Discover the game-changing benefits of Polymer Matrix Composites in construction as we delve into its versatile applications and advantages.
One of the most exciting developments is the use of polymer matrix composites (PMCs) in construction.
PMCs are a type of material that combines two or more components to create a stronger and more durable product than traditional materials such as wood, steel, or concrete. They have been used in various industries for decades, but it’s only recently that their potential for revolutionizing construction has been recognized.
From their benefits to some real-world examples of how they’re being used today – let’s dive into the world of PMCs together!
Key takeaways:
- Polymer matrix composites (PMCs) offer high strength-to-weight ratio.
- PMCs have excellent durability and resistance to corrosion.
- They can be molded into various shapes and sizes.
- PMC materials are environmentally friendly and recyclable.
- PMCs have diverse applications in construction, from bridges to buildings.
What Are Polymer Matrix Composites?
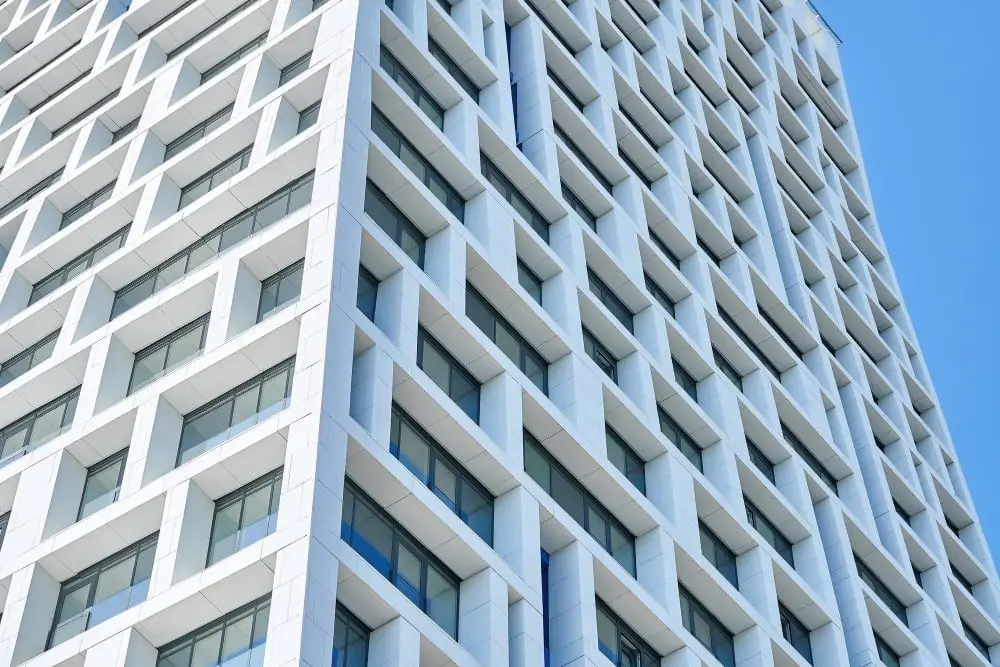
Polymer matrix composites (PMCs) are a type of composite material that consists of two or more components. The first component is the reinforcement, which provides strength and stiffness to the material.
The second component is the matrix, which holds everything together and transfers loads between fibers.
The use of PMCs in construction has been gaining popularity due to their unique properties such as high strength-to-weight ratio, corrosion resistance, durability, and design flexibility. These materials have been used in various applications such as bridges, buildings facades panels for cladding systems.
