Explore the transformative potentials of polymer technologies because these innovative materials are defining the future of construction.
Polymers are revolutionizing the construction industry, blending unparalleled durability with the creative freedom to fulfill modern structural demands.
Their diverse qualities, ranging from robust strength to exceptional thermal resistance, have made materials like PVC, polystyrene, and polyurethane mainstays in contemporary building practices.
Whether it’s through the precision of polymer injection molding or their ability to mitigate noise and vibrations, these versatile materials are addressing a myriad of construction challenges.
Dive into the world of polymer technologies to uncover how they are pioneering new forms of construction and what makes them such a key component of innovative design strategies.
Key takeaways:
- Polymers have qualities like strength and durability, making them suitable for construction.
- Polymers offer properties like flexibility and thermal resistance for innovative designs.
- Common polymers used in construction include PVC, polystyrene, and polyurethane.
- Polymer injection molding allows for precision, efficiency, and material versatility.
- Polymers can address construction challenges like noise reduction and vibration control.
Polymer Technologies in Construction
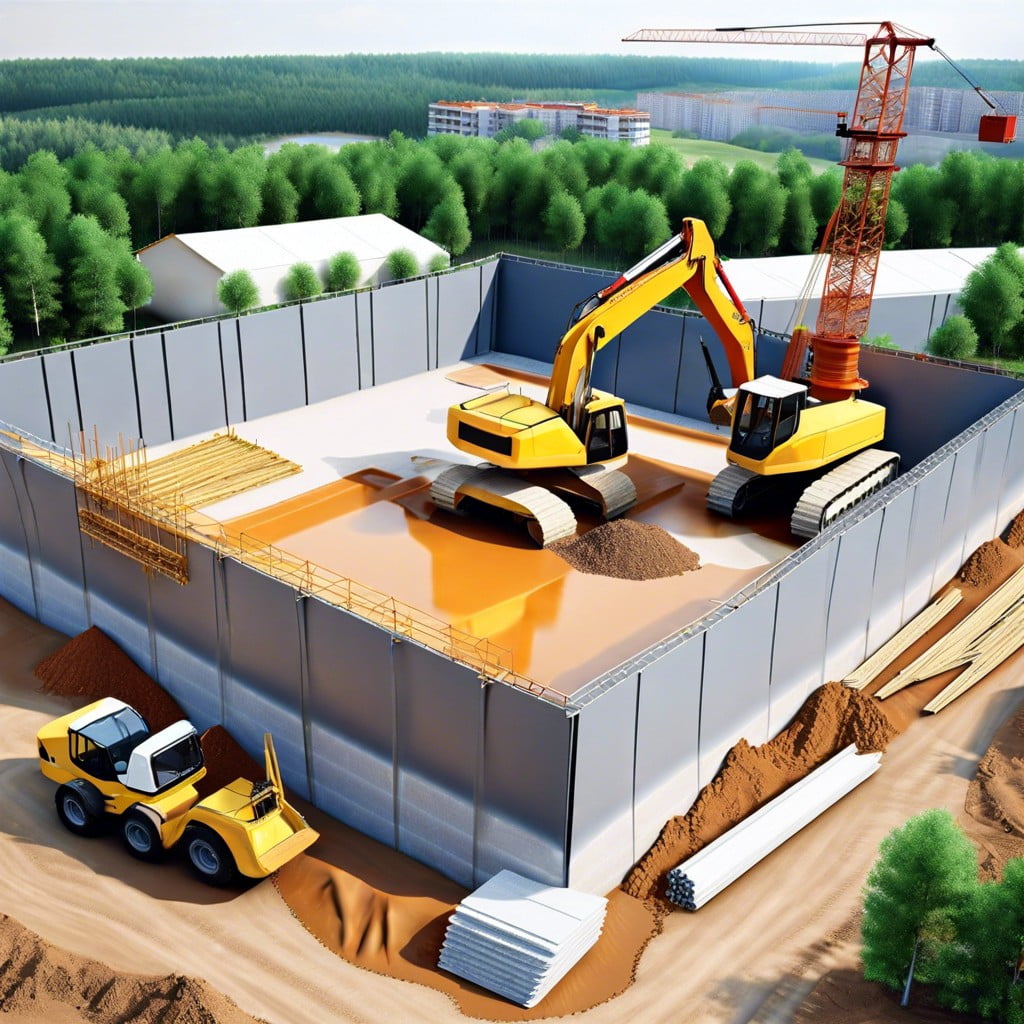
Understanding the unique qualities of polymers enables us to harness their potential in construction. These materials are valued for their strength, durability, and resistance to water, chemicals, and corrosion. Their inherent flexibility also allows them to withstand the natural movement of buildings, especially in areas prone to earth tremors or high winds.
