Explore the efficiency and versatility of Pre-Engineered Metal Buildings (PEMBs), demystifying their frame structure because your next construction project deserves this innovative solution.
Key takeaways:
- Rigid Frame Clear Span: Ideal for large, uninterrupted spaces.
- Modular Rigid Frame: Allows for wider buildings without interior columns.
- Single Slope Clear Span: Sloping roof ideal for retail spaces.
- Components of PEMBs: Roof and wall secondary elements, framed openings, insulation.
- Advantages of PEMBs: Cost-efficiency, time savings, reliability, sustainability.
Primary Steel Frame Options
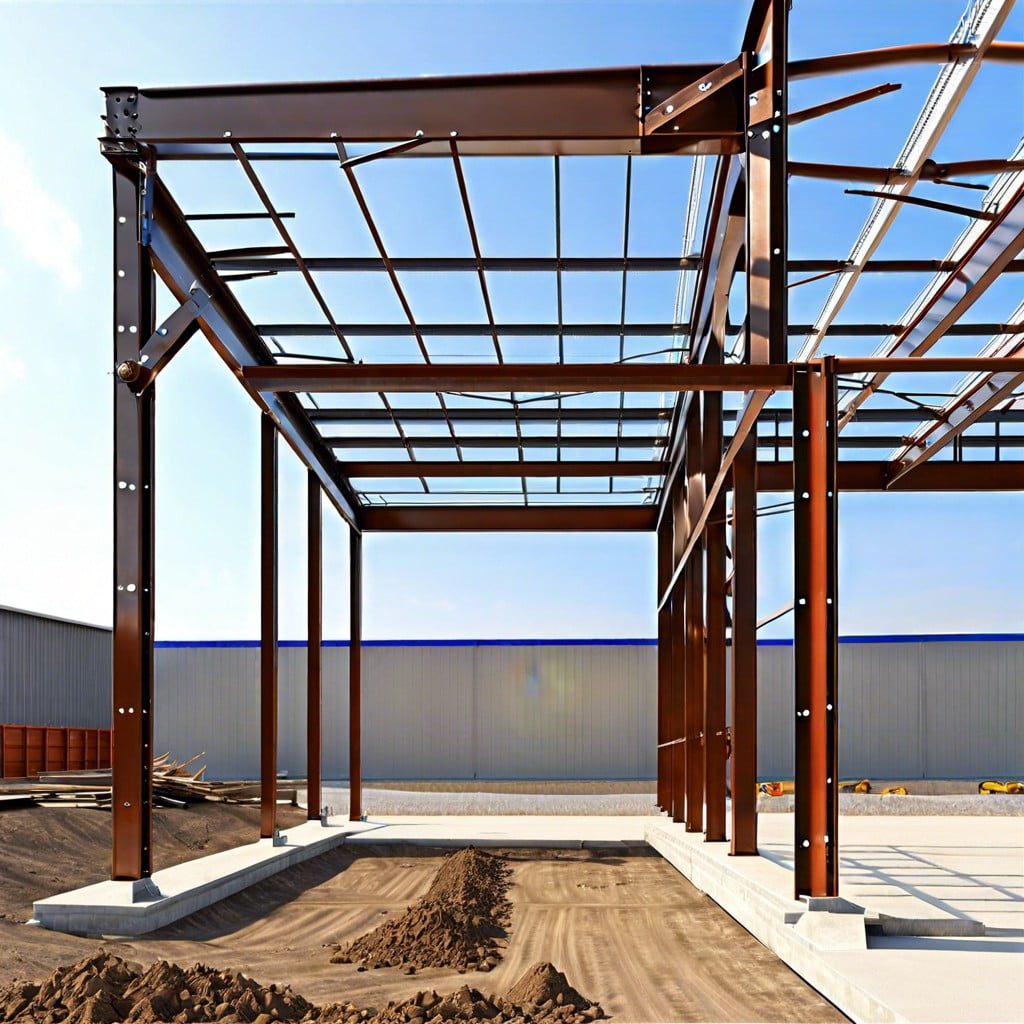
When considering primary steel frames in pre-engineered metal buildings (PEMBs), three main options surface tailored for an array of structural needs:
1. Rigid Frame Clear Span: Ideal for large, unobstructed interior spaces, this design does not require interior supports, thus maximizing floor usage. Common applications include aircraft hangars, arenas, and warehouses where uninterrupted space is crucial.