Types of Polymer Matrix Composites
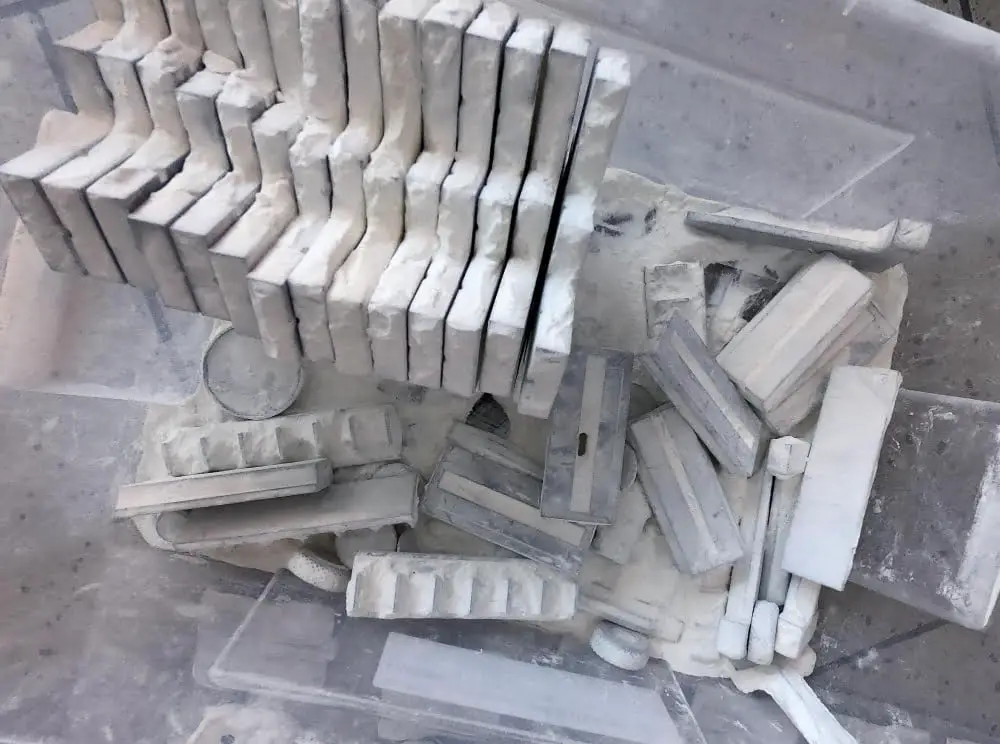
Now that we have a basic understanding of what PMCs are and their potential in construction, let’s take a closer look at the different types of polymer matrix composites available.
There are three main types of PMCs: thermosets, thermoplastics, and elastomers. Thermoset composites are made by combining two or more materials that undergo a chemical reaction when heated to form an irreversible bond.
These materials cannot be melted or reformed once they have been cured.
Thermoplastic composites, on the other hand, can be melted and reshaped multiple times without losing their strength or durability. They’re made from polymers that soften when heated but harden again as they cool down.
Elastomer composites combine the properties of both rubber-like elasticity and plastic-like stiffness to create flexible yet strong materials ideal for applications such as seals or gaskets.
Each type has its own unique set of properties making them suitable for specific applications in construction projects ranging from bridges to buildings. As you can see there is much more than meets the eye with these innovative composite materials.
Manufacturing Techniques
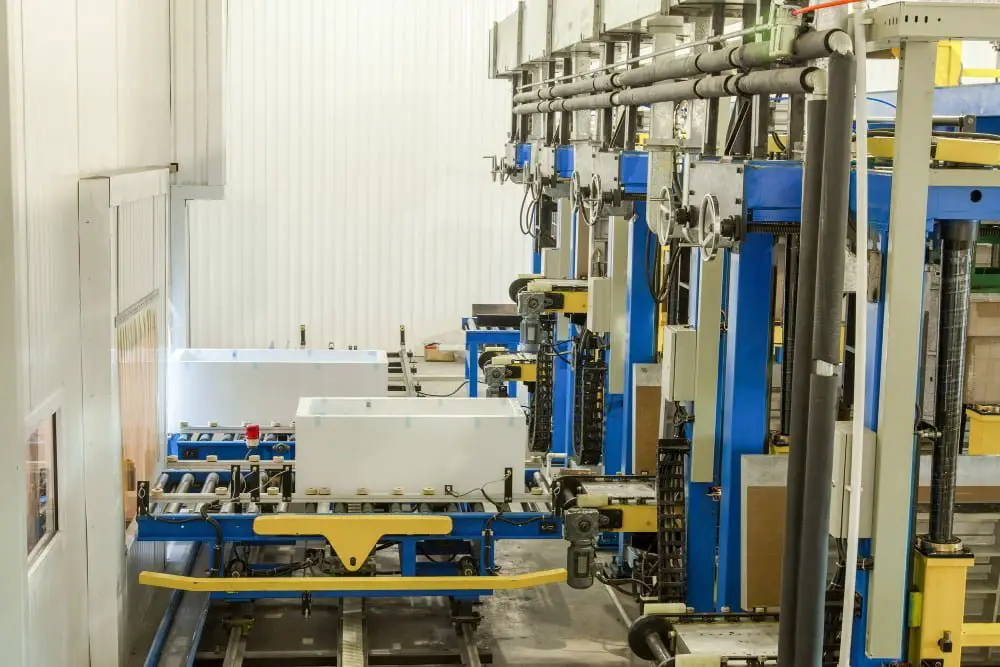
There are several techniques used to create these materials, but the most common ones include hand lay-up, filament winding, and resin transfer molding.
