Discover the efficient method of drying plastic pellets for filament extrusion to ensure high-quality output in 3D printing and other applications.
Drying plastic pellets for filament extrusion is a critical step in the production process, as it helps to remove moisture that can degrade the quality of the final product. The process typically involves using a desiccant air dryer, where the pellets are heated in a hopper to a specific temperature for a certain period of time. The key is to strike a balance; too much heat can cause the pellets to melt, while not enough may leave residual moisture. The exact specifications can vary depending on the type of plastic being used.
This article will delve into the specifics of how to properly dry different types of plastic pellets for filament extrusion, ensuring optimal results every time.
Key takeaways:
- Moisture in plastic pellets disrupts the extrusion process and affects product quality.
- Four common drying methods: hot air, desiccant, vacuum, and infrared dryers.
- Different drying techniques have unique advantages and challenges.
- The drying method should be chosen based on the type of plastic being used.
- Optimal drying conditions depend on factors such as temperature, duration, and relative humidity.
How Moisture Affects Plastic Pellets in Filament Extrusion
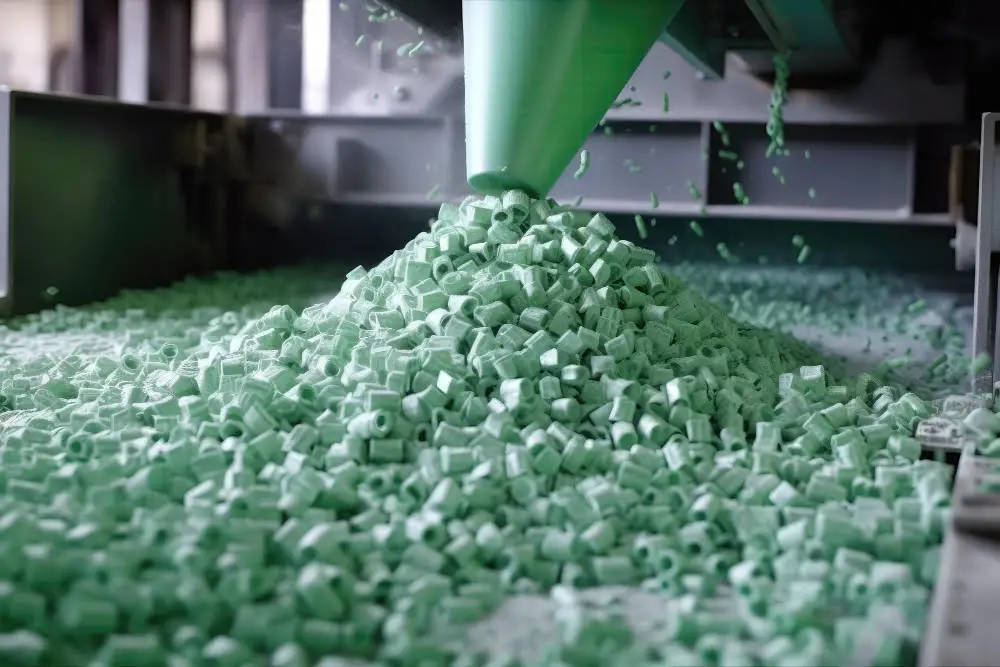
Moisture acts as a barrier during the extrusion process, disrupting the uniform melting of the pellet material. The presence of water in plastic pellets changes their melt flow behaviour, causing inconsistencies in the extrusion process that result in a flawed final product.
When water molecules penetrate the plastic, they chemically react and form steam under the intense heat of the extrusion process. The generated steam presents operational challenges, including interrupting melt flow, causing bubbles or voids, and weakening the structural integrity of the final extruded product.
The steam not only affects the product quality but also makes the extrusion process hazardous. As the water vapor expands, it creates pressure within the extruder. In extreme cases, it could lead to a violent rupture, signifying a safety concern.
Hence, prior to the extrusion process, plastic pellets should be sufficiently dried. This involves a series of steps including:
- Evacuating the initial surface water from the plastic pellets.
- Inducing heat to remove the water molecules that have penetrated the pellet’s interior.
