Discover the various types of thermosetting plastics and their unique properties as we delve into this fascinating world of heat-resistant materials!
In today’s construction industry, thermosetting plastics have become an essential material. They are used in various applications such as insulation, adhesives, coatings, and composites.
But what exactly are thermosetting plastics? Well, they are a type of polymer that undergoes a chemical reaction during the curing process and becomes irreversibly hardened. In this blog post, we will explore the different types of thermosetting plastics available in the market and their unique properties.
So let’s dive into this exciting world of polymers!
Phenol Formaldehyde Resins
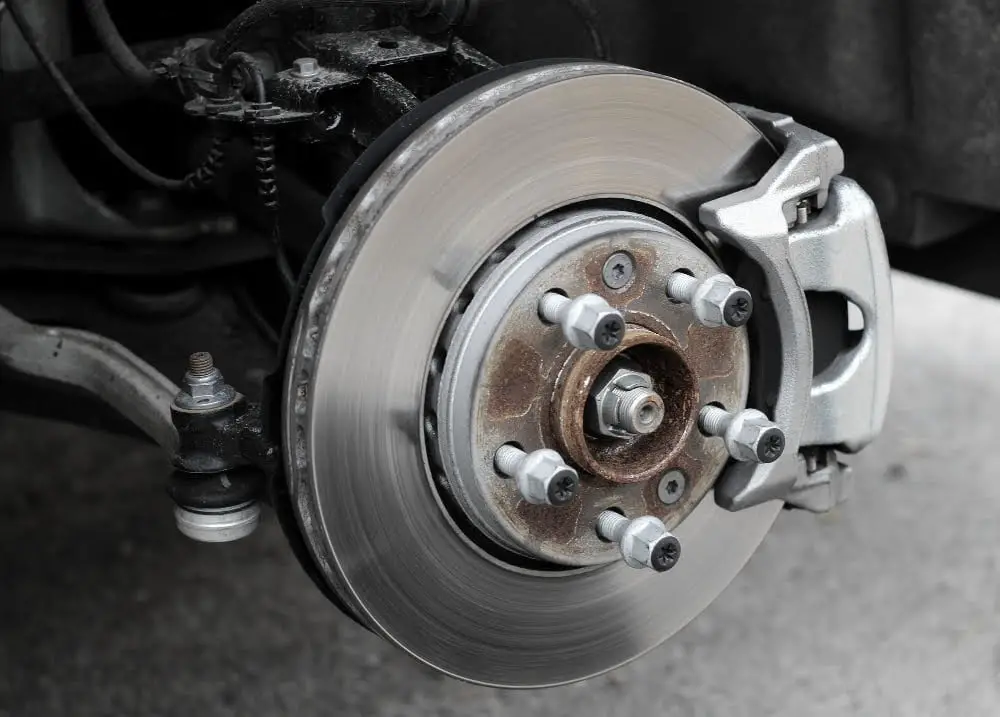
They were first synthesized in 1907 by Dr. Leo Baekeland, who named them Bakelite after himself. Phenolic resins are made by reacting phenol with formaldehyde under heat and pressure to form a hard, infusible material that is resistant to heat, chemicals, and electricity.
These resins have excellent mechanical properties such as high strength-to-weight ratio, dimensional stability even at high temperatures (up to 150°C), low water absorption rate (<1%), good electrical insulation properties (dielectric constant ~4-5), and resistance against acids/bases/organic solvents.
Due to their unique combination of physical properties mentioned above along with their affordability compared to other thermosetting plastics like epoxy or polyimide resin systems make them an ideal choice for various applications including automotive parts manufacturing (brake pads & clutch facings), electrical components production (switches & circuit breakers) as well as household items such as kitchenware handles or knobs on appliances like refrigerators etc.
Melamine Formaldehyde Resins
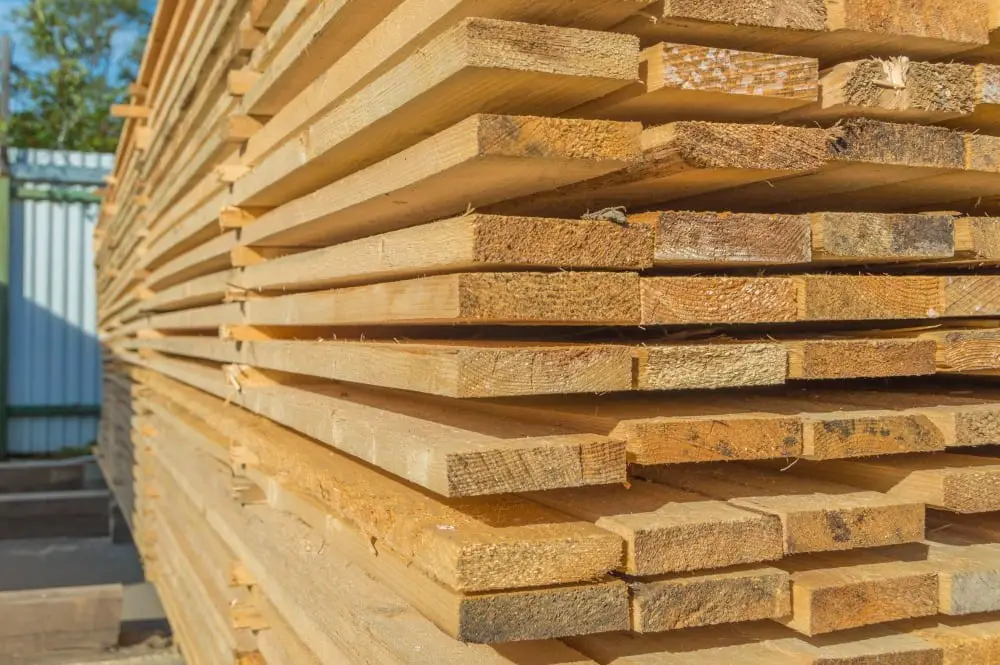
These resins are made by reacting melamine with formaldehyde, which results in a hard and durable material that can withstand high temperatures and pressures. Melamine formaldehyde resins have excellent resistance to water, chemicals, heat, and fire.
They also have good electrical insulation properties.
These types of plastics find their application as adhesives for laminates or wood products such as particleboard or plywood due to their excellent bonding strength. They are also used in coatings for appliances like dishwashers because they resist staining from acidic foods.
Urea Formaldehyde Resins
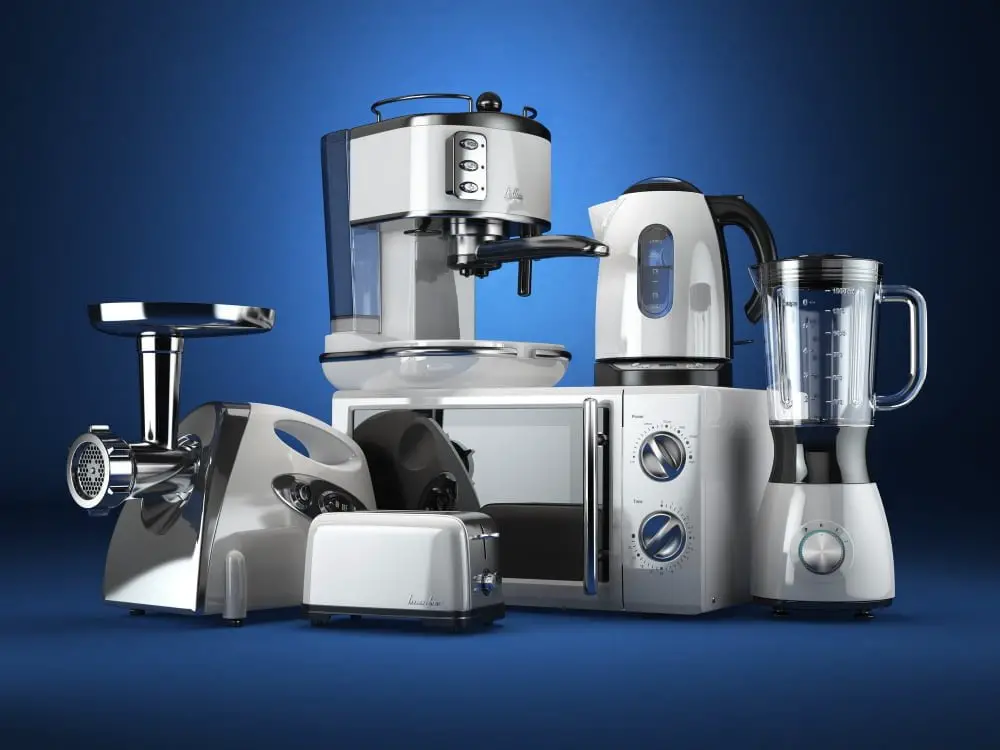
They are made by reacting urea with formaldehyde, which results in a hard and durable material. Urea formaldehyde resins have excellent water resistance, high tensile strength, and good dimensional stability.
These properties make them ideal for use as adhesives for wood-based panels such as particleboard and plywood.
In addition to their adhesive properties, urea formaldehyde resins also find application in the production of electrical appliances due to their excellent insulation properties. They can be molded into various shapes using compression or injection molding techniques.
However, it’s important to note that prolonged exposure to heat can cause these materials to degrade over time leading them susceptible cracking or breaking down under stress.
Epoxy Resins
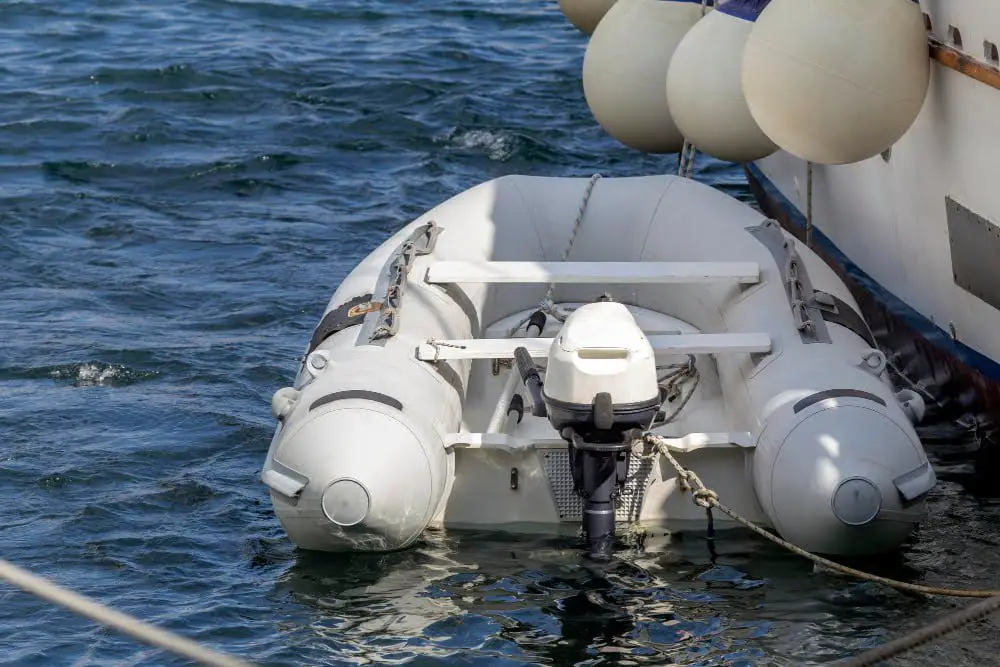
They are formed by the reaction between epichlorohydrin and bisphenol A, resulting in a highly cross-linked polymer network. Epoxy resins have high tensile strength, good adhesion to different substrates, low shrinkage during curing, and resistance to chemicals and moisture.