Hand lay-up is a manual process where layers of reinforcing fibers are placed in a mold by hand and then impregnated with resin. This technique is ideal for creating large parts or prototypes.
Filament winding involves wrapping continuous fibers around a rotating mandrel to create cylindrical shapes such as pipes or tanks. The resulting product has excellent strength-to-weight ratios due to its uniform fiber orientation.
Resin transfer molding (RTM) uses two molds – one for the top surface and another for the bottom surface – which sandwich pre-placed reinforcement material before injecting liquid resin under pressure into it. RTM produces high-quality composite parts with complex geometries at relatively low costs compared to other manufacturing methods.
Each technique has its advantages depending on what you want your final product to be like; however, all three require skilled laborers who understand how each step affects overall quality control during production processes.
As construction experts continue exploring new ways of using PMCs in their projects across various industries worldwide – from bridges over waterways connecting cities together more efficiently than ever before – it’s clear that this innovative technology will play an increasingly important role in shaping our future built environment!
Mechanical Properties
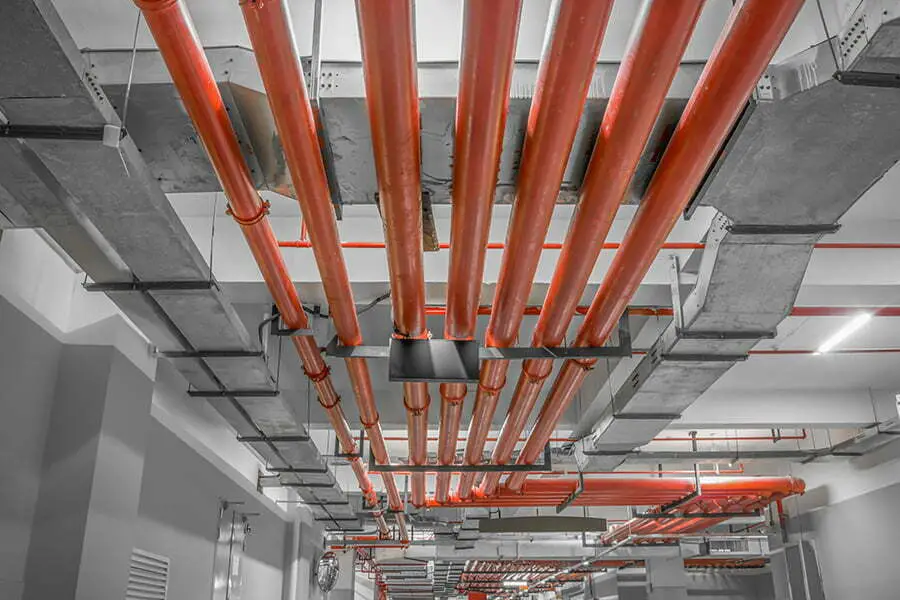
Now that we have a basic understanding of what PMCs are, let’s dive deeper into their mechanical properties. One of the most significant benefits of using PMCs in construction is their high strength-to-weight ratio.
This means that they can be much lighter than traditional materials while still maintaining the same level of strength or even higher.
The reason for this lies in the composition and structure of PMCs. They consist of a polymer matrix (such as epoxy resin) reinforced with fibers (such as carbon, glass, or aramid).
The combination creates a material that is both strong and lightweight.
In addition to their high strength-to-weight ratio, PMC materials also exhibit excellent fatigue resistance and durability over time. They can withstand repeated loading cycles without experiencing any significant damage or degradation.
These mechanical properties make PMC materials ideal for use in various applications within construction – from bridges to buildings to pipelines – where weight reduction and durability are critical factors.
As an expert in the industry who has seen firsthand how these composites perform compared to traditional building materials like concrete or steel, I am excited about what this technology could mean for future projects across all sectors!
