In this blog post, we will explore the science behind polymer composite properties and how understanding them can lead to better material selection in construction.
Polymer composites are materials made up of two or more constituent materials with different physical and chemical properties. They are widely used in construction because of their unique properties, including high strength-to-weight ratio, corrosion resistance, and durability.
But what exactly makes polymer composites so special? In this article, we will explore the science behind these materials and how understanding their properties can help you make better decisions when selecting construction materials. So sit back, grab your hard hat, and let’s dive into the world of polymer composites!
Polymer Composite Basics
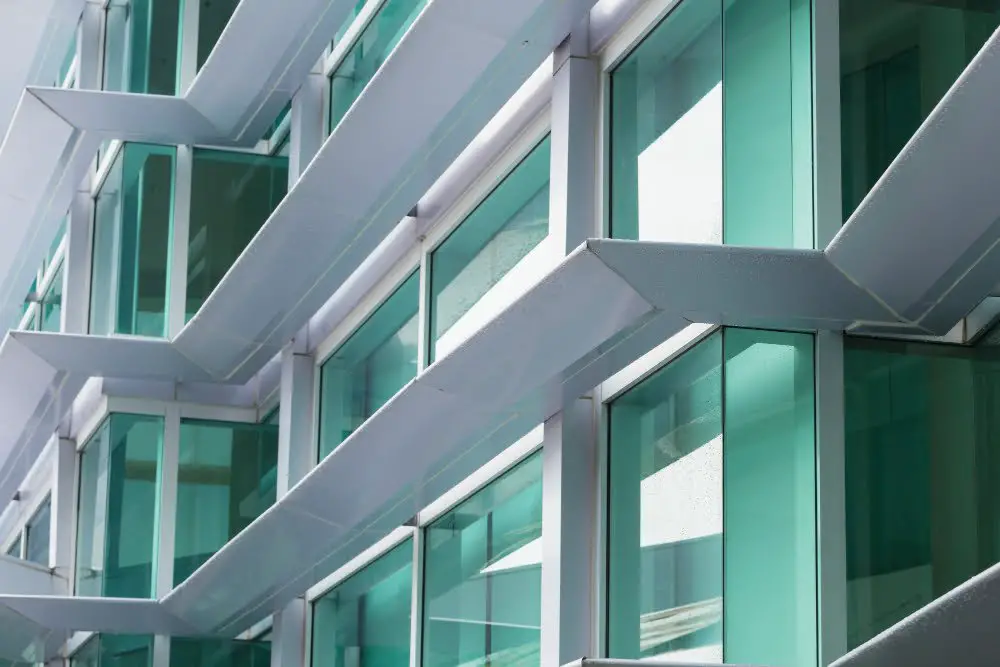
Polymer composites are materials that consist of two or more constituent materials with different physical and chemical properties. The combination of these materials creates a new material that has unique properties, making it ideal for use in construction.
Polymer composites have become increasingly popular in recent years due to their many benefits over traditional building materials such as wood and steel. They offer high strength-to-weight ratios, excellent corrosion resistance, durability against harsh weather conditions and chemicals – all while being lightweight enough to transport easily.
Understanding the basics of polymer composite properties is essential when selecting construction materials because they can be tailored to meet specific project requirements based on their composition and manufacturing process.
By understanding how these factors affect performance characteristics like stiffness or toughness (among others), you can make better decisions about which type will work best for your particular application needs.
