Explore the effective steps to eliminate splay in injection molding, enhancing the quality and appearance of your polymer products.
Splay in injection molding, a common defect often appearing as silver streaks, can compromise the aesthetic and structural integrity of your molded parts. To eliminate splay, several factors need to be considered: the material’s moisture content, the molding machine’s temperature settings, and the injection speed.
Firstly, ensure that the polymer material is properly dried, as excess moisture can lead to splay. Secondly, optimize the temperature settings of the molding machine; too high temperatures can degrade the material causing splay. Lastly, control the injection speed; a too-fast speed can cause material shearing resulting in splay.
This article will delve into these aspects in detail, providing comprehensive guidelines on how to effectively prevent splay in injection molding.
Key takeaways:
- Properly dry the polymer material to eliminate excess moisture.
- Optimize temperature settings of the molding machine to avoid material degradation.
- Control injection speed to avoid material shearing and splay.
- Trapped air, inadequate drying, high temperatures, and contamination can cause splay.
- Splay marks negatively impact appearance, production, and structural integrity.
Understanding Splay in Injection Molding
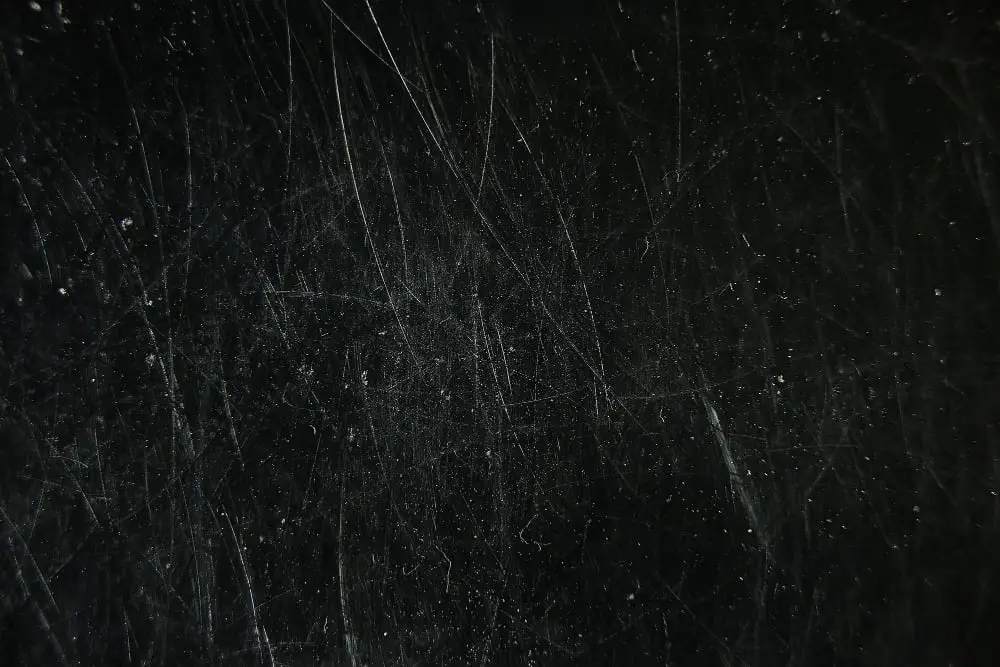
Splay is a commonly encountered problem in injection molding, recognizable as silver or silver streaks on the surface of the molded parts. Although they might seem minor, splay marks can degrade the product’s aesthetic and functional qualities, undermining its market value.
This issue typically originates from the presence of moisture in the polymer during the molding process. Even tiny amounts of water in the plastic can turn into steam when subjected to high temperatures, leading to small eruptions in the surface of the finished product.
In addition to moisture, excessive heating, rapid injection, and using an old or degraded plastic could be culprits. Such situations can cause the molten plastic to degrade and form gas bubbles, which result in splay.
To avoid splay, it is crucial to ensure that the plastic is completely dry before starting the molding process. Adjusting the temperature and rate of the injection might also be necessary for certain types of plastic. If the issue persists, consider testing with a new batch of plastic, as the old one might have degraded beyond usability.