Applications in Construction Industry
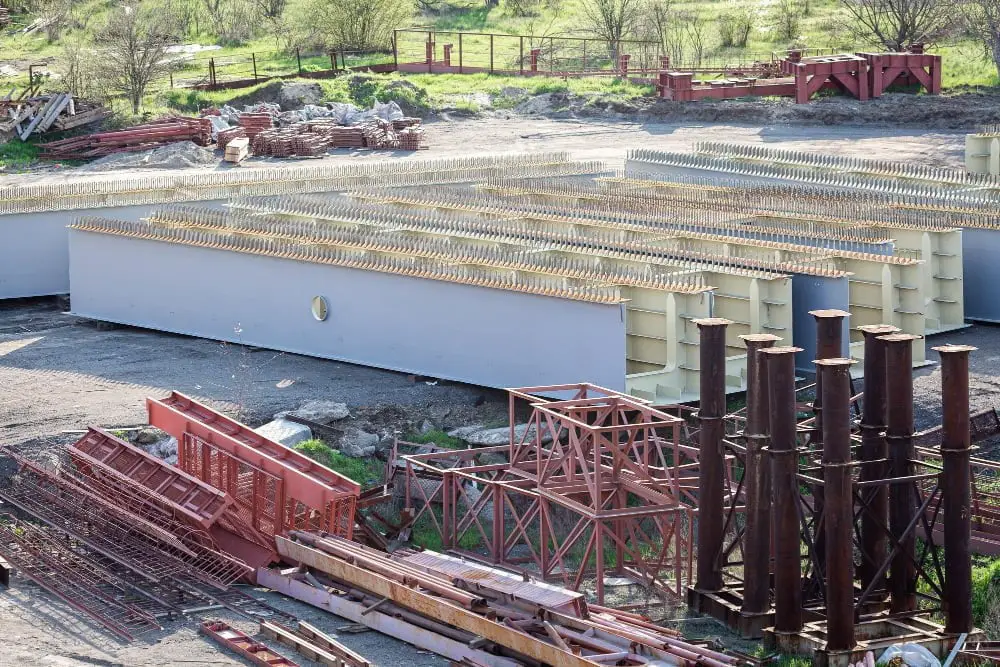
The potential applications of PMCs in the construction industry are vast and varied. From bridges to buildings, these materials have already been used successfully in a range of projects.
One example is the PMC bridge I mentioned earlier. These bridges can be prefabricated off-site and then transported to their final location, reducing construction time and costs significantly.
They’re also more durable than traditional concrete or steel bridges, with a longer lifespan that requires less maintenance.
Another application for PMCs is in building facades. The lightweight nature of these materials makes them ideal for use as cladding systems on high-rise buildings where weight restrictions are an issue.
They offer excellent thermal insulation properties which can help reduce energy consumption within the building.
PMCs have also been used extensively in seismic retrofitting projects – reinforcing existing structures against earthquakes by adding additional support elements made from composite materials such as carbon fiber reinforced polymer (CFRP).
As you can see, there’s no shortage of potential applications for PMCs within the construction industry – from improving durability to reducing costs and increasing efficiency during project delivery timescales.
Advantages and Benefits
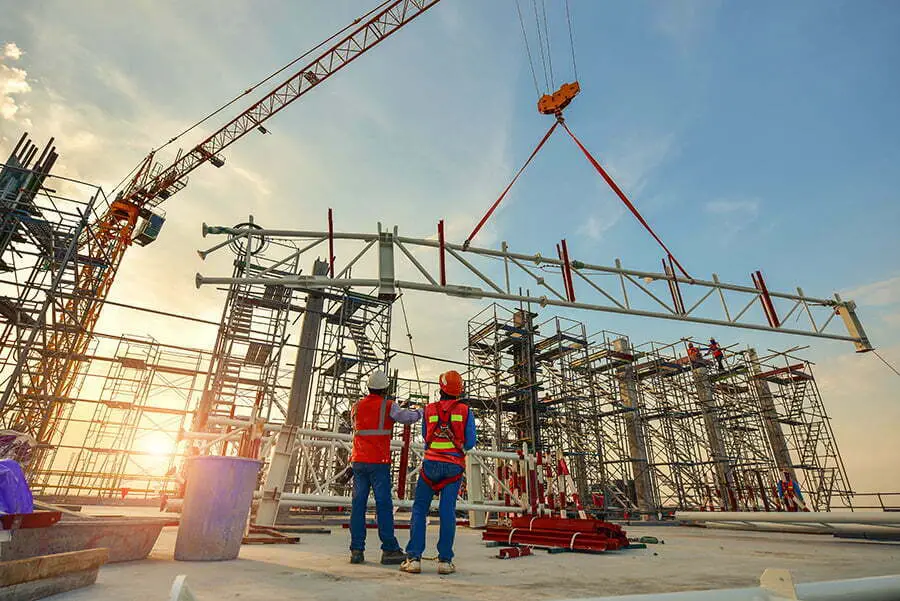
As I mentioned in the introduction, polymer matrix composites (PMCs) have been gaining popularity in construction due to their numerous advantages and benefits. One of the most significant advantages is their strength-to-weight ratio.
