Learn how heat-resistant polymers can maintain structural integrity in extreme temperatures with our informative article written by a construction industry expert.
As a construction worker, I’ve seen firsthand the impact of extreme temperatures on building materials. From scorching hot summers to freezing cold winters, these conditions can cause serious damage to structures if they’re not built with the right materials.
That’s why I’m excited to share with you today about heat-resistant polymers – a game-changing material that’s revolutionizing the construction industry.
I remember one particularly scorching summer day when I was working on a project in Arizona. The temperature had climbed well over 100 degrees and we were struggling to keep cool under our hard hats and safety gear.
As we worked, I couldn’t help but wonder how the building materials we were using would hold up under such intense heat.
That’s when my colleague pointed out something fascinating – the polymer-based insulation we were installing was specifically designed for extreme temperatures like this one. It could withstand high heat without melting or losing its shape, ensuring that the structure would remain intact even in these challenging conditions.
Since then, I’ve become fascinated by these innovative materials and their potential to transform how we build structures in all kinds of environments – from desert climates like Arizona to frigid regions like Alaska.
So let’s dive into what makes heat-resistant polymers so special and how they’re helping ensure structural integrity even in extreme temperatures!
Key takeaways:
- Heat-resistant polymers can withstand high temperatures without losing shape.
- Different polymer types (polyimide, PPO) offer unique properties and applications.
- These polymers achieve thermal stability through chemical cross-linking and additives.
- Rigorous testing methods and standards ensure materials can withstand extreme conditions.
- Heat-resistant polymers are being used in pipelines, buildings, and industrial applications.
Introduction to Heat-Resistant Polymers
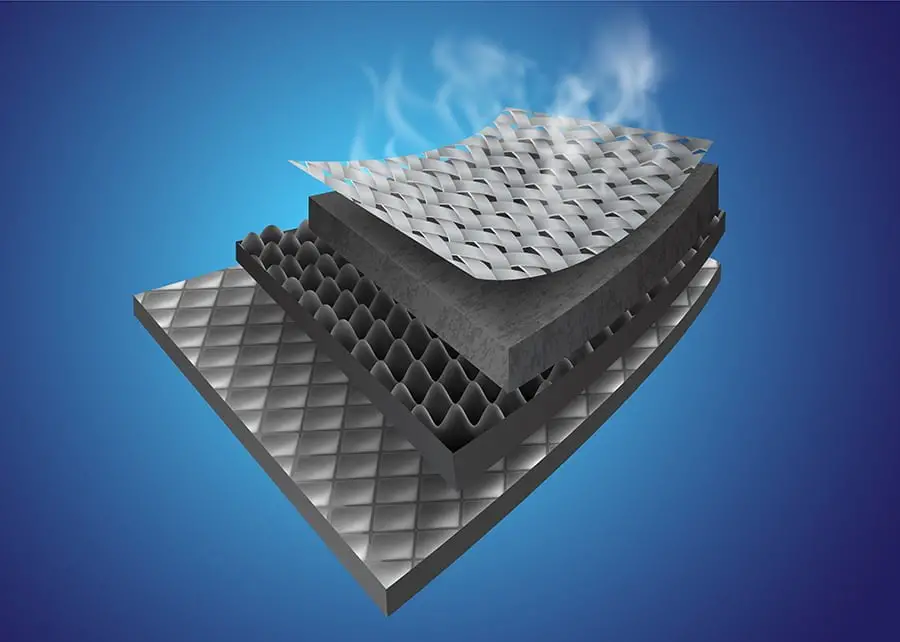
Heat-resistant polymers are a type of material that can withstand high temperatures without losing their shape or structural integrity. They’re made from long chains of molecules called polymers, which are designed to resist heat and other environmental factors that can cause damage to traditional building materials.
As my colleague explained on that hot summer day in Arizona, these innovative materials have the potential to revolutionize the construction industry by providing a solution for buildings in extreme temperature environments. Heat-resistant polymers offer many benefits over traditional building materials like steel and concrete, including increased durability and resistance to corrosion.
Since then, I’ve been researching more about heat-resistant polymers and how they work. These advanced materials come in many different forms – from insulation panels used inside walls or roofs to coatings applied directly onto surfaces like pipes or tanks.
One thing is clear: with climate change causing more frequent extreme weather events around the world, it’s becoming increasingly important for builders and engineers alike to consider using heat-resistant polymer-based solutions when designing structures meant for harsh environments. In this article we will explore some examples of how these innovative products are being used today!
