Discover how metal building framing surpasses other construction methods, because of its durability, adaptability, and cost-effectiveness in this detailed guide.
Key takeaways:
- Metal building framing types: Clear Span, Modular Frame, Single Slope, Lean-To
- Components: I-beams, girts, purlins, eave struts, anchors, bolts
- Solid-beam metal structures for warehouses and hangars
- Importance of end wall frames and columns
- Secondary framing, bracing, and framed openings.
Building Types
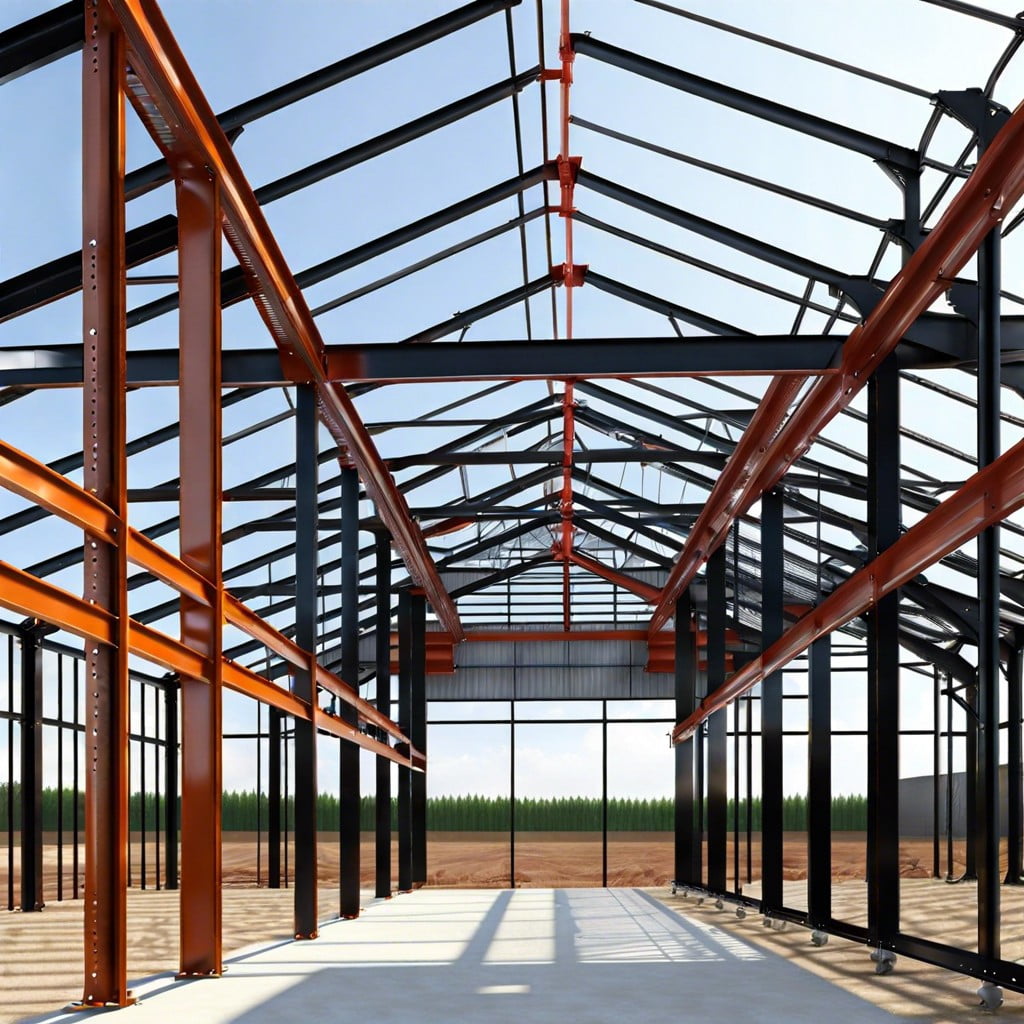
Metal structures are designed to accommodate a wide range of applications, often classified by their intended use, structural design, and size. The most common types include:
- Clear Span Buildings: These lack interior columns, providing large, unobstructed space that’s ideal for warehouses, aircraft hangars, or indoor sports facilities.