PMCs are much lighter than traditional materials like concrete or steel but can be just as strong, if not stronger.
This makes them an ideal choice for applications where weight is a concern, such as bridges or high-rise buildings. PMCs are highly resistant to corrosion and weathering compared to other materials that may deteriorate over time when exposed to harsh environmental conditions.
Another benefit of using PMCs in construction is their versatility. They can be molded into various shapes and sizes depending on the project’s requirements while maintaining structural integrity.
Moreover, since they’re made from plastic-based components rather than metal or wood-based ones used traditionally; they’re more environmentally friendly because they don’t require cutting down trees nor mining metals which could harm ecosystems during extraction processes.
These benefits make PMC an attractive option for architects and engineers looking for innovative solutions that offer both durability and sustainability without compromising on design aesthetics – something we’ll explore further later in this article!
Challenges and Limitations
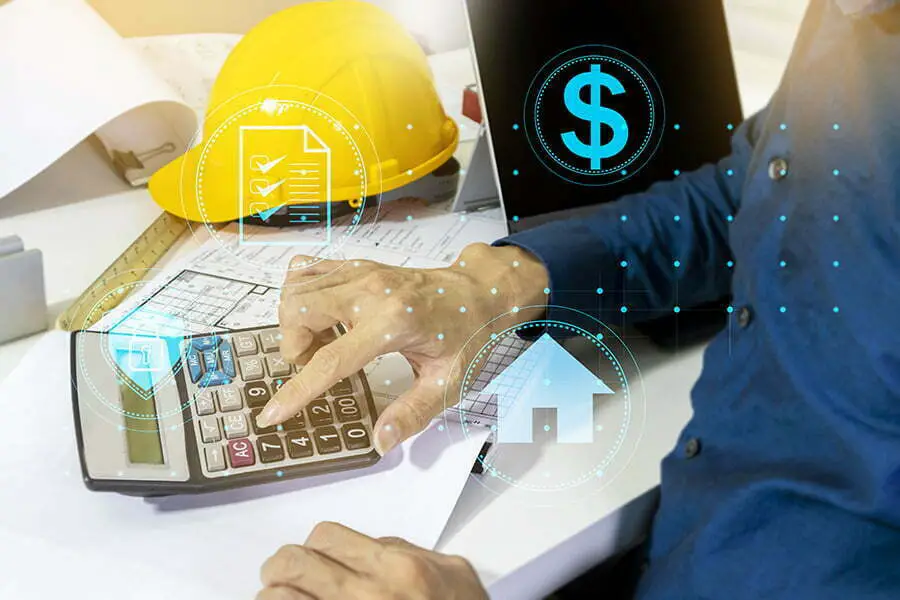
While polymer matrix composites (PMCs) have many benefits, they also come with their own set of challenges and limitations. One of the main challenges is the cost – PMCs can be more expensive than traditional materials such as concrete or steel.
This is because the manufacturing process for PMCs requires specialized equipment and expertise.
Another challenge is that not all types of PMCs are suitable for every application in construction. For example, some may not be able to withstand extreme temperatures or environmental conditions like exposure to UV rays or moisture.
Despite these challenges, researchers and manufacturers are continuously working on improving PMC technology to overcome these limitations. New advancements in material science have led to stronger and more durable composites that can withstand harsher environments while remaining cost-effective.
As a construction expert who has seen firsthand how new technologies can transform an industry, I believe that we will continue seeing exciting developments in PMC applications over time as research continues into making them even better suited for use across various sectors within construction projects around the world!