Additionally, polymers can be engineered to have fire-retardant properties, making structures safer.
The versatility of polymers extends to their various forms. Thermoplastics, for example, can be melted and reshaped multiple times, offering recyclability and adaptability to different design needs. Thermosetting plastics, on the other hand, become permanently set and are known for their structural integrity and heat resistance. Elastomers, which include rubbers, provide outstanding elasticity and are indispensable in sealing applications.
By selecting the appropriate polymer type, construction professionals can meet specific functional requirements, such as transparency in polycarbonate panels or the lightweight nature of PVC piping. These smart material choices drive efficiency and performance, underscoring polymers’ significant role in modern-day construction methodologies.
Properties of Construction Polymers
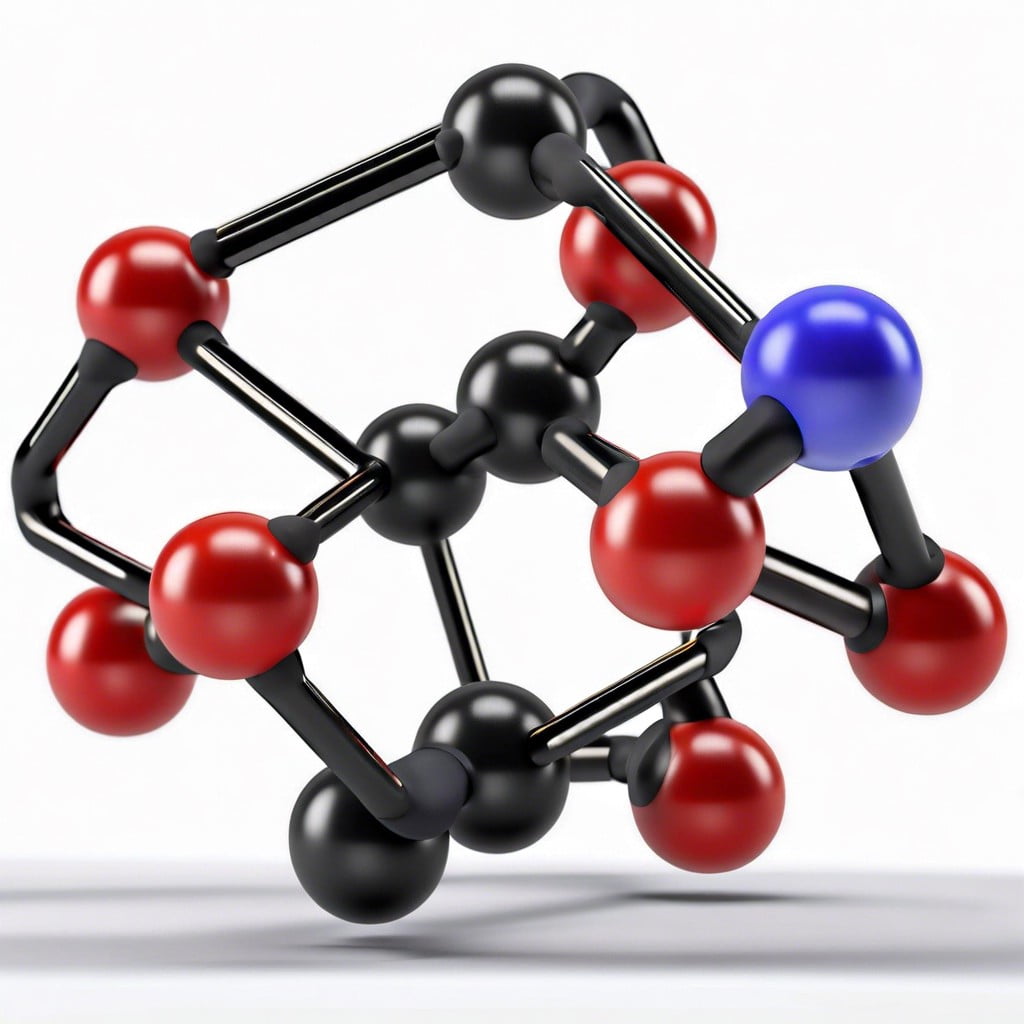
Understanding the intrinsic qualities of construction polymers is crucial as it informs their application in various building tasks.
