Discover the best types of lubricants to enhance the efficiency and quality of your plastic extrusion processes.
When it comes to plastic extrusion, the correct choice of lubricant is crucial for optimal performance and longevity of your machinery. Silicone-based lubricants are often the go-to choice due to their compatibility with various types of plastics, their high-temperature resistance, and their ability to reduce friction effectively.
However, the specific choice depends on factors such as the type of plastic being extruded, the temperature of operation, and the design of the extrusion machine. This article will delve into these considerations, providing detailed guidance on selecting the best lubricant for your specific plastic extrusion needs.
Key takeaways:
- Lubricants must provide friction reduction and heat stability.
- They should have adequate viscosity and perform well under pressure.
- Lubricants need to be compatible with the plastic material.
- Silicone-based lubricants are often a good choice for plastic extrusion.
- Proper lubricant selection improves efficiency and product quality.
Desired Properties of Lubricants
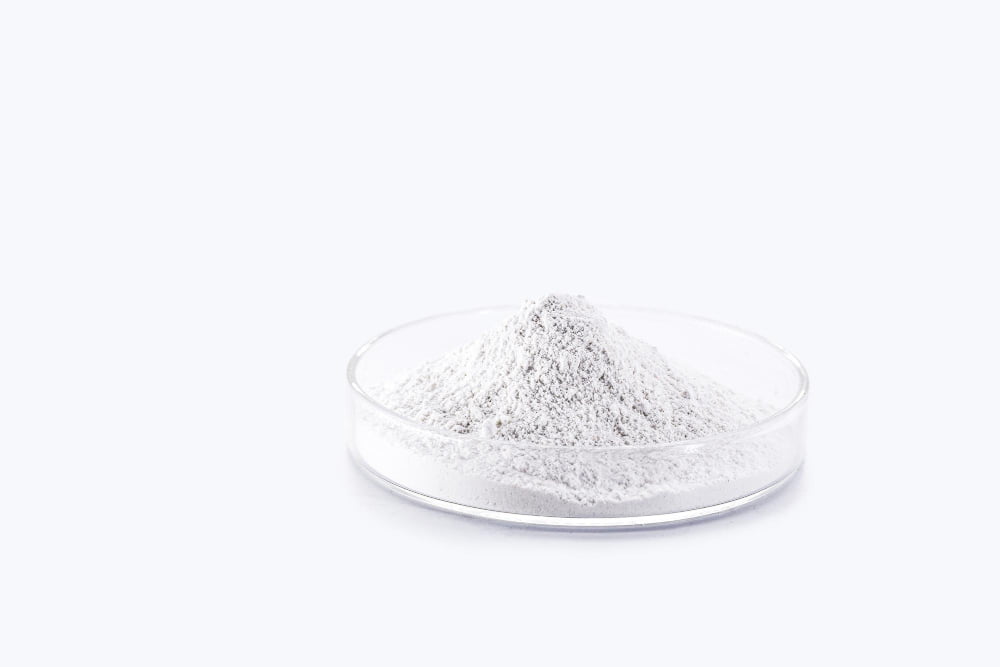
In order for lubricants to perform proficiently within a plastic extrusion system, they need to have certain essential properties.
Primarily, lubricants must provide the necessary friction reduction, acting as a buffer between equipment’s metal surfaces and the polymers. This property curbs wear and tear on machinery, extending equipment’s longevity.
They need exceptional heat stability, given the high temperatures encountered during the extrusion process. They should resist degrading or oxidizing to prevent causing harm to the polymers or extrusion equipment.
Lubricants have to possess an adequate viscosity, the ability to flow under different conditions. It should be neither too thin, risking inadequate lubrication, nor too thick, causing sluggish machine performance.
They should perform well under high pressure, crucial due to the extreme forces applied during the plastic extrusion process. Lubricants should maintain their anti-friction characteristics in these circumstances to prevent equipment damage.
Compatibility with the plastic material is central. Lubricants should not react adversely to the polymers in use, maintaining the integrity of the finished product.
Lastly, they should be easily extractable or washable post-process. Any residual lubricant on the finished product or in the machinery can disrupt the quality or slow down machine productivity.
