Learn how polymer additives enhance material properties and contribute to construction projects, making buildings stronger and more durable.
Key takeaways:
- Polymer additives enhance material properties in construction projects.
- Additives have different functions, such as stability, flexibility, fire resistance, color retention, and performance modification.
- Polymer additives can complicate recycling due to compatibility issues and degradation during the process.
- Selecting the right antimicrobial additive requires considering the plastic type, application, spectrum of activity, and regulatory compliance.
- Colorants not only enhance aesthetics but also contribute to consistency, UV stability, and recycling coding systems.
Role of Polymer Additives
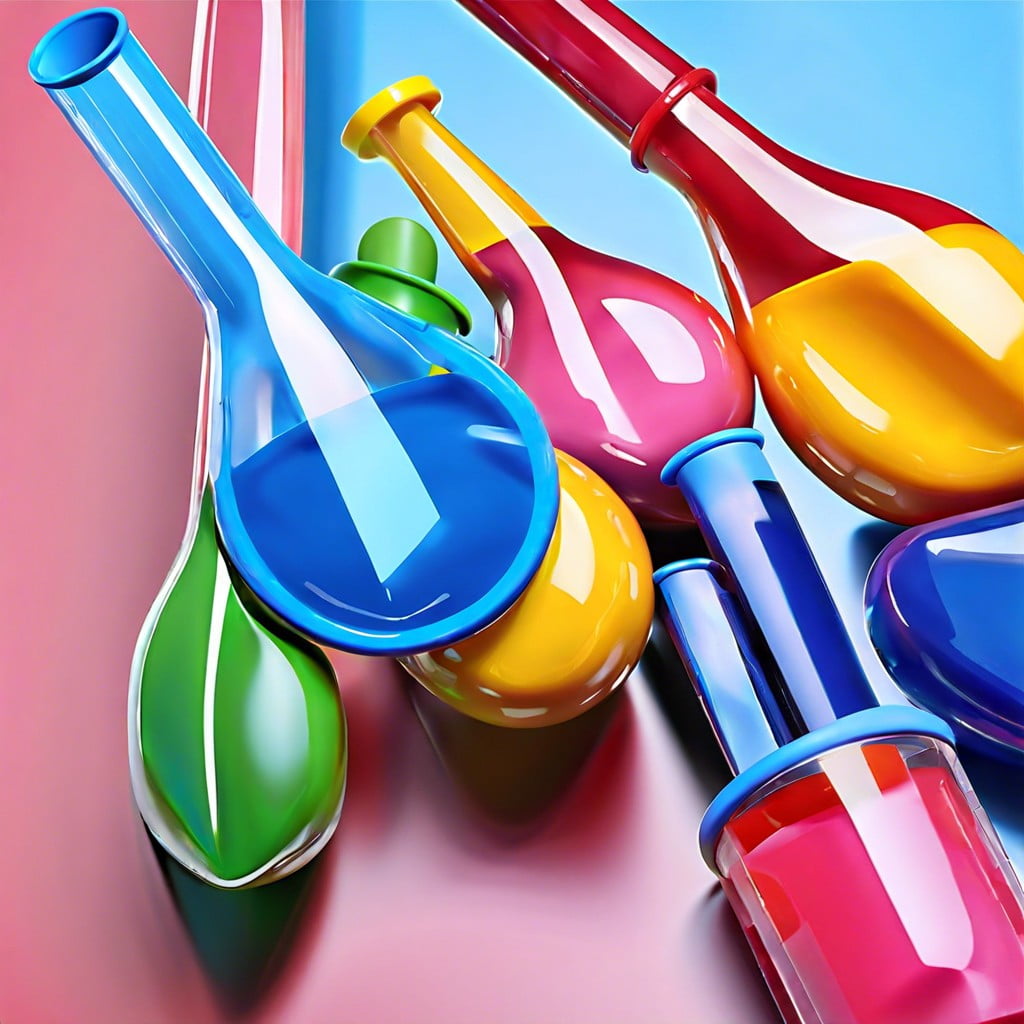
Polymer additives are like secret ingredients in a chef’s recipe; they fine-tune the end product to taste better, or in this case, perform better. Here are a few points to chew on:
- Stability Boosters: These additives protect plastics from things like sunlight and heat, which can turn a vibrant backyard chair into a brittle eyesore.
- Flexibility Friends: They ensure that your rubber boots can survive a rain dance without cracking, proving that a little bendability goes a long way.
- Fire Fighters: These are the unsung heroes that resist flames, making materials less of a fire hazard. Ever wonder why your toaster doesn’t go up in flames? Thank additives.
- Color Custodians: Ever see a playground slide fade to a sad shade of gray? Additives keep colors from washing out faster than a bad dye job in the rain.
- Performance Producers: Additives modify properties, giving you the right tool for the job. Just like you wouldn’t use a sledgehammer to swat a fly, you’d pick the right plastic for the right task.
