Dive into the fascinating world of polymer resins, because understanding this powerful material opens up a range of possibilities for construction advancements.
Key takeaways:
- Polymer resins are long chains of molecules with unique properties.
- Resins can be synthetic or derived from plants.
- There are two main types of resins: thermoplastic and thermoset.
- Thermoplastic resins can be melted and reshaped, while thermoset resins become permanently solid.
- Resins are widely used in construction for their adhesive qualities and durability.
What Are Polymers?
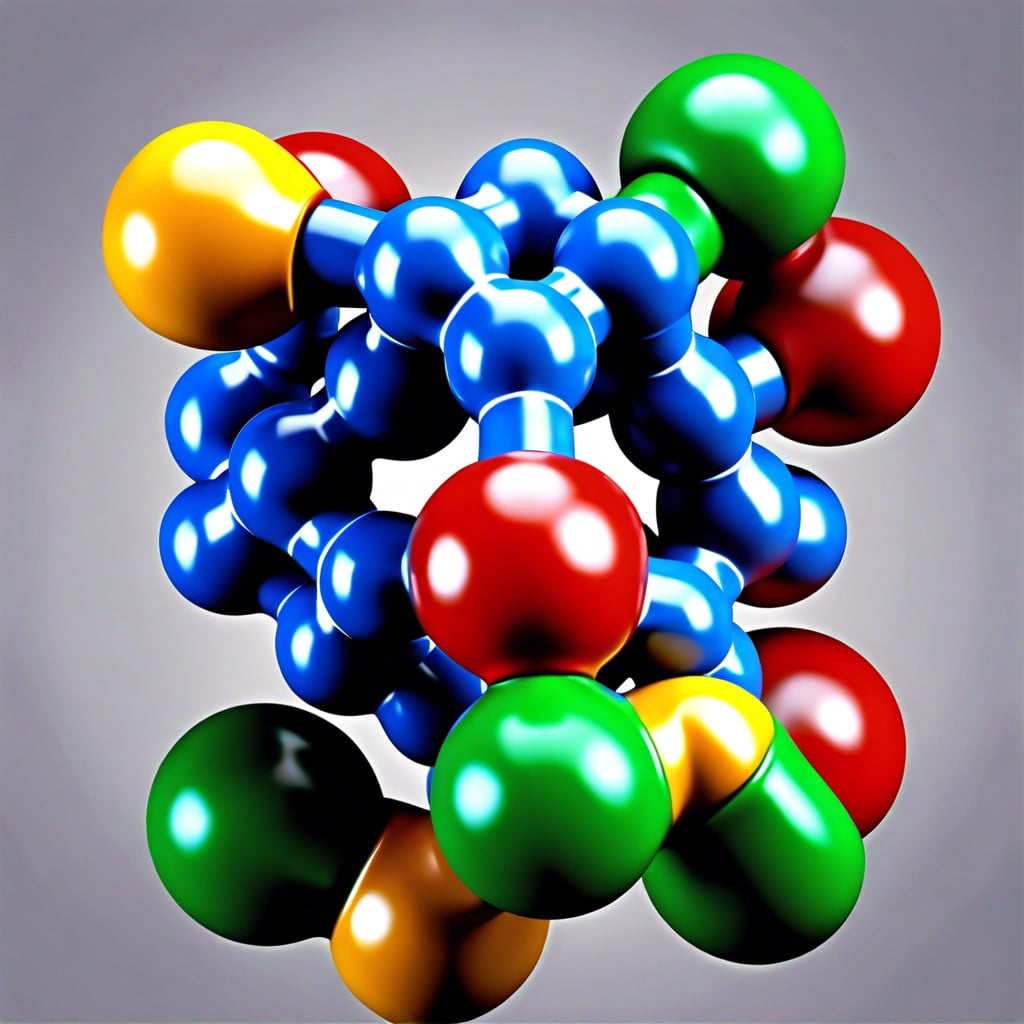
Polymers are long, repeating chains of molecules that form the building blocks of many materials around us. They come in both natural and synthetic forms. For example, the DNA in our cells is a natural polymer, as is cellulose in plants.