Remember, each polymer has specified drying conditions, temperatures, and injection rates for optimal results. By adhering to these guidelines and ensuring optimal machine condition, you can significantly minimize, if not completely eliminate, the occurrence of splay in injection molding activities.
Causes of Splay in Injection Molding
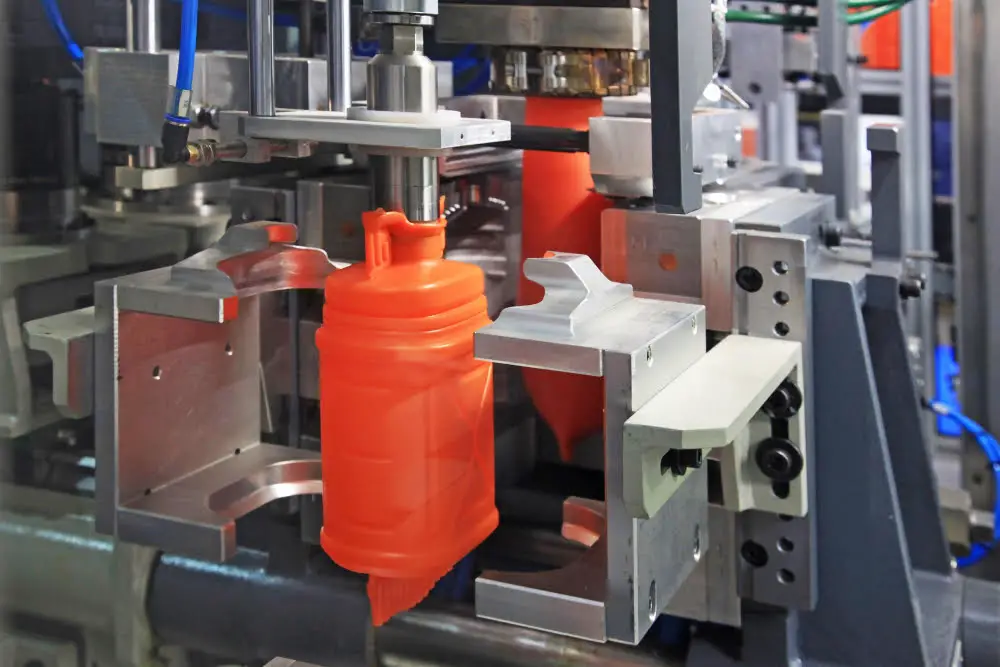
Splay, also known as silver streaking, often occurs in the injection molding process due to several underlying causes.
First, trapped or compressed air in the mold cavity usually contributes to the formation of splay. This results from the high injection speed, forcing the plastic material into the mold cavity. The trapped air does not get sufficient time to escape and thus ends up trapped within the mold, causing the splay appearance.
Secondly, inadequate drying of the polymer material before the process starts can also cause splay. Most plastic materials absorb moisture from the atmosphere, and if not properly dried, the moisture content can lead to splay. As the mold heats during the process, the moisture turns into steam hence causing the streaking effect.
Different plastic materials have varying drying requirements, all of which must be met to avoid splay in the end product.
Temperature variation is another key source of splay in injection molding. When the barrel or mold temperature significantly exceeds the optimal point necessary for processing a specific plastic material, splay can occur. High temperature can cause the material to degrade, leading to discoloration and formation of splay.
Finally, plastic material contamination is another potential cause of splay. If the material used contains foreign particles such as dust or dirt, splay might occur. Therefore, ensuring that the plastic material is clean and free from foreign particles will reduce the chances of forming splay.
