In this article, you’ll learn what polymer extrusion is and how it plays a crucial role in creating various construction materials.
Key takeaways:
- Polymer extrusion is a high-volume manufacturing process for creating continuous profiles.
- The process involves melting plastic, shaping it, and then cooling it to harden.
- Components of a plastic extruder include a screw, barrel, heaters, cooling fans, and a die.
- The process requires careful control of temperature, speed, and pressure.
- Different types of plastic extrusion processes include sheet/film, profile, tube, blown film, co-extrusion, and overjacketing.
Plastic Extrusion Definition
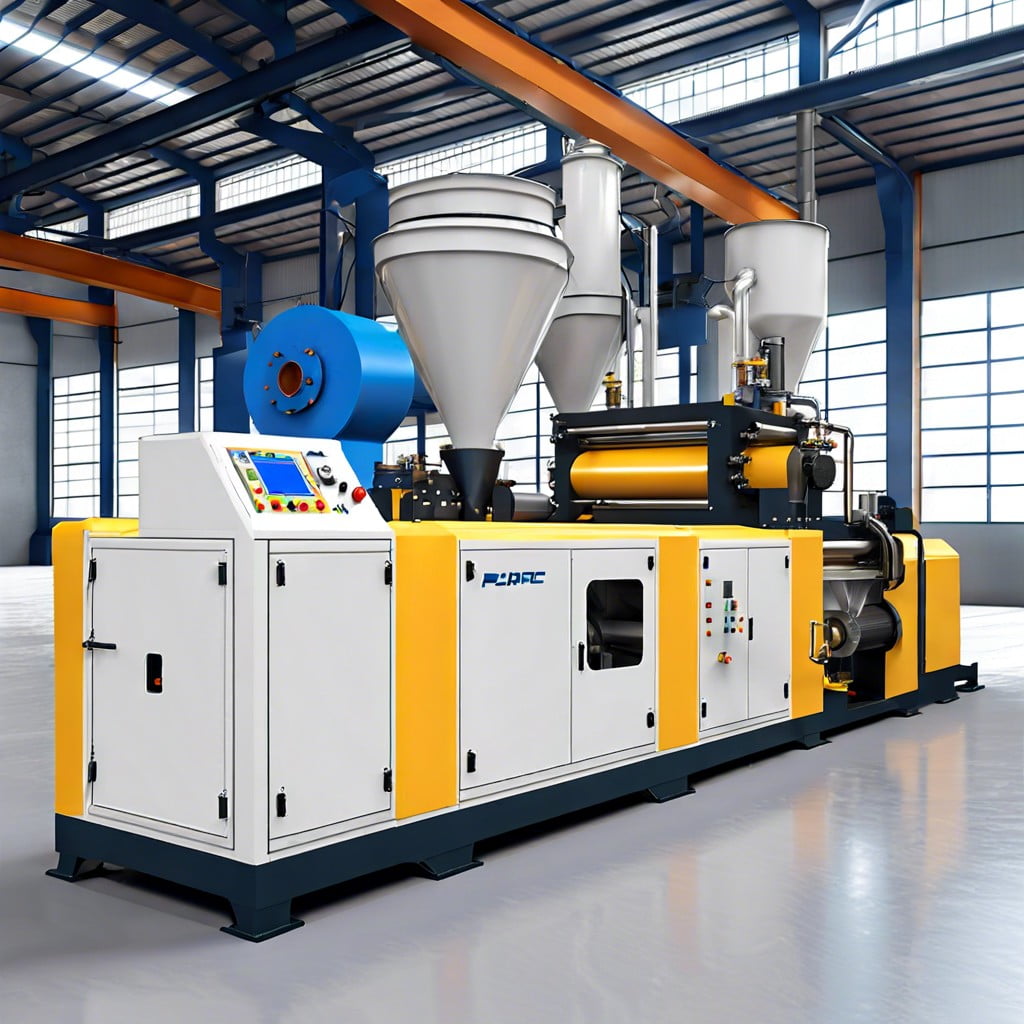
Plastic extrusion is a high-volume manufacturing process in which raw plastic is melted and formed into a continuous profile. This process starts with the feeding of plastic material (pellets, granules, flakes or powders) from a hopper into the extruder machine.
Within the extruder, a revolving screw pushes the plastic through a heated chamber, where it’s brought to a molten state. The consistency of the melted plastic is carefully controlled to ensure that the final product maintains a uniform shape and density.
As the plastic exits the extruder, it passes through a shaped die that gives it the desired cross-sectional profile. Following this, the extruded plastic is cooled, often by water or air, to harden it and help retain its shape.
Lastly, the hardened extrusion is cut or spooled into lengths suitable for application or further processing.
