Discover the transformative role of polymer concrete in the construction industry because of its impressive durability and adaptability that outperforms traditional materials.
Discover the innovation of polymer concrete, a cutting-edge composite material transforming the construction industry.
Unlike traditional concrete, this durable amalgam utilizes synthetic polymers as its binder, unlocking a host of superior qualities that cater to modern building demands.
High strength, quick curing times, and impressive chemical resistance are just the tip of the iceberg.
Whether you are in the industry, or simply intrigued by this resilient material, our comprehensive guide delves into the intricacies of its composition—from resins to aggregates—and explores the various polymers that forge its robustness.
Understanding the multifaceted properties of polymer concrete, such as its high compressive and tensile strength, low permeability, and its relatively lighter weight, will reveal why it’s rapidly becoming the go-to choice for a myriad of construction applications.
Key takeaways:
- Polymer concrete is a composite material where the binder consists entirely of a synthetic polymer.
- It offers high strength, rapid curing, and increased chemical resistance.
- Polymer concrete is composed of resins, aggregates, additives, and initiators.
- Types of polymers used in polymer concrete include epoxy resins, polyester resins, vinyl esters, methacrylates, polyurethanes, and acrylics.
- Polymer concrete has properties such as high compressive and tensile strength, low permeability, quick curing time, and lighter weight compared to traditional concrete.
Definition of Polymer Concrete
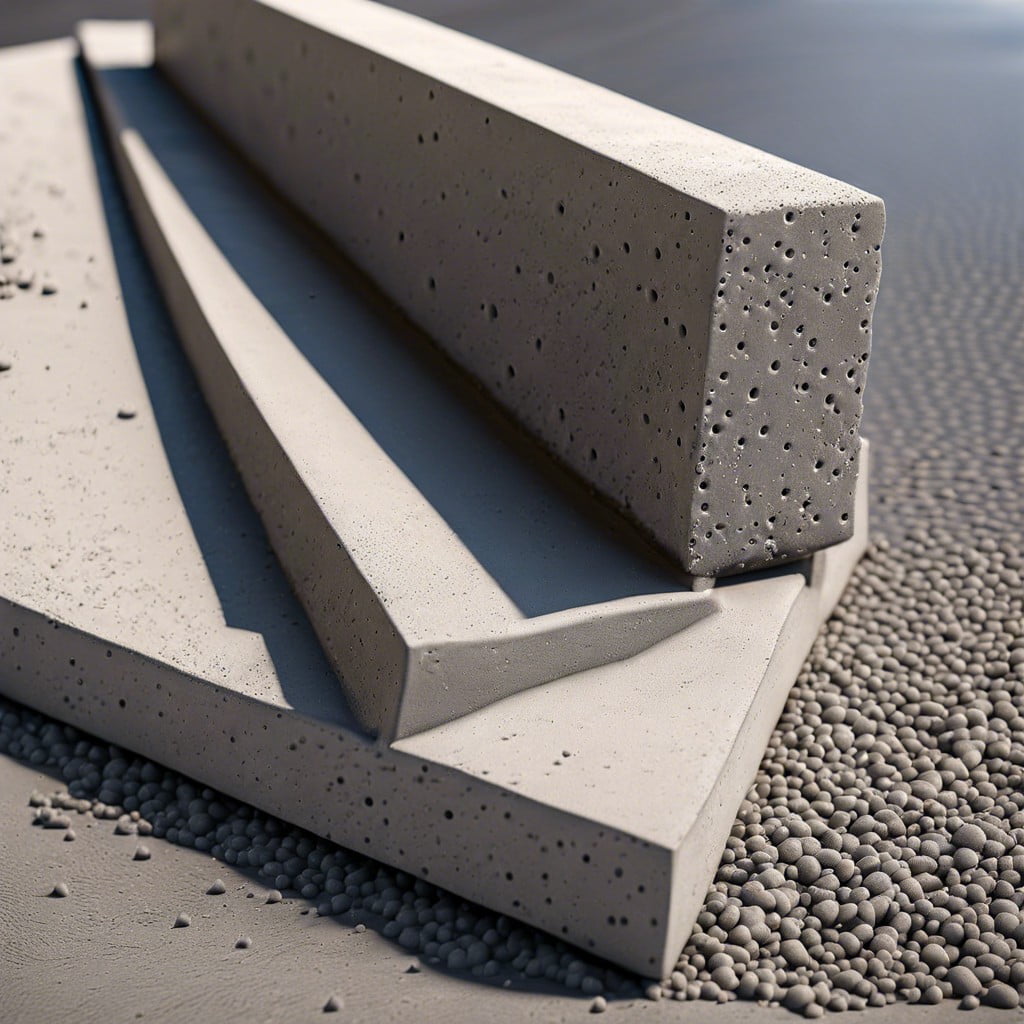
Polymer concrete is a composite material where the binder consists entirely of a synthetic polymer. It is a compound that combines polymer resins with aggregates, such as gravel, sand, or other fine and coarse mineral fillers. Unlike traditional concrete, which uses cement as a binder, the polymer acts as an adhesive, creating a stronger, more durable and versatile building material.
