Glass fiber polymer composites are revolutionizing the construction industry with their exceptional strength, lightweight and durable properties.
I was always fascinated by the towering skyscrapers and grandiose structures that surrounded me. The way they seemed to defy gravity and reach towards the sky with such ease left me in awe.
As I grew older, my passion for construction only intensified, and I found myself delving deeper into the world of materials science.
One material that has particularly caught my attention is glass fiber polymer composites. These versatile materials have been used in construction for decades, but their potential is often overlooked or misunderstood.
In this blog post, we’ll explore what makes glass fiber polymer composites so special and why they should be on every builder’s radar. So buckle up and get ready to discover a new world of possibilities in construction!
Key takeaways:
- Glass fiber polymer composites offer exceptional strength-to-weight ratio
- GFRP materials are resistant to corrosion and weathering
- Manufacturing techniques include pultrusion and filament winding
- Applications include bridges, buildings, and outdoor structures
- GFRP materials offer durability, low maintenance, and sustainability benefits
Introduction to Glass Fiber Polymer Composites
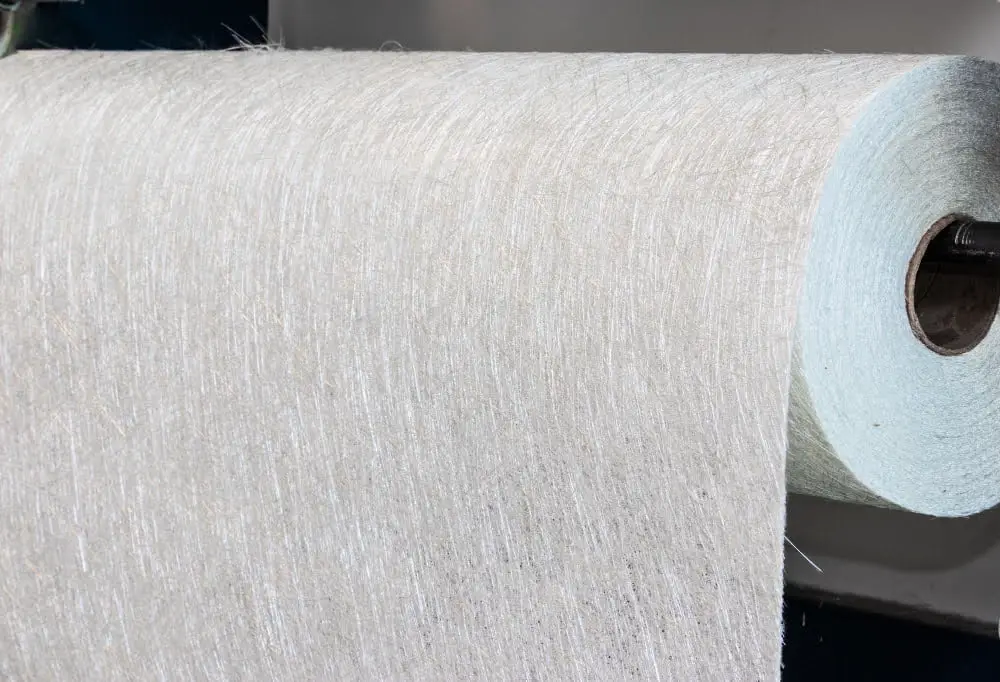
Glass fiber polymer composites, also known as fiberglass reinforced polymers (FRP), are a type of composite material made up of glass fibers and a polymer matrix. These materials have been used in various industries for decades due to their high strength-to-weight ratio, corrosion resistance, and durability.
However, it’s only recently that the construction industry has started to take notice of their potential.
As I delved deeper into the world of materials science during my studies and career in construction engineering, I discovered that glass fiber polymer composites offer unique advantages over traditional building materials like steel or concrete. They can be molded into complex shapes with ease while maintaining structural integrity; they’re lightweight yet strong enough to support heavy loads; they don’t corrode or rust like metal does; and they’re resistant to fire damage.
