Discover how SEBS polymer enhances flexibility and durability in construction materials, and where you might encounter it in everyday building applications.
Key takeaways:
- SEBS polymer combines plastic strength with rubber flexibility.
- SEBS is non-toxic and safe for healthcare and personal care products.
- SEBS has flexibility, thermal stability, weather resistance, and chemical resistance.
- SEBS is recyclable and can be processed using various methods.
- SBS is cheaper, while SEBS is more durable and weather-resistant.
Description of SEBS
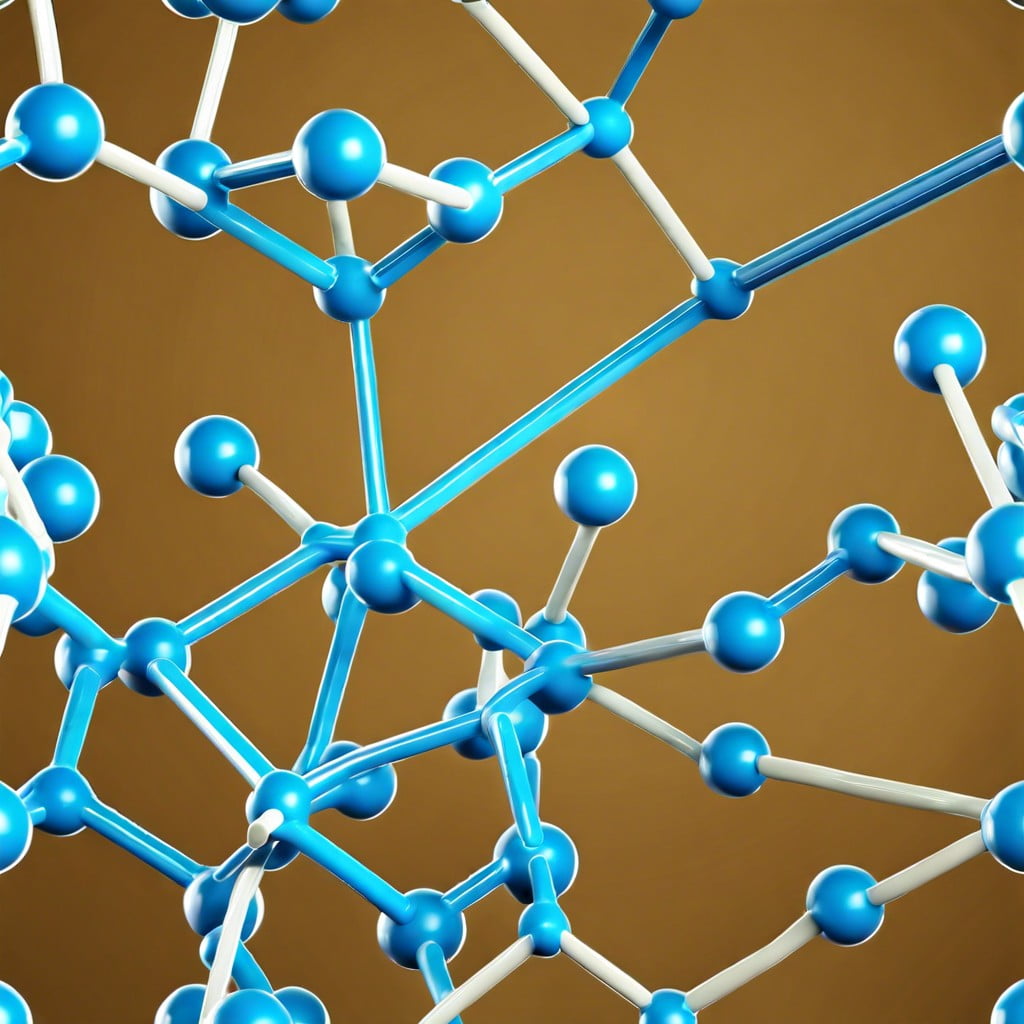
SEBS stands for Styrene Ethylene Butylene Styrene, a type of thermoplastic elastomer (TPE) known for its rubber-like properties. It is a block copolymer, which means it consists of segments of styrene and rubber arranged in a specific pattern within the polymer chain.
This material is unique because it combines the strength and processability of plastic with the flexibility and durability of rubber. The “E” in SEBS indicates that the butadiene component of its cousin, SBS, has been hydrogenated. This hydrogenation process enhances the polymer’s temperature and oxidative stability.
SEBS is also easy to color and can be processed in multiple ways, such as injection molding, extrusion, and thermoforming. Its versatility and resilience are major reasons why it’s favored in various industries.
Furthermore, SEBS is non-toxic and can be used in applications that involve skin contact, which expands its use to healthcare and personal care products. It does not contain phthalates, which are chemicals of concern in many plastic products.