Synthetic polymers, on the other hand, include plastics, which play an integral part in various industries including construction. The properties of polymers, such as flexibility, durability, and their ability to be molded, make them ideal for an array of applications. These properties are a result of the size and structure of the molecular chains that compose them.
Depending on how these chains interact and are processed, polymers can be rigid, like in PVC pipes, or elastic, like rubber.
What Are Resins?
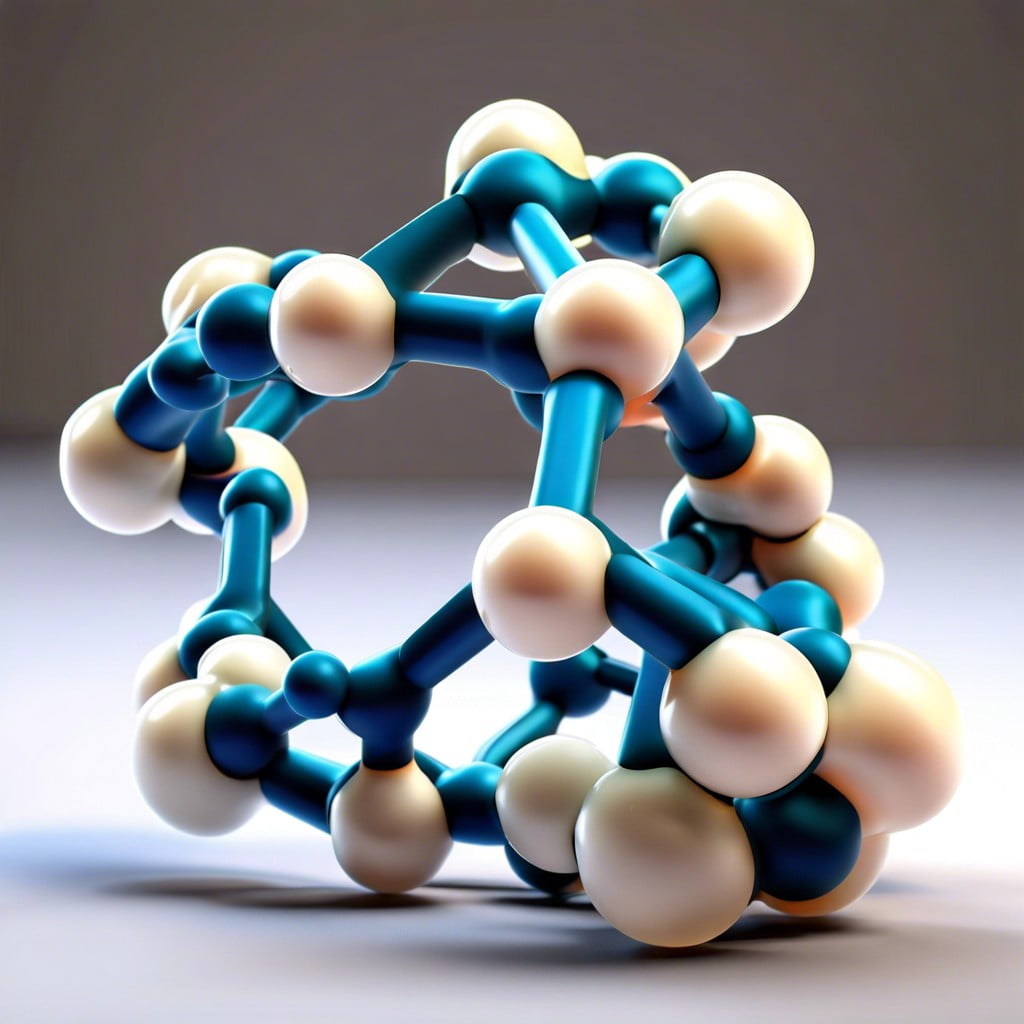
Resins are viscous substances that can be either synthetic or derived from plant exudates. In their raw state, they are typically sticky and convertible into polymers. These liquid compounds harden upon curing, a chemical process that forms a solid, three-dimensional network. Resins are valued for their ability to create protective, durable finishes and for being the foundational material in various composites.
