Explore the benefits and diverse applications of thermoplastic composite materials in construction with our expert insights.
Thermoplastic composites are a type of material made from combining plastic resin with reinforcing fibers such as carbon or glass fiber. They have been used in various industries for years but are now gaining popularity in the construction industry due to their numerous advantages.
In this article, we will explore the benefits of using thermoplastic composite materials in construction and some exciting applications that will change the way we build structures forever.
Key takeaways:
- Thermoplastic composites are lightweight yet strong and durable.
- They are resistant to extreme temperatures and harsh weather conditions.
- They are eco-friendly and can be recycled at the end of their lifespan.
- Applications include building facades, roofing systems, and bridge decks.
- Different types of thermoplastic composites offer unique characteristics for specific construction needs.
Thermoplastic Composites: An Overview
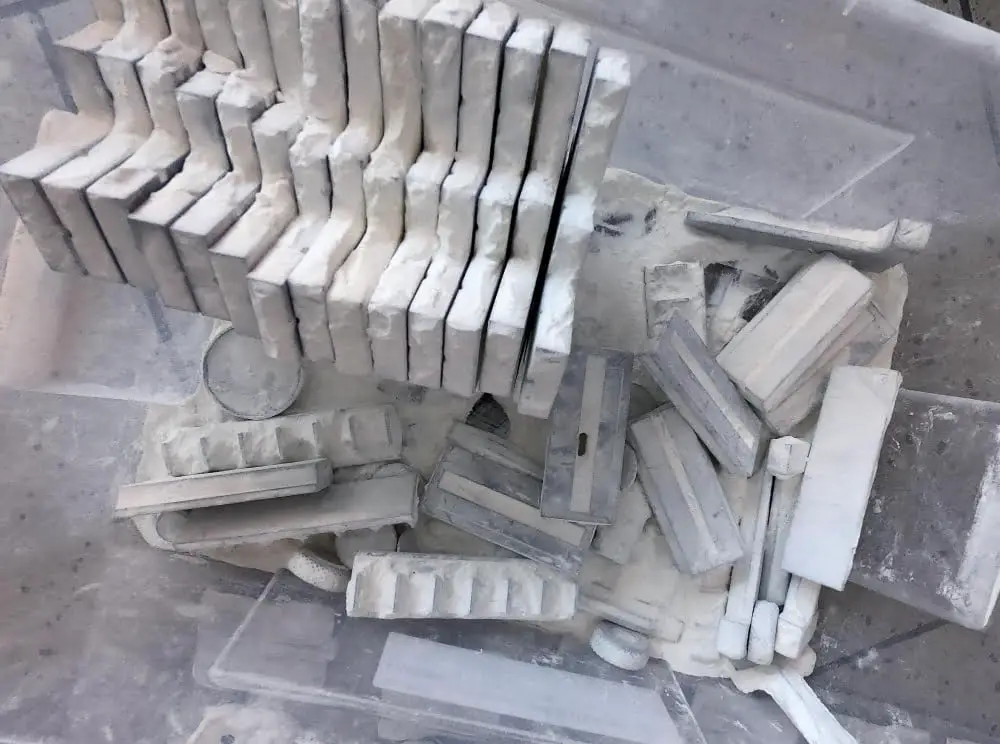
Thermoplastic composites are a type of material that has been around for decades. They have been used in various industries such as aerospace, automotive, and sports equipment manufacturing.
However, it is only recently that they have gained popularity in the construction industry.
Thermoplastic composites are made by combining plastic resin with reinforcing fibers such as carbon or glass fiber. The resulting material is lightweight yet strong and durable.
It can withstand extreme temperatures and harsh weather conditions without losing its structural integrity.