Despite these benefits though, many builders still aren’t aware of how versatile these materials can be when it comes to construction projects. That’s why I’m excited about sharing my knowledge on this topic with you today!
In this article we’ll explore some examples where glass fiber polymer composites have been successfully implemented in real-world applications within the industry – from bridges and buildings all the way down to small-scale home renovations – so you too can see just how valuable these innovative products truly are!
Properties of Glass Fiber Reinforced Polymers (GFRP)
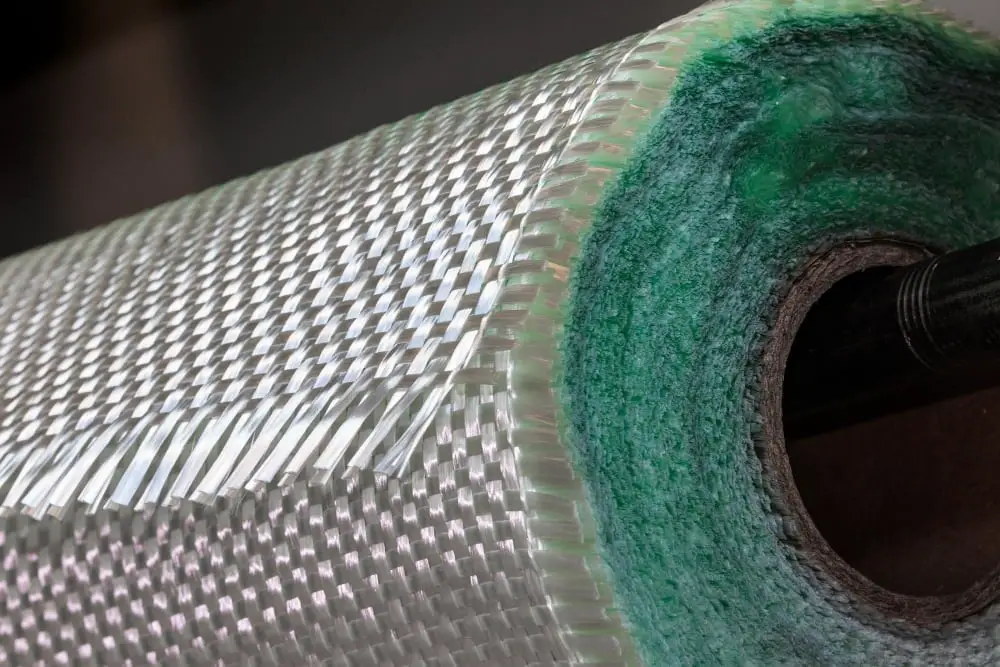
Glass fiber reinforced polymers (GFRP) are composite materials made up of a polymer matrix and glass fibers. These materials have unique properties that make them ideal for use in construction projects.
One of the most significant advantages of GFRP is their high strength-to-weight ratio. This means that they can be used to create structures that are both strong and lightweight, making them perfect for applications where weight is a concern, such as bridges or aircraft components.
Another advantage of GFRP is their resistance to corrosion and weathering. Unlike traditional building materials like steel or wood, GFRPs do not rust or rot when exposed to moisture or harsh environmental conditions.
This makes them an excellent choice for outdoor structures like decks, railings, and even entire buildings.
As I continued my research into these versatile composites during my studies in material science engineering at university; it became clear how much potential there was with this material within the construction industry – yet so few people knew about it! It’s time we shed some light on this underutilized resource!