- Modular Frame Buildings: With interior columns, these are suited for larger spaces where clear spans are impractical or cost-prohibitive. They provide excellent structural support and are often used in manufacturing or storage.
- Single Slope Frames: Offering a sloped roof in one plane, these are typically utilized in retail complexes, office buildings, and mini storages where drainage or aesthetic considerations are a priority.
- Lean-To Frames: As an attachment to existing buildings, lean-tos are a cost-effective solution for expansion, offering additional space for storage or work areas.
Each building type is engineered with specific details to ensure structural integrity, efficiency in space utilization, and adaptability to future modifications or expansions.
Components
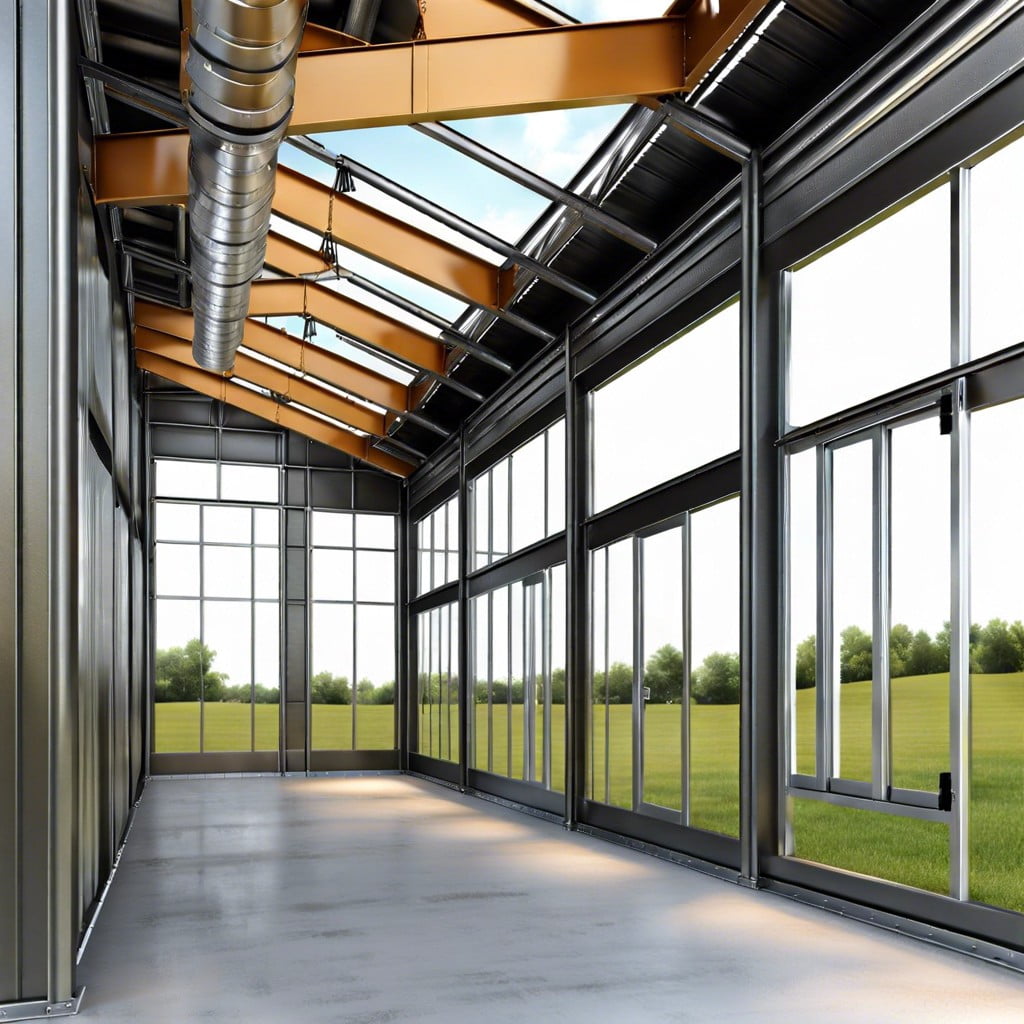
Metal building systems comprise a variety of interconnected components that collectively ensure structural integrity, functionality, and durability. The primary framing includes rigid I-beams which serve as the backbone of the structure. These are complemented by secondary framing elements such as girts and purlins, which increase stability and support wall and roof panels.
