Discover how polymer sealants enhance building durability by offering protection from various elements.
Key takeaways:
- Polymer sealants are versatile substances used to fill gaps and provide a protective barrier.
- They are strong, flexible, and durable, ideal for various applications.
- Polymer sealants resist UV light, extreme temperatures, and chemicals.
- They are used in roofing, windows, plumbing, construction, automotive, and marine industries.
- Polymer sealants are easy to apply, have superior adhesion, and are paintable.
Definition of Polymer Sealant
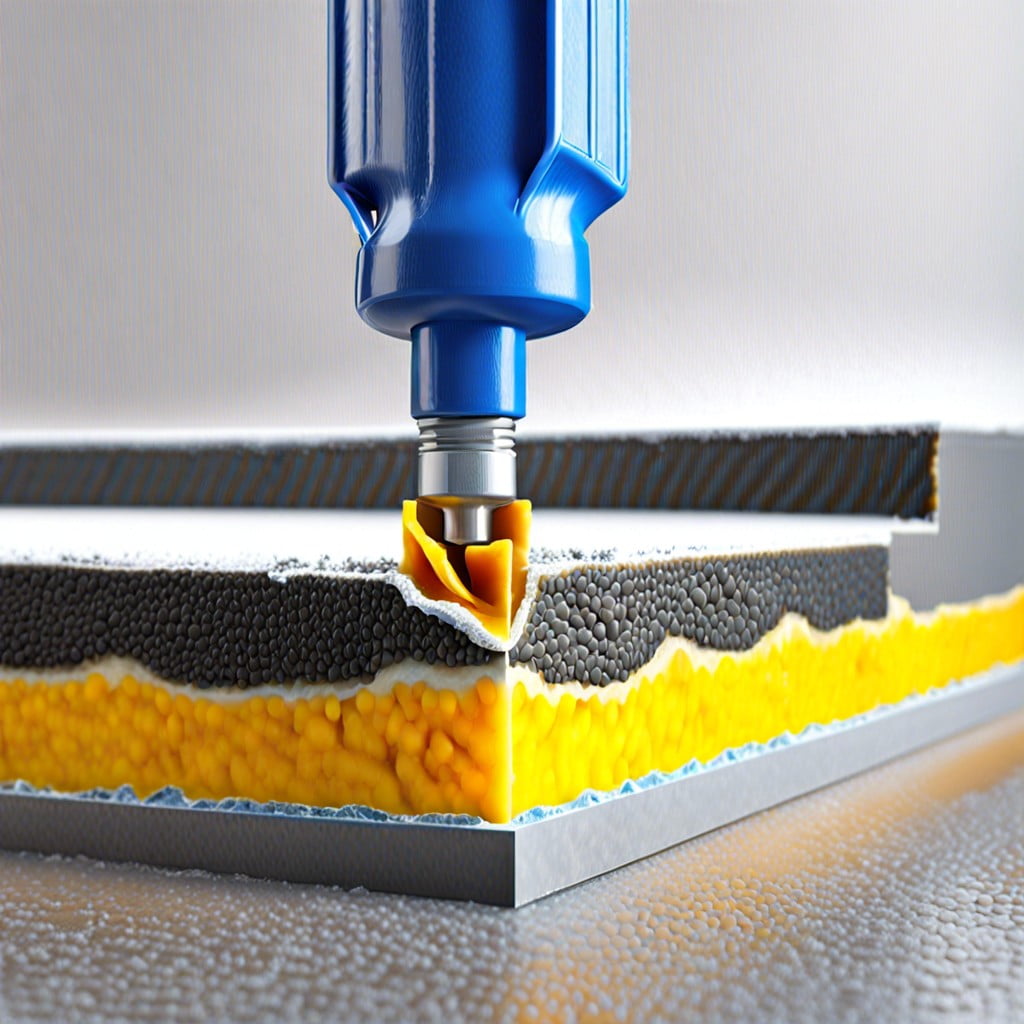
Polymer sealants are versatile substances made from polymers—long, repeating chains of molecules—that are used to fill gaps, seal joints, and provide a protective barrier against moisture, air, and contaminants.