Durability: These materials are engineered to resist wear, tear, and environmental stress, meaning structures remain intact for longer periods.
Flexibility: Their capacity to bend without breaking enables innovative architectural designs and the ability to withstand structural shifts.
Thermal Resistance: Polymers provide excellent insulation, reducing heating and cooling costs and enhancing energy efficiency.
Chemical Resistance: They are largely impervious to water, acids, and bases, safeguarding structures from corrosive substances.
Lightweight: Polymer materials are typically lighter than their metal or concrete counterparts, easing transport and installation.
Maintenance: With inherent stain and fade resistance, polymers often require minimal upkeep compared to traditional building materials.
These properties open up possibilities for customized solutions to address specific construction challenges, from reducing noise levels to enhancing thermal performance.
Types of Polymers Used in Building and Construction
Polymers serve as versatile materials in the construction industry, offering unique properties that enhance durability and efficiency. Here are several commonly used polymers:
–Polyvinyl Chloride (PVC): Renowned for its durability, this plastic is a go-to for pipes, window frames, and roofing.
–Polystyrene: Available as both a rigid form and foam, it’s widely used for insulation purposes.
–Polyethylene: Applied in vapor barriers and as panels for reducing moisture penetration.
–Polyurethane: Known for its excellent insulation capabilities, it’s often used in spray foams for thermal efficiency.
–Epoxy Resins: These provide strong adhesives as well as protective coatings for floors and structural components.
Each of these polymers is selected based on the specific requirements of a construction project, be it strength, insulation, or moisture resistance, ensuring optimal performance and longevity of the structure.
Polymer Injection Molding
Polymer Injection Molding is a versatile technique vital for producing a broad range of construction materials, from window frames to insulating joints.
The process begins with polymer granules or pellets heated into a liquid state.
This molten polymer is then injected under high pressure into a mold, taking the shape of the desired construction component.
Once cooled, the material solidifies, and the newly formed part is ejected for use or further processing.
Key points about this process include:
- Precision and Complexity: The method allows for intricate designs and precise dimensions, which is essential for components that must interlock or fit together seamlessly.
- Speed and Efficiency: Injection molding machines can produce high volumes of components with minimal waste, making it a highly efficient and cost-effective manufacturing process.
- Material Versatility: Different polymers can be used, including thermoplastics, thermosets, and elastomers, each providing specific characteristics like durability, flexibility, or fire resistance.
- Recycling and Reuse: Excess material and reject parts can often be recycled, reducing waste and supporting sustainable construction practices.
Understanding polymer injection molding is fundamental for professionals seeking innovative and effective solutions in the construction industry.
Specialty Tooling
When tackling construction projects that call for intricate designs or unique structural features, specialty tooling through polymers becomes invaluable. This process involves creating custom molds and tools that enable the precise shaping and forming of polymer materials.
- Precision: These tools are engineered with high precision to meet the exact specifications required for specific construction components. This ensures that each piece fits perfectly within the overall structure.
- Material Versatility: Specialty tooling can accommodate a wide range of polymer types—from pliable thermoplastics to sturdy thermosets—giving builders flexibility in material selection based on the desired properties of the final product.
- Cost Efficiency: By using tailor-made tools, waste is minimized, and production speed is enhanced, leading to cost savings. This is especially significant in large-scale construction projects where the volume of materials used is substantial.
- Durability: Tools are designed to withstand the rigors of repeated use, ensuring that they can produce consistent results over long periods, which is crucial for maintaining quality in construction processes.