This unique combination lends polymer concrete exceptional properties: high strength, rapid curing, and increased chemical resistance. Its ability to adapt to different environments and resist a variety of chemicals makes it ideal for specialized construction applications, particularly where performance under stress and longevity are crucial.
Composition of Polymer Concrete
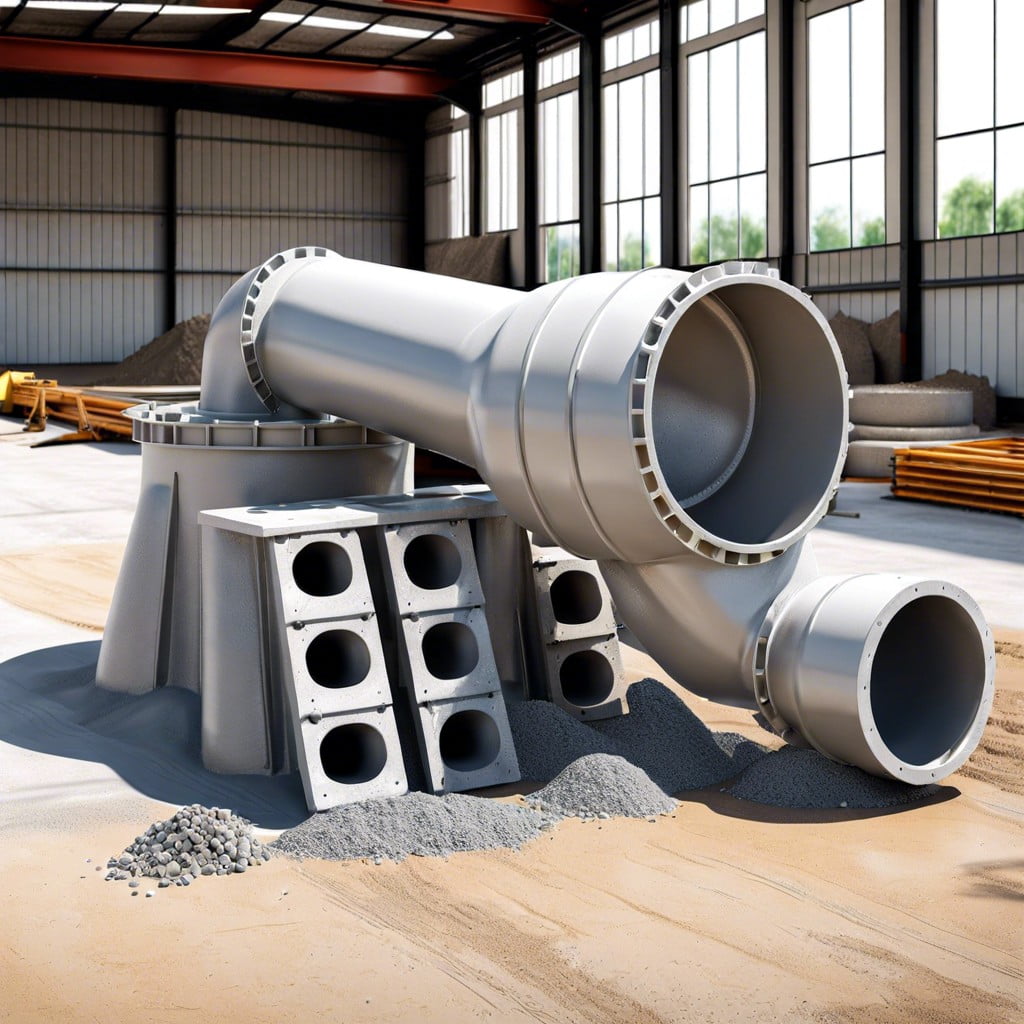
Polymer concrete is a composite material where the binder consists of a polymer instead of traditional cement. This combination endows it with unique characteristics and versatility in applications.
