Polymers can be processed and shaped into building materials through various techniques, such as extrusion, injection molding, thermoforming, and compression molding.
Polymers are a versatile class of materials that can create a wide range of products, including building materials. But how are these polymers processed and shaped into the components needed for construction?
We will explore the various methods used to process and shape polymers into building materials.
We’ll cover everything from injection molding to extrusion, so you can better understand how these processes work and why they are crucial for creating quality components.
Processing and shaping polymers into building materials involve various techniques, such as extrusion, injection molding, thermoforming, and vacuum forming. These processes involve heating the polymer to a malleable state before using pressure or molds to shape it into the desired form.
Additives may enhance certain properties of the material for specific applications.
Key takeaways:
- Polymers can be processed and shaped into building materials through various techniques such as extrusion, injection molding, thermoforming, and compression molding.
- Additives are often used to enhance specific properties of polymer-based building materials.
- Polymer processing involves methods such as extrusion, injection molding, compression molding, and thermoforming.
- Shaping polymers into building materials can be done through molding, extrusion, and thermoforming.
- Polymers offer advantages in construction such as durability, customization, and resistance to environmental factors.
Polymer Processing
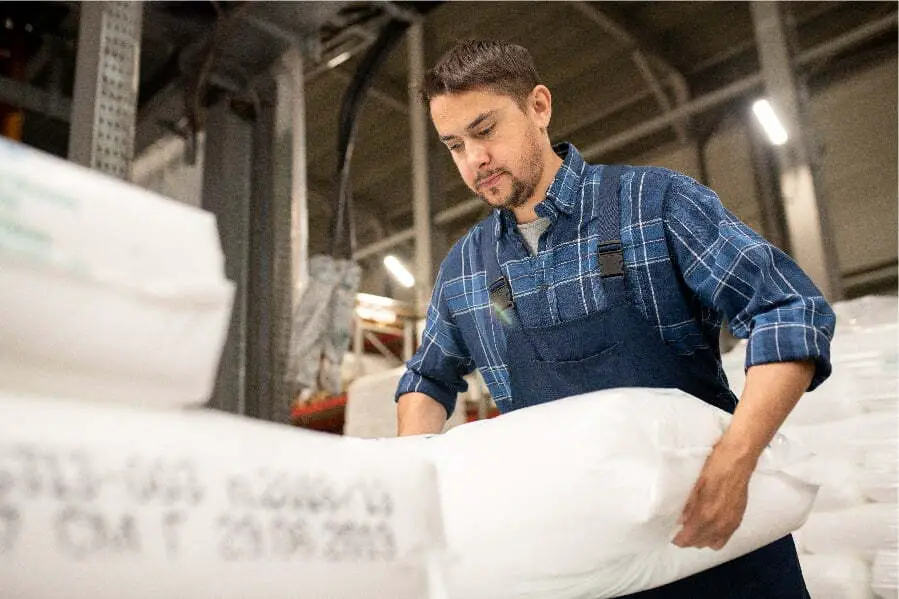
Processing is the process of transforming raw materials into a usable form. In the case of polymers, processing involves melting and molding them into desired shapes.
This can be done through various methods such as extrusion, injection molding, compression molding, and thermoforming. Extrusion involves pushing molten polymer through a die to create a continuous shape like pipes or rods.
Injection molding uses pressure to inject a molten polymer into molds designed for specific shapes and sizes. Compression molding is similar to injection molding but uses heat and pressure instead of just pressure alone.
Thermoforming uses heat to soften plastic sheets formed over molds to create complex shapes with intricate details. All these processes help turn polymers into building materials that can be used for construction projects or other applications requiring strong yet lightweight materials.
Polymer Shaping
Shaping polymers into building materials involves manipulating the material to create a desired shape. This can be done through various methods, such as molding, extrusion, and thermoforming.
Molding is when the polymer is heated and then forced into a pre-made mold that gives it its desired shape. Extrusion is when the polymer is melted down and pushed through an opening with a specific cross-section to form shapes like tubes or rods.
Thermoforming involves heating the polymer until it becomes pliable enough to be formed into different shapes by hand or with tools. These processes are used to create building materials from polymers that have specific shapes for their intended purpose.
Shaping of Building Materials
Building materials are used to construct buildings, structures, and other objects. They can be natural or artificial, including wood, stone, brick, concrete, steel, glass, plastic, and more.
Building materials are chosen based on their strength, durability, and aesthetic appeal. Polymers are a type of building material that can be processed and shaped into various forms for construction projects.
Polymers have many advantages over traditional building materials, such as being lightweight yet strong enough to withstand extreme temperatures and weather conditions. Additionally, they can be molded into any shape desired, making them ideal for creating unique designs or customizing existing structures.
Processing polymers involves heating them until they become malleable, then shaping them with tools such as molds or presses before cooling them down, so they retain their new form. This process allows polymers to be used in various ways, from insulation to roofing tiles to decorative accents on walls or furniture pieces.
Polymer Durability and Lifespan in Construction
When it comes to building materials, durability is a crucial factor. Polymers have gained popularity in construction due to their excellent durability and long lifespan.
Unlike traditional materials like wood or metal, polymers are resistant to rotting, corrosion, and degradation caused by environmental factors such as moisture or UV radiation.
The inherent properties of polymers make them highly durable. They possess high tensile strength which allows them to withstand heavy loads without deformation or structural failure.
They exhibit exceptional resistance against chemicals commonly found in construction environments.
