Dive into the captivating world of polymer synthesis, because it literally shapes the environments we live, work and play in.
Polymers are ubiquitous in modern construction, offering a vast array of applications owing to their diverse properties. Understanding polymer synthesis is paramount for innovating materials that shape our living spaces.
This article delves into the world of polymerization, explicating the intricacies of step-growth and chain-growth methods—two distinct paths leading to the formation of these versatile materials.
We’ll uncover how catalysts are pivotal in steering these processes and highlight groundbreaking developments in sustainable and self-repairing polymers.
Whether you’re a professional in the construction industry or a curious learner, this overview provides valuable insights into the evolving landscape of polymer synthesis.
Key takeaways:
- Step-Growth and Chain-Growth are the two main types of polymerization.
- Step-Growth Polymerization involves gradual bonding of monomers.
- Chain-Growth Polymerization involves rapid growth of a polymer chain.
- Catalysts play a crucial role in polymer synthesis.
- Recent advancements include biodegradable polymers and self-healing polymers.
Types of Polymerization
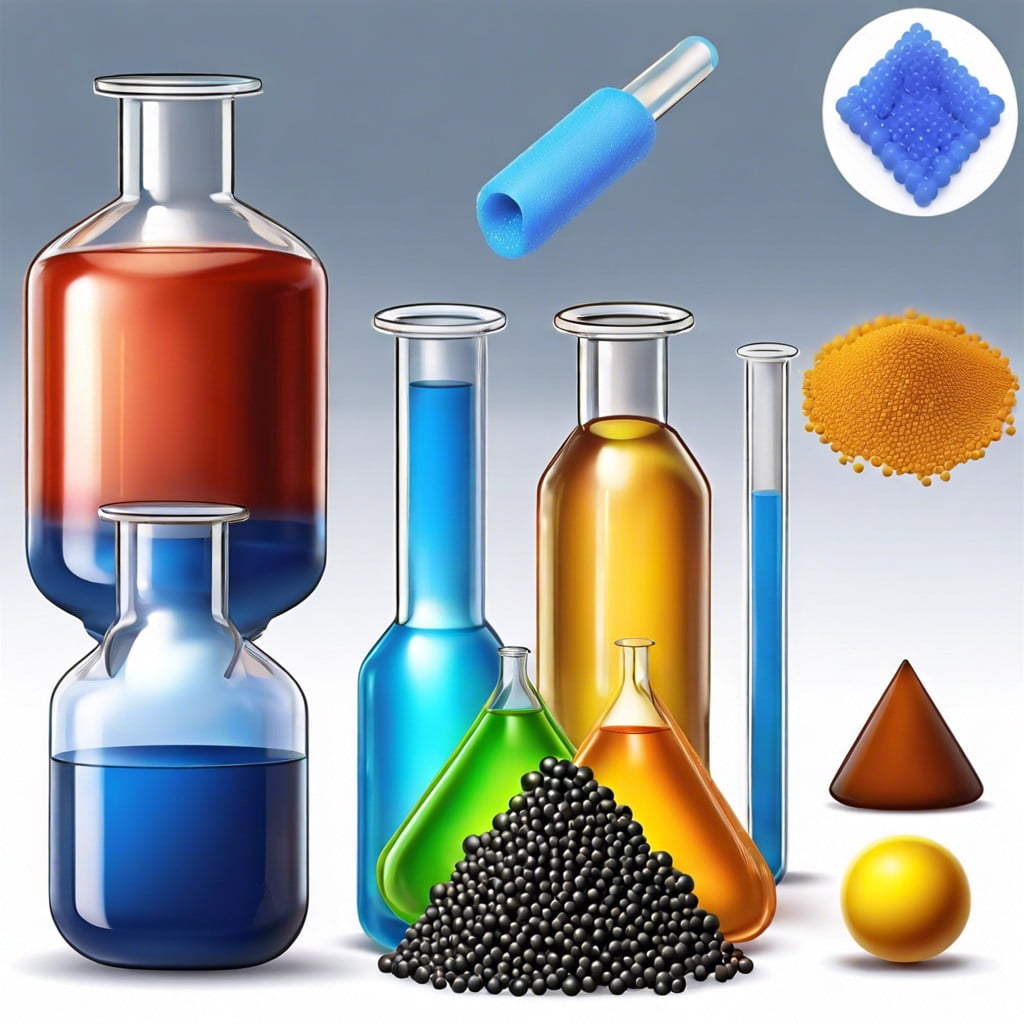
Polymerization is the chemical reaction that creates polymers from smaller units called monomers. It comes in two main varieties: step-growth and chain-growth.
