Explore the fascinating world of metal building cost statistics as we delve into trends, variations, and factors influencing prices in this comprehensive guide.
Diving straight into the heart of the matter, metal building cost statistics can vary widely depending on a range of factors. These include the type of metal used, the size of the building, the complexity of the design, and the location of the construction site.
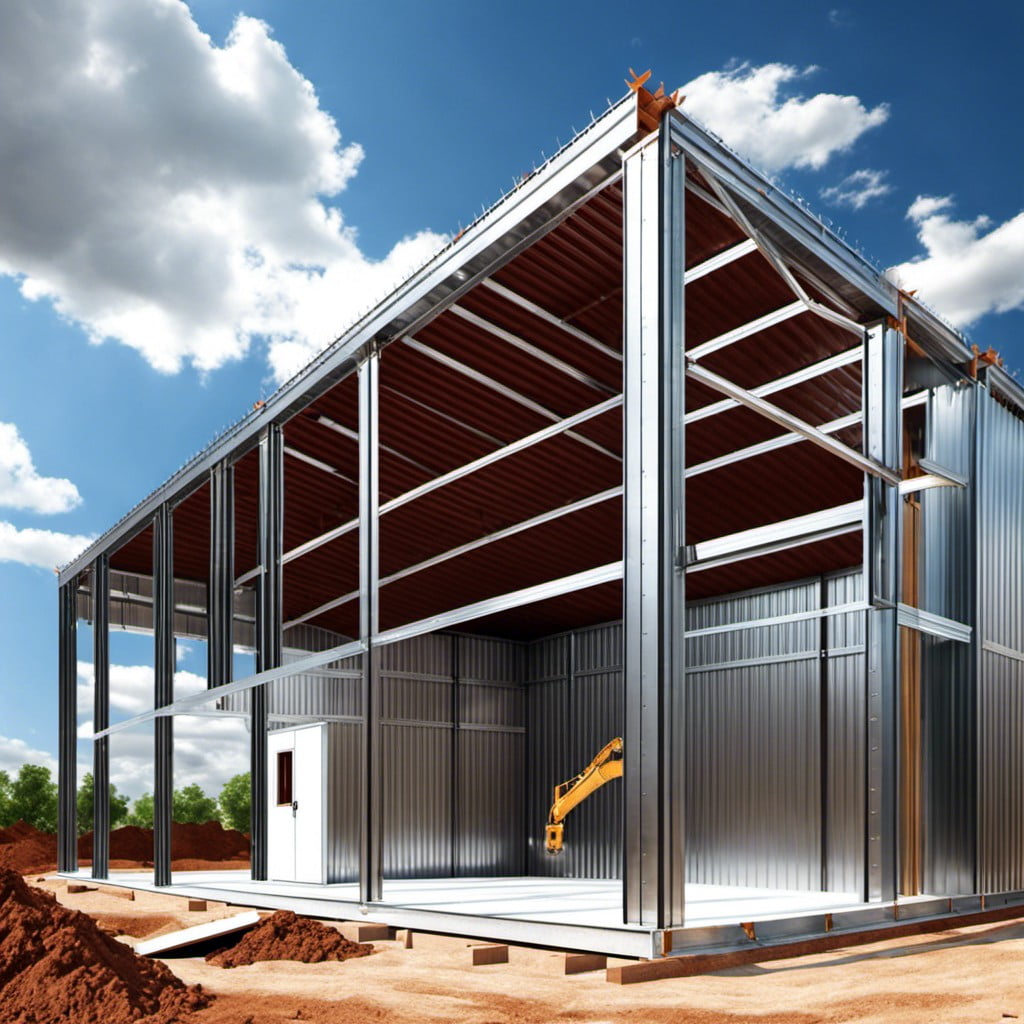
To truly understand these costs, it’s crucial to dissect each element. This article will provide a comprehensive breakdown of these components, offering you a detailed perspective on the cost dynamics in the metal construction industry.
Whether you’re a builder, a project manager, or a potential investor, this data-driven insight will help you make informed decisions about your next metal building project. Stay with us as we delve into the nitty-gritty of metal building costs.
Prefab metal building kit packages are priced between $15 and $25 per square foot.
Utilizing prefabrication methods for constructing metal buildings offers several advantages. Notably, it can lead to substantial savings. While the cost can vary depending on various factors such as the building’s size and complexity, kit packages are typically priced in a range that appeals to a wide spectrum of budgetary constraints.
The general range falls between $15 and $25 per square foot. This price includes the base building components and straightforward assembly instructions. It’s important to remember, however, that this is a baseline cost. Upgrades, customization, and shipping might add to the final bill.
Prefab metal building skyrockets to $1,306 per unit in the US.