For attaching exterior sheathing and interior walls, girts and purlins are essential. These horizontal members affix to the primary framing, creating a substrate for cladding materials. Eave struts form the transition between the roof and wall panels at the eaves, performing a similar structural support role.
The sheeting that forms the walls and roof is secured to the secondary framing. It functions not only as a weather barrier but also contributes to the building’s load resistance. Trim pieces expertly seal the junctions between sheeting and framing members, safeguarding against the elements and improving aesthetic appeal.
Anchors and bolts play a critical role in affixing the building to its foundation, ensuring stability and resistance to uplift or shifting. Meanwhile, bracing systems, which may consist of rods, cables, or angle braces, add rigidity and support against lateral forces.
Finally, framed openings are integrated into the framing to accommodate doors, windows, and vents, often reinforced with hot-rolled sections for added strength around these points. These components are meticulously designed and positioned per engineering requirements to ensure efficient load transfer and overall structural fidelity.
Solid-Beam Metal Building Structure
Solid-beam metal building structures leverage the durability and strength of steel to create rigid frameworks. These beams, often formed from I-beams or plate steel, serve as the primary vertical and horizontal supports. Each beam is precision-engineered to withstand specific loads, factoring in climatic conditions such as snow, wind, and seismic activity.
The interlocking nature of the solid-beam design contributes to the overall stability of the structure. The beams are secured at their connections with high-strength bolts, ensuring that the frame can absorb and distribute stress effectively. Moreover, this type of framing allows for large, clear-span interiors, free of interior columns, giving maximum space utility. Solid-beam structures are ideal for warehouses, aircraft hangars, and manufacturing facilities where unobstructed space is essential.
Advanced coatings protect the metal against corrosion, extending the building’s lifespan and reducing maintenance needs. As part of the design process, calculations determine the optimal beam size and thickness, ensuring each structure meets the necessary building codes and performance requirements.
End Wall Frames and Columns
End wall frames and columns are critical components that support the vertical loads and stabilize the structure against longitudinal loads. They are typically constructed from I-beams, C-sections, or tube steel, depending upon the design and load requirements. These structural elements offer versatility, as they can be designed to bear heavy loads for end-use applications such as large doors or windows.
Key points to understand about this subtopic include:
- Design Variety: Depending on the building’s intended use, the end wall can be non-load bearing (requiring support from the main frame) or load bearing, designed to carry additional weight.
- Customization: Manufacturers can tailor end wall columns to accommodate specific dimensions, allowing for the integration of various types of doors and windows.
- Anchoring and Stability: Proper anchoring to the foundation is essential for maintaining the structural integrity of the metal building; the attachment method must account for environmental stressors such as wind uplift or seismic activity.
- Expandability: End wall frames are designed to facilitate future expansion of the building. The framing can be constructed to easily remove the end wall and extend the building lengthwise.
- Access Points: In the planning stage, it is essential to consider the end wall’s role in housing entry and exit points and its implications for the overall structural support of the metal building.
Understanding the function and design of end wall frames and columns is vital to ensuring the durability and strength of a metal building over its lifespan.
Metal Building Secondary Framing Detail
Secondary framing in metal buildings, comprising girts, purlins, and eave struts, serves multiple critical functions that enhance the structural integrity and resilience of the construction.
Girts: Horizontal structural elements attached to the main frame columns, girts provide support for wall panels and transfer lateral loads to the foundation.
Purlins: These horizontal members span the length of the roof, connecting the primary frames. They support the roof sheeting and manage loads such as snow, wind, and additional roof-mounted equipment.