Types of Polymer Composites
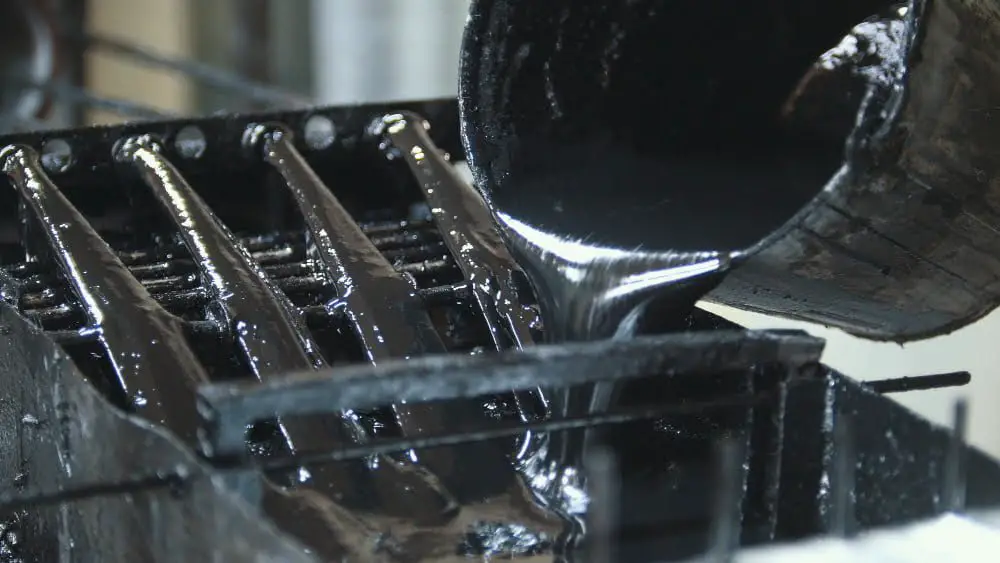
Just like how there are different types of Legos, there are also different types of polymer composites. Each type has its own unique properties and is used for specific applications in the construction industry.
One common type of polymer composite is fiber-reinforced polymers (FRPs). These composites consist of a matrix material, such as epoxy or polyester resin, reinforced with fibers made from materials like carbon or glass.
FRPs have high strength-to-weight ratios and can be used to reinforce concrete structures such as bridges and buildings.
Another type is particle-reinforced polymers (PRPs), which contain small particles dispersed throughout the matrix material. PRPs can improve mechanical properties such as stiffness and toughness while maintaining low weight.
Understanding the different types of polymer composites available allows you to select the best one for your project’s needs. Whether it’s reinforcing a bridge or constructing a new building, choosing the right composite will ensure that your structure stands strong for years to come.
Reinforcement Materials
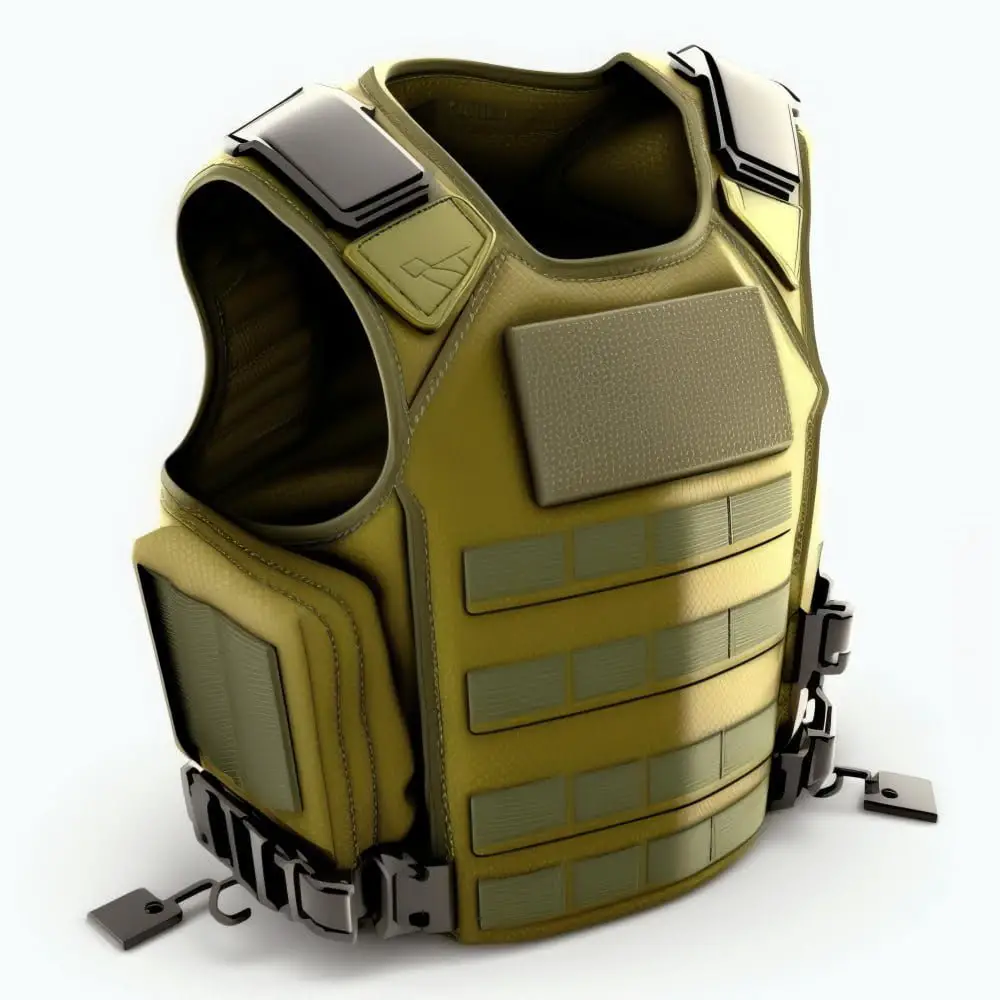
