Exploring the best polymer clay for jewelry becomes essential because the right choice can profoundly impact the beauty, durability, and uniqueness of your handmade creations.
Key takeaways:
- Sculpey Premo offers durability and vibrant colors for intricate jewelry.
- Kato PolyClay provides a robust finish and true colors after curing.
- Fimo Professional is ideal for intricate designs and colorfastness.
- Cernit Polymer Clay offers a porcelain-like finish and flexibility.
- Consider strength, color options, baking, price, and availability when choosing.
Types of Polymer Clay for Jewelry Making
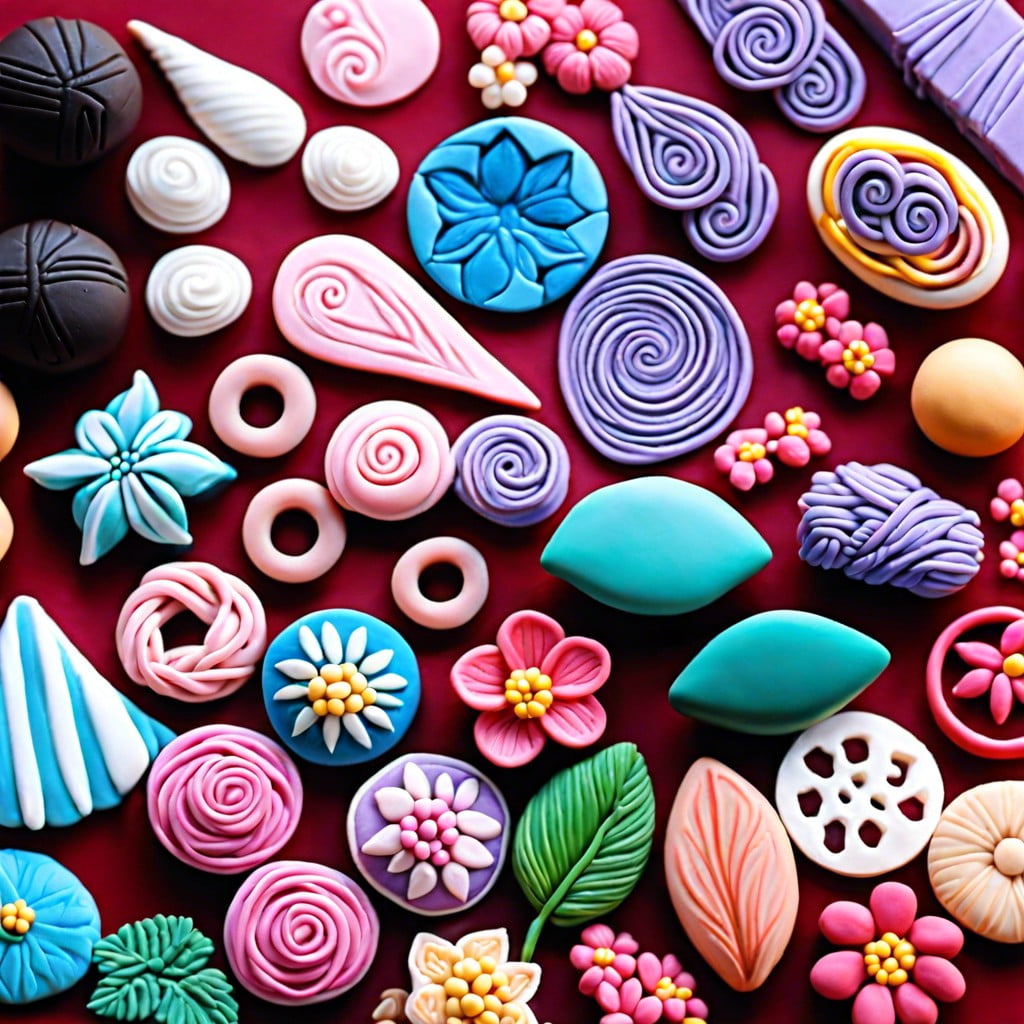
Selecting the right polymer clay is crucial for creating stunning, durable jewelry. Varieties like Sculpey Premo and Kato PolyClay offer exceptional strength and flexibility, ideal for thin or delicate designs.
Fimo Professional is renowned for its firm texture, which is perfect for intricate details and techniques like caning. Cernit Polymer Clay, on the other hand, has a porcelain-like finish that appeals to jewelers seeking a high-end aesthetic.