They serve a pivotal role in the production of plastics, varnishes, and adhesives. When discussing construction, resins are frequently employed for their adhesive qualities, corrosion resistance, and insulation properties, making them integral in the creation of sealants, flooring, and structural components.
Is a Resin a Polymer?
Absolutely, resin is a type of polymer.
Polymers are long, repeating chains of molecules that have unique physical and chemical properties.
Resin, in this vast polymer family, serves a special role due to its characteristics.
It starts as a viscous substance, which hardens when treated with heat, light, or a catalyst.
This transformation is what makes resin ideal for creating solid, durable finishes and structures in construction and numerous other applications.
The hardening process, known as curing, gives the resin its final properties – like high strength and resistance to environmental factors.
Whether it’s in a protective coating, adhesive, or composite, when you encounter a cured resin, you’re dealing with a polymer specifically engineered to perform a certain task.
Types of Resins
Thermoplastic resins soften when heated and can be remolded multiple times, making them versatile for applications like packaging, automotive parts, and consumer goods. Common examples include polyethylene, polystyrene, and polyvinyl chloride.
On the other hand, thermoset resins undergo a chemical reaction when heated, setting into a permanent shape. Due to their rigidity and heat resistance post-curing, they’re ideal for high-stress environments, like in electrical insulation and aerospace composites. Epoxy, phenolic, and polyester resins fall under this category.
Both types are pivotal in various applications, with thermoplastics being recyclable and thermosets valued for structural strength. Their unique properties determine their specific uses in the construction field.
Thermoplastic Resins
Thermoplastic resins are unique for their ability to be melted down and reformed multiple times, which allows for easy recycling and reshaping. When heat is applied, they soften into a moldable state, and upon cooling they harden. This reversible process differentiates them from thermoset resins, which cannot be melted down once they have cured.
Common examples include polyethylene (PE), used in plastic bags and bottles, polyvinyl chloride (PVC), found in pipes and window frames, and polystyrene (PS), which we see in disposable cutlery and foam packaging. In construction, thermoplastic polymers are valued for their versatility, ease of fabrication, and durability, making them ideal materials for components like pipes, insulation, and flooring.
Thermoset Resins
Thermoset resins are materials that, once cured, cannot be melted and remolded. This irreversible chemical process occurs when the resin is subjected to heat, light, or a catalyst, leading to a densely cross-linked polymer structure. This unique characteristic gives thermosets superior dimensional stability and heat resistance compared to thermoplastics.
Characteristics of thermoset resins include their ability to maintain strength and shape under high temperatures, resistance to chemical and weather damage, and electrical insulating properties. They are ideal for applications demanding long-term durability.
Common thermoset resins are epoxy, phenolic, and polyester resins. Epoxy is known for its strong adhesive qualities, making it a staple in coatings, electronics, and the aerospace industry. Phenolic resins are often found in molded products like billiard balls and countertops, while polyester resins are widely used in fiberglass materials, such as boat hulls and car bodies.
Each type of thermoset resin offers different properties and advantages, allowing for a wide array of applications in construction, automotive, aerospace, and electrical industries. The selection of a thermoset resin relies heavily on the intended function and desired performance of the end product.
Resin Curing
The process of resin curing transforms the liquid resin into a solid material. This occurs through a chemical reaction, often involving a catalyst or hardener, that cross-links polymer chains.
Here’s what you need to know:
- Curing can be initiated by heat, light, or the addition of a curing agent, depending on the type of resin.
- During curing, the resin’s viscosity increases until it hardens, which is necessary for the material’s performance in construction applications.
- This transformation gives the cured product its desired properties, such as strength, durability, and resistance to environmental factors.
- Cure times can vary, from minutes to hours, depending on the resin system and the curing conditions.
