Metal injection molding is a versatile process that combines the benefits of plastic injection molding and powdered metallurgy to create complex, high-density parts with superior strength and excellent surface finish.
Metal Injection Molding (MIM) is an advanced manufacturing technology that combines the versatility of plastic injection molding with the strength and integrity of metals. It’s a two-step process where metal powder is mixed with a binder to form a ‘feedstock’ that is then shaped into complex geometries through injection molding.
The molded part is then subjected to a process called debinding, where the binder is removed, leaving behind a ‘green part’. This part is then sintered in a high-temperature furnace to achieve its final, solid metal form. MIM is ideal for mass-producing small, intricate metal parts that would be costly or impossible to manufacture through traditional methods.
Stick around to learn more about the applications, advantages, and limitations of this innovative process.
Key takeaways:
- Metal Injection Molding (MIM) combines plastic injection molding with powdered metallurgy.
- MIM involves feedstock preparation, molding, debinding, and sintering.
- MIM is used for mass-producing small, intricate metal parts.
- Materials used in MIM include stainless steels, superalloys, low alloy steels, controlled expansion alloys, and high-density alloys.
- MIM offers advantages such as complex shape production, cost savings, design flexibility, and diverse applications.
Understanding Metal Injection Molding
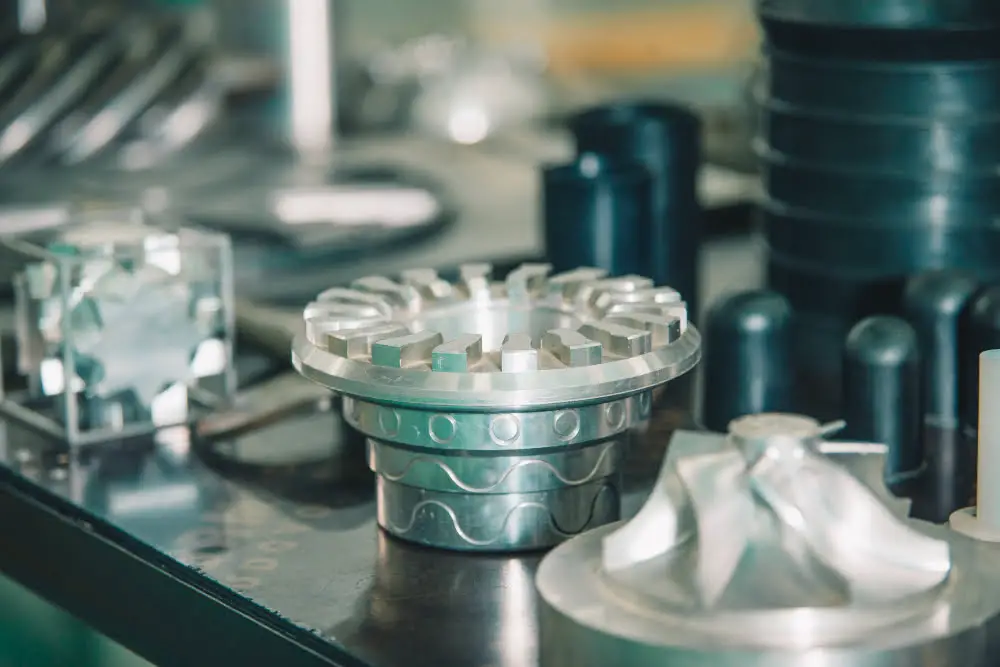
Metal injection molding (MIM) stands as a powerful technique for shaping metal parts in high volumes. This intricate process combines the flexibility of plastic injection molding with the strength and integrity of wrought metals to produce diverse shapes that may be challenging to construct through traditional methodologies.
MIM includes four key steps:
Feedstock preparation explores a mix of metal powder and a binder to create a substance that can easily be injection molded.
Molding, the next step, uses the feedstock in a heated mold to form the desired shape.
Debinding involves removing the binder to leave a fragile, metal part known as a ‘green part.’
Finally, sintering heats this ‘green part’ to a temperature below its melting point but high enough to promote diffusion bonding among particles, forming a dense, robust part.
The process allows for the production of metal parts with complex geometries and fine details, often eliminating the need for secondary processing. While the initial set-up costs can be high, the expense is overall justified considering its ability to manufacture intricate, high-volume components efficiently.