- Innovation: This approach allows for the creation of components that may not be possible with standard off-the-shelf tools, facilitating innovation in building design and functionality.
Custom Solutions for Construction Challenges
Polymers offer innovative solutions tailored to unique construction problems, enabling the industry to tackle a range of environmental and mechanical challenges:
- Noise Reduction: Advanced polymer composites can significantly dampen sound, helping to create quieter living and working spaces.
- Vibration Control: Specialty polymers can absorb and dissipate vibrations, which is crucial in protecting structures from damage, especially in earthquake-prone areas.
- Thermal Insulation: Polymer materials, with their inherent insulating properties, contribute to energy efficiency by maintaining temperature and reducing heating and cooling costs.
Each of these applications employs the versatility of polymers to address specific construction needs, enhancing the durability, safety, and comfort of built environments.
Noise Reduction
Polymers have revolutionized the way we approach the challenge of noise pollution in buildings. Their unique composition can be engineered to absorb or dampen sound waves, resulting in a quieter and more comfortable environment.
Here are some key points explaining how this is achieved:
- Absorption Qualities: Certain polymers are designed with open cell structures that trap sound waves and convert them to heat, significantly reducing noise levels. This is particularly beneficial in spaces like recording studios or busy offices.
- Damping Characteristics: By dispersing vibrational energy through the material’s inner structure, polymers prevent sound from echoing. This makes them ideal for use in construction joints and partitions.
- Mass Law: This principle states that increasing a wall’s mass can enhance its soundproofing capability. Polymers can be added as layers to existing structures to improve their mass without requiring extensive renovations.
- Resilience and Flexibility: Thanks to their flexibility, polymers can seal gaps with precision, preventing sound from leaking through crevices and contributing to a building’s overall soundproofing.
- Customization: Polymer products can be tailored to address specific frequencies of noise, which means solutions can be personalized for environments such as airports or industrial plants, where certain types of noise prevail.
By integrating these polymer technologies, construction projects can effectively mitigate unwanted noise, enhancing the living or working conditions within any built space.
Vibration Control
Vibrations in buildings can lead to noise pollution, structural damage, and discomfort. Polymers provide an effective means for dampening these vibrations, thanks to their inherent material properties.
Here are key points explaining the role of polymers in vibration control:
- Energy Absorption: Polymers have a unique ability to absorb and dissipate energy from vibrations, making them ideal as base isolators or in building joints.
- Flexibility: The elastic nature of polymers allows them to flex, which helps to absorb vibrational energy and reduce the transmission of these forces through a structure.
- Customization: Polymer formulations can be tailored to address specific vibration frequencies encountered in construction, leading to highly effective bespoke solutions.
- Durability: Resisting environmental factors such as temperature changes and moisture, polymers maintain their vibration damping characteristics over time.
- Integration: Polymers can be easily incorporated into structural components or added to existing structures as viscoelastic dampers to reduce vibration without significant alterations.
By integrating polymers in construction design, builders achieve enhanced vibration control, leading to more robust and comfortable living environments.
Thermal Insulation
Polymers play a significant role in enhancing the energy efficiency of buildings through thermal insulation. These materials are engineered to decrease the rate of heat transfer between interior and exterior environments.
Here’s how they contribute:
- Reduced Conductivity: Polymers used for insulation have a low thermal conductivity, which means they hinder the flow of heat, keeping interiors warm in winter and cool in summer.
- Air Sealing: Insulative polymers can fill gaps and cracks, creating an airtight seal. This prevents warm or cool air from escaping, maintaining a steady temperature indoors.
- Moisture Resistance: Construction polymers are often resistant to water absorption, which eliminates the risk of insulation degradation due to moisture and prevents mold growth.
- Durability: Unlike traditional insulation materials that can settle over time, polymers maintain their structure, providing long-lasting insulation without needing frequent replacement.
- Versatility: Polymer insulations are adaptable and can be used in various forms, from rigid foam boards to spray foams, to suit different construction needs.
By incorporating these materials into construction projects, builders can increase comfort, lower energy consumption, and create more sustainable living and working environments.