Recent economic data indicates a significant change in the price dynamics of metal construction, with prefab metal building unit costs reaching unprecedented levels. The figure stands at a staggering $1,306 per unit, reflecting a notable upward trend.
This surge can be attributed to a multitude of factors, including fluctuating commodity prices, labor costs, and shifts in supply and demand.
This increase ignites a corresponding impact on the construction industry, potentially altering project timelines and budgets.
The most prominent growth was recorded in April 2022 with an increase of 241$ against the previous month.
In the month of April 2022, a marked escalation was recorded in the cost of prefabricated metal building kits. Comparing it to the previous month, the industry witnessed an augmentation of $241 per unit. The reasons behind this significant growth are varied and span from supply chain interruptions to mounting raw material prices. This sudden hike underlines the volatility of the industry and emphasizes the need for consumers to stay informed about changing trends and costs.
France is the biggest client in terms of prefabrication orders with a 55% share of total exports.
Dominating the international market, France’s order volume comprises more than half of the global exports for prefabricated metal buildings. Their 55% stake in the industry speaks volumes about their reliance on this construction method.
Diversified and forward-thinking, they utilize these structures across multiple sectors, including industrial facilities, logistics, and even residential buildings.
This high demand also implies an impressive growth rate within the French construction industry.
Rising costs of raw materials such as steel and aluminum greatly impact the overall price.
Surges in raw material costs significantly contribute to the escalating expense of metal buildings. As building blocks of construction, steel and aluminum are vital, and their pricing fluctuations have a direct correlation with the final cost.
In recent years, these prices have seen an upward trend due to an array of factors such as increased demand, labor shortages, and transportation costs. For example, steel prices soared by 15% within just the first quarter of 2022.
Similarly, tariffs and trade uncertainties can lead to surges in the price of aluminum. With these dynamics at play, it becomes clear that understanding market trends for these materials proves essential in estimating metal building costs accurately.
The cost for metal buildings could extend as low as $6 and as high as $120 per sqft.
Depending greatly on their complexity, the size, and the nature of their use, metallurgical buildings can significantly vary in expenses. A most basic, stripped-down structure, perhaps a small storage or utility building, might be procured even at the lower end of the cost spectrum, around 6 dollars per sqft. On the flipside, for structures necessitating extra sturdiness or those intended for commercial or residential use, the costs can spiral to upwards of $120 per sqft. Of course, these higher-end projects often involve meticulous customizations, upgraded aesthetics, and may require the integration of systems like HVAC, thus justifying the increased cost.
A 20,000 sq.ft. metal building typically costs between $240,000 to $380,000.
A considerable variation exists in the price range of industrial-grade metal structures. For a 20,000 sq.ft. building, prospective owners can expect an investment between $240,000 and $380,000. This range accounts for different customizations and options such as delivery and installation fees, insulation, doors, windows, and accessories.
The price can also vary based on site-specific conditions, such as local building code requirements and geographical limitations. Identifying the exact features and conditions that apply to a specific project, therefore, is key to getting an accurate estimate and making financially sound decisions.
A standard metal building size comes in 10s, such as 50’x100′.
In the metal construction industry, building dimensions are often divisible by 10. Common dimensions include 50 by 100 feet, providing a total of 5,000 square feet. This size is versatile, accommodating a wide range of commercial and industrial uses. Further customization is possible, enabling owners to alter the length, width, or height to meet specific needs without a significant impact on the cost. These standardized sizes contribute to the cost-effectiveness and efficiency of metal building construction.
Many steel buildings come with flat roof pitches of 1:12 or a ft rise for every 12 ft of length.
Versatility is one vital attribute of steel structures. While flat roofs are commonly seen, the pitch isn’t strictly one dimensional. A frequent configuration is a 1:12 ratio. Equating to a one-foot vertical rise for every twelve feet of horizontal distance, this slight inclination is highly effective in shedding rainwater. Moreover, this ratio blends efficiency with aesthetics, making it a popular choice among metal building owners.
Building heights up to 40 feet are possible and can be customized to fit the owner’s needs.
Customization enables owners to utilize building heights of up to 40 feet. This feature provides more space for various uses like storage, office, or manufacturing areas. Such significant vertical space can accommodate large machinery or enable stacking of goods for businesses, thus maximizing square footage value.
The owner’s requirements guide every customization decision, ensuring a perfect fit for their specific needs. Different industries can leverage this flexibility, satisfying operational needs without compromising design parameters. This versatility underscores the appeal of metal buildings.
References:
- https://www.buildingsguide.com/
- https://www.indexbox.io/
- https://apxconstructiongroup.com/
- https://www.alliedbuildings.com/
- https://www.cdmg.com/
Recap