Process of Metal Injection Molding
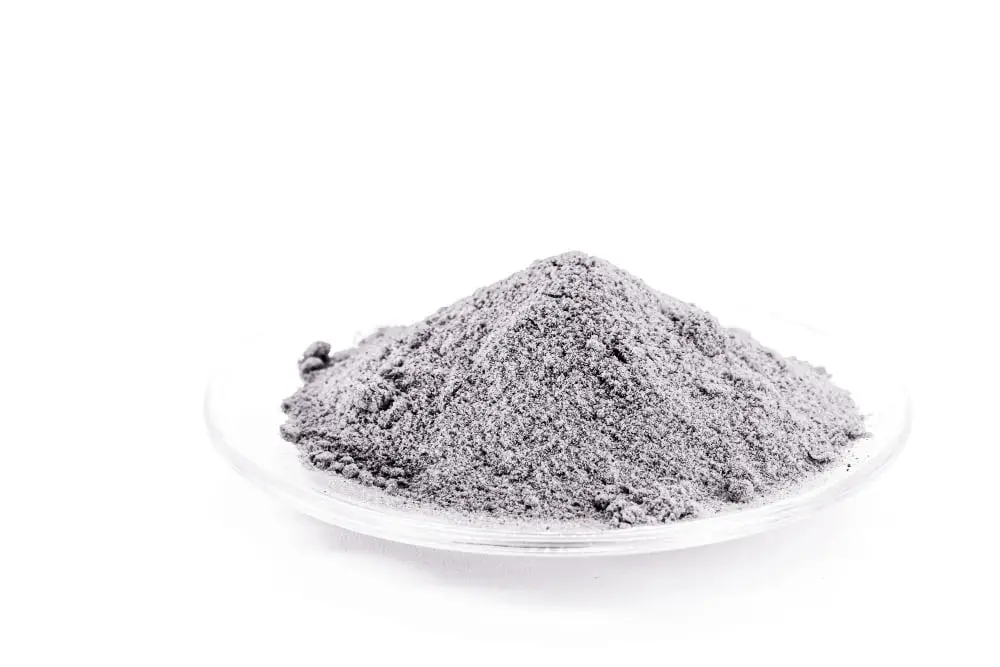
Metal Injection Molding (MIM) is a complex procedure that integrates the advantages of plastic injection molding and powder metallurgy. The process begins with a combination of metal powder and a polymer binder, which forms a feedstock. This feedstock is heated and then injected into a mold cavity to form the desired shape.
After the shape is formed, the molded part undergoes a debinding process. During debinding, the polymer binder is removed, leaving behind a “green” part consisting predominantly of metal. This is typically achieved through the use of heat or a solvent to dissolve the binder.
Finally, the “green” part is sintered – heated to a temperature just below the metal’s melting point. Sintering solidifies the metal, causing the particles to fuse together, create a denser, stronger component with the same shape as the original mold.
This process includes:
- Creating a feedstock: a mix of metal powder and polymer binder
- Injection molding: injecting the feedstock into a mold to form the shape
- Debinding: removal of the polymer binder to leave a “green” part
- Sintering: heating the “green” part to solidify and strengthen the metal structure
Working Principle of Metal Injection Molding
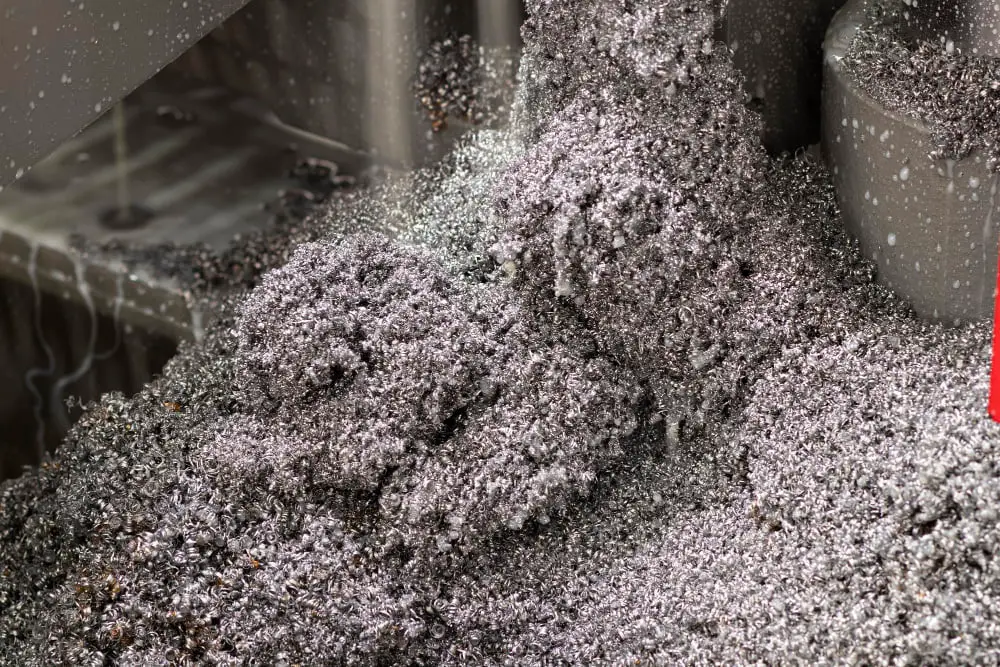
The metal injection molding process operates on four chief stages: mixing, injection, debinding, and sintering.