Step-Growth Polymerization: This process involves all monomers acting as reactive species that can link together in a stepwise fashion. Bonds form between functional groups on different monomers, leading to a gradual increase in polymer size—think of it as building a wall brick by brick.
Chain-Growth Polymerization: Unlike step-growth, chain-growth polymerization starts with the activation of a single monomer molecule, which then adds to other monomers one at a time, creating a rapidly growing chain. Here, the polymer grows much like a train adding carriages successively.
Understanding these core processes provides the foundation for exploring more specialized types of polymerization, each with its unique attributes for creating diverse and tailored polymer materials.
Step-Growth Polymerization
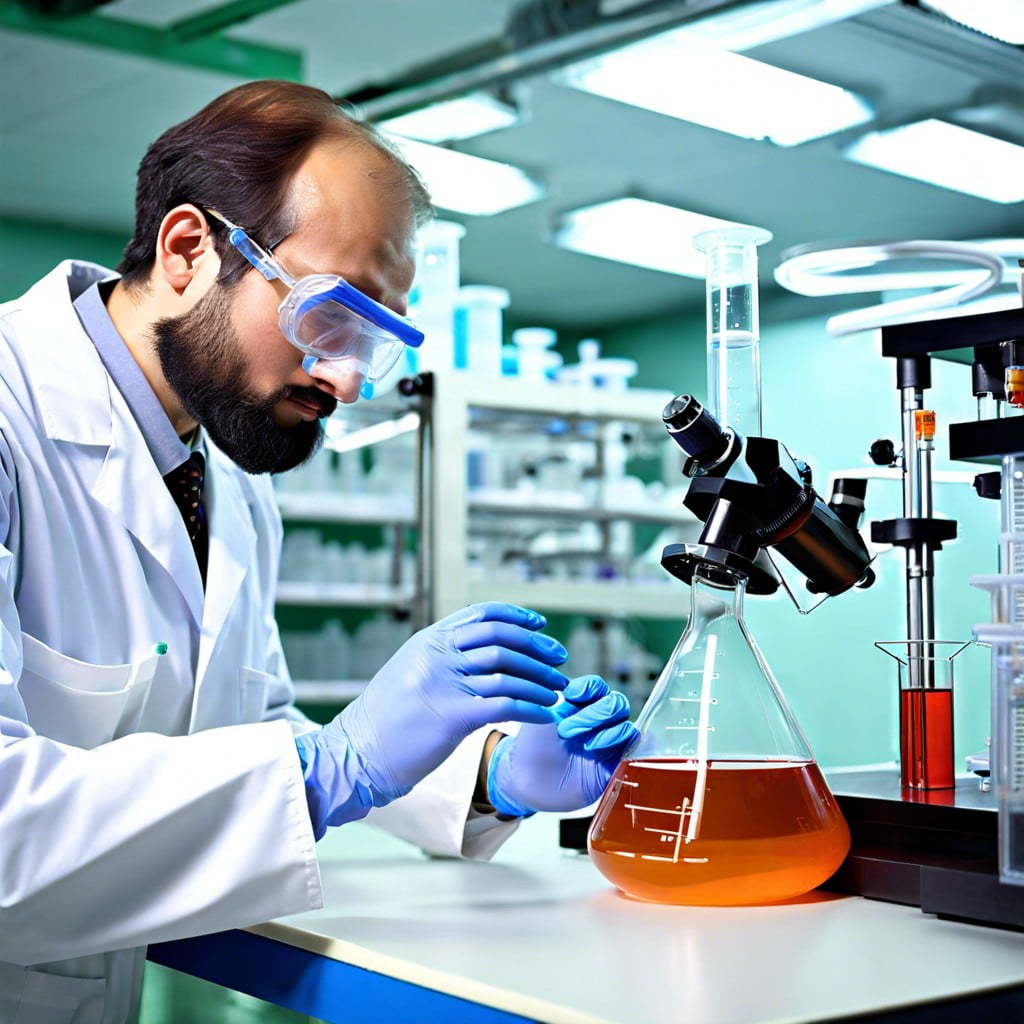
In step-growth polymerization, also known as condensation polymerization, small molecules, known as monomers, react to form larger structures in a stepwise fashion.
Here are key points to understand this process:
- Monomers with two or more reactive groups are necessary for step-growth polymerization to occur.
- As monomers join, they create dimers, which then combine to form tetramers, and so on, in a sequence of steps that result in long-chain polymers.
- Unlike chain-growth polymerization, the rate of reaction does not depend on the presence of an initiator; instead, it proceeds as long as reactive groups are available.
- The process typically involves the elimination of small molecules like water or methanol during the formation of the polymer, hence the term “condensation.”