2. Modular Rigid Frame: For those requiring wider buildings without the expense of a single clear span structure, these frames accommodate internal columns strategically placed to support the load. Although they introduce obstructions, they allow for significantly wider buildings without the excessive cost.
3. Single Slope Clear Span: Characterized by a roof that slopes in one direction, this framing option is often used for retail spaces, strip malls, and office buildings. The design offers a contemporary look while providing the clear span benefits and allowing for varying eave heights.
Selecting the appropriate frame type depends on specific project requirements, including planned use, load demands, and aesthetic preferences. Each design ensures a balance between structural integrity and efficient use of space.
Rigid Frame Clear Span
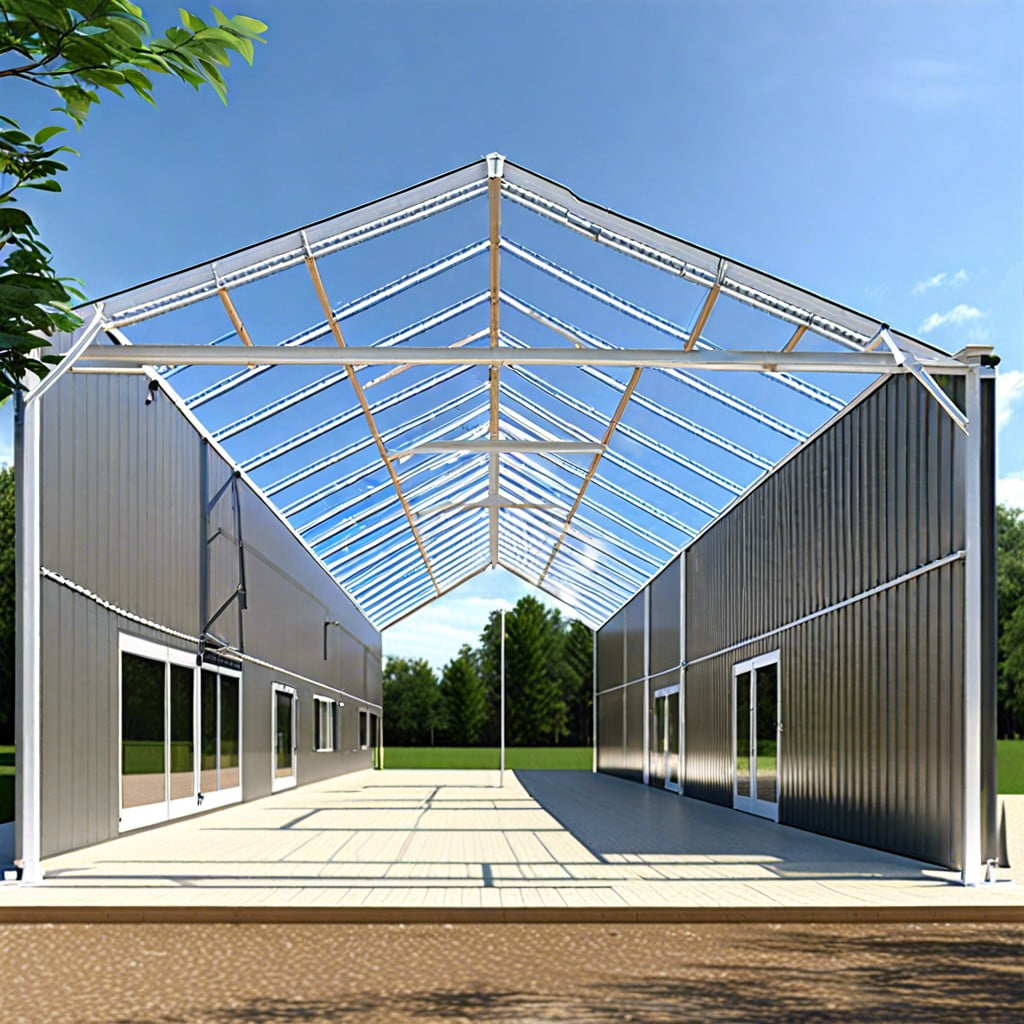
With spans reaching up to 300 feet wide, rigid frame clear span systems offer vast uninterrupted space, making them ideal for warehouses, aircraft hangars, and sports arenas where column-free interiors are paramount.