First, feedstock – a combination of metal powder and thermoplastic binder – is mixed to create a pliable material that can be molded. This pellet mixture is then heated and subsequently injected into a closed mold using the same methods as plastic injection molding.
With the form in place, it moves to the debinding phase, where the majority of the built-in binder material is chemically or thermally removed. The result, a lightly sintered ‘green’ part, still holds its shapes but remains fragile due to the porous structure.
Finally, the part goes under high-temperature sintering, forcing the remaining binder out while densifying the metal particles. This step brings the product to its final size but with denser and stronger characteristics, similar to wrought metal.
Throughout these steps, the dimensions, design intricacies, and specific material characteristics are all maintained, granting MIM a superior edge in precise, complex component creation.
Materials Used in Metal Injection Molding
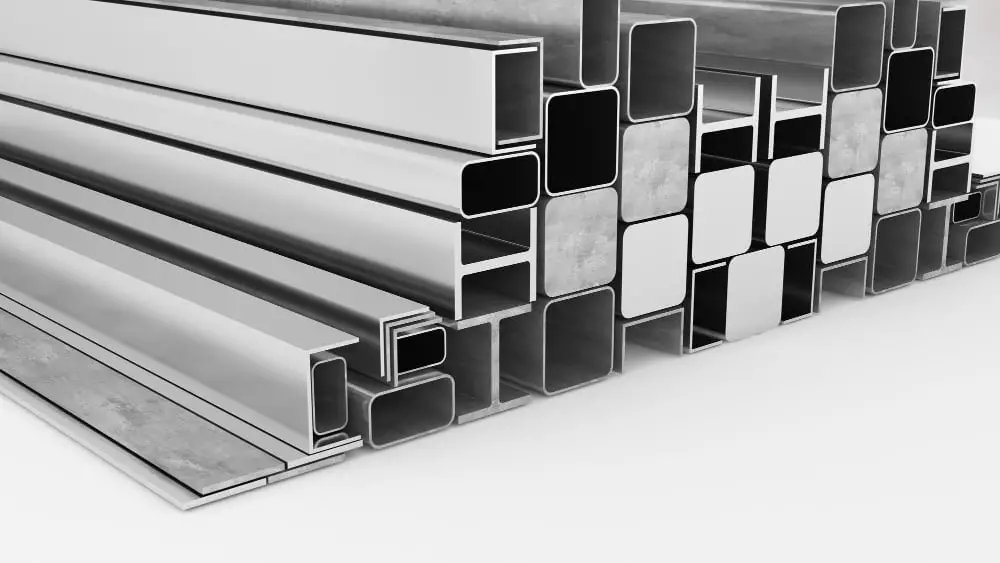
Several types of metals prove ideal for injection molding due to their specific properties.
Stainless steels are a common choice. They demonstrate high tensile strength, excellent resistance to corrosion, and ability to withstand high temperatures, making them fit for components with demanding conditions.
Superalloys, typically alloyed with nickel, cobalt, or iron, are also frequently used. Characterized by excellent strength, ability to function at high temperatures, and superior corrosion and oxidation resistance, these materials find their usage in high-performance applications such as aerospace and energy sectors.
