Exploring the possibilities, this article delves into whether Teflon, a widely used polymer, can be effectively utilized in the injection molding process.
Teflon, technically known as Polytetrafluoroethylene (PTFE), is indeed capable of being injection molded, but it’s not a straightforward process. This is because PTFE has a high melting point and is chemically resistant, which makes it challenging to mold. However, with the right equipment and expertise, it can be done successfully.
In this article, we will delve into the specifics of injection molding Teflon, discussing the process, the challenges, and the solutions in detail. So, if you’re looking to understand the complexities and nuances of injection molding Teflon, you’re in the right place.
Key takeaways:
- Teflon, also known as PTFE, can be injection molded
- Challenges include high melt viscosity, shrinkage, and sintering requirements
- The benefits of injection molding Teflon include non-stick properties, resistance to high temperatures and chemicals, and good electrical insulation properties
- Challenges in injection molding Teflon include non-stick property, high melting point, thermal degradation, and unexpected shrinkage
- Solutions include precise temperature control, specialized molds, appropriate process parameters, and regular maintenance checks.
Teflon and Injection Molding: An Overview
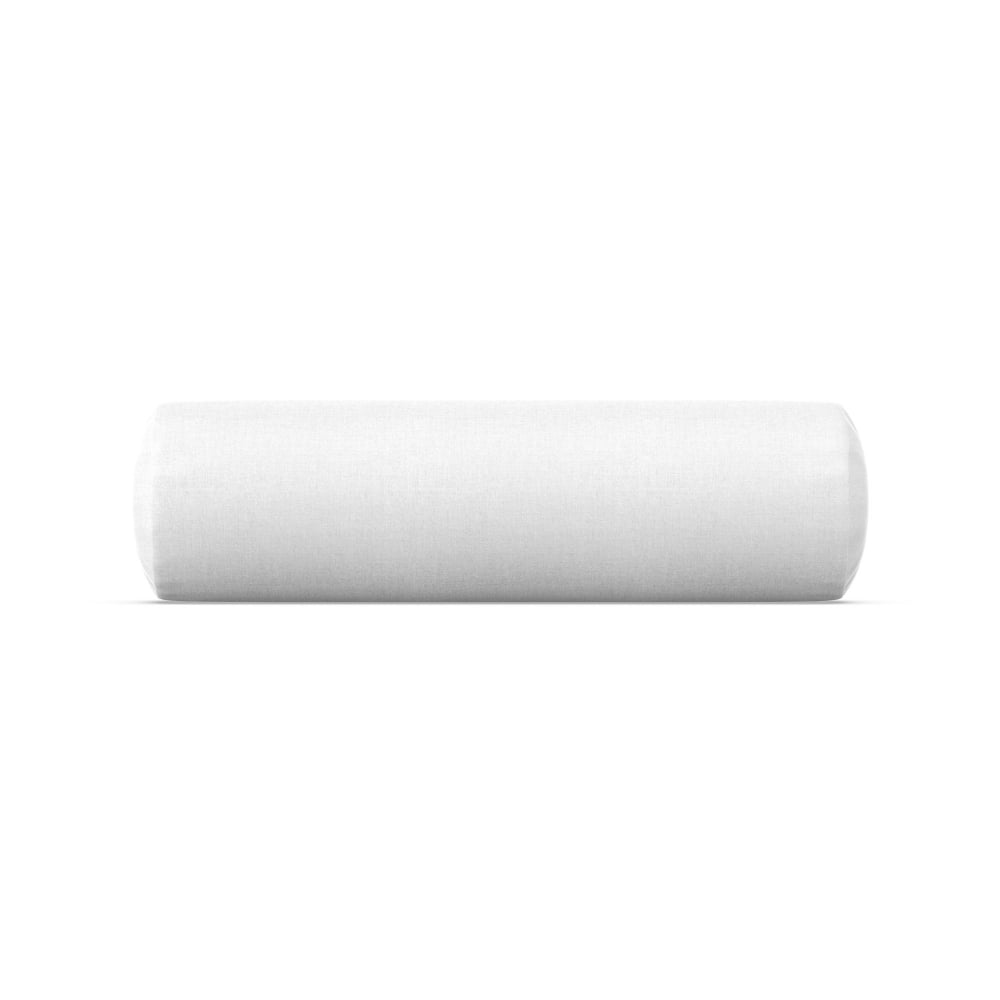
Teflon, also known as Polytetrafluoroethylene (PTFE), holds a unique set of properties that make it a high-demand polymer in various industries. Recognized for its non-stick feature, it is also highly resistant to extreme temperatures and aggressive chemicals. Moreover, its exceptional electrical properties make it a sought-after insulator.