Lubrication Theory
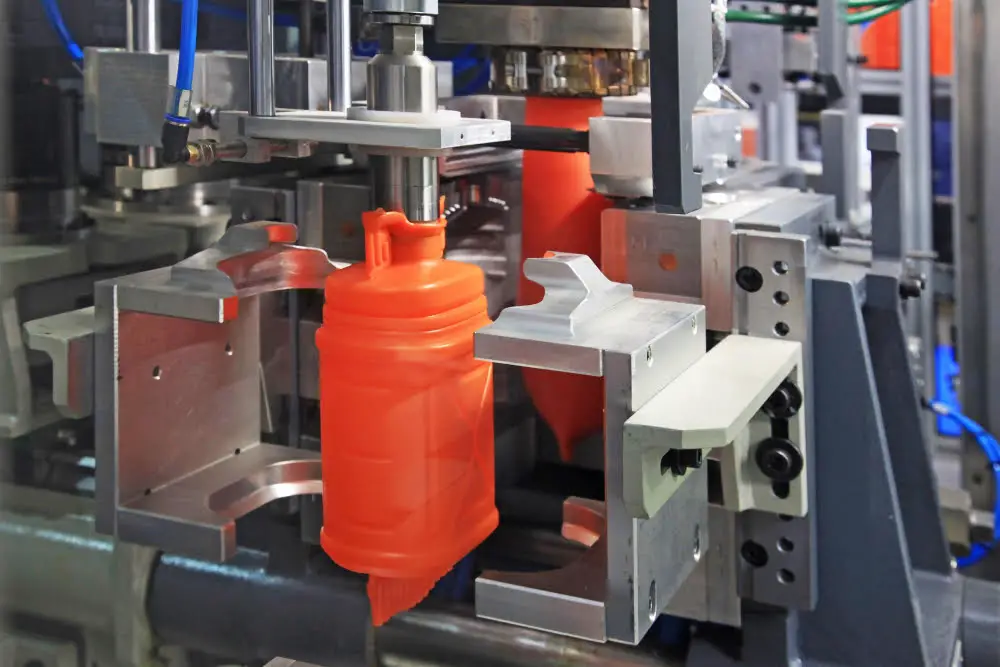
In the realm of plastics processing, particularly extrusion, lubrication plays a critical role. Its primary function happens on two levels – internal and external.
Internal lubrication targets reducing friction between polymer particles. As a result, it limits mechanical heat generation during extrusion while still maintaining the necessary viscosity of the molten plastic for shaping.
External lubrication, on the other hand, minimizes adhesion between the polymer melt and the metal surface of the extruder. This action minimizes friction, mitigates surface damage, and supports a smooth, uninterrupted flow of the plastic material.
Both internal and external lubrication require a careful choice of lubricants, balancing the need to prevent overheating, increase production speed and improve the final product’s quality.
Some essential considerations include:
- Compatibility with polymer: Lubricants need to be chemically compatible with the specific polymer in use.
- Influence on product quality: Lubricants should not negatively impact the physical properties or aesthetics of the final product.
- Process impact: Lubricants should assist in easing the extrusion process, reducing wear and tear on machinery.
Selecting the right lubricant for plastic extrusion is a critical component to ensure a smooth, efficient process and high-quality end products.