The design flexibility of these systems supports a variety of architectural styles and can accommodate future expansions with relative ease.
By leveraging the strength of high-grade steel, these frames maintain structural integrity under heavy loads and in harsh weather conditions, while the absence of interior columns maximizes usable floor space, promoting efficient layout and workflow.
The adaptability of the clear span configuration also simplifies the installation of HVAC, lighting, and sprinkler systems, streamlining the overall construction process.
Modular Rigid Frame
Modular rigid frames expand the capabilities of the traditional clear span design by allowing for larger building widths without interior columns. This design utilizes multiple sections or “modules” that are connected to form a unified structure.
By incorporating internal support columns strategically positioned, these frames optimize the use of material, providing a cost-effective solution for wide-span buildings such as warehouses, manufacturing facilities, and sports complexes.
The versatility of modular design enables future expansions with minimal disruption to existing operations. It offers the perfect balance between the expansive interior space of clear span designs and the economic benefits of multi-span construction.
Single Slope Clear Span
This design consists of a single roof plane that doesn’t rely on interior columns or supports, offering an uninterrupted interior space. The roof slopes in one direction, making it an ideal choice for buildings that require drainage towards one side, such as in areas with heavy rainfall.
It is commonly utilized in retail stores, warehouses, and industrial applications where unobstructed space is desirable for operational efficiency. The simplicity of the single slope design can also contribute to lower construction and maintenance costs, as well as ease of expansion, if necessary.
Components of Pre-Engineered Metal Buildings
Pre-engineered metal buildings (PEMBs) consist primarily of a steel frame, combined with metal cladding for walls and roofs. Key components ensuring structural integrity and functionality include:
- Roof Secondary Structural Elements: Supporting the roof covering, these components include purlins, girts, and eave struts, typically made of cold-formed steel. Purlins run parallel to the building ridge, providing rigidity and attachment points for the roof panels.
- Wall Secondary Framing: Similar to the roof, wall girts offer support to the cladding and maintain wall stability. Together with the main frames, they contribute to the overall lateral resistance of the building.
- Metal Building Framed Openings: These are structural enhancements that facilitate doorways, windows, and vents. Equipped with headers and jambs, they reinforce openings against potential stress and deformation.
- Insulation: To maintain optimal energy efficiency, insulation is a critical component often installed within the roofs and walls of PEMBs. It not only regulates temperature but also mitigates condensation and noise.
Careful integration of these elements during design and construction yields a robust, versatile structure capable of withstanding various environmental stresses while providing interior comfort and utility.
Roof Secondary Structural
Secondary structural components in pre-engineered metal buildings play a pivotal role in stability and durability. The purlins, girts, eave struts, and other secondary members bridge between primary framing elements, bolstering the roof system.
Purlins, typically Z-shaped or C-shaped, span the frames, providing substrates for attaching the roof panels. Efficient placement of these components reduces deflection and enhances the capacity to withstand environmental loads. The use of galvanized steel or similar durable materials protects against corrosion, extending the lifespan of the building.
Innovations in design have led to systems allowing for quick assembly, with components often pre-punched for seamless bolting connections. The precision of these prefabricated elements ensures a snug fit, which greatly aids in the integrity and insulation of the building.
Wall Secondary Framing
Wall secondary framing serves as the skeleton to which exterior sheathing is attached, stabilizing the walls against forces such as wind and providing support for insulation and interior finishes. Essential components include:
1. Girts: These horizontal structural members are attached to the main frames’ sidewalls. They provide lateral support to the wall panel and transfer loads to the primary frame.
2. Cee or Zee purlins: Often used interchangeably with girts, they also can serve as the horizontal framing in walls, especially when continuity is necessary for strength and stability.
3. Base angle or base channel: These run along the base of the wall panels to facilitate their attachment and ensure a proper seal against the foundation or floor, minimizing potential for moisture ingress.
4. Eave struts: At the top of wall panels, these elements provide a transition between the wall and the roof. They align with roof purlins to support roof loads and maintain the integrity of the building envelope.
When properly installed, these components ensure a rigid and durable wall system capable of withstanding environmental stresses while supporting the functional needs of the building.
Metal Building Framed Openings
Framed openings in metal buildings facilitate doors, windows, louvers, and other components that require support within the structure. These openings are engineered with structural members, often featuring hot-rolled or cold-formed steel, to reinforce the integrity of the building at penetration points. They can be categorized as follows:
- Header and jambs: The header is the horizontal support across the top of the opening, while the jambs are the vertical supports on the sides. Together, they form the framework that maintains structural performance despite the interruption in the wall panel.