As we learned in the intro, polymer composites are materials made up of two or more constituent materials with different physical and chemical properties. One of these constituents is known as the reinforcement material.
Reinforcement materials provide strength and stiffness to the composite, while another constituent called matrix material holds everything together.
Reinforcement materials can be either natural or synthetic fibers such as carbon fiber, glass fiber, aramid fiber (Kevlar), basalt fibers among others. The choice of reinforcement material depends on several factors including cost-effectiveness and desired mechanical properties.
In fact, understanding how these components work together is crucial when choosing construction materials that will withstand harsh environmental conditions like extreme temperatures or corrosive chemicals.
So next time you’re building something – whether it’s a Lego tower or a real-life structure – remember that there’s science behind every decision you make regarding your choice of composite reinforcements!
Matrix Materials
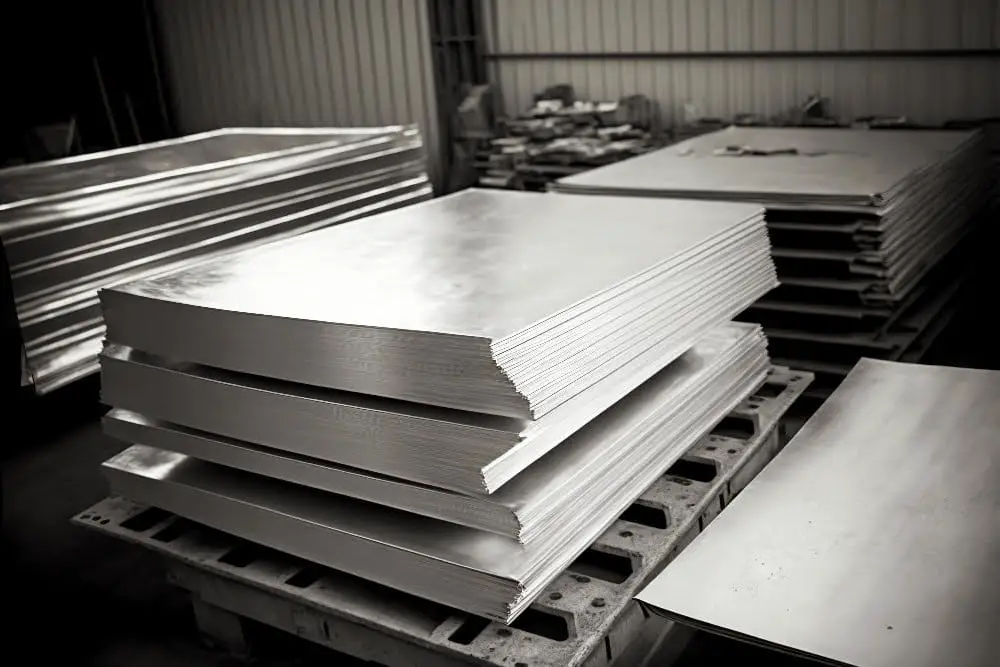
The matrix material is one of the constituents and plays a crucial role in determining the overall properties of the composite.