Here’s a look at what goes into its making:
- Resins: Epoxy, polyester, or vinyl ester resins are common choices that serve as the glue holding the material together. Each resin varies in properties, affecting the final product’s strength and environmental resistance.
- Aggregates: Similar to traditional concrete, polymer concrete also contains aggregates such as gravel, sand, and sometimes even glass fibers. The choice and size of aggregates influence the strength and weight of the final product.
- Additives: Various additives can be included to adjust setting times, enhance strength, or confer additional properties like increased resistance to chemicals or UV light.
- Initiators: When using certain resins, initiators are necessary to start the chemical reaction that causes the resin to set and harden.
It’s the synergy between these materials that allows polymer concrete to achieve its notable durability, rapid curing, and high tensile strength. Understanding the role of each ingredient provides insight into how this innovative material can be tailored to specific construction needs.
Types of Polymers Used in Polymer Concrete
Polymers play a crucial role in enhancing the qualities of concrete. They act as the binding agent in polymer concrete, replacing traditional cement. The selection of polymers depends on the desired characteristics and the specific application.
Here are a few commonly used types:
- 1. Epoxy Resins: They offer excellent adhesion, good chemical resistance, and high strength, making them suitable for heavy-duty applications.
- 2. Polyester Resins: Cost-effective and provide quick curing times, polyester resins are widely used for general-purpose repairs and construction.
- 3. Vinyl Esters: Superior in corrosion resistance and durability, vinyl esters are ideal for harsh environmental conditions.
- 4. Methacrylates: With fast curing times and good penetration capabilities, methacrylates are excellent for quick repairs and bonding new concrete to old.
- 5. Polyurethanes: Known for their flexibility, polyurethanes can withstand a wide temperature range and are good for applications requiring some movement.
- 6. Acrylics: These provide exceptional weatherability and are used in decorative facades and surfaces exposed to UV light.
Each polymer type imparts distinct advantages to the final product. Understanding the properties of these materials allows engineers to tailor polymer concrete for specific conditions, ensuring longevity and performance.
Properties of Polymer Concrete
Polymer concrete boasts an impressive array of properties that make it a standout material for construction projects. Its high compressive and tensile strengths mean it can withstand significant pressure and stress, outperforming traditional concrete in these regards.
It also has a low permeability to water and chemicals, providing enhanced resistance to corrosion, a common issue in structures exposed to harsh environments. The thermal expansion of polymer concrete is lower, which helps prevent cracking due to temperature changes.
Its quick curing time allows for faster completion of construction projects—a significant time and cost-saving benefit. Notably, polymer concrete is also lighter in weight compared to traditional concrete, facilitating easier handling and reducing transportation costs.
Advantages of Using Polymer Concrete in Construction
Polymer concrete boasts remarkable strength, often surpassing that of traditional cementitious concrete. Thanks to the polymeric binder, its adhesive qualities are greatly enhanced, affording a stronger bond between aggregates. This results in higher compressive and flexural strength, which is paramount for structural applications.
Speed of setting is another significant benefit. Polymer concrete cures rapidly, permitting early traffic on roads and minimal downtime in construction projects. The quick setting time also aids in achieving tighter construction schedules and reducing labor costs.
In terms of resistance, polymer concrete is superior when facing chemical attacks and harsh weather conditions. Its non-porosity prevents the penetration of aggressive substances, which makes it ideal for chemical containment, wastewater treatments, and industrial flooring.
Durability is a key feature, too. Structures made of polymer concrete are more resilient to freeze-thaw cycles, diminishing the risk of cracking and ensuring a longer lifespan. Plus, it’s less likely to suffer from spalling, which is the flaking or chipping of concrete surfaces.
With a lower weight than traditional concrete, it eases the load on structures and transportation, all without compromising its mechanical properties. This weight reduction can lead to savings in the supporting structure and foundation.
Lastly, its seamless finish not only looks appealing but also provides a safer, skid-resistant surface, enhancing safety in pedestrian and vehicular areas.
