Discover the step-by-step process of creating a plastic fence through extrusion, transforming raw polymer materials into durable and aesthetic outdoor structures.
Plastic fence extrusion is a process that transforms raw plastic material into a continuous profile, forming durable and versatile fences. It involves heating the plastic until it becomes malleable, forcing it through a die to shape it into the desired fence profile, and then cooling it to retain the shape.
This process requires a thorough understanding of the types of plastics suitable for extrusion, the setup of the extrusion machine, and the cooling process. By following the steps outlined in this article, you will gain a comprehensive understanding of how to make a plastic fence through extrusion.
Key takeaways:
- Plastic fence extrusion involves heating plastic to shape it
- Types of plastics used include PVC and HDPE
- Different extrusion machine types can be used for fence extrusion
- Plastic fences are durable and low-maintenance, but can fade over time
- Innovations in extrusion technology have improved fence quality and sustainability
Materials Needed for Plastic Fence Extrusion
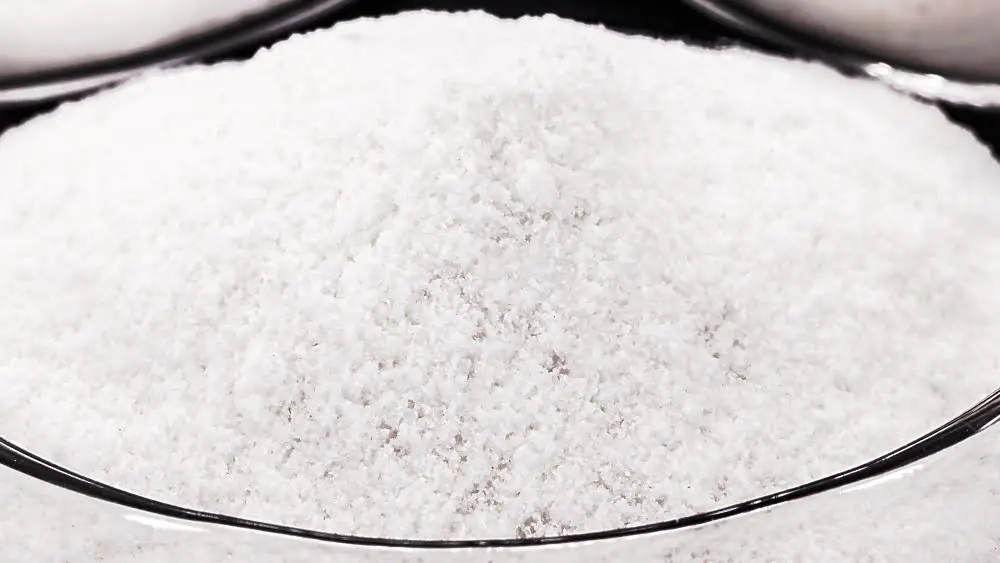
The materials used for plastic fence extrusion are vital to the resulting product’s quality and durability. First, the raw material, plastic resin or pellets, is chosen based on the desired properties of the final product.
Common selections include Polyvinyl Chloride (PVC) and High-Density Polyethylene (HDPE), both of which are known for their durability, low-maintenance nature, and wide range of suitable applications.
Relevant additives are also incorporated into the plastic matrix to enhance the product. These can be heat stabilizers, which prevent degradation caused by high temperatures during the extrusion process, ultraviolet (UV) stabilizers which help the fence resist sunlight damage, and appropriate colorants which give fences their color.
Another crucial part of the fencing material is the mold, instrumental in shaping the plastic into the desired fence profile. The mold should be designed keeping in mind the fence’s final design and application.
One must also ensure the availability of the right kind of extrusion machine for the job. Plastic extrusion machines come in different configurations and capabilities, so the one you choose should be able to handle the fence extrusion specifications you’re working with.
Finally, auxiliary equipment such as a cooling tank to aid in the solidification process, a haul-off unit for consistent drawing of the extrudate, and a cutter for making fence pieces to the desired length, are crucial pieces of the puzzle.
Remember, the quality of your materials will ultimately dictate the performance of the finished product.