The matrix material can be thought of as the baseplate that holds all the individual bricks together.It provides structural support and helps distribute loads evenly throughout the composite.
Matrix materials can be made from a variety of substances, including thermosetting resins like epoxy or polyester, thermoplastic polymers like nylon or polypropylene, and even metals like aluminum or titanium.
The choice of matrix material depends on several factors such as cost, desired mechanical properties (like strength), environmental conditions (such as temperature), manufacturing process requirements (like curing time), among others.
Understanding how different types of matrices affect composite performance is essential for selecting construction materials that meet specific project needs while also being cost-effective. In upcoming sections we will explore other key components that make up polymer composites so you too can become an expert!
Manufacturing Techniques
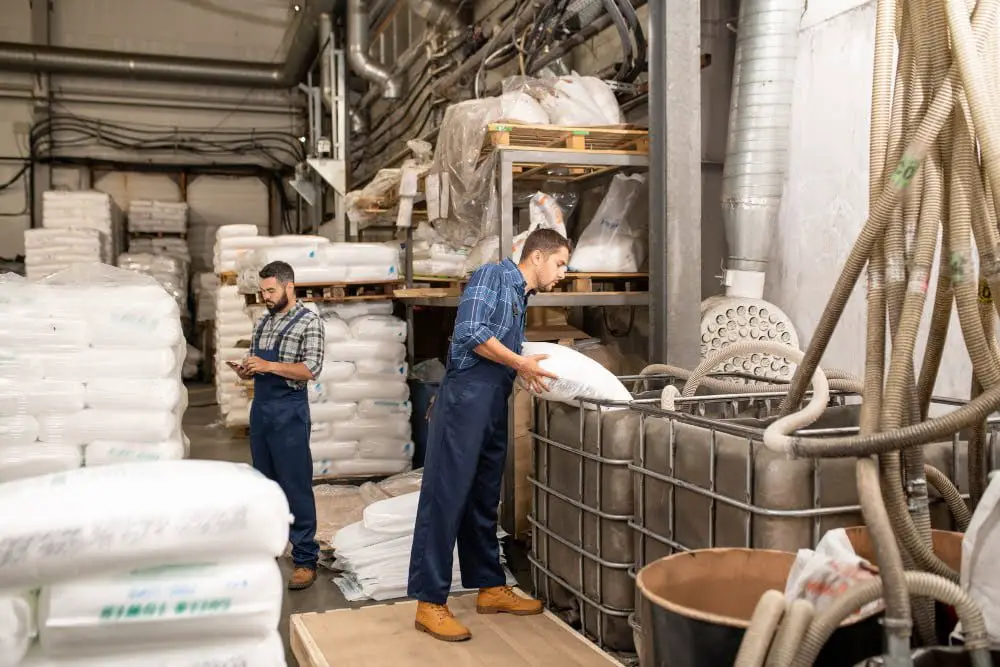
Just like building with Legos, manufacturing polymer composites requires a specific set of techniques. There are several methods used to create these materials, including hand lay-up, filament winding, and resin transfer molding.
Each technique has its own advantages and disadvantages depending on the desired properties of the final product.