- Constant monitoring of temperature and time to prevent overdrying.
- Proper storage to keep the dried pellets away from moisture until they are ready for processing.
By properly managing the moisture content of plastic pellets, we ensure a smoother extrusion process and a higher quality output product.
Key Signs Indicating the Need to Dry Plastic Pellets
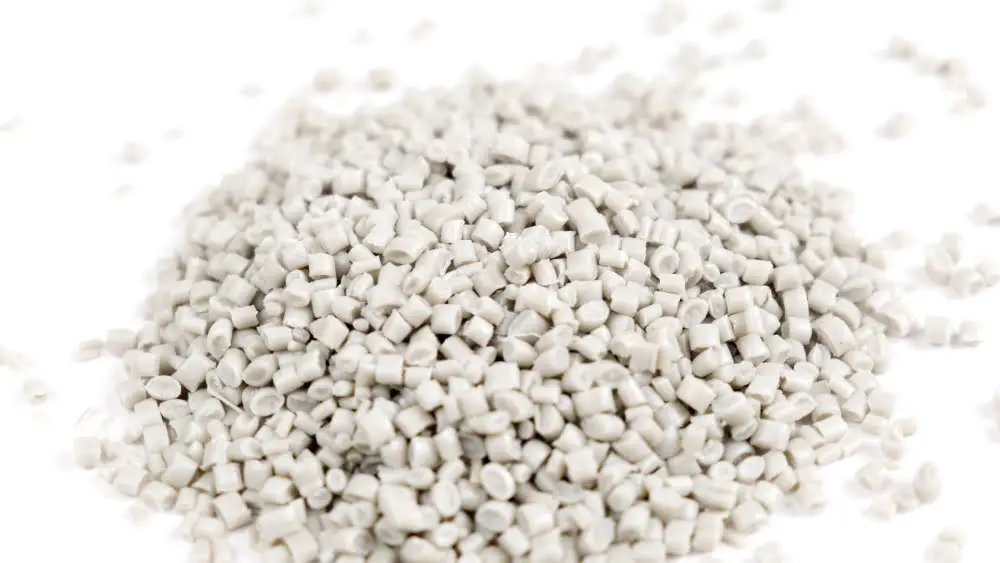
First, note the visual appearance of the pellets. Moisture-laden pellets often appear cloudy or have a dull finish, unlike dry pellets which exhibit a shiny, clear appearance.
Next, consider the performance in filament extrusion. Wet pellets are less consistent in the manufacturing process, leading to filament diameter variations. This can indicate the presence of excess moisture.
It’s also important to pay attention to the extruder’s behavior. Unwanted noises from the extruder, like popping or hissing sounds, signal that water vapor is escaping from the heated pellets.
Finally, one might observe traces of steam or water droplets in the output. This is particularly the case when high temperatures are applied during extrusion. If this happens, it signifies that your pellets were overly damp before extrusion commenced. By taking note of these indicators, efficient action to dry the pellets can be taken to maintain the quality of end product.
