Exploring the extrusion process reveals a significant amount of plastic waste, a pressing issue that demands our attention in the construction industry.
Plastic waste during the extrusion process is an issue of great concern in the construction industry. Extrusion, a common method for producing plastic components, can generate a significant amount of waste if not managed properly.
The exact amount of waste can vary, depending on factors such as the type of polymer used, the precision of the extrusion machinery, and the quality control measures in place. However, estimates typically suggest that around 2% to 10% of plastic can end up as waste during extrusion.
This article will delve into the specifics of why this waste occurs, how it can be minimized, and the innovative ways in which this waste can be repurposed, providing a comprehensive insight into the issue.
Key takeaways:
- Plastic waste during extrusion can range from 2% to 10%.
- Factors contributing to plastic waste include poor material quality and operator error.
- Plastic waste in extrusion leads to environmental pollution and long decomposition times.
- Solutions to reduce waste include improving operation techniques and implementing recycling programs.
- Using recycled materials in extrusion is cost-effective and environmentally sustainable.
Understanding the Extrusion Process and Plastic Waste
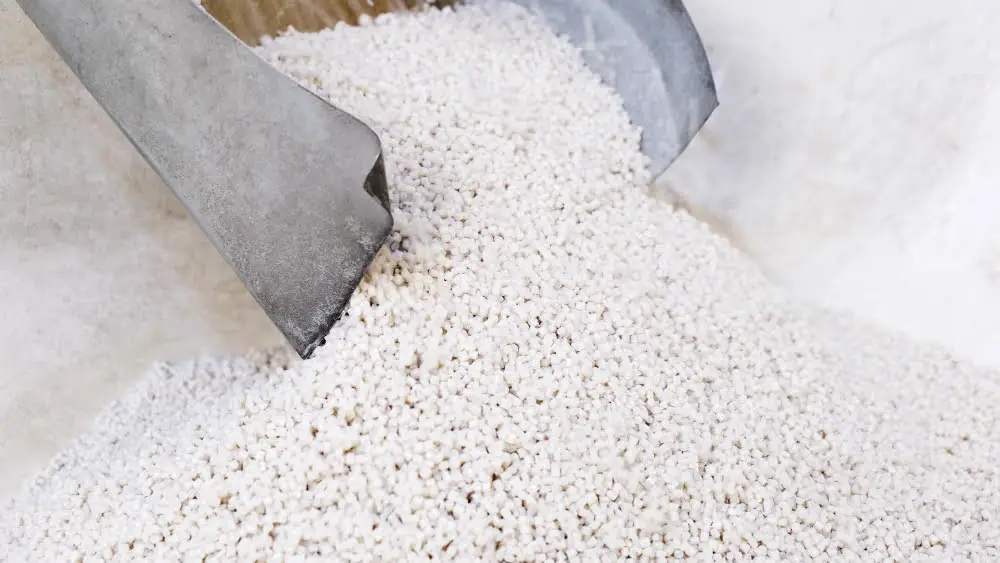
Extrusion is a common process used in many industries, including construction. It involves forcing softened material through a die, a specially designed tool, to create a product with a unique shape that carries on indefinitely until the process is halted. Like toothpaste squeezed from a tube, extruded products can be long and continuous, such as pipes or profiles.
Polymers, particularly plastics, are frequently used in extrusion due to their malleability and durability, providing versatile applications. However, the extrusion process can give way to significant waste.
- The initial stages often require a setup period where the polymer is heated and pushed through the extruder to ensure the correct shape and dimension. This pre-production plastic often ends up as waste.
- Defects or variations in the extruded product may also lead to discards. These could stem from inconsistencies in the polymer mixture, improper setup, or slight changes in the process parameters.
- Lasty, a portion of waste arises from offcuts and trimmings. These are the excess materials trimmed off to achieve the desired final product size, especially when the extruded products are meant to be of specific lengths.
The practice of reducing, reusing, and recycling this waste is a vital step, not just for cost saving but also for the sake of the environment. If not managed appropriately, plastic waste can pose a serious environmental issue due to its non-biodegradable nature and potential for pollution.
