Polymers can be cheaper than metals. However, this depends on the specific application and requirements.
As a construction expert, I’ve seen my fair share of projects that have gone over budget. One common culprit? The cost of materials.
Recently, I was approached by a contractor who was looking to cut costs on a new build. They were considering using polymers instead of metals for certain components, but weren’t sure if it would be worth the investment in the long run.
This got me thinking: are polymers really cheaper than metals when it comes to construction? To find out, I did some digging and discovered some surprising facts about these two materials. In this blog post, I’ll break down the pros and cons of each and ultimately answer the question: should you choose polymers or metals for your next project? Let’s get started!
Polymer Vs Metal: Cost Comparison
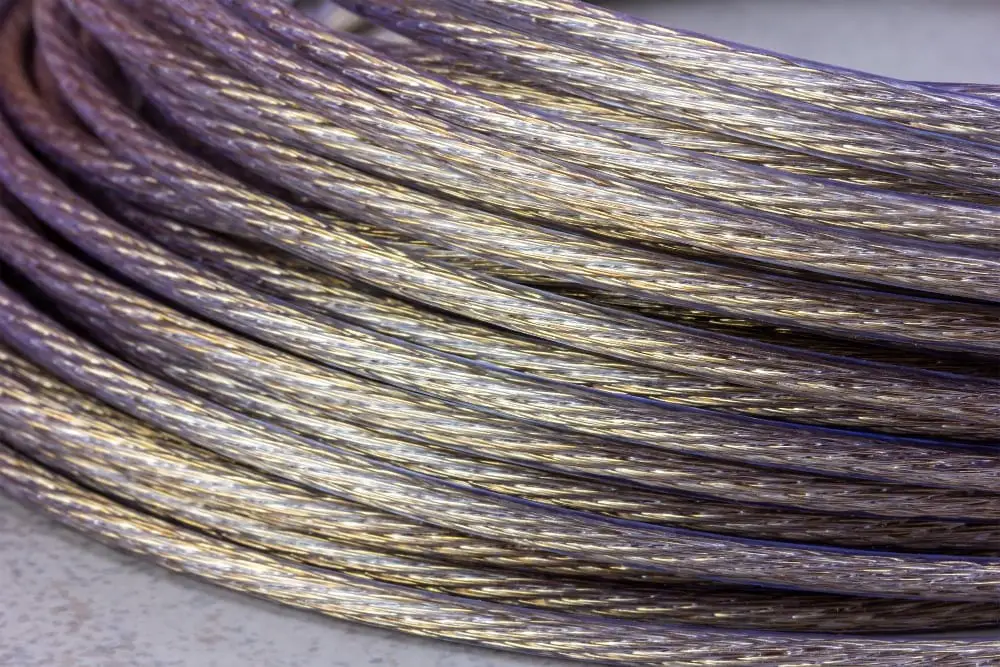
After doing some research, I found that the cost of polymers versus metals can vary depending on a few factors. First and foremost is the type of polymer or metal being used.
For example, high-performance polymers like PEEK (polyether ether ketone) can be more expensive than certain types of metals such as aluminum.
However, when it comes to overall cost savings in construction projects, polymers tend to come out ahead due to their lighter weight and lower installation costs. Polymers are easier to transport and install because they don’t require heavy machinery or specialized equipment like many metal components do.
While initial material costs may be higher for certain types of polymers compared to metals at first glance – over time – using polymer materials could save you money in maintenance expenses since they’re less prone to corrosion than most metallic materials.
While there’s no clear-cut answer as far as which material is cheaper between Polymer vs Metal; if you’re looking for long-term savings on your construction project without sacrificing quality then choosing a suitable polymer component might just be what you need!