Polymer Types and Applications
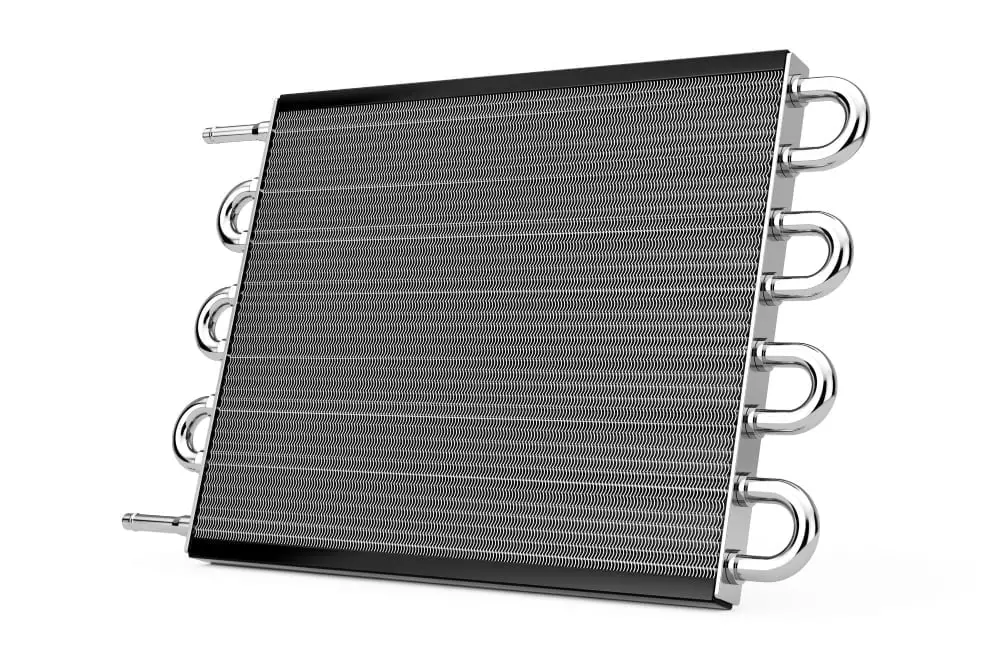
Heat-resistant polymers are a type of synthetic material that can withstand high temperatures without losing their shape or structural integrity. There are several types of heat-resistant polymers, each with its own unique properties and applications.
One common type is polyimide, which is often used in aerospace and electronics industries due to its excellent thermal stability. Another popular option is polyphenylene oxide (PPO), which has good dimensional stability at high temperatures and can be found in automotive parts such as radiator end tanks.
As I continued to learn more about these materials, I realized just how versatile they could be for construction projects. From roofing materials to insulation panels, heat-resistant polymers have the potential to revolutionize the way we build structures in extreme environments.
Imagine being able to construct buildings that could withstand not only scorching hot summers but also freezing cold winters without any damage or loss of structural integrity! With heat-resistant polymers on our side, this dream may soon become a reality.
Understanding the different types of polymer options available for various applications will help ensure that your building project remains structurally sound even under extreme temperature conditions.
High-Temperature Performance Factors
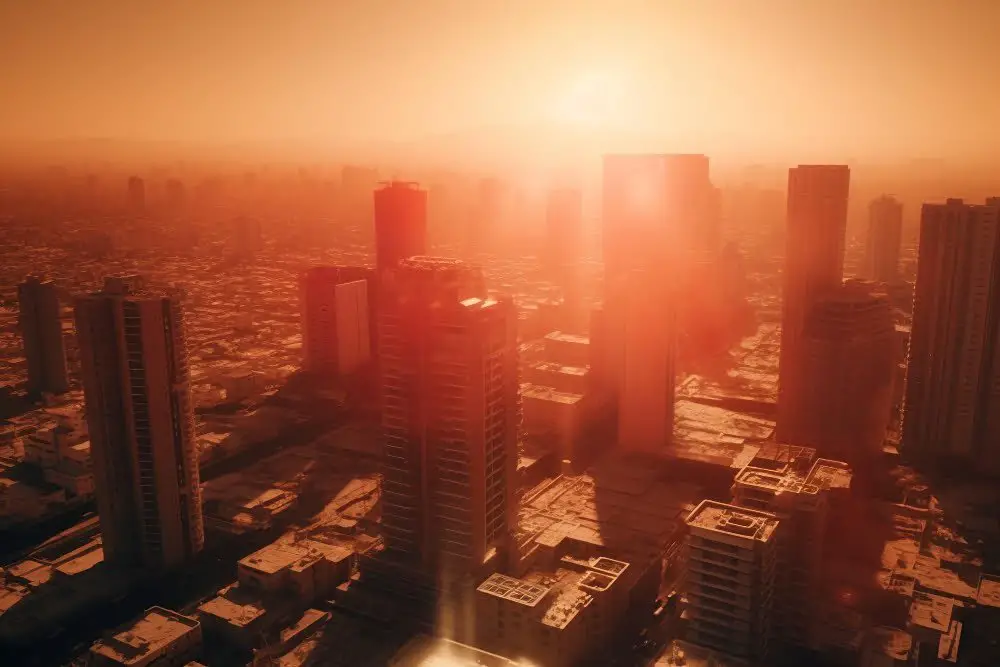
When it comes to building materials, high-temperature performance is a critical factor in ensuring structural integrity. As I learned on that sweltering day in Arizona, extreme heat can cause many materials to break down or lose their shape – which can be disastrous for the safety and stability of a structure.
