Understanding popcorn polymer can greatly enhance your safety practices in technical construction projects, this guide will provide you with essential information on how to safely and effectively use this unique material.
Key takeaways:
- Popcorn polymer has high strength-to-weight ratio and fire resistance.
- Popcorn polymer forms through polymerization process with blowing agent.
- Popcorn polymer is used for insulation, sealants, composites, and more.
- Incidents highlight the importance of proper handling and application.
- Regulatory bodies set guidelines to ensure safe usage of popcorn polymer.
Definition of Popcorn Polymer
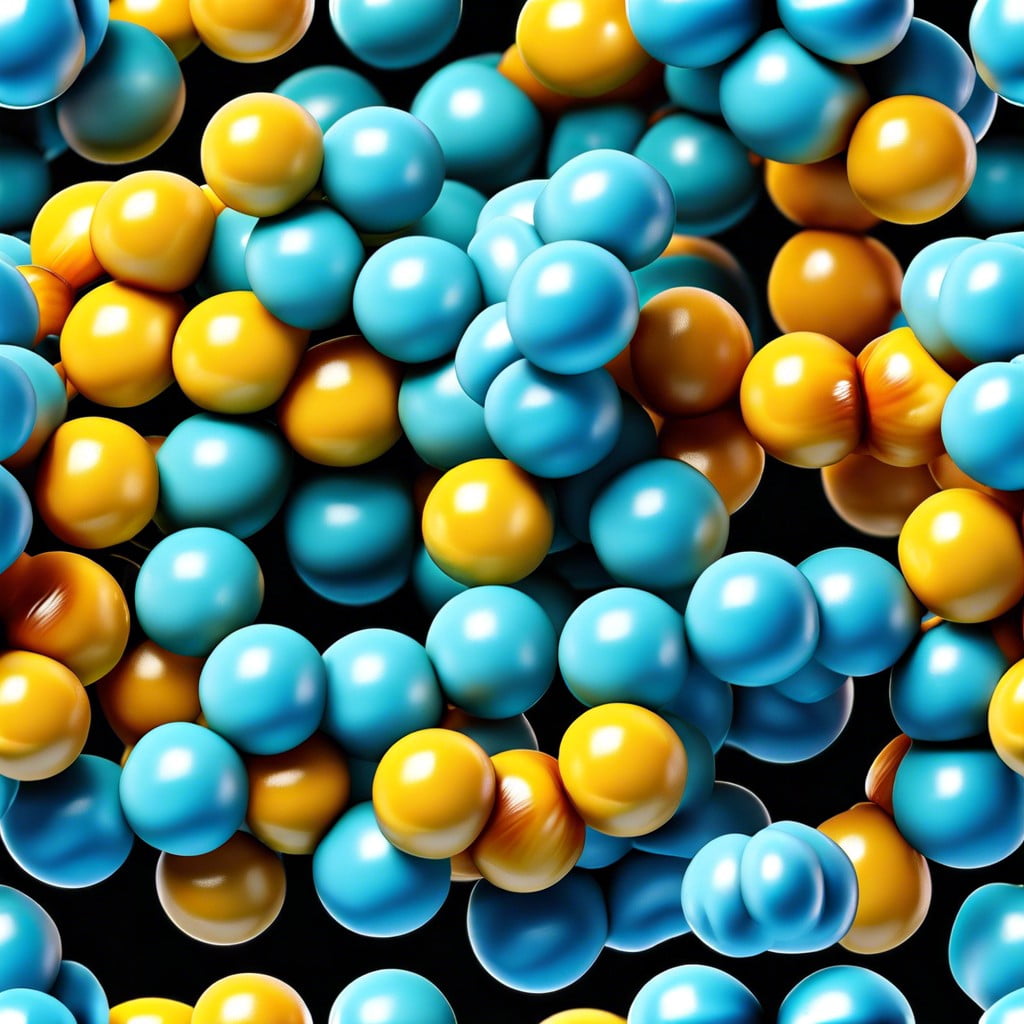
Popcorn polymer, often referred to by the technical name “phenolic foams”, resembles popcorn in texture due to its cellular structure, which is created when a phenolic resin reacts with a foaming agent. This unique structure offers excellent insulation properties, making it a valuable material in the construction industry.
The moniker “popcorn” comes from the material’s expanded, puffy appearance, much like the popular snack. Despite the lightness implied by its name, popcorn polymer is noted for its high strength-to-weight ratio and fire resistance, attributes that are crucial in building applications where safety and durability are paramount.
