Discover how fiber-reinforced polymers are transforming the construction industry. Read more to learn about their unmatched strength and durability.
As a kid, I used to love playing with Legos. I would spend hours building towering structures, intricate bridges, and even entire cities out of those colorful little blocks.
But as much as I loved my Lego creations, there was always one problem: they were fragile. One wrong move and the whole thing would come crashing down.
Fast forward to today, and it’s clear that the construction industry faces a similar challenge. We build massive skyscrapers, bridges that span entire oceans, and tunnels that burrow deep into the earth – but how do we ensure that these structures are strong enough to withstand the forces of nature?
Enter fiber-reinforced polymers (FRPs). These materials are like the superheroes of construction – they’re lightweight yet incredibly strong, flexible yet durable enough to stand up against earthquakes and hurricanes.
In this blog post, we’ll explore how FRPs are revolutionizing the way we build our world’s infrastructure – from reducing construction time to increasing safety on job sites. So strap in and get ready for a wild ride through the exciting world of FRPs!
FRP: An Overview
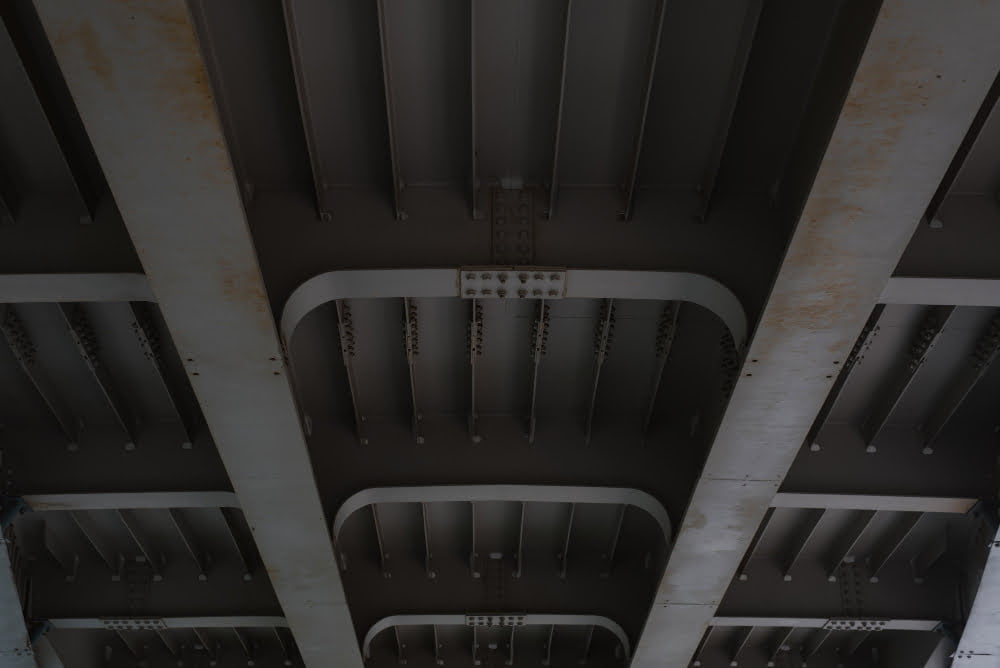
FRPs, or fiber-reinforced polymers, are composite materials made up of a polymer matrix reinforced with fibers. These fibers can be made from a variety of materials such as glass, carbon, or aramid.
The resulting material is incredibly strong and lightweight – making it an ideal choice for construction projects where weight is a concern.
But what makes FRPs so special? Well, unlike traditional building materials like steel and concrete which have been used for centuries in construction projects around the world – FRPs offer several advantages that make them stand out from the crowd.
For one thing, they’re incredibly durable. Because they’re made up of multiple layers of reinforcing fibers embedded in resin matrices – these composites can withstand high stress levels without breaking down over time like other building materials might do under similar conditions.
Additionally, because FRP structures are lighter than their steel counterparts- this means that less energy is required to transport them to job sites; reducing transportation costs while also minimizing environmental impact during shipping processes!
In short: Fiber-Reinforced Polymers (FRP) represent an exciting new frontier in modern-day engineering & architecture- offering unparalleled strength-to-weight ratios along with superior durability compared against conventional building methods!