Major Lubricants Types
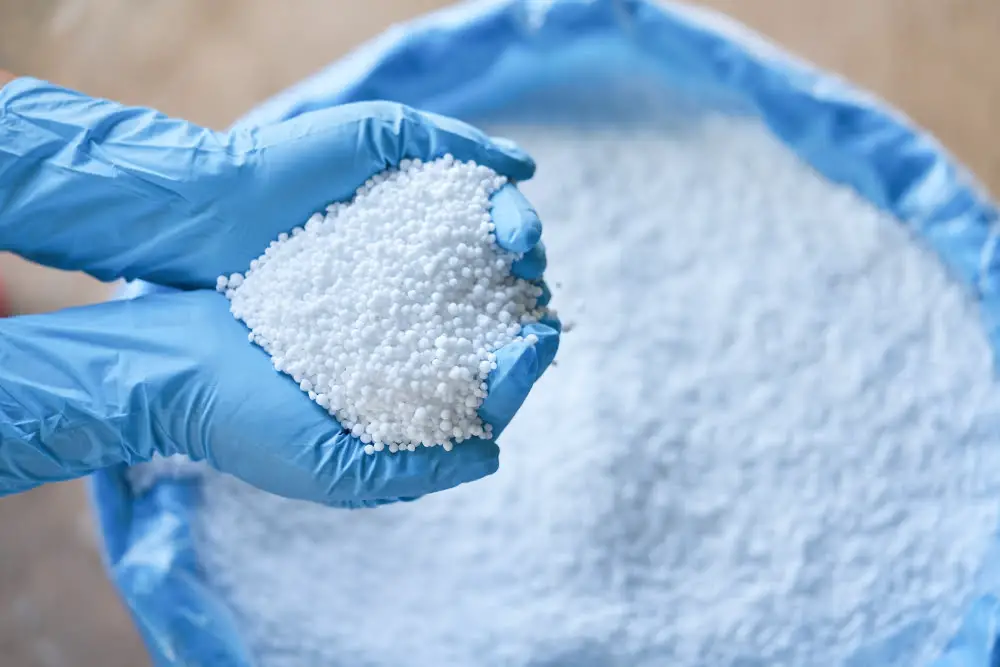
There are three fundamental types of lubricants used in the plastic extrusion process.
External lubricants primarily affect the polymer/metal interface. They promote the plastic’s flow, decrease the sticking of the material to the metal surfaces, and offer a glossier finish to the product. Stearates and polyethylene waxes are common examples of external lubricants.
Internal lubricants, on the other hand, affect the polymer/polymer interface. They decrease friction during the extrusion process by reducing the polymer’s viscosity, allowing for easier mold filling and speeding up the process. Examples of these include fatty amides and esters.
Finally, we have combination lubricants. True to their name, these lubricants deliver both the functions of internal and external lubricants. They can reduce friction at both the polymer/metal and polymer/polymer interfaces, boosting the overall efficiency of the extrusion process. They are usually available in wax-based formulations.
In the plastic extrusion process, these lubricants are not used in isolation. Either a combination of various external and internal lubricants or combination lubricants are used to achieve the desired results. To this end, understanding the specific requirements of the extrusion process and the compatibility of the lubricant with the plastic type can be very beneficial.
The selection of the lubricant is hence a highly application-specific task. One should not shy away from conducting feasibility tests or seeking professional help for making the right choice.
Factors Influencing Lubricants Selection

Several elements come into play when deciding on the optimal lubricant for your plastic extrusion process.
First and foremost, the type of polymer that is being extruded. Each variety – from PVC to polyethylene – has unique characteristics that can be enhanced or impeded by different lubricating products.
The processing temperature of the polymer, which may influence the thermal stability requirements of the lubricant, is a critical element to consider. Your lubricant needs to operate effectively under these conditions without degrading or causing problems.
The expected output speed of the extruder also impacts lubricant selection. Certain lubricants are more efficient at high speeds, reducing heat and friction while preserving the quality of the finished product.
The hardware in use is another important consideration. Certain lubricant types may be incompatible with specific machine components, potentially leading to equipment damage or product quality issues.
Finally, the desired finish of the final product is a deciding factor in lubricant choice. Certain lubricants can affect the product’s shininess, color, texture, and other surface characteristics. It’s crucial to select a lubricant that meets the desired aesthetic and performance standards.
In conclusion, choosing a lubricant for plastic extrusion is not a one-size-fits-all process. It requires careful consideration of numerous factors to ensure optimal performance, aesthetic quality, and cost-effectiveness.
Remember, a good understanding of your materials, machinery, and desired outcomes will guide you in selecting the best lubricant for your application.
