Because their flexibility and strength are changing the face of modern construction, the importance of various polymer shapes deserves your attention.
Polymers, the versatile building blocks of modern construction, offer tailored solutions to enhance building performance and efficiency. From the towering steel skeleton of skyscrapers to the intricate wiring in smart homes, polymer shapes are meticulously designed to meet specific construction needs.
Whether it’s the linear strands woven into resilient floorings or the complex network polymers holding together durable insulation materials, each shape is engineered to distribute stress, resist wear, and provide long-lasting support.
In this article, we delve into the world of polymer shapes, from the sinuous piping of thermoplastics to the robust resins of thermosets, and uncover how these shapes optimize construction projects to meet the demands of the 21st century.
Join us to explore the science behind polymer shapes and how they revolutionize the way we build.
Key takeaways:
- Polymer shapes enhance material performance in construction.
- Polymer shapes include linear, branched, cross-linked, and network polymers.
- Benefits of specific polymer shapes include stress distribution and material efficiency.
- Common thermoplastic polymer shapes in construction: pipes, insulation, profiles, flooring, roofing, electrical components.
- Common thermoset polymer shapes in construction: epoxy resins, polyester resins, phenolic resins, urea-formaldehyde.
Importance of Polymer Shapes in Construction
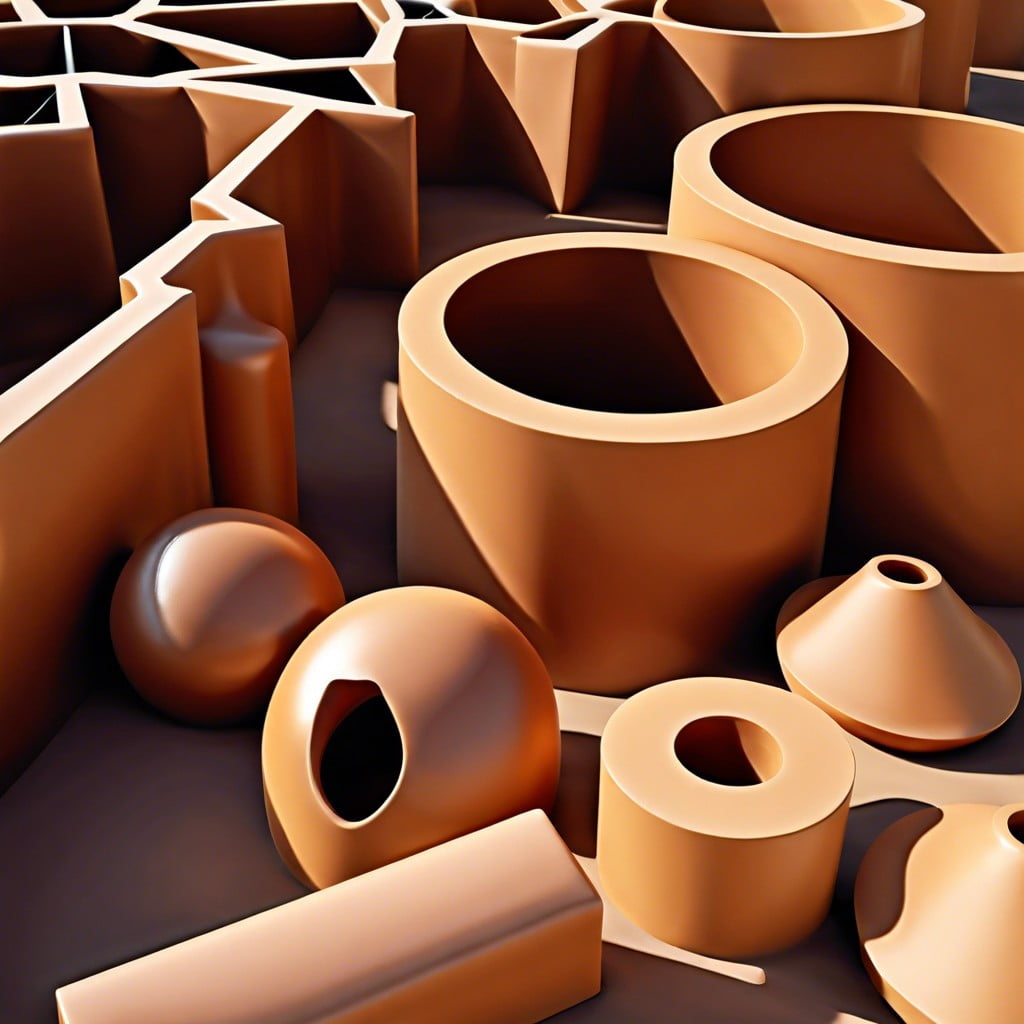
Polymers, with their versatile shapes, play a pivotal role in the structural integrity and functionality of modern construction. Their physical form directly influences a material’s mechanical properties, such as strength and flexibility, which are crucial for various applications within the building industry.
