This article will explain what PP polymer is and its common uses in various industries.
Key takeaways:
- PP polymer is a stiff and resistant plastic with a high melting point.
- It is used in packaging, automotive, textile, medical, and consumer goods.
- PP is easily recycled and can be used to create new products.
- Proper safeguards are needed during production and disposal to minimize health risks.
- PP waste in the environment can have negative ecological effects.
Chemical and Physical Properties
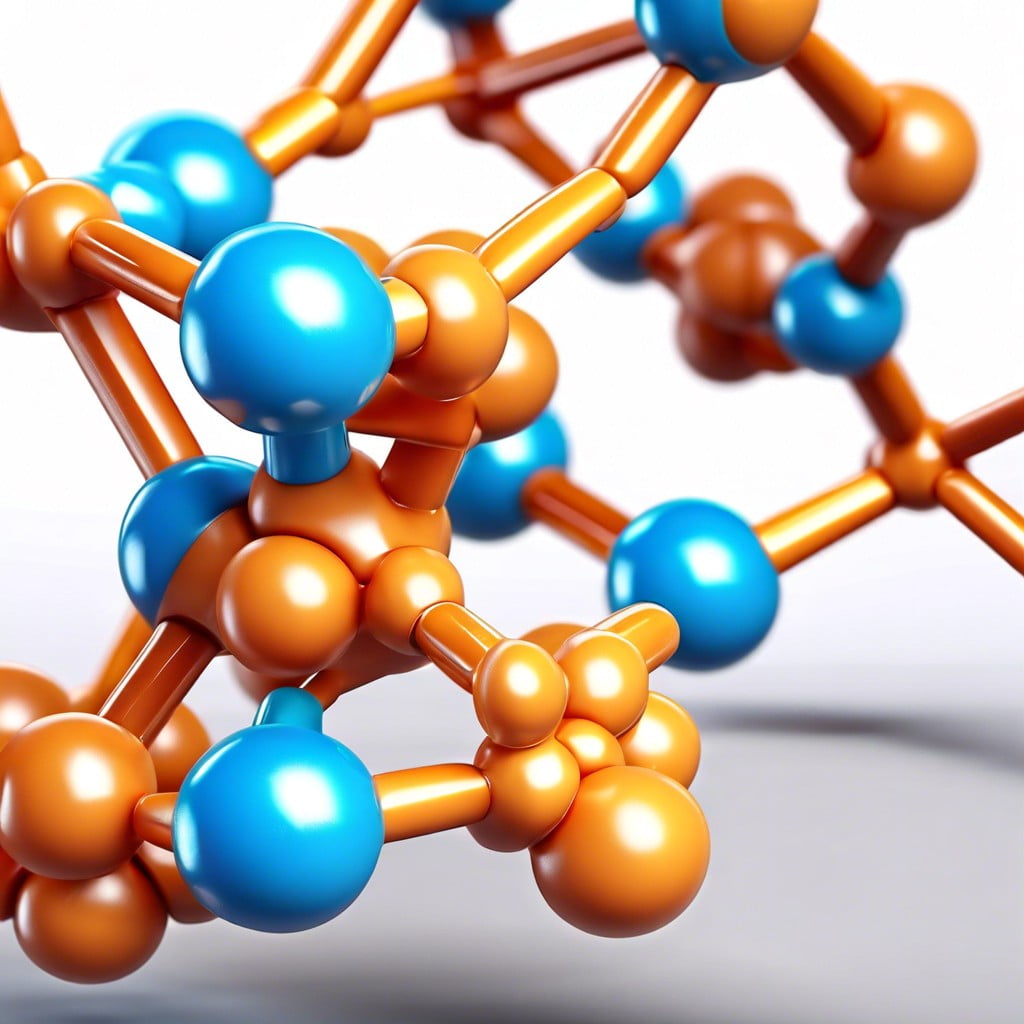
Polypropylene, often abbreviated as PP, is a type of plastic known for its stiffness and resistance to various chemical solvents, bases, and acids. It’s a thermoplastic polymer, meaning it becomes pliable or moldable above a specific temperature and returns to a solid state upon cooling.