Polymer Concrete Vs Traditional Concrete: Comparisons
When comparing polymer concrete with traditional concrete, a few key differences stand out. First, polymer concrete typically sets faster than traditional concrete, offering significant time-saving during construction projects. Its quick curing time allows for earlier traffic opening or continuation of the construction process, minimizing downtime.
Secondly, the bond strength of polymer concrete exceeds that of traditional concrete, resulting in a tougher material that can handle greater loads and resist more intense stresses. This enhanced durability means polymer concrete is often chosen for applications requiring high performance, such as repair works or heavy traffic areas.
Thirdly, the chemical resistance of polymer concrete is superior to that of traditional concrete. This property makes it a preferable choice for structures exposed to harsh chemicals, like industrial floors or waste treatment facilities, where traditional concrete might degrade more quickly.
Lastly, the lack of a hydration process in polymer concrete means it is not susceptible to freezing and thawing cycles in the same way traditional concrete is. This characteristic contributes to its longevity, especially in environments with extreme temperature fluctuations.
On the other hand, cost and availability can be limiting factors for polymer concrete. It tends to be more expensive due to the polymers used, and might not be as readily available as traditional concrete, which can affect the decision-making process for a project.
Common Uses of Polymer Concrete in Construction
Polymer concrete’s enhanced durability and resistance to a wide array of chemicals make it ideal for specialized infrastructure applications where traditional concrete might fail. Here are some key areas where this material excels:
1. Drainage Systems: It is highly resistant to acidic environments, which is crucial in sewer pipes and drainage systems.
2. Repair Work: Its fast curing time allows for rapid repairs in industrial floors and highways, minimizing downtime.
3. Bridges: It provides a protective overlay on bridge decks, shielding them from the effects of heavy traffic and environmental elements.
4. Electrical Utilities: Owing to its non-conductivity, it is used to make utility boxes, which protect electrical components from moisture and chemicals.
5. Chemical Containment: Facilities that handle corrosive substances use polymer concrete because of its excellent resistance to chemical attack.
Each of these applications takes advantage of the unique qualities of polymer concrete, showcasing its versatility in the construction industry.
Installation of Polymer Concrete
Installing polymer concrete involves a process similar to traditional concrete but with a few key differences to accommodate its unique properties. Here’s a straightforward guide to achieving the best results:
- Surface Preparation: Begin by thoroughly cleaning the area to remove dust, debris, and any contaminants that could interfere with bonding.
- Mixing: Polymer concrete components must be accurately measured and blended. Ensure the polymer resin and hardener ratios are meticulously followed for the mixture to set correctly.
- Pouring: Once mixed, the polymer concrete must be poured immediately due to its rapid setting times. It’s crucial to work fast and efficiently.
- Consolidation: Use tools like trowels or vibration to spread the material into corners and across surfaces, ensuring no air pockets or voids remain.
- Curing: Polymer concrete typically requires less curing time than traditional concrete. Follow manufacturer-specific guidelines for temperature and time to ensure complete curing.
- Finishing: After curing, the surface can be smoothed or textured, depending on the desired finish and its intended use.
Remember, precision and timing are key components when working with polymer concrete to fully leverage its performance benefits.
Maintenance and Durability
Polymer concrete boasts superior durability, largely due to its resistance to a wide range of corrosive agents, including acids, alkalis, and salts. This characteristic makes it an ideal material for applications with high exposure to such substances. Unlike traditional concrete, it does not require a sealing coat to protect it against harsh environments, further reducing maintenance needs.
The material’s resilience to freeze-thaw cycles and UV radiation helps it maintain structural integrity and appearance over time, limiting repair and upkeep requirements. The low water absorption rate of polymer concrete minimizes the potential for damage and decay caused by moisture, a common issue in traditional concrete structures.
Due to its dense and impermeable nature, polymer concrete also resists staining and retains its finish without the need for regular cleaning or special treatments. When maintenance is required, it typically involves simple pressure washing or cleaning with mild detergents.
In terms of longevity, polymer concrete structures can effectively outlast their conventional counterparts, often extending their service life by decades. This longevity translates into long-term cost savings, despite higher upfront installation expenses. The enduring nature of polymer concrete makes it a smart investment with a view toward infrastructure sustainability and reduced frequency of replacement or major repair work.