Types of Different Drying Methods for Plastic Pellets
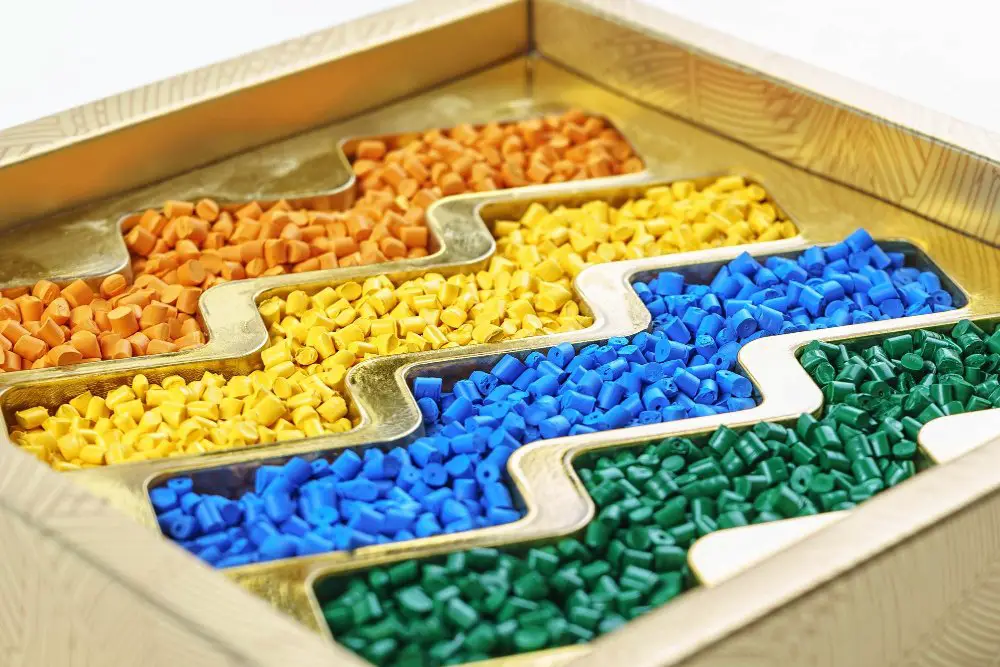
There are primarily four approaches that can be adopted to get rid of moisture from plastic pellets.
Hot air dryers are the most common and simplest. They function by circulating hot air around the plastic pellets, facilitating moisture evaporation. These dryers are economically viable, easy to use, and work well with most types of plastic.
Desiccant dryers, using a chemical substance known as desiccant, absorb the moisture from the plastic pellets. They prove useful for sensitive plastics that easily degrade when heated.
Vacuum dryers operate by reducing the air pressure around the plastic pellets. This allows the moisture to evaporate at much lower temperatures, providing a gentle drying process suitable for the most sensitive plastics.
Infrared dryers are the swiftest, employing infrared light to heat the pellets directly, without heating the surroundings. They provide a rapid and efficient drying method but require more cautious handling due to the high energy levels involved.
These strategies differ significantly in their efficiency, cost, and suitable usage scenarios – factors that should be considered when choosing a drying method. You’re advised to consult specific guidelines for the type of plastic you are working with.
Comparing the Efficacy of Various Plastic Pellet-drying Techniques
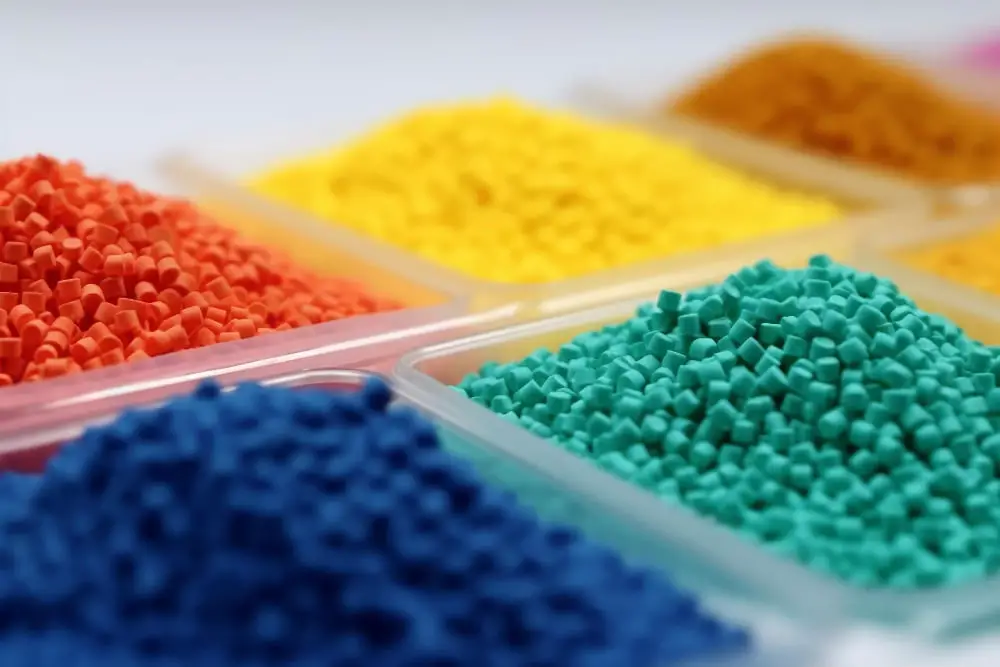
Different drying techniques possess unique advantages and challenges depending on the specific needs of an application.