Injection molding, in contrast, is a popular fabrication method known for its efficiency in manufacturing parts. The process entails injecting molten material, often a type of plastic, into a mold, then cooling it to create a solid object. This method is known for its precision, rapid production capabilities, and cost-effectiveness.
- Teflon or PTFE is a widely used polymer because of its unique properties like resistance to extreme temperatures, adverse chemicals, and its capability as an excellent insulator.
- Injection molding is a manufacturing method that is efficient and cost-effective, involving the creation of objects by injecting molten material, usually plastic, into a mould and then cooling it.
The confluence of Teflon’s advantageous properties and injection molding’s effectiveness spurs inquiry into the possibility and implications of Teflon injection molding.
Understanding the Properties of Teflon
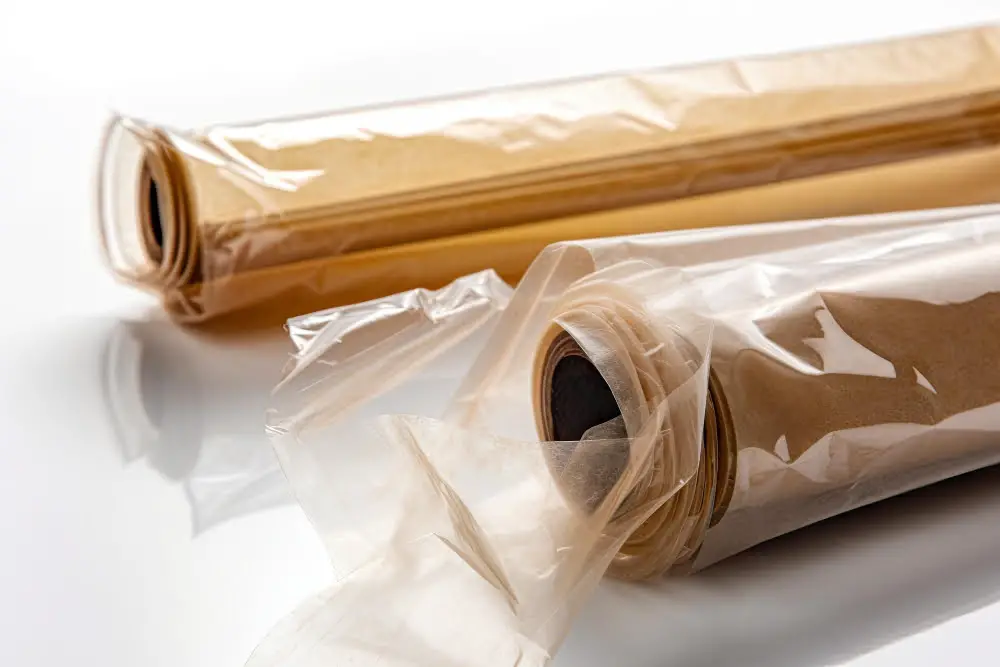
Teflon, a brand name for Polytetrafluoroethylene (PTFE), is a high-performance plastic known for its specific features. Exceptional heat resistance makes it capable of functioning in temperatures as high as 260°C and as low as -270°C. It boasts a high chemical resistance, essentially unaffected by nearly all chemicals, even under protracted exposure.
Teflon also exhibits low surface friction and is credited for its excellent non-stick properties, being highly hydrophobic, meaning it repels water. It possesses high electrical insulative properties, further broadening its appeal across different industries. Its natural white color is non-fading and UV-resistant, which can be beneficial in certain applications.