Low alloy steels expand the variety of properties through the addition of different elements. Depending on the selected component, they offer benefits such as improved hardness, wear resistance, and toughness.
Controlled expansion alloys, defined by their heat expansion properties, are suitable for precision applications. These metals limit expansion and contraction, maintaining their shape under temperature changes – a critical factor in telecommunications and aerospace industries.
Last but not least, high-density alloys offer alternatives when high weight or balance are necessary in a small package. They provide a significant advantage in sectors such as medical, defense, and automotive.
Each material selected for metal injection molding serves a unique purpose and brings special properties to the table. The right choice depends on the end application, performance requirements, and expected conditions.
Role of Superalloys in Metal Injection Molding
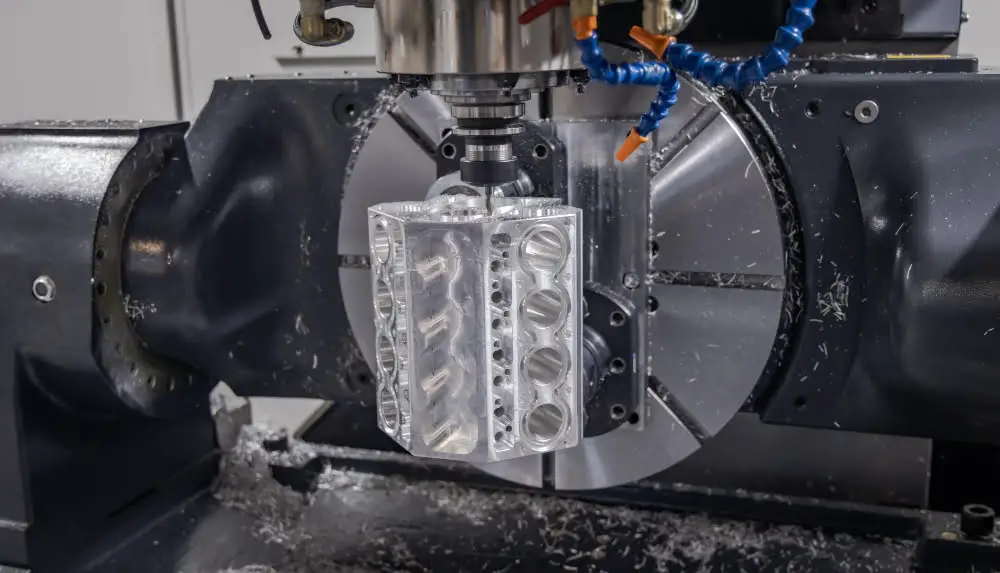
Superalloys’ inherent qualities make them suitable for certain parts molded through metal injection. Characterized by their excellent resistance to high temperatures, corrosion and wear, superalloys maintain mechanical performance at elevated conditions, far outstripping common metallic materials.
Typically, these alloys are composed of several elements including nickel, cobalt, iron, and smaller quantities of other metals like chromium, tungsten, and titanium. This blend of materials allows superalloys to resist deformation and maintain structural integrity at high stress levels.
Ideal for components exposed to intense heat or aggressive conditions, superalloys find their way into various industry applications. From aerospace parts that need to withstand extreme temperature variations to turbine blades and medical equipment demanding high-performance levels, superalloys play an intrinsic role.
To maximize the benefits of using superalloys in metal injection molding, key steps include material selection (deciding the most appropriate superalloy given the application), part design (tailoring the design to maximize the benefits of the chosen superalloy), and molding process (adjusting temperatures, pressures and cooling rates for optimal results). This process tailors the superalloy parts to meet precise application demands, truly exploiting the advantages of metal injection molding.