Case Studies in Construction Projects
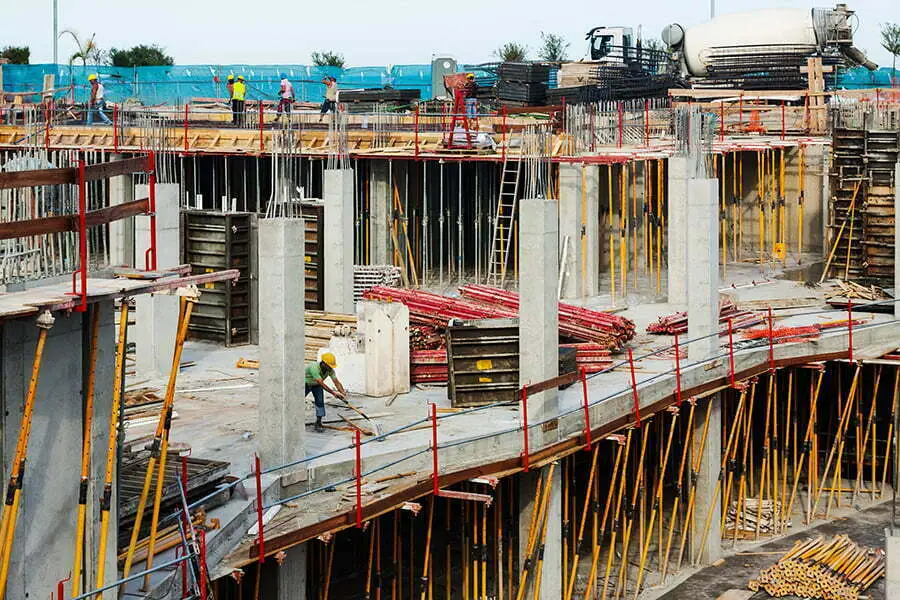
Now that we have a basic understanding of what PMCs are and their benefits, let’s take a closer look at some real-world examples of how they’re being used in construction projects.
One such example is the use of PMC panels for cladding on high-rise buildings. These panels offer superior strength and durability compared to traditional materials like aluminum or steel.
They also provide excellent insulation properties, which can help reduce energy costs for building owners.
Another application is the use of PMCs in bridge construction. As I mentioned earlier, PMC bridges are lighter yet stronger than concrete bridges.
This means they require less maintenance over time while still providing safe passage for vehicles and pedestrians alike.
In addition to these applications, PMCs are also being used in the manufacturing of prefabricated components such as beams and columns. By using pre-made components made from PMCs instead of traditional materials like wood or steel on-site assembly time can be reduced significantly leading to faster project completion times.
Environmental Impact and Sustainability of Polymer Matrix Composites
Polymer matrix composites offer several environmental benefits in the construction industry. Firstly, they are lightweight materials, which means that less energy is required for transportation and installation compared to traditional construction materials like concrete or steel.
This reduces fuel consumption and associated greenhouse gas emissions.
Polymer matrix composites have a longer lifespan than many other materials used in construction. They are highly resistant to corrosion, weathering, and degradation from UV radiation.
As a result, structures made with polymer matrix composites require fewer repairs and replacements over time.
Furthermore, these composites can be recycled at the end of their life cycle. The thermosetting polymers used as matrices can be ground into fine particles or melted down for reuse in new composite products or other applications such as road surfacing material.
Moreover, the manufacturing process of polymer matrix composites typically generates less waste compared to traditional building methods since they can be molded into complex shapes without generating significant offcuts or scrap material.
Maintenance and Lifespan of Polymer Matrix Composites in Construction
Due to their inherent properties, these materials require minimal upkeep compared to traditional construction materials.
One key advantage is their resistance to corrosion and degradation caused by environmental factors such as moisture, chemicals, and UV radiation. Unlike metals that can rust or deteriorate over time, polymer matrix composites are highly resistant to these forms of damage.
This means less frequent repairs or replacements are needed, resulting in cost savings for the project owner.
Polymer matrix composites have excellent durability and strength-to-weight ratios. They can withstand heavy loads without experiencing significant deformation or structural failure over time.
This longevity ensures that structures built with these materials maintain their integrity for extended periods.
Furthermore, the low-maintenance nature of polymer matrix composites reduces the need for regular inspections and interventions by maintenance crews. With fewer requirements for ongoing monitoring and repair work compared to other building materials like steel or concrete, project owners can save both time and money throughout the lifespan of a structure.