Factors Contributing to Plastic Waste in Extrusion Process
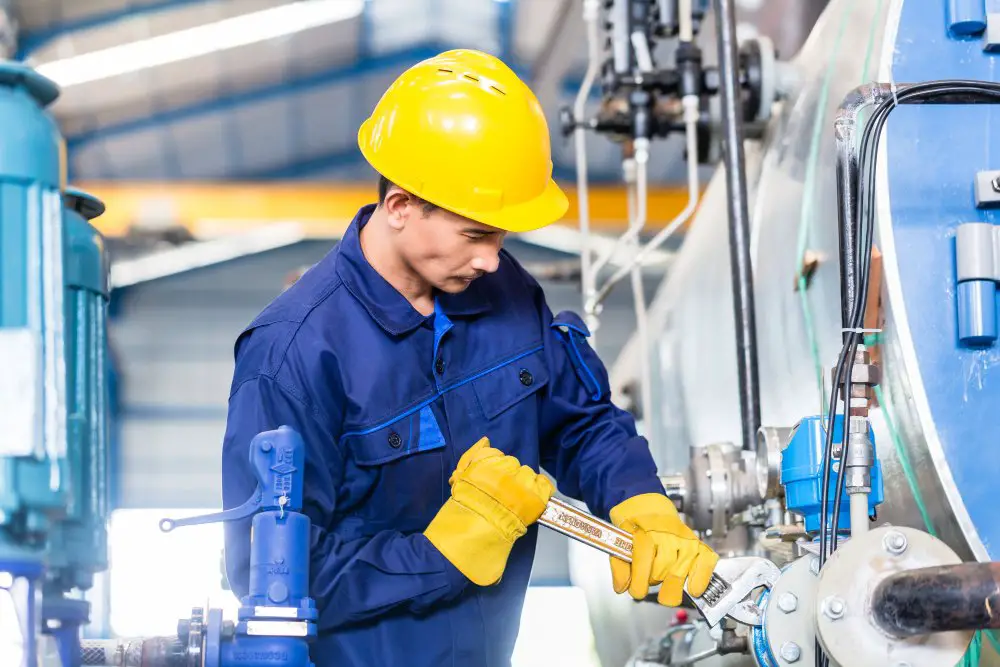
Several factors contribute to the generation of plastic waste during the extrusion process:
Poor Material Quality: Cheap, substandard plastic inputs can result in high waste percentages. Impurities in these materials often reject the final product, hence adding to the waste.
Inefficient Machinery: Outdated or poorly maintained equipment may not process the plastic effectively, causing excessive leftover material.
Operator Error: A lack of training or skills can lead to mistakes. Incorrect temperature settings or the timing of the extrusion process could contribute to a larger amount of waste.
Design Flaws: Certain designs can inadvertently lead to plastic excesses. Upon redesigning, these excesses can be minimized.
Lack of Recycling Efforts: Many manufacturers discard plastic trimmings rather than recycle them. By incorporating a recycling stream into their processes, companies can significantly minimize waste.
To address these factors and reduce waste, manufacturers could invest in higher quality materials, maintain equipment regularly, provide adequate training for staff, assess and improve designs, and integrate internal recycling processes.
Statistics On Plastic Waste During Extrusion
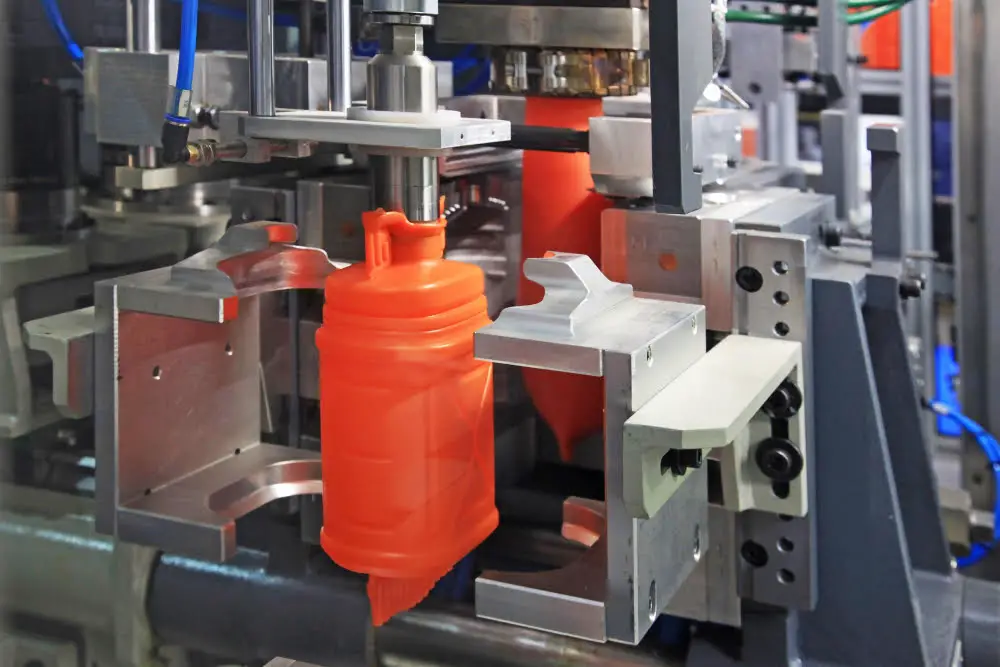
The exact numbers may vary from one operation to another, but it’s estimated that approximately 3% to 4% of all polymer processed through extrusion is lost as waste. This waste primarily originates from several sources during the extrusion process. Specifically:
- Startup and shutdown cycles: Each time an extrusion operation starts or stops, discarded plastic material forms part of the process. This is especially true when changing color or type of polymer, which results in transitional waste.
- Quality control and product rejects: Not all extruded polymers meet quality standards. Those that fail inspection account for a significant proportion of the total waste produced.
- Scrap from the trimming process: Trimming is common in extrusion to achieve required sizes or shapes. The trimmed parts often result in additional waste.
The collective volume of such waste becomes alarming when considering the global scale of polymer extrusion operations. It not only results in substantial economic loss for manufacturers but also poses considerable environmental concerns.
The crux of the matter is to make efforts to minimize this waste. There are several practical steps every manufacturer can take:
- Improve operation techniques: Proper planning and execution of startup and shutdown cycles can greatly save on waste.
- Increase QC standards: By enhancing extrusion quality control processes, one can ensure fewer product rejections.
- Efficient use of trim waste: With innovative solutions, it’s possible to feed trim waste directly back into the extrusion line.
By implementing these steps, a manufacturer can noticeably reduce polymer waste during extrusion, translating into economic benefits and environmental sustainability.
Impact of Plastic Waste During Extrusion On Environment
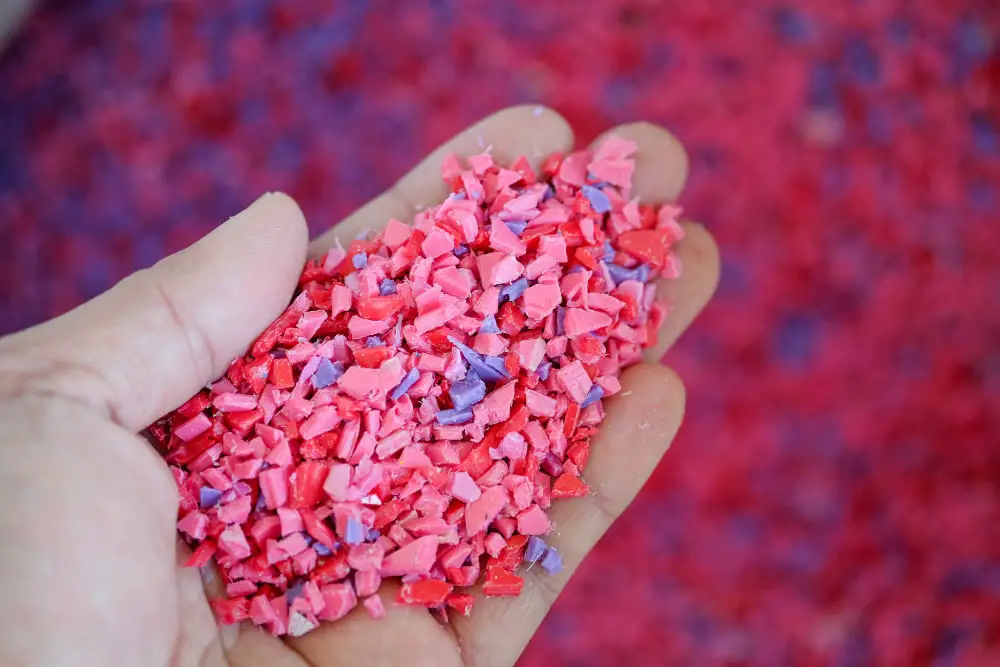
The environmental consequences of plastic waste produced during the extrusion process are significant and multifaceted.