Lubricants Selection Criteria for Polymers
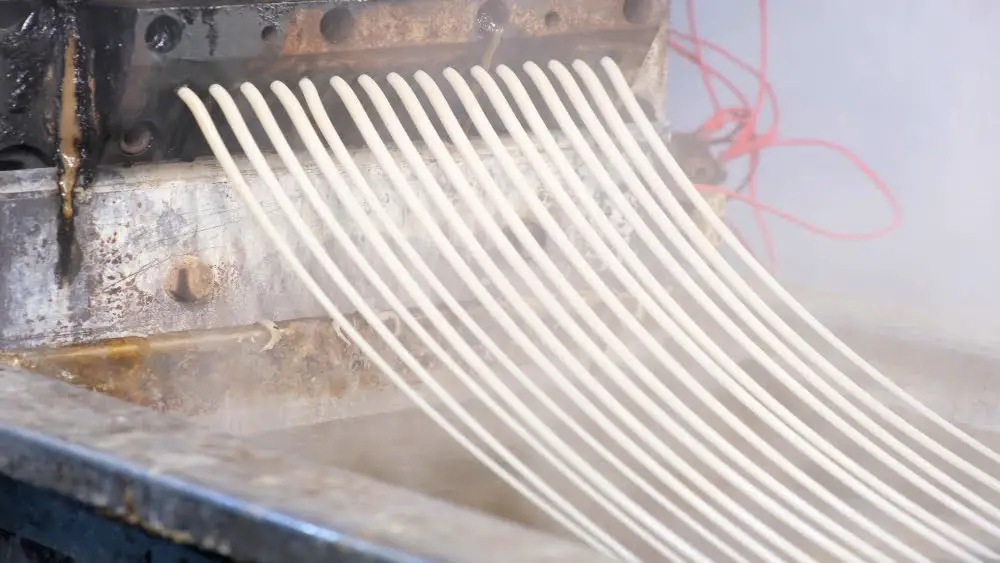
To achieve optimal performance in a polymer system, the compatibility, thermostability, and efficiency of the lubricant are important factors to consider.
Compatibility is important to maintaining the structural integrity of the polymer. Lubricants should not adversely affect the polymer’s chemical and mechanical properties.
Thermostability pertains to how the lubricant performs under heat. A good lubricant should maintain its lubricating properties even at high temperatures common in the extrusion process.
Efficiency should guide lubricant selection, based on cost-effectiveness and performance enhancements. The lubricant should minimize wear and tear on equipment, reducing costly maintenance and downtime.
When choosing a lubricant, one must also consider the specific needs of the polymer application. These factors could include the intended use of the end product, the type of polymer material being used, and the precise extrusion process employed.
In addition, the use of environmentally friendly lubricants is another selection criterion to consider. As industries aim for sustainability, a good lubricant should ideally reduce emissions, promote energy efficiency, and have a minimal environmental impact.
The interactions of the lubricant within the polymer matrix should also play a role in the selection. Keeping friction and adhesion to a minimum is important for proper function of equipment and to achieve a high-quality end product.
Last but not least, safety should never be compromised. A lubricant should be non-flammable, non-toxic, and safe for use in an industrial environment.
Solving Lubrication Issues in Polymeric Systems
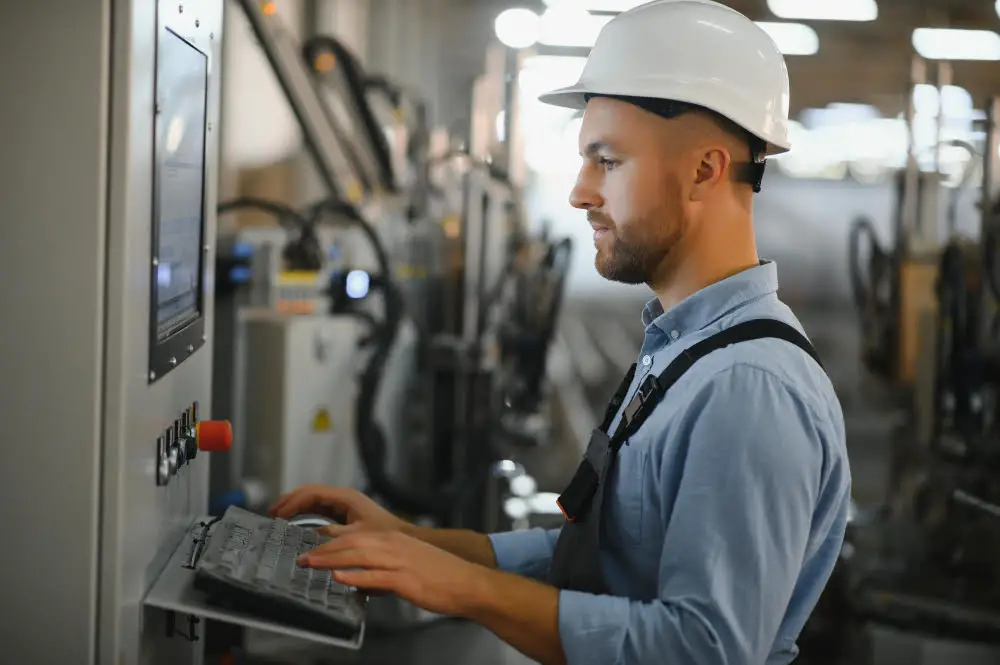
Identifying lubrication issues in polymeric systems is a critical step. These problems can be manifested in different ways, ranging from product defects to premature equipment wear or unexpected shutdowns. Here’s how you can address them:
Recognize Problems Early: Pay attention to signs such as excessive heat during extrusion or unusual wear patterns on equipment. Changes in the final product, such as warping or discolouration, can also indicate lubrication issues.