Eave Struts: A key component at the intersection of the sidewalls and roof, eave struts stabilize the structure at the eaves and provide a fixed point for roof and wall paneling to meet.
These components are crucial for maintaining the shape and durability of a metal building, as well as for ensuring that sheathing materials have a secure anchoring point. With correct installation, secondary framing effectively distributes environmental stresses, contributing to the longevity of the architecture.
Bracing
Bracing in metal building systems is crucial for stability, ensuring the structure can withstand various forces such as wind, seismic activity, and the weight of the building itself. There are several bracing options, each serving a distinct purpose:
1. Cross Bracing: Utilized commonly with cables or rods, this forms an “X” pattern within bays of the frame, significantly enhancing lateral resistance and overall rigidity.
2. Portal Bracing: Often implemented in lieu of cross bracing to allow for doorways or large openings in the walls, this method reinforces the portal columns and rafters, forming a robust frame around the opening.
3. Flange Bracing: This type of bracing connects to the flanges of purlins or girts, aiding in the support of the roof and walls against buckling under pressure.
4. Diagonal Bracing: Installed at an angle, this bracing transfers shear forces to the foundation and is typically found on end walls.
5. Wind Columns: Erected within large-span buildings where standard bracing isn’t feasible, these columns act as additional support against wind pressure.
When selecting a bracing system, compatibility with the building’s design and local building codes is paramount. The right bracing ensures the structural integrity and longevity of a metal building.
Canopies and Roof Extensions
Canopies and roof extensions offer both aesthetic and functional advantages to metal buildings. These features not only enhance the visual appeal but also provide additional weather protection for entrances and exterior storage spaces.
Design and Integration: These structures are seamlessly integrated into the metal building design to maintain structural integrity and cohesiveness. They can be particularly beneficial for doorways, windows, and outdoor work areas by providing shelter from sun and rain.
Materials and Construction: Constructed from the same high-quality metal components as the main structure, they are designed to withstand the same environmental stresses. Typically, they are made of lightweight yet durable materials for easy installation without compromising on strength.
Drainage and Maintenance: Their design includes considerations for water drainage, ensuring that precipitation is channeled away from the building and its foundation. Low maintenance needs are another advantage, as the materials used resist corrosion and weathering.
Energy Efficiency: By offering shade, canopies and extensions can contribute to reducing the heat load on a building, leading to potential energy savings. This shading can be especially valuable in areas exposed to intense sunlight.
Customization Options: With a variety of colors and styles available, these features can be tailored to match the existing building and adhere to brand standards or local architectural features.
Metal Building Sheeting Details
Sheeting affixed to a metal building provides both protection and aesthetic qualities. Typically constructed from steel, this exterior covering is essential for the building’s durability and weather resistance. The gauge, or thickness, of the metal is a key consideration, with heavier gauges offering greater strength and longevity.
Fasteners play a critical role in securing the sheeting to the framing, with options such as self-drilling screws that facilitate efficient installation. It is crucial to ensure these are properly sealed to prevent leaks. Overlaps between sheeting panels must be carefully managed to maintain a weather-tight seal, and manufacturers often utilize specific profiles to aid in this alignment.
Panels are available in a variety of profiles and finishes, allowing for customization to meet aesthetic and functional requirements. The choices include vertical or horizontal placement, and a range of colors and textures, some of which can provide additional energy efficiency benefits.
The sheeting also includes trim pieces at corners, eaves, and base conditions to ensure a finished look and to help seal the building envelope. These trim elements not only enhance the building’s appearance but also contribute to its overall structural integrity and weatherproofing.
Trim
Trim in metal building construction serves both aesthetic and functional purposes. It provides a finished look, sealing off rough edges and covering gaps where different materials or components meet. By doing so, it also acts as a barrier to the elements, helping to prevent water, wind, and pests from penetrating the building envelope.
Key points to understand about trim include:
- Types: Common types include eave trim, which caps off the edge of a roof, and corner trim, which conceals the intersection of two walls. Jamb trim is used around doors and windows, while base trim creates a seal between the bottom of the wall panels and the foundation.