For example, hand lay-up is a simple method that involves laying down layers of fiber reinforcement in a mold by hand before applying resin. This technique is ideal for creating large parts or prototypes quickly but may result in inconsistent quality due to human error.
On the other end of the spectrum is filament winding which uses continuous fibers wrapped around a rotating mandrel to create high-strength products such as pressure vessels or pipes. While this method produces consistent results with excellent strength-to-weight ratios it can be time-consuming and expensive.
Understanding these manufacturing techniques can help you select composite materials that meet your project’s requirements while staying within budget constraints.
Mechanical Properties
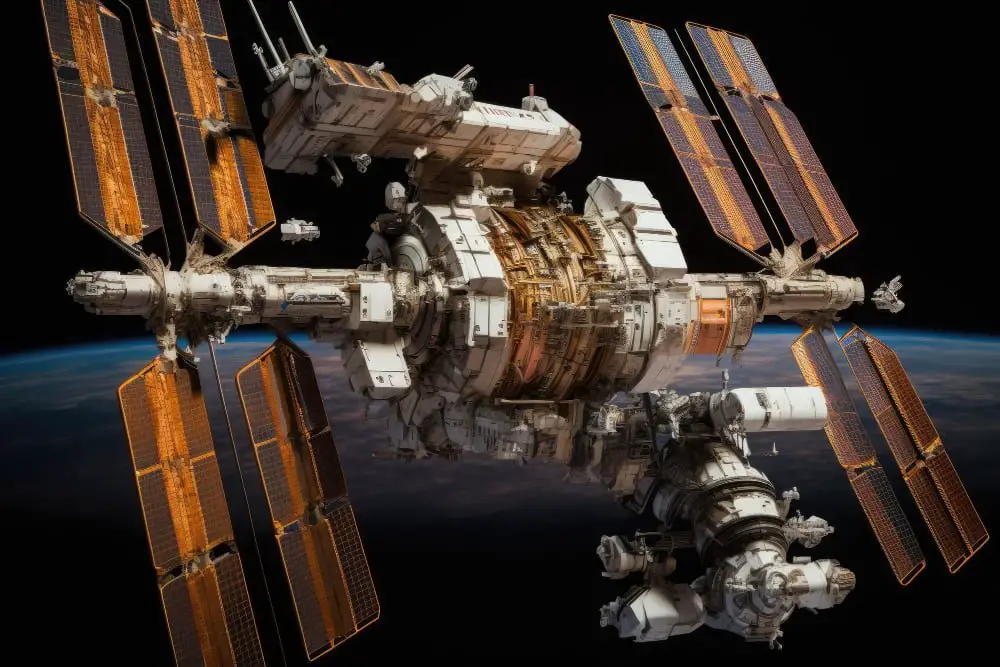
One crucial aspect to consider when choosing construction materials is their mechanical properties.
Mechanical properties refer to how a material responds to external forces such as tension, compression, and bending.
Polymer composites are known for their excellent mechanical properties. They have high strength-to-weight ratios which means they can withstand heavy loads without adding unnecessary weight or bulkiness to structures.
This makes them ideal for use in applications where weight reduction is critical such as aerospace and automotive industries.
But it’s not just about strength – polymer composites also exhibit exceptional stiffness and flexibility depending on the specific application requirements.
For example, some composite materials may be designed with higher stiffness values if they will be used in load-bearing applications like bridges or buildings while others may require more flexibility if they will be subjected to vibrations or impacts like wind turbine blades.
Understanding these mechanical properties of polymer composites can help you make better decisions when selecting construction materials that meet your project needs while ensuring safety and durability over time.
