Discover the innovative world of high temperature injection molded plastics and their versatile applications in various industries with our insightful blog.
As you may know, plastics have become a ubiquitous material in modern construction due to their versatility and affordability. However, not all plastics are created equal.
High-temperature injection molded plastics are specifically designed to withstand extreme temperatures without losing their shape or integrity. In this article, we will explore the benefits and applications of high-temperature injection molded plastics in construction projects.
Whether you’re an engineer or simply interested in learning more about polymers, this article will provide valuable insights into this fascinating field. So let’s dive in!
Overview of High-Temperature Plastics
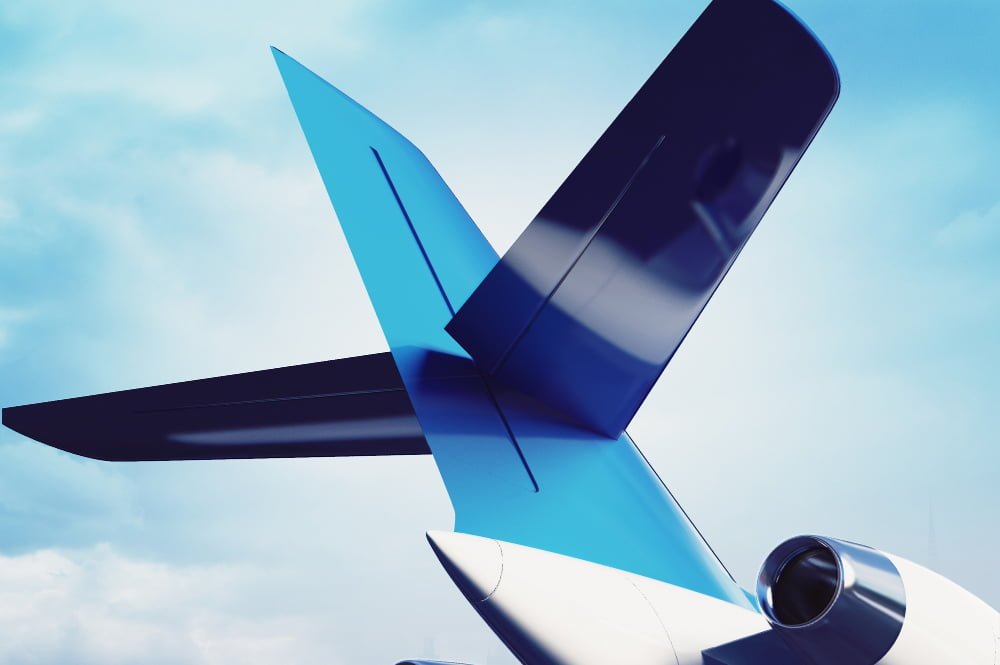
High-temperature plastics are a class of polymers that can withstand extreme temperatures without losing their shape or mechanical properties. These materials have become increasingly popular in various industries, including aerospace, automotive, electronics and medical devices.
High-temperature plastics offer several advantages over traditional materials such as metals and ceramics due to their lightweight nature, corrosion resistance and ease of processing. They also provide excellent electrical insulation properties which make them ideal for use in electronic components that generate heat during operation.
The most common high-temperature plastic used is polyphenylene oxide (PPO), which has a glass transition temperature (Tg) of around 220°C. Other high-performance thermoplastics include Vespel®, Torlon® (Polyamide-imide), PEEK (Polyether Ether Ketone), ULTEM®(Polyetherimide PEI) Celazole PBI among others with Tg ranging from 250°C to above 400°C.
Common High-Temperature Plastics
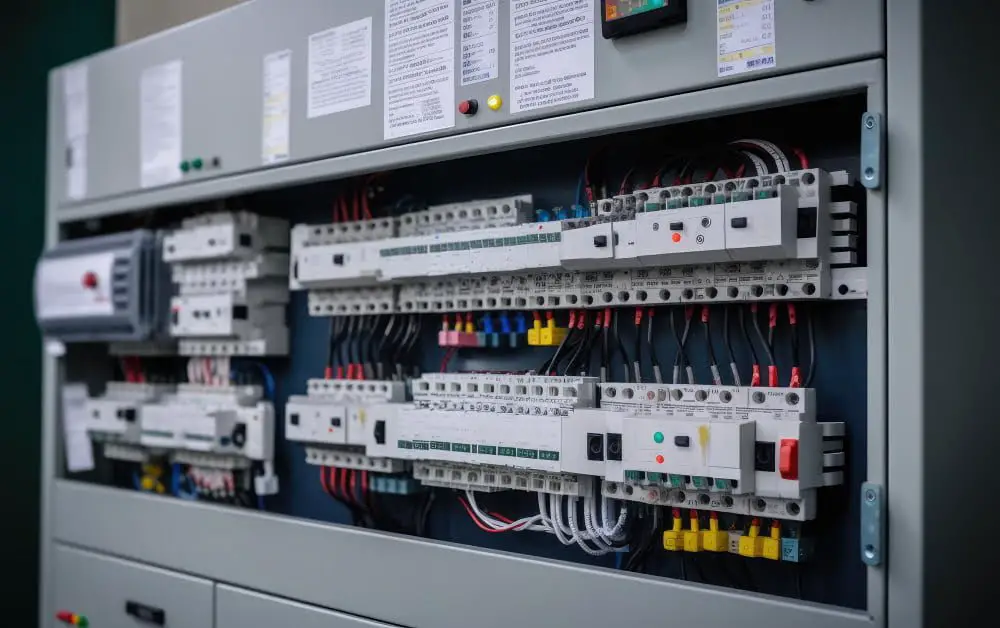
These materials have a wide range of applications in various industries, including aerospace, automotive, electronics and electrical equipment manufacturing. Some common high-temperature plastics include Vespel®, Torlon® (Polyamide-imide), PEEK (Polyether Ether Ketone), ULTEM® (Polyetherimide, PEI) and Celazole PBI.
Vespel® is a polyimide material that can withstand temperatures up to 300°C continuously with excellent dimensional stability and low wear rates. It has been used in the aerospace industry for over 40 years due to its exceptional strength-to-weight ratio.
Torlon®, on the other hand, is known for its outstanding mechanical properties at elevated temperatures up to 275°C while maintaining excellent chemical resistance. This makes it ideal for use in bearings and seals where high loads are present.
PEEK is another popular choice due to its ability to maintain stiffness at high temperature ranges of up to 250°C while also being resistant against chemicals such as acids or bases commonly found within industrial environments.
ULTEM® offers superior thermal performance with continuous operating temperature ranges from -40 °C (-40°F)to +170 °C (+338°F). Its unique combination of heat resistance coupled with flame retardancy makes it an ideal candidate for electronic components like connectors or switches that require both safety features along with durability under harsh conditions.
Celazole PBI boasts one of the highest glass transition points among all thermoplastics making it suitable even when exposed directly into flames reaching more than thousands degrees Celsius.
High-Temperature Thermoplastic Materials
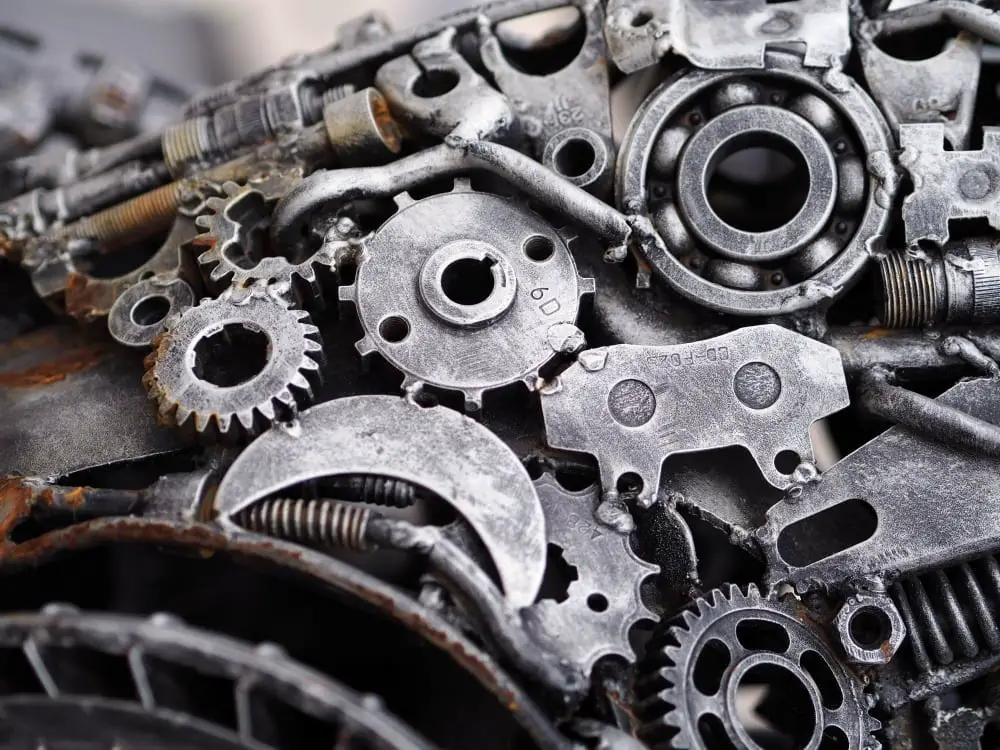
These materials have become increasingly popular in various industries due to their excellent thermal stability, chemical resistance, and durability. High-temperature thermoplastics are used in applications where traditional plastics would fail under extreme conditions such as aerospace, automotive, electronics manufacturing and oil & gas exploration.
Some common types of high-temperature thermoplastic materials include Vespel®, Torlon® (Polyamide-imide), PEEK (Polyether Ether Ketone), ULTEM® (Polyetherimide PEI) and Celazole PBI. Each material has its unique set of properties that make it suitable for specific applications.
Vespel®, for example, is known for its exceptional wear resistance at elevated temperatures making it ideal for use in bearings and bushings. Torlon® is an amorphous plastic with excellent strength retention at high temperatures which makes it perfect for use in aircraft components like gears or compressor parts.
PEEK is another popular choice because of its ability to maintain stiffness even when exposed to continuous heat up to 500°F while ULTEM offers superior flame retardancy making them both great choices when designing electrical components like connectors or switches.
Celazole PBI stands out from the rest due to its unmatched combination of temperature resistance up 800°F along with outstanding chemical inertness which makes them ideal candidates as seals/gaskets within harsh environments such as petrochemical plants.