- The polymer’s molecular weight grows gradually over the course of the reaction, and high molecular weights are achieved late in the reaction.
- Common examples include the synthesis of polyesters, polyurethanes, and polycarbonates.
Step-growth polymerization enables precise control over the polymer architecture, leading to materials with specific, desirable properties.
Chain-Growth Polymerization
In chain-growth polymerization, the polymer chain develops rapidly by successive additions of monomers to an active site on the growing chain. Here are some key points to understand this process:
Initiation: This is where the process starts. A chemical compound known as an initiator activates a monomer, creating an active site for the reaction to proceed.
Propagation: Once initiated, the monomer adds to the active site, and as more monomers keep joining, a long polymer chain forms. This step continues, adding monomer units to the growing chain.
Termination: The polymerization concludes when the active site is neutralized. This can happen in several ways, such as when two growing chains combine, the chain transfers its active site to another molecule, or it is terminated by an inhibitor.
One characteristic feature of chain-growth polymerization is that all the monomer units become part of the polymer chain at vastly different times during the reaction. This often results in high molecular weight polymers being formed rapidly at the beginning of the reaction.
Understanding the balance between these stages helps chemists control the size and structure of the polymer chains, leading to materials with tailored properties for specific uses in construction and beyond.
Radical Chain-Growth Polymerization
In radical chain-growth polymerization, the process begins with the generation of a radical, which is typically achieved through the use of an initiator. This initiator can be a compound that decomposes to produce free radicals when exposed to heat or light. Once the radical is formed, it attacks a monomer, bonding to it and creating a new radical at the end of the now extended molecule. This new radical can then react with another monomer, allowing the chain to grow in a repeating pattern.
Key points to remember:
- Initiators are critical to start the process; common initiators include benzoyl peroxide and azobisisobutyronitrile (AIBN).
- The reaction is highly sensitive to temperature and external conditions, making it relatively easy to control.
- This type of polymerization typically results in a wide distribution of molecular weights, known as polydispersity.
- The process is susceptible to various terminating events like radical recombination or disproportionation, which can affect the final polymer structure and properties.
- It’s commonly used to make polymers like polystyrene, polyacrylates, and polyvinyl chloride (PVC).
Cationic Chain-Growth Polymerization
Cationic chain-growth polymerization is a type of reaction where a positively charged species, known as a cation, acts as the driving force for polymer formation. This process typically begins with an initiator molecule that donates a positive charge to a monomer unit, creating a reactive site for further growth.
Here are some key points to understand about this polymerization method:
- Monomer Reactivity: It involves monomers that are prone to donating or sharing electrons, such as isobutylene and styrene.
- Initiators: Common initiators include strong acids like hydrofluoric acid or Lewis acids like aluminum trichloride, which are capable of forming carbocations.
- Propagation: Once the initial carbocation is formed, it readily reacts with additional monomer units, propagating the chain reaction to build up the polymer backbone.
- Environment: The reaction is sensitive to impurities, especially water, which can quench the carbocation. Hence, it requires an extremely dry and controlled environment.
- Polymer Characteristics: The resulting polymers often have a regular structure and can exhibit a range of properties from elastomers to thermoplastics, depending on the monomers used.
Understanding these fundamentals provides clearer insight into how certain plastics and rubbers are synthesized, paving the way for numerous applications from insulation to adhesives.
Anionic Chain-Growth Polymerization
Anionic chain-growth polymerization involves the addition of monomer units to a growing polymer chain with the help of a negatively charged species, an anion. This anion acts as the initiator, allowing the process to begin.
Here are some key points to understand about this mechanism:
- Highly Reactive Monomers: Typically, this method is best suited for monomers that have an electron-withdrawing group, such as styrene or acrylates, because they are more likely to react with the negatively charged initiator.
- Living Polymers: One distinctive feature of anionic polymerization is its ability to create living polymers. This means the polymer can keep growing as long as there are monomers available, without terminating the chain. The result is a polymer with a very narrow molecular weight distribution.
- Temperature Sensitivity: The reaction is sensitive to temperature, as it affects the reactivity of the anion. Lower temperatures usually favor anionic polymerizations by reducing side reactions.
- Solvent Choice: Solvents can heavily influence the polymerization. Polar aprotic solvents, such as tetrahydrofuran (THF), are often used because they do not react with the anion but can successfully dissolve both the initiator and the monomer.
- Additives: The absence of impurities is crucial. Even minute amounts of water or other protons can quench the anion, terminating the polymer chain growth.
- Control Over Polymer Structure: The anionic mechanism allows control over the polymer structure, enabling the creation of block copolymers, where different types of polymer segments are linked together.