To further enhance the longevity of polymer-based building materials, manufacturers often incorporate additives that provide additional protection against weathering effects such as fading from sunlight exposure or cracking due to temperature fluctuations.
Moreover, advancements in polymer processing techniques have enabled the development of reinforced polymers that offer even greater strength and durability for demanding applications like bridges or high-rise buildings.
The use of polymers in construction ensures longer-lasting structures with reduced maintenance requirements over time.
Advancements in Polymer Processing Technology
These advancements have led to improved efficiency, cost-effectiveness, and overall quality of the final products.
One notable advancement is the development of extrusion techniques. Extrusion involves forcing molten polymer through a die to create a specific shape or profile.
Traditional extrusion methods were limited in terms of complexity and precision. However, with new technologies such as co-extrusion and multi-layer extrusion, manufacturers can now produce building materials with intricate designs and enhanced functionality.
Another breakthrough is injection molding technology for polymers used in construction applications. Injection molding allows for high-volume production of complex shapes by injecting molten polymer into a mold under high pressure.
This method offers precise control over dimensions while ensuring consistent quality across multiple parts or components.
Furthermore, additive manufacturing (3D printing) has emerged as an innovative technique for shaping polymers into custom-made building elements with intricate geometries that would be challenging to achieve using traditional methods alone. 3D printing enables architects and designers to explore unique designs while reducing material waste during production.
Advancements have been made in composite manufacturing processes where reinforcing fibers are combined with polymers to create strong yet lightweight construction materials like fiber-reinforced composites (FRPs). Techniques such as pultrusion allow continuous production of FRP profiles that offer excellent strength-to-weight ratios compared to conventional materials like steel or concrete.
Processing Methods for Bio-Based Polymers in Construction
These polymers can be processed and shaped into various building materials using different methods. One common processing method is extrusion, where the bio-based polymer is melted and forced through a die to create a continuous profile with a desired shape.
Injection molding is another technique used for more complex shapes by injecting molten bio-based polymer into a mold cavity under high pressure. Compression molding involves placing the polymer material in between heated molds and applying pressure until it solidifies into the desired form.
Thermoforming is yet another process that utilizes heat to soften the bio-based polymer sheet which can then be molded onto specific shapes or patterns using vacuum suction or mechanical force. Rotational molding involves heating powdered biopolymer inside a rotating mold until it melts and coats its inner surface evenly before cooling down to form hollow objects like tanks or containers.
Role of Process Aids in Polymer Processing
These additives are specifically designed to improve various aspects of the manufacturing process, such as flowability, mold release, surface finish, and overall product quality.
One common type of process aid is a lubricant. Lubricants reduce friction between polymer molecules during processing by acting as a barrier between them.
This helps prevent sticking or clumping together of polymers and facilitates smoother flow through equipment like extruders or injection molding machines.
Another important class of process aids is known as dispersing agents or surfactants. These additives help disperse fillers or pigments evenly throughout the polymer matrix during compounding processes.
By promoting uniform distribution, they ensure that desired properties like color consistency and mechanical strength are achieved in the final product.
Antioxidants are yet another category of process aids used in polymer processing for construction materials. They help protect polymers from degradation caused by heat exposure during high-temperature processes like extrusion or molding.
By inhibiting oxidation reactions that can lead to material breakdown over time, antioxidants extend the lifespan and durability of building materials made from polymers.
Impact of Polymer Matrix Components On Building Material Formation
These components include polymers, fillers, plasticizers, and additives. Polymers provide the structural integrity and strength to the material while fillers enhance properties such as stiffness or flame resistance.
Plasticizers are added to improve flexibility and workability, making it easier to shape and mold the material during processing.
Additives are another important component that can modify various characteristics of building materials. They can enhance durability by providing UV resistance or increase fire retardancy by incorporating flame retardant additives into the polymer matrix.
By carefully selecting these components and their proportions in a polymer formulation, manufacturers can tailor building materials with specific properties suitable for different applications in construction. For example, adding reinforcing fibers like glass or carbon fibers enhances mechanical strength while maintaining lightweight characteristics.
Understanding how each component interacts within a polymer matrix is essential for optimizing material performance during processing as well as ensuring long-term durability once installed in buildings.
FAQ
What is the process for building and making polymers?
The process of building and creating polymers involves the combination of basic units known as monomers to form long-chain polymers, accomplished through various polymerization techniques that give rise to different types of polymers like PVC, Bakelite, and Teflon.
How are polymers processed?
Polymers are processed by first converting them into a liquid through melting or dissolution, then continuously forcing this liquid through a spinnerette to form filaments, in a process called melt spinning if the polymer forms a stable melt.
How are polymers used in construction?
Polymers in construction are prevalently utilized in various applications including flooring, windows, cladding, rainwater management, pipe systems, membranes, seals, glazing, insulation, and signage.
What are the key characteristics of polymers that make them ideal for construction purposes?
The key characteristics of polymers that make them ideal for construction purposes are their durability, resistance to corrosion, manageability, versatility, light-weight nature, insulating properties and cost effectiveness.
How has the use of polymers in construction evolved over the years?
The use of polymers in construction has evolved from basic applications, such as flexible coatings and adhesives, to advanced uses like polymer concrete, structural composites, and thermoplastic components, enhancing durability, performance, and sustainability in the build.
Can polymers play a role in sustainable and eco-friendly construction?
Yes, polymers can play a significant role in sustainable construction due to their durability, resistance to environmental conditions, light weight, and ability to be recycled or produced from renewable resources.
Recap