Environmental Impact and Sustainability of Polymer Concrete
Polymer concrete, being a composite material, carries a distinct set of environmental considerations. The sustainability of the polymer used greatly influences the overall impact of the concrete. Here’s how:
1. Resource Efficiency: Polymers can be derived from recycled plastics, reducing the need for virgin materials and promoting a circular economy.
2. Energy Footprint: The curing process of polymer concrete often requires less energy than traditional concrete, contributing to a reduced carbon footprint.
3. Durability: With a longer lifespan than conventional concrete, polymer concrete requires less frequent replacement, minimizing resource use over time.
4. Toxic Chemicals: Some polymers involve hazardous chemicals during manufacture. The industry is progressing towards more eco-friendly resins with reduced toxicity.
Understanding these points can guide better environmental practices in the construction industry and help stakeholders make informed decisions.
Cost Considerations of Polymer Concrete
Evaluating the cost of polymer concrete involves more than just comparing price tags with traditional concrete. Initially, polymer concrete tends to be more expensive per unit due to the cost of resin which serves as the binder. However, this higher upfront cost is often offset by long-term savings. Here’s why:
- Durability: Polymer concrete’s resistance to chemicals and environmental factors means less frequent repairs and replacements, translating into cost savings over the life of a project.
- Installation Efficiency: This material can be pre-cast or rapidly cured on-site, leading to shorter project timelines and reduced labor costs.
- Lower Maintenance: Its non-porous nature minimizes maintenance costs since it does not require sealing against water penetration like traditional concrete does.
- Reduced Thickness: Polymer concrete can often be applied in thinner layers than conventional concrete for the same application, saving material costs.
- Longevity: With its enhanced durability, structures built with polymer concrete can have significantly longer lifespans, providing a better return on investment.
When considering polymer concrete, it’s beneficial to conduct a life cycle cost analysis to fully comprehend the economic impact, taking into account both immediate and long-term financial implications. Some projects might find the investment worthwhile, especially in environments harsh to traditional concrete.
Specifications and Standards for Polymer Concrete
To ensure quality and performance, it is important that polymer concrete meets certain specifications and standards. These benchmarks serve to provide uniformity in testing methods, to assess properties like strength and adhesion, and to determine appropriate applications.
ASTM International Standards: ASTM provides a set of standards for polymer concrete, which includes ASTM C579 for testing the compressive strength, ASTM C580 for evaluating the flexural strength, and ASTM D412 for determining the tensile properties.
ISO Standards: The International Organization for Standardization also publishes standards relevant to polymer concrete, such as ISO 10406-2 for testing fiber-reinforced polymers.
American Concrete Institute (ACI) Guidelines: The ACI has guidelines that cover design, production, and application of polymer concrete to ensure structural soundness.
European Standards (EN): In the European market, EN standards apply, with EN 1504-3 specifying requirements for structural and non-structural repairs, which include polymer concrete.
Builders, engineers, and contractors must refer to these standards and guidelines before specifying, mixing, and applying polymer concrete to ensure that the end product will hold up to its intended use and the test of time.
Innovations and Future Outlook in Polymer Concrete Technology
As the construction landscape evolves, the polymer concrete industry is not far behind in embracing innovation. Continuous research and development are yielding exciting advancements that enhance the material’s performance and scope of application:
- Nano-technologies are being explored to improve the strength and durability of polymer concrete. Nano-particles can fill microscopic gaps in the material, leading to denser, more impermeable surfaces.
- Smart polymer concrete is on the horizon, potentially incorporating sensors that monitor structural health in real-time, forewarning of any potential issues such as cracks or stresses.
- The development of bio-based resins is gaining traction. These sustainable alternatives could reduce the environmental footprint of polymer concrete, aligning with green construction principles.
- 3D printing technology is opening doors for complex shapes and forms made from polymer concrete, allowing for more architectural freedom and reduced waste.
- Self-healing polymer concrete is an area of particular interest. By integrating microcapsules that release healing agents upon crack formation, the material can repair itself, expanding its lifespan and reducing maintenance costs.
These cutting-edge developments represent just a snapshot of the potential future pathways for polymer concrete, promising a more durable, sustainable, and intelligent infrastructure.