Each type comes with a spectrum of colors and special effects, providing endless creative possibilities for artisans. However, it’s important to consider individual project requirements, as some clays may be better suited for certain applications over others.
Sculpey Premo
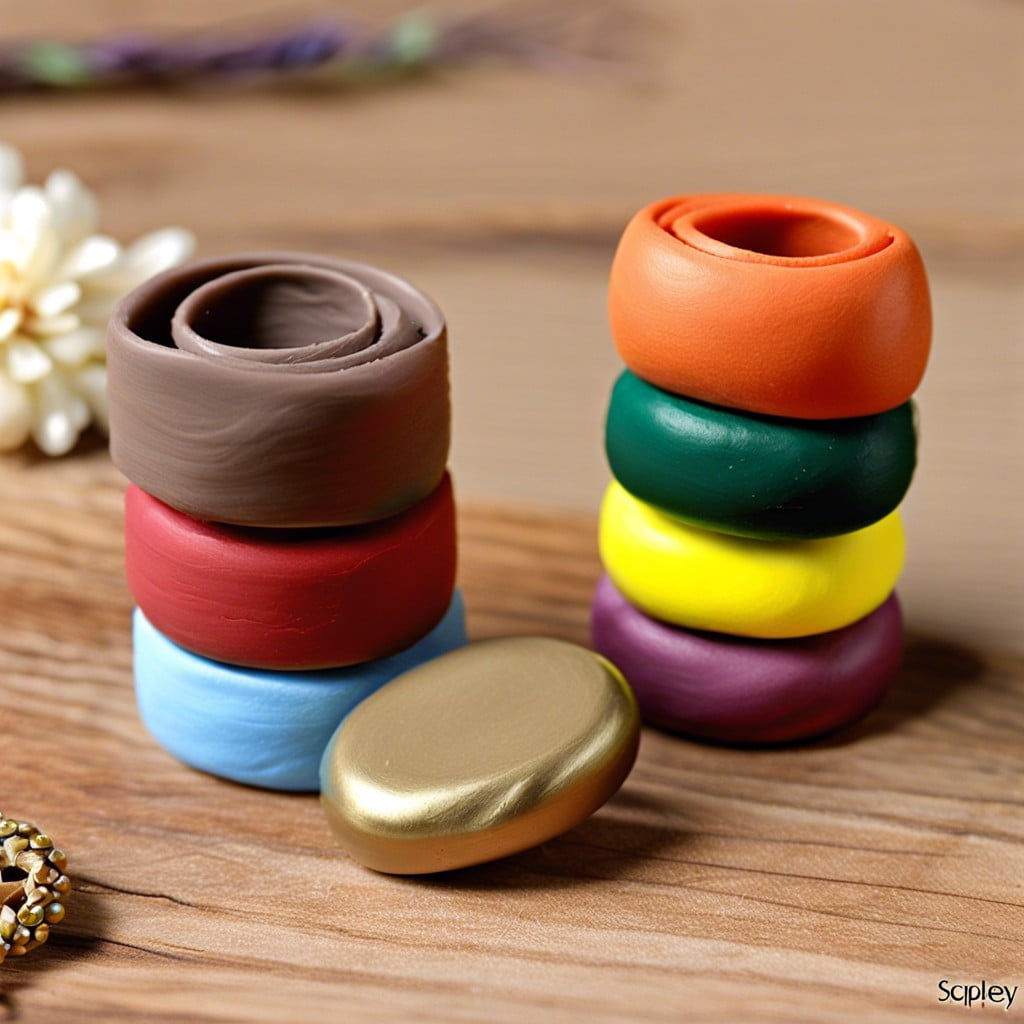
Sculpey Premo stands out for its remarkable durability after baking, which is essential for intricate jewelry that may handle frequent use. Its firm texture allows for detailed sculpting and can be softened slightly by conditioning, which involves kneading the clay to make it more pliable.
An impressive feature of Sculpey Premo is its wide variety of vibrant colors that maintain their richness even after curing. Moreover, it’s compatible with a range of mixed media and special techniques such as millefiori, caning, and image transfers.
To ensure the best outcome, it’s wise to follow the recommended baking temperature of 275°F (135°C) for 30 minutes per 1/4 inch thickness.
Sculpey Premo also offers good value, balancing quality with cost, and is readily available in most craft stores and online.
