In this buying guide, learn how to choose the right Sculpey polymer clay for your creative projects based on consistency, color, and baking properties.
Key takeaways:
- Sculpey polymer clay is made from PVC, plasticizer, and pigments.
- Sculpey clay is malleable, holds fine details, and can be reused if not baked.
- Condition the clay before working with it to prevent cracking.
- Follow safety measures when baking, including proper ventilation and using an oven timer.
- Finish and decorate your baked Sculpey clay with sanding, painting, and applying glaze or sealant.
Understanding Sculpey Polymer Clay
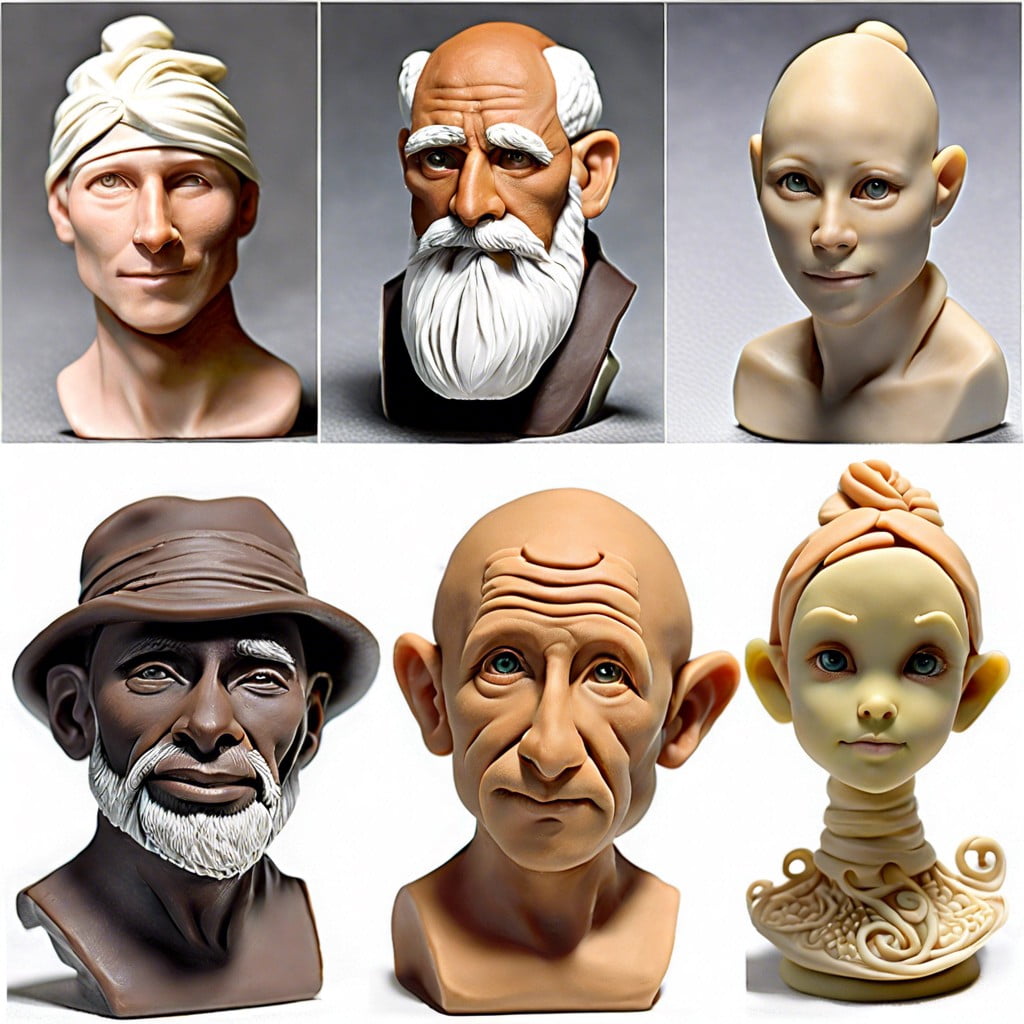
Sculpey polymer clay is a type of modeling clay made from polyvinyl chloride (PVC), plasticizer, and pigments. It remains soft until it’s baked in a home oven, at which point it hardens and becomes a permanent, durable plastic.