The Impact of Splay Marks in Injection Molding
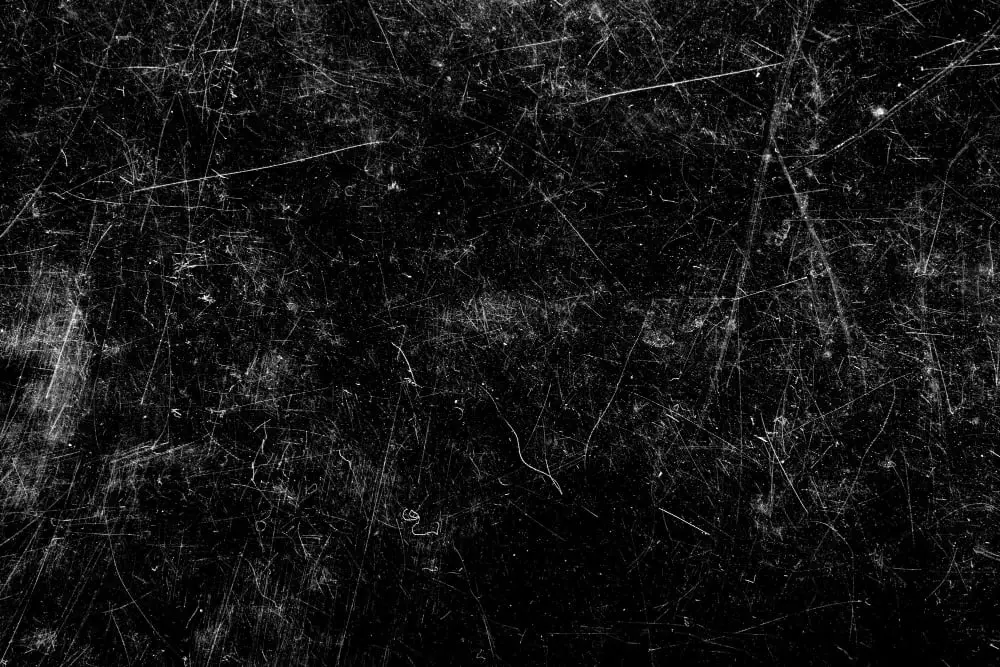
The manifestation of splay marks in injection molding can lead to an array of production, aesthetic, and functional challenges.
Splay marks often mar the surface finish, negatively affecting the aesthetic quality of the produced parts. This is particularly critical for products where appearance is a crucial sales factor, like consumer goods and automotive parts.
From a production perspective, these defects might lead to an increase in rejected parts, which in turn increases the production cost and time. In high-volume production environments, even a small percentage of rejected parts can have a considerable impact.
In terms of functionality, while some may believe that splay marks only affect appearance, certain instances of splay can also lead to structural weaknesses in the finished part. This could impact the product’s performance, reducing its durability and potentially leading to failure.
In order to avoid these complications, it is essential to understand effective ways of preventing and fixing splay in injection molding. Factors like proper material preparation, process parameter adjustment, and equipment maintenance could play a significant role here.
Preventing Splay in Injection Molding
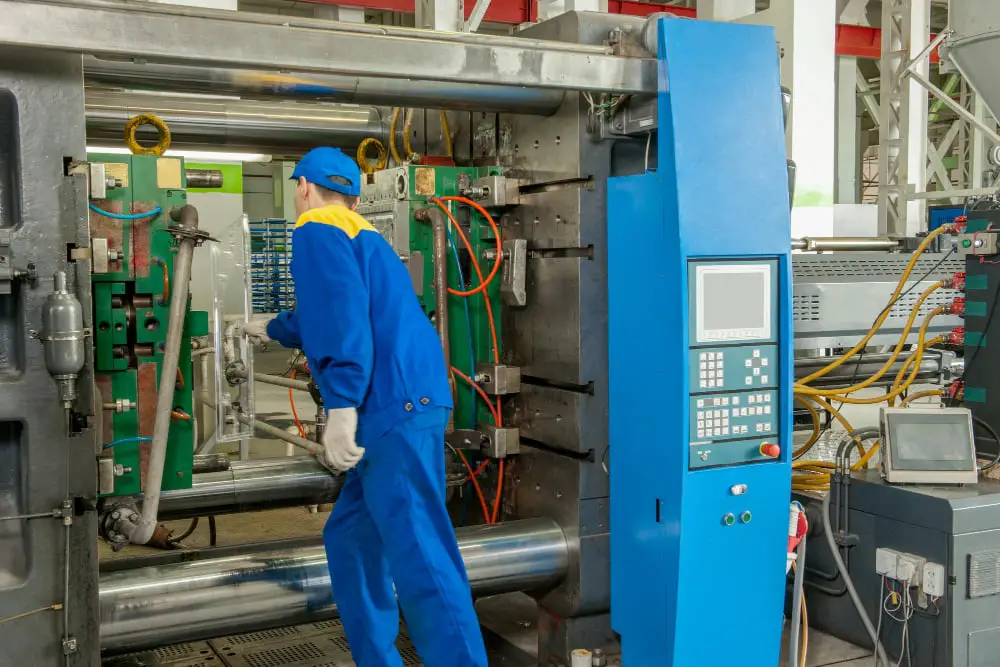
To curb the issue of splay in injection molding before it appears, there are a handful of measures to keep in mind:
Regular maintenance of the injection molding machine must be a priority, particularly cleaning the hopper, feed zone, and the screw.
