Explore the fascinating world of metal pole barns as we delve into their rising popularity, structural advantages, and diverse uses in today’s construction industry.
Diving straight into the heart of metal pole barn statistics, it’s fascinating to note the rising trend in their popularity. As of 2020, the metal building industry, inclusive of pole barns, has seen a growth rate of 3% annually.
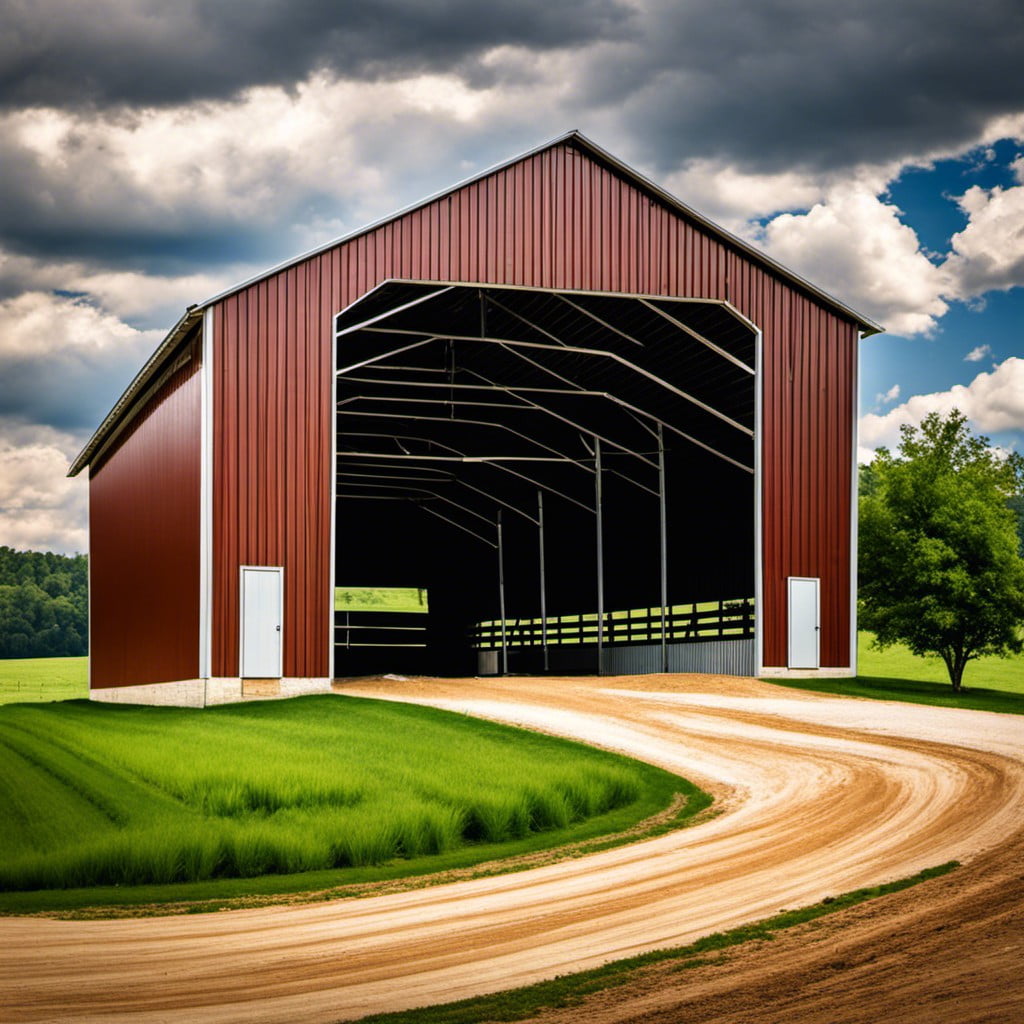
This growth is largely driven by the cost-efficiency and durability of these structures. In this piece, we’ll dissect the statistics behind this growth, exploring factors such as cost comparisons, regional popularity, and the environmental impact.
The aim is to provide you with a comprehensive understanding of the current state and future projections of the metal pole barn industry. Let’s delve into the numbers and trends shaping this sector.
The most common commercial pole barn size will be in the 30×40 range.
Diving into specific dimensions, the most frequently seen size for commercial applications falls within a specific bracket. In fact, numerous enterprises prefer a footprint of 30 by 40 feet. This size is an optimal choice for several reasons: it offers ample space for small businesses, including enough room for inventory or equipment storage, and allows a comfortable area for employee operations. Furthermore, this layout provides flexibility for various modifications such as additional office space or a small workshop, making it an advantageous and versatile selection in the pole barn industry.
The most common residential pole barn size is 24×24 and is designed for a garage or carport.