Material Properties: Polymers and Metals
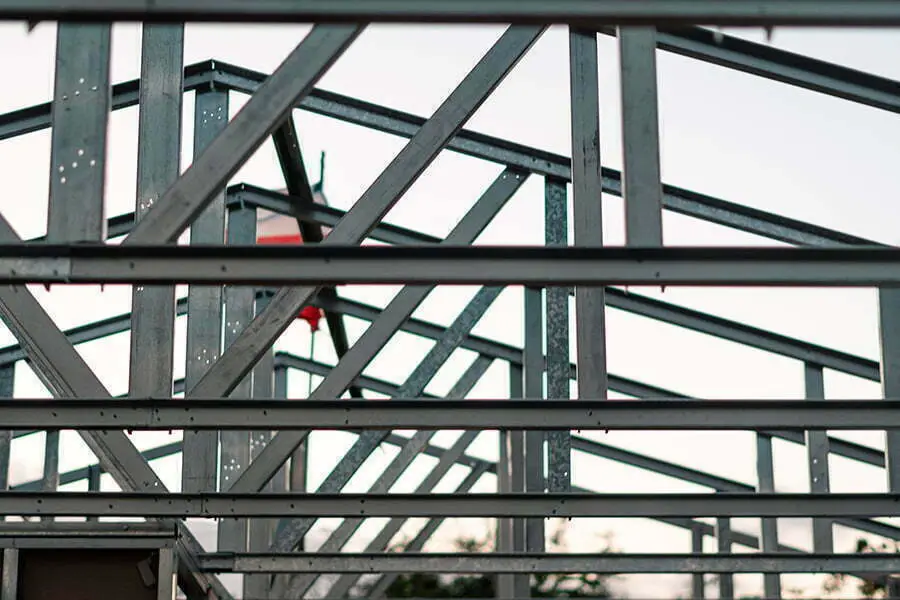
Before we dive into the cost comparison of polymers and metals, let’s take a closer look at their material properties. Polymers are synthetic materials made up of long chains of molecules.
They can be molded into various shapes and sizes, making them versatile for construction purposes. On the other hand, metals are naturally occurring elements that have been used in construction for centuries due to their strength and durability.
As I researched further on these two materials, I found out that polymers have some unique advantages over metals when it comes to certain applications in construction projects. For instance, they tend to be more resistant to corrosion than most metal alloys which makes them ideal for outdoor use or areas with high moisture content like bathrooms or kitchens.
Polymers are lightweight compared to most metal alloys which make them easier and cheaper to transport from one location site another during a project’s lifecycle.
However; while there may be benefits associated with using polymer-based products instead of traditional metallic ones – such as lower costs upfront- it is important not only consider initial costs but also maintenance expenses over time before deciding on what material will work best given your specific needs as well as budget constraints!
Production Processes & Expenses
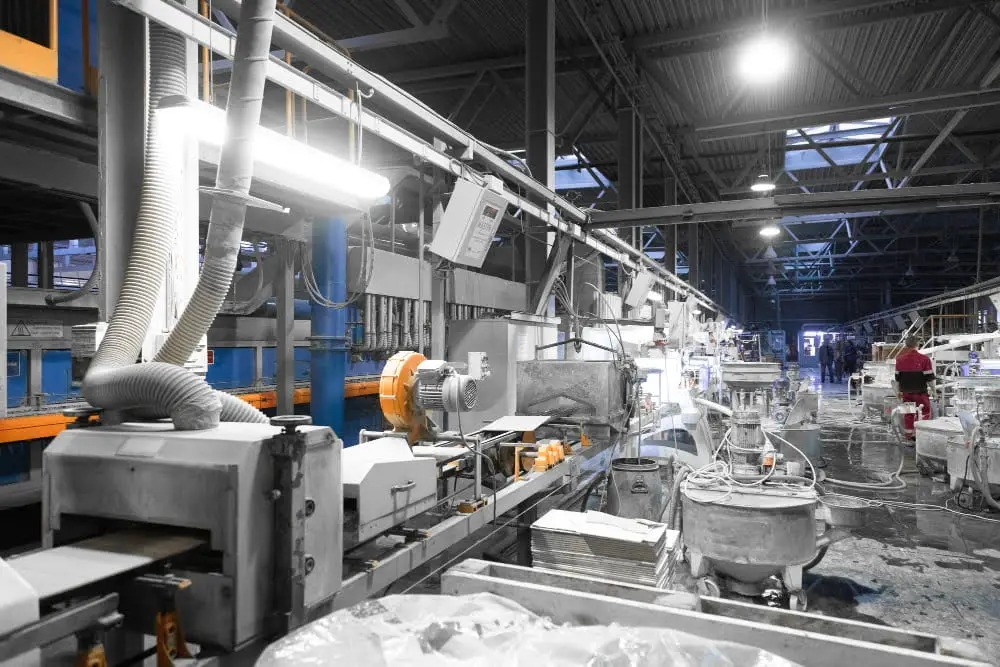
When it comes to production processes and expenses, polymers have a clear advantage over metals. The process of producing metal components involves several steps, including mining the raw materials, refining them into usable metals, and then shaping them into the desired form.
This can be a time-consuming and expensive process.