Applications of POLYDAMP® in Construction
POLYDAMP® is a suite of acoustic and thermal insulation materials specifically engineered to meet the rigorous demands of construction environments. Here are some ways it enhances building projects:
- Acoustic Insulation: It effectively absorbs sound, significantly reducing noise levels inside buildings, which is crucial for comfort in residential and commercial spaces.
- Thermal Regulation: These materials provide excellent thermal insulation, maintaining a consistent temperature by reducing heat transfer through walls and ceilings.
- Moisture Resistance: With inherent resistance to water absorption, it helps in preventing mold growth and material degradation, thus contributing to the longevity of the structure.
- Vibration Damping: Its application on surfaces can diminish vibrations, which is particularly beneficial for industrial buildings housing heavy machinery.
- Ease of Installation: The materials come in various forms, including sheets and foams, that can be easily applied to a plethora of surfaces, accommodating different design specifications.
- Versatility: From the outer walls of skyscrapers to the interior panels of residential homes, it is versatile enough to offer solutions across a wide spectrum of construction needs.
POLYFORM® Molded Foam Uses
POLYFORM® molded foam offers versatile solutions in a variety of construction applications due to its customizable properties. This foam can be engineered to any required density and firmness, serving as an excellent option for:
- Impact absorption in playgrounds and safety equipment, where its cushioning properties help to mitigate potential injuries.
- Insulation panels for buildings, aiding in energy efficiency by maintaining temperature and reducing heating and cooling costs.
- Buoyancy devices in marine construction, where the material’s ability to resist water absorption is critical for docks and floating platforms.
- Concrete molding and architectural forms, where the foam acts as a void filler that can be easily removed or left in place.
- Soundproofing materials, efficiently reducing noise transmission through walls, floors, and ceilings in both residential and commercial buildings.
Through these applications, POLYFORM® molded foam demonstrates its adaptability and effectiveness in improving safety, comfort, and performance in the construction industry.
POLYTECH® Heat Shield in Construction
In the construction industry, managing heat flow is vital for energy efficiency and occupant comfort. POLYTECH® Heat Shields serve as an effective barrier to radiant heat, reflecting it away from a building’s interior and contributing to a stable thermal environment.
- Utilizes Reflective Technology: Metallic components within the shield reflect thermal energy, rather than absorbing and conducting it.
- Lightweight Solution: Despite its powerful performance in heat deflection, the shield remains light and easy to handle, simplifying the installation process.
- Versatility: Suitable for use in roofs, walls, and floors, these heat shields can be integrated into a variety of structures, from residential homes to commercial buildings.
- Improved Energy Efficiency: By reducing the need for air conditioning in the summer months and heating in winter, this technology can lead to significant savings on energy bills.
- Enhanced Comfort: A stable indoor temperature contributes to a more comfortable living or working environment, no matter the external weather conditions.
POLYTECH® Heat Shields are a prime example of how polymer technologies are transforming the efficiency and performance of modern construction materials.
The Solution Process for Construction Needs
When crafting solutions for construction challenges, the process involves a careful evaluation of the project requirements and the selection of appropriate polymers. Here are key steps:
1. Identify Needs: Ascertain specific structural, environmental, or design needs such as load-bearing capacity or weather resistance.
2. Material Selection: Choose the right type of polymer, be it polyethylene for durability or polystyrene for insulation, that aligns with the project’s demands.
3. Design Customization: Tailor the polymer design to fit unique construction elements, ensuring it integrates seamlessly with other materials.
4. Prototyping: Create prototypes to test the polymer’s performance in real-world conditions.
5. Performance Testing: Rigorously evaluate the polymer against standard construction criteria such as tensile strength, flexibility, and thermal conductivity.
6. Iterative Improvement: Refine the polymer based on test results and feedback, optimizing its properties for construction use.
7. Production Scaling: Once the polymer meets all specifications, scale up production while adhering to quality control measures.
Through this process, specialized polymers are developed to enhance building performance, demonstrating their critical role in meeting the innovative demands of modern construction.
Collaborative Approach in Polymer Solutions
Creating successful polymer solutions for construction requires a shared effort between manufacturers, designers, and builders. This collaborative approach ensures that the final product truly meets the end user’s needs. Here are a few key concepts that underpin this shared strategy:
- Open Communication: Clear dialogue across all project phases allows for real-time adjustments and innovation.