The shape determines how a polymer interacts with other materials. For instance, polymer fibers can reinforce concrete, while films can act as vapor barriers. Specially designed shapes like polymer geogrids provide soil stabilization, and their open mesh design enhances the distribution of loads, reducing stress on underlying materials.
Additionally, the shape of polymers dictates their processing and installation techniques. Shapes that are complex, such as custom joint fillers or sealants, require precision in manufacturing but can offer improved performance when fitting into irregular spaces. On the other hand, simpler shapes like sheets and panels can be rapidly manufactured and easily installed, contributing to cost-efficiency and speed in construction projects.
In essence, optimizing the shape of polymers for construction applications allows us to tailor their properties to meet specific requirements, ensuring durability, safety, and efficiency in the built environment.
Polymer Classification By Shapes
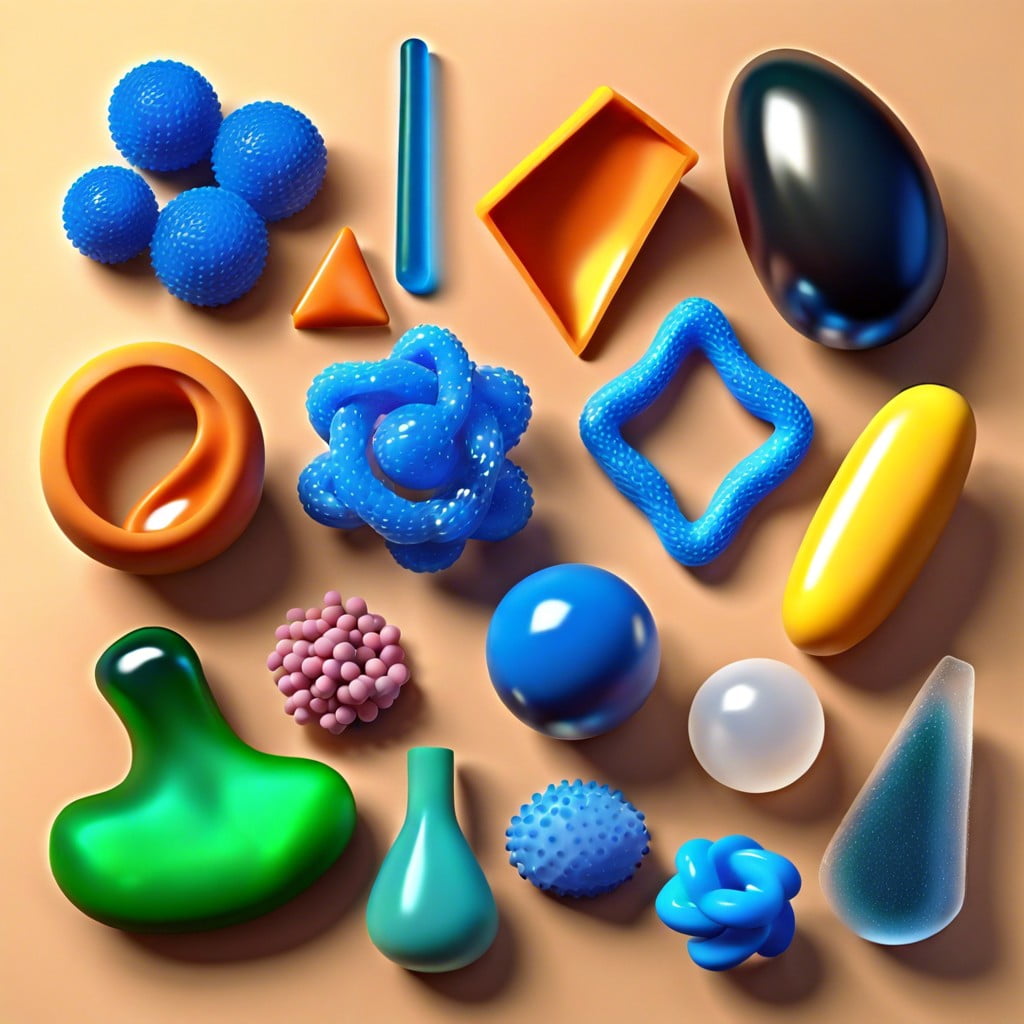
Polymers are categorized into various shapes that play pivotal roles in their application, especially in construction. Here’s a closer look at these classifications:
1. Linear Polymers: These consist of long, continuous chains. They have the ability to soften on heating and harden on cooling, making them suitable for processes like extrusion, which is utilized to produce pipes and profiles.
2. Branched Polymers: Featuring side chains attached to the main chain, these polymers have less dense structures than linear polymers and can impact properties such as flexibility and strength in products like insulation materials.