Vespel®
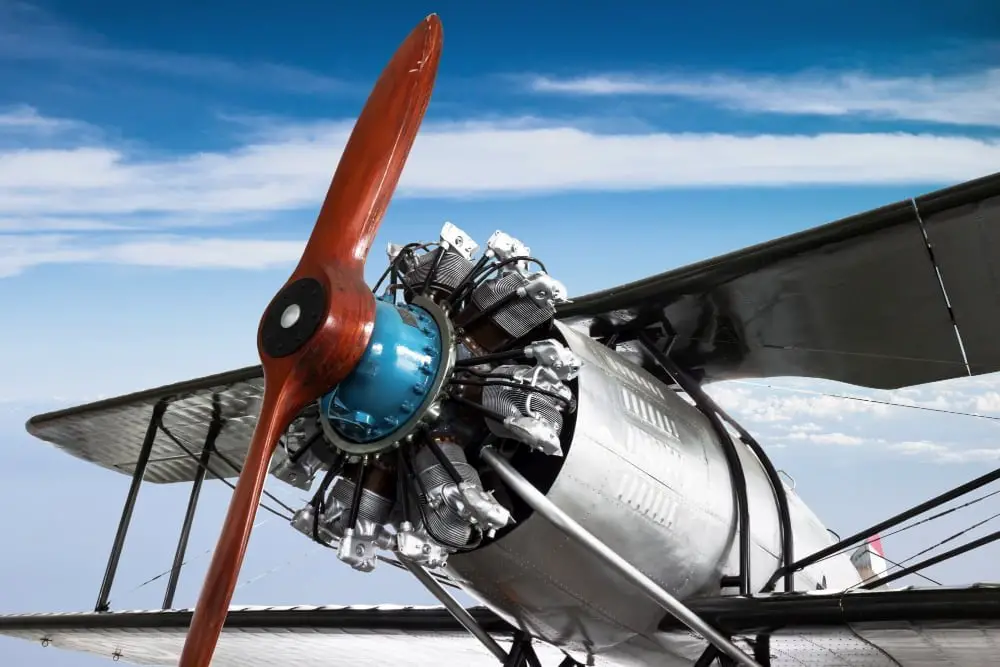
It was first introduced in the 1960s by DuPont, and since then, it has been widely used in various industries such as aerospace, automotive, chemical processing, and semiconductor manufacturing.
One of the unique properties of Vespel® is its ability to maintain its strength even at elevated temperatures up to 550°F (288°C). This makes it an ideal choice for applications where other materials would fail due to thermal degradation.
Vespel® exhibits excellent wear resistance and low friction coefficient which make it suitable for use in bearings or bushings.
In injection molding processes involving Vespel®, there are several considerations that need to be taken into account. For instance, mold design should ensure uniform wall thicknesses with draft angles between 1-3 degrees per side depending on part geometry.
The use of heat transfer channels or thermal pins can also help control temperature distribution during molding.
Torlon® (Polyamide-imide)
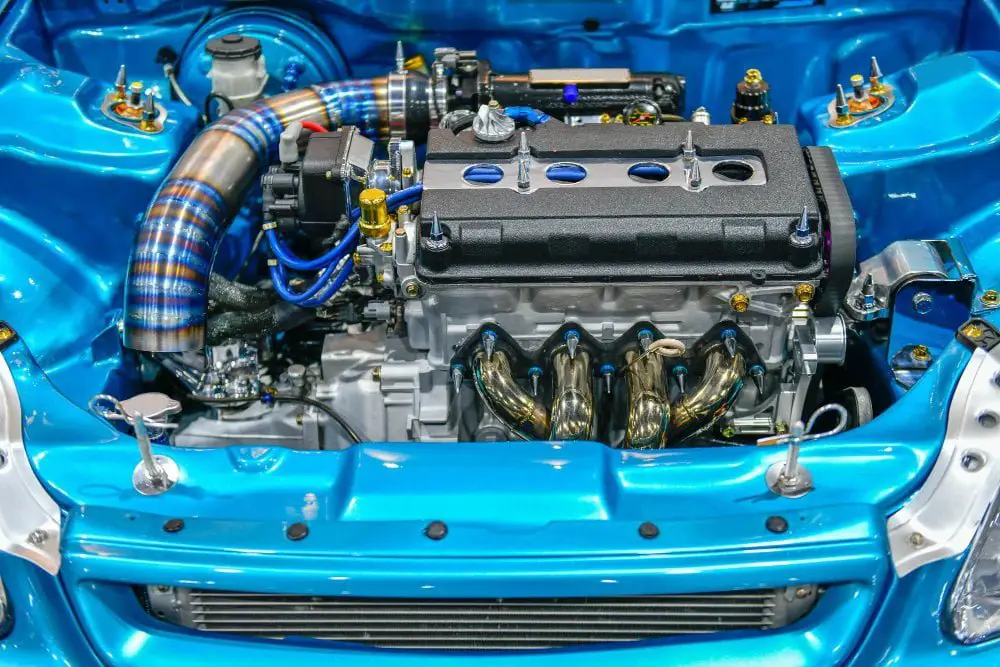
It is known for its exceptional strength, stiffness, and resistance to wear and tear. Torlon® can withstand temperatures up to 500°F (260°C) without losing its shape or integrity.
One of the unique features of Torlon® is that it has a low coefficient of thermal expansion compared to other plastics. This means that it maintains its dimensions even when exposed to extreme temperature changes.
Due to these impressive characteristics, Torlon® finds extensive use in various industries such as aerospace, automotive manufacturing, oil & gas exploration equipment manufacturing among others where parts are subjected under harsh conditions like frictional heat or chemical exposure.
In injection molding processes involving this material selection guide should be followed strictly since improper handling may lead the molded part’s failure due mainly because of warpage issues caused by uneven cooling rates during solidification.
PEEK (Polyether Ether Ketone)

It can withstand temperatures up to 500°F without losing its strength or stiffness, which makes it an attractive option for industries such as aerospace, automotive, and medical.
One of the unique features of PEEK is its ability to resist wear and tear even under extreme conditions. This property makes it suitable for manufacturing components that are subject to constant friction or abrasion.
PEEK has low moisture absorption rates compared to other plastics like nylon or acetal.
The injection molding process used with PEEK requires specialized equipment due to the material’s high melting point (around 650°F). The mold must be heated uniformly throughout the process so that there are no hot spots where the plastic could degrade prematurely.
Despite these challenges during processing, manufacturers continue using this material because of its exceptional performance characteristics in demanding environments.
ULTEM® (Polyetherimide, PEI)
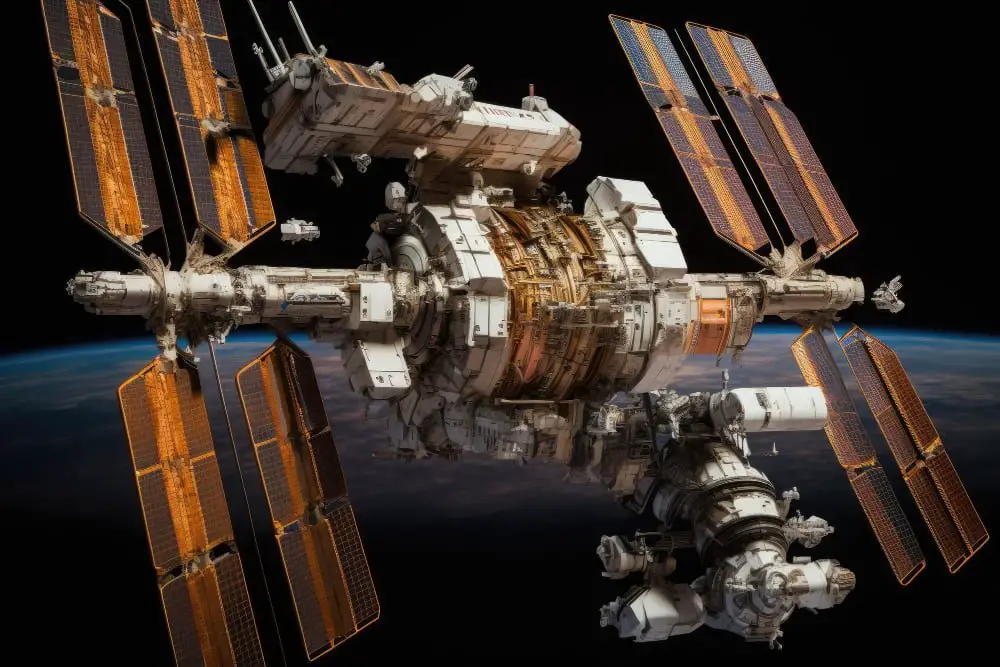
It can withstand temperatures up to 340°C without losing its strength or shape, making it ideal for use in high-temperature applications. ULTEM® also has exceptional chemical resistance and is highly resistant to hydrolysis, which makes it suitable for use in harsh environments.
One of the unique features of ULTEM® is its ability to maintain dimensional stability even at elevated temperatures. This property makes it an excellent choice for manufacturing parts that require tight tolerances and precise dimensions.
ULTEM® can be easily injection molded into complex shapes with intricate details using standard molding equipment. However, due to its high melting point and viscosity when molten, special considerations must be taken during the molding process such as selecting appropriate mold materials with good heat transfer properties.
In construction projects where extreme temperature conditions are expected such as aerospace components or automotive under-the-hood parts; ULTEM®, along with other High-Temperature Plastics like PEEK (Polyether Ether Ketone), Vespel®, Torlon®, Celazole PBI among others have become popular choices due their superior performance characteristics over traditional plastics like ABS or Nylon.