Due to these unique properties, epoxy resins find extensive use as coatings for metals or concrete structures exposed to harsh environments such as marine or industrial settings. They also serve as adhesives for bonding materials like wood or composites together.
Epoxy resin composites reinforced with fibers such as carbon fiber offer exceptional strength-to-weight ratios making them ideal for aerospace applications where weight reduction is critical.
However useful they may be though there are some disadvantages associated with using epoxy resins including their tendency towards brittleness at low temperatures which can limit their use in certain industries like automotive manufacturing where temperature fluctuations occur frequently.
Polyurethane Resins
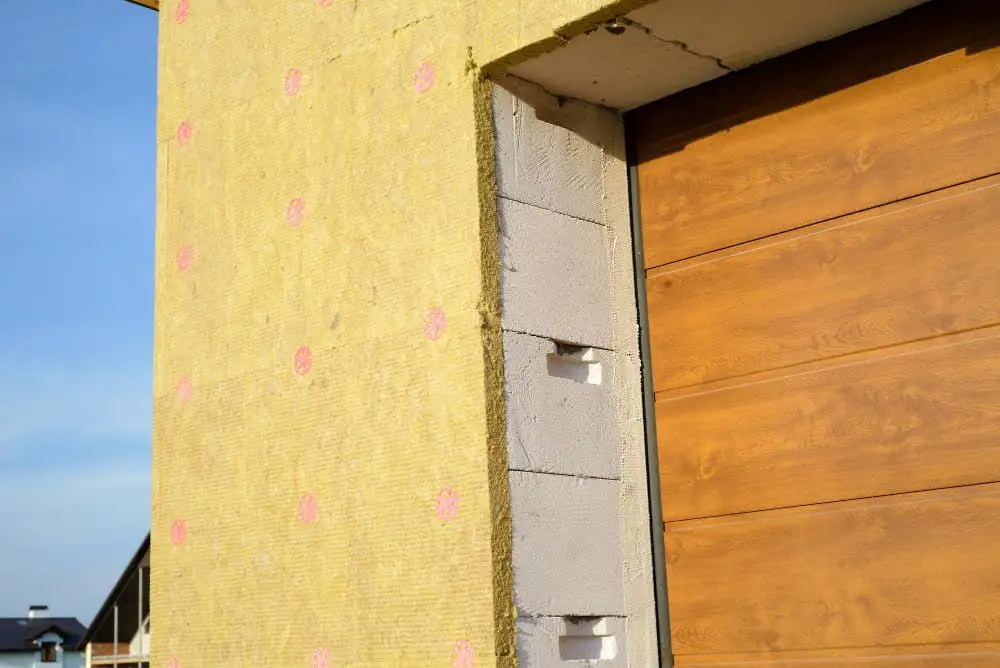
They are formed by the reaction between polyols and diisocyanates, which results in a three-dimensional network structure. Polyurethane resins have excellent mechanical properties such as high strength, toughness, and abrasion resistance.
They also exhibit good chemical resistance to oils, solvents, and acids.
One of the most significant advantages of polyurethane resins is their versatility; they can be formulated to meet specific requirements for different applications such as coatings, adhesives or foams. For example:
- In construction industry: Polyurethanes can be used for insulation purposes due to their low thermal conductivity.
- In automotive industry: Polyurethanes are commonly found in car seats because they provide comfort while being durable enough to withstand wear-and-tear.
- In electronics industry: Due to its electrical insulating properties it’s often used as an encapsulant material.
However despite all these benefits there are some disadvantages associated with using polyurethane resin materials including cost (compared with other thermoset plastics), environmental impact during production process (due mainly from emissions) ,and health concerns related exposure during manufacturing processes or disposal practices.
Unsaturated Polyester Resins
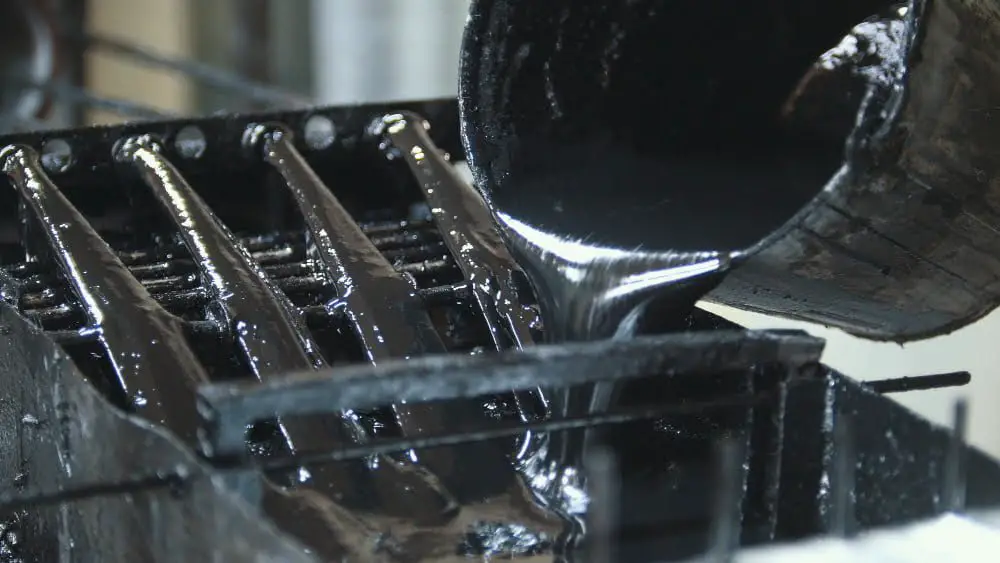
They are formed by the reaction between unsaturated dibasic acids and diols, which results in a highly cross-linked polymer network. UPRs have excellent mechanical properties, such as high strength and stiffness, good chemical resistance, and low shrinkage during curing.
One of the most significant advantages of UPRs is their versatility. They can be easily modified with various additives to enhance their performance for specific applications.
For example, adding fillers like glass fibers or carbon fibers can improve their strength and stiffness while reducing weight.
UPRs find extensive use in manufacturing composite materials such as fiberglass reinforced plastics (FRP). These composites have become increasingly popular due to their lightweight yet durable nature making them ideal for use in boats, automotive parts production among others.
Polyimides
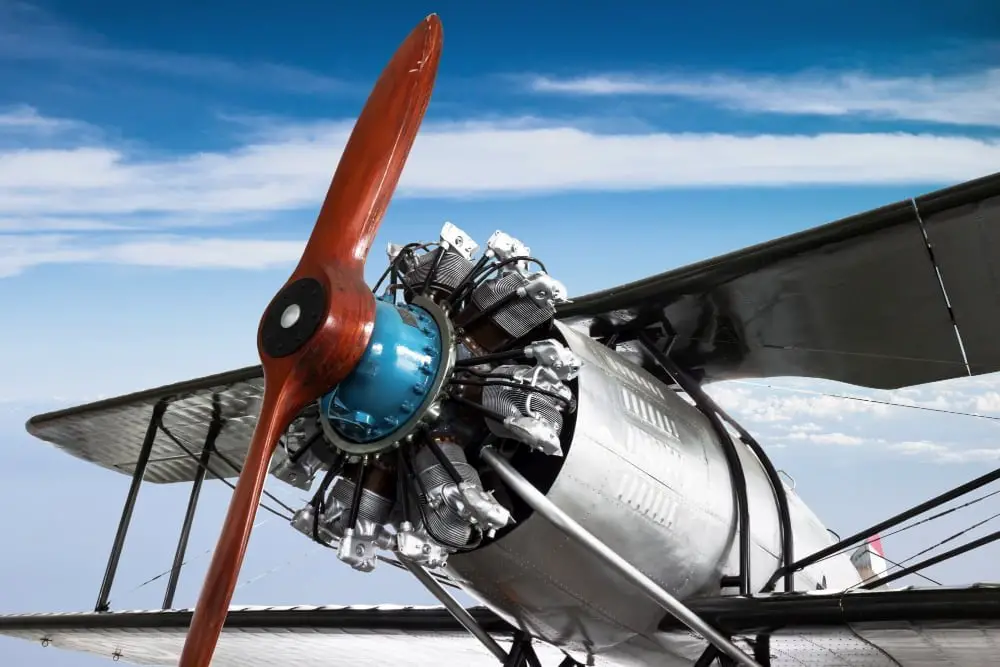
They are widely used in the aerospace industry for their ability to withstand extreme temperatures and harsh environments. Polyimides have a unique molecular structure that allows them to maintain their properties even at elevated temperatures up to 500°C.
One of the most common applications of polyimides is as an insulating material in electrical components such as motors, transformers, and generators. Their high dielectric strength makes them ideal for use in these applications where electrical insulation is critical.
Polyimide films also find extensive use in flexible printed circuits (FPCs) due to their excellent mechanical properties such as flexibility and durability. These films can be easily laminated onto other materials like copper foils or adhesive tapes without losing any of its physical or chemical characteristics.
In addition to electronics applications, polyimides also find uses in various industries like automotive manufacturing (e.g., brake pads), aerospace engineering (e.g., aircraft parts), medical devices(e.g., catheters), etc.