Advantages of FRPs
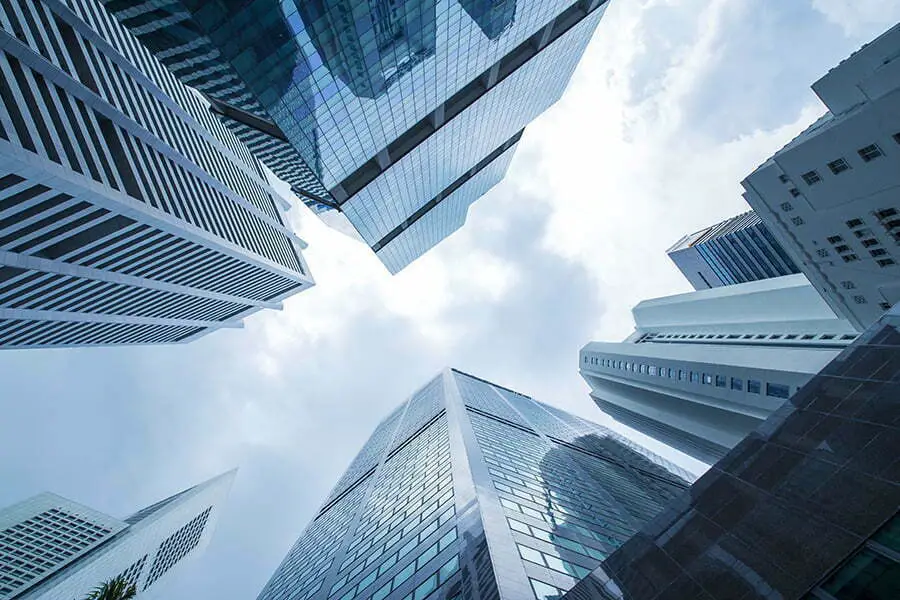
One of the biggest advantages of fiber-reinforced polymers (FRPs) is their incredible strength-to-weight ratio. Just like how Superman can lift a car with ease, FRPs are able to support heavy loads without adding unnecessary weight to a structure.
This means that architects and engineers can design buildings and bridges that are taller, longer, and more complex than ever before – all while using less material.
But it’s not just about size – FRPs also offer increased durability compared to traditional building materials like steel or concrete. Think back to my Lego creations as a kid: if I had built them out of FRP blocks instead of plastic ones, they would have been much stronger and less likely to break apart at the slightest touch.
This increased durability translates into real-world benefits for construction projects. For example, structures made with FRP reinforcements require less maintenance over time because they’re resistant to corrosion from water or chemicals in the environment.
And since these materials don’t rust or degrade over time like steel does, there’s no need for costly repairs down the line.
It’s clear that fiber-reinforced polymers have some serious advantages when it comes to revolutionizing the construction industry – whether you’re building towering skyscrapers or intricate bridges spanning across rivers and valleys alike!
Types of Fiber Reinforcements