Celazole PBI
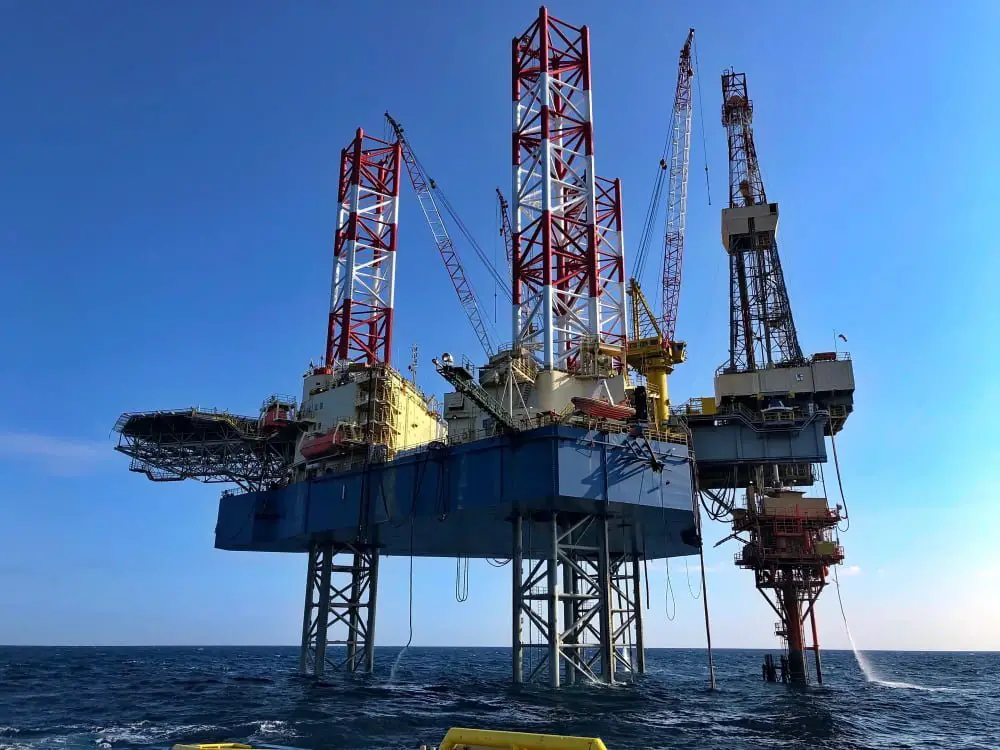
It has excellent mechanical properties, including high strength and stiffness, making it ideal for use in demanding applications. Celazole PBI also has exceptional chemical resistance and low moisture absorption, which makes it suitable for use in harsh environments.
One of the unique features of Celazole PBI is its ability to maintain its mechanical properties at elevated temperatures. This property makes it an excellent choice for applications such as aerospace components or oil drilling equipment where exposure to extreme heat is common.
In addition to its thermal stability, Celazole PBI also exhibits outstanding wear resistance and dimensional stability. These characteristics make this material well-suited for precision parts that require tight tolerances over a wide range of operating conditions.
Celazole PBI offers superior performance compared with other high-temperature plastics like Vespel® or Torlon®.
Other High Resistant Plastics
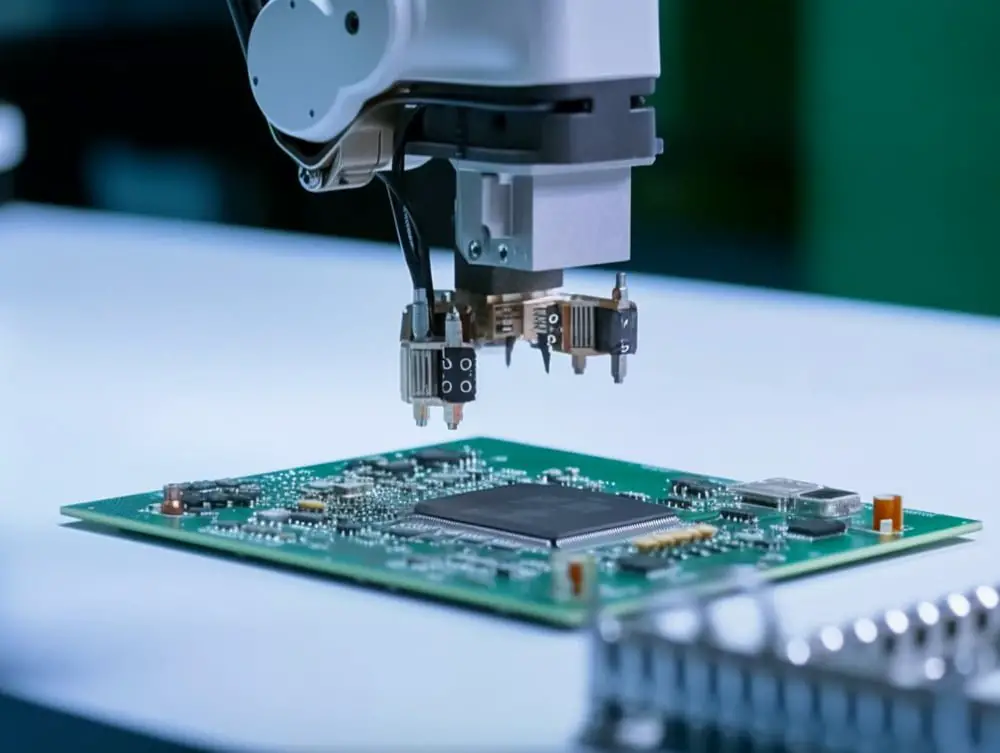
These include polyimides, polysulfones, and liquid crystal polymers (LCPs). Polyimides have a glass transition temperature of up to 400°C and can withstand continuous use at temperatures as high as 300°C.
Polysulfones are known for their toughness and chemical resistance while LCPs exhibit exceptional mechanical properties even at elevated temperatures.
These materials have unique characteristics that make them suitable for specific applications in various industries such as aerospace, automotive manufacturing, electronics production among others. However, selecting the right material requires careful consideration of factors such as operating conditions like temperature range or exposure time; mechanical requirements like strength or stiffness; chemical compatibility with other components in the system; regulatory compliance requirements among others.
Therefore it is important to work with experts who understand these nuances when choosing a plastic material for your application needs.
Injection Molding Process
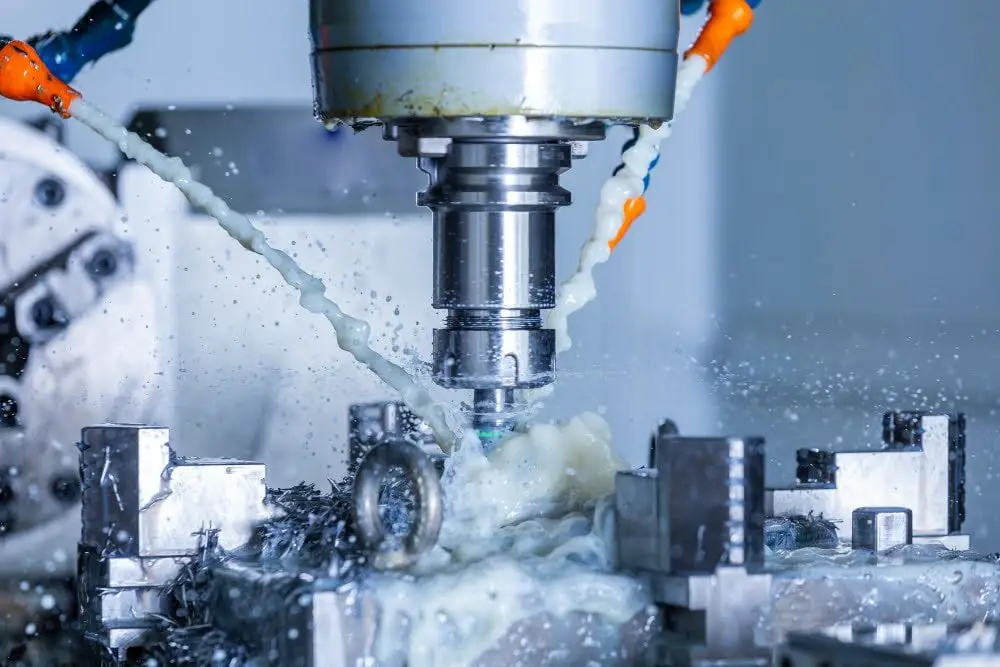
It involves melting plastic pellets and injecting them into a mold cavity under high pressure. The molten plastic then cools and solidifies, taking the shape of the mold cavity.
The injection molding process offers several advantages over other manufacturing processes, such as low labor costs, fast production times, and consistent part quality. It allows for complex shapes to be produced with precision accuracy.
When it comes to producing high-temperature plastics using injection molding techniques there are some considerations that need attention during the design phase of both parts and molds in order to ensure successful outcomes. These include selecting appropriate materials based on their thermal properties; designing molds with heat transfer channels or thermal pins; ensuring uniform wall thickness throughout parts; incorporating draft angles for easy ejection from molds among others.
Material Selection Guide
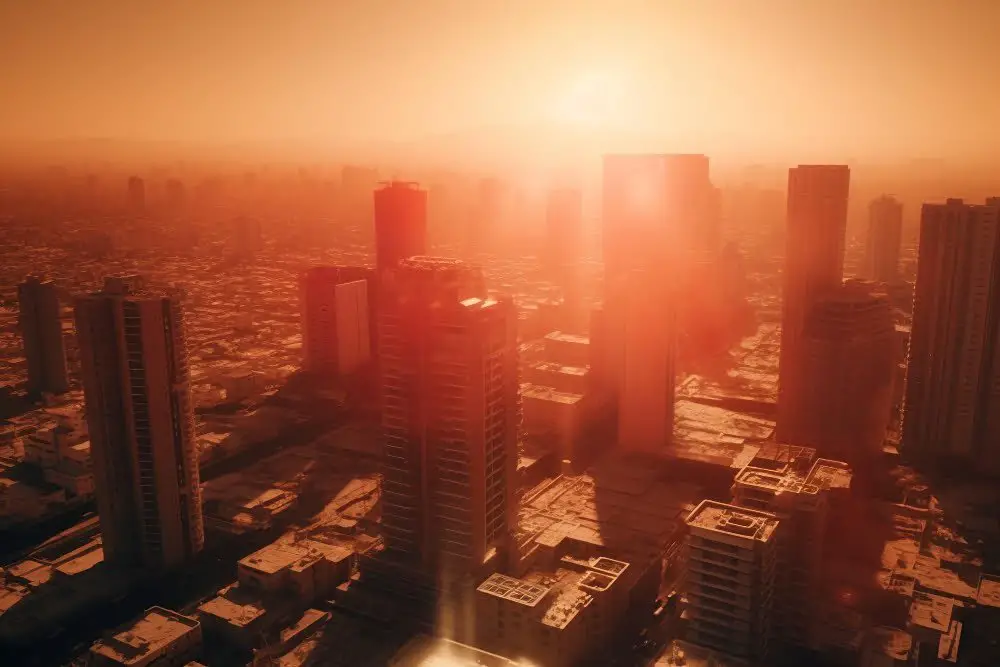
The first step is identifying the specific temperature range that your application requires. Different materials have different melting points and can withstand varying degrees of heat exposure.