- Materials: The trim is typically made of the same metal as the building’s panels, ensuring compatibility and coherence in expansion and contraction rates, color, and longevity.
- Installation: Correct installation is crucial to ensure trim performs its protective role effectively. Fasteners should be appropriately sealed and placed at the manufacturer’s recommended intervals.
- Customization: Trim is available in a variety of colors and shapes to suit different building designs and customer preferences, thereby enhancing the structure’s visual appeal.
The incorporation of trim into the building design not only elevates the overall appearance but also reinforces the structure’s integrity, making it a critical component in metal building construction.
Color & Galvalume Plus Finish Warranty
Opting for a color finish or Galvalume Plus for your metal building not only affects its aesthetic appeal but also its durability. Here are some key considerations:
- Color finishes come with a variety of warranties, typically ranging from 20 to 40 years, protecting against chipping, cracking, and peeling.
- Galvalume Plus coating offers additional aluminum and zinc elements, enhancing the steel’s resistance to corrosion and rust, making it ideal for various environmental conditions.
- The longevity of the color finish and Galvalume Plus is ensured by their resistance to ultraviolet rays, reducing fade and maintaining their integrity over time.
- Warranties for paint systems often include a guarantee against fading, chalk, and color change, subject to the manufacturers’ specifications and exclusions.
- Regular maintenance is key to prolonging the life of the finish, and any warranty claims may require documented upkeep.
- It’s essential to review the warranty details to understand the terms, limits, and responsible parties for maintenance and warranty enforcement.
In summary, investing in quality finishes can significantly extend the life and appearance of a metal structure. Ensure that you are well-acquainted with the warranty specifications to make the most of your investment.
FRAMED OPENINGS
Framed openings in metal buildings serve as structural supports for windows, doors, and other penetrations. Here are key points to understand:
- Size & Location: Openings are cut to specific dimensions and placed based on architectural design, ensuring seamless integration with the building’s aesthetic and functional layout.
- Headers & Jambs: Heavy-duty headers and jambs reinforce these areas, distributing the structural loads around the opening and preventing deformation of the metal sheets.
- Trim & Flashing: These elements seal the framed openings, providing weather resistance and enhancing the building’s thermal efficiency.
- Load Considerations: Engineering calculations are essential to determine the impact of openings on the overall structural integrity, especially for large or numerous apertures.
- Customization: Depending on the end-use, openings can be customized for insulation, fire ratings, or noise reduction criteria, making them versatile components of metal building systems.
Incorporating these openings with precise engineering not only serves functional purposes but also ensures the longevity and safety of a metal structure.
Base Conditions
The foundation of a metal building is critical for structural integrity, and various base conditions are designed to anchor the structure properly. Here are some key points on base conditions:
1. Base Angle or Base Trim: This attaches to the edge of the slab or foundation and serves to secure the bottom of the wall panels, providing weather tightness.
2. Base Girt System: Used in some buildings for more substantial base support, a horizontal girt can be installed at the base to strengthen wall panel attachment.
3. Foundation Clips: These are attached to the slab and connect to the base angle or girt. They are crucial for ensuring the frame’s stability against horizontal forces.
4. Base Closure Strip: Made of foam or rubber, this seals the gap between the base angle and the foundation, preventing insect, rodent, and moisture ingress.
5. Anchor Bolts: Embedded into the concrete foundation, they secure the steel structure to the foundation. The bolt placement must be precise, as it aligns with the holes in the base plates of the columns.
6. Concrete Footings: Depending on the building size and design, footings may be required beneath the slab, providing a deeper, grounded support system for the weight of the building.
Each base condition is configured to meet the specific demands of the building’s design and environmental challenges, and selection should be guided by the local building codes and intended use of the structure.
Metal Building Plans and Framing Details
Precision-engineered metal building plans are essential for a successful construction project. These detailed drawings serve as a roadmap, outlining every aspect of the frame’s construction, including the size and placement of each component.