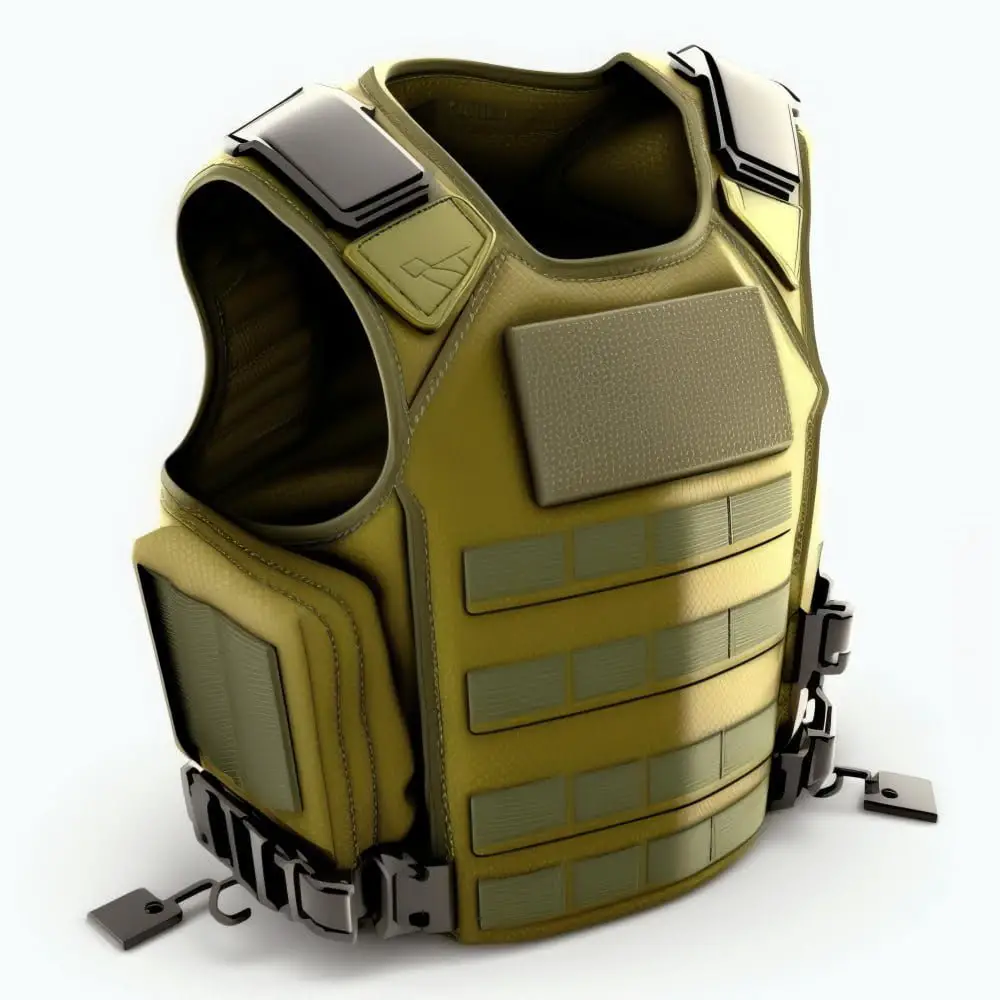
Just like how superheroes have different powers, fiber-reinforced polymers (FRPs) come in various types depending on the type of fibers used for reinforcement. The most commonly used fibers are glass, carbon, and aramid.
Glass FRPs are made by weaving together thin strands of glass into a fabric-like material. They’re affordable and easy to work with but aren’t as strong as other types of FRPs.
Carbon FRPs use carbon fibers that are incredibly strong yet lightweight. These materials can withstand high temperatures and harsh environments making them ideal for aerospace applications.
Aramid FRP is another popular choice due to its excellent resistance against impact damage and fatigue loading conditions. It’s often used in bulletproof vests or helmets because it has a high strength-to-weight ratio compared to other materials.
Each type of fiber reinforcement has its own unique properties that make it suitable for specific applications within the construction industry. By understanding these differences, engineers can choose the right material based on their project requirements – just like how superheroes pick their weapons before going out into battle!
Applications in Construction
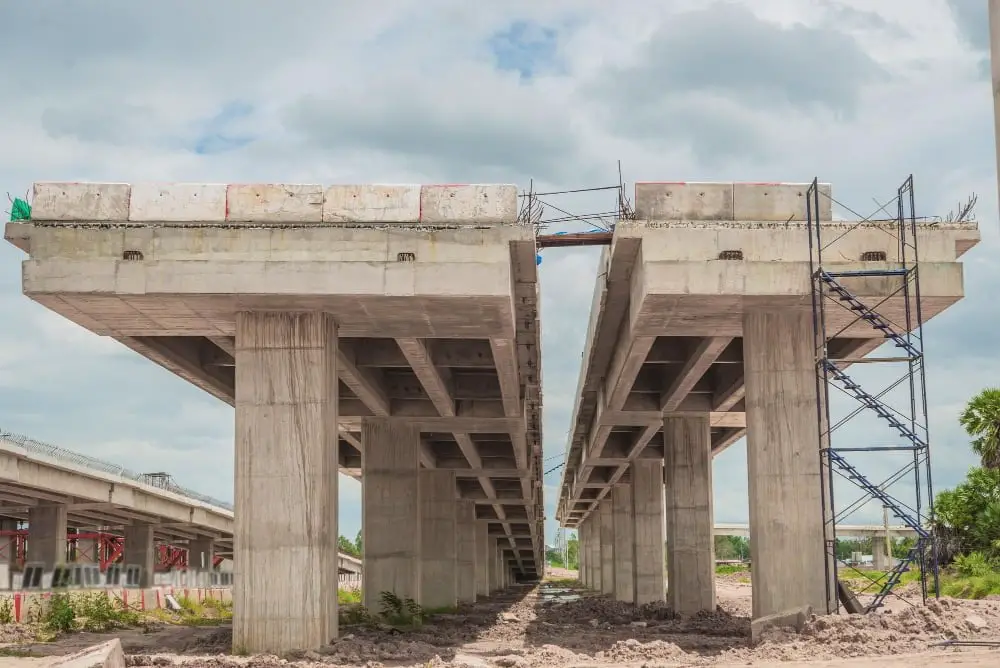
FRPs have a wide range of applications in the construction industry. One of the most common uses is in reinforcing concrete structures such as bridges, parking garages, and buildings.