Firstly, when excess plastic is not recycled, it ends up in landfills where it can take up to 1000 years to decompose due its non-biodegradable nature. While in landfills, the plastic may leach harmful substances into the soil, consequently contaminating groundwater sources.
Furthermore, the discard into natural environments, such as oceans, poses threats to aquatic life. Many marine species mistake small plastic debris for food—an ingestion that can be fatal. Additionally, large pieces of plastic can also physically trap and suffocate aquatic animals.
The manufacturing process aspect also carries implications. During production, plastic extrusion can lead to greenhouse gas emissions, contributing to climate change. Moreover, making new plastic heavily depends on crude oil and natural gas, nonrenewable resources that, when exploited, can also lead to ecological damage.
Lastly, attempts to incinerate plastic waste also carry hidden dangers. While it might seem like an effective way to reduce the waste, burning plastic releases toxic gases into the atmosphere, exacerbating the already critical air pollution issue.
To address these impacts, the plastic extrusion industry can adopt measures like improving efficiency in the manufacturing process, implementing recycling programs, and innovating with biodegradable materials. These steps aim to reduce the volume of plastic waste generated, and consequently, the associated environmental hazards.
Potential Solutions to Reduce Plastic Waste in Extrusion
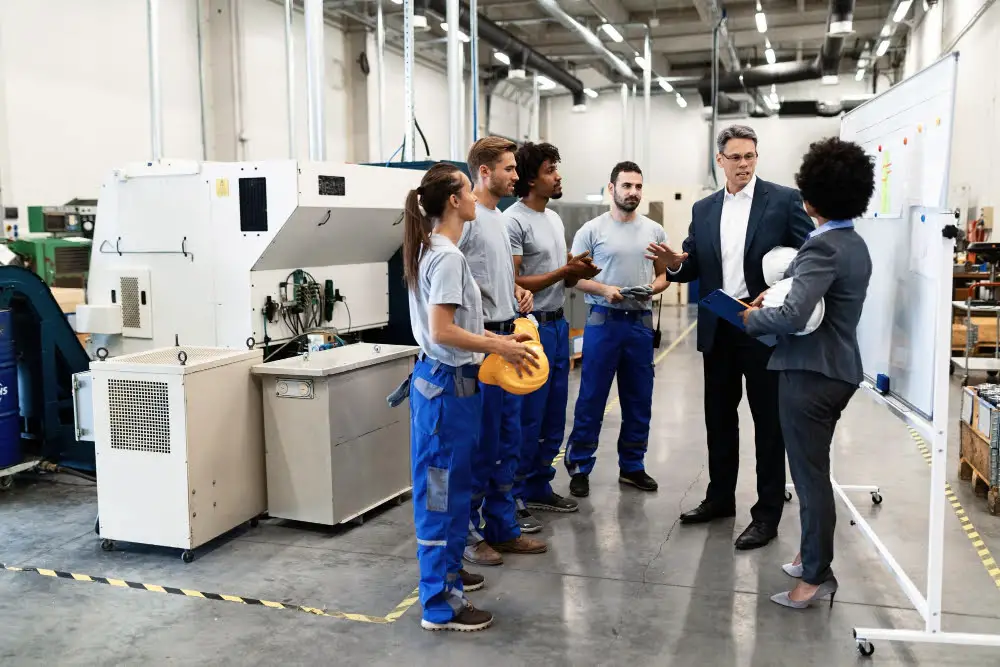
Emerging solutions offer promising ways to curb the problem of plastic waste generated during extrusion. Here we discuss some effective methods:
Improving the Feedstock Management: Enhanced control over feedstock materials can minimize waste generation. Ensuring that processes are running at suitable temperatures and speeds can significantly decrease the amount of off-grade material produced.
Utilizing Modern Extrusion Equipment: Technological advances have led to more precise extruders with better control systems. These machines have the capacity to maintain consistent extrusion rates, minimizing plastic waste.