“Maintenance” section highlights how polymer matrix composites require minimal upkeep due to their resistance against corrosion/degradation from environmental factors (moisture/chemicals/UV radiation).
Fire Resistance and Safety Measures for Polymer Matrix Composites
These materials have inherent flame-retardant properties, making them less susceptible to catching fire or spreading flames compared to traditional construction materials like wood or steel.
Polymer matrix composites can be engineered with specific additives that enhance their fire-resistant capabilities even further. These additives act as flame retardants by releasing gases when exposed to high temperatures, creating a protective barrier between the composite material and the heat source.
To ensure maximum safety, it is crucial to follow proper installation guidelines for polymer matrix composites. This includes using appropriate fasteners and adhesives specifically designed for these materials.
Regular inspections should be conducted to identify any signs of damage or degradation that could compromise their fire resistance properties.
In case of a fire incident involving polymer matrix composites, it is important to have effective evacuation plans in place along with adequate firefighting equipment suitable for combating fires involving these types of materials.
Innovation and Future Trends in Polymer Matrix Composites
Researchers and engineers are constantly exploring new ways to enhance the properties of PMCs, making them even more versatile and efficient.
One area of focus is improving the strength-to-weight ratio of PMCs. By incorporating advanced reinforcement materials such as carbon nanotubes or graphene into the polymer matrix, researchers aim to create composites that are lighter yet stronger than ever before.
This could lead to structures with reduced material usage while maintaining structural integrity.
Another exciting trend is the development of self-healing PMCs. These innovative materials have embedded microcapsules filled with healing agents that can repair small cracks or damage autonomously when triggered by external stimuli like heat or moisture.
Self-healing capabilities could significantly extend the lifespan and durability of PMC-based constructions.
There is a growing interest in sustainable alternatives for traditional petroleum-based polymers used in composite matrices. Biodegradable polymers derived from renewable resources like plant fibers or recycled plastics show promise as eco-friendly options without compromising performance characteristics.
Furthermore, advancements are being made towards integrating smart technologies into PMC applications within construction projects. For instance, embedding sensors within composite structures can provide real-time data on stress levels, temperature changes, or structural deformations – enabling proactive maintenance measures before any significant issues arise.
Comparison of Polymer Matrix Composites With Traditional Construction Materials
One key advantage is their superior strength-to-weight ratio. Compared to materials like steel or concrete, polymer matrix composites are significantly lighter while still maintaining high strength and durability.
Another benefit of polymer matrix composites is their resistance to corrosion and chemical degradation. Traditional materials such as steel can be prone to rusting or deteriorating when exposed to harsh environments, whereas polymer matrix composites have excellent resistance against these factors.
The flexibility of design with polymer matrix composites allows for greater freedom in creating complex shapes and structures that may not be feasible with traditional materials. This versatility opens up new possibilities for architects and engineers in terms of aesthetics and functionality.
Furthermore, the manufacturing process for polymer matrix composites often requires less energy compared to producing traditional construction materials like steel or concrete. This reduced energy consumption contributes positively towards sustainability efforts by reducing carbon emissions during production.
It’s important to note that while there are numerous benefits associated with using polymer matrix composites in construction, each material has its own set of strengths and weaknesses depending on specific project requirements. Therefore, it’s crucial for designers and builders to carefully evaluate which material best suits their needs before making a decision.
FAQ
What are the two types of polymer matrix materials?
The two main types of polymer matrix materials are thermoplastics and thermosetting resins.
What is the most common polymer matrix composite?
The most common polymer matrix composite is the Glass Fiber Reinforced Plastic (GFRP) Composites.
What is the role of matrix in polymer composites?
The matrix in polymer composites binds the fiber reinforcement, transfers loads between fibers, defines the overall shape of the composite, and determines the surface quality.
How does the polymer’s molecular structure affect its properties in construction?
The molecular structure of a polymer influences its properties in construction by determining its durability, flexibility, heat resistance, and chemical stability.
What are the environmental implications of using polymer composites in construction?
The environmental implications of using polymer composites in construction include the reduction of waste through efficient usage and recycling, but also potential harm due to non-biodegradability and release of toxic substances during production or if improperly disposed.
How can polymer matrix composites improve the durability of construction materials?
Polymer matrix composites enhance the durability of construction materials by providing superior resistance to corrosion, high thermal stability, increased tensile strength, and enhanced moisture barrier properties.
Recap