This article will explain what polymer composites are and their versatile roles in the construction industry.
Key takeaways:
- Polymer composites combine polymers with reinforcements for enhanced performance.
- Different types of polymer composites have unique properties and applications.
- Polymer composites are used in aerospace, construction, and automotive industries.
- Factors like polymer type, reinforcement materials, and fabrication process affect properties.
- The preparation of polymer composites involves careful selection and manufacturing processes.
Polymer Composites Definition
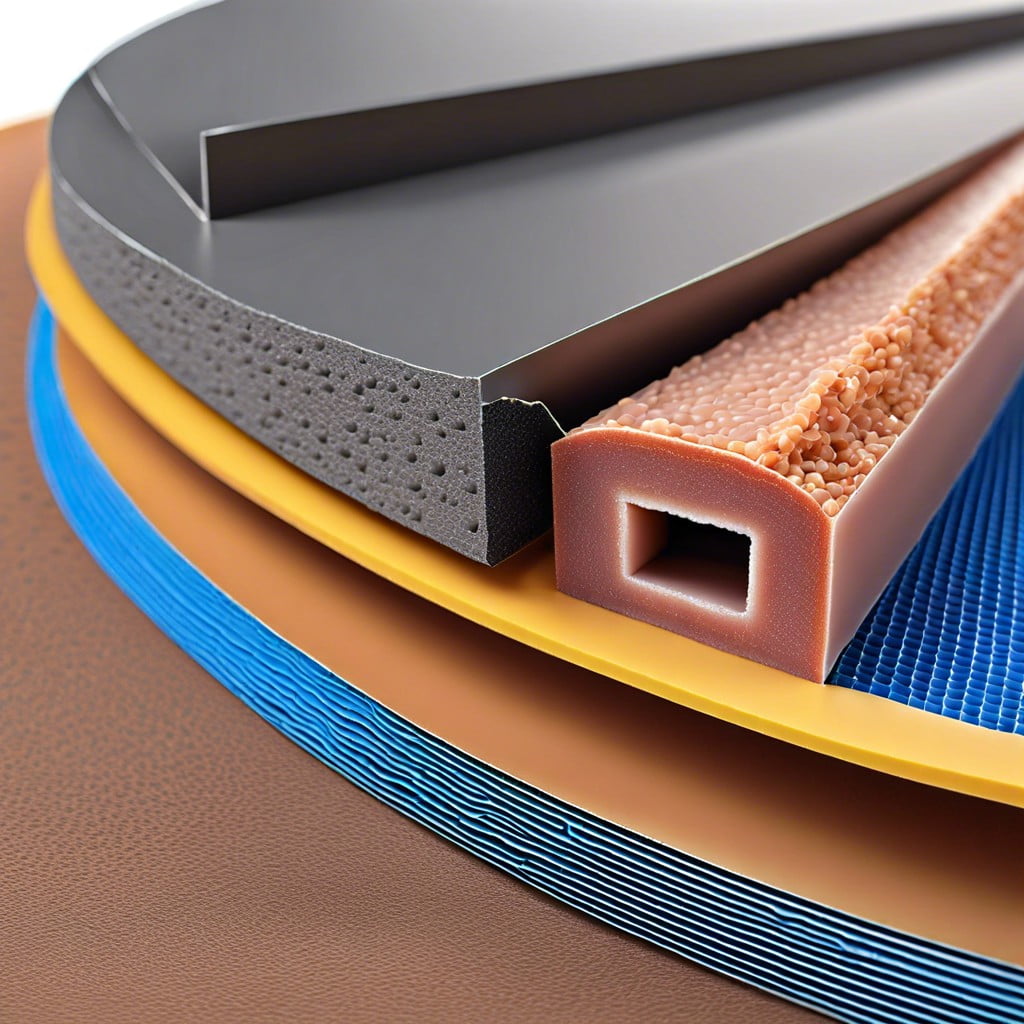
Polymer composites are materials made by combining polymers with other substances to enhance their performance. The polymer, serving as the matrix, binds together reinforcements such as fibers or particles. This union takes advantage of each component: the polymer’s flexibility and the reinforcement’s strength.
Think of the polymer matrix as a binder, like the cement in concrete, which holds together the stronger aggregates (gravel and sand). The reinforcements, often made from glass, carbon, or aramid fibers, give the composite its structural integrity, much like the steel rebar in reinforced concrete.
These composites can be tailored for specific uses by adjusting their composition. The result is a versatile material that can be engineered to be lightweight, yet exceedingly strong, corrosion-resistant, and able to withstand extreme temperatures or pressures.
Properties and Classification of Polymer Composites
Polymer composites combine polymers with reinforcing fibers or particles, resulting in materials with properties that can surpass those of their individual constituents. These composites are light yet strong, and their versatility allows them to be tailored for specific uses.