- Proper curing is critical; insufficient curing can result in a product that is weak or has poor chemical resistance.
It’s important to follow the manufacturer’s guidelines for the correct mix ratios and curing conditions to ensure optimal material properties.
Key Qualities of Good Resin
When choosing a good resin, consider the following characteristics:
- Durability: The resin should withstand daily wear and tear, and be resistant to impacts and scratches.
- Chemical resistance: Look for a resin that can resist corrosion from common chemicals to maintain its integrity over time.
- Temperature tolerance: High-quality resins maintain their performance under varying temperatures, important for both processing and end-use environments.
- Adhesion: A resin should exhibit excellent bonding properties to ensure a stable and secure hold when used with other materials.
- Water resistance: To prevent degradation, the resin should not absorb moisture, making it suitable for outdoor or high-humidity applications.
- Electrical insulation: Good resins are often non-conductive, which is crucial for applications in electrical components.
- Aesthetics: For visual applications, a quality resin should allow for a clear or colorable finish, and resist yellowing with age.
- Viscosity: Depending on the application, a resin with appropriate viscosity will ensure ease of processing and a defect-free finished product.
Selecting a resin with these qualities ensures the material meets the performance requirements of its intended application.
Main Uses of Engineering Resins
Engineering resins have become integral in various construction applications due to their high performance and durability. Here are some primary ways they’re utilized:
– Building Infrastructure: They reinforce structures like bridges and buildings, offering corrosion resistance and strength. – Electrical Components: Used in insulators, connectors, and housings, these resins provide excellent electrical insulation properties. – Plumbing Systems: Pipes and fixtures made from engineering resins are light, resistant to chemical corrosion, and easy to install. – Flooring Solutions: Epoxy resins deliver tough, long-lasting surfaces for industrial floors, withstanding high traffic and chemical spills. – Sealants and Adhesives: They create strong bonds and can seal gaps, contributing to airtight and watertight construction assemblies.Engineering resins ensure structures and components are both suitable for their purpose and equipped to last.
Resin Composites
Combining resin with reinforcing fibers creates a composite material known for its enhanced mechanical properties. This synergy results in materials that are durable, lightweight, and capable of replacing metals in some applications.
For example, in the aerospace industry, carbon fiber-reinforced composites offer a high strength-to-weight ratio, essential for fuel efficiency. Likewise, fiberglass, a glass fiber-reinforced composite, is common in boat construction due to its resistance to water and corrosion.
Additionally, construction benefits from resin composites in the form of reinforced polymer concrete, which boasts increased tensile strength compared to traditional concrete. These composites can be tailored to suit a vast range of uses by adjusting the type and amount of fiber reinforcement, resulting in customized materials for specific engineering needs.
FAQ
What is polymer resin?
Polymer resin is a solid or highly viscous substance of either plant or synthetic origin which can be converted into polymers.
What is the difference between plastic and polymer resin?
While polymer resin is an unprocessed form with high versatility and ease of repair, plastic, on the other hand, is the final processed product which lacks these properties.
Is polymer resin safe?
Polymer resins, specifically those based on formaldehyde, are not safe due to their toxic, carcinogenic properties, non-recyclable nature, and large CO2 footprint.
Is polymer and epoxy the same thing?
No, polymer and epoxy are not the same thing; while epoxy is a type of polymer, not all polymers are epoxy.
How is polymer resin used in construction?
Polymer resin in construction is mainly used as an adhesive to bind construction materials together, as a sealing agent to fill gaps, and as a surface coating to improve resilience and aesthetics.
What are the benefits of using polymer resins over traditional materials in building practices?
Polymer resins, compared to traditional construction materials, offer advantages such as improved durability, corrosion resistance, high strength-to-weight ratio, versatility in design, cost-effectiveness and sustainability.
What are some common types of polymer resins and their specific applications in construction?
Common polymer resins used in construction include polyvinyl chloride for pipework, urea-formaldehyde resins for adhesives and insulation, polyurethane for sealants and coatings, and polysulfide polymer for sealants in joints and glazing.
Recap