Different Types of Plastic Extrusion Machines Used in Plastic Fence Extrusion
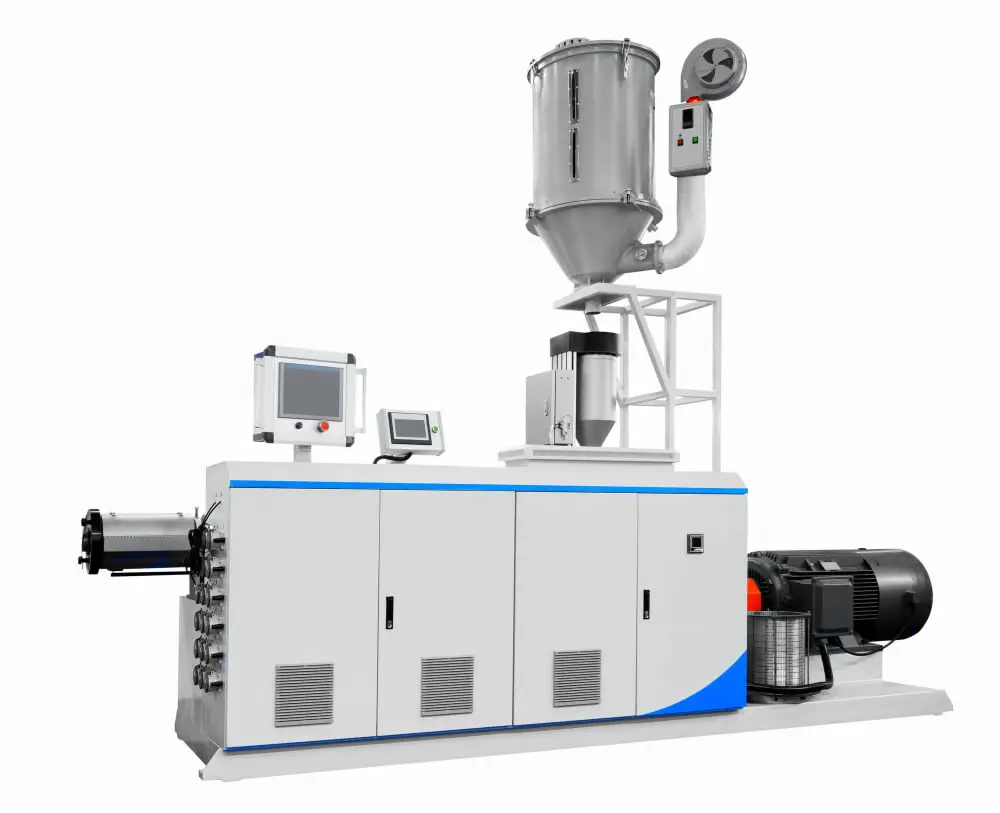
Primarily, the Single Screw Machine is the standard choice for most extrusion operations, due to its simplicity and efficiency. It uses a single rotating screw to transport and melt the plastic before forcing it through a die. This equipment is ideal for applications requiring high utilization and modest extrusion rates.
On the other hand, the Twin Screw Machine has two rotating screws working in tandem. These machines, specifically the co-rotating intermeshing type, are often used when compounding polymers with additives, offering enhanced mixing and processing capabilities.
Yet another is the Ram Extruder. These utilize a hydraulic ram that pushes the plastic material through the die. Ram extruders are ideal for low-volume jobs and can extrude hard thermosetting plastics.
For the Fence Extrusion line, specific machines have been developed which typically integrate automatic or semi-automatic capability for cavity filling, pre heating and cooling. These machines are manufactured in a range of sizes to handle different fence profile dimensions.
Knowing the appropriate extrusion machine for a specific task is key, which depends on polymer characteristics, desired output, energy consumption and cost effectiveness. Each type of machine offers different advantages which can be capitalized upon for efficient production. Ensure you choose the one most suited to your needs.