Another important consideration is chemical resistance. High-temperature plastics must be able to resist degradation from chemicals and other substances they may come into contact with during use.
Mechanical properties such as strength, stiffness, and impact resistance should also be taken into account when choosing a material for high-temperature applications.
Cost-effectiveness should not be overlooked in the selection process. While some materials may offer superior performance characteristics at higher costs, others may provide adequate performance at lower prices.
Mold Design Considerations
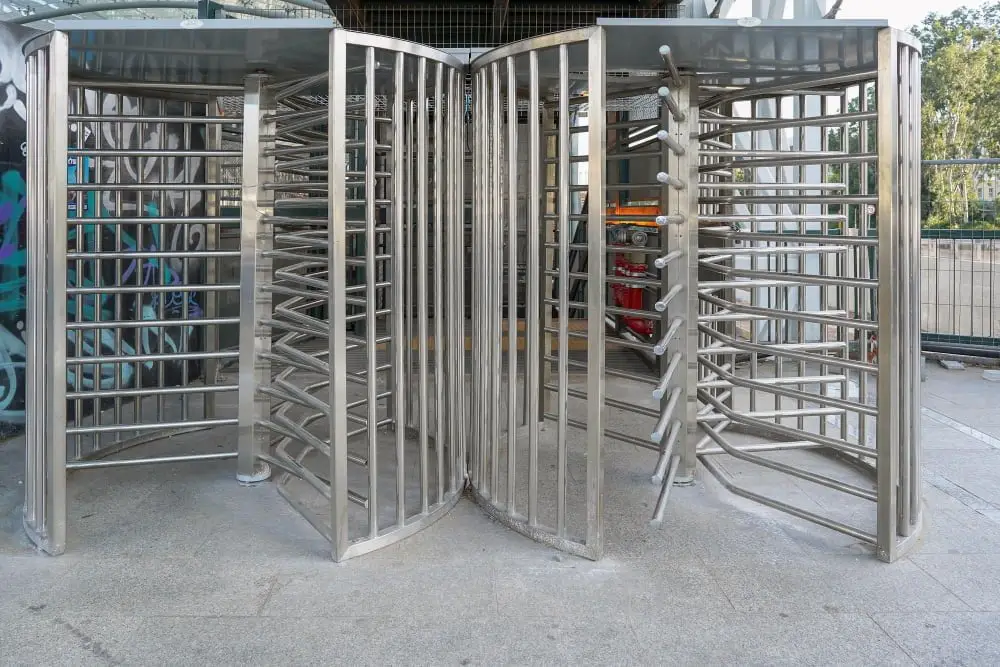
The mold must be able to withstand the extreme temperatures required for molding these materials without warping or degrading. The design of the mold can affect part quality and production efficiency.
One important consideration is material selection. The mold material should have a high melting point and good thermal conductivity to ensure even heating throughout the cavity.
Commonly used materials include tool steel, stainless steel, and copper alloys.
Another factor is uniform wall thickness in parts being produced as this helps prevent uneven cooling which could lead to warpage or distortion of parts after they are ejected from molds. Draft angle also plays an essential role in ensuring easy ejection of finished products from molds while minimizing damage during removal.
It’s crucial that designers take into account any potential issues with shrinkage when selecting their plastic resins since different types will behave differently under varying conditions such as temperature changes during processing stages like cooling down after injection molding process has been completed.
Considerations for Molding High-Temperature Plastics
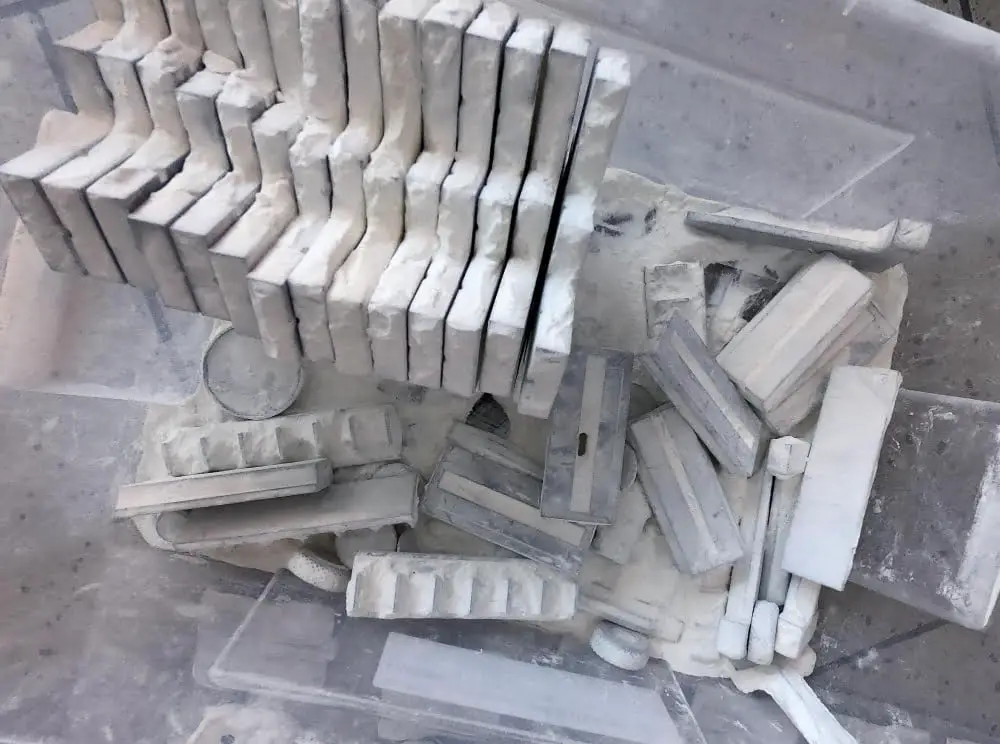
These materials require specific processing conditions and mold design considerations to ensure optimal performance and quality of the final product.
One important consideration is material selection. High-temperature plastics have different properties than standard thermoplastics, so selecting the right material for your application is crucial.
Factors such as chemical resistance, thermal stability, mechanical strength, and dimensional stability should all be considered when choosing a high-temperature plastic.
Another key consideration is mold design. The geometry of the part being molded can affect how well it will perform under high temperatures.
Uniform wall thicknesses help prevent warping or distortion during cooling while draft angles allow for easy release from the mold without damaging delicate features or causing stress points in critical areas.
Heat transfer channels within molds also play an essential role in ensuring consistent temperature distribution throughout each part’s entire volume during injection molding processes with these materials.
Include Heat Transfer Channels
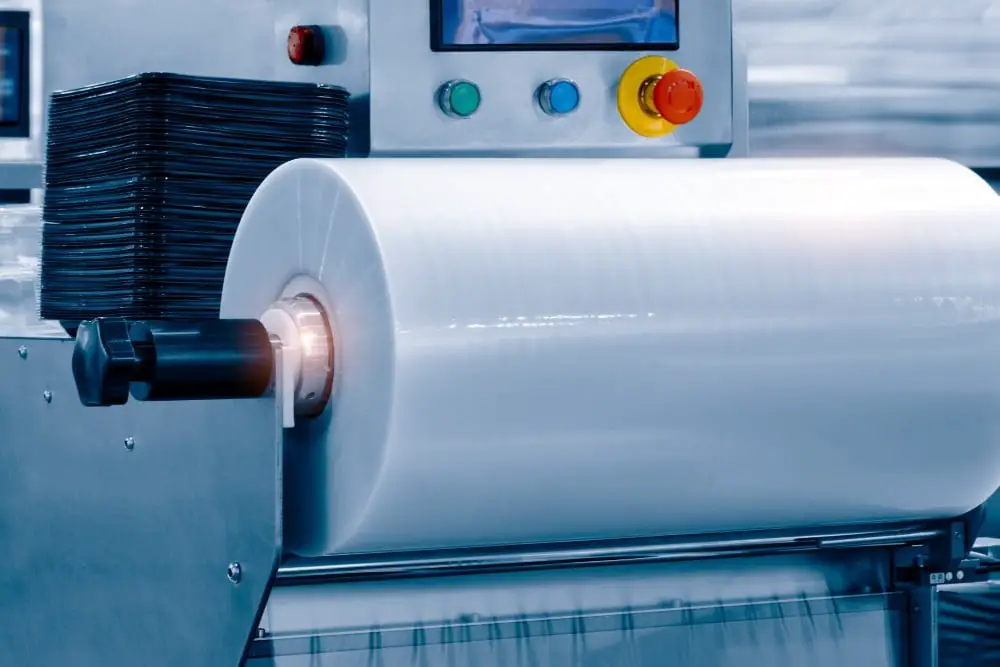
Heat transfer channels are an essential component of the mold design process for high-temperature injection molded plastics. These channels help to regulate temperature and ensure that the plastic material cools evenly throughout the mold.
Heat transfer channels can be designed in various shapes and sizes depending on the complexity of your part geometry, but they all serve one purpose: to maintain consistent temperatures during molding. By including these channels in your mold design, you can prevent warping or distortion caused by uneven cooling rates.
It’s important to note that heat transfer channel placement should also consider factors such as gate location and venting requirements. Properly placed gates will allow for efficient filling while vents will release any trapped air from within the cavity.
Incorporating heat transfer channels into your mold design is critical when working with high-temperature injection molded plastics.