Choosing the right plastic material is a vital step. Each polymer has a specific temperature and humidity threshold which should not be exceeded.
Correct drying of the polymer pellets can significantly decrease moisture content. It is of utmost importance to dry the pellets thoroughly before processing, by adhering to the manufacturer’s recommended procedure.
The hopper throat temperature should be maintained, as improper temperatures might cause some materials to cluster together and create moisture, which can, in turn, lead to splay.
Ensuring proper venting is also important, allowing trapped air and volatile components to escape.
Controlling the injection speed and pressure can help reduce splay. A lower speed and pressure at the outset, increasing gradually, can usually tackle the problem.
Paying attention to these simple steps can go a long way in preventing splay in injection molding, enhancing the overall look and quality of the manufactured plastic parts.
Fixing Splay in Injection Molding
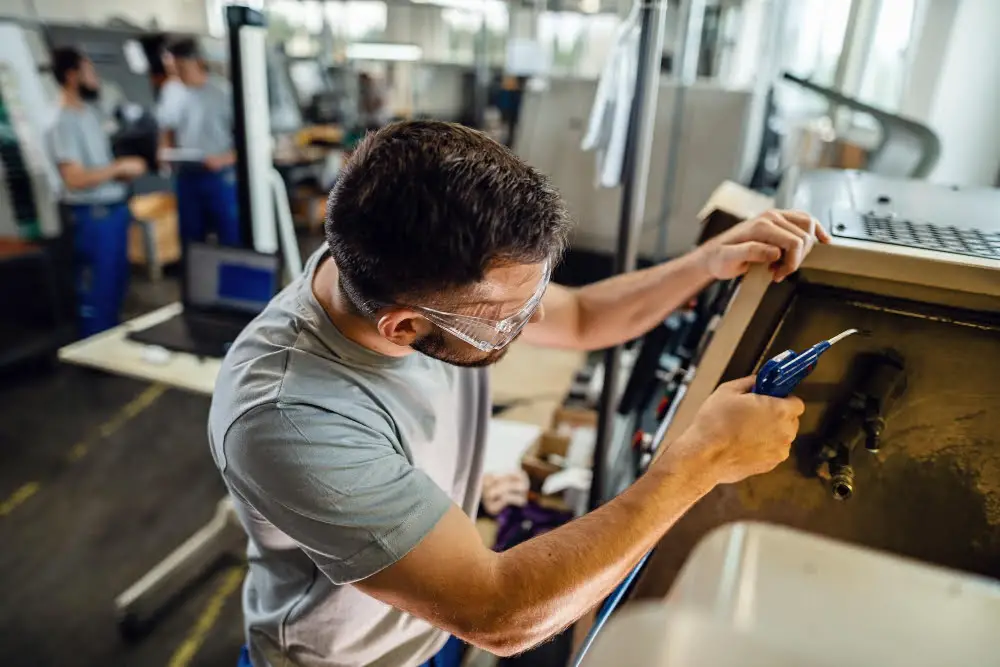
Addressing the issue of splay in injection molding may seem daunting, but following some key steps can make it more manageable.
First and foremost, regulate the processing temperature. Carefully adjusting the melt and mold temperature can help prevent excessive moisture and ultimately minimize splay.
Next, maintain dryness in all materials. It is hydroscopic raw materials, namely those that attract moisture, which contribute significantly to splay. Thus, taking care to dry these materials efficiently is essential.