Process of Making Plastic Fence Using Extrusion Machine
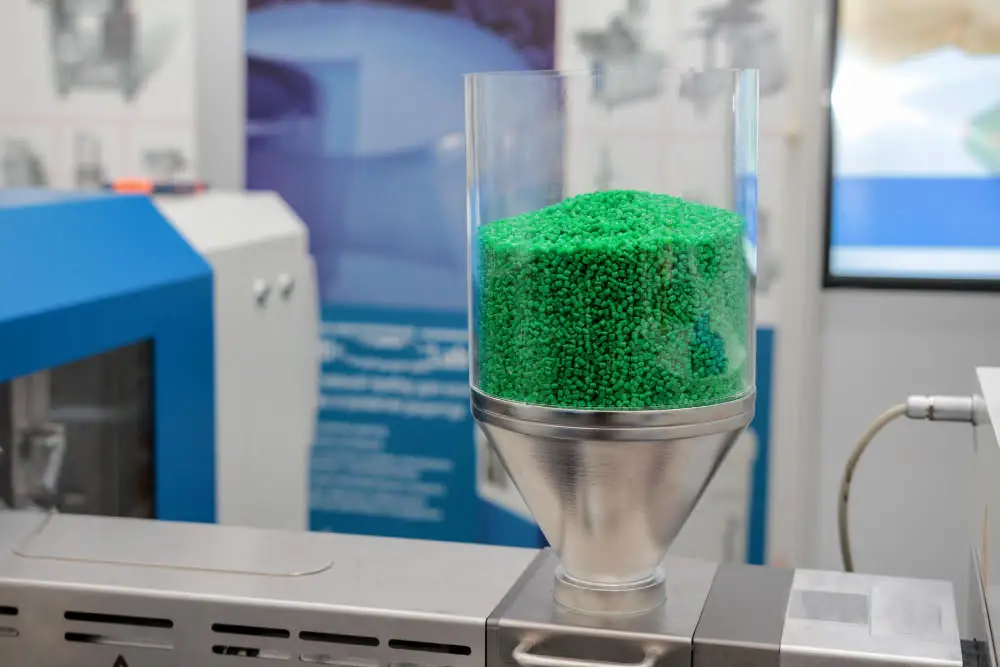
The process begins with raw plastic material like PVC which is fed into the extrusion machine’s hopper. The material is then transferred into a barrel, heated to a temperature that softens it into a molten state. From there, the heated plastic is forced through a specially designed die that shapes it into a fence profile.
This newly formed plastic profile is then quickly cooled, most commonly by water, so it can retain the fence shape. After cooling, the plastic fence is cut into desired lengths, inspected for any imperfections, and packed for shipping or installation.
While the process is automated, operators must monitor the machine settings such as temperature and pressure for best results. Regular cleaning of the extrusion machine, and scheduled maintenance helps ensure that the machine runs smoothly and the plastic fences produced are of good quality.
It’s also important to note that while this process is tailored for fence production, the type of plastic, the design of the die, and the settings of the extrusion machine can be altered to produce a wide array of other plastic products. Different types of polymers like polyethylene or polypropylene can also be extruded using this process.
Troubleshooting Tips for Plastic Fence Extrusion
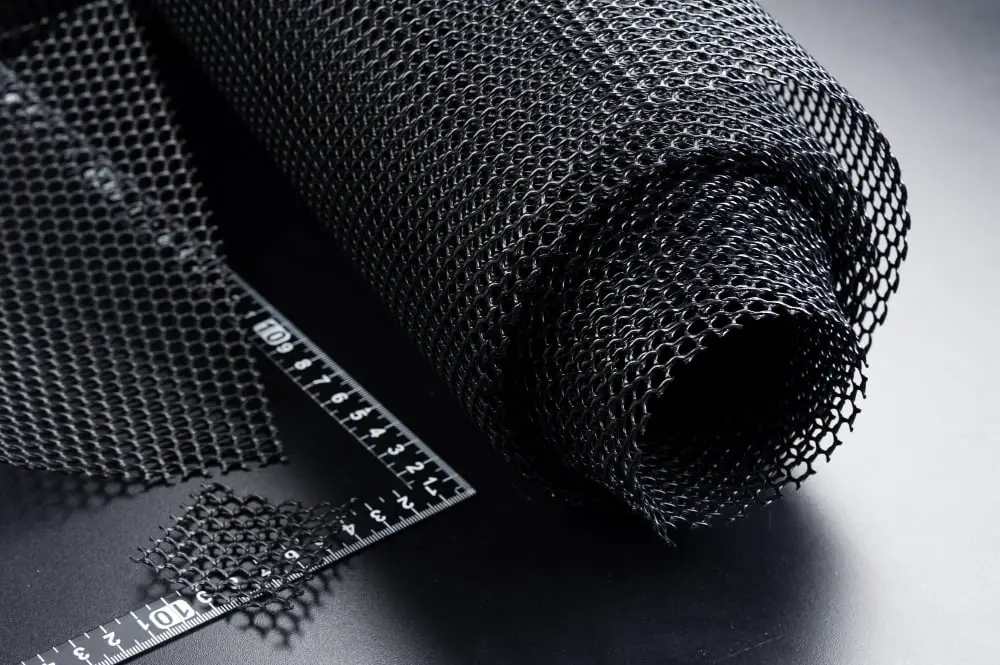
There might be instances when common problems arise during the plastic fence extrusion process. Being aware of these challenges and how to address them can save a great deal of time and money.