Use Thermal Pins
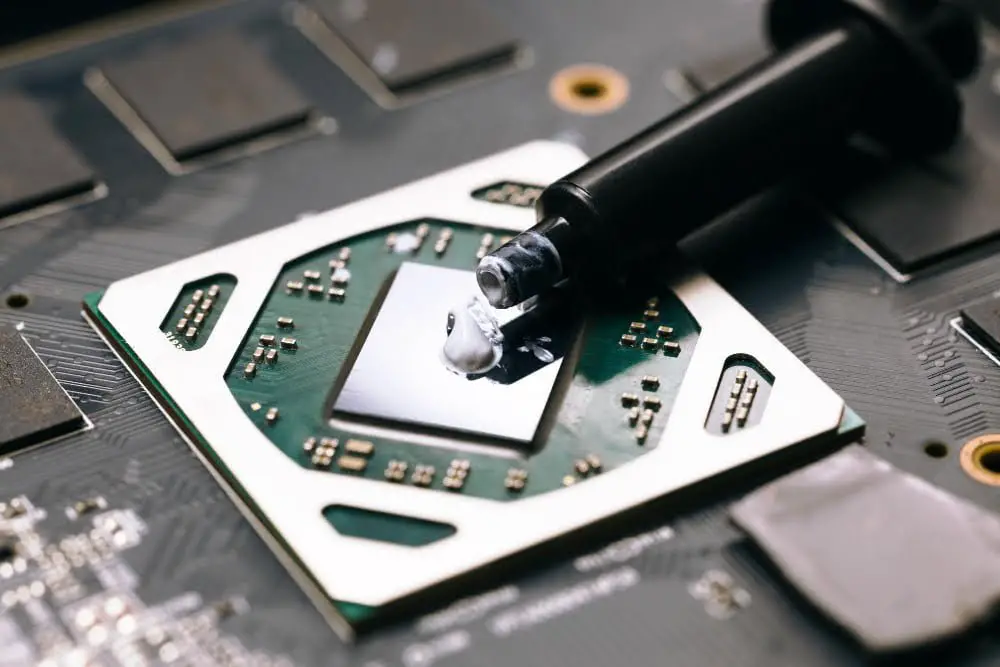
These pins help to regulate the temperature of the mold and ensure that it remains consistent throughout the entire process. By using thermal pins, you can prevent warping or distortion of your plastic parts due to uneven cooling.
The use of thermal pins is especially important when working with high-temperature plastics because they tend to cool at a slower rate than other materials. This means that if you don’t have proper heat transfer channels in place, your parts may not cool evenly, leading to defects and inconsistencies.
When designing molds for high-temperature plastics, it’s crucial to include heat transfer channels and thermal pin locations strategically. The placement should be such that they provide uniform heating across all areas while avoiding any hot spots or cold spots on your part surface.
Select the Right Mold Material
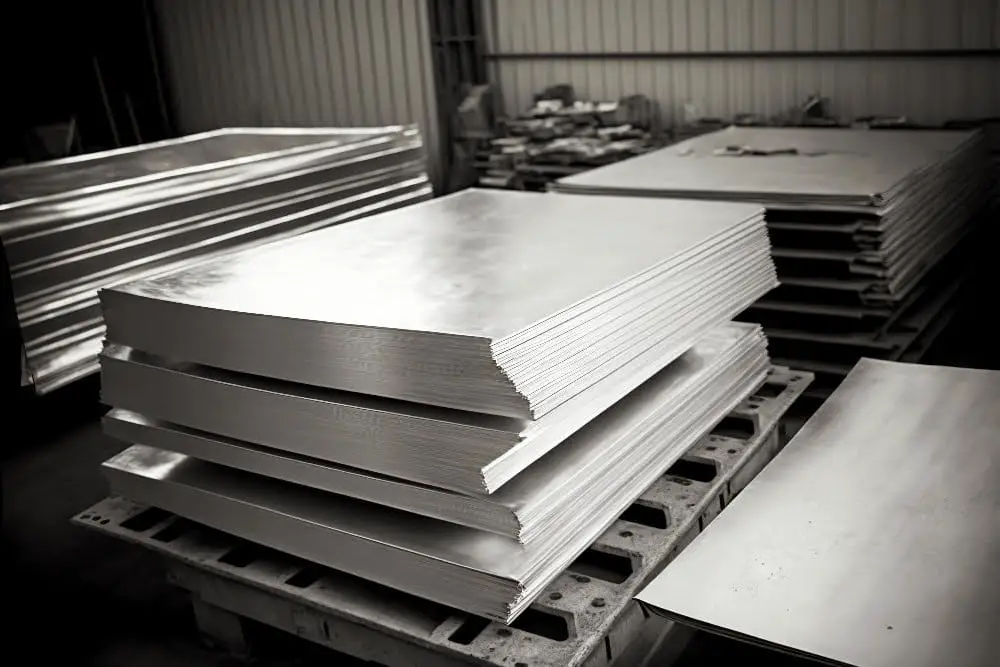
The mold material must be able to withstand the extreme temperatures and pressures involved in the molding process without degrading or warping. Common materials used for molds include steel, aluminum, and copper alloys.
Steel is a popular choice due to its durability and ability to maintain its shape at high temperatures. However, it can be expensive and may require longer lead times for fabrication.
Aluminum molds are less expensive than steel but have lower durability levels which make them more susceptible to wear over time. Copper alloys offer excellent thermal conductivity but are not as durable as steel or aluminum.
When selecting a mold material, factors such as cost-effectiveness, production volume requirements, part complexity level should also be considered alongside temperature resistance properties of each option available.
Uniform Wall Thickness
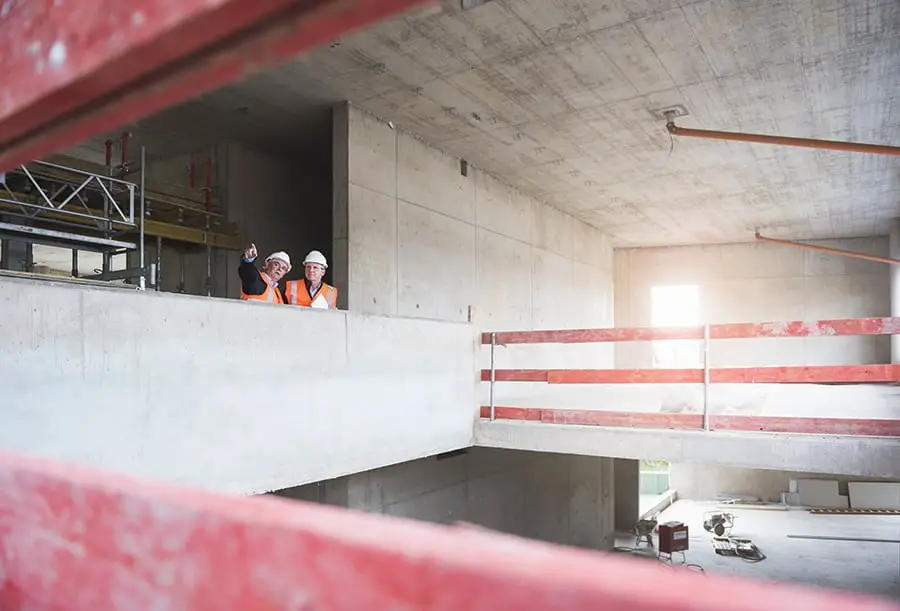
Uneven wall thickness can cause warping, sink marks, and other defects that compromise the integrity of the final product. To avoid these issues, it’s essential to maintain consistent wall thickness throughout your design.
When creating a mold for high-temperature plastics with varying geometries or complex shapes, it’s crucial to ensure that all areas have uniform walls. This will help prevent any weak spots in your finished product and ensure its overall strength and durability.
To achieve this consistency in your mold design process, you should use specialized software tools such as Moldflow® simulation software or SolidWorks® Plastics Simulation Software. These programs allow you to analyze different designs before production begins so that you can identify potential problem areas early on.
Draft Angle
It refers to the degree of taper or slope on the vertical walls of a mold that allows easy removal of the finished product from the mold cavity. Without draft angles, it would be impossible to remove a part from its mold without damaging it.
When molding high-temperature plastics, draft angles are particularly important because these materials tend to stick more tenaciously than other types of plastic. A lack of proper draft can cause parts to become stuck in their molds and lead to costly production delays.
To ensure successful molding with high-temperature plastics, designers must incorporate appropriate draft angles into their designs. The ideal angle will depend on several factors such as material type and wall thickness but generally ranges between 1° and 3° per side.
Incorporating proper design considerations like adequate draft angle is crucial when working with high temperature injection molded plastics since they require specific conditions for optimal results during manufacturing processes.
Advantages of High Temperature Plastics
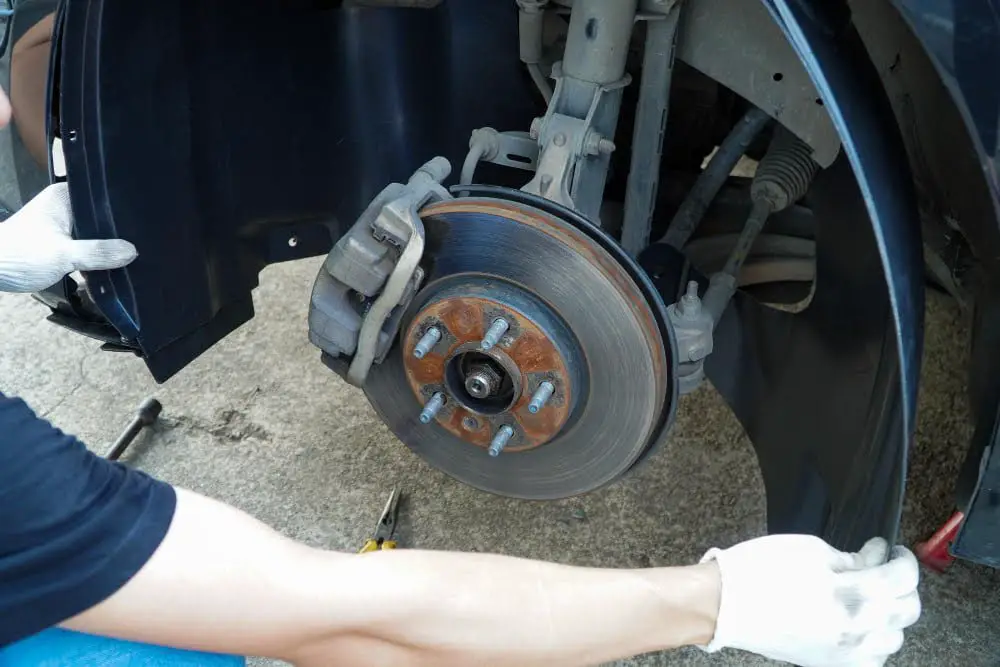
One of the most significant benefits is their ability to withstand extreme temperatures without losing their shape or mechanical properties. This makes them ideal for use in high-heat applications such as aerospace, automotive, and electronics manufacturing.
Another advantage of high-temperature plastics is their excellent chemical resistance. They can resist harsh chemicals and solvents that would otherwise damage other materials like metals or ceramics.
In addition to being heat-resistant and chemically inert, these polymers are also lightweight yet strong enough to replace heavier metal components in many applications. This not only reduces weight but also improves fuel efficiency while maintaining structural integrity.