By adding FRP bars or sheets to concrete elements, engineers can increase their strength and durability while reducing their weight.
But that’s not all – FRPs are also being used to create entirely new types of structures that were previously impossible with traditional materials. For example, researchers at MIT have developed a 3D printing process using carbon fiber-reinforced polymers (CFRPs) to create complex shapes for architectural designs.
In addition to improving structural performance and enabling innovative designs, FRPs also offer several other benefits for construction projects. They’re easy to install compared with traditional reinforcement methods like steel rebar or post-tensioning cables since they don’t require heavy machinery or specialized labor skills.
Moreover, because they’re lightweight yet strong enough even under extreme conditions like earthquakes and hurricanes; this makes them ideal for use in areas prone to natural disasters where safety is paramount on job sites.
Overall it’s clear that Fiber-Reinforced Polymers are unleashing an exciting new era in the world of construction engineering – one where we can build stronger more durable infrastructure faster than ever before!
Durability and Maintenance
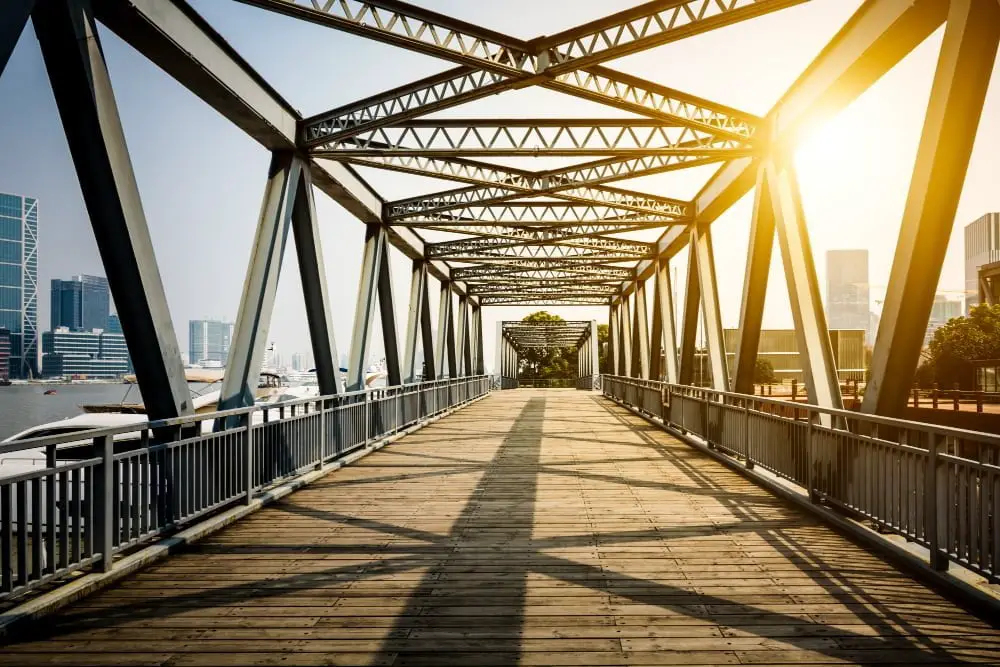
Just like how superheroes need to maintain their strength and durability, FRPs also require proper maintenance to ensure they continue to perform at their best. Fortunately, these materials are incredibly durable and require minimal upkeep compared to traditional construction materials.
One of the key advantages of FRPs is that they’re resistant to corrosion – a common problem with steel structures. This means that bridges, tunnels, and other infrastructure built with FRPs can last much longer without needing costly repairs or replacements.
Because FRP structures are lightweight yet strong enough for heavy loads, they put less stress on the surrounding environment than heavier traditional building materials. This reduces wear-and-tear on roads and other infrastructure around construction sites.