This method benefits from high efficiency and the ability to create complex cross-sections, making it integral to the production of a wide range of products, including piping, weatherstripping, and plastic sheeting.
Components of a Plastic Extruder
The heart of a plastic extruder is the screw, housed within a barrel. This screw, powered by a motor, is the primary driver for melting and pushing the polymer material through the machine. As it rotates, it not only transports the raw polymer but also applies the necessary heat and pressure for melting.
Surrounding the barrel, heaters ensure the polymer reaches its optimal melting temperature. Additionally, cooling fans are installed to prevent overheating and to maintain a consistent temperature along the barrel.
At the feeding zone, raw polymer is introduced, typically in the form of pellets or granules, from a hopper. The hopper’s design ensures a steady and controlled flow of material into the extruder.
Next comes the die, which is responsible for shaping the molten polymer into the desired profile as it exits the extruder. Die shapes are diverse, ranging from simple tubes to complex multi-chambered profiles, depending on the final product.
Finally, downstream equipment is essential for sizing, cooling, and cutting the extruded plastic into usable lengths. This equipment includes sizing plates, cooling tanks, and saws or cutters, which work in synchrony to finalize the product.
Details of the Plastic Extrusion Process
The plastic extrusion process begins with feeding raw polymer material, usually in the form of pellets or granules, into the extruder machine. A hopper sends the material into a barrel where a screw mechanism pushes the material through, generating heat from friction and sometimes additional external heating elements. This heat melts the polymer into a viscous liquid.
As the molten polymer is forced along the barrel, it is thoroughly mixed and homogenized. The consistency of the molten plastic is key – it must be fluid enough to shape but stable enough to maintain that shape upon exiting.
Towards the end of the barrel, the now-molten plastic is pushed through a die, which is a mold that gives the plastic its final shape. The die is designed based on the desired profile of the extruded plastic product, such as pipes, sheets, or films.
Following the shaping in the die, the extruded plastic enters a cooling stage to solidify the shape. Cooling is typically done by water baths, air, or contact with cool surfaces. After cooling, the product is cut to length or spooled, completing the extrusion process. This stage is crucial because proper cooling ensures the product retains its shape and properties.
Throughout the entire process, careful control of temperature, speed, and pressure is essential to produce a high-quality extruded product that meets the necessary specifications.
Types of Plastic Extrusion Processes
Different forms of plastic extrusion shape the way polymers are processed into products:
**Sheet/Film Extrusion:** This process involves squeezing molten plastic through a flat die, followed by cooling to create thin films or thicker sheets. Commonly used for packaging materials, it can also produce items like window films and sheeting for construction.
**Profile Extrusion:** By pushing plastic through a custom-shaped die, manufacturers can create continuous sections of complex cross-sectional shapes. This method is ideal for making PVC pipes, weatherstripping, and home siding.
**Tube extrusion:** Similar to profile extrusion but specifically used to create hollow tubes or pipes. It is a versatile process, with the ability to tailor wall thickness and diameter for various uses such as plumbing, medical tubing, and conduit.
**Blown Film Extrusion:** A variation of Film extrusion. In this method, air inflates the extruded plastic to form a bubble, which is then transformed into thin film upon cooling. Bags, overwrap, and agricultural films are often produced using this technique.
**Co-extrusion:** This advanced process combines two or more different materials into a single extruded profile. It allows for the production of parts with distinct layers, providing different characteristics such as barriers to moisture or gases, often used in food packaging solutions.
**Overjacketing Extrusion:** Typically used for wire coating, overjacketing covers a pre-existing product with a layer of plastic. The aim is often to enhance the durability or electrical properties of cables and wires.
Each process offers unique advantages suited to specific product requirements and applications. Understanding these types allows for the customization of materials and production methods, leading to innovative uses across industries.
Applications of Extruded Plastic Products
Extruded plastic products permeate our everyday lives, providing critical functions across a wide range of applications. In construction, extruded polymer products form sturdy window frames, weatherstripping, and insulation, contributing to energy efficiency and durability. In the medical field, extruded tubing is essential for various applications, including intravenous therapy and complex medical devices.
Beyond these, extrusion is key in creating packaging materials, such as plastic bags and wraps that protect products from damage and contamination. In the automotive industry, extrusion contributes to the manufacturing of components like door seals, dashboard trims, and bumpers, all of which rely on the versatility and resilience of extruded polymers.
Furthermore, the electronics industry benefits from extruded polymers in the form of sheathing for wires and cables, which offers protection and insulation. Lightweight and corrosion-resistant, these extruded components are vital in ensuring the longevity and safety of electrical systems.
Lastly, the significance of extruded polymers extends to the agricultural sector, where irrigation tubing and films for greenhouses play a part in food production. These applications illustrate the integral role that extruded plastic products play in advancing and sustaining various facets of our modern world.
Recap