Learn all about polymer resources and how they’re revolutionizing construction in fun and unexpected ways!
Key takeaways:
- Polymer resins: Strong, lightweight, versatile, durable, cost-effective.
- Polymer evolution: From Bakelite to sustainable skyscrapers.
- Manufacturing process: Polymerize, compound, shape – like making a smoothie.
- Recycling innovations: Biodegradable, chemical recycling, mechanical recycling, enzymes, closed-loop systems.
- Product selection: Understand needs, check durability, ensure compatibility, consider environmental impact, mind your budget.
Key Benefits of Polymer Resins
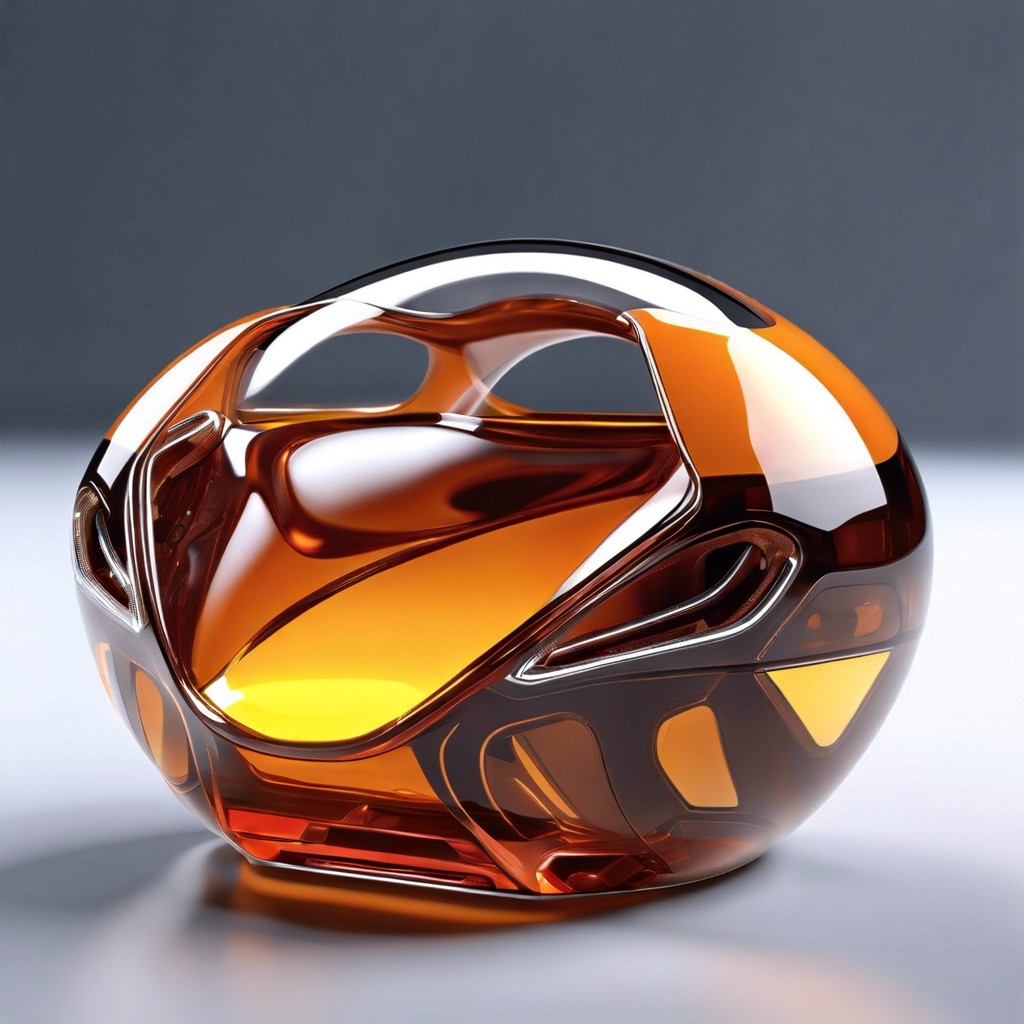
Imagine trying to build a skyscraper out of pasta. Spoiler alert: it wouldn’t last very long. That’s where polymer resins come in, adding strength and durability without turning construction into a balancing act.