That’s where heat-resistant polymers come in. These innovative materials are designed with high-temperature performance factors specifically in mind.
They’re engineered to withstand extreme temperatures without melting or losing their shape, making them ideal for use in environments where other materials might fail.
But what makes these polymers so effective at handling high temperatures? It all comes down to their unique chemical composition and molecular structure. Unlike traditional plastics or other synthetic materials, heat-resistant polymers are made up of long chains of molecules that are tightly bound together through strong chemical bonds.
This gives them exceptional strength and durability even under intense conditions like those found on construction sites during hot summers or cold winters. And because they’re able to maintain their shape even when exposed to extreme temperatures over time, they provide reliable protection against structural damage caused by thermal expansion and contraction.
In short: if you want your building project to stand the test of time – no matter how hot it gets outside – then using heat-resistant polymers is an absolute must!
Thermal Stability Mechanisms
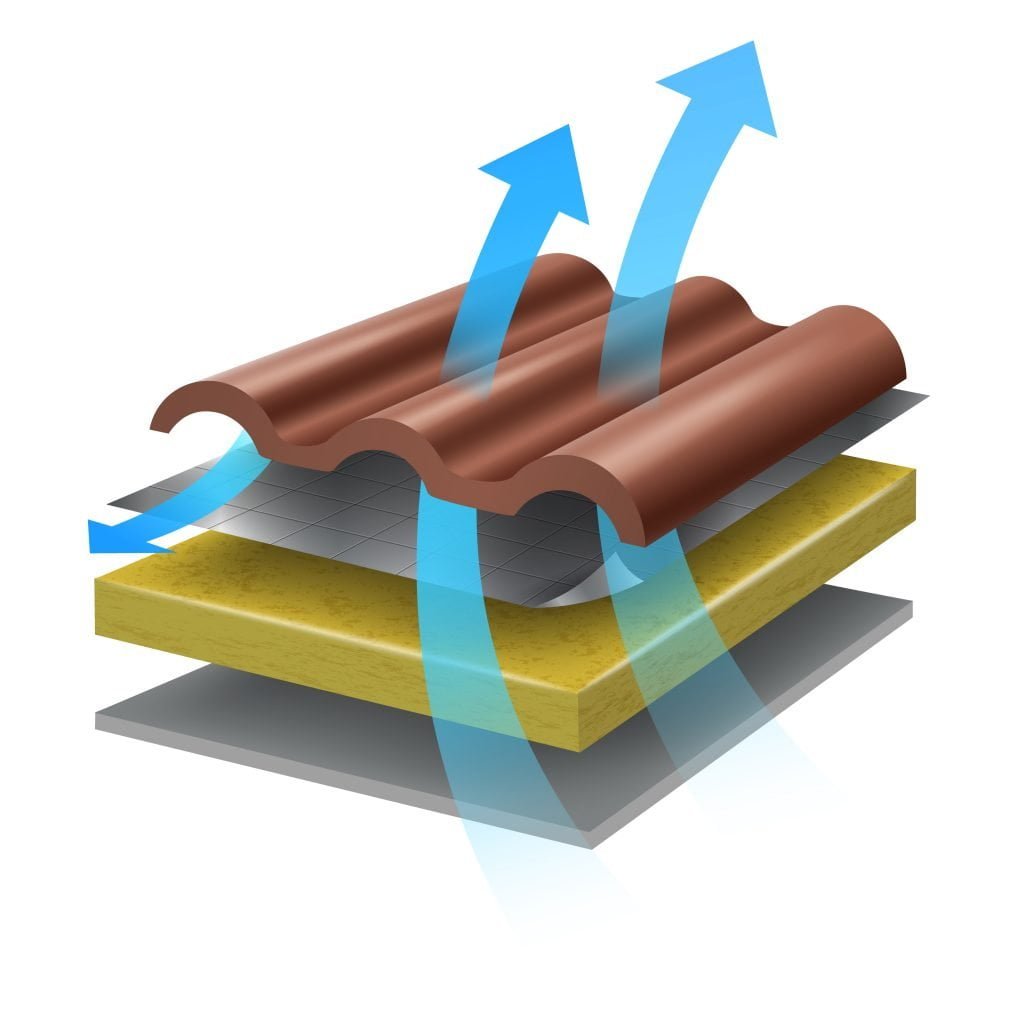
One of the key reasons why heat-resistant polymers are so effective in extreme temperatures is their thermal stability mechanisms. These materials are designed to maintain their structural integrity even when exposed to high levels of heat, which makes them ideal for use in a wide range of construction applications.