Thermal Behavior
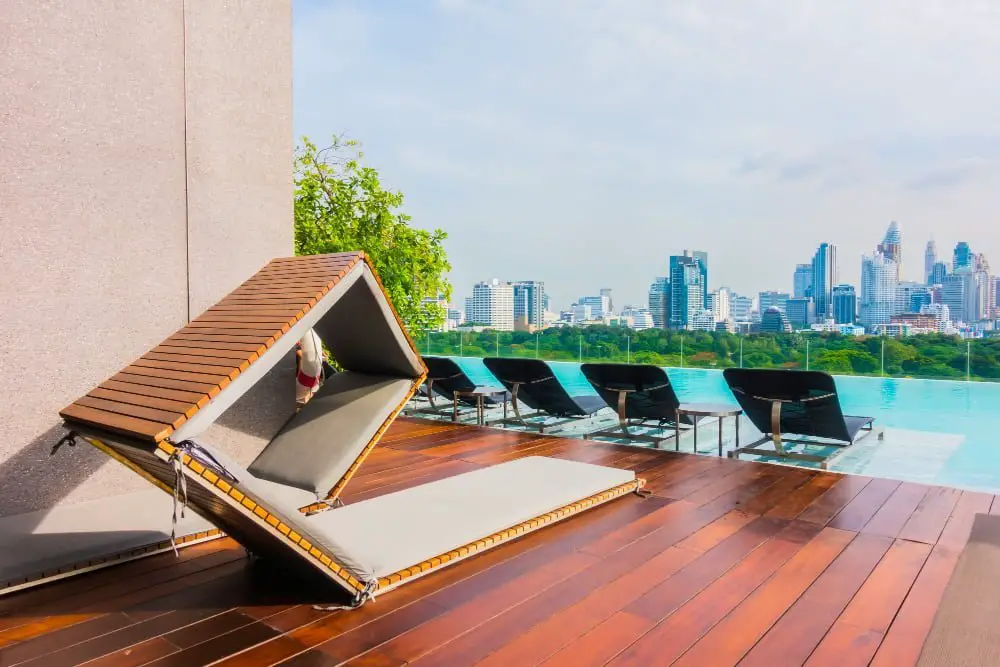
Polymer composites have unique thermal properties that make them ideal for certain applications.
Thermal expansion is a common issue in construction, especially when dealing with materials like metals and concrete. These materials can expand or contract significantly due to changes in temperature, leading to structural damage over time.
Polymer composites, on the other hand, exhibit minimal thermal expansion and contraction compared to traditional building materials. This makes them an excellent choice for structures that will be exposed to extreme temperatures or frequent temperature fluctuations.
For example, composite decking boards are becoming increasingly popular because they do not warp or crack under high heat exposure like traditional wood decks would. Similarly, polymer composite pipes are used extensively in industrial settings where they need to withstand high-temperature fluids without degrading over time.
Understanding these unique properties of polymer composites can help you make better decisions when selecting construction materials for your next project – ensuring durability and longevity while minimizing maintenance costs down the line!
Electrical Conductivity
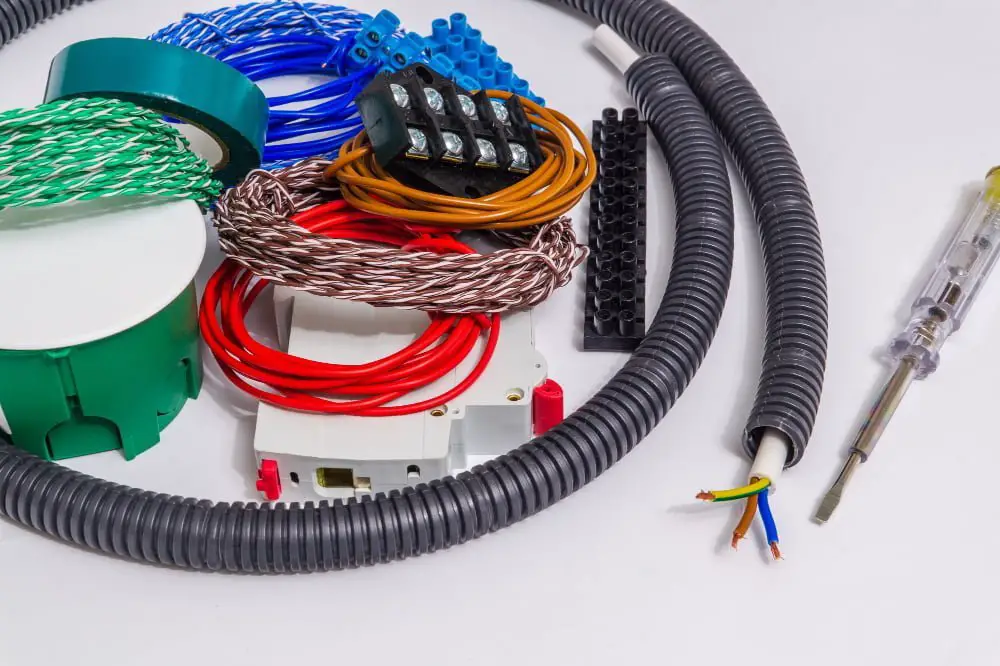
Polymer composites have a wide range of properties that make them suitable for various applications. One such property is electrical conductivity.