Notably, Teflon has a high melt viscosity and does not flow easily, which can complicate certain manufacturing processes, like injection molding. It’s crucial to keep this in mind when planning its potential use in construction projects.
Understanding the Injection Molding Process
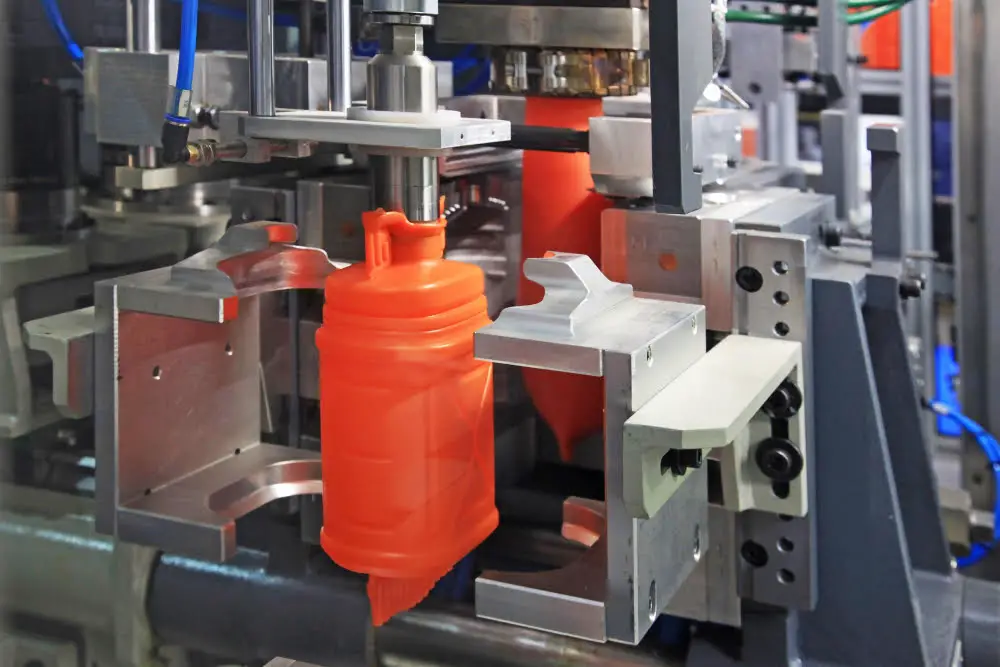
Injection molding is a widely employed manufacturing process that creates items by injecting molten materials into a mold. The basic process involves several key stages:
- Initial design and creation of a mold: This mold, often made of steel or aluminum, is custom designed and constructed to form the final polymer product.
- Preparing the polymer: The chosen polymer — in this case, we’re discussing Teflon — is prepared in pellet form.
- Heating and melting the polymer: The polymer pellets are funneled into a heated barrel, where they are melted into a liquid form.
- Injecting the molten polymer: This heated liquid is then injected at high pressure into the mold.
- Cooling and solidifying: The mold is cooled down, allowing the polymer inside to solidify into the desired shape.
- Ejecting the final product: Once the polymer has solidified, the final product is ejected from the mold, completing the process.
Understanding these steps provides the foundation for discussing the feasibility and specific considerations of injection molding Teflon.
Can Teflon Be Injection Molded?