Importance of Stainless Steels in Metal Injection Molding
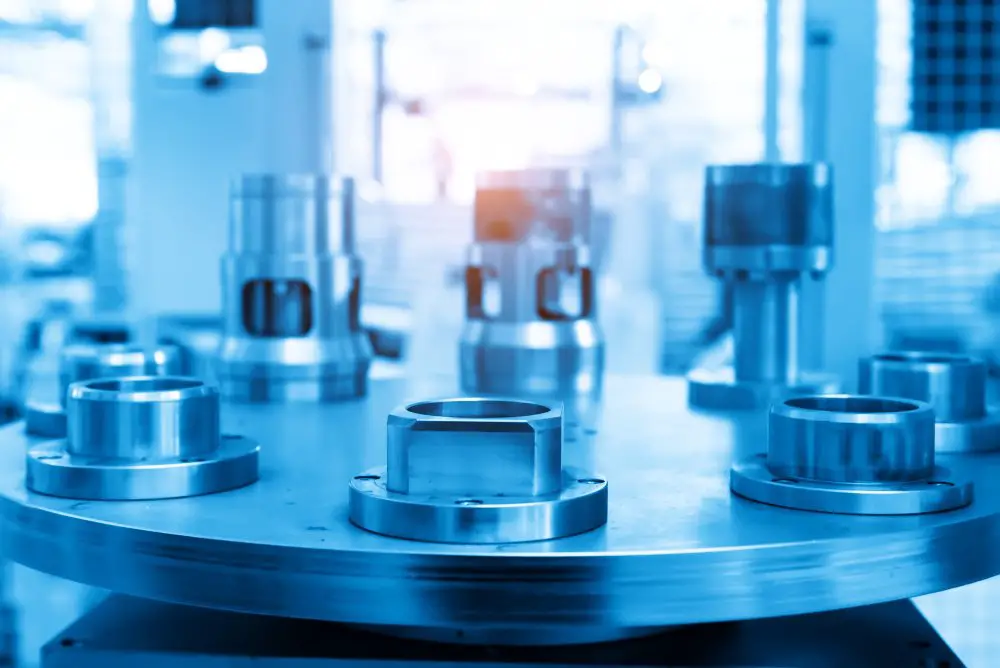
Stainless steel holds significant importance in the metal injection molding (MIM) process due to its distinct properties. Its ability to resist corrosion makes it an ideal material for MIM. As a construction material, its durability and structural stability under different conditions enhance product life, making it a popular choice for components of medical devices, aerospace, and automotive industries.
Three key aspects underscore the utility of stainless steel in MIM:
- Advanced Corrosion Resistance: Stainless steel contains chromium, which when exposed to oxygen, forms an invisible chromium oxide layer. This passive layer protects the underlying metal, making stainless steel inherently resistant to corrosion.
- Mechanical Durability: The mechanical strength and durability of stainless steel make it resist wear and tear. This property, coupled with good ductility, makes it ideal for components that require precise dimensional tolerance.
- Wide Ranges of Alloy Choices: There are numerous types of stainless steel, each designed for specific applications. From austenitic, ferritic, to martensitic steels, MIM allows the use of these different varieties, which broaden functionality and usage.
- Enabling Complex Part Designs: Due to the versatility of stainless steel, MIM allows construction of highly complex, intricate designs with high density and superior performance.
No matter the environment or application, stainless steel proves its worth in MIM, primarily due to corrosion resistance, mechanical strength, and design flexibility.
Function of Low Alloy Steels in Metal Injection Molding
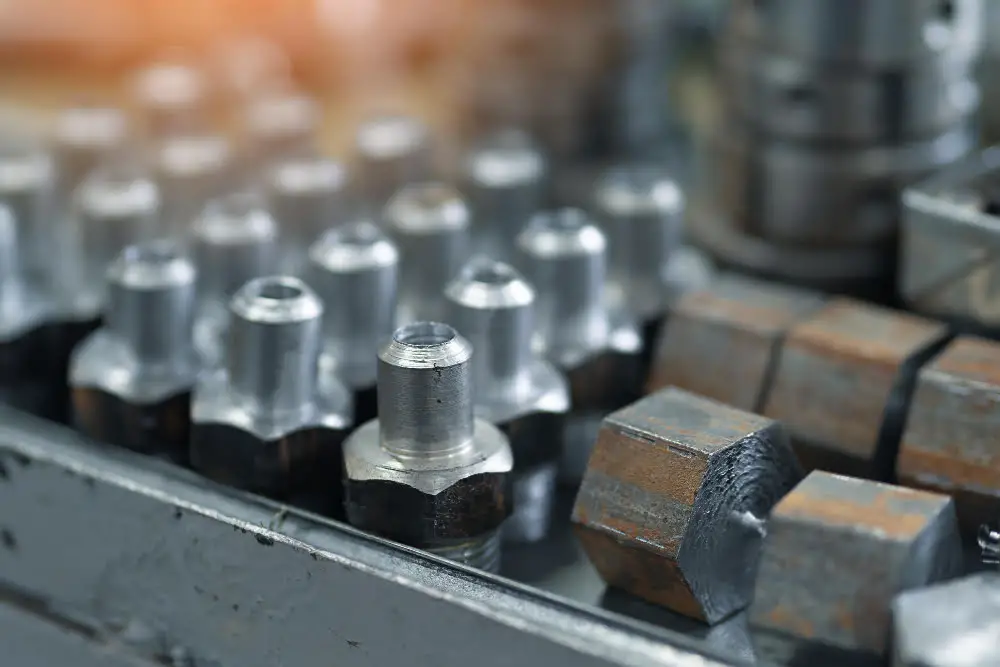
Low alloy steels, characterized by notable strength and hardness, play an integral role in metal injection molding (MIM). These properties make them an attractive choice for manufacturers employing MIM to fabricate durable components.