There are several different ways that these polymers achieve this thermal stability. Some rely on chemical cross-linking, which creates strong bonds between the polymer chains and prevents them from breaking down under high temperatures.
Others incorporate special additives or fillers that help dissipate heat and prevent it from building up within the material.
Regardless of how they achieve it, these thermal stability mechanisms make heat-resistant polymers an incredibly valuable tool for ensuring structural integrity in extreme temperatures – something I’ve seen firsthand on many job sites over the years.
In fact, just last winter I was working on a project in northern Canada where we were using these materials to build structures that could withstand sub-zero temperatures without cracking or warping. It was amazing to see how well they held up even under those challenging conditions!
I’m excited about what this technology means for our industry – not only does it allow us to build stronger and more resilient structures than ever before but also opens up new possibilities for construction projects across a wide range of environments!
Material Selection Criteria
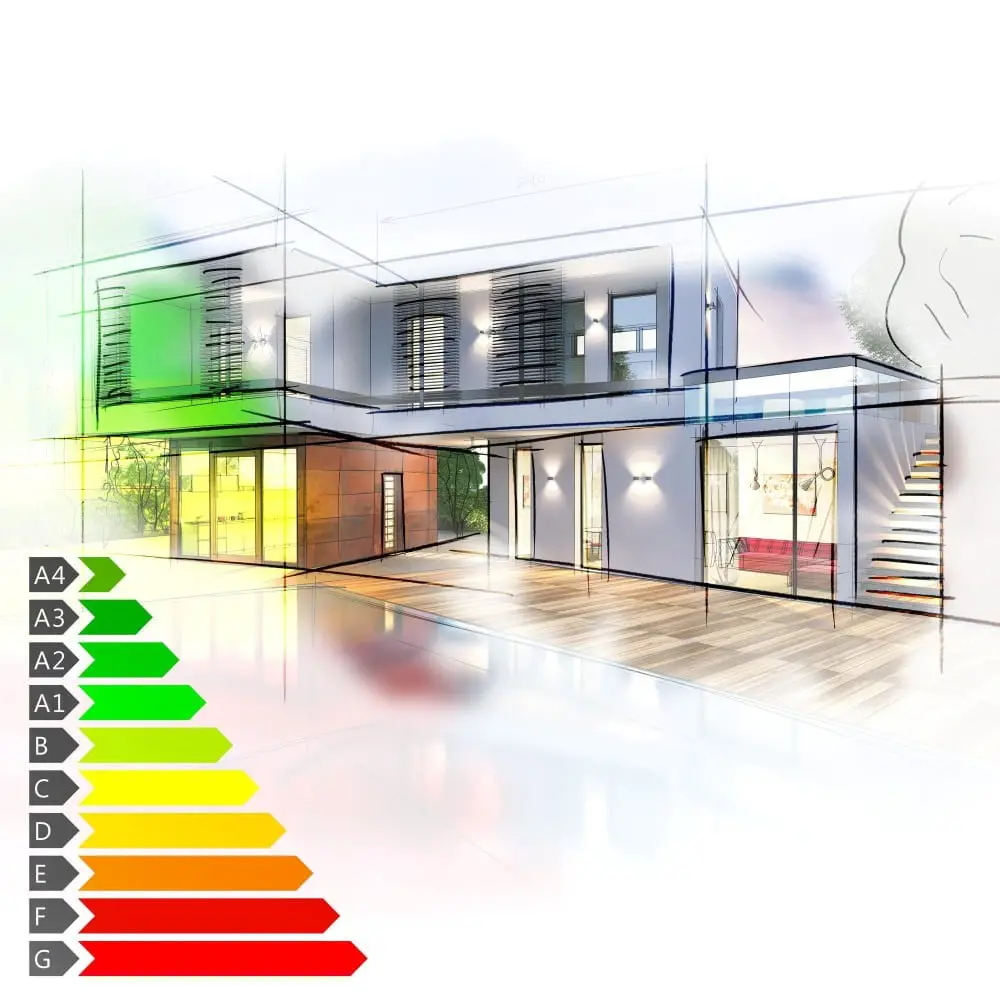
When it comes to building structures that can withstand extreme temperatures, material selection is critical. As my colleague pointed out on that scorching summer day in Arizona, not all materials are created equal when it comes to heat resistance.