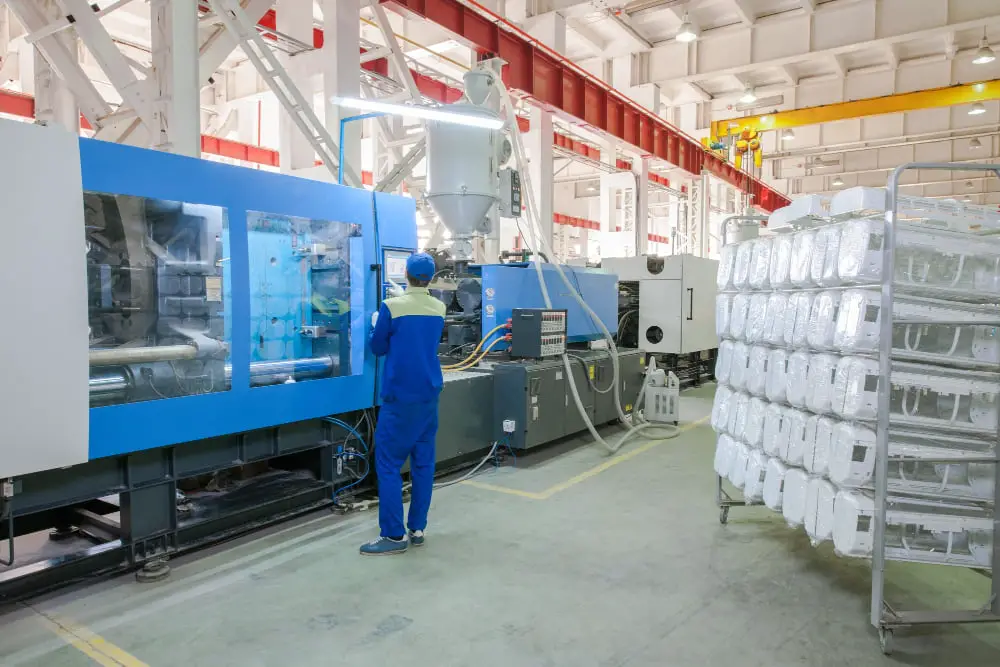
Yes, Teflon, also known as Polytetrafluoroethylene (PTFE), can indeed be injection molded, but it’s not a straightforward process. Related materials like fluoroelastomers or fluorothermoplastics are easier to mold but let’s focus on genuine Teflon for now.
When molded, Teflon can deliver parts with remarkable properties: heat resistance up to 260°C, impressive chemical resistance, excellent electrical insulation and a low coefficient of friction.
However, there are challenges due to key characteristics of Teflon:
- Melt viscosity: Teflon has a high melt viscosity. This means it requires a specialized injection molding machine to handle this high viscosity at high temperatures.
- Shrinkage: Just like other materials, Teflon shrinks as it cools, but it does so at an unpredictable rate. Therefore, precision can be a concern.
- Sintering requirement: After molding, Teflon parts must go through a sintering process. This involves further heating in a controlled-environment oven to further bond the material.
Plenty of expertise and specialized equipment are required to effectively mold Teflon, but it’s not impossible. Costs can be a factor though, usually higher than molding standard thermoplastics.
In concluding, Teflon’s impressive properties when injection molded must be weighed against the technical challenges and higher costs involved.
Benefits of Injection Molding Teflon
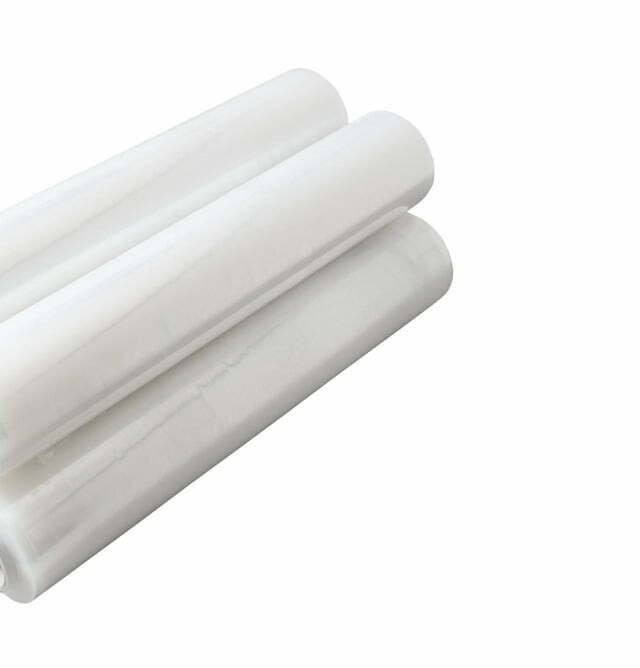
Teflon, owing to its unique characteristics, offers several advantages when it comes to injection molding.