By leveraging the unique characteristics of this polymerization method, scientists can synthesize polymers with specific properties tailored for various applications.
Ziegler-Natta Catalytic Polymerization
Ziegler-Natta catalytic polymerization is a type of chain-growth polymerization that uses specific catalysts to produce polymers with a high degree of tacticity. This process is particularly important for creating polymers like polyethylene and polypropylene, which are widely used in various applications.
- Catalysts Used: Typically composed of transition metals such as titanium compounds paired with aluminum-based co-catalysts.
- Tacticity Control: Allows for precise control over the stereochemistry of the polymer chains, influencing the material’s properties.
- Polymer Properties: Enables the production of polymers with desired characteristics, such as strength, flexibility, and melting point.
- Economic Efficiency: Offers a cost-effective approach to polymer synthesis, making it a popular choice in the industry.
- Broad Applicability: Well-suited for creating a variety of polyolefins used in everyday products from plastic containers to automotive parts.
Ring Opening Polymerization
Ring opening polymerization (ROP) is unique because it starts with monomers that have a cyclic structure. When these rings break, a reactive center is formed which initiates the polymer growth.
Here’s how the process unfolds:
- Initiation: An initiator breaks the monomer’s bond, creating an active site for the polymer chain to begin forming.
- Propagation: The active site on the new polymer chain attacks another monomer, repeating the ring-breaking process, and the chain grows.
- Termination: The reaction can be halted by various methods, depending on the desired polymer length and properties.
Several factors influence ROP, including temperature, the presence of a catalyst, and the type of monomer used. The versatility of this method lies in its ability to create polymers with unique properties, which are not achievable by other polymerization techniques. Examples include polylactide (PLA) and polyethylene oxide (PEO), which have applications in biodegradable plastics and pharmaceuticals.
Addition Copolymerization
In this process, two or more different types of monomers combine, contributing their distinct properties to create versatile materials. Picture building blocks of varying colors and shapes coming together to construct a unique structure.
- Monomers with double or triple bonds are the key players, opening up to link with other monomers.
- Each addition preserves the unsaturation of the reactive site, allowing the chain to grow.
- The sequence of monomers can be random, alternating, or arranged in blocks, affecting material properties.
- Temperature, pressure, and catalysts are critical factors that control the reaction rate and polymer structure.
- Policarbonate and polyvinyl chloride are everyday materials derived from this technique, showcasing its prevalence in producing diverse and functional polymers.
Chain Topology in Polymer Synthesis
Chain topology refers to the arrangement and sequence of monomer units within a polymer. This structure influences a polymer’s physical properties and how it performs in different applications. Imagine linking hands with a group of friends—how you link up can lead to different shapes and patterns; polymers work similarly.
Linear Polymers: These are like a single string of pearls, where each pearl represents a monomer unit. They’re simple, long chains that can slide past each other, making materials like plastic bags flexible.
Branched Polymers: Picture a tree with branches extending out from a trunk. Branched polymers have side chains that jut out from the main backbone, impacting how tightly they can pack together, and thus, affecting the density and melting point of the material.
Crosslinked Polymers: Think of a fishnet, where the knots are monomers connected in a network. Crosslinks tie different polymer chains together, leading to materials that are stronger and less soluble, like the rubber used in car tires.
Star Polymers: Just as stars radiate arms out from their center, star polymers have multiple chains growing out from a central core. This unique structure can lead to enhancements in properties like viscosity and drug delivery capabilities.
Understanding chain topology allows scientists to tailor polymers for specific building applications, such as making them more durable, flexible, or heat-resistant. It’s a cornerstone of material science, enabling the creation of innovative materials for the construction industry.
Factors Influencing Polymer Synthesis
Several key elements shape the course and quality of polymer synthesis processes, performing integral roles in determining the properties of the resulting materials.
Monomer Purity: Traces of impurities can drastically affect polymerization, leading to unintended reactions or defects.
Temperature and Pressure: Precise control of these conditions ensures the correct reaction pathways are followed, affecting polymerization rates and the polymer’s molecular weight.
Catalysts and Initiators: These chemicals are crucial for kickstarting and steering polymer reactions, influencing chain length and architecture.
Solvent Choice: The solvent can impact the polymerization process and end properties of a polymer by affecting the reaction environment.
Reaction Time: Longer reaction times can lead to higher molecular weights and different polymer structures, while shorter times may yield lower molecular weights.
Each factor interplays with the others, making polymer synthesis a complex yet finely tunable process. By understanding and manipulating these factors, chemists tailor polymers for a vast array of applications.