Regulating injection speed is another important step to keep splay at bay. Fast injections may result in an unstable melt front, leading to splay, so reducing the speed can be beneficial.
Next, consider the condition of the machinery used. Well-maintained and clean equipment can play a significant role in preventing splay. Regular inspection and servicing, including checking for worn screws and barrels, ensures that the machine performs at its best.
Lastly, the cooling time is another factor that needs attention. A longer cooling time can help the polymer to solidify adequately, making the part less susceptible to splay.
Remember, the key to fixing splay lies in the careful control and monitoring of the entire injection molding process.
Implications of Splay in Plastic Production
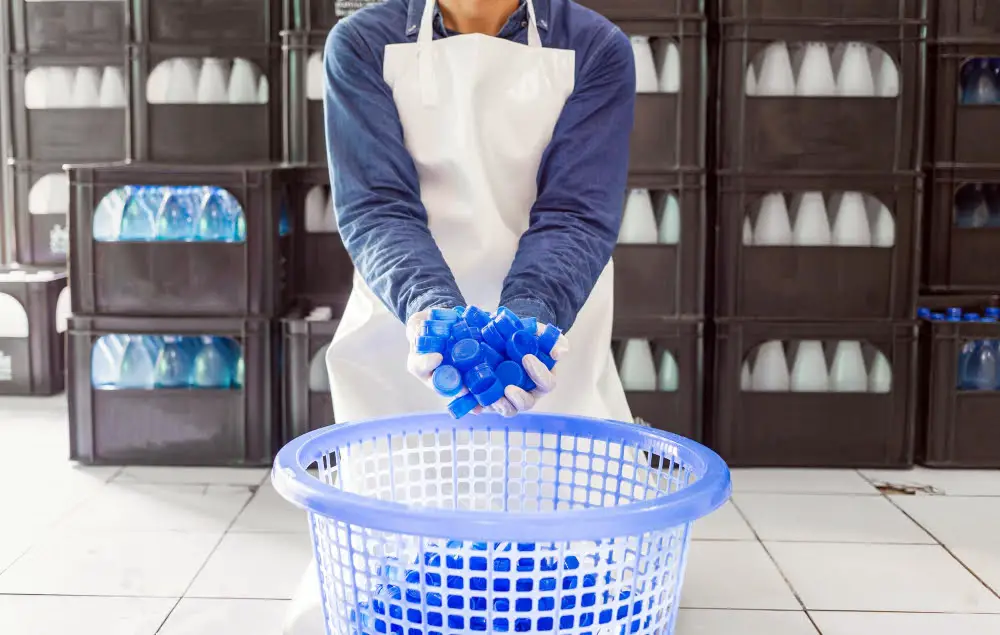
Splay marks can degrade the aesthetic appeal of a product, influencing customers’ buying decisions – a critical concern in industries where design and appearance matter. They have operational impacts as well, leading to an increased number of rejected parts.
High rework and scrap costs are a direct consequence of splay marks. This not only increases the cost of production but also impacts the sustainability process as more material is wasted.
The presence of splay indicates improper injection molding conditions. This could range from poor equipment maintenance, incorrect material handling to unsuitable process parameters. Ignoring splay thus could lead to further, potentially irreversible damage to the molding machinery.
A commonly overlooked effect is the potential undermining of a part’s structural integrity. Splay often affects the consistency of the plastic, which might impact the strength of the final product. In sectors such as construction or automotive, where the mechanical strength of a part is critical, the presence of splay could lead to safety concerns.
Understanding these implications aids in realizing the importance of tackling splay issues swiftly and effectively. Necessary actions include adapting appropriate maintenance procedures, optimizing process conditions, and using correct handling measures for molding materials. The key is not just to fix the evident damage, but to trace and rectify its root cause to prevent recurrence.