References On Polymer Concrete
To deepen your understanding of polymer concrete, a wealth of scholarly articles, technical data sheets, and industry reports are at your disposal. Professional organizations like the American Concrete Institute (ACI) publish guidelines and standards essential for those in the field. For cutting-edge research, journals such as the Journal of Polymer Engineering and Science offer peer-reviewed articles on the latest advances.
For practitioners, trade publications like Concrete International provide case studies and practical applications, highlighting how polymer concrete performs in real-world settings. Manufacturers often supply data sheets that detail the technical specifications of their polymer-based products, vital for ensuring compliance with project requirements.
Educational institutions may also have published findings from their own studies, which can be rich resources for understanding the fundamental behaviors and properties of polymer concrete under various conditions. Lastly, the internet is a repository of webinars and instructional videos that visually demonstrate polymer concrete applications, handling, and installation techniques, making complex information more accessible.
Informational Resources On Polymer Concrete
For those seeking to expand their understanding of polymer concrete and its applications, a wealth of informational resources is available.
- Professional Organizations: Groups such as the American Concrete Institute (ACI) and the Society for the Advancement of Material and Process Engineering (SAMPE) offer detailed technical resources, including guides and standards relevant to polymer concrete.
- Scientific Journals: Articles from journals like the Journal of Polymer Engineering provide peer-reviewed research findings on the latest developments in the field.
- Trade Magazines: Publications like ‘Concrete Construction’ offer accessible articles focusing on practical applications and case studies.
- Technical Webinars and Workshops: These offer direct interaction with experts in the field and often include Q&A sessions for personalized advice.
- Online Forums and Groups: Platforms like LinkedIn groups or Reddit communities enable networking with peers and experts for tips, troubleshooting, and shared experiences.
- Government and Educational Institution Publications: Many universities and government bodies publish research papers and reports on infrastructure projects involving polymer concrete.
- Manufacturers’ Literature: Technical datasheets, product manuals, and white papers from polymer concrete product manufacturers provide usage instructions and performance data.
By tapping into these resources, professionals and enthusiasts alike can stay informed on the latest best practices, innovations, and research in the use of polymer concrete in construction.
Practice Oriented Papers and Articles On Polymer Concrete
Practice oriented papers and articles offer valuable insights into the real-world applications and techniques involved with polymer concrete. They often present case studies that highlight the material’s performance in various environmental conditions and structural demands.
Here are some key insights from such literature:
- Installation Best Practices: These resources provide step-by-step guides on how to correctly mix, pour, and cure polymer concrete to ensure the best outcomes.
- Repair and Retrofitting: Papers may detail methods for using polymer concrete in repairing existing structures, showcasing its adhesive properties and compatibility with different materials.
- Innovative Applications: Learn from examples where polymer concrete has been used in novel ways, such as in the creation of chemical-resistant tanks or as a protective coating for bridges and piers.
- Cost-Benefit Analysis: Articles often include comparative studies analyzing the long-term costs savings due to the durability and low maintenance of polymer concrete.
- Technological Advancements: These writings keep professionals abreast of the latest advancements in polymer concrete formulations and equipment used for its application.
By exploring these resources, construction professionals can stay informed on the practical aspects of working with polymer concrete, leading to more effective and innovative uses of the material in the field.
Education Publications On Polymer Concrete
For professionals and students eager to deepen their understanding of polymer concrete, various educational publications offer insights. Textbooks and academic journals often contain detailed chapters dedicated to the material, exploring its chemical composition, mechanical properties, and applications in construction.
Highly regarded journals publish peer-reviewed articles that discuss recent advancements and research findings. Meanwhile, technical reports from industry associations can be invaluable for practical knowledge, providing guidelines on best practices for installation and maintenance.
Online platforms and educational databases like JSTOR or ScienceDirect are treasure troves of such literature. Conference proceedings and symposium papers also give snapshots of cutting-edge innovations and collaborative efforts in the field.
For those seeking learning materials with a more instructive slant, instructional videos and webinars presented by experts can offer step-by-step demonstrations on working with polymer concrete. Moreover, university courses may include studies on advanced building materials, often available through open courseware, bridging the gap between academia and real-world application.
Why Polymer Concrete?
Polymer concrete (PC) is chosen for its superior qualities over traditional concrete. Here are a few reasons:
- Enhanced Strength: PC has a higher compressive and tensile strength, which enables structures to withstand heavy loads and harsh conditions without cracking.
- Rapid Curing: It sets quickly, significantly reducing waiting times before a structure can be put into service.