One such issue could be the discoloration of the fence on extruding. This is often due to overheating or retaining the polymer’s heat for too long. To combat this, adjusting the temperature setting on the extruder machine may be necessary. Also, clear the extruder thoroughly to avoid any residual dye or polymers which can lead to discoloration.
Another frequent problem is warping, which is usually a direct result of uneven cooling. Maintaining consistent cooling temperatures, and ensuring the fence material is adequately supported during the cooling process can eliminate such issues.
For uneven extrusion or inconsistency in thickness, do regular checks on the settings of your extrusion machine and verify the measurements of the die. Adjusting the speed of the machine helps to maintain a uniform dimension.
Breakage or brittle fences can be due to insufficient resin in the polymer blend. Thus, consider adjusting the amount of resin in your polymer mix to resolve this.
Remember that regular maintenance of the extrusion machine is crucial in ensuring a smooth fence extrusion procedure. It’s essential to keep the machine clean and lubricated.
These simple steps can significantly reduce any production hiccups and ensure a smooth plastic fence extrusion process.
Maintenance and Care for Plastic Fence Extrusion Machine
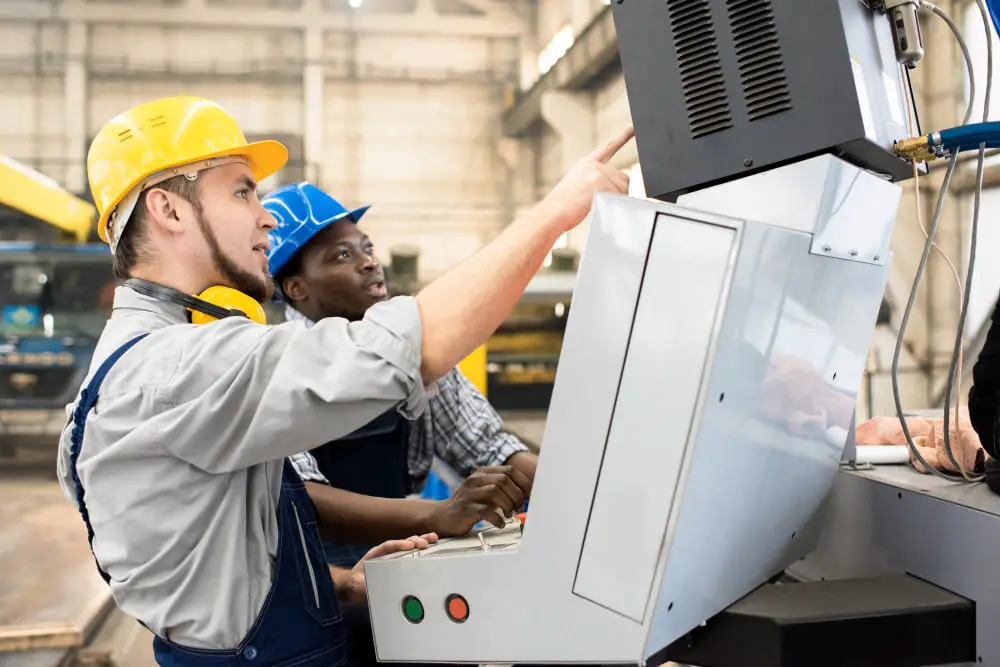
Regular inspection of the machine parts is crucial. Look out for signs of wear and tear, especially in high-strain components, like screws and barrels.
Routine cleaning of the extrusion machine helps prevent build-up of excess material. Unwanted residues can influence the quality of the extruded plastic fences.