The 24×24 dimension is the most prevalent among residential pole barns, catering particularly to the need for garages or carports. This size is popular chiefly for its practicality and convenience, providing ample space for storing two average-sized cars with room left for some additional storage or workspace.
Tailoring the design and features to accommodate garage or carport requirements, such structures often include large openings for span, access and ventilation. It’s not unusual to see these barns outfitted with additional features like insulation, electrical systems, concrete floors, or even a small loft for extra storage.
A standard workshop can range in size from 20×12 to 30×26.
Establishing the ideal space for a standard workshop requires a thoughtful consideration of the necessary room for tools, machinery, and maneuverability. Sizes typically fall between 240 square feet (a 20×12 structure) and 780 square feet (measuring 30×26). These dimensions allow for comfortable occupancy, safe operation of equipment, and efficient storage and organization.
It’s important to remember, however, that these dimensions are not strict requirements, and needs may vary based on individual tasks and equipment used within the workshop.
The tallest pole constructed is 54′ to the peak.
Delving into construction records, an exceptional structure draws attention – a mighty 54-foot tall metal pole barn. This pinnacle registers as the current height record for this kind of structure.
To truly appreciate this monumental figure, understand the span from base to peak reaches nearly as high as a five-storey building.
The towering barn illustrates the remarkable flexibility and strength of metal construction, demonstrating that pole barns can comfortably exceed traditional residential and agricultural building dimensions when needed.
Pillaring high into the sky, this structure masterfully marries functionality with architectural audacity, pushing the conventional boundaries of metal pole barn construction.
The building shell takes 40% of the total cost of pole barn structures.
Comprising a significant portion of the overall expense, the building shell typically absorbs around 40% of a pole barn’s total cost. Like a supportive skeleton, this shell is essential as it forms the structure’s core framework. Costs associated with its construction vary based on material costs, pole-size and wall-height specifications, labor rates, and geographical location. Such expenditure is indeed rational, given its vital role in ensuring the building’s soundness, stability, and longevity.
Whether housing livestock or storing supplies, the outlay in the barn’s shell reflects in its functionality and durability.
The standard cost per square foot for a metal pole barn ranges between $15 to $40.
Depending on several key factors such as the region, complexity of design, and the current price of materials, the financial outlay for constructing a metal pole barn consistently ranges from $15 to $40 per square foot. This figure includes the cost of materials and labor. Customization of pole barns, like the inclusion of doors, windows, or insulation, and the type of the metal used, can also influence the overall cost per square foot.
It is important for potential contractors or homeowners to conduct in-depth research on pricing in their local area, solicit multiple bids, and be clear on their requirements before making an investment decision.
The average cost for a 30×40 pole barn ranges between $18,000 to $48,000.
Diving into the specifics, it’s important to understand that while constructing a 30×40 pole barn, the budget should align between $18,000 and $48,000.
This estimate includes factors such as the type of metal used, location, labor costs, and any additional features like insulation or interior walls.
However, it must be noted that these prices can flex, influenced predominantly by market fluctuations, the intricacy of design, and potential customization needs.
For a 40×60 pole barn, the average cost for installation is $36,000 to $96,000.
Shifting our focus to larger structures, we uncover intriguing cost patterns. On average, the installation of a 40×60 pole barn falls between $36,000 and $96,000. While acknowledging this wide range, it’s critical to understand the factors at play. These include the differences in material choices, added features, regional labor rates, and the complexity of the design.
Each can markedly influence the final expenditure, with the material costs being the pivotal element. In essence, a more intricate design or higher quality materials are going to push your budget towards the higher end of the spectrum, and vice versa. Therefore, with careful planning and smart choices, you can efficiently navigate through this financial landscape while ensuring a reliable and durable metal pole barn.
Pole barn materials make up 65% to 75% of the total project cost.
It is worth noting that the bulk of a pole barn project’s budget is often consumed by the cost of materials. The percentage, in fact, ranges between 65% and 75% of the total expenditure. These materials include everything from metal panels and trim, to roof purlins and wall girts. Also included in this price are all the critical components like trusses, doors, windows, and hardware. Financing these elements can guide one’s budget planning, helping to avoid unanticipated expenses. Therefore, it is advisable to thoroughly research materials and their market prices before initiating such a project.
The labor cost to build a pole barn averages $5 to $10 per square foot.
Labor costs form a significant part of the overall expenses involved in constructing pole barns. Generally, these charges can range from as low as $5 to as high as $10 per square foot.
This means that for a structure measuring 2,000 square feet, for instance, labor costs alone could run anywhere between $10,000 and $20,000.
These expenses can fluctuate based on factors such as the complexity of the project, local labor rates, and the time of year.
Therefore, it is crucial to factor this in during the budgeting process for a more accurate financial projection.
References:
- https://www.extremepolebuildings.net/
- https://info.fbibuildings.com/
- https://homeguide.com/
Recap