Advantages of Thermoplastic Materials
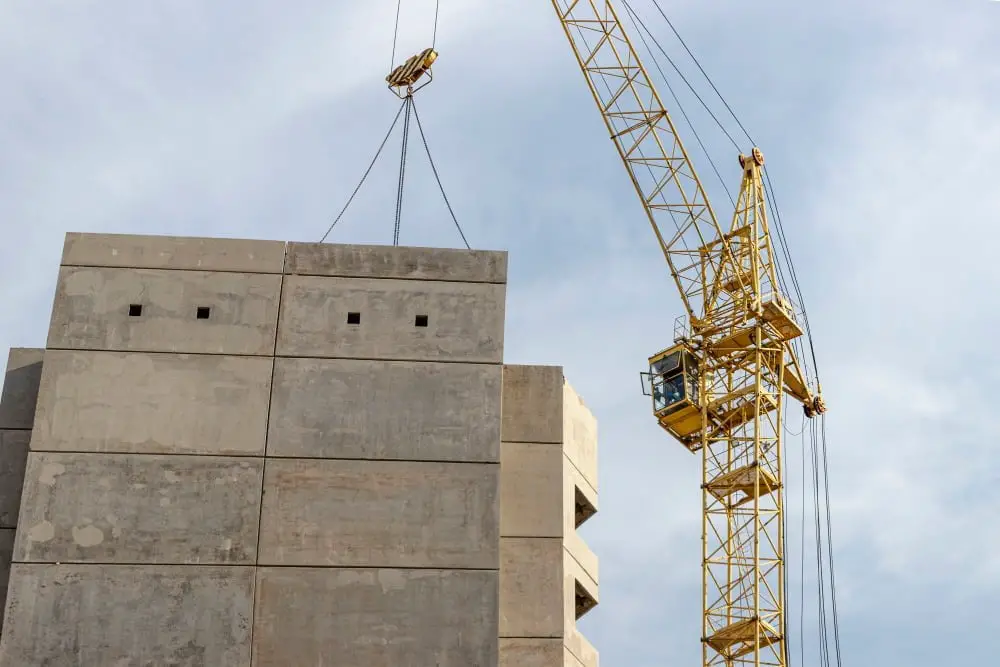
One of the main advantages of thermoplastic composite materials is their strength and durability.
With thermoplastic composites, structures can withstand harsh weather conditions such as extreme heat or cold without losing their shape or integrity.
Another advantage is that they are lightweight yet strong, making them ideal for use in construction projects where weight plays a significant role in design considerations. This means that architects and engineers can create larger structures without worrying about adding extra support beams or columns.
Thermoplastic composites are also resistant to corrosion and chemicals which makes them perfect for use in areas where exposure to these elements is common such as bridges, tunnels, and pipelines.
In addition to being durable and lightweight, thermoplastics are also eco-friendly since they can be recycled at the end of their lifespan instead of ending up in landfills like traditional building materials do.
Applications in Construction Industry
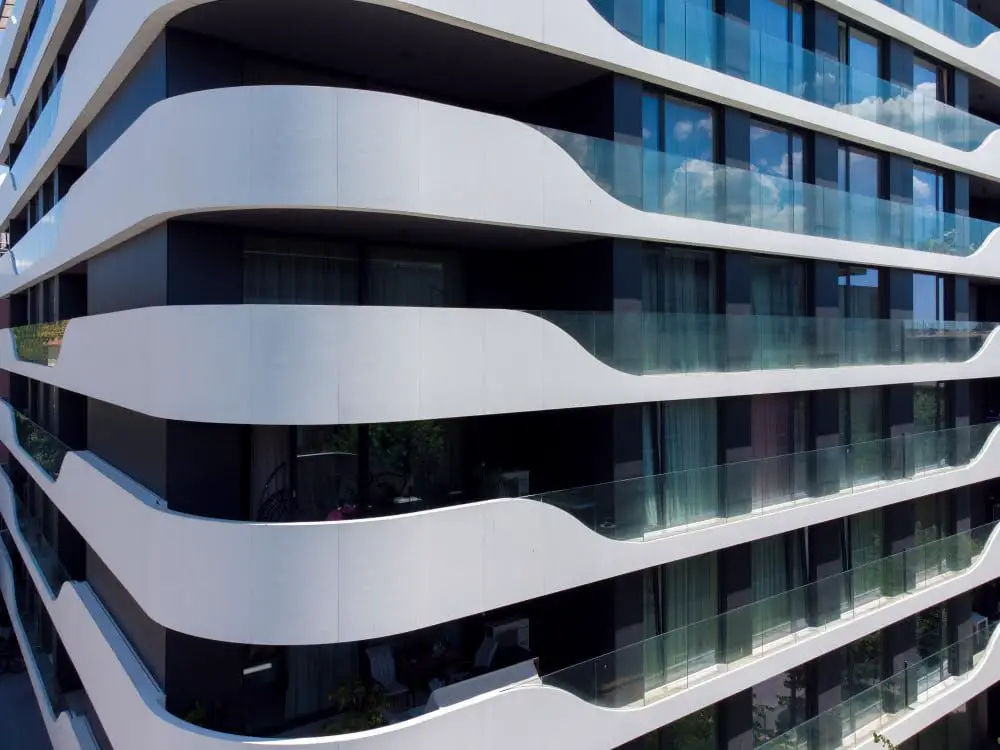
Thermoplastic composite materials have a wide range of applications in the construction industry. One of the most exciting uses is in building facades.