Ensure that the cooling system works optimally. Overheating can adversely affect the machine’s performance and the quality of plastic fences produced.
The alignment of dies in the machine is vital. Misalignment can lead to uneven extrusions and should be corrected immediately.
Proactive replacement of worn-out parts saves from unexpected disruptions in production. Arrange for spare parts in advance and replace any component showing signs of excessive wear.
The machine operator must follow the manufacturer’s operating instructions carefully. This includes, for instance, not exceeding the recommended feed rate as this can put strain on machine parts and lead to premature failure.
Finally, proper lubrication of moving parts is important. This reduces friction, aids smooth operation, and extends the lifespan of the machine.
Implementing these practices in a regular maintenance program helps to enhance the operational efficiency and longevity of a plastic fence extrusion machine.
Pros and Cons of Plastic Fences Created By Extrusion
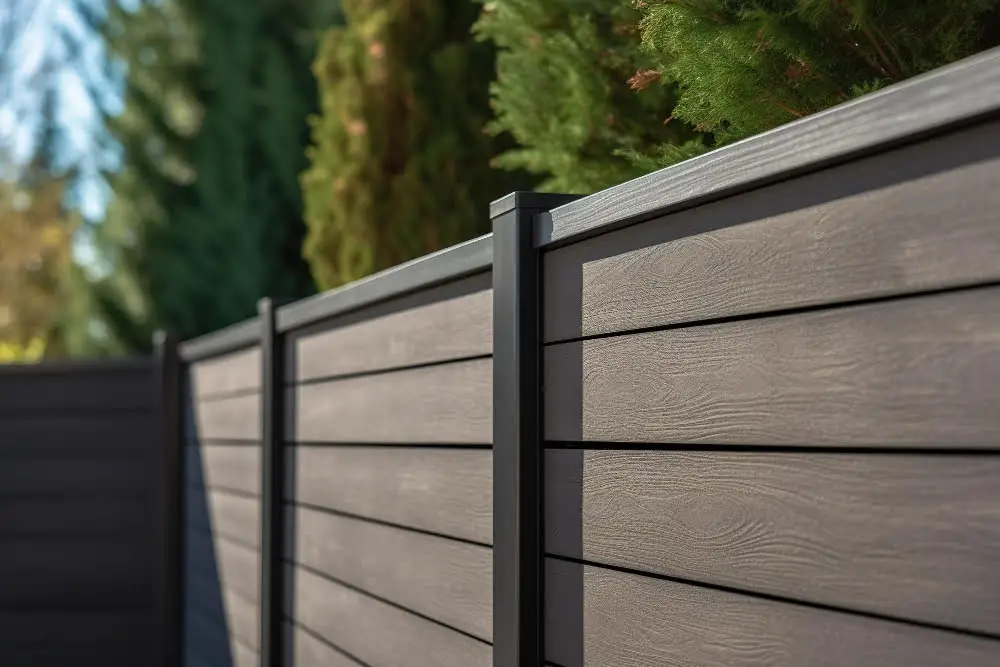
On the plus side, plastic fences produced through extrusion are known for their durability. Unlike wooden fences, they don’t rot, rust, or warp. Their maintenance needs are minimal, requiring only an occasional wash. Additionally, they are easy to install, and can be designed to mimic other materials, offering aesthetic flexibility.
However, there are few points for consideration. First, while extruded plastic fences are more resistant to weathering, prolonged exposure to sunlight can lead to color fading. Over time, they can become brittle, especially in colder climates. Finally, although plastic is generally a cost-effective material, the initial cost of installation of a plastic fence may be higher than a traditional wooden one. Also, it’s worth noting that they are less environmentally friendly, given that plastic is non-biodegradable.
To address some of these issues, innovations in the manufacturing process are currently being studied. For instance, UV-resistant plastics are being developed to combat color fading. Similarly, composite fences are becoming popular as they combine the best characteristics of wood and plastic.