So what criteria should you consider when selecting materials for a project in an environment with extreme temperatures? Here are a few key factors:
Temperature range: Consider the highest and lowest temperatures the structure will be exposed to over its lifetime.
This will help you determine which materials can handle those extremes without degrading or losing their shape.
Thermal conductivity: Materials with high thermal conductivity transfer heat more easily than those with low thermal conductivity.
In some cases, this may be desirable (such as using metal roofing panels to quickly dissipate heat), while in other cases it may be best to use insulating materials that resist heat transfer.
Chemical resistance: Extreme temperatures can also impact how different chemicals interact with building materials – so if your project involves exposure to certain chemicals or substances (like acids), make sure your chosen material is resistant enough not only against temperature but also chemical corrosion.
As I learned from my experience working on construction projects across various environments, choosing the right material for each specific job requires careful consideration of these and other factors.
Thankfully, advancements like heat-resistant polymers have made this process easier by providing us builders access innovative solutions designed specifically for challenging conditions like extreme temperature ranges!
Processing Techniques for Durability
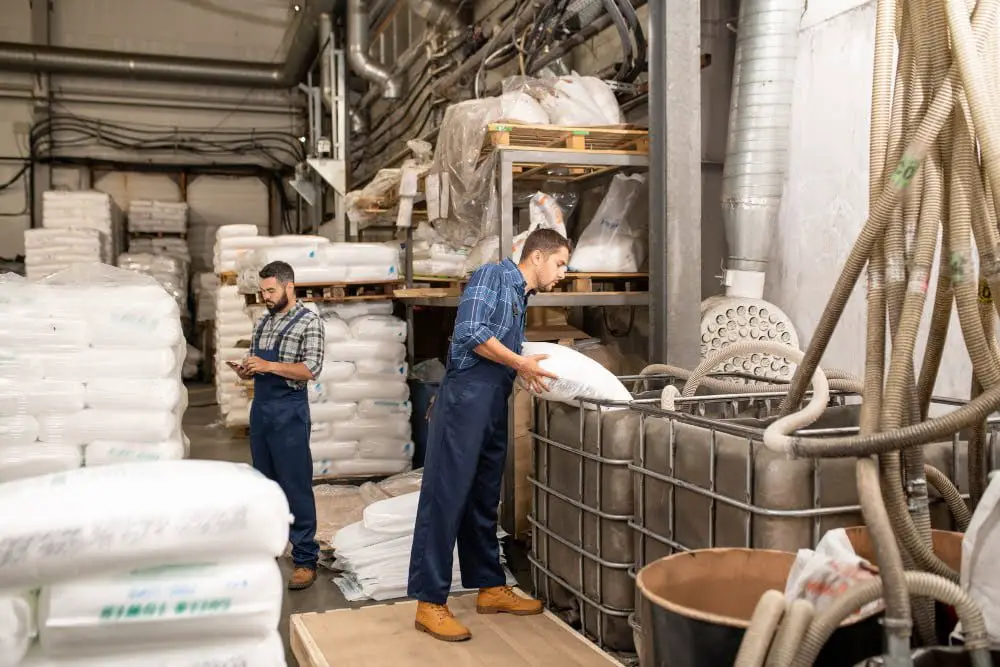
One of the key factors that make heat-resistant polymers so effective is their durability. These materials are designed to withstand extreme temperatures without breaking down or losing their shape, making them ideal for use in a wide range of construction applications.
But how exactly are these polymers made to be so durable? It all comes down to processing techniques.
During the manufacturing process, heat-resistant polymers undergo a series of treatments and modifications that enhance their strength and resilience. For example, some types of polymer may be reinforced with fibers or other additives that help improve their resistance to high temperatures.