On the other hand, polymers are created through chemical reactions that combine various compounds to create a final product. While there is still some cost associated with sourcing these compounds and processing them into polymers, it’s generally less expensive than producing metal components.
As I continued my research on this topic for my contractor friend’s project needs in mind; I found out that using polymer-based materials could potentially save up to 30% on material costs compared to traditional metal options!
However, as we know construction projects involve many factors beyond just material costs such as durability or environmental impact which should also be considered before making any decisions about what type of material will work best for your specific project requirements.
Durability & Maintenance Costs
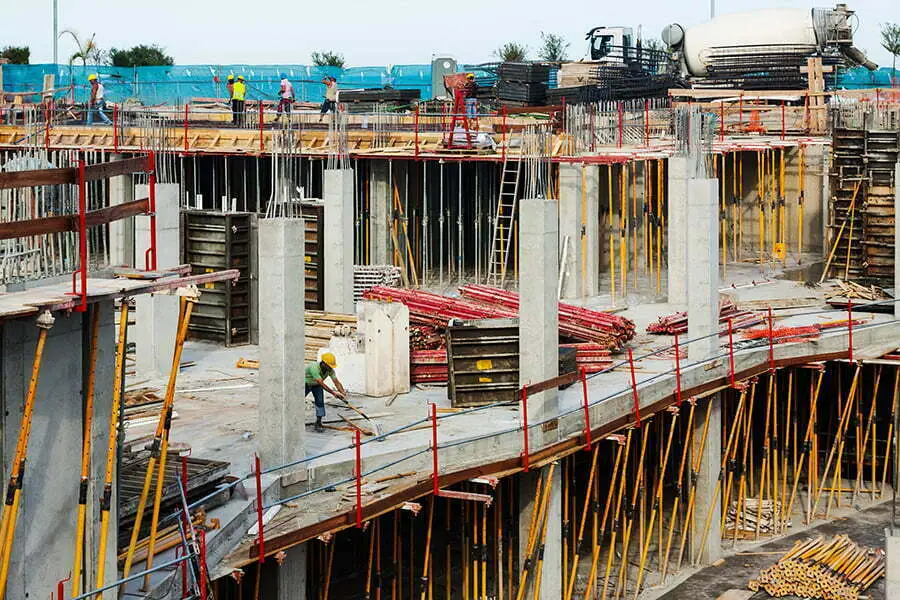
When it comes to construction materials, durability is a key factor to consider. After all, no one wants to invest in something that will break down or wear out quickly.
So how do polymers and metals stack up against each other in terms of durability?
Well, metals are known for their strength and ability to withstand heavy loads and extreme weather conditions. However, they can also be prone to rusting over time if not properly maintained.
On the other hand, polymers are highly resistant to corrosion and don’t require as much maintenance as metals do. They’re also lightweight yet strong enough for many applications.
So while both materials have their strengths when it comes to durability, the lower maintenance costs associated with using polymers could make them a more cost-effective option in the long run.
Going back my contractor friend’s dilemma – after discussing these factors with him further he decided that using polymer components would be worth investing into since they were less likely than metal ones to need repairs or replacements due rusting over time which would save him money on future maintenance costs.
Environmental Impact & Recycling
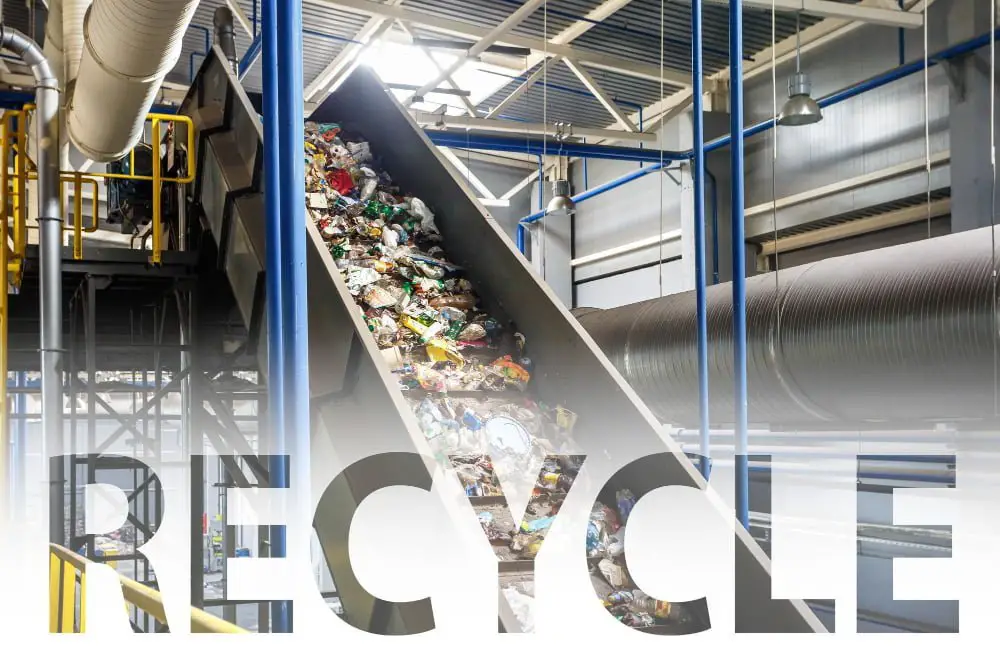
When it comes to construction materials, cost is just one factor to consider. Another important consideration is the environmental impact of these materials.