Manufacturing Techniques for GFRP Composites
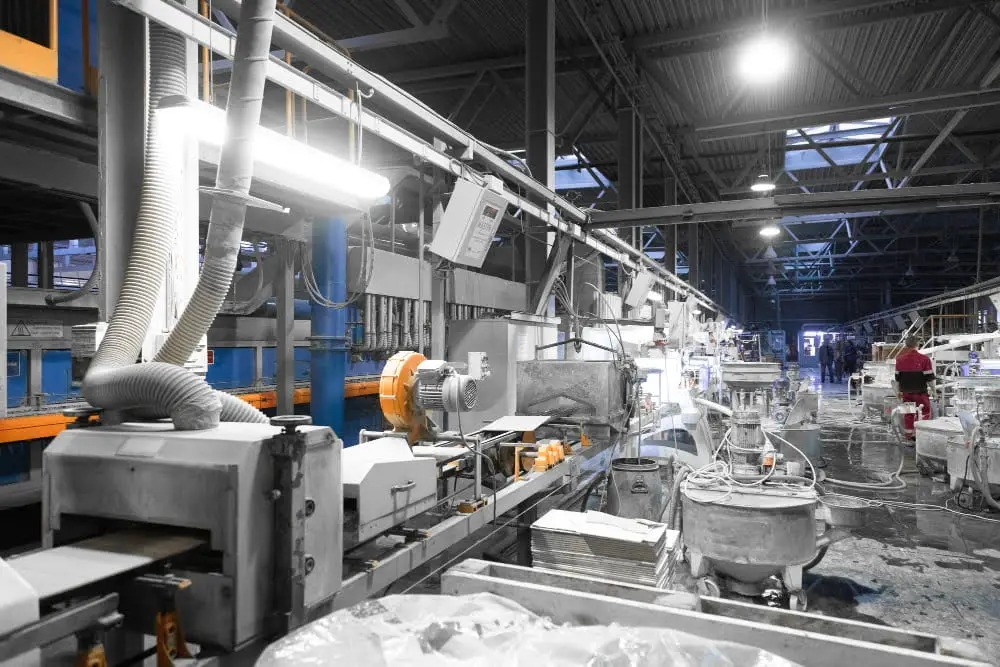
Manufacturing techniques for glass fiber polymer composites (GFRP) have come a long way since their inception. Initially, GFRP was produced using hand lay-up methods that were labor-intensive and time-consuming.
However, with advancements in technology, manufacturers can now produce GFRP using automated processes such as pultrusion and filament winding.
In pultrusion, continuous strands of glass fibers are pulled through a resin bath before being fed into a heated die where the curing process takes place. This method allows for high-volume production of consistent quality products with minimal waste.
Filament winding involves wrapping continuous strands of glass fibers around a rotating mandrel while simultaneously applying resin to create cylindrical shapes such as pipes or tanks. This technique is ideal for producing complex shapes that require strength in multiple directions.
The versatility offered by these manufacturing techniques has made GFRP an attractive option for construction projects ranging from bridges to wind turbine blades. With its lightweight yet durable properties and ability to be molded into various shapes and sizes, it’s no wonder why builders are turning towards this material more frequently than ever before!
Applications in Construction Industry

Glass fiber polymer composites have a wide range of applications in the construction industry. One of their most significant advantages is their versatility, which makes them suitable for use in various structures and environments.
For instance, glass fiber polymer composites are commonly used to reinforce concrete structures such as bridges and buildings. They can also be used to create lightweight panels that are ideal for cladding or roofing systems.
As I continued my research into these materials, I was amazed by the many ways they could be utilized in construction. From creating durable pipes and tanks to designing intricate architectural features like domes and arches – glass fiber polymer composites offer endless possibilities.
What’s more impressive is that these materials can withstand harsh weather conditions without corroding or deteriorating over time. This durability makes them an excellent choice for coastal areas where saltwater corrosion poses a significant challenge to traditional building materials like steel or wood.
It’s clear that glass fiber polymer composites have revolutionized the way we think about construction materials. Their versatility has made them an essential component of modern-day architecture while offering builders new opportunities for innovation and creativity!