Formation Process of Popcorn Polymer
Popcorn polymer forms through a process known as polymerization, where small molecules called monomers join to create long chains. For popcorn polymers, this process involves a blowing agent. Here’s how it unfolds:
1. Initiation: Monomers, often styrene, are mixed with a blowing agent under controlled conditions. The reaction begins with the application of heat or a chemical initiator.
2. Expansion: As the temperature rises, the blowing agent, typically a gas such as pentane, activates and expands. This creates small, closed-cell bubbles within the material, much like kernels popping into popcorn.
3. Cooling and Solidifying: Once the desired degree of expansion is reached, the material is cooled. This halts the reaction and solidifies the structure, locking the ‘popped’ bubbles in place, which results in a lightweight, yet rigid polymer.
4. Curing: Finally, the polymer may undergo additional treatments, like curing, to achieve specific properties, such as enhanced strength or resistance to moisture.
Understanding the fine balance of temperature, monomer, and blowing agent is crucial to producing popcorn polymers with specific characteristics suitable for construction applications.
Applications in Construction
Popcorn polymer, due to its unique structure, finds a niche in the construction industry, enhancing materials used in varied applications. Its high expansion ratio lends it to act as an efficient insulating agent in walls and roofs. When integrated into sealants, its expansive nature helps to fill in cracks and gaps, providing airtight seals that enhance energy efficiency.
Additionally, its lightweight yet robust qualities make it a preferred choice for creating composite materials. These composites offer strength without significantly adding to structural weight, beneficial for modern architectural designs. Its shock-absorbing properties are advantageous in flooring systems, particularly in spaces where reduced vibration and noise levels are desired.
Given its resistance to moisture and mold growth, it is also used to protect vulnerable areas of buildings from water damage. Within concrete, popcorn polymer beads can be added to improve the mixture’s workability and reduce its overall density, which can be especially useful in non-load-bearing structures where weight is a concern.
Lastly, it’s utilized in decorative elements due to its ability to be molded into various shapes and textures, providing an artistic flair to building facades and interior elements. These practical applications demonstrate how popcorn polymers contribute to innovative and efficient construction techniques.
Case Studies: Incidents Involving Popcorn Polymer
Popcorn polymer’s unique expanding properties have led to significant incidents that underscore the need for proper handling and application within the construction field. One noteworthy case was at a manufacturing plant where the polymer was inadvertently exposed to moisture, triggering an uncontrolled expansion. This resulted in structural damage to the facility due to the pressure exerted by the expanding material.
In another instance, a residential building experienced severe indoor air quality issues when popcorn polymer used for insulation broke down over time, releasing volatile organic compounds (VOCs) into the living space. This situation highlighted the importance of understanding the longevity and environmental interactions of polymers.
Furthermore, a bridge retrofit project saw the innovative use of popcorn polymer as a lightweight fill material. However, incorrect mixing ratios during installation led to uneven expansion and, consequently, structural inconsistencies that had to be rectified at additional costs.
These examples emphasize the necessity for meticulous attention to material specifications, environmental conditions, and long-term behavior when utilizing popcorn polymer in construction to ensure safety and durability of the structures.
Regulatory Considerations and Standards
Regulatory bodies such as the U.S. Environmental Protection Agency (EPA) and the European Chemicals Agency (ECHA) set guidelines to ensure materials like popcorn polymer are used safely and responsibly in construction. These guidelines focus on the chemical’s impact on indoor air quality, flammability, and potential toxicity.
Industry standards, such as the American Society for Testing and Materials (ASTM), often detail the methods for testing polymer properties and performance criteria for building materials. Contractors and manufacturers need to comply with these regulations and standards, which also include proper labeling, safe handling practices, and disposal procedures for polymer waste.
Regular updates to these regulations reflect ongoing research and technological improvements, ensuring materials are used in a way that prioritizes health and safety.
FAQ
What is popcorn polymer?
Popcorn polymer, also known as α-polymer, is a porous polymeric resinous material that resembles popcorn in appearance and behaves like a macroporous copolymer with a small specific inner surface.
What are the hazards of popcorn polymer?
The hazards of popcorn polymer include its ability to build mechanical force that can rupture process equipment and potentially cause blockage in safety venting devices.
How are popcorn polymers used in the construction industry?
Popcorn polymers are used in the construction industry to create lightweight, sound-absorbing insulation materials.
What are the properties that make popcorn polymers advantageous for specific applications?
Popcorn polymers are advantageous for specific applications due to their exceptional structural stability, flexible physical properties, high chemical resistance, and ability to absorb and desorb gases and volatile organic compounds.
Are there sustainable or eco-friendly alternatives to popcorn polymers in building materials?
Yes, there are sustainable alternatives to popcorn polymers in construction, such as biodegradable polymers, recycled polymers, and natural fiber-reinforced polymers.
Recap