Hot air drying is the most commonly used method. It uses a consistent airflow at high temperatures to evaporate moisture. This method is straightforward, but can sometimes lead to surface-level drying while leaving internal moisture untouched.
Vacuum drying utilizes reduced pressure to lower the boiling point of water, leading to quicker drying at reduced heat. However, efficient vacuum systems can be costly.
Desiccant drying uses a hygroscopic substance to absorb moisture from the pellets. This method works well for many types of plastic but replacing the desiccant can be a hassle.
Infrared drying exposes the pellets to infrared radiation, heating them quickly and efficiently. The agitation feature in modern infrared dryers also allows for a uniformly drying process.
Heated hopper drying is a method in which heated air is circulated around the entire hopper. This method is relatively economical, efficient, and doesn’t require constant monitoring.
The principle factors to consider when deciding among these techniques include the type of plastic being dried, the extent of drying needed, available equipment and energy usage. Remember, the effective drying of plastic pellets doesn’t just improve the final product quality, but will improve filament extrusion efficiency as well.
Choosing the Appropriate Drying Method Based On Plastic Type
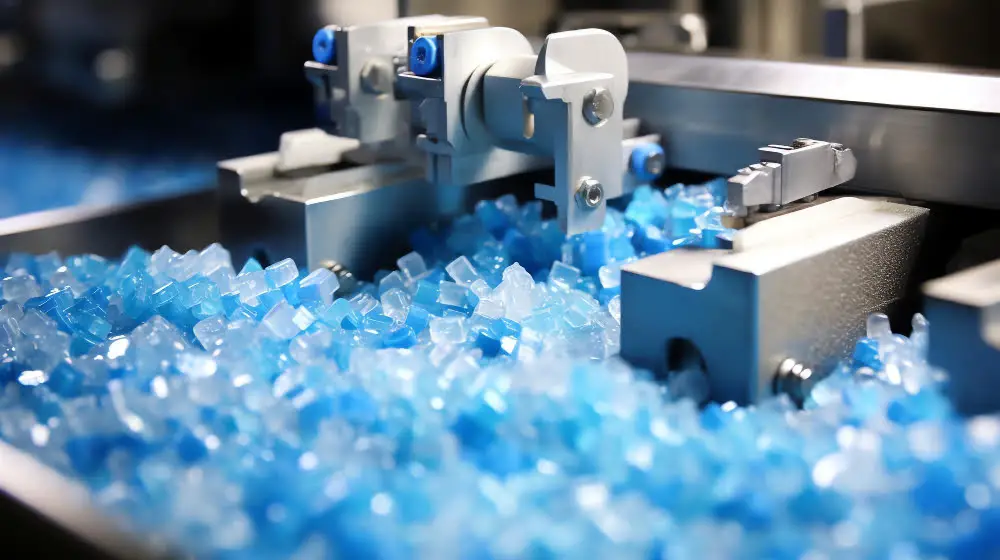
Each type of plastic resin has particular characteristics that render one drying method superior to others. These are primarily impacted by factors such as the melting point, glass transition temperature, and water absorption level.
Hot air drying is a common approach universally applicable for all types of plastics. It operates by directly supplying heated air to the plastic pellets.
Vacuum drying goes one step further and removes air from the drying process, making it an excellent choice for heat-sensitive plastics. This method can reduce drying time significantly.
Desiccant drying, suitable for plastic types highly sensitive to moisture, such as nylon and polyester. It uses a desiccant material to absorb moisture from the air before it contacts the plastic pellets.
Infrared drying employs infrared rays to heat the pellets directly without the need for air as a heat transfer medium. This method is ideal for high-density plastics which have a slow drying kinetic.
Before selecting a method, it’s crucial to refer to the pellet manufacturer’s recommendations. It will help to ensure the successful drying of plastics and maintain the quality of filament extrusion.
