This article provides a clear explanation of what Fiber Reinforced Polymers are, how they are produced, and their critical role in modern construction.
Key takeaways:
- FRP combines a polymer matrix with fiber reinforcement.
- Different fibers (glass, carbon, aramid, basalt, natural) have specific advantages.
- Manufacturing processes include pultrusion, filament winding, hand lay-up, injection molding, and RTM.
- FRP has applications in retrofitting, corrosive environments, and unique designs.
- Future trends in FRP technology include nanotechnology, eco-friendly resins, self-healing materials, hybrid composites, 3D printing, smart systems, and modular construction.
DEFINITION OF FIBER-REINFORCED POLYMER (FRP)
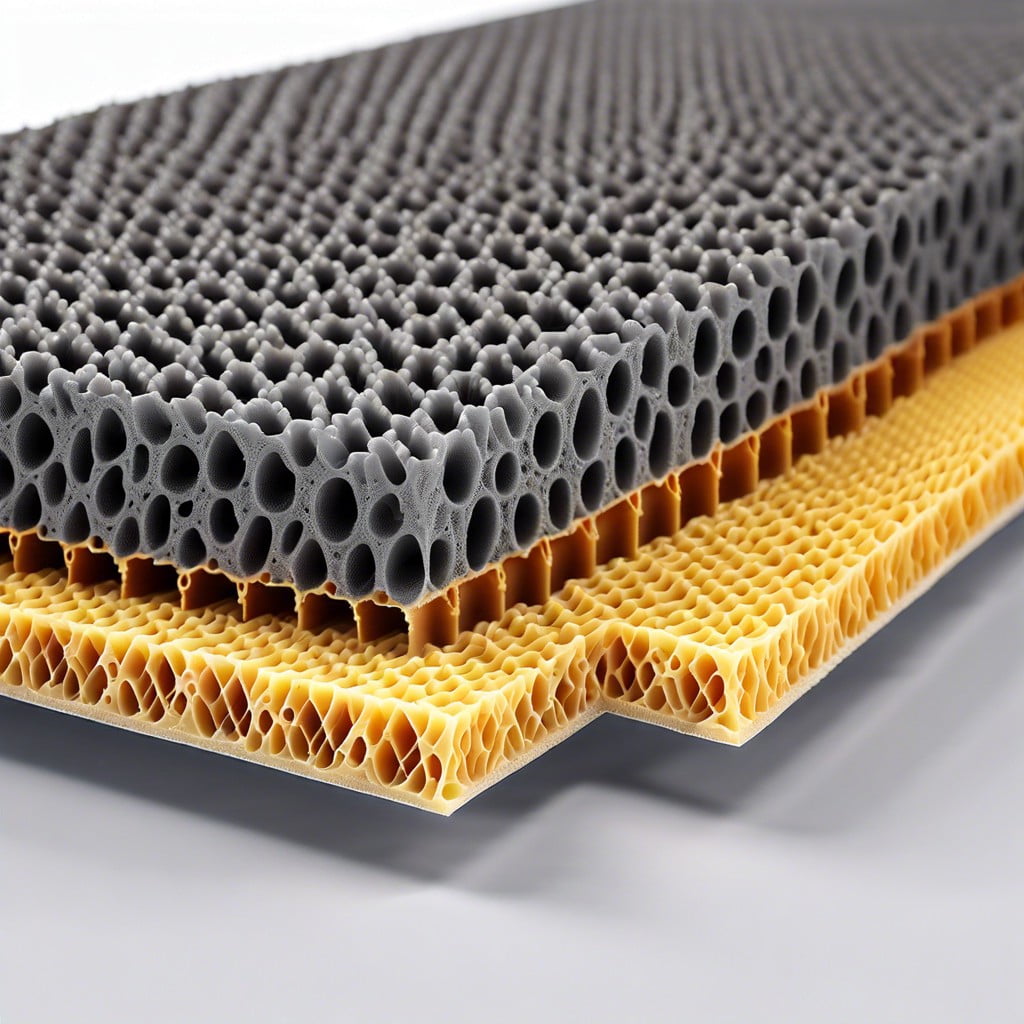
Fiber-reinforced polymer, commonly known as FRP, combines a polymer matrix with a fiber reinforcement. The polymer, which might be an epoxy, vinyl ester, or polyester thermosetting plastic, serves as a glue that binds together the reinforcing fibers. These fibers, generally made of glass, carbon, or aramid, are strong and stiff, providing the primary load-bearing capability.
By embedding the fibers in the polymer matrix, the resulting material leverages the strength and elasticity of the fibers while the polymer protects and shares the stresses between fibers, resisting cracks and fractures. This synergy gives FRP enhanced mechanical properties, making it a high-strength, lightweight alternative to conventional materials like steel or concrete.
FRP is customizable; different fiber orientations allow for tailored strength characteristics to suit specific applications, whether that’s high tensile strength, corrosion resistance, or durability. This flexibility makes FRP a versatile choice for construction endeavors where material performance can be matched to the unique demands of the project at hand.
TYPES OF FIBERS USED IN FRP
Fibers are the backbone of FRP, providing strength and flexibility to the polymer matrix. Different fibers have distinct properties that make them suitable for various applications.
1. Glass Fibers: These are the most common, offering a good balance between cost and performance. They increase the material’s strength and are corrosion-resistant.
2. Carbon Fibers: Known for their high stiffness and strength, carbon fibers are used when lightweight and superior mechanical properties are essential. They’re more expensive but provide a higher strength-to-weight ratio.
3. Aramid Fibers: Notable for their toughness and resistance to impact, aramid fibers such as Kevlar® are used in applications where durability is critical.
4. Basalt Fibers: Emerging as an environmentally friendly option, basalt fibers are made from volcanic rock. They exhibit good chemical resistance and mechanical properties.