First off, these materials are incredibly strong and lightweight. You get the muscle without the bulk, kind of like a gymnast. They can take a beating and still hold up.
Next on the list, polymers are versatile. You can mold them into almost any shape you need, from pipes to panels. Think of them as the Play-Doh of the construction world.
They are also incredibly durable. They don’t rust, rot, or corrode. Unlike metal or wood, they won’t turn into a pile of junk if they get wet.
Finally, polymer resins are cost-effective. They are cheaper to produce and transport, which means more budget for other fancy construction projects—or perhaps a coffee machine for the break room.
History and Evolution
Alright, imagine it’s the late 19th century. A guy named Leo Baekeland is fiddling around in his lab, accidentally inventing Bakelite, the granddaddy of all modern polymers. Fast forward a few decades, and World War II accelerates the development of synthetic materials, giving us nylon and polyethylene.
– The 1950s roll in, bringing us the era of mass-produced plastics. Suddenly, everything from Tupperware to hula hoops is made from polymers.
– The 1970s see a shift towards better, stronger, and lighter materials. This is the decade where reinforced plastics enter the construction scene, paving the way for the future.
– In the 2000s, the focus shifts to sustainability. Bio-based plastics and advanced recycling technologies start to take the spotlight.
It’s been quite the journey, right? From Bakelite radios to sustainable skyscrapers, polymers have come a long way.
Manufacturing and Compounding Process
To create polymers, you have to start with the building blocks called monomers. Imagine them as Lego pieces. These pieces are chemically bonded together to form long chains, or polymers.
First, you have polymerization. It’s like a big party where monomers find each other and decide to stick together. There are different types of polymerization, but let’s avoid crashing that chemistry lecture.
Once your polymer chains are ready, they move on to compounding. This is where you jazz things up. Additives are blended in to give the polymer specific properties. Need it to be stronger? Tougher? Fire-resistant? Compounding is like adding spices to a sauce.
Then, they mix it all up, usually in a machine that’s like a gigantic blender. Heat it, cool it, shape it. Voilà, you have the polymer ready for whatever dazzling construction project you’ve got in mind.
In simpler terms: think of it as making a super smoothie. Monomers are your fruits, polymerization is blending them, and compounding is adding the yummy extras like honey or protein powder. Now you have your high-energy drink, or in this case, a construction-ready polymer!
Recycling Innovations
One amazing recycling innovation is the development of biodegradable polymers. Imagine plastic that just… vanishes! These polymers break down naturally over time, reducing landfill waste. They’re a win-win for the environment and our conscience.
Then, there’s chemical recycling, which sounds like magic but is actually science. Instead of melting down old plastics, this process breaks them into their basic building blocks. These building blocks can then be reassembled into brand new products. It’s a bit like LEGO, but with fewer painful stepping incidents.
Mechanical recycling is another technique, where polymers are shredded and re-melted into new forms. This method has been around for a while and is super effective for certain types of plastics. Picture a phoenix rising from the ashes, but in a more eco-friendly fashion.
Also, some clever folks have created enzymes that eat plastic. These little helpers break down PET, a common polymer in bottles, into harmless substances. It’s like having a tiny, invisible cleanup crew.
Finally, let’s talk about closed-loop systems, which are popping up more in construction. In these systems, old materials are continuously recycled into new ones, cycling through like water in a fountain. This reduces waste and keeps resources in play.
With these innovations, our world is becoming a cleaner, greener place, proving that with a bit of ingenuity, we can transform trash into treasure.
Product Selection Guide
Choosing the right polymer for your construction project can feel like shopping for shoes—so many options, but only one perfect fit!
- Understand Your Needs: What’s the project? Is it waterproofing, insulation, or something else entirely? Your answer will guide you.
- Durability Matters: Look at the lifespan. High-traffic areas will need polymers with higher wear resistance.
- Look at Compatibility: Not all polymers get along with other materials. Make sure your choice won’t lead to any chemical quarrels.
- Environmental Impact: Some polymers are more eco-friendly than zesty oranges. Opt for recycled or recyclable options if possible.
- Budget: While top-shelf polymers have more bling, sometimes a mid-range choice does the job without breaking the bank.
Remember, picking the right polymer is like picking a dance partner—you want reliability, compatibility, and a bit of flair!
Recap