How to Determine the Optimal Drying Conditions for Plastic Pellets
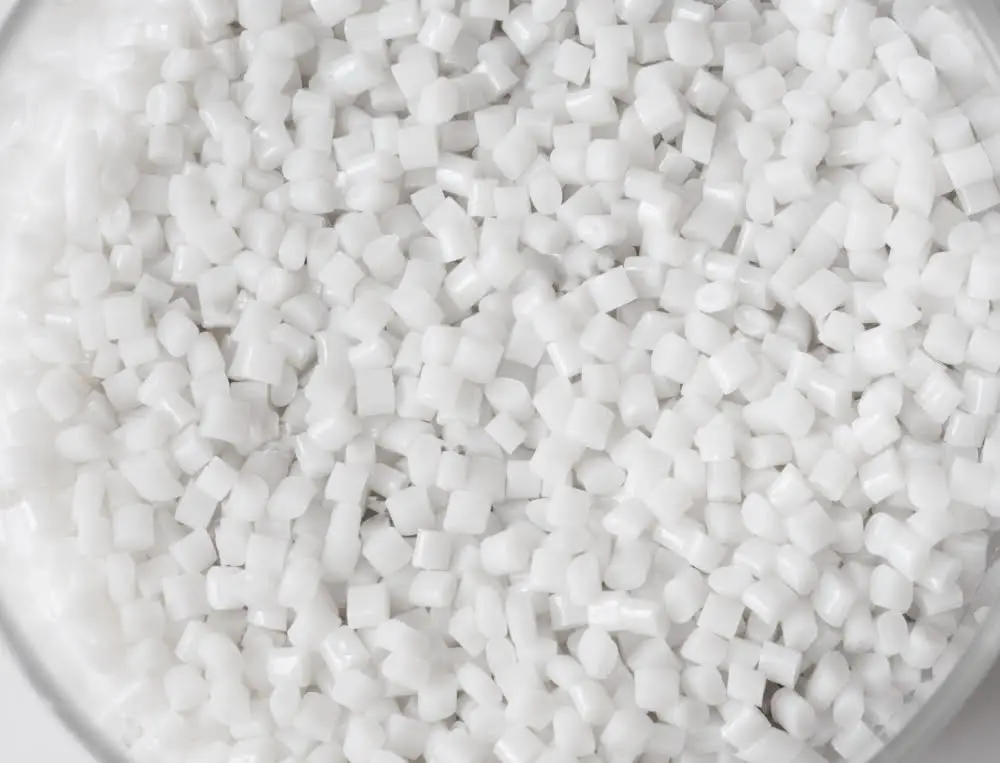
Understanding the type of plastic is the starting point for determining drying conditions. There are countless types of plastics, and each possesses unique physical and chemical properties.
To establish the most favorable drying conditions, identifying moisture absorption characteristics is essential. Some polymers can absorb a large amount of moisture from the air if not properly protected, which can affect the extrusion process.
Targeted drying temperatures are dictated by the specific type of plastic in use. For instance, polyethylene terephthalate (PET) requires a higher drying temperature than polylactic acid (PLA).
Setting the right duration for drying is essential. While some pellets may require a few hours, others might need upwards of 16 hours. An under-dried pellet can cause potential defects in the final product, but over-drying could lead to thermal degradation of the polymer.
Relative Humidity (RH) also plays a crucial role in ascertaining optimal drying conditions. Certain dryers can reduce RH to nearly zero, and typically, the lower the RH, the better.
Lastly, constantly monitoring and adjusting dryer settings according to changes in ambient conditions, plastic formulation, or throughput rates ensures the success of the filament extrusion process.
Remember, experimenting, documenting your process, evaluating the results, and fine-tuning your settings is part and parcel of achieving optimal drying conditions.