Other processing techniques might involve subjecting the material to intense pressure or temperature changes during production. This can help create stronger bonds between molecules within the polymer structure, resulting in a more robust final product.
It’s clear that careful attention must be paid not only to selecting appropriate materials but also employing proper processing techniques when working with heat-resistant polymers. By doing so we can ensure structural integrity even under extreme conditions like those I experienced on my project in Arizona – and keep our buildings standing strong for years into the future!
Testing Methods and Standards
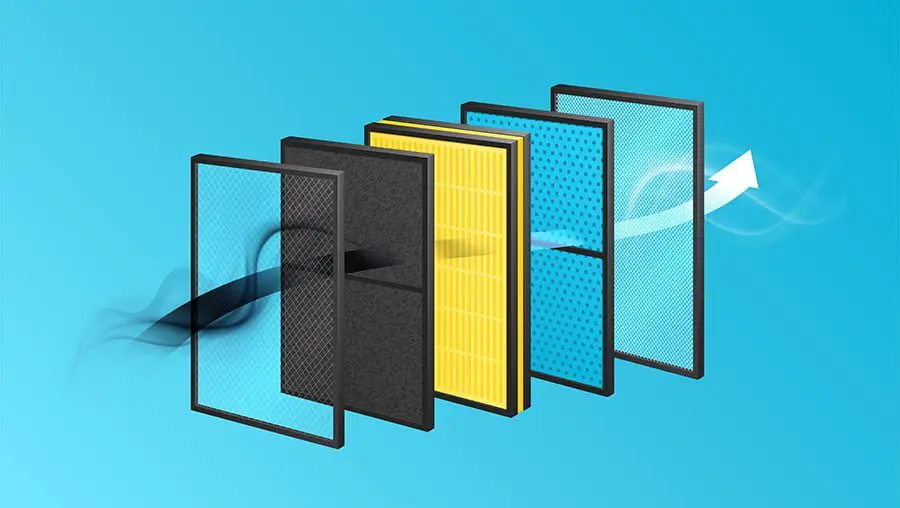
To ensure that heat-resistant polymers are up to the task of withstanding extreme temperatures, rigorous testing methods and standards have been developed. These tests evaluate a material’s ability to maintain its structural integrity under high heat conditions.
One such test is the Heat Deflection Temperature (HDT) test, which measures a polymer’s ability to resist deformation when exposed to elevated temperatures. The HDT value indicates the temperature at which a material will begin to deform under load.
Another important standard for evaluating heat-resistant polymers is ASTM E119, which assesses fire resistance in building materials. This test evaluates how long it takes for a material sample exposed to fire and high temperatures before it fails structurally or allows flames or hot gases through.
These testing methods help ensure that only materials capable of withstanding extreme conditions are used in construction projects where they’re needed most – from skyscrapers in urban areas prone to wildfires, industrial facilities near furnaces or ovens as well as oil rigs located on deserts where temperature can reach over 50°C during daytime hours.
As we continue exploring new frontiers and pushing boundaries with our buildings’ designs and locations – from underwater hotels off Dubai coastlines all way up into space stations orbiting Earth – these innovative materials like heat-resistant polymers will play an increasingly critical role in ensuring their safety and longevity even amidst harsh environments.
Case Studies in Extreme Environments
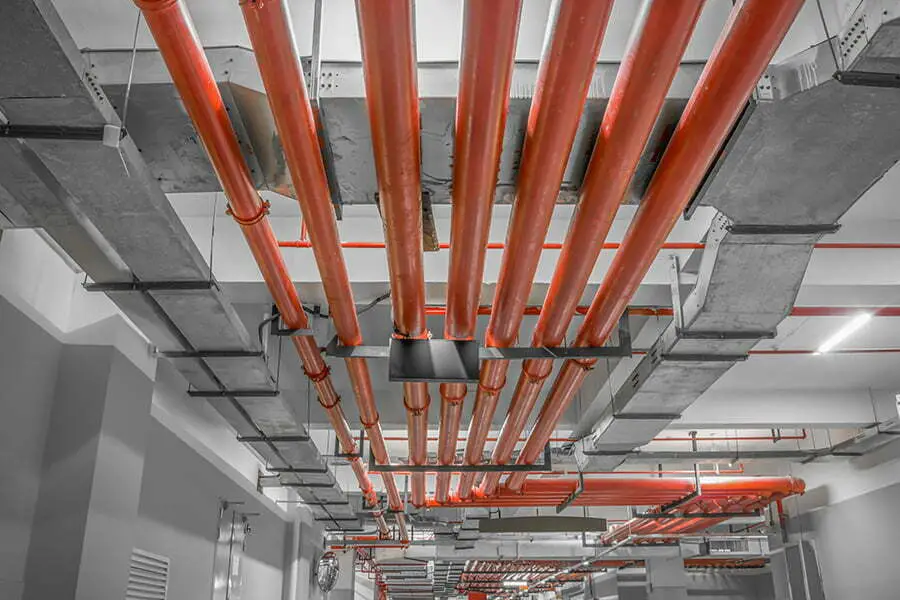
One of the most impressive things about heat-resistant polymers is their ability to perform in a wide range of extreme environments. From high-temperature industrial settings to frigid arctic conditions, these materials have been put to the test and proven their worth time and time again.