Bismaleimides
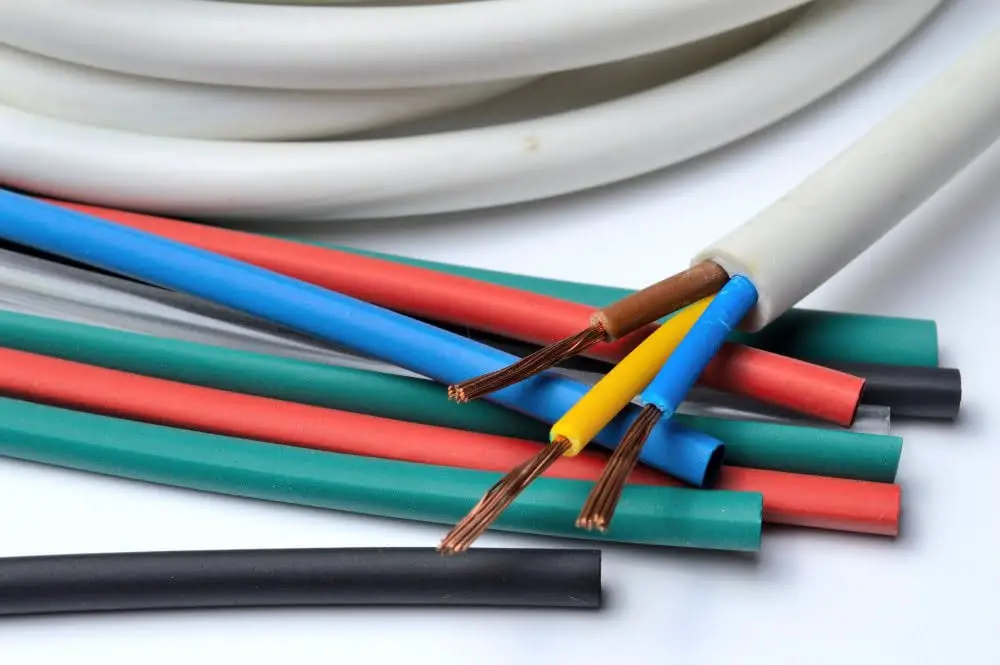
They are used in high-performance applications such as aerospace, automotive, and electronics industries. Bismaleimides have a unique molecular structure that provides them with exceptional heat resistance, chemical stability, and dimensional stability.
These materials can withstand temperatures up to 400°C without losing their strength or stiffness. This makes them ideal for use in high-temperature environments where other plastics would fail.
Bismaleimide resins also have good electrical insulation properties which make them suitable for electronic components.
One of the most significant advantages of bismaleimides is their ability to be reinforced with fibers such as carbon or glass fiber composites to create strong lightweight structures that can withstand extreme conditions.
Cyanate Esters
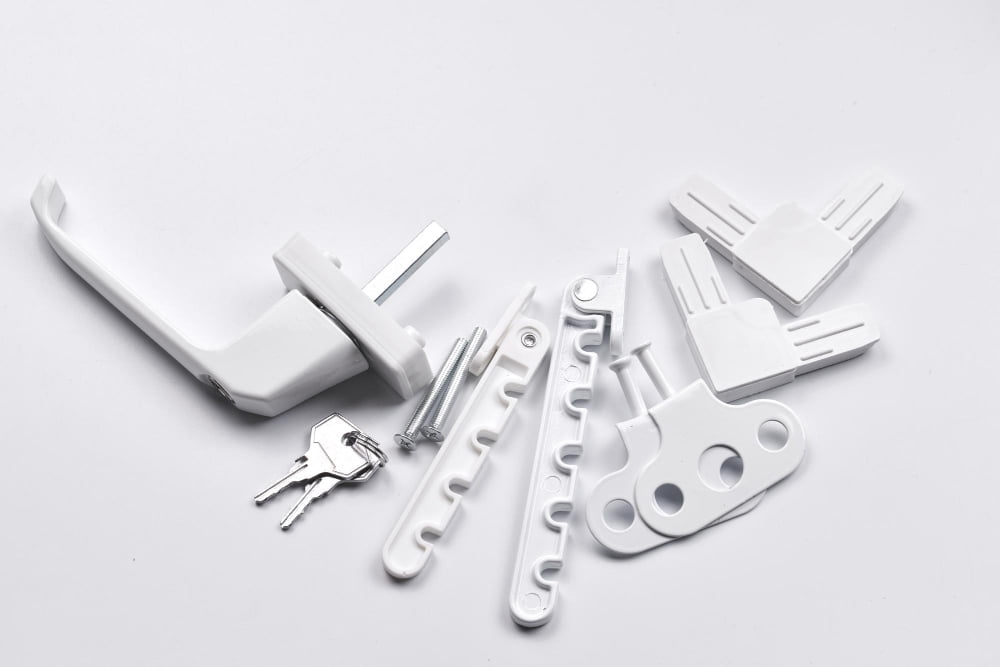
They have high glass transition temperatures, low dielectric constants, and good resistance to moisture absorption. Cyanate esters also exhibit low outgassing characteristics which make them ideal for use in the aerospace industry.
One of the unique features of cyanate ester resins is their ability to cure at relatively low temperatures compared to other thermosetting plastics. This makes them suitable for use with temperature-sensitive substrates such as electronic components.
Cyanate ester resins can be used alone or blended with other materials such as graphite fibers or aramid fibers (Kevlar) to form composites that offer superior strength-to-weight ratios compared to traditional metals like steel or aluminum.
Cyanate esters have been found useful in applications where dimensional stability is critical, such as precision optics and semiconductor manufacturing equipment.
Benzoxazines
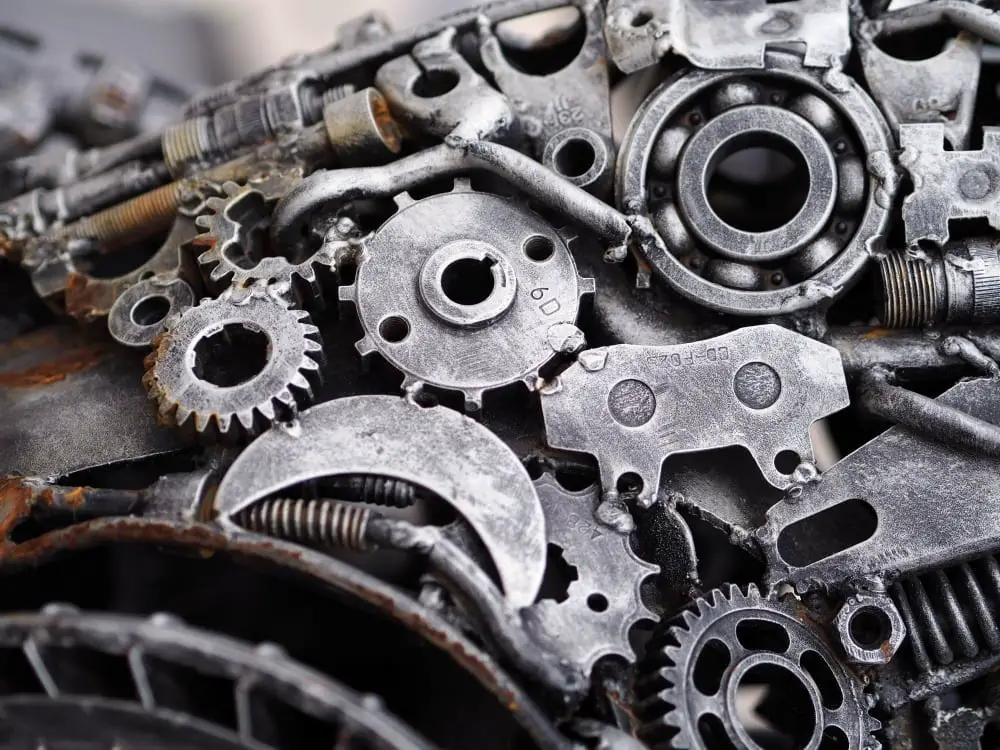
They are known for their excellent thermal stability, low water absorption, and high mechanical strength. Benzoxazines also exhibit good flame retardancy and chemical resistance.
These materials were first developed in the 1980s but only gained commercial interest in the early 2000s. Since then, they have been used extensively in various applications such as aerospace components, electronic devices, automotive parts and structural composites.
One of the key advantages of benzoxazine resins is their ability to cure at lower temperatures compared to other thermosetting plastics like epoxy resins or phenolic resins. This makes them ideal for use with temperature-sensitive substrates such as plastics or metals.
Another advantage is that benzoxazine-based composites can be easily recycled by grinding them into small particles which can be reused as fillers or reinforcements for new composite materials without losing any significant mechanical properties.
Diallyl Phthalates
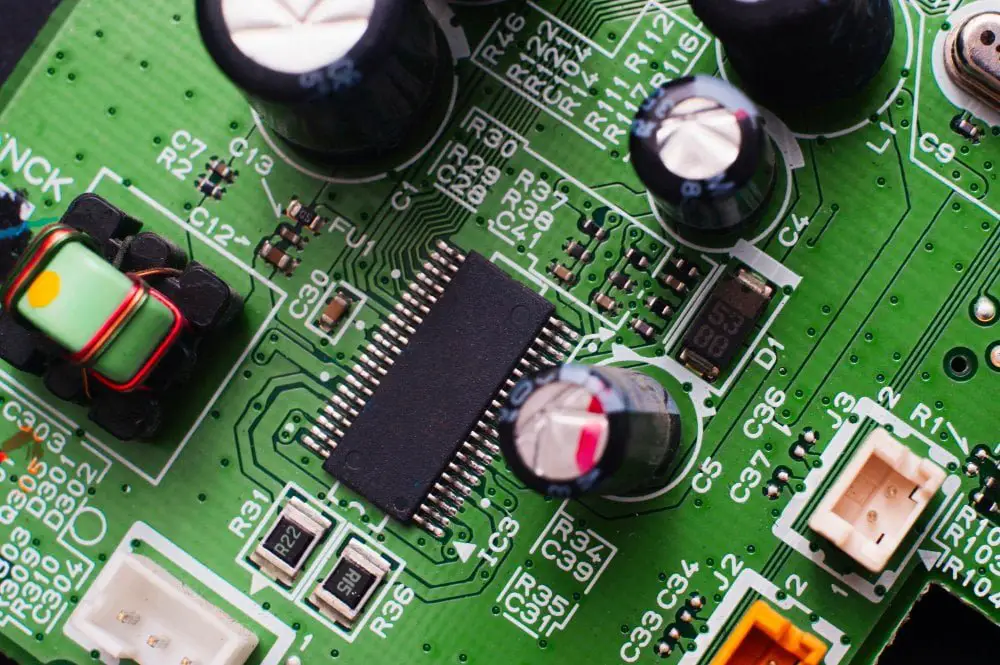
It has excellent dielectric properties, high heat resistance, and good dimensional stability. DAP can be cured by heating under pressure or with a catalyst to form cross-linked networks.
The unique properties of DAP make it an ideal material for manufacturing printed circuit boards (PCBs), switches, relays, connectors, and other electronic components. Its ability to withstand high temperatures makes it suitable for use in harsh environments such as aerospace applications.
However, like all thermosetting plastics, DAP has its limitations too. It cannot be re-melted or reshaped once cured which limits its recyclability options compared to some other types of plastics.