Moreover, high temperature plastics have a longer lifespan than traditional materials due to their superior durability against wear and tear caused by friction or impact forces.
Applications and Industries
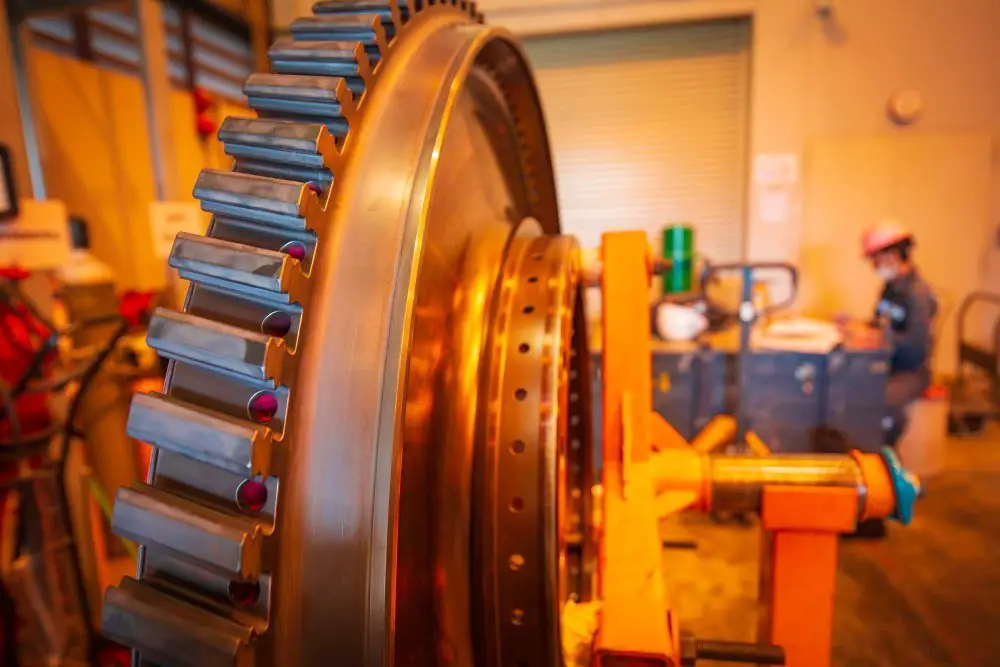
One of the most significant advantages is their ability to withstand high temperatures without losing their shape or integrity, making them ideal for use in harsh environments. These materials are commonly used in aerospace and aviation industries for manufacturing engine components, electrical connectors, and other critical parts that require high heat resistance.
In the automotive industry, high-temperature injection molded plastics are used to manufacture under-the-hood components such as air intake manifolds and valve covers. They also find application in electronics manufacturing where they serve as insulators due to their excellent dielectric properties.
The medical industry has also embraced these materials due to their biocompatibility properties which make them suitable for implantable devices such as pacemakers and surgical instruments that require sterilization at elevated temperatures.
Other notable applications include oil & gas exploration equipment like drill bits; food processing machinery; industrial pumps & valves; chemical processing equipment among others.
Overcoming Challenges
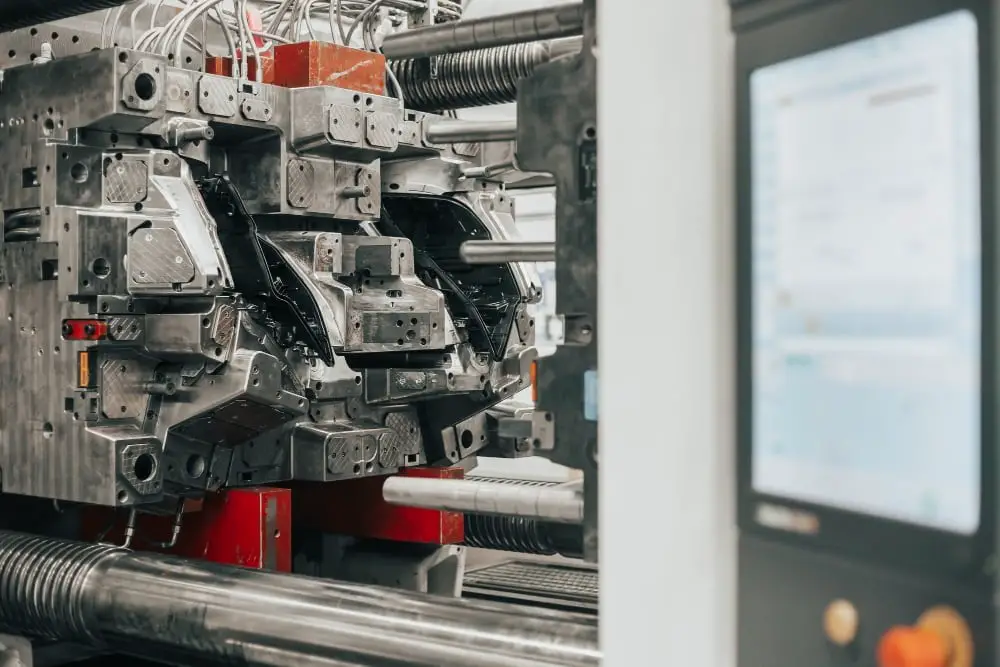
One of the biggest challenges is ensuring that the plastic material maintains its integrity during and after molding. High-temperature plastics are prone to warping, cracking or even melting if not handled properly during manufacturing.
To overcome these issues, it’s essential to select a suitable mold design and material for high-temperature injection molding. The mold should be designed in such a way that it can withstand high temperatures without deforming or breaking down over time.
Another challenge is maintaining uniform wall thickness throughout the part being molded. This requires careful consideration of factors such as draft angle and gate location when designing molds for high temperature plastic parts.
Post-molding processes like annealing may be necessary to relieve internal stresses within parts made from certain types of high temperature plastics like PEEK (Polyether Ether Ketone) which tend to shrink upon cooling leading to dimensional instability.
Challenges and Solutions in High-Temperature Plastic Molding
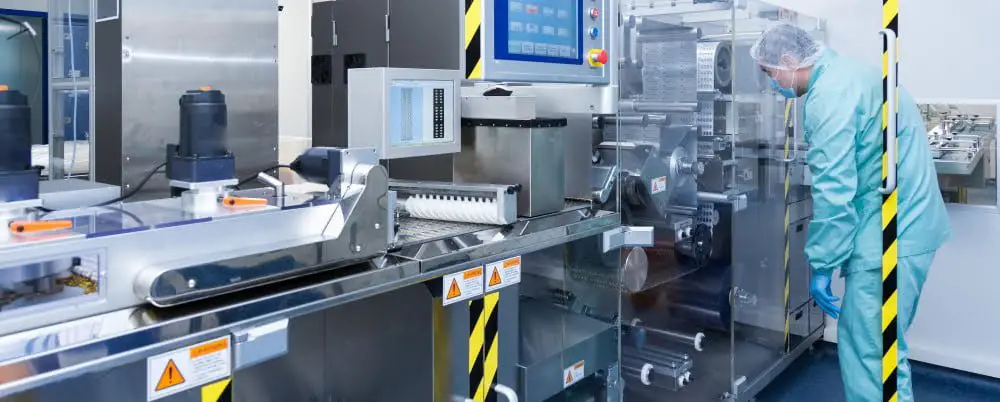
One of the most significant challenges is maintaining consistent temperature control throughout the injection molding process. High-temperature plastics have a narrow processing window, which means they must be processed within a specific temperature range to achieve optimal results.
Another challenge is ensuring uniform wall thickness in molded parts. Variations in wall thickness can lead to warping or distortion, compromising part integrity and functionality.
To overcome these challenges, manufacturers use specialized equipment designed for high-temperature plastic molding processes. This includes molds with heat transfer channels and thermal pins that help maintain consistent temperatures throughout the mold cavity.
Selecting appropriate mold materials such as steel alloys with high thermal conductivity helps ensure proper cooling rates during production runs while minimizing cycle times.
Energy Efficiency
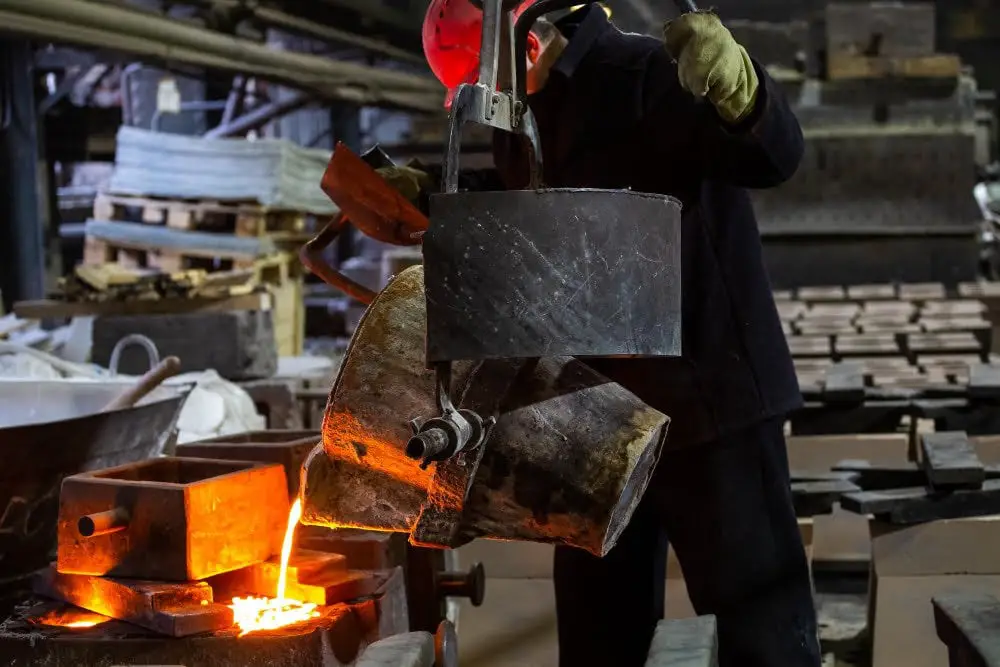
The molding process requires less energy compared to other manufacturing processes, such as metal casting or machining. High-temperature plastics have a lower thermal conductivity than metals, which means they retain heat better and require less energy for heating or cooling.
Moreover, the use of high-temperature injection molded plastics in construction can lead to significant reductions in overall building energy consumption. For example, replacing traditional metal components with plastic ones can reduce the weight of a structure while maintaining its strength and durability.