The lightweight and durable nature of thermoplastic composites make them an excellent choice for cladding systems, which can be used to cover entire buildings or specific areas such as balconies or sunshades.
Another application is in roofing systems, where thermoplastic composites are used to create strong and weather-resistant panels that can withstand extreme temperatures and harsh weather conditions.
Thermoplastic composite materials are also being used for bridge decks due to their high strength-to-weight ratio, corrosion resistance, and low maintenance requirements. These properties make them ideal for constructing long-lasting bridges that require minimal upkeep over time.
In addition to these applications, thermoplastic composites are also being explored as a potential replacement for traditional concrete structures due to their ability to resist cracking under stress while maintaining flexibility over time.
Types of Thermoplastic Composites
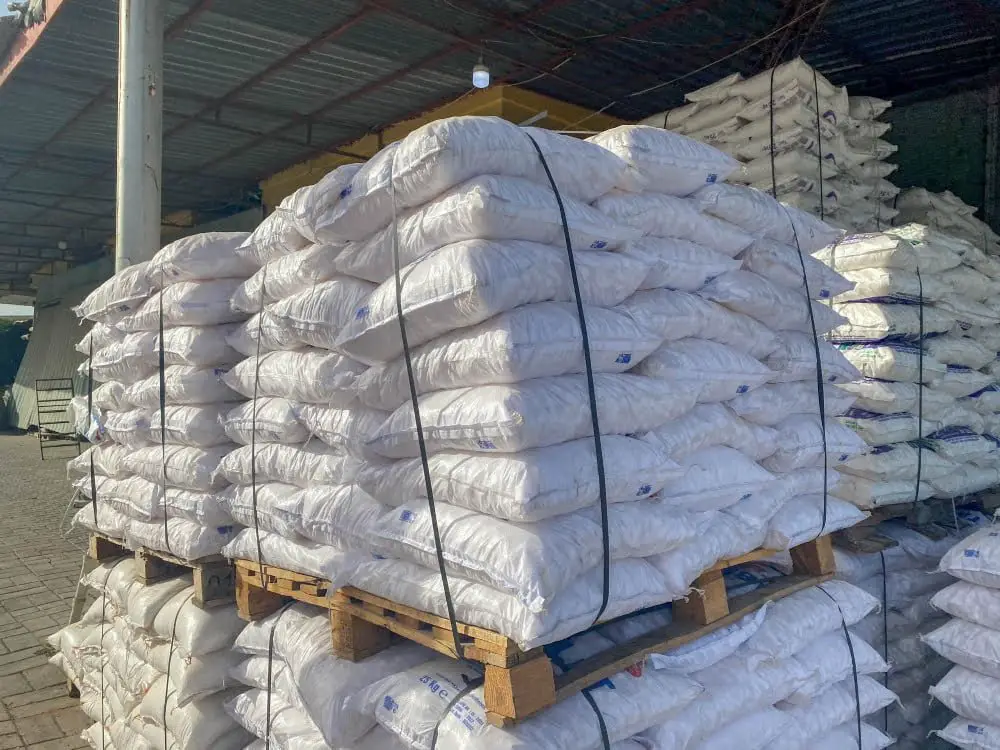
These are the most common types of thermoplastic composites:
1. Polypropylene (PP) Composites: These composites have excellent chemical resistance and low moisture absorption properties, making them ideal for outdoor applications.
2. Polyamide (PA) Composites: PA composites offer high strength and stiffness while being lightweight at the same time, making them perfect for structural components.
3. Polycarbonate (PC) Composites: PC composites have exceptional impact resistance and transparency properties that make them suitable for glazing applications such as skylights or windows.
4. Acrylonitrile Butadiene Styrene (ABS) Composities: ABS is a popular choice due to its ease of processing, good dimensional stability, and excellent surface finish quality.
Each type has unique characteristics that make it suitable for specific construction needs. Thermoplastic composite materials offer numerous advantages over traditional building materials such as concrete or steel – they’re lighter yet stronger than their counterparts; they’re resistant to corrosion; they can be molded into complex shapes with ease; plus many more benefits.