The durability of fiber-reinforced polymers makes them an attractive option for long-term investments in construction projects. With proper maintenance practices in place (such as regular inspections), these superhero-like materials can continue protecting our world’s infrastructure for years – even decades – into the future!
Cost-Effectiveness Analysis
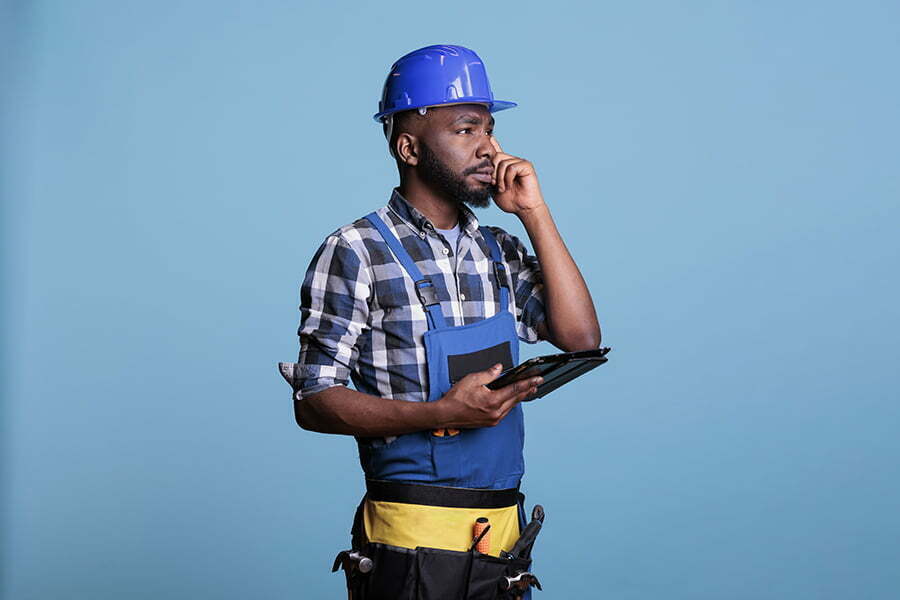
When it comes to building structures that can withstand the test of time, cost is always a major consideration. That’s where fiber-reinforced polymers (FRPs) come in – not only are they incredibly strong and durable, but they’re also cost-effective.
In fact, studies have shown that FRP materials can actually save money over traditional construction methods. For example, using FRP reinforcement instead of steel rebar in concrete structures can reduce material costs by up to 30%.
Because FRPs are lightweight and easy to install compared to traditional materials like steel or concrete, labor costs may also be reduced.
But it’s not just about upfront savings – there are long-term benefits as well. Because FRPs don’t corrode like steel does over time due to exposure from moisture or chemicals present in the environment; this means less maintenance is required for these types of structures which translates into more significant savings down the line.
Overall when considering all factors such as durability and longevity along with initial installation costs – Fiber-Reinforced Polymers prove themselves an excellent choice for any project looking at both short term gains as well as long term sustainability goals!
Environmental Impact
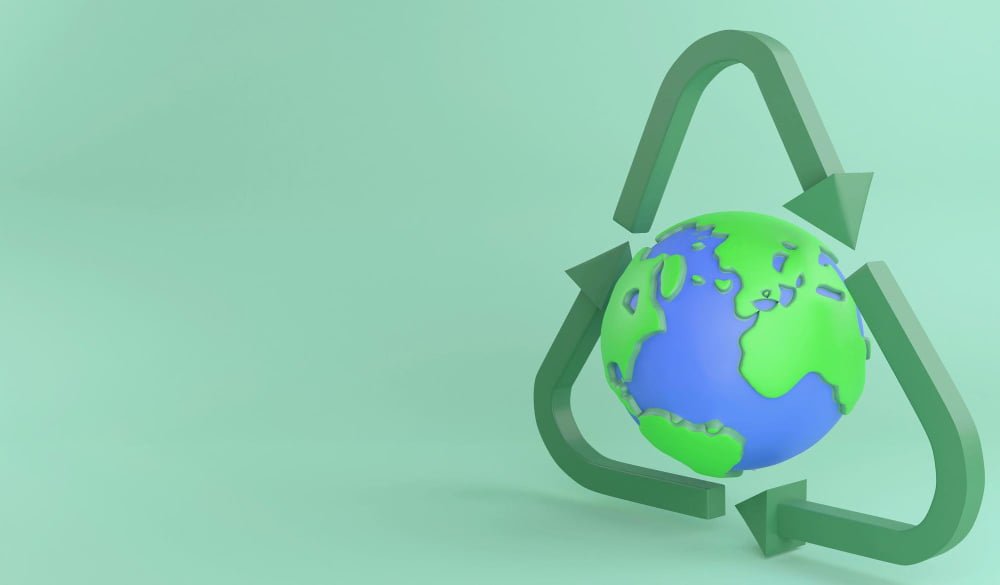
But it’s not just their strength and durability that make FRPs so exciting – they also have a significantly lower environmental impact than traditional construction materials. As we become more aware of the impact our actions have on the planet, finding sustainable solutions for building is becoming increasingly important.