This reduction in weight translates into lower transportation costs during construction and reduced structural loads on buildings that result in fewer materials used.
Quality Control
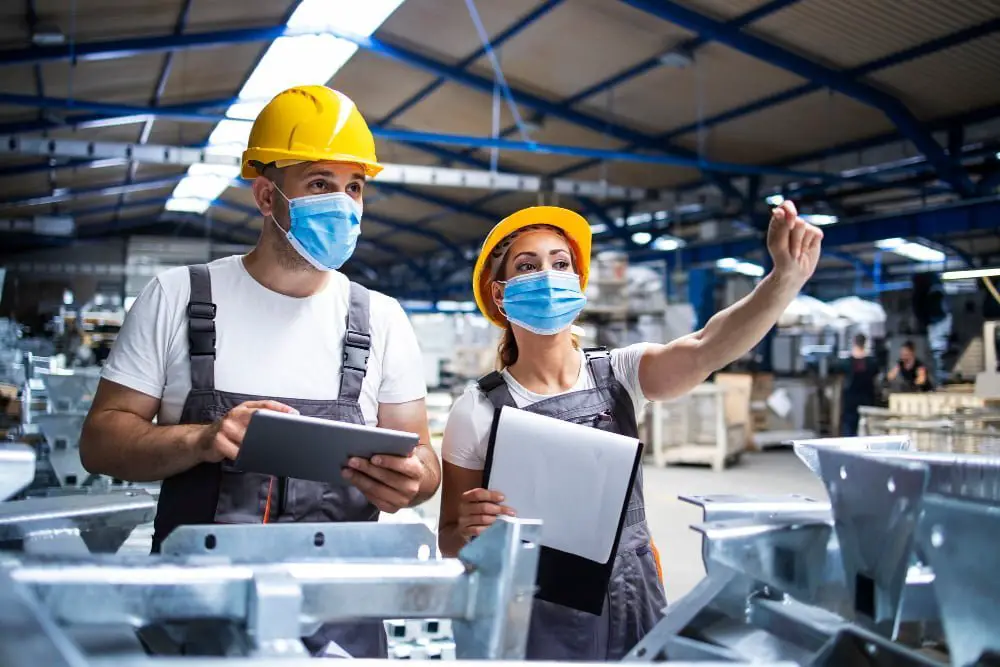
It ensures that the final product meets all required specifications and standards. Quality control starts with material selection, where manufacturers must choose materials that meet specific requirements for strength, durability, and heat resistance.
During production, quality control measures include monitoring temperature and pressure levels to ensure consistency in each batch of molded parts.
After production is complete, quality checks are performed on finished products to ensure they meet customer expectations. These checks may include visual inspections or more advanced testing methods such as x-ray analysis or ultrasonic testing.
In addition to ensuring product quality during manufacturing processes, it’s also important for manufacturers to have a robust system in place for tracking defects or issues that arise during use by customers. This allows them to identify potential problems early on before they become major issues affecting many customers.
Cost Analysis
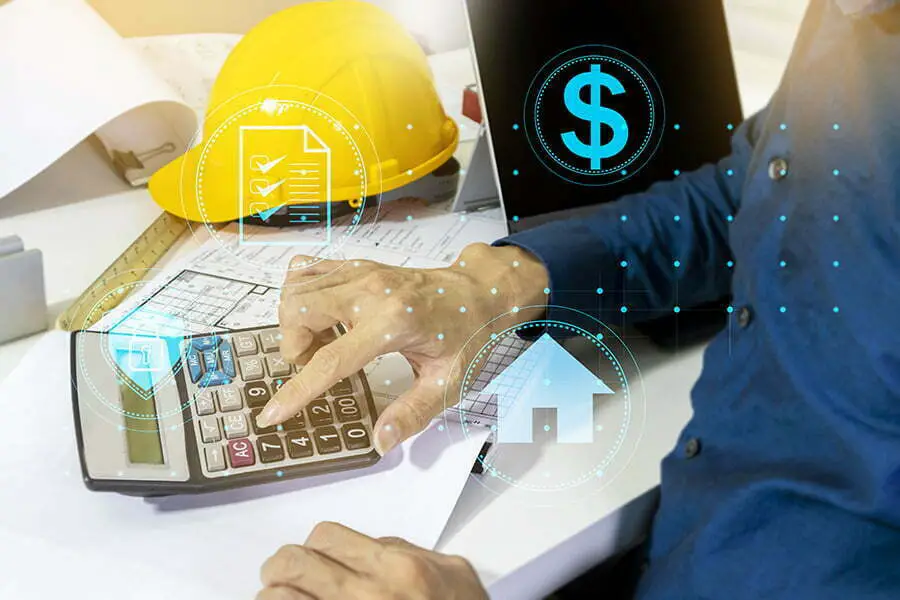
While these materials offer superior performance in extreme temperatures, they can be more expensive than traditional thermoplastics. However, it’s essential to weigh the benefits against the costs and determine if high-temperature plastics are worth investing in for your specific application.
When conducting a cost analysis, it’s crucial to consider all aspects of production and not just material costs. Factors such as tooling expenses, energy consumption during molding processes, post-molding processing requirements (such as machining or finishing), and transportation costs should also be taken into account.
It’s important to note that while initial investment may seem higher with high-temperature injection molded plastics compared to other materials like metal or ceramics; their durability often leads them towards being a more economical choice over time due to their longevity.
Trends and Innovations
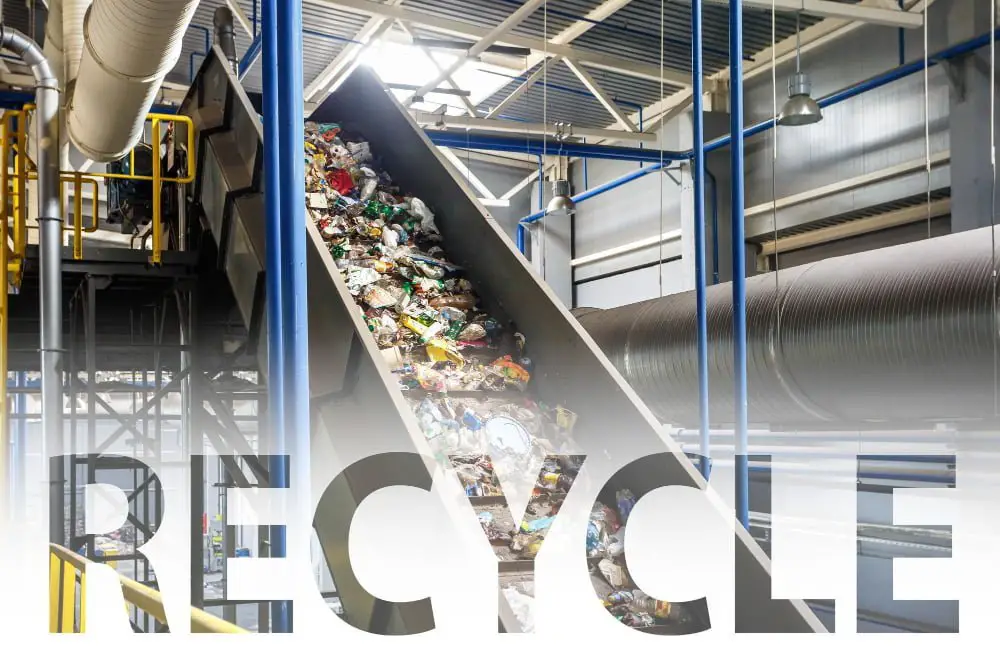
One trend that has emerged in recent years is the use of sustainable materials in plastic production. Manufacturers are now exploring ways to reduce their carbon footprint by using biodegradable or recycled plastics.
Another innovation that has gained popularity is 3D printing technology for creating molds. This method allows for greater design flexibility, faster turnaround times, and reduced costs compared to traditional mold-making techniques.
Furthermore, advancements in material science have led to the development of high-performance polymers with enhanced properties such as improved wear resistance or higher strength-to-weight ratios. These innovations have expanded the range of applications where high-temperature injection molded plastics can be used.
Sustainability Efforts
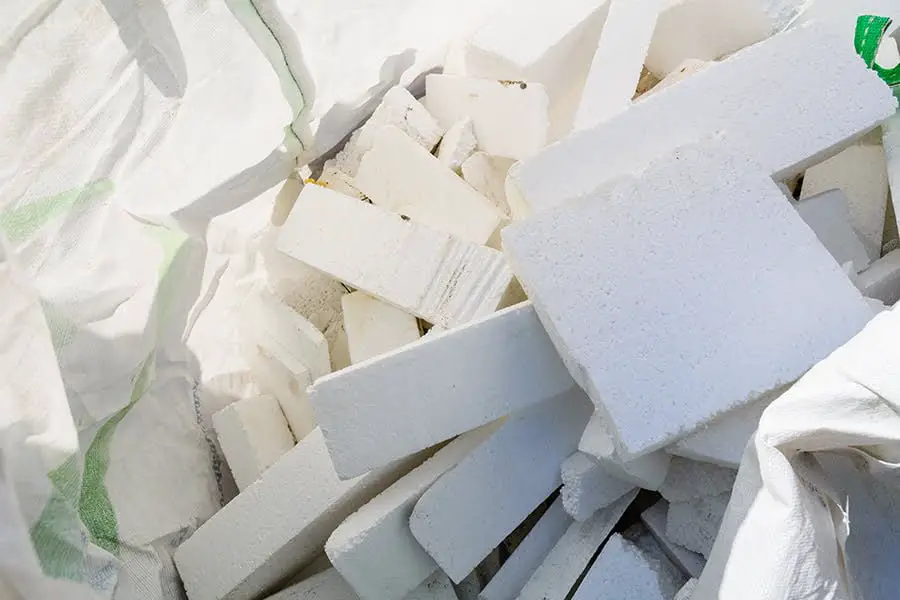
The plastics industry is no exception. High-temperature injection molded plastics have been developed with sustainability in mind, and manufacturers are constantly looking for ways to reduce their environmental impact.
One way that high-temperature plastic manufacturers are reducing their carbon footprint is by using recycled materials in the production process. Recycled materials can be used to create new products without having to extract new resources from the earth.
Another way that high-temperature plastic manufacturers are promoting sustainability is by designing products with longer lifespans. By creating durable and long-lasting products, fewer replacements will be needed over time, which reduces waste and conserves resources.