- Chemical Resistance: The non-porous nature of PC makes it highly resistant to a wide range of chemicals, making it ideal for industrial flooring and chemical containment structures.
- Durability: The material’s exceptional durability extends the lifespan of installations, ensuring they remain functional for years with minimal maintenance.
- Lightweight Nature: PC is lighter than conventional concrete, easing the load on structures and reducing transportation and handling costs.
- Waterproof: Its low permeability prevents water infiltration, protecting reinforced steel elements within concrete from corrosion.
Each of these points contributes to why polymer concrete is a choice material for many construction applications, especially where traditional concrete might fall short.
The Problem: Corroded Precast Concrete
Precast concrete, favored for its strength and efficiency, often succumbs to the relentless force of corrosion. This degradation process accelerates in harsh environments where chemicals, salt, and moisture relentlessly attack the reinforcements within the concrete.
Here’s how corrosion undermines the integrity of precast concrete:
- Chemical Attacks: When harmful chemicals infiltrate concrete, they can cause reactions that deteriorate the material from within.
- Salt Induced Corrosion: In coastal areas or regions where deicing salts are used, chloride ions can penetrate precast concrete and corrode the steel reinforcement, undermining structural integrity.
- Carbonation-Induced Corrosion: Exposure to carbon dioxide reduces the concrete’s pH, compromising the natural passivation layer that protects steel rebars, leading to rust and weakening.
- Moisture Penetration: Water seeps into concrete over time, which can result in internal damage and promote corrosion of the embedded metal.
- Freeze-Thaw Cycles: In cold climates, the freeze-thaw process can exacerbate minute cracks, facilitating the entry of corrosive agents and accelerating structural decay.
Addressing these corrosion issues is crucial to preserving the longevity and safety of precast concrete structures.
The Solution: Armorock Polymer Concrete
Armorock polymer concrete represents a cutting-edge solution to tackle the issue of corrosion in precast concrete structures. By integrating polymer resins with traditional concrete constituents, it significantly enhances the durability of construction materials.
Here are some key points to understand about Armorock:
- Corrosion Resistance: The polymer matrix in Armorock does not succumb to corrosion like conventional steel reinforcement, ensuring a longer service life for structures exposed to harsh chemicals or saltwater environments.
- High Strength: It possesses a high compressive and flexural strength, which makes it capable of withstanding heavy loads and impact without compromising integrity.
- Low Maintenance: With its non-porous nature, it resists water infiltration and, as a result, reduces the need for frequent maintenance operations.
- Rapid Installation: Armorock slabs can be quickly installed due to their prefabricated nature which saves time on construction sites.
- Versatility: It is suitable for a wide range of applications, from sewer systems to marine structures, providing a robust solution for areas demanding high durability.
- Customizability: The material can be tailored to meet specific performance requirements, such as dimensional stability or thermal resistance, by adjusting the type and quantity of polymer resin used.
Through these points, it is evident that Armorock polymer concrete offers a practical and lasting solution for modern construction challenges.
FAQ
What is a polymer concrete?
A polymer concrete is a type of composite material where the traditional cement hydrate binders in regular cement concrete are entirely replaced with polymer binders or liquid resins, resulting in a distinctive concrete-polymer composite.
Is polymer concrete stronger than concrete?
Yes, polymer concrete is stronger than Portland cement concrete, boasting attributes like increased bond strength, enhanced freeze-thaw resistance, and high abrasion resistance.
What is the difference between polymer concrete and polymer modified concrete?
Polymer concrete substitutes Portland cement with a polymer binder, while polymer modified concrete incorporates polymer solutions into the traditional Portland cement concrete mix to enhance desired properties.
What are the primary components of polymer concrete?
The primary components of polymer concrete are an aggregate mixture and a polymer resin used as a binder.
How does the production process of polymer concrete differ from traditional concrete?
The production process of polymer concrete differentiates from traditional concrete through the inclusion of polymers or synthetic resins as a main component instead of cement, thereby resulting in a higher tensile strength, chemical resistance, and lower permeability material.
What are some specific construction applications where polymer concrete is particularly beneficial?
Polymer concrete is particularly beneficial in construction applications such as bridge decks, industrial flooring, precast components, and trench drains due to its added durability, quick curing times, and superior resistance to chemical corrosion.
Recap