- Interdisciplinary Expertise: Leveraging the knowledge of chemists, engineers, and architects can lead to breakthroughs in material application and functionality.
- Customization: Working together allows for tailored polymer solutions that address specific environmental factors or design requirements unique to each project.
- Problem-Solving: By sharing perspectives, teams can more effectively troubleshoot and refine polymer applications, ensuring reliability in the final construction.
- Feedback Loops: Receiving and acting upon feedback from the construction site back to the lab ensures continuous improvement of materials and processes.
Through this partnership, polymer technologies are pushed beyond their conventional boundaries, offering revolutionary solutions in the world of construction.
Technical Datasheets for Construction Materials
Technical datasheets are essential tools for architects, engineers, and contractors. They provide detailed information on material properties, helping professionals make informed decisions about the suitability of polymers for specific construction projects.
Here are key elements typically found in datasheets:
- Material Composition: Breaks down the polymer’s chemical structure and additives.
- Physical Properties: Includes density, melting point, and moisture absorption rates, which affect durability and longevity.
- Mechanical Properties: Tensile strength, elongation, and modulus of elasticity indicate how the material will handle stress and strain.
- Thermal Properties: Important for understanding insulation performance and behavior under temperature variations.
- Fire Resistance: Ratings and compliance with industry standards, such as flame spread or smoke development index.
- Environmental Impact: Information on recyclability and compatibility with green building practices.
- Certifications: Lists approvals and standards met, reassuring that materials meet safety and performance regulations.
By examining these datasheets, construction professionals can compare materials’ characteristics, leading to well-suited polymer selection for their projects.
Dedicated Supplier Relationships
In the realm of construction, reliable supplier relationships are pivotal for consistent quality and timely delivery of polymer materials. These partnerships guarantee access to the latest polymer technologies and technical support throughout the project lifecycle.
- Just-In-Time Delivery: Streamlined logistics ensure that materials arrive when needed, reducing storage costs and minimizing waste.
- Customization and Scalability: Close collaboration with suppliers allows for custom-tailored polymer solutions that can scale up to meet project demands.
- Material Consistency: Ongoing communication ensures that the materials supplied maintain consistent properties, essential for structural integrity and performance.
- Innovation Sharing: Suppliers often provide insights into emerging polymer technologies, giving construction projects a competitive edge.
- Cost Management: Established supplier relationships can lead to negotiated pricing and cost savings over time due to the economies of scale and mutual trust.
By forging strong supplier partnerships, construction projects benefit from a dependable flow of high-quality materials, alongside expert advice and potential cost reductions.
Quality Assurance in Polymer Products
Ensuring polymers perform consistently in construction is crucial for safety and longevity. Quality assurance (QA) processes rigorously test these materials to meet standards and specifications.
1. Material Testing: Polymers undergo tensile, compression, and impact tests to assess strength, elasticity, and durability under various conditions.
2. Certification Compliance: Products must adhere to industry standards, such as ASTM or ISO, certifying they fulfill regulatory requirements.
3. Batch Consistency Checks: Each production batch is inspected to ensure uniformity in properties and performance across all polymer units.
4. Aging and Environmental Tests: Samples are exposed to extreme temperatures, moisture, and UV radiation to simulate long-term environmental effects.
5. Quality Control Documentation: Detailed records track each step of the QA process, allowing for traceability and accountability.
6. Customer Feedback Integration: Reviews from field applications inform ongoing improvements, ensuring materials evolve with the demands of construction projects.
By incorporating these practices, stakeholders can trust in the quality and reliability of polymer products used in building and construction.
Research & Development in Construction Polymers
Advancements in polymer technologies are crucial for meeting modern construction demands. Innovative research and development efforts focus on creating materials that provide enhanced durability, energy efficiency, and environmental sustainability. Here are some key points regarding these endeavors:
- Collaboration: Scientists and engineers often work with architects and builders to identify specific industry needs, tailoring polymer properties to suit various construction applications.
- Performance Testing: R&D involves rigorous testing for stress resistance, longevity under extreme conditions, and compatibility with other construction materials.