Advantages and Limitations of GFRP Materials
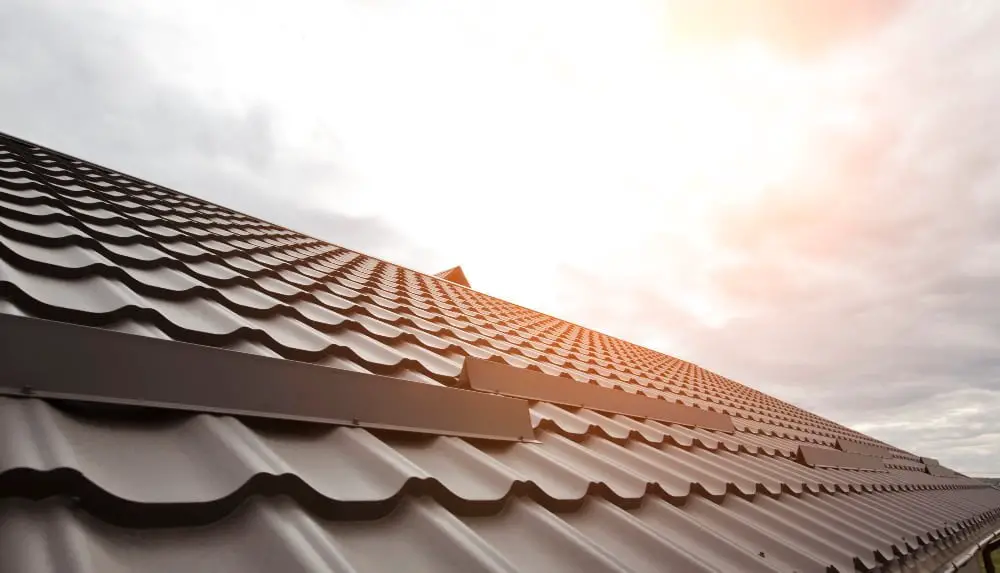
Glass fiber polymer composites, or GFRP materials, have become increasingly popular in the construction industry due to their unique properties. One of the main advantages of GFRP is its high strength-to-weight ratio.
This means that it can withstand heavy loads while remaining lightweight and easy to handle during installation.
Another advantage is its resistance to corrosion and weathering. Unlike traditional building materials such as steel or wood, GFRP does not rust or rot when exposed to moisture or harsh environmental conditions.
This makes it an ideal choice for structures located near bodies of water like bridges and piers.
However, there are also limitations when using GFRP materials in construction projects. One limitation is its relatively high cost compared to other building materials like concrete or steel.
While it has excellent tensile strength (resistance against stretching), it may not be suitable for compression applications where concrete would be a better option.
Despite these limitations, many builders are turning towards glass fiber polymer composites as a versatile alternative material that offers unique benefits over traditional options.
Design Considerations for GFRP Structures
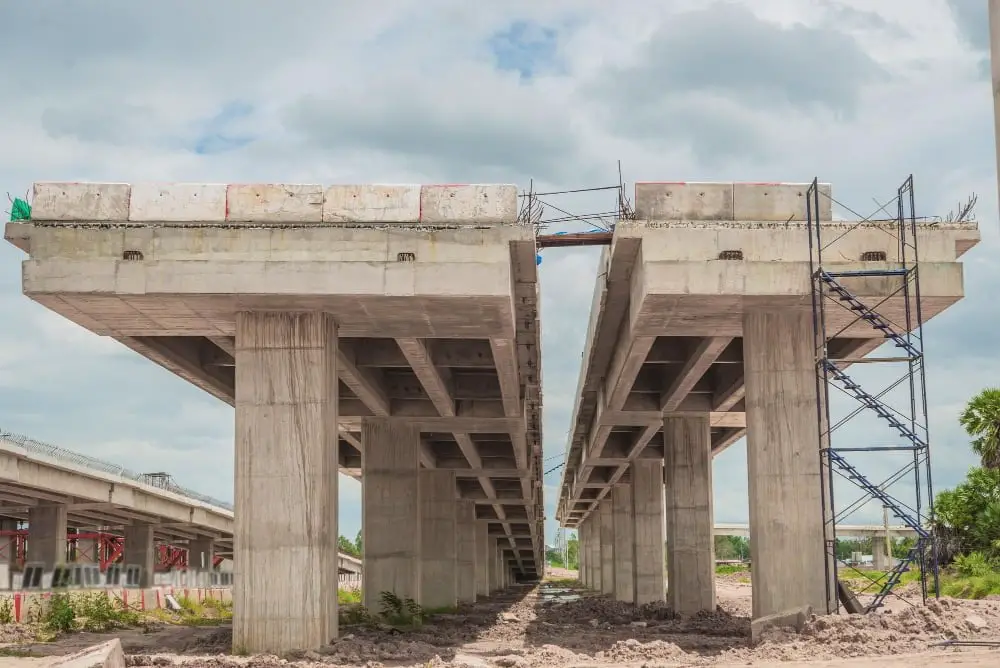
When it comes to designing structures with glass fiber polymer composites (GFRP), there are a few key considerations that builders need to keep in mind. One of the most important is understanding the material’s unique properties and how they can be leveraged for optimal performance.