Polymer composites can be designed to conduct electricity or insulate against it, depending on their intended use. For example, composite materials used in electrical wiring must have high conductivity to allow the flow of electricity without resistance.
On the other hand, composite materials used as insulation must have low conductivity to prevent electric shock and fires.
The ability to control electrical conductivity makes polymer composites an ideal material for a variety of applications beyond just construction. From electronics and aerospace industries to medical devices and renewable energy systems – these versatile materials are changing how we build our world.
Understanding these unique properties is crucial when selecting construction materials because it ensures that you choose the right material for your specific project needs while also considering factors like cost-effectiveness and sustainability.
Durability and Aging
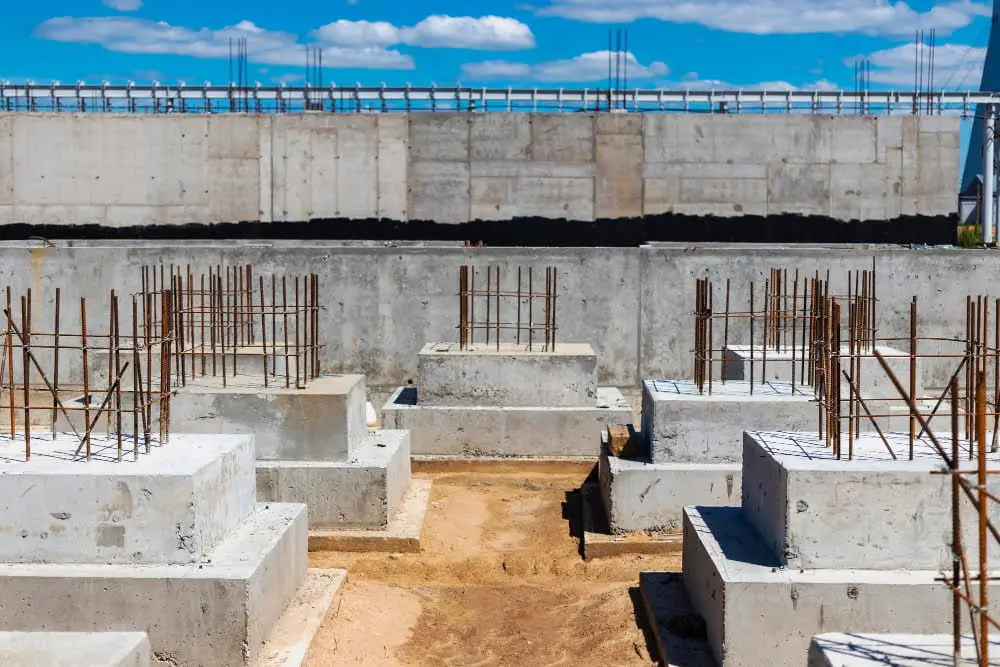
Polymer composites are known for their exceptional durability and resistance to aging. Aging can cause materials to weaken over time due to exposure to environmental factors such as sunlight, moisture, and temperature changes.