Kato PolyClay
Kato PolyClay stands out for its remarkable durability and finish, making it a favorite among professional jewelry artists. Its firmer texture requires conditioning, which can be efficiently done by kneading or using a pasta machine. Once conditioned, it maintains its shape well, allowing for precise and intricate designs without fear of distortion during the baking process.
With a wide range of vibrant colors that can be mixed to create custom shades, Kato PolyClay offers artists the freedom to bring their vision to life. The colors remain true after curing, featuring a semi-gloss finish that can be sanded and buffed to a high shine without the need for glazes or varnishes.
For best results, bake Kato PolyClay at 300°F (150°C) for 30 minutes per 1/4 inch (6 mm) thickness. Remember that proper curing is crucial for achieving the optimal strength and finish that this polymer clay is known for.
Fimo Professional
Fimo Professional is renowned for its firm texture, which makes it particularly suitable for creating intricate jewelry pieces, where precision is key.
This attribute allows for detailed sculpting without the clay becoming too soft or sticky. It has a wide range of vibrant colors that can be mixed to create custom hues, providing an extensive palette for artisans to express their creativity.
Given its high level of pigmentation, the colors remain true even after baking, ensuring that the finished jewelry piece looks as intended. The clay also exhibits minimal color shift or fading over time, which is essential for pieces that will be worn and subjected to sunlight.
The curing process for Fimo Professional requires temperatures of roughly around 110°C (230°F) for 30 minutes, depending on the size of the piece. Uniform baking is critical to the durability of the final product, so using an oven thermometer is recommended to ensure the temperature is accurate.
Furthermore, once baked, Fimo Professional exhibits excellent hardness and strength, making it less prone to breakage from everyday wear. This factor is crucial for jewelry items that are often subject to more handling and potential stress. It’s also worth noting that the cured clay can be sanded, drilled, and carved, providing additional options for post-baking customization.
Cernit Polymer Clay
Cernit Polymer Clay shines for its porcelain-like finish, which makes it a preferred choice for jewelry artisans aiming for a high-quality, sophisticated look.
Its composition allows for a remarkable degree of detail, meaning that even the most intricate designs can be effectively realized.
It’s known for its strength post-baking, which translates to durable jewelry pieces able to withstand wear.
The color range of Cernit is expansive, including a number of metallic and translucent shades that can elevate the aesthetic of your creations.
Even after curing, the colors remain vivid and do not fade easily, ensuring that the jewelry retains its beauty over time.
The malleability of Cernit before curing is just right—not too soft nor too hard—which facilitates shaping and blending without premature hardening.
Despite its firm texture, once conditioned, it works smoothly, making it a good option even for those new to polymer jewelry.
While the price point may be slightly higher than other polymer clays, the premium finish and lasting durability often justify the cost for professional jewelry makers.
Remember, when baking Cernit, it is important to follow the temperature guidelines closely to avoid brittleness or discoloration, ensuring the perfect result for your creations.
Factors Influencing the Choice of Polymer Clay
When selecting polymer clay for jewelry, consider several important characteristics.
Strength and Flexibility: Jewelry is subject to wear and tear, so choose a clay that, once cured, offers a balance of sturdiness and flexibility to avoid breakage.
Color Options and Effects: The available colors and the ability to blend them to create custom shades are crucial for design variety. Some clays also offer effects like metallic, glitter, or translucent finishes to enhance your creations.
Baking and Curing Considerations: Each clay has specific baking instructions to achieve the best results. Pay attention to temperatures and times to ensure your pieces are properly cured without discoloration or burning.
Price and Availability: Your budget and the ease of obtaining the clay might affect your choice. While some clays are widely available at local craft stores, others might be more specialized and require online purchase.
These factors should guide you towards the clay that will best suit your jewelry projects, making them beautiful, durable, and unique.
Strength and Flexibility
When choosing a polymer clay for jewelry, considering the material’s post-baking strength and flexibility is crucial, as these properties directly affect the durability and wearability of the finished pieces.
Post-Baking Strength: Look for a clay that when cured, can withstand slight bending without cracking, important for thin pieces like earring posts or delicate bracelets.
Flexibility: A certain level of flexibility can prevent breakage from accidental drops or impacts, especially important for larger pieces like bangles that might experience more stress.
Conditioning: Proper conditioning of the clay before use can enhance both strength and flexibility.
Baking Times: Follow the recommended baking times and temperatures as underbaking makes the clay brittle, while overbaking might turn it brown and affect its integrity.
Remember, the right balance between these properties will prevent your jewelry from becoming too brittle or too malleable, preserving its shape and quality over time.