- Environmental Impact: Emphasis on developing eco-friendly polymers includes reducing the carbon footprint during manufacture and making materials recyclable or biodegradable.
- Smart Polymers: Research is delving into ‘smart’ polymer systems that can adapt to environmental changes, like temperature-responsive insulation.
- Compliance: New polymer formulations are tested to ensure they meet building codes, safety standards, and performance certifications.
Through these efforts, the goal of R&D in construction polymers is to pave the way for safer, more efficient, and sustainable building practices.
EGuide for Profitable Purchasing in Construction Materials
Navigating the procurement of construction materials effectively can impact a project’s profitability. An EGuide serves as a digital roadmap, offering valuable insights into purchasing decisions.
Here are key points the guide covers:
- Current Market Trends: Understanding the prevailing prices and demands can help forecast costs and secure materials at competitive rates.
- Performance Metrics: Identifying the performance characteristics of polymers ensures that the right material is selected for specific construction needs.
- Supplier Evaluation: The guide provides criteria for assessing suppliers, focusing on reliability, quality of materials, and delivery timeframes.
- Lifecycle Costs: It demonstrates how to evaluate not just the initial costs but also the durability and maintenance expenses over the material’s life.
- Regulatory Compliance: Staying informed about building codes and environmental regulations to ensure that materials meet legal requirements.
- Bulk Buying Advantages: The guide highlights how purchasing in larger quantities can reduce costs and secure a consistent supply chain.
Utilizing an EGuide helps streamline the decision-making process, leading to more strategic and lucrative procurement practices in construction projects.
Metal Injection Molding in Construction
Metal injection molding (MIM) combines the design flexibility of plastic injection molding with the strength and durability of metal. This advanced process has entered the construction scene to address the need for intricate, high-performance metal parts.
MIM works by mixing fine metal powders with a polymer binder to form a feedstock. This feedstock is then heated and injected into a mold, much like plastic processing. Once the part cools, the binder is removed through a debinding process, and the part is sintered in a furnace, causing the metal particles to fuse into a dense, robust component.
This approach offers several benefits for the construction industry:
- Customization: Complex shapes that were previously impossible or too expensive to achieve with traditional metalworking can now be created with ease.
- Efficiency: MIM allows for high volume production of components with minimal material waste.
- Strength: Components produced have similar mechanical properties to wrought materials, suitable for structural applications.
- Cost-Effectiveness: MIM is often more economical for small-sized, intricate parts than traditional machining, especially when production volumes are high.
The MIM process is particularly suited for creating small, intricate parts such as connectors, fasteners, and various hardware essential in modern construction. As buildings and structures become more complex and materials more specialized, MIM provides the flexibility and efficiency required to meet contemporary construction demands.
FAQ
What is polymer Technology?
Polymer technology is a specialized field of study that explores the development, properties, and applications of plastic materials, textile fibers, fabrics, and composite materials, with an emphasis on creating environmentally sustainable materials.
Who owns polymer technologies?
Polymer Technologies Inc. is owned by Mr. Robert Prybutok.
Where is polymer technologies located?
The headquarters of Polymer Technologies, where the majority of its manufacturing and testing facilities are, is located in the Pencader Corporate Center in Newark, Delaware.
What Technology uses polymers?
Technology uses polymers in fields such as construction, packaging, decoration, electrical engineering, communications, and the automotive and aviation industries.
How do polymers contribute to advancements in construction technology?
Polymers contribute to advancements in construction technology by providing materials that are lightweight yet highly durable, resistant to environmental degradation, and able to facilitate innovative designs due to their versatility.
What are the diverse applications of polymers in sustainable building design?
Polymers are widely utilized in sustainable building design for insulation, waterproofing, enhancing the strength and durability of structures, creating flexible flooring, and as a composite material for pipes, wiring and roofing.
What are the potential challenges and benefits associated with using polymer materials in construction?
Using polymer materials in construction presents significant benefits such as high durability, resistance to corrosion, design flexibility and cost effectiveness but have accompanying challenges like low heat resistance, sensitivity to UV radiation, and impact on the environment due to non-biodegradability.
Recap