They come in various chemical compositions, such as silicone, polyurethane, and acrylic, tailored to meet specific requirements in construction and other industries.
These sealants are notable for their strong adhesion, flexibility, and durability, which make them ideal for a wide range of applications from window installation to plumbing.
They can be formulated to resist environmental factors like UV light and extreme temperatures, ensuring long-lasting protection in different conditions.
Properties and Applications of Polymer Sealants
Polymer sealants boast impressive flexibility, allowing them to accommodate movement and settling in structures. They create durable, water-resistant barriers that effectively prevent leaks. Due to their adhesive properties, they bond well with various materials like glass, wood, and concrete, making them versatile for different construction needs.
Their resistance to temperature changes and UV light is noteworthy, meaning they perform reliably across climates and seasons. These sealants also exhibit resistance to chemicals, contributing to their longevity even in harsh environments.
In the realm of applications, polymer sealants are champions in both indoor and outdoor settings. They are used to seal joints and cracks in roofing, windows, and plumbing systems. In construction, they facilitate airtight sealing in building envelopes, enhancing energy efficiency. Additionally, they’re a go-to for automotive and marine industries for sealing and bonding components due to their robustness against weather and water exposure.
Lastly, their easy application and curing process make them a convenient choice for DIY enthusiasts and professionals alike. They are available in different viscosities, catering to a wide array of sealing tasks from fine crack filling to sealing sizable gaps.
Benefits and Comparison With Other Sealant Types
Polymer sealants offer several advantages over traditional options like silicone or urethane. A key benefit is their superior adhesion to a wide variety of substrates, including glass, aluminum, wood, and some plastics. This ensures a robust and durable bond, crucial in construction where different materials meet.
Another advantage is their flexibility. Polymer sealants can withstand significant movement or expansion of the materials they’re bonding, which is vital for temperature-induced contraction and expansion in structures. They can thus maintain an effective seal longer than other sealants that may crack or degrade under similar conditions.
Additionally, polymer sealants often come with enhanced UV resistance, making them less prone to deteriorate when exposed to sunlight. This is particularly beneficial for exterior applications where sunlight can be relentless.
Importantly, these sealants are usually paintable after curing, offering an aesthetic advantage as they can be easily integrated into the overall design without remaining visible.
While silicone sealants are also flexible and have good temperature resistance, they don’t bond with as many materials as polymers and are typically not paintable. Urethane sealants are strong and adhere well, but their UV resistance is inferior compared to polymer options.
In terms of health and safety, polymer sealants are often a lower-VOC (volatile organic compounds) alternative, emitting fewer harmful fumes during application and curing.
In summary, polymer sealants are versatile, durable, and offer excellent performance for a range of construction needs, often outperforming other sealant types in key areas of application, longevity, and aesthetics.
How to Apply Polymer Sealant, Curing Time, and Maintenance Tips
Before applying polymer sealant, ensure the surface is clean, dry, and free of any loose particles or previous sealant residues. Apply the sealant using a caulking gun or a spatula, depending on the viscosity of the product. Smooth the sealant with a wet finger or a tool dipped in soapy water for a clean finish.
Curing time varies among products but generally ranges from 24 to 48 hours for a surface skin to form. Full cure may take up to a week, during which the area should remain dry and undisturbed.
For maintenance, periodically inspect sealed areas for cracks or adhesion loss. Clean the surface with mild soap and water, avoiding abrasive materials that might damage the seal. If necessary, touch up or reapply the sealant following the original application guidelines to ensure continued protection and function.
Environmental Considerations and Safety Measures
Polymer sealants often contain volatile organic compounds (VOCs) which can evaporate and impact indoor air quality. For eco-conscious usage, opt for sealants with a low VOC content. Some products are even water-based, further reducing environmental impact.
Proper ventilation is key when applying sealants to safeguard against inhaling fumes. It’s advisable to use personal protective equipment like gloves and masks, especially in confined spaces. Always adhere to the manufacturer’s guidelines for safe application and disposal to minimize hazards and ensure environmental protection.
Additionally, many manufacturers are developing bio-based polymer sealants that offer a more sustainable option by utilizing renewable resources and reducing reliance on petroleum-based materials.
Recap