Silicone Resins
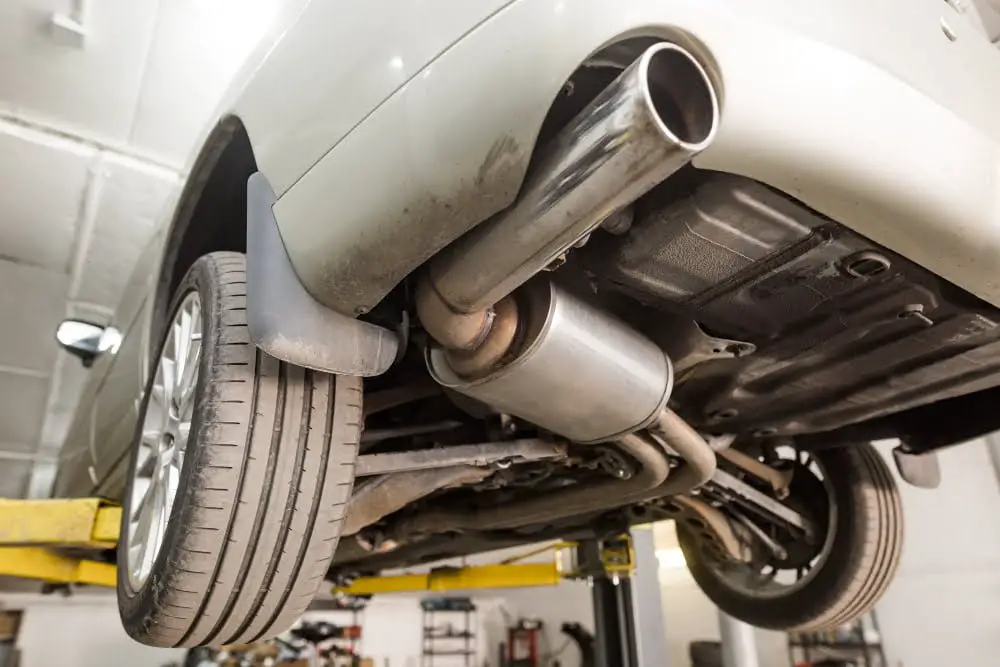
They are widely used in the electronics industry for encapsulation and potting applications due to their high dielectric strength. Silicone resins also have good adhesion to various substrates such as metals, glass, ceramics, and plastics.
In addition to their use in electronics applications, silicone resins find application in coatings for high-temperature environments such as exhaust systems or industrial ovens. They can withstand temperatures up to 500°C without significant degradation or loss of mechanical properties.
Another advantage of silicone resins is their ability to resist UV radiation and oxidation which makes them ideal for outdoor applications where exposure to sunlight is inevitable.
However, one disadvantage of silicone resin is its relatively low mechanical strength compared with other thermosetting plastics like epoxy or polyurethane. This limits its use in structural components but does not affect its suitability for non-load-bearing parts.
Vulcanized Rubber
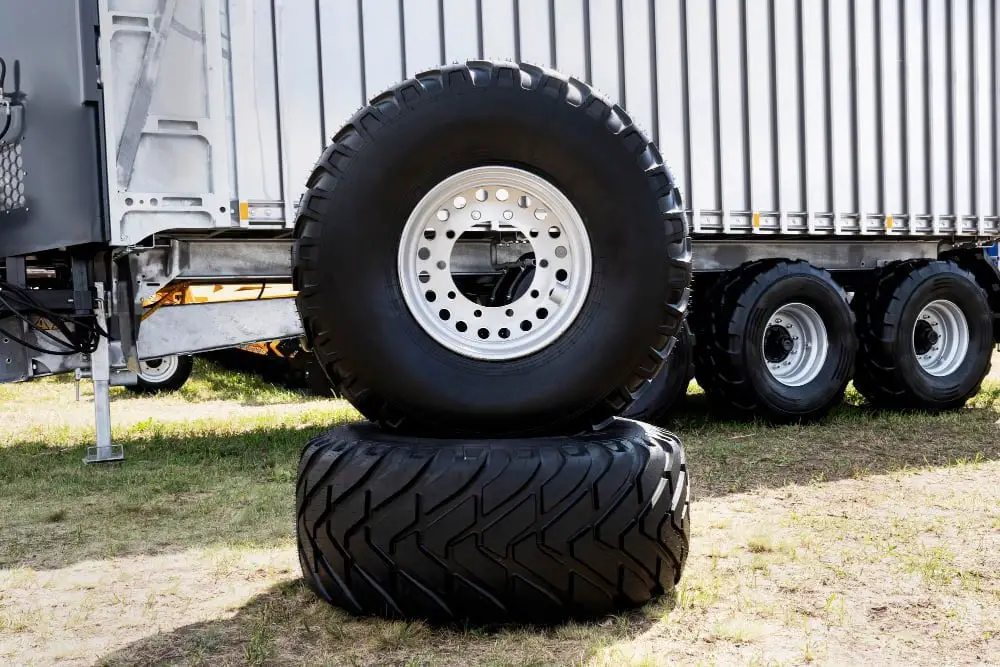
This process was discovered by Charles Goodyear in 1839 when he accidentally spilled rubber mixed with sulfur onto a hot stove. The resulting material was much stronger and more durable than regular rubber.
The vulcanization process involves heating the raw rubber material along with sulfur or other curatives to create cross-links between the polymer chains. These cross-links give vulcanized rubber its unique properties such as increased tensile strength, resistance to abrasion and tearing, improved elasticity over a wide range of temperatures, and resistance to chemicals.
Vulcanized Rubber is used in various applications such as tires for vehicles (cars/trucks), conveyor belts for industrial use due to their high wear-resistance property; shoe soles because they are flexible yet sturdy enough; gaskets/seals because they can withstand high pressure without breaking down easily.
Bakelite
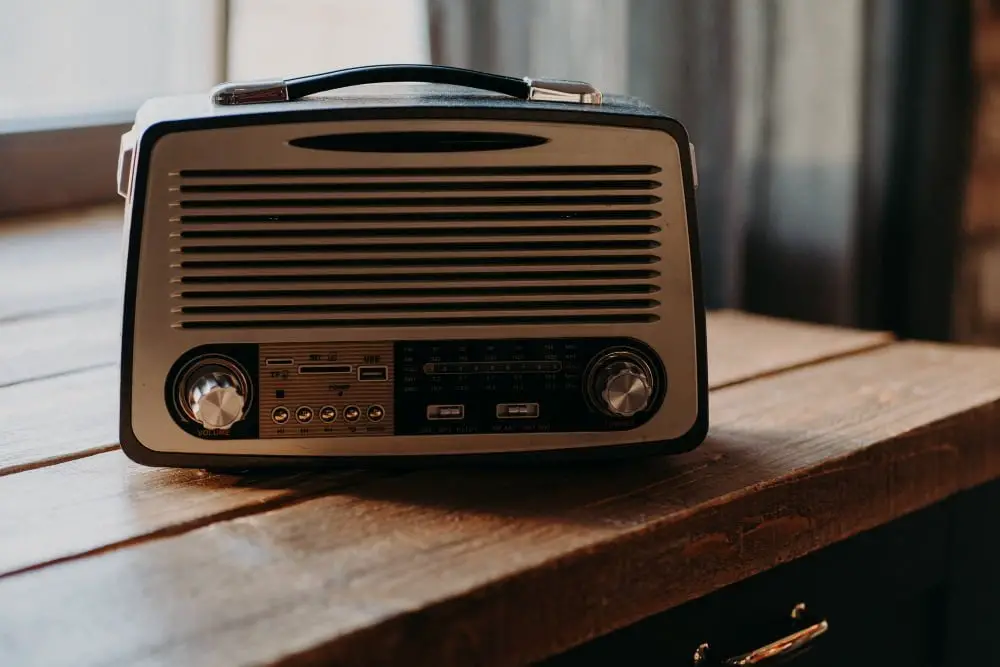
It was invented by Belgian chemist Leo Baekeland in 1907, who named it after himself. Bakelite is a phenolic resin that can be molded into various shapes and forms when heated under pressure.
It was widely used during the early 20th century for its electrical insulating properties, making it an essential material for radios, telephones, and other electronic devices.
One of the unique features of Bakelite is its ability to withstand high temperatures without melting or deforming. This property made it ideal for use in electrical switches and sockets where heat resistance was crucial.
Today, Bakelite has been largely replaced by newer materials with better performance characteristics such as epoxy resins or polyurethane resins but still finds some niche applications due to its excellent insulation properties.
Properties and Applications
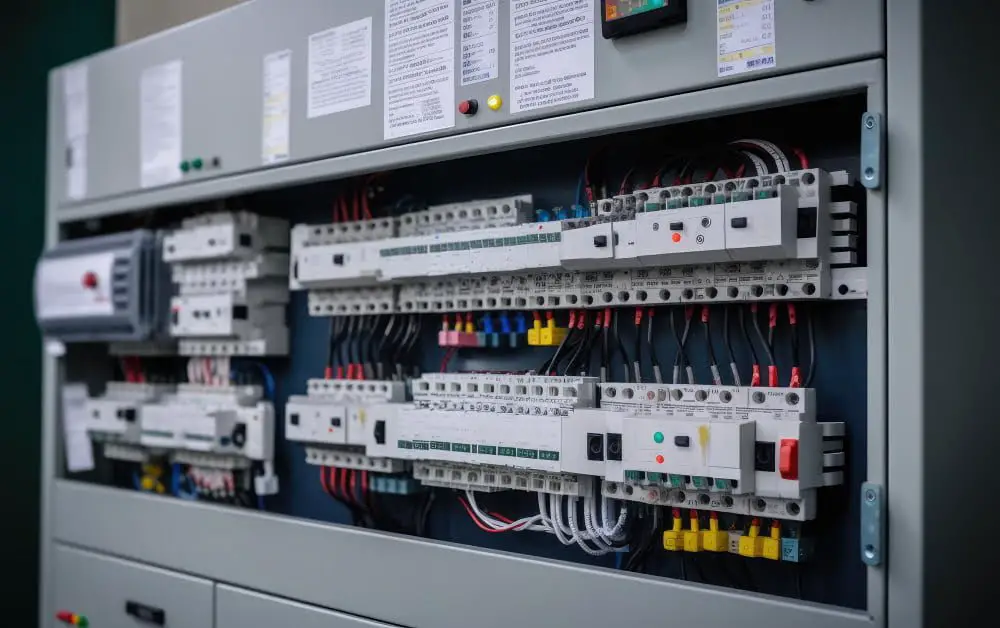
One of the most significant advantages of thermosetting plastics is their ability to withstand high temperatures without losing their shape or strength. They are also highly resistant to chemicals, making them suitable for use in harsh environments.