Remember, the goal isn’t just to make materials last longer or look prettier. It’s about making sure they do their job well, from the soles of your hiking boots to the insulation on your house.
Additives Incorporation in Polymer Formulation
Imagine a superhero squad, each member bringing a special power to the table. That’s like polymer additives in a polymer mix. They swoop in to give plastics superpowers they wouldn’t have on their own!
First off, stability is a big deal. Additives like UV stabilizers and antioxidants help plastics endure sunbathing without a meltdown or an age crisis. It’s like sunscreen and anti-wrinkle cream, but for materials!
Then, there’s the strength game. Impact modifiers are the gym buddies for your polymers. They bulk up the plastic so it can take a hit without cracking. Imagine plastic doing push-ups, that’s what impact modifiers are all about.
Slip agents have a different vibe. These are the smooth talkers that let plastic surfaces glide past each other. Without them, you’d have more screeching bags at the grocery store than a flock of angry seagulls.
Flame retardants are the brave firefighters. They jump into the formulation to slow down any fiery shenanigans. They ensure that if things heat up, your plastic won’t turn into an indoor barbecue.
And let’s not forget the color squad. Colorants make sure your plastics aren’t just lurking in the shadows. They bring the visual pop, making everything from your phone case to your garden chair look snazzy.
All these additives join forces in the polymer formulation to save the day, making plastics tougher, longer-lasting, safer, and prettier. They’re the unsung heroes behind your everyday plastic products.
Impact of Plastic Additives On Recycling
Plastic additives play a double-edged sword role in recycling. On one hand, additives like stabilizers and flame retardants increase a product’s life and safety standards. On the flip side, when it’s time to break down and repurpose these materials, they can toss a wrench into the works.
Different additives may not play nicely together, making the recycled material’s properties a bit unpredictable. For instance, PVC containing different plasticizers can be like mixing oil and water—they resist blending, resulting in a less than stellar recycled product.
Recycling facilities must jump through hoops to separate plastics by type and additives to avoid contamination. Imagine trying to bake a cake with all the ingredients mixed up – additives make sorting and recycling plastics a similar challenge.
Moreover, some additives can degrade during the recycling process, which is like trying to recharge a battery that’s past its prime. As they break down, they might release substances that could be harmful or reduce the quality of the recycled product.
Not all doom and gloom though! Innovations are underway to develop additives that make the recycling process smoother than a fresh jar of peanut butter. Biodegradable additives and those designed for compatibility with multiple resins are game-changers for greener recycling.
Selecting the Right Antimicrobial Additive for Your Plastic Products
Selecting the right antimicrobial additive is like picking a winning team – it requires knowing the players and the game they’re playing. These additives function as the defensive line against bacteria, fungi, and other microorganisms, ensuring your plastic products remain hygienic and durable.
First, you’ll want to consider the type of plastic and its application. For instance, kitchenware demands a different antimicrobial touch than medical devices. Your choice of additive must be compatible with the base material; otherwise, it’s like mixing oil and water – not a good fit.
Next is the spectrum of antimicrobial activity. Think about it as the range of germs your product can guard against. Some additives are like snipers, targeting specific microorganisms, while others are more like a swiss army knife, warding off a broad array of unwanted bugs.
Regulatory compliance is the rulebook these additives play by. Various industries have different standards, and you must ensure your additive choice doesn’t land you in hot water. In food contact applications, for instance, the additive has to meet FDA regulations – no ifs, ands, or buts about it.
Finally, consider the longevity and consistency of antimicrobial performance. You wouldn’t want a guard that dozes off during their shift. Select an additive that offers lasting protection to keep your products in the safe zone for the long haul.
Remember, the right choice can extend the life of your product and keep it looking sharp as a new pin. So, take your time, do your homework and your plastic will stand up to the critter test with flying colors.
The Importance of Colorants in Plastic Manufacturing
Adding a splash of color to plastics isn’t just about making them pretty. Colorants carry a heavy load in functionality, too. They help manufacturers achieve consistency in appearance, which is critical for brand identity and consumer trust. Imagine picking up your favorite soft drink and the bottle is a different shade of green than usual – kind of sets off alarm bells, doesn’t it?
The selection of colorants can influence more than just aesthetics. Some provide additional UV stability, slowing down the degradation process when plastics bask in the sun. Ever left a toy out all summer and found it faded and brittle? That’s UV radiation at work, and the right colorant could’ve helped it keep its color and strength.
Colorants can also be part of a clever coding system within the recycling industry, signaling the type of plastic and detouring it to the correct processing route. Life’s easier when you’re on the right path, after all.
In a nutshell, colorants are small but mighty players that transform the world of plastics from a grayscale film to a technicolor blockbuster, with benefits that go beyond skin deep.
Recap