Color Options and Effects
The diverse palette available in polymer clays is pivotal for jewelry artists who aim to create pieces that stand out. Different brands offer their unique range of colors, from vibrant primaries to subtle pastels and complex metallics. Moreover, some clays are imbued with special effects like translucency, which can mimic the look of glass or semi-precious stones when cured.
For those seeking a custom hue, many polymer clays can be mixed, much like paint, to create a specific shade or gradient. Texture effects, such as glitter or mica particles, can be found within certain clays, adding a distinctive sparkle or pearlescent sheen to finished pieces. Keep in mind that the final color and effect may change slightly after baking, depending on the clay’s composition and the temperature used.
Understanding color permanence is also essential. Look for polymer clays known for their colorfastness to ensure that your jewelry maintains its vibrancy over time. High-quality options are less likely to fade or change color with exposure to light or skin contact.
For intricate designs, consider clays that allow for crisp detail without bleeding or color migration during conditioning or baking. With the right choice of color and effect, your polymer clay jewelry will not only be attractive but express your creative vision with precision.
Baking and Curing Considerations
Ensuring that your polymer clay jewelry is properly baked is crucial for its durability and longevity. Here’s what you need to consider when baking and curing your creations:
1. Temperature Accuracy: Follow the manufacturer’s recommended baking temperature. Use an oven thermometer to verify your oven’s accuracy to prevent under or over-baking, which can compromise the strength of the piece.
2. Baking Time: Thicker pieces may require longer baking times than what is prescribed. It’s often better to err on the side of baking a little longer at the correct temperature rather than higher temperatures for shorter periods.
3. Oven Type: Convection ovens typically provide a more even heat distribution compared to toaster ovens, which can have hot spots. Whichever you use, preheat it properly.
4. Surface: Bake your jewelry on a ceramic tile or a piece of parchment paper to avoid shiny spots and ensure even heat distribution. Never bake directly on metal or unprotected surfaces.
5. Tenting: Covering your pieces with an aluminum foil tent can protect the colors from darkening and prevent scorching.
6. Post-Baking: Some clayers ‘anneal’ their finished pieces–a process of slowly cooling the piece to prevent thermal shock and potential cracking. This often entails leaving the piece in the oven to cool gradually or bathing it in warm water post-baking.
Always test bake a sample of your clay to fine-tune the process before baking your final jewelry pieces.
Price and Availability
Polymer clay’s cost can vary significantly depending on brand reputation, specialized formulations, and pigment quality. Premium brands like Fimo Professional and Cernit usually command higher prices due to their renowned strength and extensive color palettes, catering to both amateurs and professionals.
On the other hand, Sculpey’s various lines offer a range of prices, with options like Sculpey III being more affordable and ideal for hobbyists.
Bulk purchasing often leads to cost savings, so consider buying larger packs if you craft regularly. Additionally, specialty and metallic colors may come at a premium compared to standard ones. Keep an eye out for sales at local craft stores or online discounts, which can reduce costs significantly over time.
Availability is another crucial factor. While some brands like Sculpey and Fimo are widely available at most craft stores, others like Kato PolyClay might require a special order or online purchase. If you live in an area with limited access to craft stores, online shopping will be a valuable resource, but remember to account for shipping times and costs when planning your projects.
Comparison of Popular Polymer Clay Brands for Jewelry
Each brand of polymer clay has its unique set of characteristics that cater to different jewelry-making needs.
- Sculpey Premo is renowned for its firmness which makes it great for detailed work and its flexibility post-baking reduces the risk of breakage. It comes in a broad spectrum of colors, including metallics and translucents, making it a versatile choice for artists.
- Kato PolyClay hardens to a robust finish and maintains vivid colors after curing. It’s a bit firmer than other brands, so it may require more conditioning but provides high-quality results for professional-looking jewelry.
- Fimo Professional has a smooth and firm consistency ideal for intricate designs. It boasts excellent shape stability during baking, ensuring that your delicate shapes don’t distort.
- Cernit Polymer Clay has a porcelain-like finish and is highly flexible, which is perfect for thin pieces that need to stand up to wear and tear.
When deciding on a brand, consider your project’s requirements—detail, strength, color fidelity, and finish. Also, think about your personal working style and whether you prefer a firmer or softer clay. Each brand offers unique benefits, so you may find yourself using different types for specific projects or effects.