Another property that makes thermosetting plastics popular is their excellent electrical insulation properties. This feature makes them an ideal material choice for electronic components such as circuit boards, transformers, and insulators.
In addition to these features, thermosetting plastics are also known for being strong and durable materials with low shrinkage rates during curing processes. These characteristics make it possible to produce complex shapes with tight tolerances while maintaining structural integrity.
Due to these unique properties, there has been a growing demand for the use of thermoset materials in various industries such as construction, automotive manufacturing electronics industry among others.
Processing Techniques
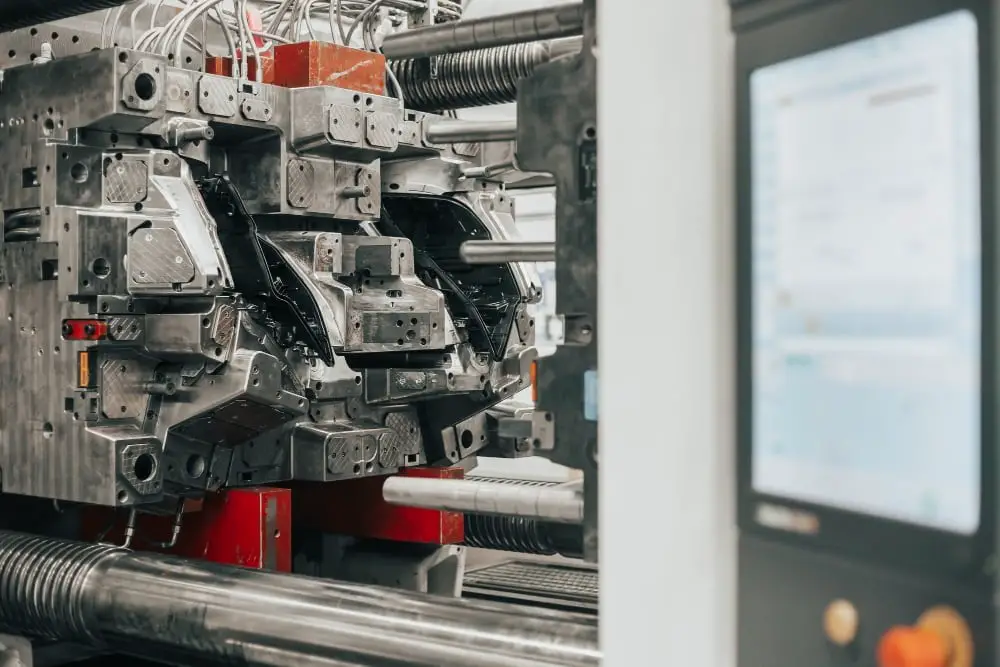
The curing process, which involves the chemical reaction that hardens the material, requires precise temperature and pressure control to achieve optimal results. There are several techniques used for processing thermosetting plastics, including compression molding, transfer molding, injection molding and resin infusion.
Compression Molding: This technique involves placing preheated plastic into a mold cavity and applying heat and pressure until it cures. Compression molding is commonly used for high-volume production of parts with complex shapes.
Transfer Molding: Transfer molding uses a plunger to force molten plastic through runners into heated molds under high pressure. This method allows for more intricate designs than compression moulding but can be slower due to its complexity.
Injection Molding: Injection moulding injects molten plastic directly into the mold cavity under high-pressure conditions using an injection unit attached to the machine’s barrel end or screw extruder assembly at one end while clamping plates hold both halves together during curing time period before releasing them once cured enough so they don’t deform when removed from their respective cavities by ejector pins located on opposite sides of each half plate set up within this type system.
Resin Infusion: Resin infusion is another popular technique that uses vacuum-assisted impregnation (VAI) or vacuum-assisted resin transfer (VARTM) methods where liquid resins are drawn through dry fiber reinforcements via negative air pressures applied over time periods ranging anywhere between minutes up-to hours depending upon size/complexity involved in making desired product(s).
Advantages and Disadvantages
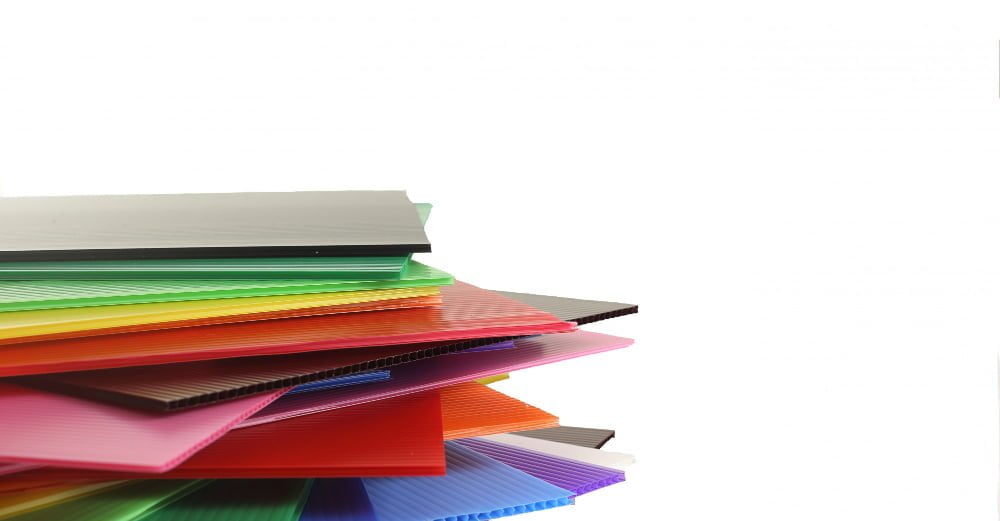
They are highly resistant to heat, chemicals, and electricity. They also have excellent dimensional stability, meaning they do not shrink or expand when exposed to temperature changes.
Thermosetting plastics are strong and durable.
However, there are some disadvantages associated with the use of thermosetting plastics as well. One major disadvantage is that once cured or hardened during the manufacturing process; they cannot be melted down again for recycling purposes like their counterpart – Thermoplastics can be recycled multiple times without losing their properties.
Another disadvantage is that these materials tend to be brittle in nature which makes them prone to cracking under high stress conditions such as impact loads.
Environmental Impact and Recycling
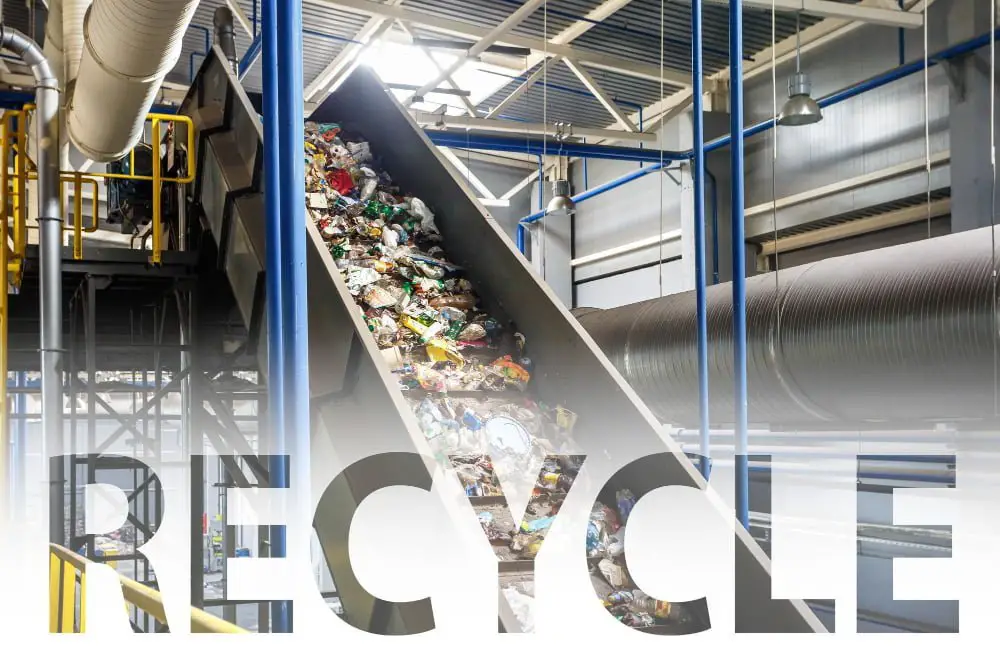
The manufacturing process of these materials involves high energy consumption, which contributes to greenhouse gas emissions. Some thermosetting plastics contain hazardous chemicals that can be harmful to human health and the environment.
Recycling is one way to reduce waste from thermosetting plastics. However, recycling these materials can be challenging due to their cross-linked structure that makes them difficult to break down into their original components for reuse.
One method used in recycling is mechanical grinding or shredding followed by re-molding into new products such as park benches or playground equipment. Another approach involves using pyrolysis technology where heat breaks down the plastic into its constituent parts for use in other applications.
Despite challenges associated with recycling thermoset polymers compared with traditional recyclable materials like metals or glass; research continues towards developing more efficient methods for processing this type of plastic waste while minimizing environmental impacts caused by its production cycle.
Health and Safety Considerations
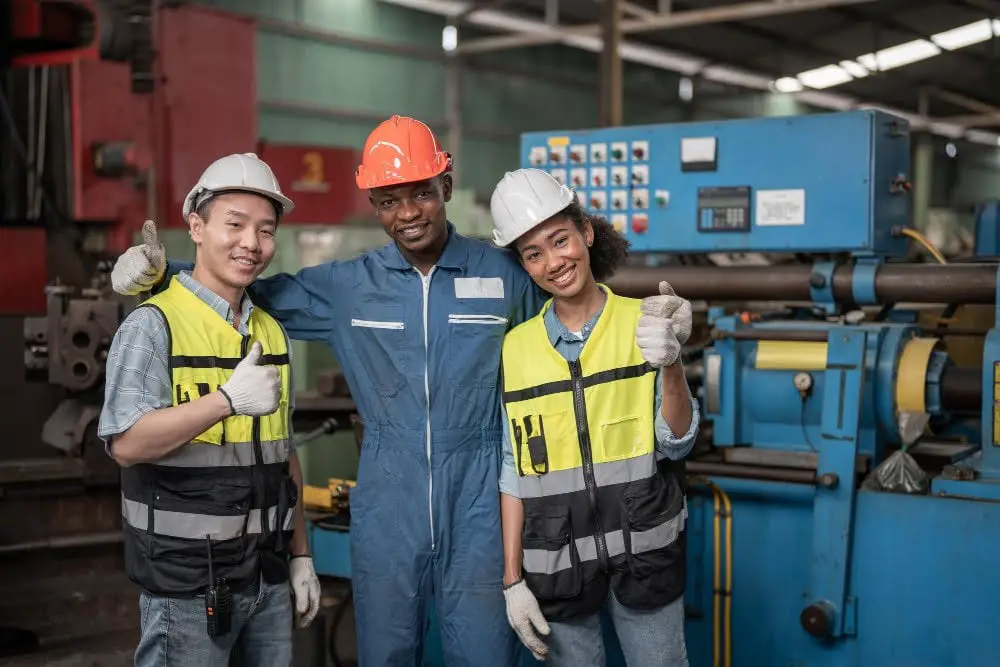
During the manufacturing process, workers may be exposed to hazardous chemicals such as formaldehyde, styrene, or methylene chloride. These chemicals can cause respiratory problems if inhaled over a prolonged period.