For example, GFRP has excellent strength-to-weight ratio, making it ideal for applications where weight reduction is critical. This means that designers can create structures that are both strong and lightweight, which opens up new possibilities in terms of design flexibility.
Another consideration when working with GFRP is its resistance to corrosion and weathering. Unlike traditional building materials like steel or wood, GFRP does not rust or rot over time.
This makes it an attractive option for outdoor applications such as bridges or marine structures.
Builders must also consider the manufacturing process when designing with GFRP. The material requires specialized equipment and expertise to produce high-quality components at scale.
However, once these components have been manufactured correctly using proper techniques such as vacuum infusion molding (VIM) or resin transfer molding (RTM), they offer exceptional durability and longevity compared to other materials.
Glass fiber polymer composites offer a range of benefits over traditional construction materials but require careful consideration during design due their unique properties – including strength-to-weight ratio; resistance against corrosion/weathering; manufacturing processes required – all factors which make them versatile options worth considering by any builder looking towards future-proofed construction solutions!
Durability and Maintenance Aspects
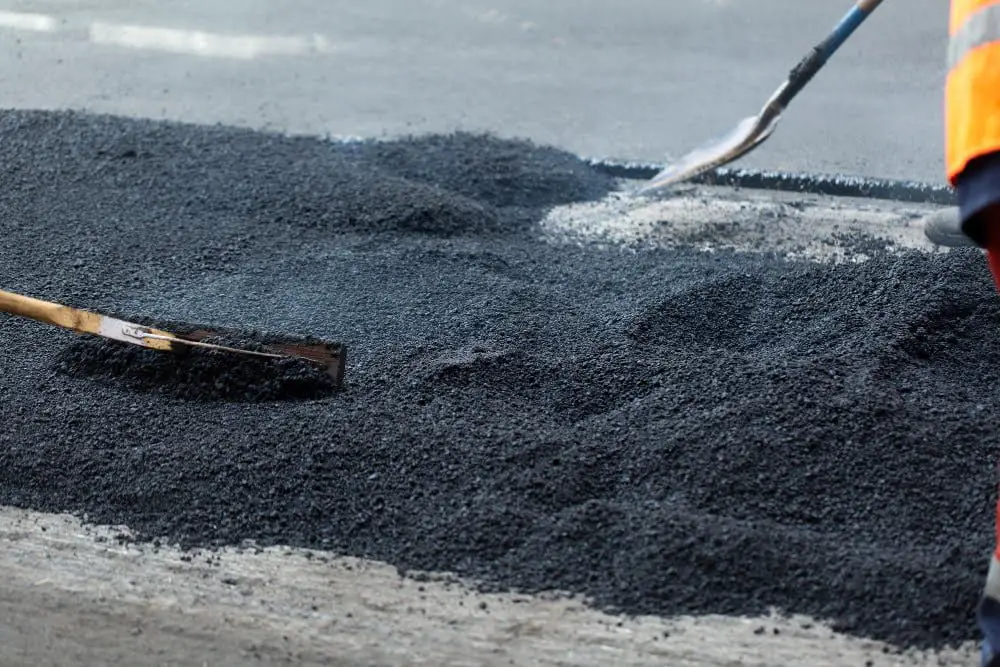
When it comes to construction materials, durability and maintenance are two critical factors that cannot be overlooked. After all, what good is a building if it can’t withstand the test of time or requires constant upkeep? This is where glass fiber polymer composites truly shine.
