Dive into the dynamic world of the polymer concrete market as we unravel its various aspects, trends, and underlying statistics in this comprehensive blog post.
The global polymer concrete market is a dynamic and rapidly evolving sector, seeing significant growth over the past few years. This growth is primarily driven by the increasing demand for chemical-resistant construction materials, the rising number of construction activities around the globe, and the superior properties of polymer concrete over traditional concrete.
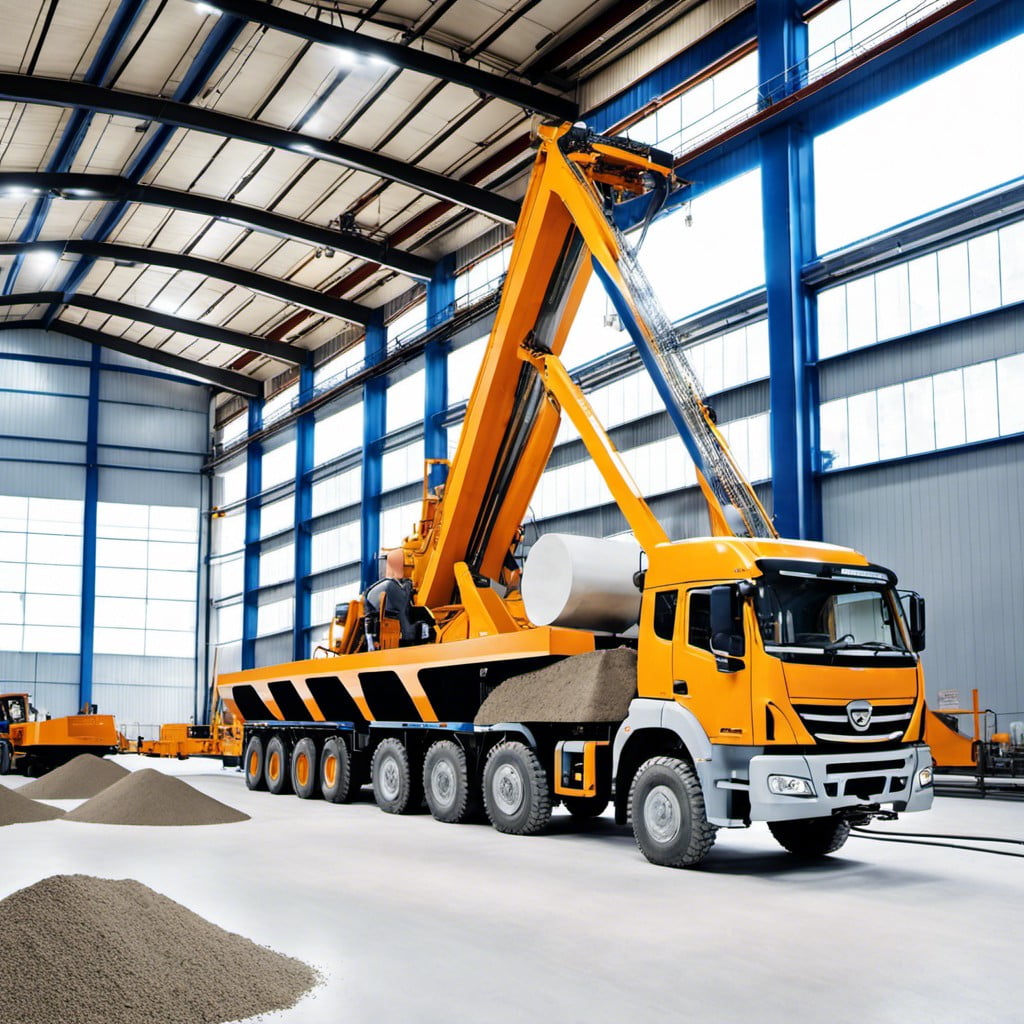
Delving deeper into the numbers, we’ll explore the market size, segmentation, growth factors, and future forecasts, providing a comprehensive understanding of the current status and future prospects of the polymer concrete industry. Whether you’re an investor, a manufacturer, or simply interested in the market dynamics, this analysis will offer valuable insights into the polymer concrete market.
The polymer concrete market size is set to be valued at around $465 million in early 2022
As we move into the early phase of 2022, it’s expected that the valuation of the polymer concrete sector will hover close to $465 million.
This projected figure underlines the increasing demand for polymer-based concrete products, which have significantly gained consumer traction owing to their enhanced durability and compatibility with various construction environments.
The expanded use in infrastructure and residential construction projects globally contributes greatly to this projected upswing in market esteem.
There’s a healthy CAGR of 7.7% growth rate from 2022 to 2023
As we venture deeper into the analysis, it is remarkable to note that the expected Compound Annual Growth Rate (CAGR) for the sector is rather promising. Clocking in at an impressive 7.7% from 2022 to 2023, this growth encapsulates the sector’s robust dynamic and the timeless relevance of polymer concrete in the modern world.
This upward trajectory is fueled by ongoing technological advancements coupled with a growing demand in residential, non-residential, and infrastructure segments. The improvements in manufacturing efficiency, quality, and versatility of polymer concrete products only further facilitate this striking growth pattern.