Tips and Techniques for Working With Polymer Clay
To create stunning polymer clay jewelry, consider these practical pointers:
1. Conditioning Clay: Ensure your clay is properly conditioned before sculpting. This increases flexibility, making it easier to shape and blend without cracking.
2. Clean Workspace: Keep your working area and tools clean to prevent dust and lint from embedding into the clay. Wipe surfaces with a damp cloth and wash your hands regularly.
3. Blending Colors: Mix colors thoroughly for a uniform shade or slightly for marbled effects. Experiment with color gradients for unique designs.
4. Tools: Invest in quality sculpting tools. Items like needle tools, rollers, and texture sheets can enhance detail and finish.
5. Thickness Consistency: Maintain uniform thickness to prevent weak spots. Use a pasta machine or acrylic roller for even sheets.
6. Avoiding Fingerprints: Fingerprints can be minimized by handling the clay with latex gloves or smoothing surfaces with a soft tool.
7. Curing Techniques: Follow the manufacturer’s instructions for curing temperature and time. Use an oven thermometer to ensure accuracy.
8. Sanding and Buffing: After baking, sand your pieces with wet/dry sandpaper to achieve a smooth finish. Buffing can be done by hand or with a machine for extra gloss.
9. Protective Coating: Apply a sealant like a varnish or resin to protect the surface and enhance depth and shine, ensuring your jewelry lasts.
Remember, patience is key when mastering polymer clay techniques, so take your time to refine your skills for the best results in your jewelry creations.
Baking Tips for Durable Jewelry Pieces
For your polymer clay jewelry to stand the test of time, proper baking is crucial. Follow these essential tips:
1. Check the Package Instructions: Different clays have varying baking temperatures and times. Adhere to the manufacturer’s guidelines for best results.
2. Use an Oven Thermometer: Ovens can be inaccurate. A thermometer ensures you’re baking at the correct temperature to prevent burning or under-curing.
3. Protect Your Pieces: Tent your creations with aluminum foil during baking to shield them from direct heat and to prevent scorching.
4. Baking Surface Matters: Bake on ceramic tiles or parchment paper to distribute heat evenly and avoid shiny spots on the bottom of your pieces.
5. Thickness Counts: The thicker the piece, the longer it needs to bake. Conversely, thin, delicate parts require less time in the oven to avoid brittleness.
6. Post-Baking Bath: For added strength, immediately plunge your hot, baked pieces into ice water. This process, known as quenching, can increase their durability.
Follow these practices to ensure your crafted jewelry withstands wear while retaining its beauty and integrity.
Common Questions and Troubleshooting
Why is my polymer clay breaking after baking?
Brittle clay results from either underbaking or a too low temperature. Ensure that you follow the recommended temperature settings and baking time provided by the clay manufacturer. It’s essential to use an oven thermometer to monitor the temperature for accuracy.
How can I prevent fingerprints on my clay?
Fingerprints can be minimized by working with cool hands and rolling the clay with an acrylic roller. If fingerprints do appear, gently smooth the surface with a piece of plastic wrap or a dab of baby oil before baking.
Can I mix different brands of polymer clay?
Yes, mixing brands is generally okay and can often yield a new clay with desirable properties from both. However, always make sure to test the mixed clay’s durability after baking, as different formulas may affect the strength of the final product.
What should I do if the clay is too soft or sticky?
Soft or sticky clay can be firmed up by refrigerating it for a short time. You may also leach excess plasticizers by sandwiching the clay between sheets of paper for a few hours. This makes it easier to handle intricate details in jewelry pieces.
My clay colors seem to darken after baking, why is this happening?
This darkening effect can be caused by overbaking or baking at too high a temperature. Always check the accuracy of your oven’s temperature with a separate oven thermometer and bake for the recommended time. Covering your pieces with aluminum foil can also help prevent color darkening.
Where to Find High-Quality Polymer Clay
High-quality polymer clay is readily available both online and in craft stores. Here’s where you can get your hands on the best varieties:
- Online Marketplaces: Look for reputable sellers on platforms like Amazon, Etsy, and eBay who specialize in crafting supplies.
- Specialized Craft Stores: These stores often provide a wide selection of brands and colors along with expert advice.
- Direct from Manufacturers: Purchasing directly from the manufacturer’s website ensures that you get fresh, properly stored clay.
- Art Supply Shops: They stock a broad range of materials for professional artists, including premium polymer clays.
- Community Recommendations: Join online forums or social media groups focused on polymer clay to get suggestions from experienced users.
Remember to check reviews to ensure the quality and authenticity of the product before making a purchase.