Thanks to their unique composition, these materials offer exceptional strength and resistance to wear and tear. They’re highly resistant to corrosion from chemicals or moisture, making them ideal for use in harsh environments like coastal areas or industrial settings.
But perhaps one of the most significant advantages of glass fiber polymer composites when it comes to maintenance is their low-maintenance requirements. Unlike traditional building materials like wood or concrete that require regular painting or sealing, these composite materials require little more than occasional cleaning with soap and water.
This means less time spent on upkeep for builders and property owners alike – allowing them more time (and money) for other important aspects of construction projects. With such impressive durability combined with minimal maintenance needs, there’s no doubt that glass fiber polymer composites are an excellent choice for any builder looking towards the future!
Case Studies On GFRP Composite Projects
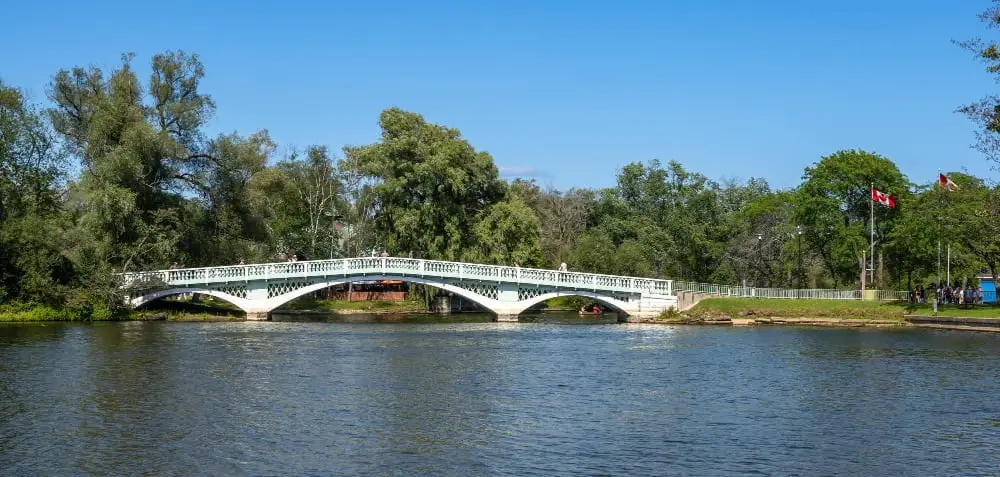
One of the best ways to understand the potential of glass fiber polymer composites is by looking at real-life examples. Over the years, there have been several successful projects that have utilized GFRP composites in innovative ways.
One such project was the rehabilitation of a bridge in Ontario, Canada. The bridge had suffered significant damage due to corrosion and needed extensive repairs.
Instead of using traditional materials like steel or concrete, engineers opted for GFRP composite reinforcement bars and plates.
The use of these materials not only provided superior resistance against corrosion but also reduced weight significantly compared to traditional alternatives. This allowed for easier transportation and installation on-site while minimizing disruption to traffic flow during construction.
Another notable example is a pedestrian walkway built over an active railway line in Australia using GFRP composite beams as support structures. The lightweight nature and high strength-to-weight ratio made it possible for engineers to design longer spans without compromising safety or stability.