However, polymer composites have been shown to maintain their strength and structural integrity even after years of exposure. This is because they are made up of multiple layers that work together synergistically.
The outer layer protects against environmental damage while the inner layers provide strength and support. Understanding how polymer composite materials age can help you make better decisions when selecting construction materials for your project.
By choosing durable options like polymer composites, you can ensure that your structures will stand strong for years or even decades into the future – just like my childhood Lego creations!
Applications in Construction
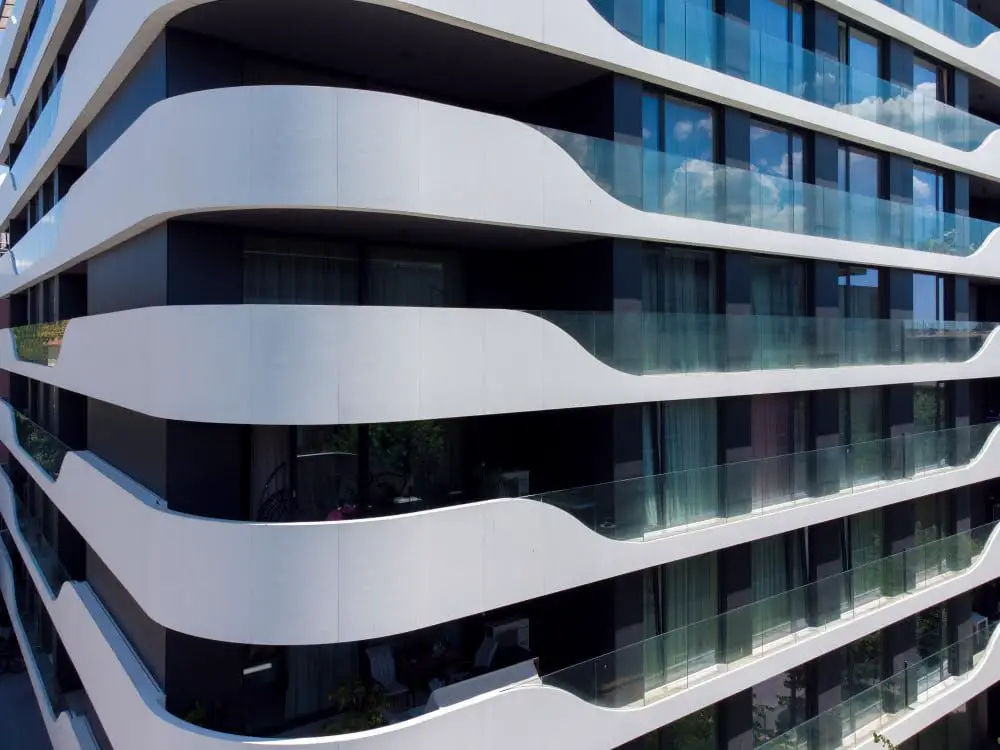
These materials have revolutionized the construction industry by providing unique properties that traditional materials like steel or concrete cannot match.
Polymer composites are used extensively in various applications within the construction industry, including:
- Bridges: Polymer composite bridges are lightweight yet strong enough to withstand heavy loads and harsh weather conditions.
- Building facades: Composite panels can be used as cladding material for building exteriors due to their durability and resistance to corrosion.
- Pipes: Composite pipes offer excellent chemical resistance, making them ideal for transporting corrosive fluids such as acids or alkalis.
- Flooring systems: Composites can be used as flooring material due to their high strength-to-weight ratio and slip-resistant properties.
- Roofing systems: Composite roofing is becoming increasingly popular because of its ability to resist extreme weather conditions while still being lightweight
Understanding the science behind polymer composites is crucial when selecting materials for your next project since it will help you make informed decisions about which type of composite would work best based on your specific needs.
Recap