FAQ
Which clay is best for jewellery making?
The best clay for jewellery making is EClay Terracotta Clay.
Is Sculpey or FIMO better?
Considering its strength and flexibility for modeling and handling, Super Sculpey or Sculpey Firm are better choices than Fimo.
Is FIMO effect good for jewelry?
Yes, FIMO professional, being a firmer clay, is well-suited for jewelry-making due to its ability to hold a delicate structure better.
What is the best finish for polymer clay jewelry?
The best finish for polymer clay jewelry is either light-bodied Pledge Floor Gloss or Varathane Gloss Floor Finish as they dry quickly without reacting with the clay, or a crystal-clear varnish which is frequently used by artists.
How does temperature affect the curing process of polymer clays like Sculpey and FIMO?
Temperature greatly affects the curing process of polymer clays like Sculpey and FIMO as higher temperatures speed up the curing process, but excessive heat can cause the clay to burn or crack.
Can polymer clay jewelry be repaired if damaged, and how?
Yes, damaged polymer clay jewelry can be repaired by re-baking the item after applying fresh clay or liquid polymer to the damaged parts.
What are the key differences between pre-colored and paintable polymer clays for jewelry making?
Pre-colored polymer clays eliminate the need for painting after sculpting, while paintable polymer clays provide greater flexibility with customization through post-sculpting application of paint colors.
Polymers, often seen in the form of plastics and resins, are widely used in construction due to their durability, ease of manufacture, versatility, and resistance to harsh environmental conditions.
Moving to polymers in construction, they come in various forms – plastics, foams, rubbers, and composites – and can serve a multitude of functions within a construction project. Their versatility, durability and cost-effectiveness make them highly desirable in this industry
Polymers, in the forms of plastics, foams, rubbers, and composites, are highly desired in the construction industry due to their versatility, durability, and cost-effectiveness.
Polymers are long-chain molecules that can add strength, flexibility, and durability to construction materials, making them essential in the development of strong, weather-resistant buildings and infrastructures.
Polymers in construction bring substantial longevity to structures. Due to their resistance to corrosion, the need for maintenance or replacement is significantly reduced. Their inbuilt flexibility is also beneficial, permitting adjustments to building design which could be cost-prohibitive with metal or wood. Polymer materials can also stand up to extreme weather conditions, including rain, humidity, and UV light, making them ideal in various climates and geographic locations
Polymers in construction contribute to the durability of structures due to their corrosion resistance, cost-effective flexibility in design alterations, and resilience in extreme weather conditions including rain, humidity, and UV light.
Polymers, versatile materials with high durability and resistance to various environmental conditions, are extensively used in the construction industry in applications ranging from structural elements to insulation.
Despite these benefits, using polymers in construction comes with heated environmental and sustainability debates. Many plastics are notably difficult to recycle, leading to concerns about waste disposal. Advancements continue in the development of biodegradable polymers and recycling techniques to help mitigate these environmental implications
Yes, the use of polymers in construction has sparked environmental and sustainability concerns due to their difficulty to recycle, however, ongoing advancements in the development of biodegradable polymers and improved recycling techniques are aimed at mitigating these environmental implications.
Polymer usage in construction primarily involves enhancing durability, resistance to environmental factors, and improving aesthetic appeal due to the availability in various colors and finishes.
The field of construction polymers is vast and evolving. Examples of specific applications include: Polystyrene foam used as insulation, Polyvinyl Chloride (PVC) for plumbing pipes and vinyl siding, and Polyethylene for vapor barriers and exterior panels
Construction polymers, such as Polystyrene foam for insulation, Polyvinyl Chloride (PVC) for plumbing pipes and vinyl siding, and Polyethylene for vapor barriers and exterior panels, are integral to modern building techniques.
Polymers, large molecules composed of repeated subunits, are extensively used in construction due to their durability, resistance to environmental conditions, insulation properties, and flexibility, offering applications in concrete, coatings, insulation, adhesives, sealants, and composite materials.
In conclusion, polymers have carved out a substantial role within the construction industry. Their strengths lie in their versatility, longevity, and cost-effectiveness. However, as the industry grows, so does the pressure to address environmental and sustainability challenges related to their use. The industry needs to balance these challenges with the advantages if polymers are to continue playing a pivotal part in modern construction
Indeed, polymers offer versatility, longevity, and cost-effectiveness in construction, but addressing environmental and sustainability challenges is vital for their ongoing use in the industry.
Recap