Available in a wide range of colors, Sculpey is favored for its malleability, ease of handling, and its ability to hold fine details, making it a go-to material for artists and hobbyists.
It can be sanded, drilled, carved, and painted after baking, lending itself to a wide range of creative projects from jewelry making to sculpting miniature figures.
Unlike traditional clay, Sculpey does not dry out when exposed to air and can be reused if not baked, offering flexibility and lowering waste.
Working With Sculpey Clay
Sculpey polymer clay is malleable and versatile, making it ideal for crafting a wide range of items from jewelry to home decor.
Before starting, condition the clay by kneading until it’s soft and pliable, which enhances its workability and prevents cracking.
Roll, shape, or sculpt it into your desired form, utilizing standard clay tools to add details or textures.
For intricate projects, you may blend different colors to create gradients or marbling effects.
If the piece is large or has varying thicknesses, build an armature out of wire or foil to provide internal support.
Remember, it’s wise to periodically check your progress and make sure the clay hasn’t warmed up too much from handling, as this can make intricate work difficult.
If it does, simply let it rest for a few minutes to firm up again before continuing your work.
Safety and Baking Instructions
When baking Sculpey polymer clay, it is essential to follow specific safety measures to ensure a successful curing process:
- Preheat your oven to the recommended temperature on the Sculpey package, typically between 275°F (130°C) and 300°F (149°C). An oven thermometer can help verify accuracy.
- Place your piece on a ceramic tile, glass surface, or a baking sheet lined with parchment paper to avoid direct contact with the oven rack and ensure even heat distribution.
- Bake for the prescribed time, usually 15 minutes per 1/4 inch (6mm) thickness. Underbaking leads to brittle projects, while overbaking can cause discoloration or burning.
- Use an oven timer to prevent overbaking. Every oven is different, so watching the first few times you bake a project can help avoid mishaps.
- Allow the clay to cool completely before handling. Newly baked Sculpey retains heat and can cause burns or warping if moved prematurely.
- Ensure proper ventilation in your workspace by opening windows or using an oven hood to disperse fumes produced during baking.
- Keep the area clear of flammable materials and never leave the oven unattended while in use.
Adhering to these instructions not only maximizes your safety but also produces the best results for your creations.
Finishing and Decorating
Once your Sculpey project is baked and cooled, it’s time to give it that final touch. Sand any rough edges with fine-grit sandpaper to achieve a smooth surface.
If necessary, wash the piece with soap and water to remove residue. Apply acrylic paints for color or use Sculpey glaze to add a glossy finish.
You may also consider buffing the baked clay to enhance its natural sheen. If embedding stones or attaching metal findings for jewelry, use strong adhesives like epoxy or super glue.
Consider varnish or sealant for added protection, especially on items that will be handled frequently.
Remember, personalization is key – from the choice of color to the pattern design, this stage is all about expressing your creativity.
Creative Applications
Sculpey polymer clay’s versatility opens up a world of creative possibilities. Crafters can sculpt miniature figurines, fashion intricate pieces of jewelry, or even create realistic-looking flowers that will last indefinitely.
Artists often use the clay for decorative homeware, like custom knobs for drawers or detailed picture frames. For educational purposes, it can be molded into anatomical models or historical artifacts for hands-on learning.
Moreover, mixed media art pieces frequently incorporate Sculpey clay for 3D effects and texture. The material’s adaptability also allows for the creation of personalized gifts such as holiday ornaments or bespoke keychains.
The only real limit is one’s imagination, as this malleable medium can bring even the most ambitious designs to life.
Recap