The superior strength of these alloys make them optimal for heavy-duty applications. Components made from low alloy steel are most likely to withstand high stress scenarios without deformation.
The hardness of low alloy steel provides resistance to wear and tear. This characteristic extends the life of components crafted from this material, reducing replacement frequency.
This material also provides excellent surface finish, which indicates less requirement for post-processing techniques. The reduced need for further polishing or treatment translates to less manufacturing time and cost.
In MIM, low alloy steels’ compatibility with heat treatment further assures durability. Components can undergo processes like quenching or annealing to enhance various physical properties, such as hardness and toughness, based on the intended application.
Furthermore, low alloy steels can be readily mixed with binding agents in the MIM process. This blending ability facilitates a better flow of material in the mold, ensuring precise and detailed component shapes.
Remember, the successful use of low alloy steels in MIM depends heavily on understanding the material’s properties and how best to harness them during the process.
Application of Controlled Expansion Alloys in MIM
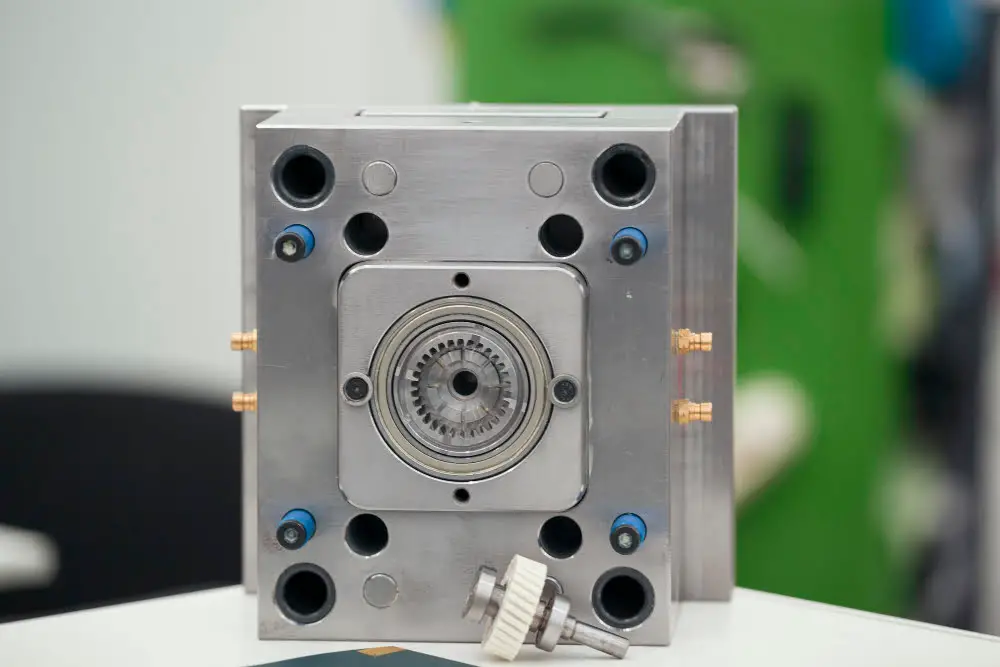
Controlled expansion alloys are a vital component in the metal injection molding process. These alloys are typically made up of nickel or iron, combined with other materials, such as silicon or aluminum. The overall proporting of every ingredient is meticulously managed to accomplish a precise and consistent rate of thermal expansion.