3. Cross-linked Polymers: With networks of bonds linking chains together, cross-linked polymers form rigid, three-dimensional structures. They are commonly used in resins and sealants for their durability and resistance to deformation.
4. Network Polymers: These have multidimensional networked structures, offering high strength and rigidity. Materials like epoxy, used in heavy-duty concrete repairs and reinforcements, exemplify network polymers.
Each shape determines a polymer’s physical properties and its suitability for various construction tasks, from load-bearing components to insulation.
Benefits of Specific Polymer Shapes
Polymer shapes are tailored to enhance a material’s performance in construction. Here’s how specific shapes can be advantageous:
1. Stress Distribution: Geometrical polymers like honeycombs distribute loads evenly, lessening stress at pressure points and increasing durability.
2. Insulation: Foamed polymers have air pockets, significantly improving thermal and acoustic insulation properties.
3. Material Efficiency: Fibers or rods can reinforce other materials, offering strength without excessive weight, leading to material and cost savings.
4. Aesthetics and Functionality: Certain shapes such as sheets or tiles can be designed to interlock, aiding in ease of installation while also contributing to the visual appeal of a structure.
5. Flow Dynamics: In piping and ductwork, polymers can be moulded for smoother surfaces to reduce drag and improve flow efficiency for liquids and gases.
6. Chemical Resistance: Specially shaped polymer coatings can protect structures from harsh chemicals, extending the lifespan of the construction materials.
Fabrication Techniques for Polymer Shapes
Creating precise polymer shapes involves various fabrication techniques tailored to the material type and the desired application. The most common methods include:
- Extrusion: Polymers are heated and forced through a die of the desired cross-section, producing long sections like pipes or profiles.
- Injection Molding: Melted polymer is injected into a mold where it cools and solidifies into a complex shape, ideal for mass production of components.
- Thermoforming: Sheets of thermoplastic polymer are heated until pliable, then shaped over a mold by vacuum or pressure before cooling.
- Rotational Molding: Polymer is added to a hollow mold which is then heated and rotated to coat the interior uniformly, forming hollow items.
- 3D Printing: Also known as additive manufacturing, this method deposits material layer by layer to build up the final shape, allowing for intricate designs and on-demand production.
Each technique offers diverse properties and shapes; the choice depends on factors such as the complexity of the design, material properties, production volume, and cost considerations.
Common Thermoplastic Polymer Shapes in Construction
Thermoplastics are the workhorses of construction materials, favored for their ability to be molded when heated and retain shape once cooled. Here’s how they come into play:
- Pipes and Fittings: Polyvinyl chloride (PVC) pipes are ubiquitous, valued for their durability and water resistance.
- Insulation Foam: Polystyrene comes as foam boards, serving as excellent insulation while being lightweight.
- Profiles for Windows and Doors: Rigid PVC or polyurethane profiles offer high strength and weather resistance for frames.
- Flooring: Vinyl tiles made from PVC provide a versatile and waterproof flooring solution.
- Roofing Sheets: Polycarbonate sheets are chosen for their transparency and impact resistance, great for skylights.
- Electrical Components: Light switches and cable insulation often employ polyethylene due to its electrical insulative properties.
These shapes demonstrate thermoplastics’ versatility in contributing to a building’s functionality and longevity.
Common Thermoset Polymer Shapes in Construction
Thermoset polymers are like the set-and-forget materials of the construction world. Once they cure, they’re locked into a stable, heat-resistant state that doesn’t melt down, making them stellar players for sturdy applications.
Here’s how they show up on the construction site:
- Epoxy Resins: Masters of adhesion, you’ll find them bonding everything from concrete slabs to fiber-reinforced composites.
- Polyester Resins: These versatile performers are used in laminates and as a matrix for fiberglass.
- Phenolic Resins: Found in insulating materials and fire-resistant claddings due to their outstanding thermal stability.
- Urea-Formaldehyde: Commonly chosen for adhesives and molding compounds for its strong mechanical properties.
From adhesives and coatings to composites and foam insulation, these materials are tailored to serve specific construction needs with immense reliability. Think of them as the customized toolkit for builders, providing solutions that stay true to form under pressure.
The Impact of Shape On Polymer Performance
The configuration of a polymer can markedly influence its mechanical properties and suitability for construction applications.
Surface Area to Volume Ratio: Polymers with high surface area-to-volume ratios, like thin films or fibers, can have faster reaction rates due to more substantial exposure to surrounding materials or conditions.
Stress Distribution: Certain shapes, such as I-beams made from polymer composites, distribute stress more effectively across their structure, enhancing load-bearing capacity and resistance to deformation.
Interlocking Ability: Some polymer shapes, like interlocking bricks or tiles, capitalize on their geometry to provide additional structural stability without the need for adhesives or fasteners.