5. Natural Fibers: Sourced from plants or animals, such as flax, jute, and wool, these fibers are sustainable and biodegradable, albeit with less structural strength compared to synthetic options.
Each of these fibers, when embedded in a polymer matrix, serves to address specific structural requirements and brings unique advantages to construction materials.
MANUFACTURING PROCESSES OF FRP
The creation of fiber-reinforced polymers involves intricately combining fibers with a polymer matrix. This unification bestows the final material with enhanced strength and durability characteristics.
Key manufacturing processes include:
- Pultrusion: Here, fibers are pulled through a resin bath and then through a heated die where they become set into a strong, continuous composite profile. It’s similar to extrusion, but instead of pushing the material out, it’s pulled.
- Filament Winding: This technique involves winding filaments under tension over a rotating mandrel. Resin is applied during or after this winding process. It’s particularly suitable for making tubes, tanks, and cylindrical shapes.
- Hand Lay-Up: One of the simplest methods, the hand lay-up involves placing the fiber reinforcements in a mold and manually applying the resin to build up the FRP layer by layer. It allows for great flexibility in shapes and is ideal for custom projects or low-volume production.
- Injection Molding: Short fibers are mixed with the polymer before it’s injected into a heated mold. This method is fast, precise, and perfect for high-volume manufacturing of small to medium complex parts.
- Resin Transfer Molding (RTM): Here, fibers are placed into a closed mold cavity, then injected with resin. RTM is known for producing consistent, high-quality products that have two smooth finished surfaces.
By choosing the appropriate manufacturing process, builders and engineers can tailor the properties of FRP to meet the specific demands of their construction projects.
APPLICATIONS AND LIMITATIONS OF FRP IN CONSTRUCTION
Fiber-reinforced polymers, known for their high strength-to-weight ratio, have revolutionized the construction industry. In the field of civil engineering, their lightweight nature aids in the ease of installation, especially for applications high above the ground or in hard-to-reach places. For instance, FRP is frequently used in the retrofitting of structures, where it is wrapped around columns or beams to enhance their load-bearing capacity without substantial weight increase.
FRP materials are also notable for their corrosion resistance, making them ideal for use in harsh environments such as coastal regions or chemical plants where traditional materials might degrade quickly. Moreover, the flexibility of FRP finds applications in creating uniquely shaped elements or in slender structures like pedestrian bridges, thanks to its ability to be molded into intricate designs without sacrificing durability.
Despite these advantages, the use of FRP is not without its limitations. Its initial cost can be higher than traditional materials like steel and concrete, which may be a deterrent for some projects. Additionally, while FRP resists corrosion, it can be sensitive to prolonged UV exposure and extreme temperatures. In fire scenarios, its performance is a concern, requiring additional treatments or design considerations to ensure safety.
The versatility of FRP continues to expand as the industry seeks new solutions for more sustainable and resilient infrastructure. Its current applications serve as a testament to its potential, tempered by mindful consideration of its limitations when planning construction projects.
FUTURE TRENDS IN FRP TECHNOLOGY
Advancements in FRP technology are paving the way for smarter, stronger, and more sustainable construction materials. Here are some of the anticipated trends:
- 1. Nanotechnology Integration: The inclusion of nano-sized particles in FRP can dramatically enhance properties like strength, thermal behavior, and chemical resistance.
- 2. Eco-friendly Resins: Development of bio-based resins aims to reduce the environmental impact of traditional FRP manufacturing processes.
- 3. Self-Healing Materials: FRPs that can repair small cracks or damages on their own, thereby extending the life of the structure, are under research.
- 4. Hybrid Composites: Mixing different types of fibers in a single FRP composite can yield optimized materials tailored for specific applications.
- 5. 3D Printing of FRP: 3D printing technologies are being adapted to create complex FRP structures, offering new design possibilities and reducing waste.
- 6. Smart FRP Systems: Embedding sensors within FRPs could enable real-time monitoring of the health of structures, alerting for maintenance needs.
- 7. FRP in Modular Construction: The use of FRP in prefabricated modular units is expected to reduce construction times and costs while increasing efficiency.
FAQ
What are the 4 main types of FRP?
The four main types of Fiber-Reinforced Polymer (FRP) are glass, carbon, natural, and aramid.
Is FRP stronger than steel?
While the strength-to-weight ratio of Glass Fiber Reinforced Polymer (FRP) is superior to that of steel, it falls short in stiffness-to-weight ratios, needing thickness adjustments to meet certain requirements.
What is FRP used for?
FRP, or Fiber Reinforced Polymer, is predominantly utilized in construction for creating sturdy, scratch-resistant, high impact-resistant walls and surfaces in diverse settings such as schools, hospitals, recreational facilities, and industrial locations.
Is FRP good material?
Yes, Fiberglass-Reinforced Polymer (FRP) is a good material for construction due to its strength, lightweight nature, and corrosion-resistant properties.
How does the manufacturing process impact the properties of FRP?
The manufacturing process of Fiber Reinforced Polymer (FRP) significantly determines its mechanical properties by affecting the fiber-matrix interface, fiber alignment, and overall structure, impacting the final product’s strength, stiffness, and durability.
What features make FRP an ideal choice for construction reinforcement?
FRP, or Fiber-Reinforced Polymer, is ideal for construction reinforcement due to its high strength-to-weight ratio, corrosion resistance, and flexibility, allowing it to enhance structural integrity without additional weight or susceptibility to environmental damage.
What are the potential drawbacks of using FRP in construction projects?
The potential drawbacks of using Fiber Reinforced Polymer (FRP) in construction projects include relatively high material costs, susceptibility to UV damage, limited fire resistance, and the need for specialized training for installation.
Recap