Some companies have implemented closed-loop systems where they recycle scrap material generated during manufacturing back into raw material feedstock or other useful applications within their own facilities rather than sending it off-site as waste.
Safety Precautions
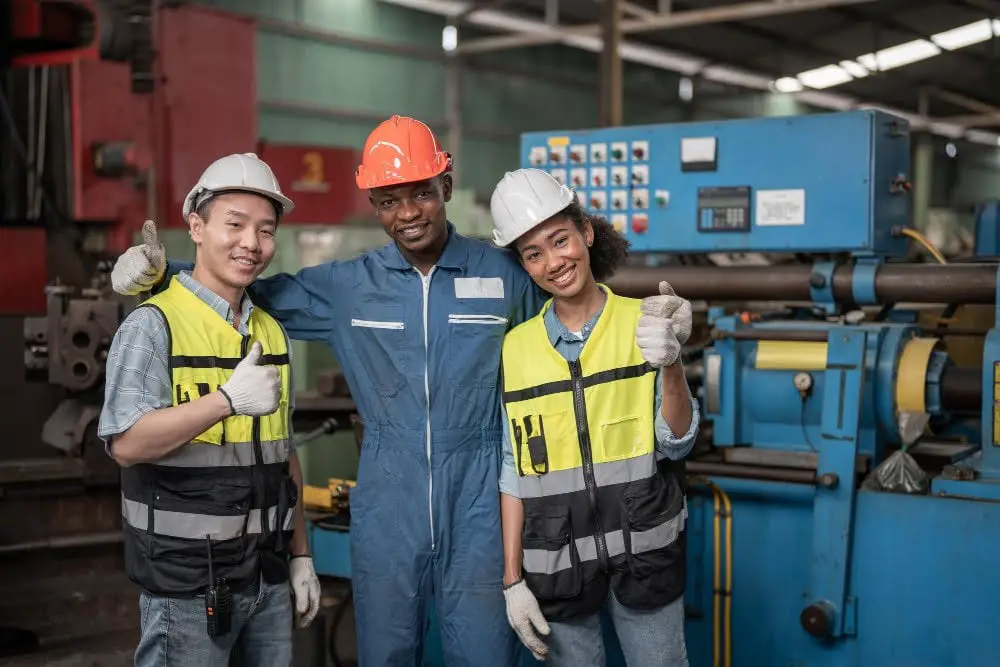
These materials can be hazardous if not handled correctly. The first step in ensuring safety is to wear appropriate personal protective equipment (PPE), including gloves, goggles, and a respirator mask.
It’s also crucial to follow the manufacturer’s instructions for handling and storing these materials properly. High-temperature plastics should be stored in a cool, dry place away from direct sunlight or heat sources that could cause them to degrade prematurely.
During the molding process itself, operators must remain vigilant about potential hazards such as burns from hot molds or molten plastic material splashing out of the mold cavity during ejection.
Post-molding Processes
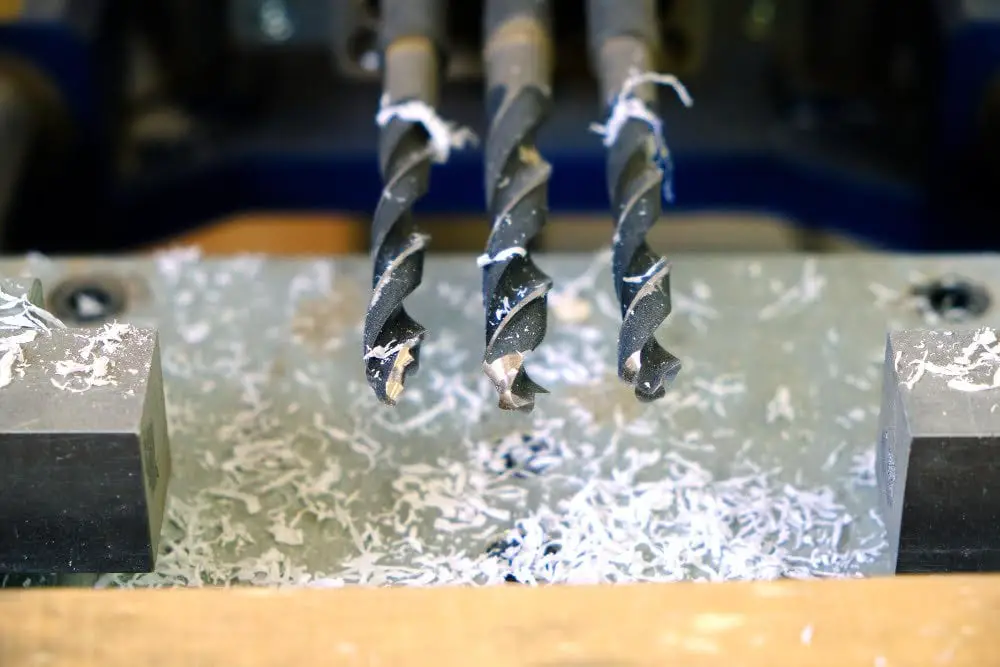
These processes include trimming, drilling, machining and polishing. Trimming is done to remove any excess material from the molded part while drilling is used for creating holes or threads in specific areas of a component.
Machining involves cutting away unwanted material using various tools such as lathes and milling machines. This process can be time-consuming but it allows for greater precision when creating complex shapes or features on a part.
Polishing is also an important post-molding process that enhances surface finish quality by removing any imperfections left behind during manufacturing. It gives parts a smooth texture which makes them more aesthetically pleasing and easier to clean.
Post-molding processes play an essential role in ensuring that high-temperature injection molded plastics meet industry standards for quality and performance.
Case Studies

Let’s take a look at some case studies to understand how these materials are being utilized.
In the aerospace industry, high-temperature plastics such as PEEK and ULTEM® have been used to replace metal parts due to their lightweight properties. For example, Boeing 787 Dreamliner uses over 30 tons of carbon fiber reinforced plastic (CFRP) composites that include PEEK thermoplastic matrix resin for structural components.
In the automotive industry too high temperature resistant polymers are gaining popularity because they can withstand extreme temperatures under the hood without losing their shape or integrity. BMW has replaced metal with Torlon® polyamide-imide in its M-series engines’ throttle valves resulting in weight reduction by up to 50%.
Medical devices also benefit from using high-temperature injection molded plastics since they can be sterilized repeatedly without degrading material quality or performance. The use of Vespel® polyimide is common for surgical instruments like forceps and scissors due to its biocompatibility properties.
Future of High-Temperature Injection Molded Plastics
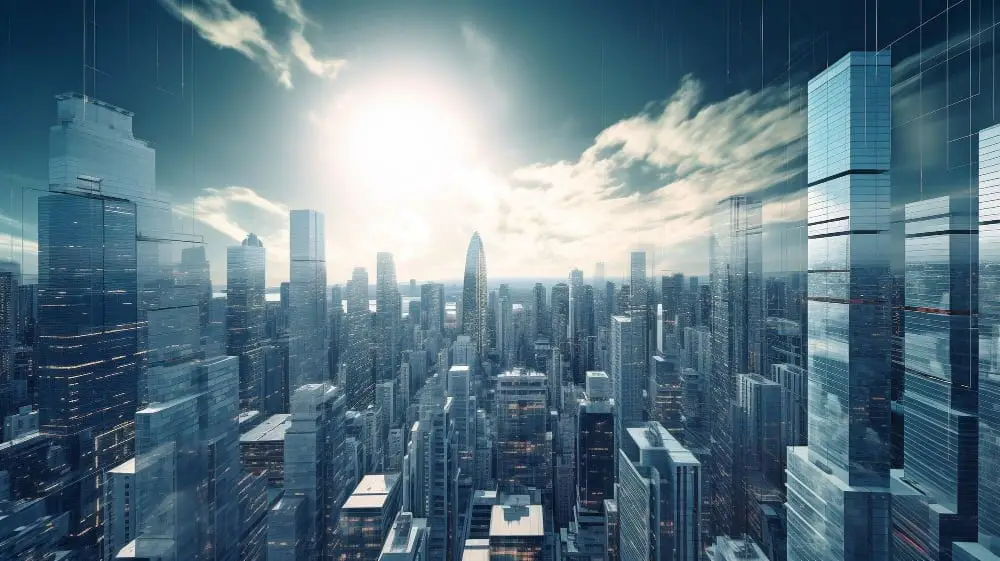
With new materials being developed and innovative manufacturing techniques emerging, we can expect even more applications for these versatile polymers in the years to come.
One area where high-temperature plastics are expected to make a significant impact is in the automotive industry. As electric vehicles become more prevalent, there will be an increased demand for lightweight yet durable components that can withstand extreme temperatures.
High-temperature injection molded plastics offer a viable solution as they are not only strong but also resistant to heat and corrosion.
Another promising application of high-temperature plastic molding is in aerospace engineering. The ability of these materials to withstand extreme temperatures makes them ideal for use in aircraft engines and other critical components that operate under harsh conditions.
Advancements such as 3D printing have opened up new possibilities for creating complex geometries with precision accuracy using high temperature thermoplastic materials like PEEK or ULTEM®.
FAQ
What temperatures can HDPE be injection molded?
HDPE can be injection molded at temperatures ranging from 400°F to 430°F for optimal results.
What is the temperature for plastic injection molding?
The temperature for plastic injection molding is typically between 150 and 350°F (65 and 177°C).
Which Mould is suitable for high temperature?
The suitable moulds for high temperature include Teflon materials, PSU, silicone, polyether imide, polyether ether ketone, liquid crystal polymer, and modified nylon, with some reaching up to 350 degrees Celsius.
Can HDPE plastic be injection molded?
Yes, HDPE plastic can be injection molded as it is a resin typically found in pellet form, designed for high impact, high-stress crack resistance, extreme durability, and excellent processability in molding applications.
What are the optimal processing temperatures for different types of high-temperature plastics in injection molding?
Optimal processing temperatures for high-temperature plastics in injection molding are: PEEK at 700°F (371°C), PPS at 600-650°F (316-343°C), and PPA at 590-610°F (310-321°C).
How do cooling times vary for high-temperature injection molded plastics?
“High-temperature injection molded plastics have longer cooling times due to their elevated thermal properties.”
What considerations should be taken into account when designing molds for high-temperature injection molding?
When designing molds for high-temperature injection molding, one must consider factors such as material selection for mold components, robust cooling systems, and efficient ejection mechanisms.
Recap