For example, in Alaska’s Prudhoe Bay oil field – one of the coldest places on Earth – heat-resistant polymers are used extensively in pipeline insulation. These pipelines transport crude oil from drilling sites across hundreds of miles through some of the harshest weather conditions imaginable.
Without proper insulation, they would be at risk for damage or failure due to freezing temperatures.
Similarly, in hot desert climates like Dubai where temperatures can soar above 120 degrees Fahrenheit during summer months, buildings must be constructed with materials that can withstand intense heat without losing structural integrity over time. Heat-resistant polymers are increasingly being used as an alternative material for roofing systems and exterior cladding because they offer superior thermal stability compared to traditional building materials like metal or concrete.
These case studies demonstrate just how versatile and effective heat-resistant polymers can be when it comes to ensuring structural integrity under extreme temperature conditions.
As we continue exploring new frontiers both here on Earth and beyond our planet’s atmosphere into space exploration missions – there will undoubtedly be even more opportunities for this innovative material technology!
Advancements in Heat-Resistant Polymer Manufacturing
Manufacturing heat-resistant polymers has seen significant advancements in recent years. Researchers and engineers have been working tirelessly to develop new formulations and processing techniques that enhance the thermal stability of these materials.
One notable advancement is the incorporation of nanotechnology into polymer production, which allows for improved heat resistance properties.
By adding nanoparticles such as graphene or carbon nanotubes to polymer matrices, manufacturers can create composites with enhanced thermal conductivity and mechanical strength. These reinforcements help dissipate heat more efficiently, preventing degradation at high temperatures.
Novel manufacturing processes like 3D printing have revolutionized the production of complex geometries using heat-resistant polymers. This technology enables precise control over material deposition and layering, resulting in components with tailored properties suitable for extreme temperature applications.
The continuous research efforts dedicated to understanding the behavior of polymers under different temperature conditions have also contributed significantly to advancements in their manufacturing process. By gaining a deeper understanding of how molecular structures influence thermal stability, scientists can design custom-made polymers that withstand specific temperature ranges without compromising structural integrity.
Lifecycle and Durability of Heat-Resistant Polymers
Understanding the lifecycle and durability of these polymers is essential for their effective application in construction.
The lifecycle of heat-resistant polymers begins with their manufacturing, where specific additives and processing techniques are employed to enhance their resistance to high temperatures. These specialized materials undergo rigorous testing to ensure they meet industry standards for performance and safety.
Once installed, heat-resistant polymers exhibit remarkable durability under extreme temperature conditions. They can withstand prolonged exposure without significant degradation or loss of mechanical properties.
This longevity is attributed to the inherent chemical stability and thermal resistance engineered into these materials during production.
However, it’s important to note that while heat-resistant polymers offer exceptional performance at elevated temperatures, they may still experience some degree of degradation over time due to factors such as oxidative reactions or thermal cycling effects. Therefore, regular inspections and maintenance are necessary for monitoring any signs of wear or deterioration that could compromise structural integrity.
To extend the lifespan of heat-resistant polymer-based structures further, proper installation techniques must be followed along with adherence to recommended operating parameters specified by manufacturers. Periodic evaluations should be conducted by qualified professionals who can assess potential risks associated with environmental factors like UV radiation exposure or chemical interactions.
Environmental Impacts of Using Heat-Resistant Polymers
While these polymers offer numerous benefits, such as enhanced structural integrity and durability in extreme temperatures, it is crucial to understand their potential effects on the environment.
One key aspect to consider is the production process of heat-resistant polymers. The manufacturing of these materials often involves energy-intensive processes and may require the use of certain chemicals or additives.