Maintaining and Storing Dry Plastic Pellets for Filament Extrusion
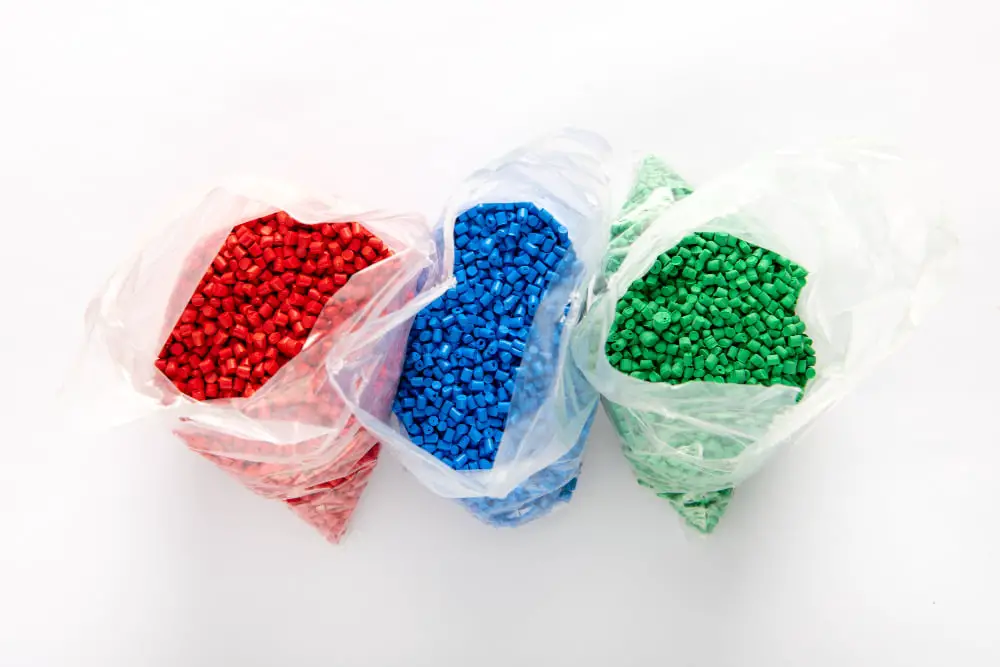
Maintaining the dryness of pellets is as essential as the drying process itself. Sealed containers serve as the best storage options, ensuring that moisture doesn’t seep into the pellets again.
Avoiding open-air storage is crucial. Storing them in airtight and waterproof containers helps in keeping out humidity. It extends the shelf-life of the pellets, preserving their ideal state for filament extrusion.
In case of bulk storage, a climate-controlled room with dehumidifiers is preferred. This ensures a low-moisture atmosphere, preserving the dryness of the pellets over extended periods.
Remember to establish a first-in, first-out system. This method reduces the chance of the pellets absorbing moisture, operating on the principle of using the oldest stock first.
Minimize exposure of the dried pellets to air. When using the pellets, make sure that the storage container is open for the shortest time possible to prevent moisture from coming in.
When transferring the pellets from the dryer to the extruder, use enclosed hoppers. This avoids exposure to humidity and maintains the integrity of the dried pellets.
In terms of maintenance, it’s important to regularly check storage containers for potential leaks. Identify any signs of moisture within and take the necessary precautions to rectify the situation. Regular inspection ensures the efficient performance of the filament extrusion process.
FAQ
How do you dry ABS pellets?
ABS pellets can be effectively dried by using a regular oven, toaster oven, dedicated filament dryer or a food dehydrator, typically at a temperature range of 65-70°C for a period of 2-6 hours.
How do you turn pellets into filaments?
Pellets are transformed into filaments through a process where they are melted into a molten form by heating elements in a zone, and then pushed out of a meticulously crafted nozzle by a rotating screw, consequently giving the plastic its string-like filament form.
Does TPU filament need to be dried?
Yes, TPU filament generally requires drying because its high water content can cause printing issues such as low layer adhesion, extrusion bubbling, and blobs.
What is the optimal temperature for drying PETG pellets?
The optimal drying temperature for PETG pellets is around 65°C (150°F).
How does humidity affect the drying process of plastic pellets?
Humidity slows down the drying process of plastic pellets as it increases the moisture content in the air which the pellets absorb making them take longer to dry.
Can over-drying negatively impact the quality of filament extrusion?
Yes, over-drying can negatively impact the quality of filament extrusion as it may lead to brittleness and dimensional instability.
Recap