It is essential that proper protective equipment such as respirators and gloves are worn when handling these materials. Adequate ventilation systems should be installed in work areas where thermosetting plastics are being processed.
Once cured or hardened into their final form, most thermosetting plastics do not pose any significant health risks unless they are burned or incinerated improperly. Burning these materials releases toxic fumes that can harm both humans and the environment.
Therefore it’s crucial to dispose of them properly by following industry standards for recycling or disposal methods recommended by regulatory agencies like EPA (Environmental Protection Agency).
Industry Standards and Regulations
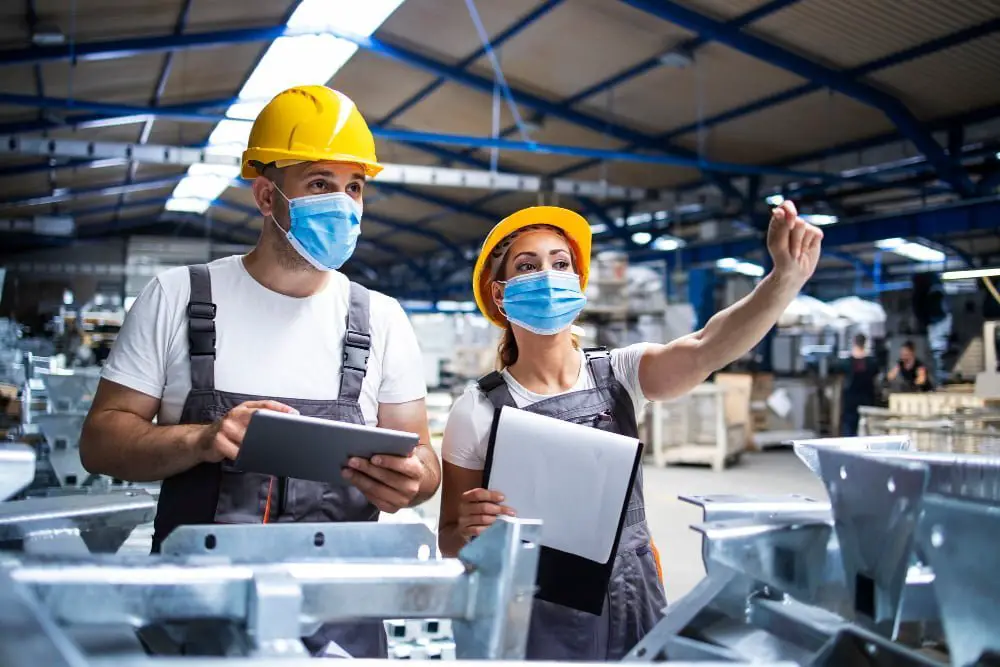
These regulations are put in place to ensure that the materials used are safe for human health, environmentally friendly, and meet specific performance requirements.
In the United States, organizations such as ASTM International (American Society for Testing Materials) develop industry standards for thermosetting plastics. The European Union has its own set of guidelines under REACH (Registration, Evaluation, Authorization and Restriction of Chemicals).
These guidelines aim to protect human health by regulating the use of hazardous chemicals.
It is essential that manufacturers comply with these regulations when producing products made from thermosetting plastics. Failure to do so can result in legal action against them or even a recall on their products if they pose a risk to public safety.
Applications of Thermosetting Plastics
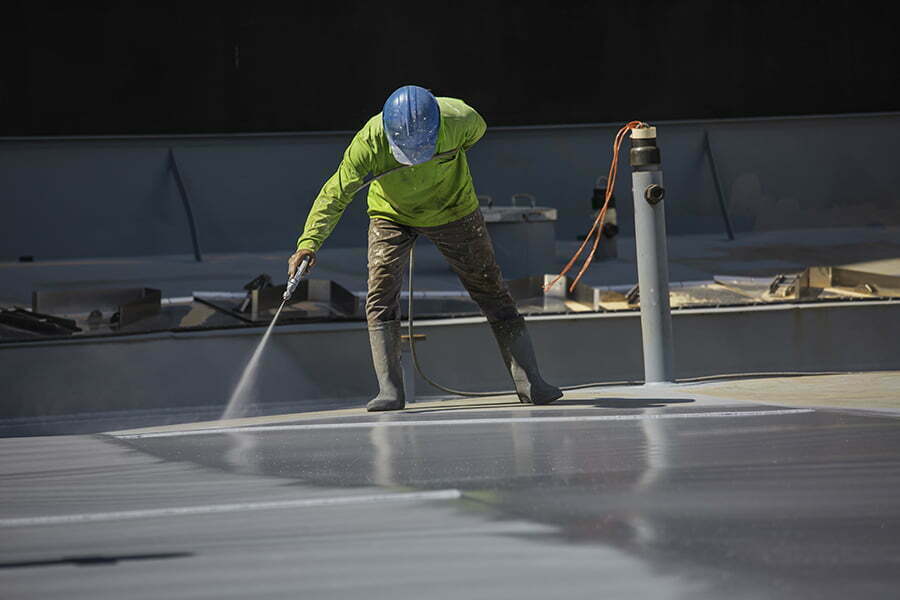
Due to their unique properties, they are preferred over other materials such as thermoplastics and metals. One of the most common applications is in the construction industry where they are used for insulation, adhesives, coatings, and composites.
They are also widely used in electrical and electronic equipment due to their excellent dielectric properties.
In addition to these industries, thermosetting plastics find use in automotive parts such as brake pads and clutch facings because of their high heat resistance capabilities. The aerospace industry also uses them extensively for aircraft components that require high strength-to-weight ratios.
Another significant application area is sports equipment manufacturing where composite materials made from thermosetting resins provide superior performance characteristics compared to traditional materials like wood or metal.
Thermosetting Plastics in Electronics
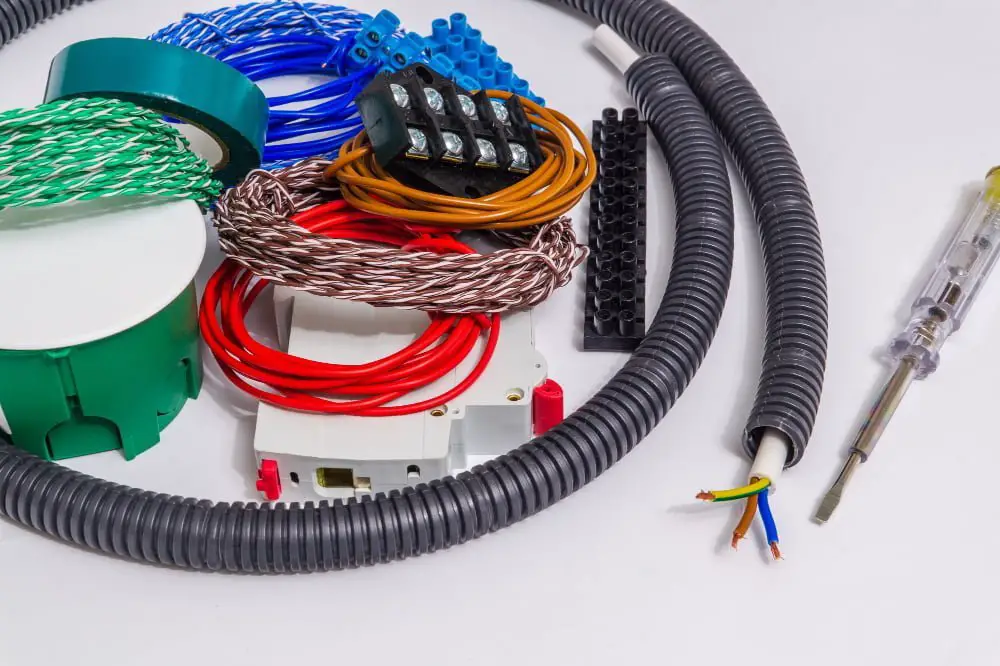
They are used to manufacture various electronic components such as printed circuit boards (PCBs), connectors, switches, and insulators. The excellent electrical insulation properties of thermosetting plastics make them ideal for use in high voltage and high-temperature environments.
One common type of thermosetting plastic used in electronics is epoxy resin. Epoxy resins are widely used as adhesives, coatings, encapsulants, and potting compounds due to their excellent mechanical strength and chemical resistance.
Another popular application for thermosetting plastics is molding compounds that can be filled with conductive materials like copper or silver flakes to create electrically conductive parts such as heat sinks or electromagnetic interference (EMI) shields.
In addition to their electrical properties, many types of thermoset materials also offer superior thermal stability compared with other plastic types which makes them suitable for use in harsh environments where temperature fluctuations may occur frequently.
Thermosetting Plastics in Construction
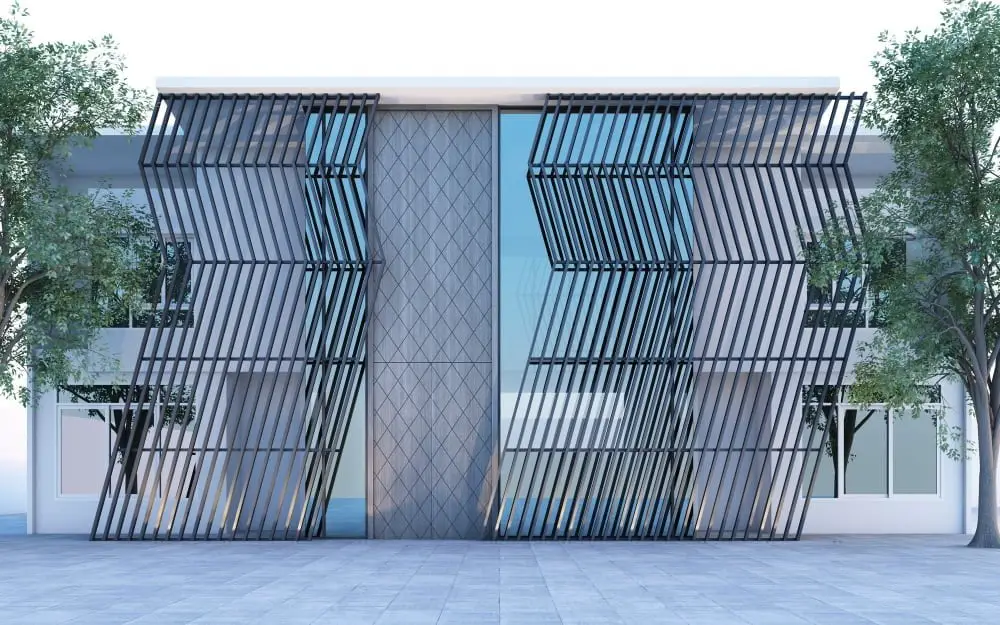
They are used in various applications such as insulation, adhesives, coatings, and composites. One of the most common uses of thermosetting plastics is for electrical insulation purposes.