These case studies demonstrate how glass fiber polymer composites can be used effectively across various applications within construction projects – from bridges and tunnels to buildings’ facades – providing cost-effective solutions with long-term durability benefits over conventional building materials like steel or concrete.
Evolution of Glass Fiber Polymer Composites in Construction
Glass fiber polymer composites (GFRP) have come a long way in revolutionizing the construction industry. Initially developed for aerospace applications, GFRP materials quickly found their place in various construction sectors due to their exceptional properties and versatility.
Over the years, advancements in manufacturing techniques and material formulations have further enhanced the performance of GFRP composites, making them an attractive alternative to traditional construction materials.
In the early stages of development, GFRP was primarily used as reinforcement for concrete structures. The high strength-to-weight ratio of glass fibers made it an ideal choice for reinforcing concrete elements such as beams and columns.
This allowed engineers to design more efficient structures that could withstand higher loads while reducing overall weight.
As research continued, new applications emerged where GFRP offered significant advantages over conventional materials like steel or wood. Today, we see glass fiber polymer composites being used extensively in infrastructure projects such as bridges and tunnels due to their corrosion resistance properties.
Moreover, architects are increasingly incorporating GFRP into building facades because they offer greater design flexibility compared to traditional cladding systems while maintaining structural integrity.
The evolution of glass fiber polymer composites has also led to innovations like pultruded profiles which are widely used for window frames and curtain walls due to their excellent thermal insulation properties along with durability against weathering effects.
Environmental Impacts and Sustainability of GFRP Materials
One key advantage is their lightweight nature, which reduces transportation energy requirements and associated carbon emissions during delivery to the construction site. GFRP composites have a longer lifespan compared to traditional materials like steel or wood, resulting in reduced waste generation over time.
Another significant environmental benefit of GFRP materials is their corrosion resistance. Unlike steel reinforcements that can corrode when exposed to moisture or chemicals, GFRP composites are highly resistant to corrosion.
This property not only extends the service life of structures but also minimizes maintenance needs and reduces the use of chemical treatments for protection against corrosion.
Furthermore, using GFRP in construction helps conserve natural resources as it requires less raw material extraction compared to traditional alternatives such as concrete or steel. The production process for glass fibers involves melting silica sand at high temperatures instead of extracting iron ore or limestone required for manufacturing conventional building materials.
In terms of sustainability, GFRP composites can be recycled at the end-of-life stage by separating them from other components used in construction applications. Recycling allows these composite materials to be reused rather than ending up in landfills—a practice that aligns with circular economy principles and contributes positively towards reducing waste generation.
Codes and Standards for Using GFRP in Construction
These regulations provide guidelines for design, manufacturing, installation, and inspection processes to ensure that GFRP materials meet specific performance requirements.
In many countries, organizations such as ASTM International (American Society for Testing and Materials), ACI (American Concrete Institute), ISO (International Organization for Standardization), and CSA Group develop codes and standards specifically tailored to GFRP applications. These documents outline the minimum requirements that must be met when using GFRP materials in various construction projects.
The codes cover a wide range of aspects related to GFRP composites including material properties, structural design considerations, fabrication techniques, quality control measures during manufacturing processes like pultrusion or filament winding methods. They also address issues such as fire resistance ratings or corrosion protection strategies when using these materials.
Adhering to these codes ensures uniformity across different projects while guaranteeing safety levels are maintained throughout the lifespan of structures built with GFRP composites. Compliance with established standards not only enhances confidence among designers but also provides assurance to regulatory authorities responsible for approving building permits.
It is essential for architects/engineers involved in designing structures with glass fiber polymer composite components familiarize themselves with relevant local building codes before incorporating them into their designs.
Cost-Benefit Analysis of GFRP Versus Traditional Materials
Glass Fiber Polymer Composites (GFRP) have gained popularity due to their unique properties and advantages over traditional materials like steel or concrete.
One significant advantage of GFRP composites is their lightweight nature. This characteristic reduces transportation costs, simplifies installation processes, and requires less labor compared to heavier traditional materials.