- Trim and flashing: To ensure weather tightness and a finished appearance, trim and flashing are installed around framed openings. This detail not only protects the building from the elements but also provides a neat and clean look.
- Load considerations: Properly designed framed openings account for wind, snow, and seismic loads. This ensures the building’s resilience and stability are preserved, even where modifications like doors and windows are introduced.
- Field-located vs. factory-located: Field-located openings provide flexibility onsite but need careful consideration to not compromise structure, whereas factory-located openings come pre-engineered, following precise design specifications for a seamless fit.
By incorporating framed openings, pre-engineered metal buildings accommodate a range of functional elements while safeguarding structural performance and aesthetic appeal.
Insulation
Effective insulation is a key component in the energy efficiency and comfort of a metal building. It performs multiple roles:
- Temperature Control: It keeps interiors cool in summer and warm in winter, reducing the need for extensive heating and cooling.
- Moisture Barrier: Proper insulation minimizes condensation, protecting against rust and corrosion.
- Energy Savings: By stabilizing the internal climate, insulation cuts down on energy costs.
- Sound Dampening: It also acts as a sound barrier, keeping external noise out and reducing echo within the structure.
Options vary from fiberglass and rigid board to reflective foil and spray foam. Each material has its thermal resistance, known as R-values, with higher R-values representing greater insulating power. The choice of insulation should match the climate of the area and the intended use of the building to ensure maximum efficiency and comfort.
Advantages of Pre-Engineered Metal Buildings
Cost-efficiency emerges as a foremost benefit, with pre-engineered metal buildings typically requiring less capital than traditional construction methods. Less labor, fewer materials, and a streamlined design process contribute significantly to these savings.
Time savings are also evident, as these structures are designed and fabricated offsite, allowing for a much shorter construction timeline. This leads to a faster return on investment as facilities can become operational sooner.
Reliability and durability are key characteristics, attributed to the high-quality steel and advanced engineering. These buildings withstand adverse weather conditions, require minimal maintenance, and have long life spans.
Sustainability is an additional advantage. Pre-engineered metal buildings are often made from recycled materials and are themselves fully recyclable, reducing their environmental footprint. Moreover, their energy efficiency can be enhanced with proper insulation and design, leading to lower utility costs.
Cost-Efficient
Pre-engineered metal buildings (PEMBs) present a cost-effective solution due to several factors that affect the bottom line during construction and over the building’s lifespan.
Bulk Material Purchase: Manufacturers buy steel in large quantities at a lower price, transferring the savings to the customer.
Streamlined Design: Standardized designs and factory-made components reduce architectural and engineering costs.
Reduced Labor Costs: The simplicity of assembly with PEMBs necessitates less labor, which can significantly cut down on construction costs.
Limited Waste: Precision manufacturing leads to minimal onsite waste, which not only is environmentally beneficial but also reduces the costs associated with waste removal.
Energy Efficiency: The availability of advanced insulation packages and tight-fitting panels minimizes energy consumption, lowering utility bills.
Low Maintenance: The durability of steel and the quality of prefabricated components mean reduced maintenance costs over the life of the building.
These elements work synergistically to make PEMBs an economically smart choice for a variety of construction needs.
Time Savings
Pre-engineered metal buildings (PEMBs) expedite construction through prefabrication of components. By manufacturing parts in a controlled environment, onsite assembly is streamlined, significantly reducing construction timelines compared to traditional methods.
This efficiency ensures faster occupancy and quicker return on investment. The integration of computer-aided design (CAD) and manufacturing technologies furthers this efficiency. Additionally, the ease of assembly requires less skilled labor and minimizes weather-related delays, maintaining the project’s pace.
These factors collectively contribute to the notable time savings inherent in PEMB construction.
Reliability and Durability
Pre-engineered metal buildings (PEMB) stand out for their superb strength-to-weight ratios, offering exceptional resistance to environmental stressors such as heavy winds, snow loads, and seismic activity. The engineering behind these structures is centered on ASTM International standards, ensuring they meet rigorous safety and performance benchmarks.
