant biodegradable plastics have a promising future as they provide a viable solution for applications where both strength and sustainability are crucial.
In recent years, significant advancements have been made in developing biodegradable polymers with improved creep resistance. Researchers are exploring different approaches such as incorporating reinforcing fillers or modifying the polymer structure to enhance their mechanical properties and reduce deformation over time.
One of the key trends in this field is the use of natural fibers or nanoparticles as fillers in biodegradable plastics. These reinforcements can improve stiffness and strength while reducing creep under load conditions.
For example, adding cellulose nanofibers derived from renewable sources like wood pulp has shown great potential in enhancing both mechanical performance and degradation characteristics of these materials.
Another trend is focused on optimizing polymer structures through chemical modifications or blending techniques to achieve better creep resistance without compromising their degradability. By carefully tailoring molecular weight distribution, cross-linking density, or copolymerization ratios, researchers aim to strike a balance between durability and eco-friendliness.
Furthermore, ongoing research aims at understanding how processing parameters affect the final material’s microstructure and its impact on long-term performance under stress conditions. This knowledge will enable manufacturers to optimize production methods for achieving consistent quality control while maintaining desired levels of creep resistance.
Influence of Filler Materials On Creep Resistance
By incorporating fillers into polymer matrices, their mechanical properties can be significantly improved. Fillers such as glass fibers, carbon nanotubes, and mineral powders help to reinforce the polymer structure and reduce deformation under long-term stress.
The addition of filler materials increases the stiffness and strength of polymers, making them more resistant to creep deformation over time. The fillers act as barriers that restrict molecular chain movement within the material when subjected to constant load or elevated temperatures.
Glass fiber-reinforced plastics (GFRPs) are widely used in construction due to their excellent creep resistance properties. The high aspect ratio of glass fibers provides enhanced reinforcement by distributing stress more evenly throughout the material matrix.
Carbon nanotubes (CNTs) have also shown promising results in improving creep resistance due to their exceptional mechanical properties. CNTs possess high tensile strength and stiffness while maintaining flexibility at small scales, making them ideal for reinforcing polymers against creeping behavior.
Mineral powders like talc or mica can improve both thermal stability and dimensional stability by reducing internal stresses caused by temperature changes during service life. These fillers act as nucleating agents that promote crystallization within polymers, resulting in reduced molecular mobility and improved overall performance against creeping tendencies.
It is important for engineers and designers working with plastic components exposed to long-term loads or elevated temperatures to consider suitable filler materials based on specific application requirements.
Design Considerations for Creep-Resistant Materials
First and foremost is the selection of the appropriate polymer matrix. Certain polymers have inherently better creep resistance than others, so choosing a material with a high glass transition temperature (Tg) can help mitigate creep deformation.
Another important factor is the reinforcement of the polymer matrix. Incorporating fillers such as fibers or particles can significantly enhance creep resistance by providing additional strength and stiffness to counteract deformation over time.
The design geometry also plays a crucial role in minimizing creep effects. By optimizing wall thicknesses, avoiding sharp corners or stress concentration points, and utilizing ribbing or other structural features for added support, it’s possible to reduce stress levels within the material and thus decrease its susceptibility to creeping.
Furthermore, considering operating conditions like temperature fluctuations is essential when designing with creep-resistant materials. Elevated temperatures tend to accelerate creeping behavior; therefore, selecting materials that maintain their mechanical properties at higher temperatures becomes imperative for long-term performance.
Lastly but equally important is proper testing during product development stages. Conducting thorough evaluations under realistic conditions helps identify potential weaknesses early on while allowing adjustments in design parameters if necessary.
Limitations and Challenges in Enhancing Creep Resistance
One of the main limitations is the inherent nature of polymers, which tend to have lower stiffness compared to metals. This can make it challenging to achieve high levels of creep resistance without sacrificing other desirable properties such as flexibility or impact strength.
Another challenge lies in selecting suitable additives or fillers that can improve creep resistance without negatively impacting other performance characteristics. The choice of additives must strike a balance between enhancing mechanical properties and maintaining processability.
Furthermore, optimizing processing conditions is crucial for achieving improved creep resistance. Factors such as temperature, pressure, cooling rates, and molding techniques all play a significant role in determining the final material’s ability to resist deformation over time.
Long-term testing is necessary for accurately assessing a material’s true creep behavior under real-world conditions. Conducting these tests requires time and resources but provides valuable insights into how materials perform over extended periods.
Lastly, there are economic considerations when developing highly specialized polymers with enhanced creep resistance. The cost associated with research and development efforts aimed at improving this property may result in higher-priced materials compared to conventional options.
Addressing these limitations while overcoming technical challenges will pave the way for more advanced polymer formulations with superior long-term stability against deformation – ultimately expanding their applications across various industries where durability is paramount.
Recap