One standout characteristic of PP is its high melting point, around 130°C to 171°C, which allows it to be used in applications that involve heat, such as dishwasher safe containers and car parts that must withstand high temperatures.
Additionally, polypropylene is lightweight yet rugged, making it an ideal choice for products that benefit from being easy to transport yet durable, like reusable shopping bags and storage containers. Its ability to resist moisture also makes it a popular choice for outdoor applications and for products exposed to water.
Synthesis
Polypropylene, commonly known as PP, is primarily produced through a process called polymerization of propylene gas. This involves using a catalyst system, typically based on titanium chloride and various co-catalysts. The process can occur under different conditions, yielding distinct types of PP with varying properties.
Two main methodologies are employed:
- Slurry Process: In this method, propylene is polymerized in a solvent, which keeps the polymer particles suspended. This is suitable for creating a type of PP known as homopolymer.
- Gas Phase Process: This involves polymerizing propylene in a gaseous state within a reactor vessel. It allows for the production of both homopolymers and copolymers, providing flexibility in the final product’s applications.
Each method has its optimal settings and catalysts which influence the molecular structure and the material properties of the resulting PP, such as its melting point, stiffness, and impact resistance. These choices are crucial as they dictate the polymer’s suitability for various applications, stretching from automotive parts to textile and packaging.
Applications
Polypropylene (PP) polymer is a versatile material used in various industries due to its resistance to heat, chemicals, and fatigue. Here are some key applications:
– **Packaging Solutions**: PP is a favorite for containers and wrappers partly because it doesn’t react with water, acids, or bases, ensuring products stay safe and uncontaminated.
– **Automotive Components**: Known for its toughness and low cost, PP is used to make automotive parts such as bumpers, dashboards, and interior panels, which benefit from its light weight and durability.
– **Textile Manufacturing**: PP fibers are used in making carpets, rugs, and ropes with its resistance to staining and bleaching making it ideal for both indoor and outdoor use.
– **Medical Sector**: Due to its non-reactive nature, PP is used in making medical components including syringes and vials that require sterility and chemical resistance.
– **Consumer Goods**: Everyday items like plastic chairs, toys, and luggage often use PP to leverage its moldability and robust nature, allowing for products that withstand daily wear and tear.
By integrating into various products, polypropylene enhances functionality without high costs, showcasing its adaptability across different sectors.
Recycling
Polypropylene, or PP, is easily one of the most recycled polymers, and for good reason. Its resilience to different chemical solvents, acids, and bases allows it to travel through the recycling process without degrading significantly. The recycling process consists of several steps: collection, sorting, cleaning, melting, and reshaping. Here, comprehension of each step can shed light on its eco-friendliness and sustainability.
First off, after collection, sorting is critical. PP items must be separated based on their color and condition because contaminated or mixed materials can complicate the recycling process.
Following sorting, the cleaning process removes any impurities. This step is vital; clean materials ensure the recycled PP has the widest possible use in manufacturing new products.
Then, the clean PP is melted at a controlled temperature, which transforms it into pellets. These pellets are the raw materials for producing new PP goods—from automotive parts to reusable shopping bags.
Each step is essential to maintaining the cycle of PP recycling, allowing us to reuse this versatile material in various applications while contributing to environmental conservation.
Health Concerns
Polypropylene, or PP, is widely regarded as a safe material for various applications, including food containers and medical equipment. However, certain aspects related to its production and disposal deserve attention.
During production, workers may face exposure to potentially harmful chemicals. Proper safeguards and workplace safety measures are crucial to minimize health risks.
While PP itself is largely inert and stable, concerns arise during its combustion. Burning PP can release toxic substances such as acrolein and formaldehyde. Hence, proper disposal and recycling are essential to prevent harmful environmental and health effects.
Finally, like all plastics, the presence of PP in the environment as waste can contribute to broader ecological issues. Wildlife can mistakenly ingest small pieces, causing harm or death to the creatures.
By understanding and addressing these concerns, we can better manage PP’s use and maximize its benefits while minimizing its risks.
Recap