For example, epoxy resins are widely used as a coating material for electrical equipment because they provide excellent dielectric strength and thermal stability.
Another application of thermosetting plastics in construction is composite materials. Composite materials made from reinforced plastic offer high strength-to-weight ratios that make them ideal for use in building structures such as bridges and roofs.
Thermoset polymers also find use as adhesives or binders to join different components together permanently without any risk of separation under extreme conditions like heat or moisture exposure.
In addition to these applications, thermoset polymers can be molded into complex shapes using injection molding techniques which makes them suitable for manufacturing parts with intricate geometries required by modern architectural designs.
Thermosetting Plastics in Automotive Industry
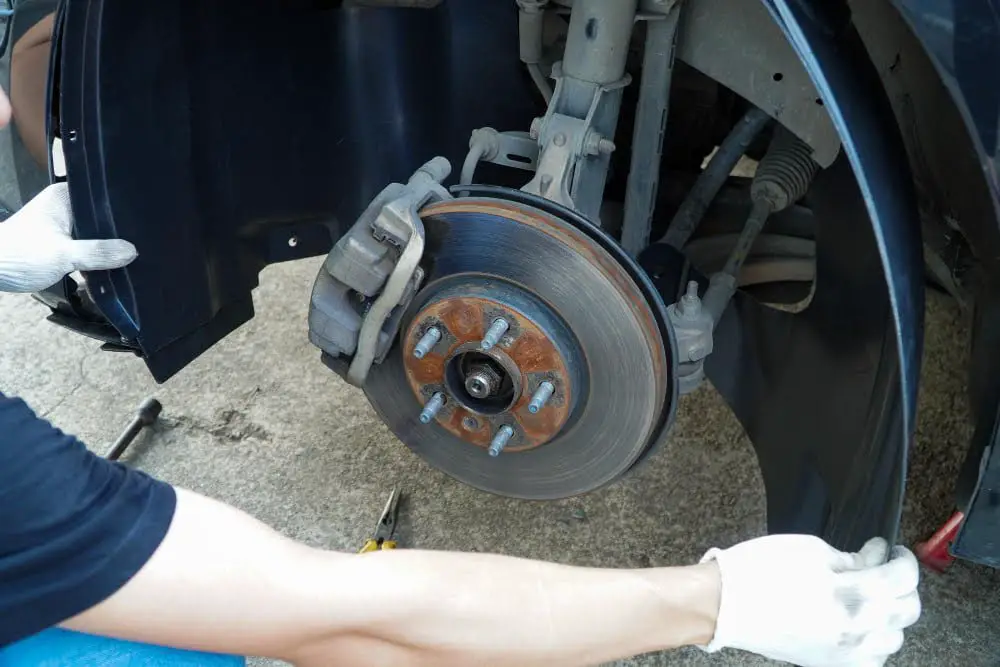
They are used to manufacture various components such as brake pads, engine parts, electrical connectors, and interior trims. One of the most common thermosetting plastics used in this industry is phenolic resin due to its excellent heat resistance and mechanical strength.
Phenolic resins are commonly used for manufacturing brake pads because they can withstand high temperatures without losing their shape or structural integrity. They provide good friction properties that allow for efficient braking performance.
Another application of thermosetting plastics in the automotive industry is with regards to electrical connectors. These components require materials that can withstand high temperatures and resist corrosion while maintaining their dimensional stability over time.
Thermoset materials like epoxy resins meet these requirements perfectly.
In addition to providing superior performance characteristics compared to traditional metal-based alternatives, using thermoset materials also results in lighter weight parts which contribute towards fuel efficiency improvements – an important consideration given today’s focus on reducing carbon emissions from vehicles.
Recycling and Disposal of Thermosetting Plastics
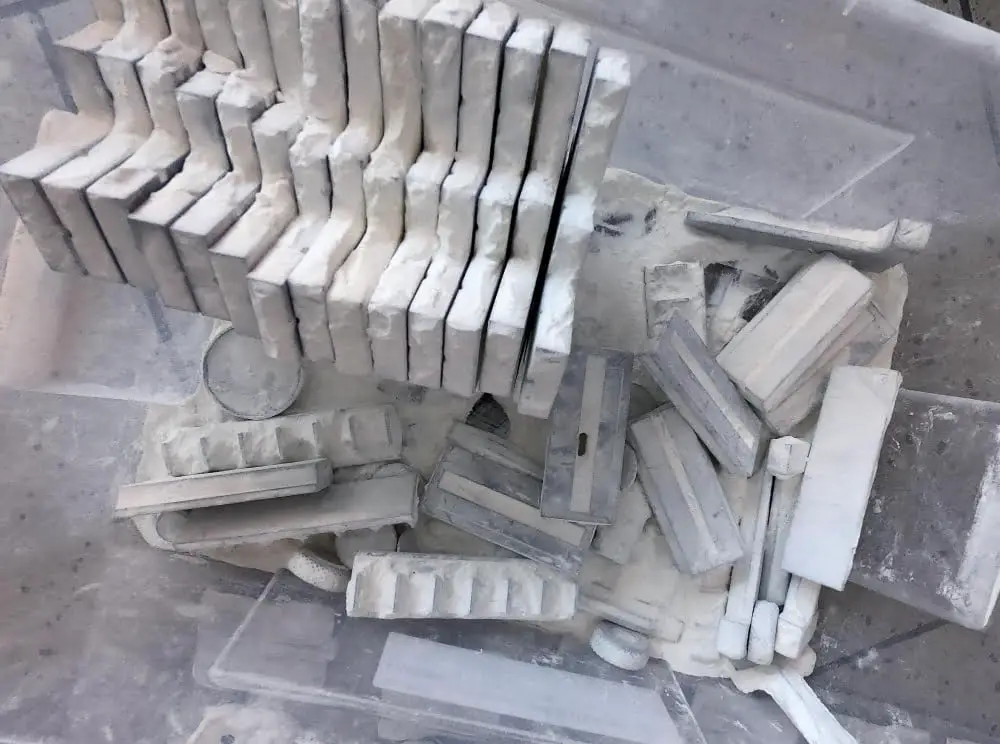
However, these properties also make them difficult to recycle or dispose of properly. Unlike thermoplastics that can be melted down and reshaped multiple times without losing their original properties, thermosets cannot be re-melted once they have been cured.
The disposal of thermoset materials is a significant challenge as they do not decompose easily in landfills. Burning them releases toxic gases into the atmosphere which poses a threat to human health and the environment.
However, there are some recycling methods available for certain types of thermosetting plastics such as grinding them into small particles that can be used in construction materials like asphalt or concrete mixtures. Another method involves using pyrolysis technology where the material is heated at high temperatures in an oxygen-free environment to break it down into smaller molecules that can then be reused.
It’s important to note that recycling options vary depending on the type of resin used in manufacturing products made from these materials. Therefore proper identification is necessary before any attempt at recycling or disposal takes place.
RTM Thermosetting Plastics (Fiberglass-Reinforced)
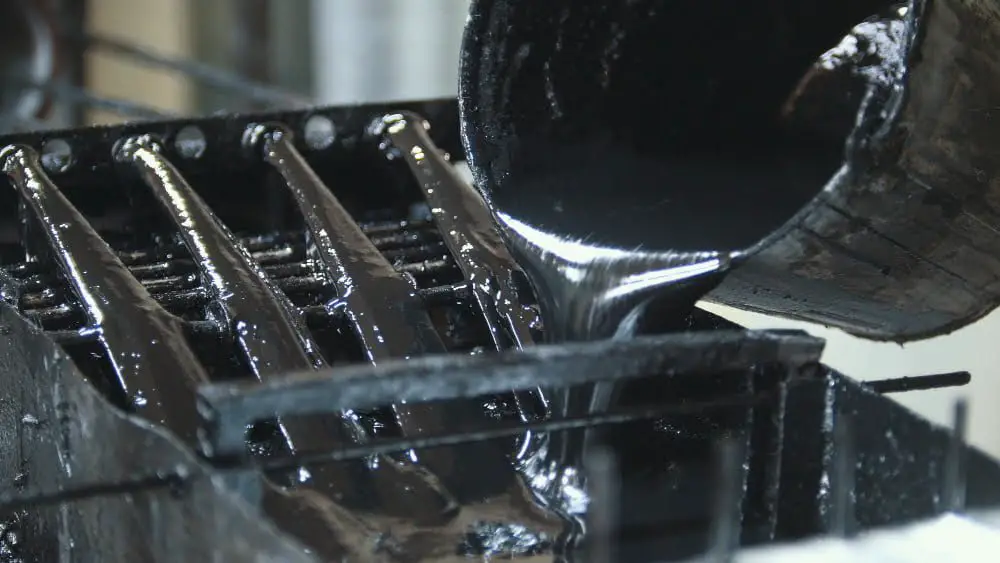
This technique involves injecting liquid resin into a closed mold containing pre-placed reinforcement fibers, such as fiberglass or carbon fiber. The mold is then heated and pressurized, allowing the resin to cure and harden.
The resulting product has excellent strength-to-weight ratio properties, making it ideal for use in various applications such as automotive components, aerospace structures, marine equipment and sporting goods. RTM thermosetting plastics are also known for their resistance to heat distortion and chemical corrosion.
One of the significant advantages of using RTM technology is that it allows manufacturers to create complex shapes with precise dimensions while maintaining consistent quality throughout production runs. This method reduces waste by minimizing excess material usage during fabrication.
However, there are some limitations associated with RTM technology; one being that it requires specialized equipment which can be costly initially but pays off in the long run due to its efficiency in producing high-quality products at scale.