Depending on the matrix and reinforcement materials used, polymer composites can be mainly divided into two groups: thermosetting and thermoplastic composites. Thermosetting composites, once hardened, cannot be reshaped with heat, making them suitable for high-temperature applications. On the other hand, thermoplastic composites can be reheated and reshaped, offering convenience in processing and recycling.
The reinforcements in these composites are commonly made from fiberglass, carbon, or aramid fibers, each contributing unique strengths and weaknesses to the composite material. For example, fiberglass is cost-effective and versatile, carbon fibers offer high stiffness and strength for weight, and aramid fibers are known for their resistance to impact.
Key properties like tensile strength, flexibility, and thermal stability are influenced by factors including the type of polymer, the nature and orientation of the reinforcement, and the quality of the bond between them. By adjusting these parameters, engineers can create polymer composites for a multitude of construction needs, from insulating materials to load-bearing components.
Applications of Polymer Matrix Composites (P.M.C.’s) and Metal Matrix Composites (M.M.C.’s)
Polymer matrix composites, consisting of a polymer resin reinforced with fibers like glass or carbon, are celebrated for their strength-to-weight ratio. This property makes them ideal for aerospace applications, where reducing weight is crucial for fuel efficiency and performance. Aircraft components, including wings and fuselage sections, often utilize these lightweight yet robust materials.
In the construction industry, polymer matrix composites are used for bridge reinforcements and repair, being both durable and resistant to environmental degradation. They also feature in the manufacturing of wind turbine blades due to their flexibility and fatigue resistance, which allows for the absorption of wind energy without material compromise.
Transitioning to metal matrix composites, these incorporate a metal like aluminum or titanium with reinforcing fibers. They shine in automotive engineering, with applications ranging from brake rotors to engine components. Their high thermal conductivity and wear resistance improve vehicle performance and longevity.
Additionally, in the arena of sports equipment, the integration of metal matrix composites has improved the durability and precision of items like golf clubs and bicycles, offering both professional athletes and enthusiasts tools that enhance their performance through superior materials engineered to endure and excel.
Factors Affecting Properties of Polymer Composites
Several factors can influence the properties of polymer composites, steering their performance and suitability for construction applications:
– **Type of Polymer**: The kind of polymer used as a matrix material—be it thermoset, like epoxy or polyester, or thermoplastic, like polyethylene—dictates the composite’s overall characteristics, such as elasticity, strength, and temperature resistance.
– **Reinforcement Materials**: The nature of the reinforcing fibers—glass, carbon, or aramid—and their properties heavily affect the tensile strength, stiffness, and weight of the composite.
– **Fabrication Process**: The way a composite is manufactured—hand lay-up, pultrusion, or resin transfer molding—can result in varied degrees of fiber alignment, porosity, and resin distribution, which in turn impact the mechanical and physical properties of the final product.
– **Fiber-Matrix Interface**: The bond strength between the fibers and the matrix is pivotal. Proper adhesion ensures effective stress transfer, enhancing the composite’s structural integrity.
– **Environmental Conditions**: Exposure to UV light, moisture, chemicals, and temperature variations can degrade polymers, alter the composite’s dimensions, reduce mechanical strength, or induce chemical resistance changes.
By manipulating these factors, engineers can tailor polymer composites to meet specific requirements of construction projects, ensuring the materials’ performance aligns with the demands of the application.
Method of Preparation and Product Research and Development
Creating polymer composites involves a systematic and sophisticated process, starting from the selection of the base materials to the final production phase. Here are the key points to understand about this process:
Composite preparation begins with choosing the right polymer resin and reinforcing materials. The type of resin—be it epoxy, polyester, or polyamide—depends on the desired end properties of the composite, such as strength, flexibility, or resistance to heat and chemicals.
Reinforcing fibers like glass, carbon, or aramid are selected based on the necessary structural characteristics. These fibers provide the composite with higher tensile strength and rigidity.
The manufacturing process can vary greatly. Techniques such as hand lay-up are used for simpler, low-volume items. For complex shapes or high-volume production, methods like injection molding, compression molding, or pultrusion are employed.
The curing stage is crucial, where the composite material solidifies into its final form. Conditions such as temperature and pressure are carefully controlled to achieve the best material performance.
In parallel, product research and development is an ongoing process. It focuses on improving existing composites and inventing new ones to meet evolving industry demands. This entails extensive testing for durability, environmental resistance, and compliance with safety standards.
Advancements in technology and material science continuously influence the development of stronger, lighter, and more versatile composites that propel the construction industry forward. Through a blend of innovation and engineering, the latest discoveries are turned into practical solutions that address a wide range of construction challenges.
Recap