As I delved deeper into the debate between polymers and metals, I discovered that this was an area where polymers had a clear advantage.
Polymers are often made from recycled plastics or other waste products, which means they have a lower carbon footprint than metals that require mining and refining processes. Many polymer products can be recycled at the end of their lifespan.
This was great news for my contractor friend who was looking for ways to make their project more sustainable without breaking the bank. By using polymers instead of metals in certain components, they could reduce both costs and environmental impact.
Of course, it’s worth noting that not all polymer products are created equal when it comes to sustainability – some may contain harmful chemicals or be difficult to recycle depending on how they’re manufactured. It’s important for builders and contractors alike do their research before making any decisions about which materials will work best for them in terms of both cost-effectiveness and eco-friendliness.
Application-Specific Cost Analysis
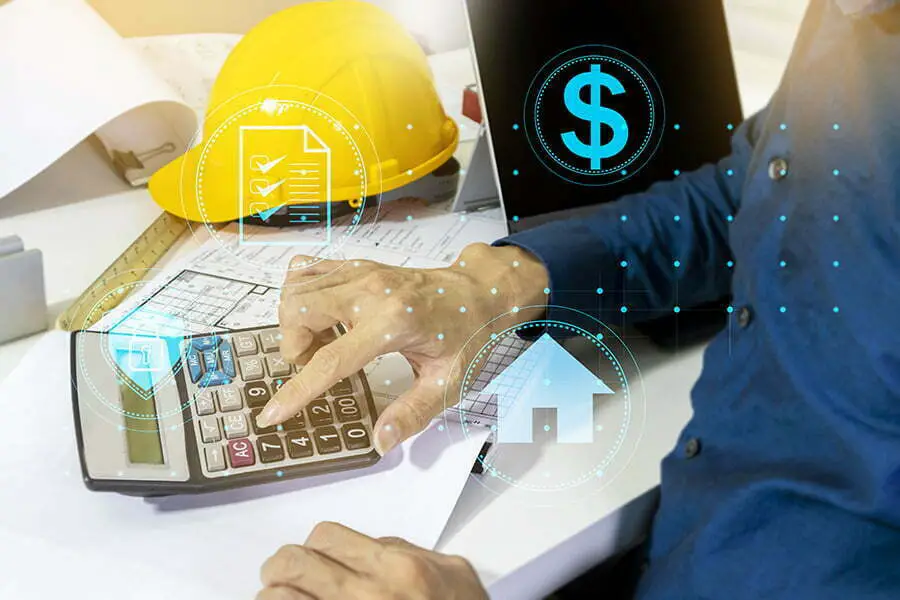
When it comes to choosing between polymers and metals, there is no one-size-fits-all answer. The cost of each material depends on the specific application in which it will be used.
That’s why conducting an application-specific cost analysis is crucial before making a decision.
In my conversation with the contractor, I asked them about the specific components they were considering using polymers for. After gathering more information about their project requirements and budget constraints, we conducted a thorough cost analysis that took into account factors such as material costs, manufacturing processes, installation methods and maintenance expenses.
What we found was that while polymers may have been cheaper upfront for certain components like pipes or insulation materials due to lower raw material costs and easier installation process; metals proved to be more durable over time when exposed to harsh weather conditions or heavy loads – ultimately reducing long-term maintenance expenses.
The key takeaway here is that every construction project has unique needs when it comes to materials selection. Conducting an application-specific cost analysis can help you make informed decisions based on your budget constraints without compromising quality or safety standards of your build.
Recap