Monitor and Adjust: Don’t overlook the importance of frequently monitoring and adjusting the lube levels. Variances in temperature and pressure during the extrusion process can impact lube effectiveness.
Pick the Right Kind: Ensure you’re using the right type of lubricant for your polymer. For instance, silicone-based lubes are a better fit for polymers that are exposed to high temperatures.
Perform Regular Maintenance: Clean and inspect equipment regularly. This helps reduce residues that can interfere with lubricant perfomance and cause premature equipment breakdowns.
Consider Additives: Finding the right additive can extend the life and performance of your lube. They can help to minimize deposits and reduce friction, improving overall efficiency.
Consult the Experts: For persistent issues, don’t hesitate to call in professionals. Experts in polymers and lubricants can provide insights into best practices and techniques, helping to ensure smooth operation and a high-quality final product.
Suitable Lubricant/Wax Grades for Polymers
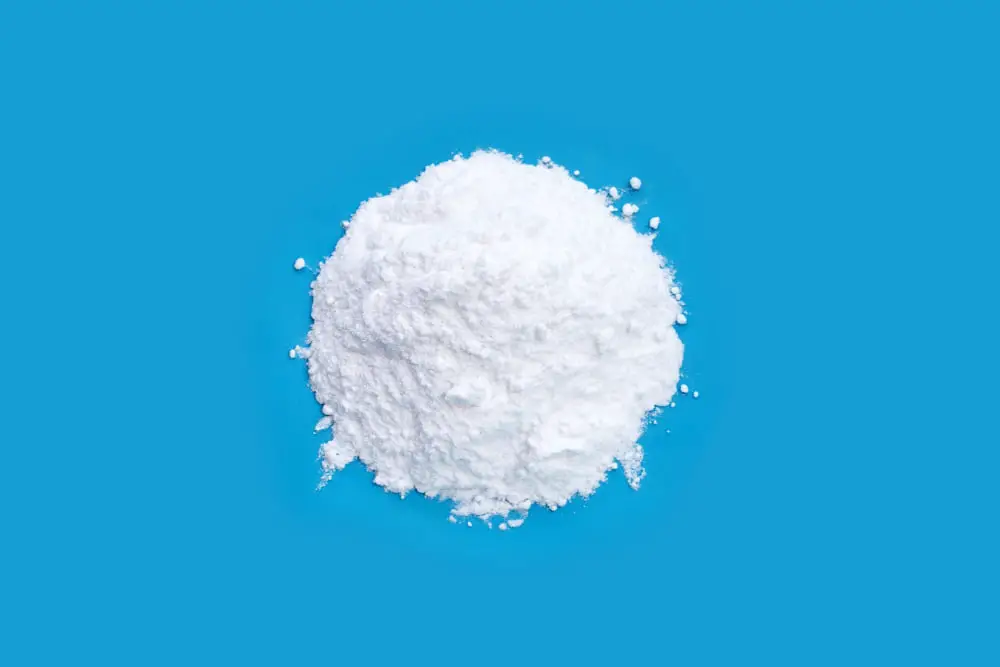
The right choice of lubricant can significantly influence the outcome of a plastic extrusion process. When referring to suitable lubricant/wax grades for polymers, a few key considerations emerge.
First, the lubricant’s compatibility with the polymer material forms a crucial component. External lubricants that are less compatible with polymers can form a lubricating layer between the processing equipment and the polymer, limiting the deposition of plastic materials on the equipment.