RIM Thermosetting Plastics
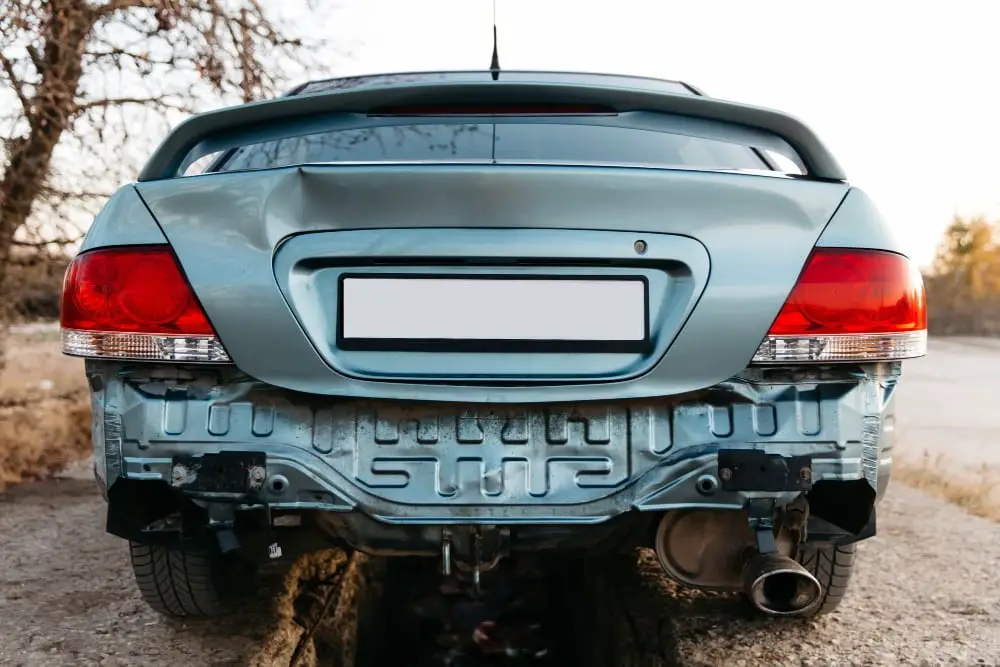
It involves the mixing of two liquid components, which are then injected into a mold where they react and cure to form the final product. RIM thermosetting plastics have excellent mechanical properties, high dimensional stability, and good chemical resistance.
One of the significant advantages of RIM thermosetting plastics is their ability to be molded into complex shapes with tight tolerances. This makes them ideal for use in automotive parts such as bumpers, fenders, and body panels.
Another advantage is that they can be reinforced with various materials such as glass fibers or carbon fibers to enhance their strength and stiffness further. This makes them suitable for applications that require high-performance materials like aerospace components or medical devices.
However, one disadvantage of RIM thermosetting plastics is that once cured; they cannot be re-melted or reshaped like some other types of plastic materials. Therefore it’s essential always to get your design right before production begins.
Other Thermosetting Plastic Types
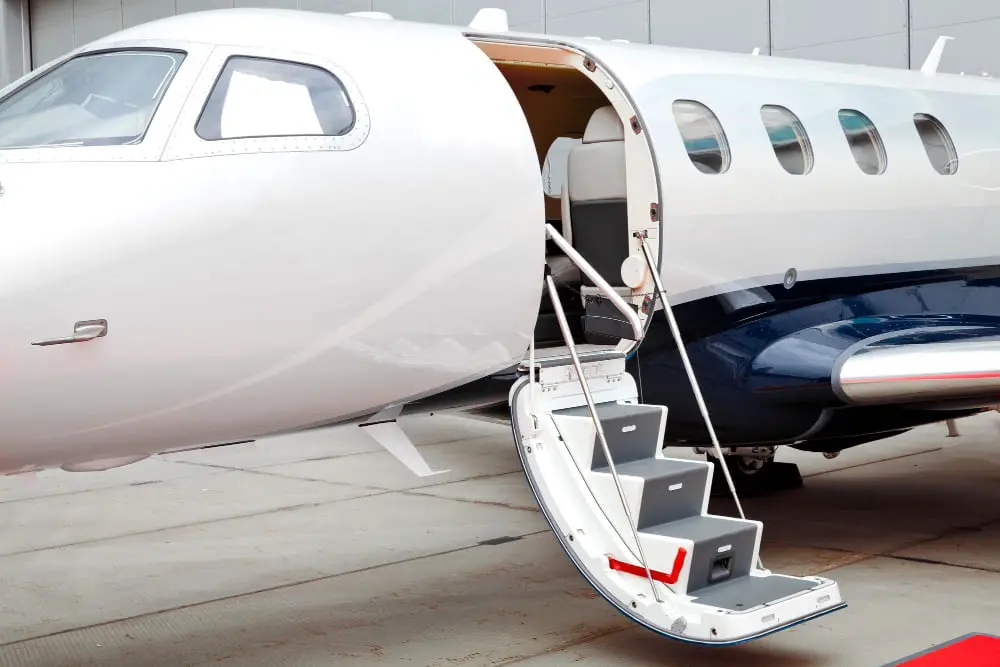
One such material is cyanate esters. Cyanate esters offer excellent thermal stability, low dielectric constant, and high strength-to-weight ratio.
They are widely used in aerospace applications due to their ability to withstand extreme temperatures.
Another type of thermoset plastic is benzoxazines which exhibit excellent mechanical properties such as high stiffness and strength while maintaining good toughness at elevated temperatures. Benzoxazines also have a low coefficient of thermal expansion making them ideal for use in electronic packaging.
Diallyl phthalates (DAP) are another group of thermosetting plastics that possess exceptional electrical insulation properties coupled with good chemical resistance making them suitable for use in printed circuit boards (PCBs).
Silicone resins offer superior heat resistance compared to other types of polymers while still retaining flexibility even at extremely low temperatures (-100°C). This makes silicone resins ideal for use in harsh environments where exposure to extreme temperature fluctuations is expected.
Comparison of Thermosetting and Thermoplastic Materials
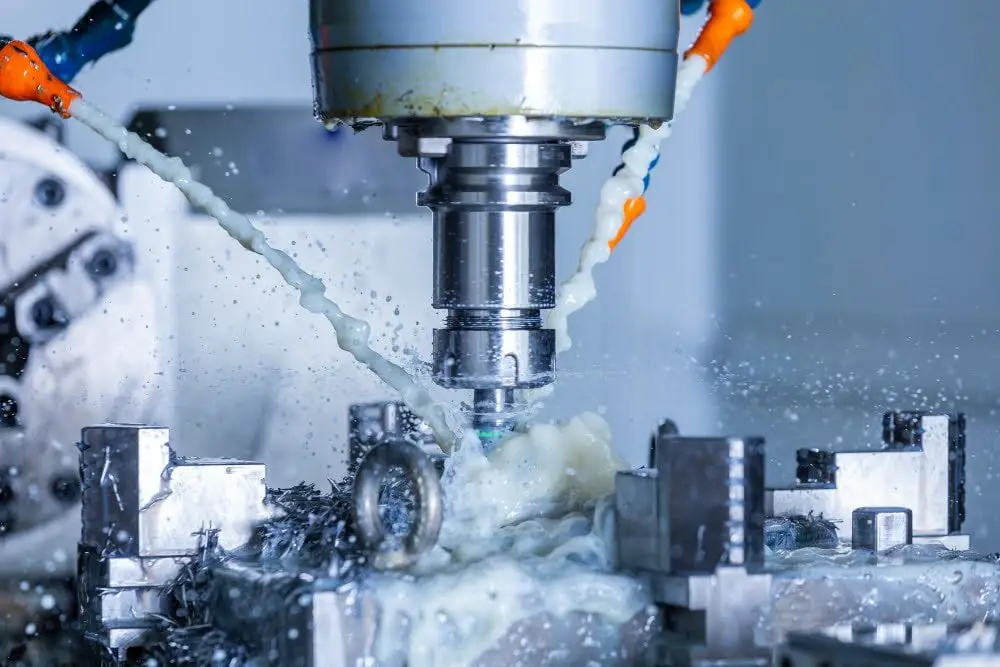
While both have their unique properties, they differ significantly in terms of structure, processing techniques, and performance characteristics.
Thermosetting plastics undergo a chemical reaction during the curing process that results in irreversible hardening. In contrast, thermoplastics can be melted repeatedly without undergoing any significant change to their molecular structure.
Another key difference between these two types of materials is their ability to withstand heat. Thermosetting plastics exhibit excellent thermal stability and can resist high temperatures without melting or degrading.
On the other hand, most thermoplastics have lower heat resistance than thermosets.
In terms of processing techniques, it’s easier to mold or shape thermoplastic materials using methods such as injection molding or extrusion due to its reversible nature compared with thermo-setting plastic which requires more complex processes like compression molding or transfer molding for shaping into desired forms.
Benefits of Thermoset Materials

One significant benefit is their excellent heat resistance, which makes them ideal for high-temperature applications. They also have superior chemical and corrosion resistance properties compared to thermoplastics.
Another advantage of thermosetting plastics is their dimensional stability and low shrinkage rate during the curing process. This property ensures that the final product retains its shape and size even under extreme conditions.
Thermosets are also known for their exceptional strength-to-weight ratio, making them an excellent choice for lightweight structures such as aircraft components or automotive parts.
Furthermore, these materials can be molded into complex shapes with intricate details using compression molding or injection molding techniques. This feature allows manufacturers to produce customized products according to specific design requirements while maintaining consistent quality standards.
Thermoset materials are highly durable and long-lasting due to their cross-linked molecular structure that prevents degradation from exposure to UV light or moisture over time.
The benefits of using thermosetting plastics make it clear why they have become a preferred material in many industries today. Their unique properties provide numerous advantages over other types of polymers while offering versatility in manufacturing processes without compromising on quality standards.
FAQ
What are 5 examples of thermosetting polymers?
Five examples of thermosetting polymers are Bakelite, Epoxy Resin, Melamine Resin, Duroplast, and Urea-Formaldehyde.
What are some examples of thermosetting plastics?
Some examples of thermosetting plastics are epoxy, silicone, polyurethane, and phenolic.
Which 6 is an example of thermosetting plastic?
Example 6 of thermosetting plastic is Vinyl Ester Resin, as it cannot be reheated once set and is permanently set.
What are the primary differences between thermosetting and thermoplastic polymers?
The primary differences between thermosetting and thermoplastic polymers are that thermosetting polymers are rigid, heat-resistant and cannot be reprocessed, while thermoplastic polymers are more flexible, melt when heated, and can be reprocessed multiple times.
How are thermosetting plastics commonly used in various industries?
Thermosetting plastics are commonly used in various industries for applications such as electrical insulation, automotive components, and construction materials due to their heat resistance, dimensional stability, and strength.
What are the key factors contributing to the high resistance of thermosetting plastics to heat and chemicals?
The key factors contributing to the high resistance of thermosetting plastics to heat and chemicals are their cross-linked molecular structure and strong covalent bonds.
Recap