Innovations in Plastic Fence Extrusion Technology
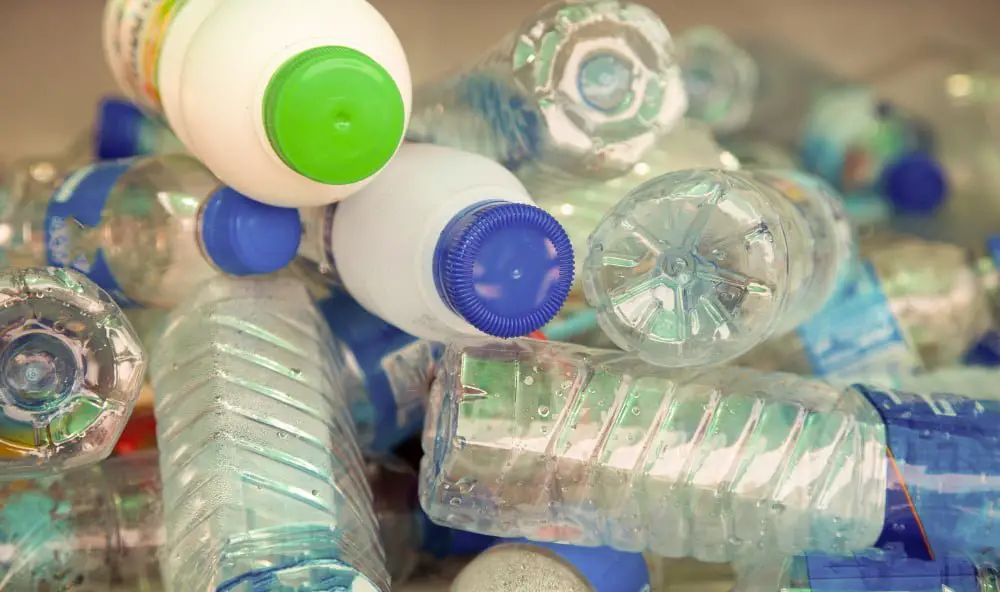
Innovation in the field of plastic fence extrusion technology has significantly transformed over recent years.
Firstly, the introduction of biocompatible and biodegradable polymers has allowed for more environmentally-friendly fencing options. These materials can decompose over time, causing less harm to the environment post-use.
The development of co-extrusion technology has also been a game-changer. In this process, layers of different types of plastic are extruded simultaneously. The end-product is a fence with an exterior layer that can withstand harsh weather conditions, providing longer durability.
Advancements in automation technology have significantly increased efficiency. Sophisticated computer control systems now precisely measure the volume of plastic going into the extruder, improving overall product consistency and reducing material waste.
Another significant innovation is the use of precision extrusion, which has upped the quality and accuracy of plastic fencing designs. This technique brilliantly maps complexity, allowing for the creation of intricate patterns and designs.
Finally, incorporating recycled plastic into the extrusion process has also become popular. This not only reduces waste but also utilizes existing resources to create cost-effective fences.
Overall, these innovations have dramatically improved the performance and lifespan of plastic fences while reducing environmental impact.
FAQ
What is the process of PVC profile extrusion?
The process of PVC profile extrusion involves feeding the PVC extrusion compound into an extruder from a hopper, where it is melted and subsequently forced through a die that determines the resultant cross-sectional profile.
What is extruded fencing?
Extruded fencing refers to fences made from materials like aluminum or vinyl that are shaped and molded into specific forms by being forced through a die in a process called extrusion.
How are plastic fences made?
Plastic fences are primarily manufactured using monoextrusion, where polyvinyl chloride is injected with ultraviolet inhibitors, or co-extrusion, which involves the use of two layers of PVC – a coverage layer and an inner layer.
What kind of plastic are fences made of?
Fences are commonly made of vinyl, a type of plastic that involves PVC (polyvinyl chloride), which offers excellent impact strength, durability, and weatherability.
What are the main advantages of using PVC in fence construction?
The main advantages of using PVC in fence construction are its resistance to weathering, rot and insect damage, low maintenance needs, and versatility in design and color.
How does the quality and longevity of plastic fencing compare to traditional materials?
Plastic fencing, made from durable polymers, often outlasts traditional materials like wood or metal due to its resistance to weather, rot, and pests.
What is the environmental impact of producing and recycling plastic fences?
The production and recycling of plastic fences contribute to the environmental impact by consuming energy, releasing greenhouse gases, and potential plastic waste pollution, yet recycling mitigates these effects by reducing the need for new raw materials.
Recap