Firstly, it has an exceptional non-stick property, thus reducing the chance of the material sticking to mold cavities, increasing efficiency and reducing downtime for cleaning.
Secondly, Teflon exhibits excellent resistance to high temperatures and chemicals, ensuring durability of the mold and making it suitable for demanding applications.
Thirdly, components made from Teflon are known to have good electrical insulation properties and low friction coefficient, which provides additional design flexibility for various industrial applications.
Lastly, Teflon also offers an excellent surface finish to the components, reducing the need for further finishing processes, and ultimately leading to cost savings.
Notwithstanding these compelling advantages, injection molding of Teflon does pose some challenges, such as its high processing temperature and inconsistencies, which we’ll discuss in the following sections.
Challenges in Injection Molding Teflon
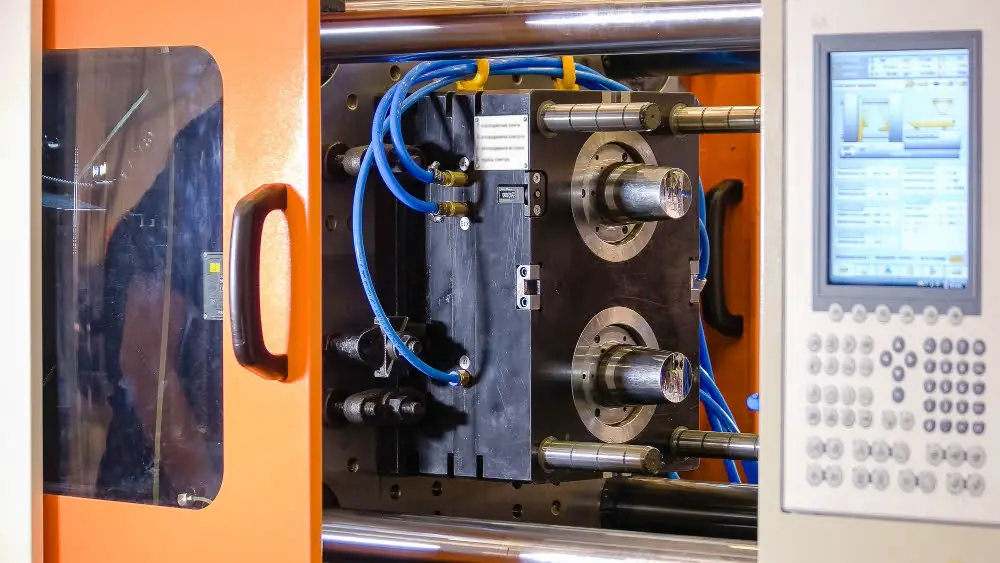
Teflon, despite its numerous advantages, presents a unique set of challenges for injection molding owing to its distinct properties.
Teflon’s inherent non-stick property, the same quality that makes it popular in cookware, complicates the molding process. It is resistant to the sticking necessary for the mold to effectively shape it.
The high melting point of Teflon, ranging from 260 to 327 degrees Celsius, can cause difficulties. Standard injection molding equipment may not reach these temperatures or maintain them consistently, risking incomplete or flawed molding.
Its sensitivity to thermal degradation is another issue. If the temperature remains too high for an extended time, Teflon can decompose, producing harmful fumes and affecting product quality.
Lastly, unexpected shrinkage during the cooling stage may alter final product dimensions. Variations might render a final component useless if precise specifications are not met.
Solving these challenges requires specialized equipment or additives to modify Teflon’s properties. This increases the complexity and cost of Teflon injection molding, a factor that needs careful consideration in its application.