The key features of these plans often include:
- Layout: Displays the arrangement of columns, beams, purlins, and girts, ensuring structural integrity and efficient use of materials.
- Elevation Details: Provides a side view of the building to illustrate the relationships between different building heights and roof pitches.
- Section Views: Cut-away representations that offer an inside perspective on the construction, such as the connection between the foundation and the framing.
- Connection Details: Depicts the specific fastening and welding methods used to join metal components, which is critical to the building’s strength.
- Load Calculations: Includes the design loads for various elements, accounting for environmental factors like snow, wind, and seismic activity to comply with local building codes.
- Accessory Placement: Indicates the position of windows, doors, and ventilation systems for optimal functionality and aesthetics.
Understanding these plan elements is crucial to ensure that the framework is built to exact specifications, providing long-lasting durability and safety.
Foundation Plans Resource
Understanding the importance of a solid foundation for a metal building is paramount. Foundation plans are detailed drawings that communicate the exact dimensions, construction design, and specific requirements needed to support the structure. Typically, these plans must adhere to local building codes and are often necessary to obtain building permits. They outline specifics such as footing depth, slab thickness, and the placement of rebar or anchors that secure the metal frame.
To ensure accuracy and safety, it’s recommended to work with a structural engineer who can provide a certified foundation plan suited to the building design and local soil conditions. These professionals take into account factors such as load distribution, wind uplift, and seismic activity. Using a resource that specifies the foundation plans can offer several advantages:
- Customization according to the geographical location and environmental conditions.
- Specification of suitable materials for long-term durability and structural integrity.
- Clarification of the load-bearing capacity needed for the intended use of the building.
- Provision of precise anchor bolt settings necessary for securing the metal structure to the foundation.
Securing a reliable foundation plans resource early in the project timeline is critical to laying a proper groundwork for metal building construction and ensuring a smooth integration of the frame and foundation.
Free (Initial) Certified Building Plans for ALL 50 States
Navigating the permitting process for a metal building project can be streamlined with access to certified building plans. These plans are designed to meet the structural codes and requirements specific to each of the 50 states, ensuring compliance from the outset.
Initial certified plans typically include detailed drawings of the frame, including precise measurements, load calculations, and specifications of materials. Having these documents from the start facilitates easier communication with local building authorities and speeds up the approval process.
Additionally, some manufacturers and suppliers offer these initial certified plans at no extra cost when a metal building kit is purchased, contributing to cost savings and reducing the time frame for project commencement.
It’s important to confirm that the plans are stamped by a licensed engineer familiar with the state’s building codes where the structure will be erected.
FAQ
What is the spacing for metal building frames?
Metal building frames are typically spaced every 20 to 25 feet, but they can be engineered for different lengths based on the design requirements.
How do you attach wood framing to a metal building?
Attaching wood framing to a metal building requires the utilization of at least 2.5″ long screws such as Teks™ or self-drilling metal screws, ideally with a hex-head, after pre-drilling holes into the wood, and then fastening these screws through the wood and into the metal frame.
What is a framed opening in a metal building?
A framed opening in a metal building is an open portion of a wall specifically designed for access that includes elements such as jambs, header or sill, trim, and fasteners, accommodating features like overhead doors, windows, vents, or storefront glass.
What are the key considerations for metal building insulation?
Key considerations for metal building insulation include determining the right R-value, considering the type of insulation material (like fiberglass, spray foam, or reflective foil), ensuring proper installation to prevent condensation, and taking into account the specific insulation requirements of different building sections such as walls and roofs.
How do you determine the load capacity of a metal building frame?
The load capacity of a metal building frame is determined by factors including the type and grade of metal used, the thickness of the elements, the overall design, and the loads to which it will be subjected in terms of wind, snow, seismic activity, and occupancy use.
Can you modify a metal building frame post-construction?
Yes, a metal building frame can be modified post-construction, although it requires careful planning, specialized knowledge, and often professional assistance to ensure structural integrity is maintained.
Recap