Effective Solutions for Minimizing Splay Marks
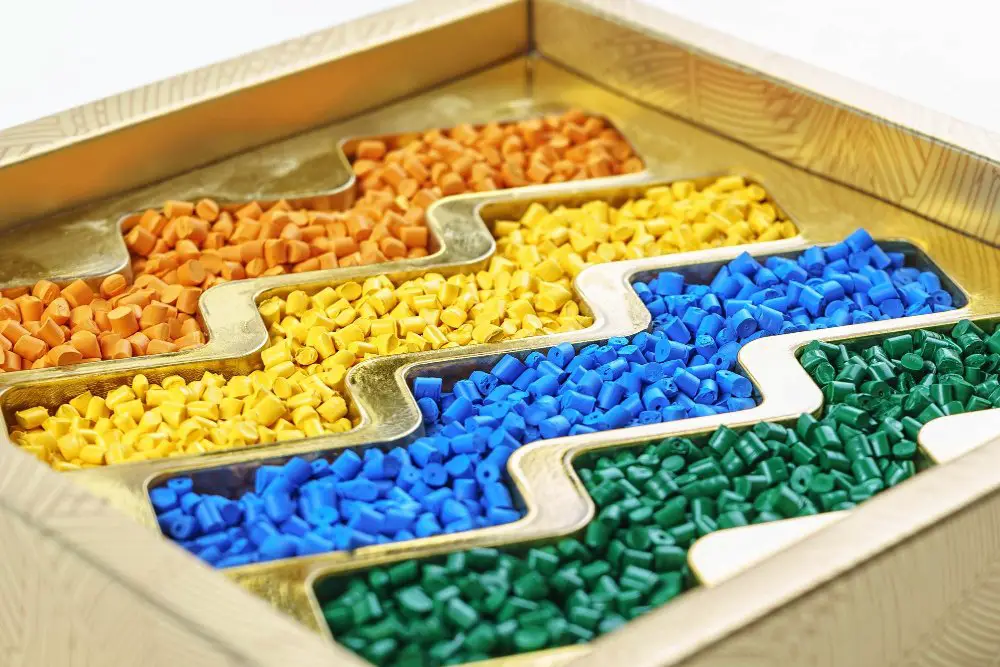
Firstly, optimizing the drying process is essential. This often involves properly drying the polymer material before molding to maintain its integrity.
Secondly, regulating the temperature also plays a significant role. The mold temperature should be controlled to prevent the occurrence of splay marks.
Thirdly, adjusting the injection speed can be instrumental. A slower speed may lessen the risk of splay by minimizing the introduction of moisture into the material while ensuring a more uniform filling of the mold.
Another strategy is the careful handling and storage of the material. Keeping the material properly sealed in low humidity storage can prevent the absorption of moisture, a common cause of splay.
Lastl*y*, maintaining the equipment used in the process is critical. Regular checks and cleaning of the injection nozzle can help avoid splay as any debris or contamination can compromise the molding process and cause splay.
By incorporating these steps, we can reduce the possibilities of splay in injection molding, assisting in enhancing the final product’s aesthetics and physical properties.
FAQ
How do you reduce splay?
To reduce splay in plastics, it’s essential to keep the material dry as moisture can cause condensation on the surface of plastic granules, leading to this issue.
What is splay in injection molding?
Splay in injection molding refers to a cosmetic imperfection characterized by the formation of silver or white streaks on the surface of the molded plastic part.
What is the cause of splay?
Splay in polymers is caused primarily by moisture trapped in the resin that turns into steam within the heated barrel of an injection molding machine, leading to the formation of tiny gas bubbles that streak across the plastic during injection.
What is the molding defect splay?
Splay is a common molding defect characterized by off-color streaks, often silver, appearing on the surface of plastic injection molded products.
How do material properties influence splay in injection molding?
Material properties, specifically viscosity, thermal conductivity, and melt temperature, critically influence splay in injection molding by determining the flow and cooling rates in the cavity.
What are the effective preventive measures against splay in the injection molding process?
Effective measures preventing splay in the injection molding process encompass drying polymers properly before use, maintaining mold temperatures above the polymer’s glass transition temperature, and optimizing barrel temperatures and injection speeds for effective polymer melting and molding.
How does the splay defect impact the final product’s quality in injection molding?
The splay defect in injection molding results in a visible, streak-like discoloration on the final product, thereby reducing its aesthetics and potentially its physical properties and performance quality.
Recap