Maintaining consistent thermal expansion is important for specific applications, particularly in industries like electronics and telecommunications. Here, components often experience drastic temperature changes and need to maintain their original shape and properties. The accurate control of thermal expansion offered by these alloys makes them invaluable to metal injection molding.
Furthermore, their use in the MIM process enables the manufacture of complex pieces with high precision and fine details. This makes it possible for sectors such as aerospace and precision instruments to benefit from high-performing parts, made quickly and cost-effectively via this method.
Finally, these alloys also have excellent corrosion-resistant properties. Hence, they are useful in environments where durability and long-lasting performance are critical. This corrosion resistance is another reason why controlled expansion alloys are preferred in the MIM process.
Understanding these key facts helps to appreciate the value controlled expansion alloys bring to the MIM process and why they’re used in various industries.
Use of High Density Alloys in MIM
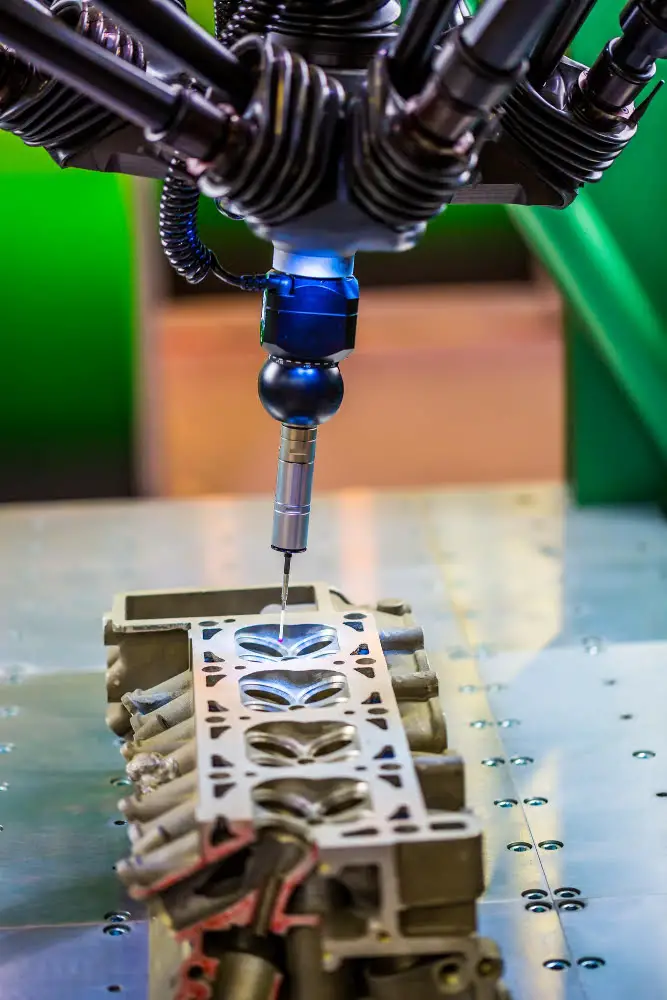
High density alloys pose an interesting facet of Metal Injection Molding (MIM). These alloys consist mainly of metals like tungsten, tantalum, and other similar materials. The significance of these kinds of substances in MIM is threefold:
- Enhanced Material Performance: The primary metals applied in high-density alloys considerably increase material durability due to their inherent toughness. These alloys, when used in the MIM process, contribute to the manufacture of components that can withstand high stress and pressure without deformation.
- Radiation Shielding: A unique application comes in the form of radiation shielding. High-density alloys, when used in the MIM process, create parts with successful radiation-blocking properties. This makes them ideal for use in medical and nuclear power industries.
- Weight Considerations: High-density alloys account for weight in applications where it’s mandatory. By using these alloys in MIM, heavy components can be produced without increasing the overall size of the part, providing a balanced solution for particular engineering challenges.
Just by following these simple comprehensions it’s easy to see why high density alloys have proven to be a valuable contributor in the MIM process.