Emphasizing Preventive Maintenance: Regular equipment check-ups and cleaning can help identify and fix problems before they lead to excess waste. Extruder screens, for instance, should be cleaned to facilitate consistent flow and mitigate waste caused by clogs.
Implementing Recycling Programs: Facilities should develop robust recycling programs to reprocess extrusion waste materials into new products. This includes implementing regrind systems to recover and reuse plastic scrap.
Investing in Worker Training: An educated workforce can operate machinery correctly, improve efficiency, and make better decisions regarding plastic consumption and waste management. This effort entails training about correct equipment handling, waste minimization, and on-site recycling.
Through these practical steps, the industry can make significant strides in managing plastic waste, increasing efficiency in the extrusion process, and conserving the environment.
Comparative Analysis: Using Recycled Materials in Plastic Extrusion Products
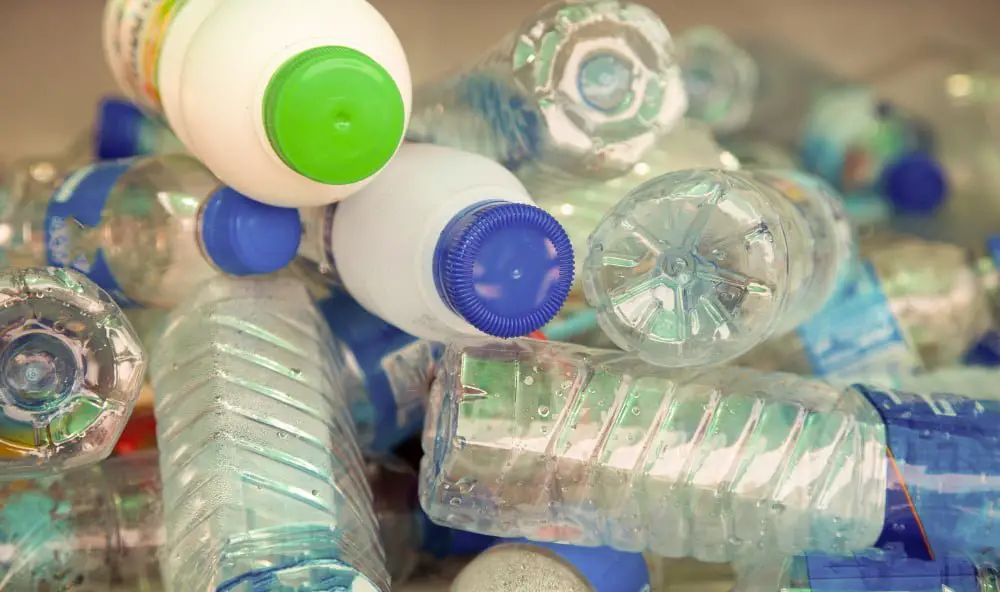
Recycled plastic offers several benefits when utilized in the extrusion process. Given the environmental implications of plastic production, it’s crucial to explore these upsides:
- Environmental sustainability is the chief advantage. By reclaiming and repurposing plastic, we conserve resources and lessen the burden on waste management systems.
- Recycled plastic can be as cost-effective as virgin material, if not more. Production costs may be reduced due to the lessened need for new raw materials.
- Quality isn’t compromised, contrary to some misconceptions. Advanced recycling technologies often render plastic that is nearly indistinguishable from new materials. The performance of extrusion products from recycled plastic is often on par with those made from virgin material.
Taking into account these benefits, manufacturers can incorporate more recycled plastic into their processes. On the consumer end, it’s important to support businesses that prioritize recycled materials. Both actions contribute to reducing the plastic waste caused by the extrusion process.
Adopting such measures supports environmental sustainability while maintaining industry standards in extrusion production quality. It offers a comprehensive approach to balance the demands of production with the need for environmental conservation.