Second, the lubricant’s viscosity, defined by resistance to flow, holds importance. Lower viscosity grades are often preferred as they promote an easier flow and improved distribution within the polymer matrix during extrusion.
Third is the question of thermal stability. A lubricant with excellent thermal stability can help minimize degradation of both the lubricant and the polymer during the extrusion process.
Lastly, consider the interaction of the lubricant with other additives. The ability to form stable complexes resistant to separation during processing and end-use conditions offers an advantage.
To optimize the extrusion process, select a lubricant with the following properties:
- Ideally low viscosity
- Stability under high temperature
- Functions well with other process additives
- Compatible, yet sufficient in limiting polymer-material deposition
Rigid PVC Fusion in Extrusion Process
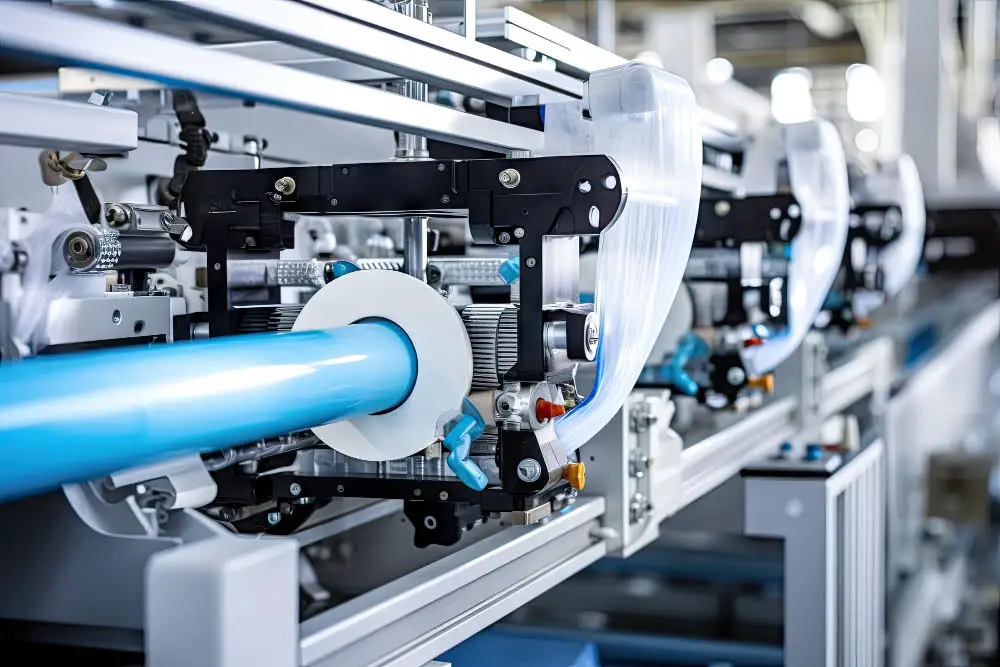
In the extrusion process, PVC (Polyvinic Chloride) gets heated until it reaches a state of plasticity which makes it malleable. This fusion process is a critical component:
- Initially, the PVC starts as a hard, rigid material. By applying heat, it transitions into a semi-fluid state.
- The temperature must be carefully monitored. Too much heat can decompose the PVC, leading to-HCl gas release, and too little heat prevents proper fusion.
- The extruder’s role is crucial, as it ensures uniform heat distribution.
- After reaching the desired temperature and achieving a homogenous mass, the material is pushed through a die, giving it the desired shape.
- Adequate lubrication plays a fundamental role by reducing friction and preventing degradation.
- Internal lubricants help in PVC fusion. They reduce the viscosity of the PVC melt, allowing for less energy consumption during the extrusion process.
- External lubricants are used to lower the adhesion between the PVC and metal surfaces, ensuring smooth extrusion and preventing sticking to the machine parts.
While rigid PVC fusion in an extrusion process involves complexity, understanding the key steps, right temperature control, and appropriate lubricant choice lead to a successful process.