Galvanized steel, a common material in PEMB frames, provides a protective coating that resists rust and corrosion, extending the lifespan of the building. Additionally, the connections between the structural elements, typically bolted for precision, contribute to the overall stability and robustness of the construction.
The reliability of PEMBs is further backed by manufacturers’ warranties, often spanning several decades, underlining the confidence in their durability. Regular maintenance can prolong the service life of these structures, and should a component need replacement, the modular nature of PEMB design simplifies repairs, minimizing downtime and associated costs.
Sustainability
Metal buildings not only offer strong and quick construction options but also provide remarkable sustainability benefits. Thanks to the high recyclability of steel, these structures are inherently eco-friendly. At the end of their life cycle, nearly all components can be melted down and reused without any loss in quality, reducing the need for virgin materials.
Moreover, the energy efficiency of metal buildings is heightened through the use of insulated panels and advanced weatherproofing technologies, which keep heating and cooling demands to a minimum. The tight construction minimizes air infiltration, further enhancing energy conservation.
Eco-conscious advances don’t stop there. The reflectivity of metal surfaces counters the urban heat island effect, and when combined with appropriate insulation, the overall thermal performance is optimized. This translates to a lower carbon footprint for the duration of the building’s lifecycle.
Lastly, the adaptability of steel structures plays into the sustainability factor. Their modular design and non-load-bearing walls allow for easy renovations and adaptability to future needs, reducing the necessity for new construction and minimizing waste.
Collectively, these attributes contribute to a smaller environmental impact and position pre-engineered metal buildings as a forward-thinking choice for environmentally conscious construction.
Commercial Applications of Pre-Engineered Metal Buildings
Pre-engineered metal buildings (PEMBs) serve various commercial sectors due to their flexibility, durability, and cost-effectiveness. Retail storefronts and strip malls benefit from the clear spans and column-free interiors, allowing for customizable floor plans and maximized retail space.
For the industrial sector, warehouses and distribution centers utilize PEMBs for their vast spaces, essential for storage and logistics operations.
Auto shops and service buildings also leverage the high ceilings and open layouts of PEMBs for equipment maneuverability and service bays.
In agriculture, these structures provide ideal conditions for farm equipment storage, processing plants, and even large-scale indoor riding arenas.
Office complexes and corporate campuses are adopting PEMBs for rapid deployment and potential future expansion capabilities. The modular design allows for convenient scalability, meeting the growing demands of businesses.
Sporting facilities, including gymnasiums and indoor training centers, choose PEMBs for their clear spans that offer obstruction-free space necessary for athletic activities.
Similarly, event centers such as banquet halls and exhibition spaces utilize the large, open-concept areas for flexible seating arrangements and event configurations.
Lastly, aerospace and aviation industries favor PEMBs for hangars and assembly buildings due to the ability to accommodate large door systems and high clearance requirements, ensuring the safety and security of aircraft and equipment within.
PEMBs’ adaptability makes them a go-to solution for a plethora of commercial functions, underlining their integral role in the construction industry.
FAQ
What is a PEMB structure?
A PEMB structure is a pre-engineered metal building consisting of structural steel parts that are prefabricated elsewhere, then assembled at their ultimate location.
What is the difference between Pemb and conventional steel?
The primary differences between a Pre-Engineered Metal Building (PEMB) and conventional steel structures lie in the cost and construction speed, with PEMBs being typically more cost-effective and quicker to erect, while conventional steel offers greater design flexibility and durability.
What is the difference between PEB and structural steel?
The key distinction between Pre-Engineered Buildings (PEB) and structural steel lies primarily in their design and details, where PEB metal follows a three-plate design manufactured entirely in one factory, while structural steel does not.
What are the key benefits of employing a PEMB structure for industrial buildings?
PEMB (Pre-Engineered Metal Buildings) structures for industrial buildings offer key benefits such as cost-efficiency, strength and durability, customizable designs, construction speed, and environmental friendliness.
How do weather and environmental considerations impact the design and installation of PEMB structures?
Weather and environmental considerations significantly impact the design and installation of Pre-Engineered Metal Building (PEMB) structures, dictating material choice, insulation needs, and specific design elements like wind resistance and snow load capacity.
In what situations would conventional steel structures be preferred over PEMB options?
Conventional steel structures are generally preferred over Pre-Engineered Metal Buildings (PEMB) in scenarios where highly unique, architecturally intricate designs, or strict building code regulations are key considerations.
Recap