These factors can contribute to greenhouse gas emissions and other forms of pollution if not properly managed.
At the end-of-life stage, proper disposal or recycling methods must be employed for heat-resistant polymer products. If not handled correctly, they could potentially end up in landfills where they may take a long time to degrade or release harmful substances into soil and water systems.
To mitigate these environmental impacts associated with using heat-resistant polymers, manufacturers are increasingly adopting sustainable practices throughout their supply chains. This includes implementing cleaner production techniques that reduce energy consumption and emissions during manufacturing processes.
Furthermore, efforts are being made towards developing more eco-friendly alternatives by exploring bio-based sources for polymer production or utilizing recycled materials whenever possible without compromising performance characteristics.
Cost-Benefit Analysis of Heat-Resistant Polymers
While these specialized materials may come at a higher initial cost compared to traditional alternatives, their long-term benefits often outweigh the upfront investment.
One significant advantage of heat-resistant polymers is their durability and extended lifespan. These materials are designed to withstand extreme temperatures without compromising structural integrity.
As a result, they require minimal maintenance and replacement over time, reducing overall costs associated with repairs or replacements.
Heat-resistant polymers offer excellent energy efficiency properties. Their ability to insulate against high temperatures can contribute to reduced heating and cooling expenses in buildings located in hot climates or near industrial processes generating substantial amounts of heat.
Furthermore, using these advanced polymer solutions can lead to improved safety measures by preventing fire hazards caused by overheating or melting materials during extreme temperature events. This not only protects occupants but also reduces potential property damage and insurance claims.
It’s important for project managers and engineers alike to consider the long-term financial implications when evaluating different construction material options for projects that will be exposed to high temperatures regularly or intermittently throughout their lifecycle.
Future Trends in Heat-Resistant Polymer Use and Development
Researchers and engineers are constantly exploring new ways to improve these materials and expand their applications. Here are some exciting trends in the use and development of heat-resistant polymers:
1. Enhanced Performance: Scientists are working on developing heat-resistant polymers with even higher temperature thresholds, allowing them to withstand extreme conditions that were previously unattainable.
This will open up opportunities for their use in industries such as aerospace, automotive, electronics, and energy.
2. Sustainable Solutions: With growing environmental concerns, there is a push towards developing eco-friendly alternatives to traditional heat-resistant polymers that rely on fossil fuels or have high carbon footprints during production or disposal processes.
Bio-based or recycled polymer options may become more prevalent in the future.
3. Nanocomposites: Incorporating nanoparticles into polymer matrices can significantly enhance their thermal stability while maintaining other desirable properties like strength and flexibility.
Ongoing research aims at optimizing nanocomposite formulations for various applications where superior thermal resistance is required.
4. Improved Manufacturing Techniques: Advancements in manufacturing techniques such as 3D printing offer exciting possibilities for creating complex geometries using heat-resistant polymers with precision control over material composition at a microscale level.
5. Multifunctional Materials: The integration of additional functionalities within heat-resistant polymer systems is an area gaining attention among researchers.This includes incorporating self-healing capabilities,reinforcing electrical conductivity,and improving flame retardancy.These multifunctional materials could find application across diverse sectors including construction,aerospace,and electronics industry.
These emerging trends indicate a bright future for the utilization of advanced heat- resistant polymeric materials across various industries.They hold great potential not only in ensuring structural integrity but also enabling innovation by pushing boundaries beyond what was previously thought possible.
FAQ
What is an example of heat-resistant polymer?
An example of a heat-resistant polymer is Polyetherimide (PEI).
What material is the most heat-resistant?
The material with the most heat-resistance is ceramics.
What polymers do not melt?
Thermosetting polymers are the type of polymers that do not melt due to the presence of strong covalent bonds known as cross-links, which are hard to break when heated.
Which plastic do not melt on heating?
The type of plastic that does not soften and melt on heating is Bakelite.
How are thermosetting polymers utilized in the construction industry?
Thermosetting polymers are utilized in the construction industry as adhesives, coatings, and foams due to their heat resistance and structural integrity.
What advancements have been made in developing fire-retardant polymers?
Significant advancements in fire-retardant polymers include the development of intumescent coatings which can swell to form a protective char layer during a fire, blocking heat and reducing flammability.
How does the chemical structure of a polymer affect its heat resistance?
The chemical structure of a polymer, specifically the strength and type of its intermolecular forces, determines its heat resistance because stronger forces increase the energy required to break bonds and, thereby, enhance the polymer’s thermal stability.
Recap