Overall, SEBS provides an excellent balance of properties that benefit creators and manufacturers across a wide spectrum of products.
Properties of SEBS
SEBS, or Styrene-Ethylene/Butylene-Styrene, is a block copolymer valued for its impressive combination of strength, flexibility, and durability. Here are some key attributes:
**Flexibility and Elasticity**: Much like rubber, SEBS can be stretched significantly and will return to its original shape when released, making it ideal for products that need to maintain form after bending or distorting.
**Thermal Stability**: It withstands a wide temperature range, remaining flexible at low temperatures and stable at high temperatures. This makes it useful in environments with temperature fluctuations.
**Weather Resistance**: Exposure to UV radiation, rain, and other environmental elements does not easily degrade SEBS. Its long-term stability outdoors is a crucial factor in its application in the construction sector.
**Chemical Resistance**: SEBS is resistant to acids, bases, and other aggressive substances. As a result, products made from SEBS have a longer lifespan even when they come into contact with chemicals.
**Colorability**: SEBS easily accepts dyes and pigments, allowing for a vast range of color options without sacrificing material integrity.
**Processing Versatility**: It can be processed using conventional plastic technologies, such as injection molding and extrusion, simplifying the manufacturing process of complex parts.
**Recyclability**: Unlike many rubbers, SEBS can be recycled, which is becoming increasingly important in sustainable construction practices.
Together, these properties contribute to SEBS’s popularity across various applications in construction, where performance and longevity are paramount.
Differences Between TPE Elastomers SBS and SEBS
SBS (Styrene-Butadiene-Styrene) and SEBS (Styrene-Ethylene/Butylene-Styrene) are both Thermoplastic Elastomers (TPEs), but they have notable distinctions due to their chemical structures.
Chemically, SBS is a triblock copolymer made by polymerizing styrene and butadiene. It mimics the properties of rubber; it’s flexible and can be stretched, but it isn’t resistant to weathering or UV light, and it can struggle with high temperatures.
SEBS, on the other hand, is an SBS molecule that has been hydrogenated. The hydrogens add to the double bonds of the butadiene segments to form ethylene/butylene segments. This process significantly improves its thermal stability, UV and ozone resistance, and makes it more suitable for outdoor applications.
The hydrogenation in SEBS not only enhances its physical properties but also leads to a lower glass transition temperature. Consequently, SEBS retains its elasticity and flexibility over a broader temperature range compared to SBS.
In terms of applications, SBS is often the choice for lower-cost products where durability and weather resistance aren’t critical. SEBS, with its superior durability, can be found in products that require prolonged exposure to the elements, such as sealants, gaskets, and medical devices.
In processing, both materials offer the advantage of being shaped by conventional thermoplastic processing techniques like injection molding and extrusion, yet SEBS often presents a better balance of ease of processability and final product performance.
Application Range for SBS and SEBS Grades
SBS (styrene-butadiene-styrene) and SEBS (styrene-ethylene/butylene-styrene) are versatile polymers used across various industries due to their unique properties. The range of applications for these materials can largely be attributed to their blend of rubber-like flexibility and thermoplastic processing abilities.
In the automotive sector, SBS is often found in the production of car tires, providing enhanced grip and wear resistance. SEBS, on the other hand, with its superior weather and UV resistance, proves invaluable in creating exterior automotive components that require long-lasting durability.
The footwear industry also benefits from these thermoplastic elastomers (TPEs). SBS is incorporated into shoe soles for cost-effective production without compromising on comfort or design. SEBS, offering a higher end finish, is used for the soles of more premium products, where its resistance to degradation improves longevity and performance.
In consumer goods, SEBS’s hypoallergenic nature makes it an excellent choice for medical supplies, like tubing and grips, and toys that require a soft touch yet stringent safety standards. Its ability to be sterilized without losing properties ensures safety and durability in healthcare products.
For roofing and waterproofing solutions, SBS-modified bitumen is favored for its flexibility at low temperatures and excellent elongation properties, which allow it to withstand structural movements. SEBS’s advancement over SBS comes in the form of improved thermal stability, making it suitable for applications requiring consistent performance in fluctuating temperatures.
Packaging materials utilize both SBS and SEBS to produce items that are tough yet flexible. SEBS in particular offers clarity and can be used in the manufacture of soft touch grips, providing a comfortable and secure holding surface for various packaged goods.
These polymers find roles in adhesives and sealants as well. SBS is commonly a base for pressure-sensitive adhesives, like those in tapes and labels, while SEBS provides a more weather-resistant option that maintains adhesive properties in challenging environments.
The examples provided underscore the adaptability of SBS and SEBS. The choice between them depends on the specific requirements of the application, including costs, performance expectations, and environmental exposure.
Recap