Exploring Solutions for Effective Teflon Injection Molding
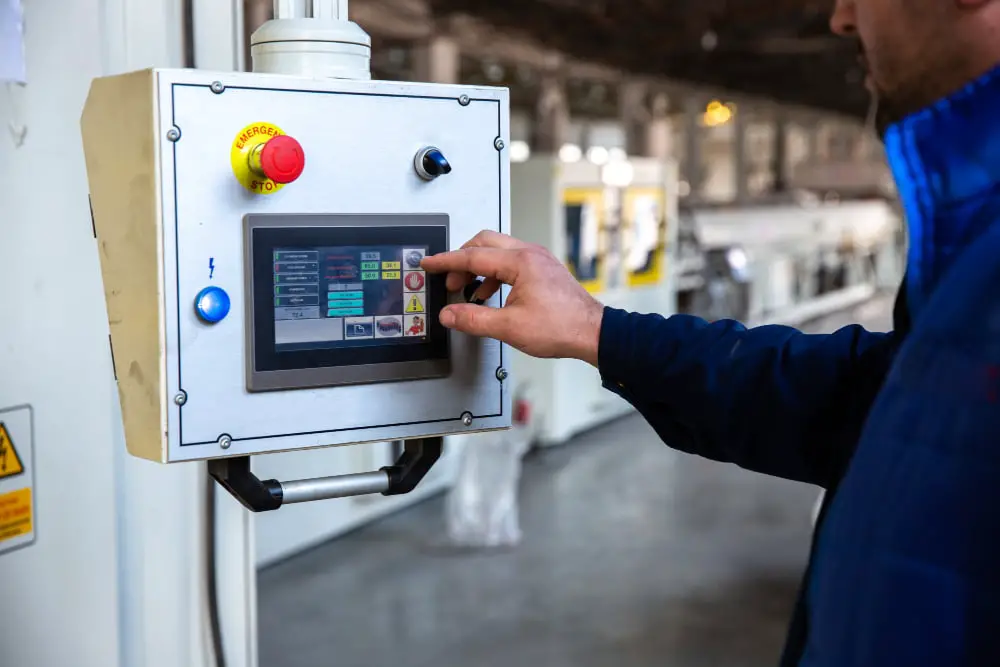
In order to realize effective Teflon injection molding, certain measures can be undertaken.
Adherence to precise temperature control is paramount since Teflon requires higher temperatures, often between 660 to 930 degrees Fahrenheit. This is necessary to ensure the polymer achieves a molten state suitable for injection molding.
Opting for specialized molds designed with materials that can withstand Teflon’s high-temperature requirements is essential. Tools like chromium and steel alloy molds are robust and can tolerate these extreme conditions, ensuring longevity and consistent results.
The use of appropriate process parameters, like high injection speed and pressure, is crucial. It helps in adequately filling the mold and ensuring the Teflon achieves desired shapes with accurate details.
Preventing degradation is important as well. When exposed to excessive heat for prolonged periods, Teflon can degrade, causing off-gassing. This can be avoided by minimizing its exposure to high heat for extended periods.
Finally, conducting regular maintenance checks, timely machine optimizations, and process audits of the injection molding machinery helps maintain consistency of results. These practices ensure the equipment is at peak performance and able to handle Teflon’s unique molding process.
FAQ
Can you injection Mould Teflon?
Yes, Teflon™ thermoplastics can indeed be used for injection molding.
What metals can be injection molded?
Metals that can be injection molded include ferrous alloys such as steels, stainless steels, tool steels, iron-nickel magnetic alloys, and specialty ferrous alloys like Invar and Kovar.
What plastics can you injection mold?
The most common plastics that can be injection molded are acrylic (PMMA), acrylonitrile butadiene styrene (ABS), and nylon (polyamide, PA).
Can threads be injection molded?
Yes, threads can be injection molded, although this may result in small parting lines on the threads.
How does the injection molding process of Teflon differ from other polymers?
The injection molding process of Teflon differs from other polymers due to its high melting point, necessitating special molds and machinery for shaping.
What are the advantages of injection molding Teflon in contrast to other plastics?
Injection molding Teflon provides exceptional heat resistance, reduced friction, and excellent electrical insulation properties, exceeding the capabilities of many other plastics.
Can recycled Teflon be used in injection molding processes?
No, recycled Teflon cannot be used in injection molding processes due to its resistance to flow when melted.
Recap