Importance of Lubricant Type in Plastic Extrusion Process
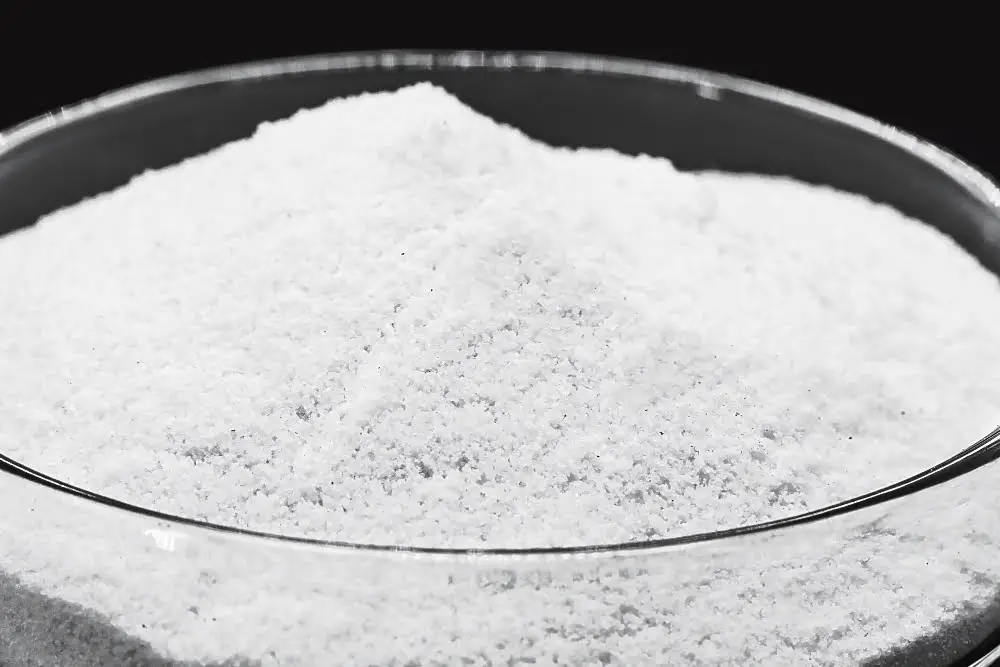
Choosing an appropriate lubricant significantly impacts the overall plastic extrusion process.
Certain lubricants help reduce friction between the polymer and the machine parts, thus lowering the wear on machinery. Higher machinery lifespan results in cost-effectiveness in the long term.
Besides lowering friction, lubricants also aid in heat distribution. This factor is crucial as an even temperature across the polymer ensures uniform melting, contributing to the creation of a high-quality end product.
However, not every lubricant is suitable for all types of plastic. Each polymer has specific requirements, making lubricant selection critical.
There is also the question of compatibility. The chosen lubricant must be compatible with the polymer and other additives. Incompatible lubricants may lead to a range of issues like discolouration or degradation of the polymer.
Lastly, lubricants can influence the speed of the extrusion process. Some lubricants enable faster production rates without compromising the quality of the plastic.
Thus, it is important to critically understand these aspects while choosing a lubricant for the plastic extrusion process. It contributes greatly to the operational efficiency, quality of product and ultimately, the overall effectiveness of production.
FAQ
What is the lubricant used in extrusion?
In the process of direct hot extrusion of steel, glass is commonly used as a lubricant.
What lubricant is safe for plastic?
Silicone, PFPE, synthetic hydrocarbons, and mineral oils are generally safe lubricants for plastic, ensuring to consider their suitability at varying operating temperatures.
What lubricants are used in cold extrusion?
Lubricants used in cold extrusion include varieties of cold extrusion oils and heavy duty forming lubricants, notably those under the HAKUFORM product line.
What is lubricant for polymer processing?
Lubricant for polymer processing is a substance that reduces friction and heat within polymer molecules, facilitating better flow and minimal temperature increase, with stearic acid and its metal salts being the most common type.
How does the type of lubricant affect the quality of plastic extrusion?
The type of lubricant significantly influences the quality of plastic extrusion by affecting the polymer’s flow, reducing friction in the machinery, thus contributing to a more uniform, smoother plastic product.
What factors should one consider when choosing lubricants for plastic extrusion process?
When choosing lubricants for the plastic extrusion process, one should consider the type of plastic being used, the performance requirements of the finished product, the operating temperature and the environmental conditions.
Can the improper use of lubricants damage the polymer during extrusion?
Yes, the improper use of lubricants can cause damage to the polymer during extrusion.
Recap