Case Study: How Noteworthy Industries Are Reducing Plastic Waste During Extrusion
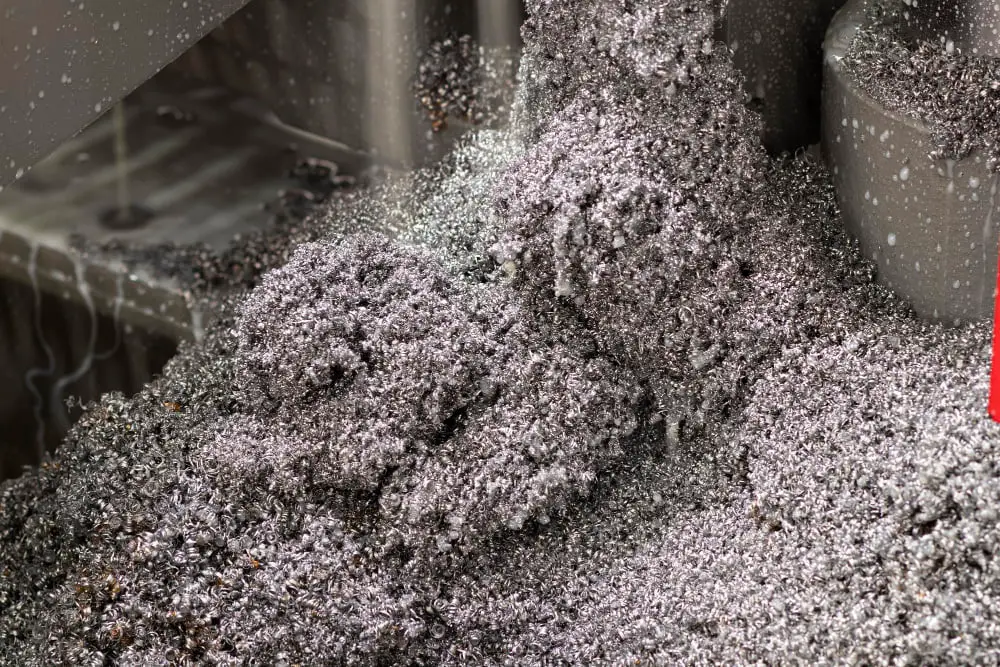
Industries around the globe are implementing innovative strategies to curb plastic waste generated by the extrusion process.
Precision-based technology is gaining significant traction in the manufacturing sector. Innovative companies like Techouse Inc. are utilising machines with precise controls in temperature, pressure and speed to mitigate wastage during the extrusion process.
Repurposing of plastic trimmings and purgings is another onset trend. Instead of discarding these by-products, facilities like Valenan Corp are melting them down to be reused in the manufacturing production line.
Some companies introduce recycled and biodegradable materials into the process. GreenPlas Inc., for instance, substitutes traditional petroleum-based polymers with alternatives like polylactic acid (PLA), a biodegradable polymer derived from renewable resources.
Additionally, the use of real-time monitoring systems helps to instantly identify and rectify issues leading to material wastage. For example, PolyPro Tech uses advanced sensor technology to detect any material waste in the extrusion process thereby minimizing the excess production.
Lastly, implementing stringent quality controls guarantees that only products meeting specific standards are finalized, reducing the need for additional material for re-works which leads to decreased wastage. CanTech Manufacturing Inc. has demonstrated this approach, remarkably reducing its plastic waste.
By sharing these strategies, it’s easy to see how different sectors are actively working to reduce plastic waste during the extrusion process. These innovative methods could be potentially employed by other businesses and even at the household level to make a collective impact.
FAQ
What percentage of plastic is wasted?
Approximately 79% of produced plastic ends up as waste, either in landfills or in the natural environment.
Why is only 9 of plastic recycled?
Plastic recycling is limited to about 9% due to the high costs associated with the energy-intensive recycling process, which ultimately makes recycled plastic more expensive compared to newly produced plastic.
Is more than 40 percent of plastic used just once before it is thrown away?
Yes, over 40 percent of plastic is used only once before it is discarded into the environment.
What percentage of plastic is incinerated?
Approximately 19% of plastic waste is incinerated.
How does the extrusion process contribute to the wastage of plastic in construction?
The extrusion process in construction can contribute to plastic wastage due to the generation of off-cut materials and rejected products that are not recycled.
What approaches can be integrated into the construction sector to reduce single-use plastic wastage?
The construction sector can reduce single-use plastic wastage by integrating approaches such as recycling and repurposing discarded plastic into building materials, adopting biodegradable polymers, and minimizing packaging waste through supplier negotiations.
What are the environmental implications of incinerating plastic waste generated from construction activities?
Incinerating plastic waste from construction activities leads to significant environmental issues, including air pollution due to toxic fumes and the escalation of non-renewable resource consumption.
Recap