Applications of Synthetic Polymers
Synthetic polymers are versatile materials used in a myriad of construction applications, each exploiting their unique properties. For instance:
- Insulation: Foam polystyrene and polyurethane are used for thermal insulation in walls and roofs, helping maintain temperature and reduce energy consumption.
- Piping: PVC and polyethylene pipes, valued for their light weight and corrosion resistance, serve for water supply and sewage systems.
- Paints and Sealants: Polymers like acrylics enhance paint durability and weather resistance, while silicone-based sealants provide flexible and watertight joints.
- Flooring: Epoxy and polyurethane coatings create hard-wearing surfaces suitable for industrial environments.
- Concrete Reinforcement: Polymer fibers added to concrete can increase its tensile strength and durability, often replacing traditional steel rebar in some applications.
- Adhesives: Polymer-based adhesives offer strong, long-lasting bonds for various construction materials, from wood to metal.
This broad application spectrum underscores synthetic polymers’ role in building lighter, stronger, and more energy-efficient structures.
Innovations in Polymer Technology
Recent advancements have been pivotal in refining polymer properties and expanding their applications. One of the significant breakthroughs is in the field of biodegradable polymers, which are designed to break down more quickly, reducing their environmental impact. Examples include polylactic acid (PLA) and polyhydroxyalkanoates (PHA), both derived from renewable resources.
Self-healing polymers present another forefront of innovation. These materials can repair themselves when damaged, extending their lifespan. This is usually achieved through a triggered reaction within the polymer that seals cracks or breaks upon the application of certain stimuli, such as heat or light.
Smart polymers, which respond to external stimuli like temperature, pH, or light, have introduced new functionalities. For instance, temperature-sensitive polymers can undergo a drastic change in their physical properties with slight variations in temperature, making them useful for drug delivery systems and switchable adhesives.
Conducting polymers have also garnered attention with their capacity to conduct electricity, which is a departure from the traditional insulating nature of polymers. Polyaniline and polythiophene have been used in electronic devices, solar cells, and even antistatic materials.
Finally, nanocomposite technology involves reinforcing polymers with nanoparticles—such as clay, carbon nanotubes, or graphene—to dramatically improve mechanical, thermal, and barrier properties. This innovation is tailoring polymers for high-performance applications, from automotive parts to advanced packaging.
The Role of Catalysts in Polymer Synthesis
Catalysts are pivotal in polymer synthesis, as they speed up chemical reactions without being consumed in the process. They enable polymerization at lower temperatures and pressures, drastically improving efficiency and cost-effectiveness.
- Controlled Reactions: Catalysts help maintain consistent reaction conditions, yielding polymers with predictable properties like chain length and molecular weight.
- Selectivity: Specific catalysts can dictate the type of polymerization, such as Ziegler-Natta catalysts for polyethylene and polypropylene, ensuring precise control over the structure of the polymer chain.
- Reduced Imperfections: The presence of a catalyst can minimize side reactions, which in turn reduces defects in the polymer chain enhancing the material’s mechanical and chemical properties.
- Environmental Impact: They play a crucial role in green chemistry by reducing the need for harsh chemicals and minimizing waste during polymer production.
By manipulating catalysts, chemists can tailor the properties of polymers for diverse applications ranging from lightweight automotive parts to biodegradable plastics.
FAQ
What is the process used to synthesize polymers?
The synthesis of polymers typically involves a process known as ring-opening polymerization, where a ring-shaped molecule reacts with a monomer to form a linear polymer chain.
What are examples of synthesized polymers?
Synthetic polymers include materials such as nylon, polyethylene, polyester, Teflon, and epoxy.
What involves polymer synthesis?
Polymer synthesis involves the production of polymers through a polymerization reaction, which proceeds by adding monomers (single units) and subsequently removing water molecules.
Is polymer synthesis hard?
Polymer synthesis can be complex due to the need to manipulate their properties, such as their hardness or flexibility, stability, or degradability, depending on their intended application.
How do environmental factors affect polymer synthesis?
Environmental factors like temperature, humidity, and light exposure can significantly influence polymer synthesis, affecting factors like reaction speed, polymer size, and structure.
What are the key considerations in scaling up the polymer synthesis process for industrial use?
The key considerations in scaling up the polymer synthesis process for industrial use include raw materials availability, manufacturing cost, reaction control (temperature, pressure, and time), safety and environmental impacts, equipment scalability, quality control, and post-production processing.
What advancements have been made recently in the field of polymer synthesis?
Recent advancements in polymer synthesis include developing evening smarter self-healing polymers, rapid production techniques for high-performance plastics, and the creation of sustainable polymers from renewable sources.
Recap