Benefits and Practical Applications of Metal Injection Molding
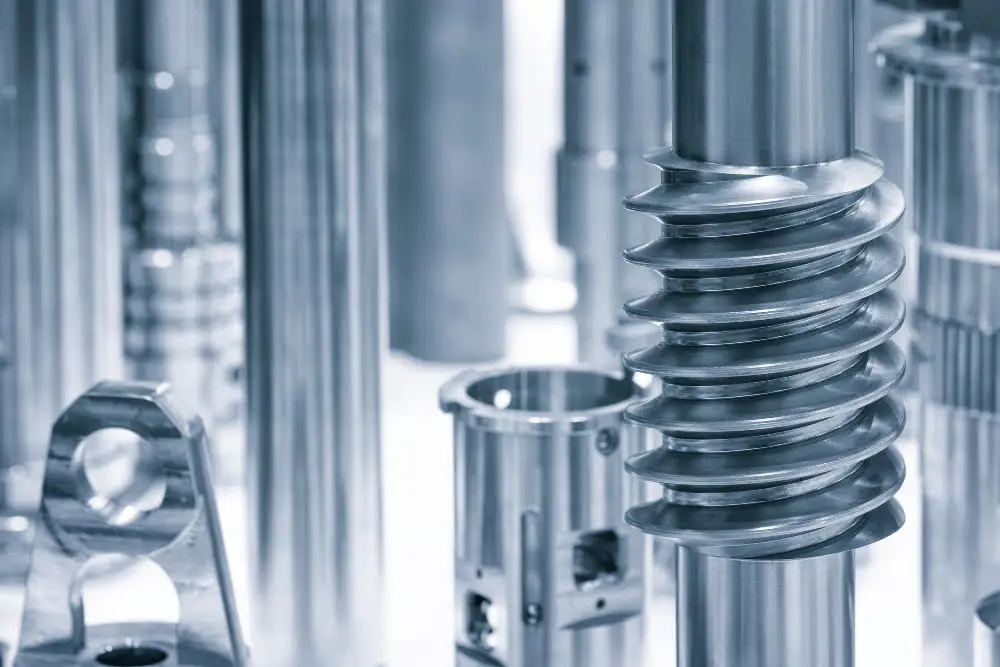
Metal Injection Molding (MIM) offers numerous advantages and is used in a wide variety of situations.
Firstly, it is beneficial due to its capability for high-volume production of complex shapes. MIM eliminates the need for secondary operations, as the pieces created are net-shaped and require little to no further processing.
Secondly, MIM can result in significant cost savings in the production process. This could be achieved through reduction in assembly operations, infusing extra performance traits or by producing intricate shapes that would be expensive if machined from solid materials.
Thirdly, MIM offers a diverse selection of alloys, increasing design flexibility. Due to the versatility of materials, including stainless steel, nickel alloys, and titanium, designers have greater freedom to create products to precise specifications.
Lastly, MIM has extensive applications covering various fields such as the automotive industry, medical and dental devices, firearms, electronics, and more. For instance, it is used to manufacture surgical instruments and orthodontic braces in the medical field, or delicate connectors and sensors in technology equipment.
FAQ
What is metal injection molding used for?
Metal injection molding is primarily used in industries like aerospace, automotive, and medical devices, where it offers a cost-effective alternative to conventional metal manufacturing processes due to its ability to combine the design flexibility of plastic injection molding with the robustness and endurance of metallic materials.
How is metal injection Moulding done?
Metal injection molding is a process in which feedstock is melted and injected into a mold’s cavity, allowing it to cool and solidify into the desired part’s shape.
What metal is used for injection molding?
Metal used for injection molding includes materials like precious metals, titanium alloys, cobalt-chromium, nickel, nickel-base super alloys, molybdenum, molybdenum-copper, cemented carbides (WC-Co), cermets (Fe-TiC), and particulate composites.
What is the difference between metal injection molding and plastic injection molding?
While both techniques involve injecting materials into a mold, metal injection molding utilizes metal powder bound to a thermoplastic binder to produce metal parts, requiring extra steps to remove the binder and sinter the powder, contrastingly plastic injection molding directly utilizes molten plastic.
What are the advantages and disadvantages of metal injection molding in construction?
Advantages of metal injection molding in construction include precision in creating complex shapes and high volume production, while its disadvantages are high initial setup cost and complexity in molding sizeable parts.
How does metal injection molding affect the physical properties of the final product?
Metal injection molding enhances the physical properties of the final product by providing uniform density and superior dimensional and structural precision.
Are there any environmental considerations to take into account with metal injection molding?
Yes, metal injection molding has environmental considerations such as the energy-intensive nature of the process and potential for hazardous waste generation.
Recap