FRPs are made from composite materials that can be recycled at the end of their lifespan, reducing waste in landfills. Because they’re lightweight and easy to transport, less energy is required to move them around during construction.
As I watched my Lego creations crumble as a child, I never would have guessed that one day I’d be writing about how fiber-reinforced polymers could help save our planet. But here we are – with these innovative materials poised to revolutionize not only how we build but also how sustainably we do it.
Case Studies & Examples
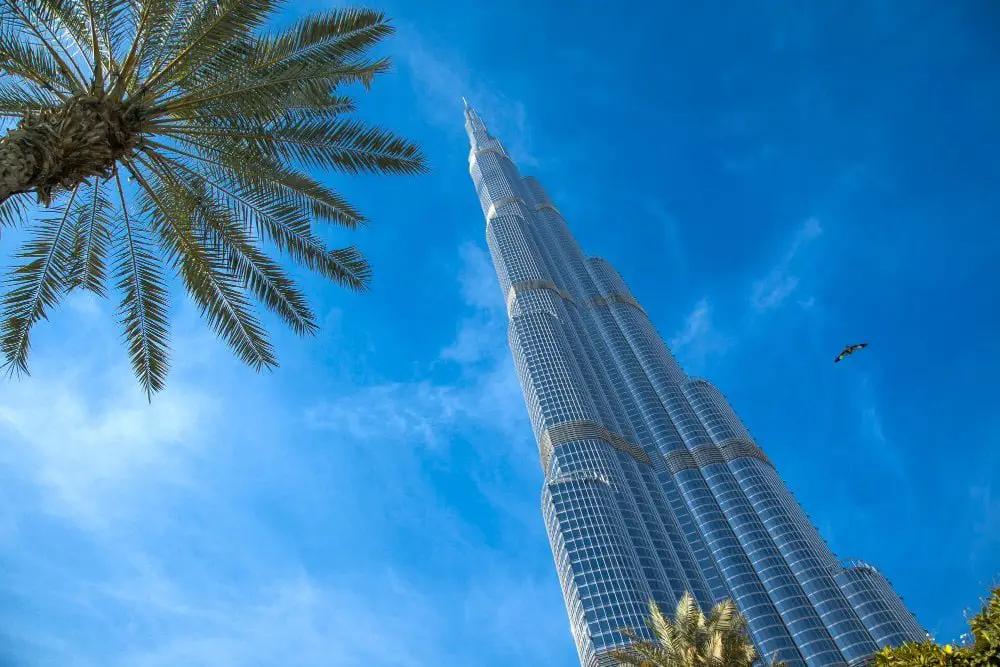
One of the most exciting things about fiber-reinforced polymers (FRPs) is that they’re already being used in a wide range of construction projects around the world. Let’s take a look at some case studies and examples to see just how powerful these materials can be.
In Japan, engineers have been using FRP composites to reinforce bridges for over 20 years. One notable example is the Akashi Kaikyo Bridge, which spans nearly two miles across the Akashi Strait.
This bridge was built with more than 100,000 tons of steel and concrete – but it also features over 1,700 FRP cables that help support its weight.
Another impressive use of FRPs can be found in Dubai’s Burj Khalifa – currently the tallest building in the world. The tower stands at an incredible height of 828 meters (2,716 feet), but what many people don’t realize is that it also contains thousands of square meters worth of composite materials made from carbon fibers and epoxy resins.
These are just two examples among many others where fiber-reinforced polymers have been successfully implemented into large-scale construction projects worldwide. As we continue to explore new ways to harness their power and potential applications within our industry – one thing remains clear: Fiber-Reinforced Polymers are here to stay!
Recap