The lighter weight of GFRP can result in reduced foundation requirements for structures.
Another benefit is the high strength-to-weight ratio offered by GFRP composites. They possess excellent tensile strength while being significantly lighter than steel or concrete counterparts.
This property allows for longer spans between supports in structural applications without compromising safety or performance.
In terms of durability, GFRP composites exhibit exceptional resistance against corrosion caused by moisture exposure or chemical agents commonly found in construction environments. Unlike steel reinforcements that can rust over time leading to structural degradation, glass fiber polymer composites remain unaffected by these corrosive elements.
Although initial material costs may be higher compared to traditional alternatives such as steel reinforcement bars or concrete forms; when considering long-term maintenance expenses associated with corrosion prevention measures required for conventional materials – such as coatings and repairs – using GFRPs becomes a more cost-effective solution over time.
Furthermore, the versatility of manufacturing processes enables customization options with complex shapes that are difficult or expensive using other methods/materials—reducing waste during production while optimizing design possibilities tailored specifically for each project’s needs.
Technological Advancements in GFRP Composite Manufacturing
These advancements have led to improvements in both the quality and efficiency of GFRP production.
One notable advancement is the development of automated manufacturing processes. Automated systems allow for precise control over various parameters such as fiber alignment, resin distribution, and curing conditions.
This ensures consistent quality throughout the composite material, resulting in enhanced structural performance.
Another breakthrough is the use of advanced modeling and simulation techniques during product design and development stages. Computer-aided design (CAD) software enables engineers to create complex geometries with optimized fiber placement, ensuring maximum strength while minimizing material usage.
Furthermore, innovations like robotic arm technology have revolutionized GFRP fabrication by enabling continuous filament winding processes at high speeds with improved accuracy. This has significantly increased productivity while maintaining excellent mechanical properties.
Researchers are exploring new methods for incorporating functional additives into GFRP composites during manufacturing processes. By adding nanoparticles or other materials with specific properties into polymer matrices or coatings on glass fibers themselves, it becomes possible to enhance characteristics such as fire resistance or self-healing capabilities.
Overall these technological advancements continue to push boundaries in GFRP composite manufacturing by improving efficiency, precision control over production variables leading to higher-quality products that meet stringent industry standards.
FAQ
Is fiberglass a polymer or composite?
Fiberglass is a composite material, specifically a fiber-reinforced polymer with glass fibers embedded within it.
What is glass fiber reinforced polymer used for?
Glass fiber reinforced polymer, often abbreviated as GRP, is predominantly used to enhance stability, durability, and resistance in industrial and commercial building structures, with its strength, adaptability, and versatility in molding into various shapes, styles, and sizes.
What is an example of a glass fiber reinforced polymer?
A common example of a glass fiber reinforced polymer (GRP) is E-glass, an alumino-borosilicate glass, with E-CR-glass being frequently used in applications requiring high acid corrosion resistance.
How is the manufacturing process of glass fiber reinforced polymers conducted?
The manufacturing process of glass fiber reinforced polymers involves melting glass and drawing it into fibers, combining it with polymer resin, and molding it into the desired shape.
What are the advantages and possible limitations of using glass fiber reinforced polymers in construction?
The use of glass fiber reinforced polymers in construction offers benefits such as high strength-to-weight ratio, corrosion resistance, and design flexibility, but their high initial cost and susceptibility to UV radiation and high temperatures present potential limitations.
Can the properties of glass fiber reinforced polymers be tailored and how does it affect their application in different construction scenarios?
Yes, the properties of Glass Fiber Reinforced Polymers (GFRP) can be tailored by modifying fiber orientation, matrix elements, and the manufacturing process, enabling its use in diverse construction scenarios such as bridge decks, reinforcement bars in concrete, and seismic retrofitting due to its high strength-to-weight ratio, corrosion resistance, and design versatility.
Recap