Thermal Properties: The shape of a polymer can determine its thermal performance. For instance, polymer foam insulation boasts a shape that traps air in closed cells, thereby reducing heat transfer.
Hydrodynamics and Aerodynamics: In applications like pipes or cladding, the shape of polymers affects fluid dynamics, impacting flow resistance and potentially leading to energy savings.
Light Manipulation: Certain polymer shapes, such as corrugated sheets or lenses, can be used to diffuse, focus, or redirect light, which can be particularly useful in daylighting solutions for buildings.
Understanding these aspects helps in selecting the optimal polymer shape for a given construction need, ensuring functionality and longevity of the material in its application.
Innovative Polymer Shapes and Structures
Advancements in materials science have paved the way for exciting developments in the realm of polymers used in construction. These innovations are not only transforming the physical properties but also the aesthetic possibilities of structures:
- Self-healing Polymers: Ingenious shapes, such as vascular networks within materials, facilitate self-repair, drastically reducing maintenance costs.
- Aerogels: These are ultralight structures with incredible thermal insulation properties, often resembling solid smoke in appearance yet strong enough for architectural use.
- 3D-printed Polymer Components: Custom shapes can be created with complex geometries that were previously impossible or too expensive to manufacture, optimizing material usage and structural integrity.
- Smart Polymers: Responding to environmental stimuli, such as temperature or pH changes, these materials can alter their shape, leading to dynamic structures that adapt to weather or load conditions.
- Composite Materials: By combining polymers with other substances like glass fibers or nanoparticles, designers achieve unique shapes and enhanced material traits tailored for specific construction needs.
Each innovation unlocks new potential for construction projects, challenging traditional design limitations and fostering a future of creativity and sustainability.
Challenges in Shaping Polymers for Construction Uses
When tailoring polymers to construction needs, several challenges may arise. First, ensuring consistency in the polymer’s shape is critical, as deviations can weaken the structure. Temperature control during shaping is also vital; too high and the material may degrade, too low and it may not form properly.
Moreover, some complex shapes are inherently difficult to produce due to limitations in molding or extrusion techniques. For example, intricate designs may require advanced fabrication methods, which can be costly and time-consuming.
Compatibility with other building materials is another hurdle. The chosen polymer must adhere well to different substrates without compromising its structural integrity. Additionally, environmental factors such as UV exposure and temperature fluctuations can impact the longevity of the shaped polymer, making the choice of material and design crucial.
Addressing these challenges often requires a multidisciplinary approach, combining material science with cutting-edge manufacturing technologies to ensure that the polymer shapes can be reliably produced and will perform well in their intended applications.
Future Trends in Polymer Shape Design and Application
Advancements in technology pave the way for exciting prospects in the field of polymer shapes. With a constant push towards innovation, here are some emerging trends:
1. 3D Printing: The rise of 3D printing technology allows for the creation of complex polymer geometries that were once difficult or impossible to produce. This trend is expected to grow, offering custom solutions for specific construction applications.
2. Self-healing Materials: Research is focusing on polymers that can self-repair after damage, extending the life of construction materials and reducing maintenance costs.
3. Smart Polymers: The development of polymers that can change shape in response to external stimuli, such as temperature or pH, offers new possibilities for dynamic structures and responsive building envelopes.
4. Nanotechnology: Integrating nanomaterials with polymers is forecasted to produce composites with superior strength, durability, and thermal properties, which could redefine construction standards.
5. Biodegradable Polymers: As sustainability becomes a priority, there is an increased interest in developing polymers that can decompose naturally, reducing the environmental impact of construction waste.
These forward-looking trends suggest a future where polymer shapes are not only tailored to their application but are also smarter, more durable, and environmentally friendly.
FAQ
Who owns polymershapes?
Polymershapes is owned by SABIC, a global petrochemicals manufacturer based in Riyadh, Saudi Arabia.
How many locations does polymershapes have?
Polymershapes has over 80 locations across the Americas.
What are the two types of plastic?
The two types of plastic are thermoplastic and thermosetting.
What is the introduction of plastic?
Plastics are typically human-made materials derived from fossil fuel-based chemicals like natural gas or petroleum, though recent methods also use renewable materials such as corn or cotton derivatives.
What are some common applications of polymers in construction?
Polymers in construction are commonly used in insulation, flooring, windows, pipes, adhesives, sealants, and protective coatings due to their versatility, durability, and resistance to environmental conditions.
How do polymers improve the durability of construction materials?
Polymers enhance the durability of construction materials by increasing their hardness, flexibility, and resilience to environmental conditions such as heat, cold, and moisture.
What is the environmental impact of using polymers in construction?
The environmental impact of using polymers in construction includes the potential for non-biodegradability leading to waste accumulation, carbon emissions during production, and possible release of harmful chemicals during degradation.
Recap