Manufacturing Techniques & Processes
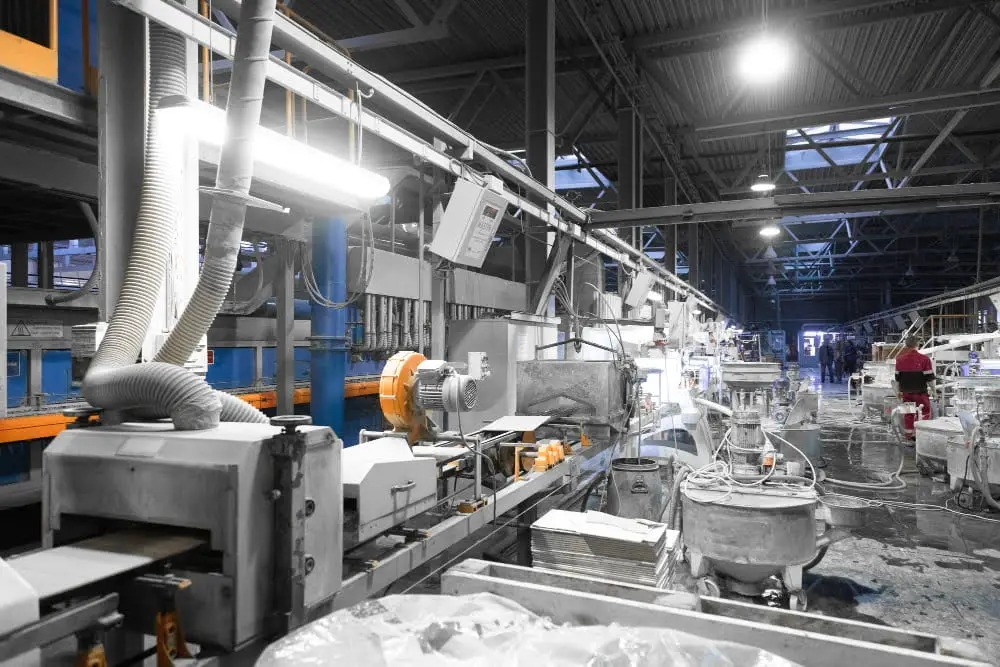
There are several techniques involved in producing these materials, including compression molding, injection molding, and filament winding.
Compression molding involves placing the reinforcing fibers into a mold cavity before injecting molten plastic resin under high pressure. This technique is ideal for creating large parts with complex shapes.
Injection molding uses melted plastic resin that is injected into a mold cavity containing pre-placed reinforcing fibers. The mixture then cools and solidifies to form the final product.
Filament winding involves wrapping continuous strands of fiber around a rotating mandrel while simultaneously applying heat or pressure to melt the thermoplastic matrix material onto it. This technique produces strong cylindrical shapes such as pipes or tanks.
Each manufacturing process has its advantages depending on what type of structure needs to be built using thermoplastic composites. In addition to their versatility in production methods, these materials offer numerous benefits over traditional construction materials such as steel or concrete – they are lightweight yet incredibly strong and durable against harsh weather conditions.
Future Trends in the Use of Thermoplastic Composites in Construction
As construction practices continue to evolve, so does the use of thermoplastic composites in the industry. These versatile materials offer a range of benefits that make them attractive for various applications.
Looking ahead, there are several future trends emerging in the use of thermoplastic composites in construction.
One trend is the increasing adoption of lightweight and high-strength thermoplastic composite materials for structural components. These materials have excellent mechanical properties and can be tailored to specific project requirements, offering enhanced durability while reducing overall weight.
Another trend is the integration of smart technologies into thermoplastic composite structures. By embedding sensors or actuators within these composites, it becomes possible to monitor structural health or even enable self-repair capabilities.
This opens up new possibilities for creating intelligent buildings that can adapt and respond to changing conditions.
Advancements in additive manufacturing techniques are expected to play a significant role in shaping future trends with thermoplastic composites. 3D printing allows for complex geometries and customization options that were previously challenging with traditional manufacturing methods.
This technology enables architects and engineers greater design freedom while optimizing material usage.
Furthermore, sustainability will continue driving innovation within this field as environmental concerns become increasingly important across industries including construction. Thermoplastics offer advantages such as recyclability which aligns well with sustainable building practices by reducing waste generation during both production and end-of-life stages.
Recyclability and Environmental Impact of Thermoplastic Composites
Unlike thermoset composites, which are difficult to recycle due to their irreversible curing process, thermoplastics can be melted down and reshaped multiple times without losing their properties. This means that end-of-life thermoplastic composite products can be recycled into new materials or used for other applications.
The recyclability of thermoplastic composites not only reduces waste but also contributes to a more sustainable construction industry. By diverting these materials from landfills, we can minimize the environmental impact associated with traditional disposal methods.
Furthermore, the production of thermoplastic composites generally requires less energy compared to other construction materials like steel or concrete. This lower energy consumption translates into reduced greenhouse gas emissions during manufacturing processes.