Consequently, key industry players and investors can anticipate lucrative opportunities in the forthcoming year.
The market is expected to reach US$ 979.2 million by 2032
Bearing a compound annual growth rate (CAGR) of approximately 7.7%, the upswing in demand is to surge the polymer concrete market valuation significantly.
By 2032, it is projected that the figure would skyrocket, resting in the vicinity of a hefty US$ 979.2 million.
This escalation will be a testament to expanding infrastructure, residential, and non-residential sectors.
The underlying strength of this form of concrete, which excels in durability, chemical resistance, and ease of molding, is tapping into the environmental friendliness niche, further bolstering the prospective growth.
By the end of 2022, the market grew to US$686.8 million
Experiencing a surge in demand across various industrial applications, the polymer concrete market saw impressive gains in the last 12 months. The total value skyrocketed, realizing a fiscal endpoint of US$686.8 million.
This substantial increase was prompted by the material’s distinct advantages over traditional concrete, including enhanced strength and durability.
Expanding public infrastructure projects and private investment in residential and non-residential property developments contributed significantly to this growth.
Infrastructure, residential, and non-residential remain to be the segments where polymer concrete is used
Infrastructure holds a significant share with polymer concrete majorly employed in vital projects like roads, civil engineering works, and water management systems due to its corrosion and freeze-thaw resistance and rapid curing time. In this segment, polymer concrete is often used in repair work instead of full-scale construction due to its high cost.
The residential sector is another major area where polymer concrete finds application. It’s highly utilized in high-load-bearing structures, specifically repair work for homes and flats to boost structural integrity without the need for demolition or extensive labor.
Non-residential sectors such as schools, hospitals, and corporate buildings also use polymer concrete. Predominantly used in the repair and restructuring of old buildings, its high durability and resistance to environmental effects make it a popular choice.
Vinyl acetate is one of the most malleable polymers used to alter concrete for cementitious toppings
In the realm of polymers used in the manufacture of cementitious toppings, vinyl acetate stands prominent. Its malleability sets it apart, enabling significant alterations to the substance of the concrete. This remarkable plasticity enables the creation of flexible, high-strength overlays capable of withstanding various environmental conditions and mechanical stressors.
Additionally, the use of vinyl acetate aids in enhancing durability, reducing brittleness, and improving tensile strength, making it an ideal choice for vital infrastructural projects, residential buildings, and non-residential facilities.
Furthermore, the use of this polymer in altering concrete stimulates improved water resistance, thus extending the life span of the structure.
USA, along with China, Japan, and India are the top countries driving the polymer concrete market
Collectively accounting for a substantial market share, these giants of the industry underscore the key roles they play in driving global demand. The U.S. consistently holds a dominant position, largely credited to its well-established construction sector and steadfast focus on infrastructure development. Meanwhile, China leads the Asian market, where rapid urbanization stokes growth.
Likewise, Japan’s commitment to sophisticated technology parallels its push toward innovative manufacturing processes, bolstering the industry. India, while trailing behind, cannot be overlooked. Its demand is underpinned by a surging residential sector and large-scale infrastructural projects.
These four nations’ contributions collectively fuel the forward movement of the polymer concrete market.
The cost of polymer in a cubic yard of concrete ranges between $70 to $350 per cubic yard
Undeniably, material costs can significantly influence choices within the construction realm. While traditional materials like cement and concrete continue to dominate the market, the increasing use of polymer concrete provides a more cost-effective alternative.
Prices can vary depending on the specific polymer used and the quantities required, but typically, adding polymer to a cubic yard of concrete will increase costs by $70 to $350. This broad pricing spectrum reflects the diversity in polymer types and grades. Higher prices are generally associated with superior-quality polymers offering enhanced strength and durability, while lower costs are frequently associated with more basic, commodity-type polymers.
The standard for polymer-cement ratio of the latex-modified concrete ranges from 5 to 15%
With regards to latex-modified concrete, a significant variable to consider involves the proportion of its two core components – polymer and cement. Empirical data indicates that the most effective blend typically lies within a 5% to 15% range of polymer to total cementitious materials. This ratio allows for reliable gains in durability, tenacity, and water resistance, making the choice of polymer content integral to the overall project quality. This strategic balance ensures firms can optimize their resources efficiently, producing robust and resilient final products that cater to diverse industry requirements.
The optimum polymer content varies from 12 to 14%
Achieving the right balance in polymer proportion in polymer concrete is crucial. Content exceeding 15% tends to result in diminishing mechanical properties, making it less optimal for use. On the other hand, decrease below 12% results in inadequate coating of aggregate particles by the polymer, leading to lower durability. Thus, for maximum efficiency and optimal mechanical properties, keeping polymer content between 12 to 14% is deemed ideal by most manufacturers in the industry. This range delivers a balance, ensuring both durability of the composite material and cost-effectiveness in its manufacturing process.
References:
- https://concretefinancialinsights.com/
- https://www.globenewswire.com/
- https://www.researchnester.com/
- https://www.marketsandmarkets.com/
- https://www.idc-online.com/
- https://www.sciencedirect.com/
Recap