The recyclability and lower environmental impact make thermoplastic composites an attractive choice for sustainable construction practices.
The Role of Thermoplastic Composites in Disaster-Resistant Construction
These materials have the ability to withstand extreme weather conditions, such as hurricanes, earthquakes, and tornadoes. Their high impact resistance makes them ideal for reinforcing structures against potential damage caused by natural disasters.
One of the key advantages of thermoplastic composites is their lightweight nature compared to traditional building materials like steel or concrete. This characteristic allows for easier transportation and installation during emergency situations when time is critical.
Thermoplastic composites offer excellent corrosion resistance properties that make them highly suitable for coastal areas prone to saltwater exposure or regions with high humidity levels. They do not rust or degrade over time like metals do, ensuring long-term structural integrity even in harsh environments.
Furthermore, these composite materials can be designed with specific fire-retardant properties that enhance safety measures in disaster-prone areas. By incorporating flame retardants into the composition of thermoplastics during manufacturing processes, they become less susceptible to ignition and slow down flame spread if exposed to fire incidents.
High-Temperature Resistant Thermoplastic Compounds in Construction
These compounds are engineered to withstand extreme heat conditions, making them ideal for applications where traditional materials may fail.
One of the key advantages of high-temperature resistant thermoplastic compounds is their ability to maintain structural integrity even at elevated temperatures. This makes them suitable for use in environments such as industrial settings, power plants, and fire-resistant structures.
In addition to their excellent heat resistance, these thermoplastics also offer other desirable properties that make them attractive for construction purposes. They possess good mechanical strength and durability, allowing them to withstand heavy loads and harsh operating conditions over an extended period.
Moreover, high-temperature resistant thermoplastics can be easily molded into complex shapes using various manufacturing techniques like injection molding or extrusion processes. This versatility enables architects and engineers greater design freedom when incorporating these materials into construction projects.
Furthermore, these advanced composites exhibit low thermal expansion characteristics compared to traditional building materials like metals or ceramics. This property helps minimize dimensional changes caused by temperature fluctuations during operation or exposure to external heat sources.
Advanced Manufacturing Methods and Innovations in Thermoplastic Composites
These developments have opened up new possibilities for their application in construction projects.
One such innovation is automated fiber placement (AFP), which allows for precise control over the orientation of fibers during the manufacturing process. This method ensures that the composite material has optimal strength and stiffness properties, making it ideal for structural applications.
Another notable advancement is additive manufacturing or 3D printing of thermoplastic composites. This technique enables complex geometries to be created with ease, reducing waste materials and allowing for customization on a large scale.
It also offers faster production times compared to traditional methods.
Furthermore, researchers are exploring nanotechnology-based enhancements for thermoplastic composites. By incorporating nanoparticles into these materials, they can improve mechanical properties such as strength, toughness, and flame resistance while maintaining lightweight characteristics.
These advanced manufacturing methods not only enhance the performance of thermoplastic composites but also offer cost-effective solutions by streamlining production processes. As a result, we can expect to see increased adoption of these innovative techniques in various construction applications ranging from bridges and buildings to infrastructure projects like pipelines or offshore structures.
FAQ
What is a thermoplastic composite?
A thermoplastic composite is a type of material that utilizes a thermoplastic matrix, enabling it to soften when heated and solidify without degradation when cooled, allowing for remolding.
What are thermoplastic composites examples?
Examples of thermoplastic composites include Polyethylene (PE), Polypropylene (PP), and Polybutylene Terephthalate (PBT).
Where are thermoplastic composites used?
Thermoplastic composites are typically used in the construction of lightweight structures, storage tanks, door and window frames, and panels.
What are the benefits of thermoplastic composites?
Thermoplastic composites offer benefits such as higher impact resistance, unique processing capabilities, lightweight properties, strength and environmental advantages, which contribute to reduced fuel costs and increased environmental sustainability.
How are thermoplastic composites manufactured?
Thermoplastic composites are manufactured through a process that involves heating a polymer until it becomes pliable, blending it with reinforcing fibers, and then cooling it to create a solid composite material.
What is the environmental impact of using thermoplastic composites?
The environmental impact of using thermoplastic composites includes resource depletion due to their petroleum-based origin and pollution from their manufacture and disposal, but it can be mitigated through recycling and sourcing from renewable materials.
How do thermoplastic composites compare to traditional materials in terms of strength and durability?
Thermoplastic composites are typically stronger and more durable than traditional materials given their high resistance to impact, corrosion, and extreme weather, and they retain these properties for prolonged periods.
Recap